Processus ULCORED
Processus ULCORED
ULCORED est un procédé de réduction directe (DR) qui produit du DRI (fer réduit directement) dans un four à cuve, soit à partir de gaz naturel (GN), soit à partir de gaz réducteur obtenu par gazéification du charbon. Les gaz de dégagement du puits sont recyclés dans le procédé après la capture du dioxyde de carbone (CO2), qui quitte l'usine DR sous forme de flux concentré et est stocké. L'étape DRI produit un produit solide qui est ensuite fondu à l'aide d'un four à arc électrique (EAF). Le processus a été conçu principalement en 2006 par une équipe dirigée par LKAB, Voest-alpine et MEFOS.
L'objectif du procédé ULCORED était de réduire la consommation de GN nécessaire à la production de DRI. Il a été réalisé en remplaçant la technologie traditionnelle de reformage par l'oxydation partielle (POx) du NG. Combiné avec le dispositif CCS, ULCORED peut réduire de 70 % les émissions de CO2 par rapport à la moyenne de la route BF.
Le concept du procédé ULCORED consiste à séparer le CO2 du gaz de procédé. Il se caractérise par un effort pour adopter un processus DR à base de gaz pour une émission minimisée de gaz à effet de serre (GES), en utilisant la technologie de capture et de stockage du CO2 (CSC) et en même temps pour une utilisation minimisée de l'énergie. Le processus est conçu de manière à permettre l'extraction et le stockage du CO2. Le processus dépend donc également de CCS avec une capture en cours similaire.
Le processus est basé sur l'utilisation d'un levier de vitesses pour convertir le gaz de monoxyde de carbone (CO) de l'arbre en hydrogène (H2) avec une unité d'élimination du CO2. Cela ouvre une nouvelle évolution innovante du concept de processus.
Les principales caractéristiques du procédé ULCORED DR incluent (i) l'utilisation d'oxygène (O2) au lieu de l'air résultant en un gaz d'échappement de près de 100 % de CO2 qui doit uniquement être comprimé, (ii) il existe des possibilités de réduire l'exigence de GN de 15 % à 20 %, et (iii) le charbon, la biomasse, la biogazéification des déchets et le H2 peuvent être utilisés comme alternative au GN.
Le concept d'ULCORED est de répondre à la demande de réduction des émissions de CO2 en utilisant la réduction directe à base de minerai de fer et de gaz pour la production de DRI. Le concept comprend l'utilisation de 100 % d'oxygène (O2), de POx au lieu de reformeurs, d'un décaleur pour la production de gaz de réduction/excès sans CO2 et l'agent réducteur étant soit du gaz naturel, soit du gaz de synthèse issu de la gazéification du charbon/de la biomasse. Le gaz réducteur produit par la gazéification du charbon peut également être utilisé à la place du GN.
Procédé ULCORED DR basé sur NG
Les principales caractéristiques du procédé ULCORED DR basé sur NG sont (i) pas de reformeur, (ii) pas de réchauffeur et (iii) haute pression. En raison de la haute pression, il y a moins de vitesse de gaz dans l'arbre DR, moins de fluidisation et moins de fines quittant l'arbre DR. De plus, en raison de la haute pression, des unités d'élimination de CO2 et de POx plus petites sont nécessaires et la puissance requise pour le compresseur de recyclage est moindre.
L'originalité du concept est l'utilisation d'O2 à la place de l'air, ce qui signifie qu'il n'y a pas ou peu d'azote (N2) dans le gaz. Le reformage se fait par une unité POx de conditionnement du gaz de réduction (Fig 1). La technologie remplace le reformage classique du GN par oxydation partielle du gaz pour réduire la consommation de GN nécessaire à la production de DRI. La réaction POx qui a lieu est CH4 + 0,5O2 =CO + 2H2 avec delta H =– 8,6 Kcal/mol.
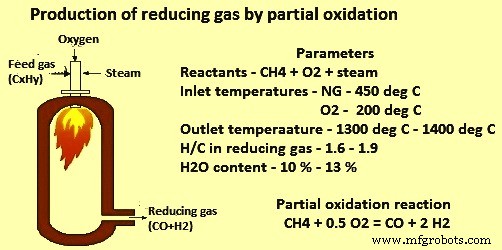
Fig 1 Réduction de la production de gaz par oxydation partielle
L'unité pilote pour la désoxydation partielle a été testée à Linde en deux campagnes avec un nouveau brûleur conçu pour le gaz d'alimentation riche en H2. Un réacteur tubulaire avec du gaz préchauffé (60 % H2 et 40 % CH4) a été utilisé. Les conclusions des essais de l'unité pilote étaient (i) Le brûleur et le réacteur pouvaient fonctionner sans problème, (ii) une flamme stable sans production de bruit significative pouvait être obtenue, (iii) la production de suie devrait être inférieure à 300 mg /N cum à 460 mg/N cum volume de gaz humide, et (iv) en raison de la pression atmosphérique, la teneur en CO2 et CH4 était supérieure aux pré-calculs sur la base de l'équilibre supposé. Une pression de fonctionnement plus élevée jusqu'à 7 kg/cm² peut réduire ce contenu.
