Processus de haut fourneau de recyclage de gaz supérieur
Processus de haut fourneau de recyclage de gaz supérieur
Dans le domaine de la production de métal chaud (HM) par haut fourneau (BF), la technologie la plus prometteuse pour réduire significativement les émissions de CO2 (dioxyde de carbone) est le recyclage du CO (monoxyde de carbone) et du H2 (hydrogène) de la gaz sortant du top BF. La teneur en CO et H2 du gaz BF supérieur a le potentiel d'agir comme éléments gazeux réducteurs, et par conséquent leur recirculation vers le BF est considérée comme une alternative efficace pour améliorer les performances du BF, améliorer l'utilisation du C (carbone) et du H2, et réduire l'émission de CO2. Cette technologie de « recyclage de gaz supérieur » (TGR) est principalement basée sur la réduction de l'utilisation de carbone fossile (coke et charbon) avec la réutilisation des agents réducteurs (CO et H2), après l'élimination du CO2 du haut BF gaz. Cela conduit à réduire les besoins énergétiques. En raison des avantages d'une productivité élevée, d'un taux PCI (injection de charbon pulvérisé) élevé, d'un faible taux de carburant et d'une faible émission de CO2, etc. , le procédé TGR-BF est considéré comme l'un des procédés prometteurs pour la fabrication du fer à l'avenir.
Dans le TGR-BF, de l'oxygène (O2) est insufflé dans le BF au lieu d'air chaud pour éliminer l'azote (N2) dans le gaz BF supérieur. Une partie du gaz de tête BF contenant CO et H2 est réutilisée comme agent réducteur dans le BF. Le CO2 du gaz de gueulard BF est capté puis stocké. Plusieurs procédés de recyclage ont été proposés, évalués ou pratiquement appliqués pour différents objectifs. Ces procédés se distinguent par (i) avec ou sans élimination du CO2, (ii) avec ou sans préchauffage, et (iii) la position d'injection.
Le concept du TGR-BF (Fig 1) implique de nombreuses technologies qui incluent (i) l'injection de composants de gaz BF supérieurs CO et H2 dans les tuyères du puits et du foyer, (ii) la réduction de la consommation d'entrée de C fossile en raison de la réduction du coke (iii) l'utilisation de gaz O2 pur au lieu d'air soufflé chaud à la tuyère du foyer (élimination du N2 du processus) et (iv) la récupération de CO2 pur du gaz BF supérieur pour le stockage souterrain.
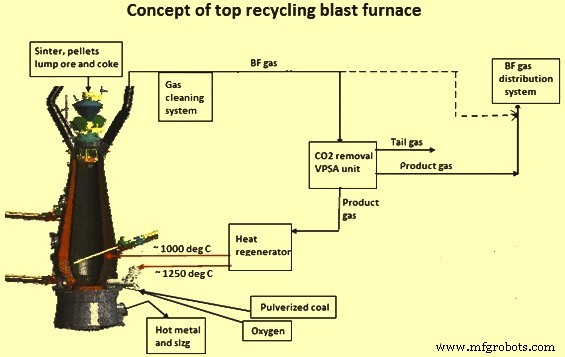
Fig 1 Concept de TG-BF
Le concept de recyclage des gaz de haut a été testé expérimentalement au BF expérimental (EBF) du LKAB à Lulea, en Suède. L'EBF a été modifié et une usine de séparation des gaz basée sur la technologie VPSA (vacuum pressure swing adsorption) a été construite à proximité de l'EBF.
Historique du recyclage des gaz BF top
Pour abaisser le taux du réducteur et pour augmenter la productivité du BF, plusieurs nouveaux concepts basés sur le procédé BF conventionnel, ont été introduits au cours du XXe siècle.
