Alcoa poursuit l'excellence en matière de fiabilité
Si vous ne supportez pas la chaleur, vous feriez mieux de ne pas chercher d'emploi à l'usine d'Alcoa Primary Metals dans le sud de l'Indiana.
Les cuves cracheur de feu et les creusets remplis de métal en fusion peuvent pousser la température ambiante de l'atelier de production à près de trois chiffres. La chaleur rayonne visiblement des machines. Des filets de sueur coulent le long des joues et du dos des travailleurs. Des pauses fréquentes pour l'eau et le Gatorade sont une nécessité.
C'est un environnement physiquement exigeant, mais la chaleur réelle référencée dans le premier paragraphe concerne davantage la position de cette usine particulière dans l'industrie de la fonderie d'aluminium. Ce site, qui fait partie des énormes opérations d'Alcoa à Warrick, a été construit à la fin des années 1950 et a commencé à produire de l'aluminium brut pour l'industrie de la tôle de canette au début des années 1960.
C'est une vieille usine dans une industrie sensible à l'âge et à la technologie. Il y avait 33 fonderies américaines en activité en 1980. Aujourd'hui, il y en a 13. Seulement 6 pour cent de la capacité mondiale d'aluminium seront produits cette année dans des fonderies de plus de 50 ans. Le temps presse.
A cet état, ajoutez ceci :
-
25 % de la main-d'œuvre de l'usine est actuellement éligible à la retraite en raison de l'âge ou des années de service ;
-
les salaires payés par l'usine sont parmi les plus élevés de l'industrie; et,
-
il y a quelques années, les coûts d'entretien de cette fonderie par tonne métrique d'aluminium produite étaient les deuxièmes les plus élevés du système mondial d'Alcoa.
Pouvez-vous sentir la chaleur? Tous les employés de cette usine le font. Mais au lieu d'attendre une disparition qui semblait imminente, le personnel de maintenance et d'exploitation est intervenu et a pris des mesures.
«Nous devons nous y raccrocher si nous voulons maintenir ce niveau de vie et garder cette usine en vie», déclare Mark Keneipp, directeur du système d'entreprise de la fonderie Alcoa. « C'est la nouvelle réalité. Vous n'avez qu'à faire avec. »
Cela commence par un regard dans le miroir.
« Notre défi était et reste d'être compétitif en termes de coûts malgré notre vieillesse », explique Keneipp. « Nous ne sommes plus en tête de la courbe des âges. Nous devons avoir un horizon de 15 à 20 ans pour attirer des capitaux au sein d'Alcoa. Si c'est 25 à 30 ans, ce serait formidable. Pour ce faire, nous devons continuellement prouver que nous sommes une usine allégée, rentable, stable et efficace. »
Ce n'est pas un environnement pour les faibles. Mais grâce au travail acharné et à la persévérance, il y a de nombreuses récompenses.
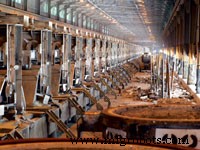
Délai d'appel
Les efforts visant à maintenir la présence d'Alcoa Primary Metals dans la communauté manufacturière du sud de l'Indiana ont commencé au niveau de l'entreprise.
En 1997, Alain Belda, PDG d'Alcoa, a commencé à appliquer les principes du système de production Toyota (TPS) aux 250 sites de son entreprise dans le monde.
Rodney Cunningham (à gauche), responsable de la production de l'usine d'aluminium, coordinateur de processus Larry York et senior Brian Audie, ingénieur des procédés, se tient à l'intérieur d'un réservoir d'alumine vacant sur le terrain des opérations Warrick d'Alcoa. Le site utilisait traditionnellement quatre de ces réservoirs comme récipients de stockage pour l'alumine, un ingrédient clé dans le processus de fusion de l'aluminium. Les initiatives de production au plus juste et la pensée critique ont conduit l'usine à réduire ses effectifs à deux réservoirs, ce qui a permis à l'entreprise d'économiser une grosse somme d'argent.