Le puits DR a un flux à contre-courant de gaz réducteur injecté au niveau des tuyères et le minerai de fer est alimenté à froid par le haut. Le four fonctionne à une pression de 6 kg/cm² et à une température d'environ 900 degrés Celsius. Le gaz de puits est susceptible de contenir principalement du CO, du CO2, du H2 et du H2O.
Les gaz d'échappement de l'arbre, contenant principalement du CO, du CO2 et du H2O, sont conduits à travers un dispositif de changement de vitesse (un ou deux étages) convertissant le CO en H2. L'utilisation d'un sélecteur de gaz à eau entraîne une teneur élevée en H2 dans l'arbre de réduction. La réaction de changement de gaz à l'eau est CO (g) + H2O (g) <–> CO2 + H2. Presque tout le CO dans les gaz d'échappement du puits est déplacé vers H2 et le CO2 est éliminé dans l'unité d'élimination du CO2. L'augmentation de la production de gaz en excès augmente la demande d'énergie pour l'unité d'élimination du CO2 et la production d'O2. Le calcul du niveau correct d'excès de gaz est un processus itératif. Les niveaux estimés d'excès de gaz seront plus élevés pour cette raison. Le niveau excédentaire estimé de 2,2 giga calories par tonne de DRI devrait compenser la demande d'électricité supplémentaire. Ceci peut être réalisé grâce à une dérivation de certains gaz directement vers le levier de vitesses. La quantité de gaz contournée est déterminée sur la base des propriétés du gaz de réduction dans l'arbre de réduction. En raison de l'augmentation des volumes de gaz dans le système, le levier de vitesses et les unités d'élimination du CO2 nécessitent des investissements supplémentaires.
Dans l'unité de changement de vitesse, la réaction de déplacement du CO est exothermique et l'équilibre favorise la conversion du CO à un rapport vapeur/gaz élevé et à basse température, tout en n'étant pas affecté par la pression. Dans un système adiabatique, le glissement de CO réalisable est déterminé par la température de sortie. La conversion dans un seul lit de catalyseur est limitée par l'équilibre et, au fur et à mesure que la réaction progresse, la température élevée limite finalement la poursuite de la réaction. Cette limitation peut être surmontée avec un système à deux étages consistant en un changement à haute température suivi d'un changement à basse température, avec un refroidissement inter-lits. Une température de fonctionnement basse donne l'équilibre thermodynamique le plus favorable et donc le glissement minimum de CO. La plupart des usines H2 modernes ont des systèmes de refroidissement en amont du réacteur de conversion à basse température pour permettre un fonctionnement proche du point de rosée du gaz de procédé. Une marge de sécurité au-dessus du point de rosée doit être utilisée pour assurer une évaporation complète des gouttelettes d'eau qui peuvent se former dans le refroidisseur.
En fonction du rapport de vapeur, le réacteur de conversion à basse température peut être capable de fonctionner à une température aussi basse que 190 degrés C sans se soucier de la condensation. Dans le concept, le gaz supérieur passe par un dispositif de changement de température haute et basse avec récupération de chaleur entre les deux. Le décaleur à haute température convertit 97,2 % du CO et le décaleur à basse température complète à 99,5 % de conversion. L'échangeur de chaleur chauffe le gaz recyclé et sa capacité est calculée sur la base d'une différence de température définie du côté chaud de 50 deg C. Un excès de chaleur dans l'échangeur de chaleur produit de la vapeur vers le réseau de vapeur via un condenseur/rebouilleur.
L'unité d'élimination du CO2 est utilisée pour éliminer le CO2 du gaz produisant un gaz de réduction riche en H2 qui est réinjecté dans le procédé. L'unité d'élimination du CO2 est décidée par une distribution pour l'efficacité d'élimination du CO2, la récupération de H2 et de N2. Les deux procédés d'élimination du CO2 qui peuvent être utilisés sont le procédé d'adsorption modulée en pression sous vide (VPSA) ou le procédé d'épuration aux amines. Le choix de l'unité d'élimination du CO2 (VPSA ou amine) dépend des exigences locales. S'il y a un surplus de vapeur, l'extraction de CO2 exigeante en énergie peut être effectuée avec l'énergie de vapeur de l'usine au lieu de l'électricité nécessaire au VPSA. Les deux technologies ont des avantages et des inconvénients qui doivent être analysés plus en détail. Les deux technologies fonctionnent avec le concept ULCORED. Il est également possible d'utiliser une adsorption modulée en pression (PSA) pour l'élimination du CO2 à la place de l'unité VPSA en raison de la pression déjà élevée disponible dans le processus.