Déjà dans les années 1920, un concept a été développé pour l'injection du gaz réducteur chaud dans le BF. Le volume de gaz inférieur des tuyères dans le four devait être compensé par l'injection de gaz réducteur préchauffé à 1000 °C avec 27 % de CO, 33 % de H2 et 26 % de N2 dans la zone inférieure de l'arbre. En conséquence, seuls 30 % du coke (à l'époque 345 kg/tML) se sont avérés nécessaires pour le procédé BF. Au milieu des années 1960, cette idée a été reprise en Belgique et au début des années 1970, les premiers essais ont été réalisés sur un foyer BF de 4,6 m de diamètre à Cockerill-Seraing en Belgique. Une quantité spécifique de 400 N cum/tHM de gaz reformé qui a été préchauffé jusqu'à 1000 deg C a été injectée dans l'arbre inférieur du BF. Un taux de remplacement de 0,22 kg à 0,26 kg de coke par N cum de gaz réducteur a été observé.
D'autres enquêtes n'ont pas été menées pour des raisons économiques en raison du coût élevé du gaz naturel. A la fin des années 1970, les travaux de développement d'un nouveau procédé ont commencé en Allemagne dans lequel l'injection d'O2 pur froid, de carburant et de gaz recyclé était réalisée à deux niveaux de tuyère. Sur la base de cette idée, un procédé a été développé au Canada en 1984 pour un BF conventionnel sans deuxième rangée de tuyères. La principale caractéristique de ce concept était l'injection de charbon pour remplacer le coke. Les deux concepts n'ont jamais été réalisés et se sont terminés uniquement en tant qu'étude.
Presque au même moment, cette idée a été utilisée par NKK au Japon où une deuxième rangée de tuyères a été installée au milieu du puits. Du gaz réducteur préchauffé, constitué de gaz de gueulard recyclé sans élimination de CO2, a été injecté dans ces tuyères. Le gaz a été chauffé par combustion partielle avec de l'oxygène. De l'O2 froid, du charbon et du gaz de gueulard recyclé froid ont été injectés dans les tuyères du foyer. NKK a testé le procédé dans un BF expérimental avec 3 tuyères, un volume intérieur de 3,9 m² et un diamètre de foyer de 0,95 m. Le taux d'injection de charbon pourrait être augmenté à 320 kg/tML, tandis que le taux de coke pourrait être réduit à 350 kg/tML. La pénurie de gaz combustible dans l'aciérie intégrée à cause du recyclage du gaz BF supérieur a stoppé le développement de ce procédé, car le prix de l'énergie électrique et du gaz naturel était élevé au Japon.
La première exploitation commerciale d'un BF avec recyclage des gaz de tête a été réalisée à la fin des années 1980 en 12 campagnes par RPA Toulachermet en Russie au BF numéro 2 avec un volume utile de 1033 m3. Dans ce concept de procédé BF tout coke, du gaz de gueulard chaud et presque exempt de CO2 a été insufflé dans les tuyères du foyer, avec de l'O2 pur. Le gaz de gueulard décarbonaté a été chauffé dans des poêles chauds jusqu'à 1200 degrés C. Avec ce nouveau procédé, près de 250 000 tonnes de métal chaud (HM) ont été produites. Le taux de coke le plus bas atteint était de 367 kg/tML, par rapport à la référence de 606 kg/tML, ce qui signifiait une réduction du taux de coke de 239 kg (39 %). Au cours de ces campagnes, de graves brûlures de la tuyère ont été constatées, entraînant des modifications de la conception de la tuyère. Des difficultés avec le système de nettoyage au CO2 ont finalement arrêté le processus. En tenant compte de ces investigations de fond, le concept de TGR-BF ULCOS (ultra-low carbon di-oxide steelmaking) a été développé en 2004.
Développement d'ULCOS TGR-BF
Les travaux de développement ont été réalisés en deux phases. Dans la première phase de développement, qui s'est déroulée de 2004 à 2009, le procédé a été nommé « nouveau procédé de haut fourneau ULCOS ». Au cours de cette phase, trois nouveaux concepts de processus ont été développés et testés. Dans la deuxième phase qui a débuté en 2009 et qui a été baptisée "Procédé de haut fourneau à recyclage de gaz supérieur ULCOS", deux campagnes supplémentaires ULCOS TGR-BF ont été menées.