TPS est une philosophie de fabrication au plus juste fondée sur la production « juste à temps », l'élimination des déchets et la résolution rapide des problèmes. Cependant, la fonderie de l'Indiana a fait une découverte importante lors de la mise en œuvre du système.
"TPS, Flow et Lean ne fonctionnent pas si vous avez un équipement instable et imprévisible", explique Keneipp.
Une maintenance efficace, rationalisée et rentable de l'usine et la fiabilité des machines doivent primer.
Pour illustrer son propos, Keneipp propose un schéma appelé « l'iceberg de maintenance ». Au-dessus de l'eau se trouvent les coûts d'entretien directs liés aux matériaux, à la main-d'œuvre, aux heures supplémentaires, aux services contractuels, aux frais généraux et aux avantages. Sous la surface se cachent des coûts indirects liés aux temps d'arrêt, à l'installation et au démarrage, aux horaires manqués, aux stocks excédentaires, à la gestion de crise, aux achats d'urgence et à un effet d'entraînement global sur la production.
« Les composants indirects sont pris en otage par l'équipement et les processus instables d'une usine », dit-il.
Tous ces déchets encrassent le système et augmentent les coûts d'exploitation et de maintenance.
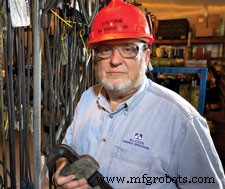
En 2002, cette fonderie avait des coûts d'entretien totaux de plus de 35 millions de dollars. Son ratio « douloureusement élevé » de plus de 137 $ en coûts d'entretien pour chaque tonne métrique d'aluminium produite (voir « Les faits » pour le tonnage annuel) l'a placé à l'avant-dernière place des fonderies d'Alcoa dans le monde. La moyenne mondiale en 2002 était de 90 $ la tonne métrique.
Cette usine d'Alcoa et ses dirigeants avaient deux options.
« Le directeur de l'usine, Royce Haws, a dit que nous allions réduire nos coûts. Ce n'était pas une option de rester où nous étions. Cela allait arriver », dit Keneipp. « Nous pourrions le faire de manière intelligente ou à courte vue. Quand vous êtes myope, ce sont des jours effrayants. Il est difficile d'attirer des capitaux dans l'usine pour s'occuper des choses qui doivent être faites lorsque vous différez simplement l'entretien. Personne ne se sent bien dans cette approche. C'est la motivation pour que les gens cherchent quelque chose de mieux. »
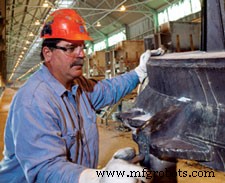
Attraper les vagues
Si vous ne l'avez pas encore deviné, l'usine d'Alcoa a choisi l'approche intelligente pour réduire les coûts de maintenance. Les responsables de la maintenance se sont associés à des consultants de Life Cycle Engineering (LCE) et du Ron Moore Group au début de 2003 pour créer une approche appelée Reliability Excellence Process, qui a été déployée en trois « vagues ». Le processus est basé sur la conviction qu'un partenariat formalisé et bien défini est impératif entre la maintenance et l'exploitation. Dans ce partenariat, les opérations sont propriétaires de l'équipement et ont un intérêt primordial dans la fiabilité. La maintenance est un partenaire égal dédié à fournir des méthodes, des compétences, une expertise et un soutien opportuns et efficaces.
« C'est un grand changement », déclare Joseph Motz, surintendant de l'ingénierie de la fiabilité. "Auparavant, c'était un environnement en silo avec beaucoup de doigté."
Le métal en fusion est coulé à partir d'un creuset
dans le département Lingot de l'usine d'Alcoa.
Quelques exemples :
Un opérateur a remarqué un problème potentiel. Aucun correctif n'a été planifié ou effectué. La machine est tombée en panne. À qui la faute ?
Ou bien, la maintenance s'est présentée pour un travail de maintenance préventive de deux heures. Pendant qu'il était dans la machine, il a détecté des problèmes supplémentaires et a terminé le travail de PM huit heures plus tard, ce qui a eu un impact sur la sortie. À qui la faute ?