Le type de processus sélectionné affecte le schéma de processus et la mise en page. Le procédé VPSA nécessite, y compris la cryogénie et la compression à une pression de 110 kg/cm², 260 kWh de puissance par tonne de CO2 captée. Dans le cas du procédé de lavage aux amines, avec des amines hautes performances (méthyldiéthanolamine activée, aMDEA), le processus complet (amines et compression à une pression de 110 kg/cm²) nécessite environ 1,6 tonne de vapeur basse pression et 160 kWh de puissance par tonne de CO2 capturé.
La partie du gaz riche en H2 nettoyé contenant du N2 est évacuée du procédé afin de contrecarrer l'accumulation de N2 dans le gaz de réduction. Le gaz de purge est un gaz précieux qui peut être utilisé pour la production de vapeur ou le chauffage dans le système.
Le schéma de principe du procédé ULCORED à base de gaz naturel est donné en Fig 1.
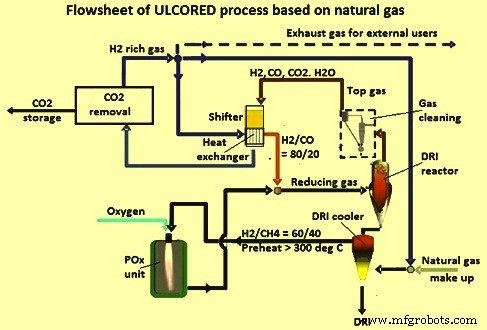
Fig 2 Schéma de principe du procédé ULCORED basé sur le gaz naturel
Procédé ULCORED DR basé sur la gazéification du charbon
L'option la plus économe en CO2 avec ULCORED est l'utilisation d'un gazéifieur de charbon produisant du gaz de synthèse pour l'usine DR et du gaz H2 pauvre en CO2 pour tous les utilisateurs de l'usine. Ce concept peut être adapté à la fois aux systèmes existants et aux systèmes modernisés.
Le concept basé sur le charbon est basé sur la production de gaz réducteur en utilisant la technologie existante de gazéification du charbon et soit la désulfuration à froid (basée sur la technologie existante) soit la désulfuration au gaz chaud. Le concept utilise l'O2 au lieu de l'air et inclut le stockage du CO2. La teneur élevée en H2 dans l'arbre de réduction est obtenue grâce à l'inverseur de gaz d'eau. L'excédent de gaz H2 est fourni aux autres utilisateurs de l'usine.
La gazéification du charbon est une technique bien connue et devrait être l'une des futures techniques de conversion d'énergie après l'épuisement des réserves de pétrole et de gaz. Il existe plusieurs technologies développées pour la gazéification du charbon. Il existe des différences entre les technologies mais elles fonctionnent généralement avec un rendement de conversion du C relativement élevé, généralement supérieur à 80 %. Un grand avantage de la gazéification du charbon est la possibilité de nettoyer efficacement le gaz de synthèse (tel que le soufre, le mercure, etc.) avant utilisation.
Le four à cuve pour la production de DRI fonctionnant à une pression de 6 kg/cm2, la pression du gaz du gazéifieur est diminuée grâce à une turbine de détente qui récupère également de la puissance (de 30 kg/cm2 à 6 kg/cm2).
Le procédé ULCORED DR peut être facilement intégré à une unité de gazéification du charbon, intégrant les avantages de l'originalité du concept du procédé. Le charbon est fourni à l'usine de gazéification du charbon. Le soufre est éliminé du gaz de synthèse par désulfuration à chaud ou à froid. Le gaz de synthèse propre est mélangé avec du gaz de recyclage riche en H2 nettoyé, préchauffé dans le refroidisseur DRI ou à partir de l'échangeur de chaleur entre le décaleur haute température et basse température.
Il existe trois manières différentes d'intégrer le gazogène au procédé ULCORED DR. Le gazéifieur peut être intégré soit en tant que gaz de synthèse froid, soit d'une manière où l'énergie thermique dans le gaz chaud du gazéifieur est utilisée. Trois configurations différentes ont été illustrées à la Fig 3. La possibilité de produire un excès de H2 pour le système est activée grâce à la dérivation du gaz de synthèse nettoyé directement vers les unités de changement de vitesse.