Au cours du développement, des modèles de bilan thermique et massique et un modèle 3-D axisymétrique du BF ont été utilisés pour le calcul des données principales et de l'état interne du processus pour la sélection des meilleurs paramètres de fonctionnement. Quatre alternatives ont été définies et examinées pour l'éventuelle économie de C accessible et la faisabilité de faire fonctionner le BF sous ces nouveaux concepts. La conclusion était que les alternatives 1, 3 et 4 devraient permettre d'obtenir une économie de C fossile de 21 % ou plus avec un niveau élevé d'injection de charbon pulvérisé. L'alternative 2 a été rejetée en raison de la faible économie de C attendue et de la nécessité d'une technologie difficile pour chauffer le gaz de recyclage en deux étapes d'abord dans un récupérateur, puis un chauffage supplémentaire par oxydation partielle. Toutes les alternatives comprenaient l'élimination du CO2 et l'injection de gaz produit riche en CO dans les tuyères du foyer, l'utilisation d'O2 pur et l'injection de charbon avec le gaz réducteur. Dans toutes les alternatives, l'utilisation de la biomasse, du minerai partiellement réduit et du gaz riche en hydrogène a été considérée comme une possibilité à l'avenir.
Dans l'alternative 1 (Fig 2), le gaz produit décarbonaté est injecté à froid avec de l'O2 pur et du charbon au niveau des tuyères du foyer et chaud au niveau des tuyères du puits. Un point critique de cette alternative était le faible débit de gaz froid au niveau de la tuyère du foyer, entraînant des tailles de canalisation plus petites et des températures de flamme plus élevées par rapport au procédé BF normal. De plus, une nouvelle conception de tuyère était nécessaire en raison des faibles débits de gaz.
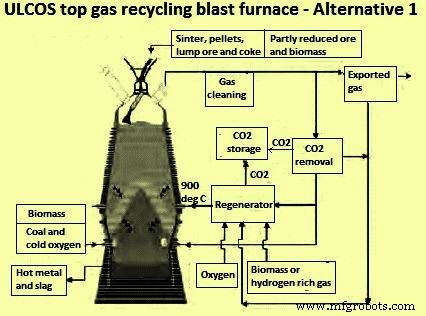
Fig 2 Haut fourneau à recyclage de gaz par le haut ULCOS – Alternative 1
Dans l'alternative 3 (Fig 3), le gaz produit décarbonaté a été injecté à chaud dans les tuyères du foyer normal avec de l'O2 et du charbon. Pour atteindre une économie de carbone élevée, il était nécessaire de fonctionner avec une faible RAFT (température de flamme adiabatique du circuit) et en même temps avec un taux d'injection de charbon élevé.
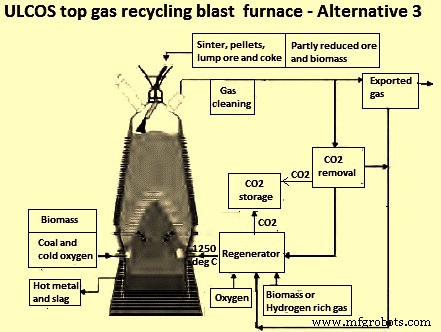
Fig 3 Haut fourneau à recyclage de gaz par le haut ULCOS – Alternative 3
Dans l'alternative 4 (Fig 4), le gaz produit décarbonaté était injecté chaud au niveau des tuyères du foyer et chaud au niveau du puits inférieur. La température du gaz recyclé variait de la température ambiante à 1 250 deg C.