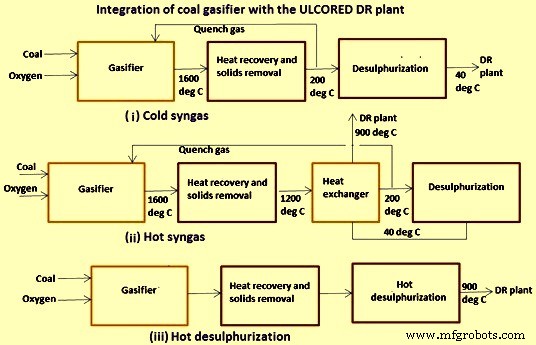
Fig 3 Intégration du gazéifieur de charbon avec l'usine ULCORED DR
L'oxygène est principalement consommé dans le gazéifieur de charbon, mais aussi avant le puits, dans un petit POX, assurant une température correcte du gaz de réduction. Le gaz décalé est un gaz qui doit être dérivé vers le décaleur pour assurer la bonne composition du gaz de réduction, c'est-à-dire augmenter la quantité de H2. Le CO2 éliminé est la quantité de CO2 qui est séparée du flux de traitement principal dans le processus d'élimination du CO2. Le schéma de traitement du procédé ULCORED à base de charbon est illustré à la Fig 4.
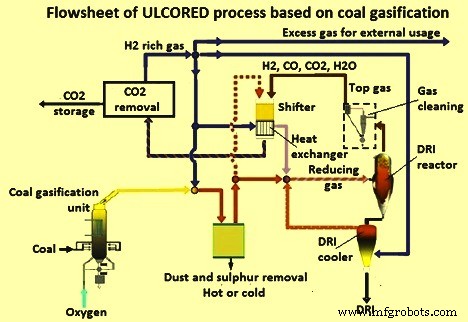
Fig 4 Schéma de principe du procédé ULCORED basé sur la gazéification du charbon
L'utilisation d'un gazéifieur de charbon et d'un décaleur dans le système permet de dériver une partie du gaz de synthèse directement vers le décaleur, générant plus de gaz que nécessaire pour l'usine de réduction directe. Cette caractéristique permet de générer un combustible pauvre en CO2 pour l'aciérie. Il permet d'avoir une source de CO2 hors du système, ce qui permet essentiellement de capturer et de stocker tout le CO2 généré dans le système de fabrication de l'acier.
Statut actuel du processus ULCORED DR
Des études approfondies du modèle fondamental pour le processus ULCORED DR ont été achevées. Ces études de modèles comprenaient des modèles à l'échelle des pastilles, des modèles de puits et des modèles de processus par des simulations de schémas de traitement. Les études de modèles ont contribué à la compréhension fondamentale du processus de RD, y compris sa dynamique. La modélisation du schéma de traitement a contribué à l'optimisation de la disposition du processus pour s'adapter au processus ULCORED DR dans l'environnement de l'aciérie. Différentes approches adoptées lors des études de modélisation ont produit des résultats similaires. Ces études ont créé une base crédible pour l'évaluation du concept dans différents scénarios. Des calculs d'équilibrage matière, d'équilibrage massique, d'équilibrage énergétique et d'émissions de CO2 ont été effectués pour 1 tonne de sortie DRI froid avec 92 % de métallisation et 2,76 % de C.
L'une des options intéressantes est une usine ULCORED DR est la production de LRI (fer moins réduit) et un haut fourneau (BF) conventionnel ou sans N2 pour produire la fonte (HM) avec une économie supplémentaire d'émissions de CO2. LRI est un choix alternatif au lieu de DRI compte tenu des tests réussis effectués dans le BF expérimental LKAB. Le test LRI avec un produit DR réduit à seulement 65 % de degré de métallisation a répondu très positivement dans le BF avec des conditions de four remarquablement stables et une faible consommation de coke inférieure à 200 kg/tML.
Le résultat de ces études est que le procédé ULCORED DR peut être une «solution rapide» pour une amélioration des émissions de CO2 sur le terrain, en particulier là où le GN est relativement bon marché. Dans le cas d'une aciérie intégrée avec voie BF, LRI peut être un choix compte tenu des tests réussis effectués dans le BF expérimental LKAB.
Le procédé ULCORED DR doit d'abord être testé en pilote, une étape qui pourrait profiter de l'opportunité du four EDRP (pilote expérimental de réduction directe), que LKAB prévoit d'ériger dans les années à venir en complément de son BF expérimental à Lulea, en Suède. Les spécifications de l'EDRP sont (i) 1 tonne de fer par heure de production, (ii) recirculation du gaz de gueulard, (iii) plage de pression de service de 0 kg/cm² à 8 kg/cm² dans le four à cuve, (iv ) débit de gaz compris entre 1 700 N cum et 3 100 N cum par heure, et (v) température du four à cuve comprise entre 900 deg C et 1 050 deg C.
ULCORED sera probablement un candidat pour moderniser les usines de réduction directe existantes, une fois sa viabilité démontrée à l'échelle du pilote puis du démonstrateur, ce qui prendrait également 10 à 15 ans ou plus.
Processus de fabrication