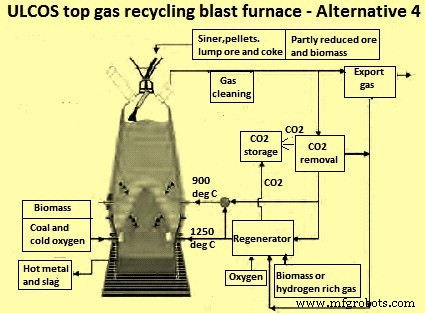
Fig 4 Haut fourneau à recyclage de gaz par le haut ULCOS – Alternative 4
Dans les variantes 1 et 4, le gaz produit est également injecté à travers des tuyères de puits. Les différences sont la température d'injection de gaz et la position des points d'injection. Dans tous les cas, la moindre partie du gaz était chauffée dans un système régénératif. Les économies de carbone fossile attendues pour l'alternative 1 étaient de 21 % à un taux de charbon de 170 kg/tML, l'alternative 3 était de 24 % à un taux de charbon de 180 kg/tML et l'alternative 4 était de 25 % à un taux de charbon de 150 kg/tML. .
Une modélisation mathématique des conditions du raceway et des essais de gazéification ont ensuite été réalisés et des investigations à l'échelle laboratoire et pilote ont été réalisées pour la conception et l'ingénierie des tuyères sous les contraintes d'injection simultanée de gaz recyclé, d'O2 pur et de charbon pulvérisé. La géométrie de la tuyère a été améliorée sur la base des résultats des calculs pour éviter les points chauds et les pannes pendant le fonctionnement et pour maintenir une impulsion suffisante du flux de gaz pour former un chemin de roulement avec une profondeur suffisante.
Campagnes du processus TGR-BF dans le BF expérimental
L'objectif des essais était de démontrer le fonctionnement de l'EBF en mode TGR complet avec O2 pur et PCI au niveau des tuyères du foyer. Ceci a été réalisé selon les trois alternatives définies. La charge ferreuse était constituée de 30 % de pastilles et de 70 % d'aggloméré. Le taux de production de HM a été maintenu à un niveau constant de 1,5 tonne par heure et le taux de PCI a varié entre 130 kg/tML et 170 kg/tML. Au cours des différentes périodes d'essai, le volume de gaz de gueulard recyclé a été maximisé afin d'obtenir une économie maximale de carbone fossile. Les résultats obtenus lors des essais en EBF ont ensuite été comparés aux calculs du modèle.
L'alternative 3 et l'alternative 4 ont été testées en 2007, lors de la première campagne après un démarrage classique. L'alternative 3 a été testée pour l'optimisation à l'automne 2009 lors de la deuxième campagne qui a été suivie d'un test de l'alternative 1. Lors de la troisième et dernière campagne en 2010, l'accent a été mis sur l'alternative 4 à 900 ° C. L'alternative 4 a été considérée comme une alternative privilégiée pour le projet de démonstration de suivi ULCOS BF à l'échelle industrielle. La limite de 900 deg C pour la température du gaz réinjecté a été fixée pour éviter les problèmes de réduction de la silice par H2 des matériaux réfractaires.
Au cours de chaque campagne, des mesures in situ de la température et de la composition des gaz ainsi que des échantillons du matériau de charge ont été prélevés à partir de l'EBF avec les deux sondes en charge. Pour étudier le comportement du matériau de charge dans les nouvelles conditions de fonctionnement, des paniers avec différents matériaux d'aggloméré et de granulés ont été chargés dans l'EBF juste avant l'arrêt de la campagne. Ces paniers ont été récupérés de l'EBF lors de la dissection du four après la trempe à l'azote. Cela avait été fait lors des campagnes de 2007 et 2010. Lors de la deuxième campagne de 2009, seule la trempe a pu être effectuée en raison d'une fin de campagne non préparée en raison d'un problème dans le système de facturation EBF et, par conséquent, aucun panier n'a été facturé.
Au cours des campagnes, des échantillons de la zone cohésive ont été récupérés et la taille et la forme du chemin de roulement ont été mesurées pour une enquête plus approfondie. Les campagnes ont commencé par une semaine de fonctionnement normal BF conventionnel (soufflage d'air chaud) avec frittage, d'abord pour le chauffage et la stabilisation thermique, puis pour établir une référence pour le fonctionnement BF conventionnel. Après la référence, un arrêt a été effectué pour déconnecter le ventilateur et connecter le gaz produit aux réchauffeurs de galets (régénérateurs). Le démarrage en mode TGR-BF a été réalisé par soufflage artificiel composé d'O2 froid des lances et de N2 chaud des réchauffeurs à galets. Par étapes progressives, le N2 des réchauffeurs de galets a été remplacé par du gaz de gueulard décarbonaté (gaz produit).
Résultats des campagnes de l'ULCOS TGR-BF
La première conclusion qui ressort des campagnes est qu'il est possible d'opérer le procédé ULCOS TGR-BF. Aucun problème lié à la sécurité n'était survenu pendant les campagnes avec le nouveau processus. Le fonctionnement de l'unité VPSA, qui est la deuxième installation importante, s'est déroulé sans problème et sans défaillance majeure. L'EBF couplé à la cellule VPSA a très bien fonctionné pendant les campagnes.
Cependant, il convient de noter que le fonctionnement de l'unité VPSA a été influencé par les changements dans la composition du gaz de gueulard et le volume du gaz provenant de l'EBF. Par conséquent, les deux unités devaient être exploitées dans une relation très étroite. Le taux maximum de gaz de gueulard recyclé qui a été atteint lors des campagnes était d'environ 90 %.
Au cours des campagnes du procédé TGR-BF, un fonctionnement stable du BF a été expérimenté avec une descente en douceur de la charge et il était facile de maintenir la stabilité thermique. L'efficacité du gaz dans le puits BF était stable au cours des différentes alternatives et il y avait une bonne répartition du gaz comme le montrent les mesures des sondes de puits en charge. Cependant, il y a eu quelques pannes d'équipement pendant les campagnes en raison desquelles l'EBF a dû être arrêté pendant l'opération dans les nouvelles conditions de procédé. Certains longs arrêts ont nécessité de revenir à l'étape de fonctionnement du "fonctionnement conventionnel" avec souffle chaud artificiel d'O2 froid et fonctionnement N2 chaud. Les petits arrêts n'ont nécessité que l'arrêt de l'injection de gaz et l'ajout de coke et/ou de charbon supplémentaires.
Après le démarrage avec du N2, lorsqu'il n'y a pas de gaz BF supérieur disponible, le gaz produit peut être recyclé à nouveau dans un délai d'environ 1 heure. Tous les problèmes ont été résolus comme prévu et la stabilité thermique du BF n'a jamais été sérieusement menacée. Tout au long de la campagne, l'expérience acquise et la confiance accrue ont permis progressivement d'accélérer la reprise de l'EBF (au niveau de la production). A chaque changement d'alternatives (3 à 4, 3 à 1), le BF a été arrêté pendant environ 8 heures pour effectuer les raccordements gaz nécessaires aux tuyères du puits et le changement des tuyères du foyer.
Les expériences menées au niveau du laboratoire ont montré que le matériau de charge conventionnel ne serait pas un problème pour le nouveau procédé. Cela s'est confirmé au cours des campagnes. Aucun problème de procédé particulier n'était lié aux propriétés des matériaux de la charge. Les résultats des sondes et des échantillons d'excavation ont montré le profil de réduction d'un four de travail central qui est un faible niveau de réduction au mur et un niveau de réduction plus élevé au centre du four pour les échantillons d'aggloméré et de pastilles. Des essais de culbutage sur les échantillons d'excavation avaient montré un comportement de désintégration similaire à celui d'un procédé BF classique qui correspondait aux essais en laboratoire. À partir des travaux de test de charge, il a pu être conclu que les propriétés de charge telles qu'elles sont utilisées dans le BF conventionnel actuel ne semblent pas poser de problème pour le procédé ULCOS TGR-BF.
Les résultats obtenus lors des campagnes ULCOS TGR-BF ont été très encourageants en matière d'économie de C (charbon et coke). Les essais de l'ensemble des trois campagnes avaient montré une diminution substantielle du taux de réducteur qui était obtenue par l'injection du gaz de tête BF décarbonaté. Au cours des trois campagnes, l'apport de charbon et de coke est passé d'environ 530 kg/tML à 400 kg/tML, ce qui représente une économie considérable de C. L'apport de carbone a été réduit de 470 kg/tML à environ 350 kg/tML, ce qui a entraîné une une économie de C d'environ 25 %.
Bien que l'alternative 1 n'ait pas pu être pleinement explorée en raison de l'arrêt précoce de la deuxième campagne, la réduction maximale de l'apport de C via le coke était de 21 % par rapport à la période de référence en fonctionnement BF conventionnel. Pour cette alternative, une nouvelle technologie de tuyère a été développée. La conception de la tuyère consistait en des tuyaux coaxiaux avec le tuyau intérieur utilisé pour l'injection du charbon pulvérisé et le tuyau extérieur pour l'injection d'O2. Les trois tuyères installées ont très bien fonctionné et après le démontage, aucun dommage ni usure n'a été observé. Le VPSA a pu recycler jusqu'à 88 % du gaz de gueulard BF.
En ce qui concerne l'alternative 3, la consommation de C pourrait être réduite jusqu'à 15 % lors de la première campagne avec un taux de recyclage des gaz de tête d'environ 72 %. Les résultats de cette alternative étaient inférieurs (environ 15 %) à ceux attendus des calculs de bilan thermique et massique (24 %) car il s'agissait de la première expérience avec le mode de recyclage des gaz de gueulard et le procédé n'était pas optimisé. Lors de la deuxième campagne, les résultats de cette alternative ont été bien meilleurs, lorsque la réduction maximale de l'apport de C d'environ 25 % a été atteinte avec un taux de recyclage des gaz de tête jusqu'à 90 %.
Dans le cas de l'alternative 4, une économie de C de 24 % a été obtenue avec un taux de recyclage des gaz de tête de 90 %. En termes de consommation de coke et de charbon, le nouveau procédé (alternative 4) a permis d'économiser jusqu'à 123 kg/tML par rapport à la période d'exploitation de référence. A partir de ces résultats, une bonne corrélation entre la quantité de gaz injecté (CO+H2) et la réduction du taux de réducteur a pu être déterminée. L'apport de C via le coke et le charbon pourrait être réduit de 17 kg en moyenne par 100 N cum de gaz (CO+H2) injecté.
Les campagnes d'EBF ont prouvé qu'il est possible d'exécuter un processus BF à un niveau de consommation de C fossile beaucoup plus faible par rapport au niveau de consommation de l'actuel BF. Une économie de C jusqu'à 25 % a été prouvée par l'injection du gaz de gueulard décarbonaté réducteur. Il s'agit d'une baisse significative par rapport au procédé BF actuellement le mieux exploité. En fait, l'application de la technologie BF-TGR sur le BF moderne devrait conduire à réduire la consommation de C d'un niveau actuel d'environ 405 kg C/tML à un niveau d'environ 295 kg C/tML.
L'unité VPSA a fonctionné de manière stable. Il avait été constaté que l'unité VPSA pouvait traiter 97 % du gaz de gueulard du BF. La fraction volumique moyenne de CO2 dans le gaz injecté était d'environ 2,67 % et le taux de récupération de CO était de 88 %, répondant aux exigences de quantité et de qualité. Combiné avec les unités VPSA et CCS, les émissions de CO2 réduites par le procédé TGR-BF pourraient atteindre 1270 kg/tML, ce qui représente 76 % des émissions totales de CO2 dans le procédé de fabrication du fer. 24 % du CO2 réduit l'a été par le recyclage du gaz et les 52 % restants ont été transportés et stockés sous terre par CSC.
Du point de vue du procédé, on peut affirmer que le fonctionnement ULCOS est plus stable que le fonctionnement BF conventionnel, en ce qui concerne la température et la qualité du HM. Cela semble essentiellement dû à la plus faible influence de la réaction de perte de solution liée aux niveaux beaucoup plus faibles de taux de réduction directe (DRR). La valeur la plus basse observée de ce DRR est de 5 %. Rien n'indiquait dans les résultats d'exploitation qu'il s'agissait effectivement de la valeur minimale pouvant être atteinte dans l'ULCOS TGR-BF. La qualité du HM a été largement impactée par le fonctionnement de l'ULCOS TGR-BF. En particulier, une diminution substantielle de la teneur en silicium (supérieure à 1 % absolu) et une augmentation corrélative de la teneur en C ont été observées. Il faut cependant souligner que la teneur en silicium dans le fonctionnement BF conventionnel est beaucoup plus faible (environ 0,5 % dans le BF conventionnel contre environ 2,0 % dans l'EBF), et qu'il ne faut donc pas s'attendre à un changement aussi important lors de l'application de l'ULCOS. Procédé BF-TGR à l'échelle industrielle.
Les campagnes d'essais d'ULCOS TGR-BF ont montré que le nouveau procédé TGR-BF est faisable et facile à mettre en œuvre. Il peut être utilisé avec une bonne sécurité, une grande efficacité et une forte stabilité. Les campagnes d'essais ont prouvé qu'il était possible de basculer le fonctionnement de l'EBF entre 4 modes de fonctionnement (classique, alternatives 1, 3 et 4). Il a également prouvé qu'il est possible de faire fonctionner le procédé BF et l'usine de séparation des gaz VPSA en boucle fermée. Les économies de C obtenues étaient cohérentes avec les prédictions des calculs du schéma de traitement. Les tests ont également indiqué que les matériaux de charge conventionnels frittés, les pastilles et le coke conviennent au procédé ULCOS TGR-BF.
Sur la base de l'expérience des campagnes EBF, les éléments qui nécessitent une attention particulière pour une application industrielle sûre et durable du procédé ULCOS TGR-BF sont (i) le risque de fuite de gaz au niveau de la tuyère peut exiger que le niveau de la tuyère soit physiquement séparé de la salle de coulée pour protection contre l'incendie, (ii) risque de fuite dû à la flexion des brides à haute température, (iii) allongement de la cheminée des poêles/chauffages chauds pour éviter les gaz toxiques dans les environs, (iv) pour éviter les pannes lors de la phase de démarrage , le personnel opérationnel doit être formé au gaz artificiel pendant le test de fonctionnement, (v) des paramètres d'injection optimaux sont importants pour éviter l'accumulation/le colmatage au nez de la tuyère, (vi) l'importance du contrôle individuel du débit de soufflage vers les tuyères pour éviter l'accumulation d'excès d'O2 et de charbon pulvérisé dans la tuyère en cas de colmatage, (vii) le choix des réfractaires et la fabrication des éléments réfractaires sont à modifier et l'utilisation d'ancres en acier C est à éviter si possible, alternativement ivement d'autres matériaux que l'acier C doivent être utilisés, ou l'acier revêtu d'alumine, et (viii) il est important d'éviter les poussières métalliques grâce à une sélection rigoureuse des pièces métalliques.
Les résultats des tests ont montré que l'alternative 4 avait le meilleur effet de réduction des émissions et a été sélectionnée comme premier choix pour l'essai à l'échelle industrielle BF lors de l'étape suivante.
Processus de fabrication
- Système d'automatisation, de mesure et de contrôle du processus de haut fourneau
- Génération et utilisation de gaz de haut fourneau
- Utilisation de coke de noix dans un haut fourneau
- Injection de charbon pulvérisé dans un haut fourneau
- Irrégularités du haut fourneau pendant le fonctionnement
- Système de refroidissement de haut fourneau
- Systèmes de chargement par le haut des hauts fourneaux
- Chimie de la fabrication du fer par procédé de haut fourneau
- Comprendre le processus de soudage au gaz