La réponse dans ces cas était à la fois la maintenance et les opérations.
« Nous avons dû réaliser que nous étions tous dans la même équipe », dit Motz. « Nous sommes tous ici pour fabriquer de l'aluminium. Si nous allons dans des directions différentes et ne travaillons pas ensemble, le processus ne fonctionne pas."
La vague 1 de l'approche en trois vagues a commencé en juin 2003.
"La vague 1 était Ron Moore", explique Keneipp. « Nous l'avons fait venir pour parler avec les principaux dirigeants de l'usine. Il a défié les paradigmes séculaires. « Vous devez adopter davantage une philosophie de propriétaire d'actifs. » « Vous gaspillez de l'argent. » Il secoue les choses et ouvre les yeux. »
La vague 2 est arrivée en août avec une évaluation complète de l'excellence de la fiabilité par le LCE. Sur une période de deux semaines, l'entreprise a mené de longs entretiens avec 90 employés d'exploitation et de maintenance (horaires et salaires), ainsi qu'avec le contrôleur de l'usine.
Les informations ont conduit à :
-
une analyse financière détaillant la valeur estimée pour combler les écarts d'excellence en matière de fiabilité par rapport au coût de mise en œuvre (présenté comme un calcul de retour sur investissement );
- un plan directeur préliminaire décrivant les processus et les méthodologies nécessaires pour combler les lacunes.
« Nous voulions examiner notre condition actuelle et identifier une condition cible », explique Keneipp. "L'écart entre ces deux est votre douleur ou votre gain. Cela vaut-il la peine de combler le fossé? Nous devions prouver cette valeur à la haute direction. Nous devions prouver qu'il était avantageux d'investir de l'argent dans l'ancienne usine.
« Face à tous les faits, il était prudent d'obtenir l'approbation de l'argent dès que possible pour continuer. »
La vague 3 a commencé en septembre. Responsables des opérations et de la maintenance :
-
mis en œuvre le plan directeur
-
éduqué tous les employés sur leurs nouveaux rôles et responsabilités liés à l'augmentation de la fiabilité de l'équipement
-
organisé des ateliers sur les techniques appropriées d'amélioration de la fiabilité
-
établi des processus définis et des mesures efficaces des progrès
"Ce n'est pas facile. Rien de tout cela ne l'est », déclare Rodney Cunningham, directeur de la production de la salle de cuve. « Mais si vous avez un engagement de gestion et un partenariat entre la maintenance et l'exploitation, vos chances de succès augmentent. Sans ces choses, vous n'y arriverez pas."
Mettre la barre plus haut
L'établissement de définitions dans divers domaines a contribué à déclencher des améliorations. L'objectif principal était de définir « qu'est-ce qui est possible ? » et "qu'est-ce que le progrès ?"
Une réponse est venue en acceptant l'efficacité globale de l'équipement (OEE) comme une mesure clé à l'échelle de l'usine. L'OEE suit les sources de perte d'exploitation, y compris la disponibilité, les performances et la qualité des équipements, et est exprimé en pourcentage des performances optimales.
"C'est essentiellement défini par certaines des meilleures performances passées", Tom Svoboda, responsable de la production d'électrodes. « Vous l'avez vu arriver. Ce n'était ni fictif ni hypothétique. Que l'équipement fonctionnait extraordinairement ce mois-là ou que vous soyez vraiment au top du processus, cela s'est produit. La question est, si vous l'avez fait pendant cette période de temps, pourquoi ne pouvez-vous pas le faire tout le temps ?"
En utilisant une analogie sportive pour illustrer l'importance d'un TRS à 100 %, si un sauteur en hauteur saute normalement de 6 pieds 6 pouces mais établit un record personnel de 7 pieds, ce qui a spécifiquement conduit à cette performance maximale de 100 %. S'est-il entraîné différemment ? A-t-il changé son alimentation avant la compétition ? A-t-il porté des chaussures différentes ? Il a littéralement relevé la barre. Que peut-on apprendre et que peut-on faire pour atteindre cette marque maintes et maintes fois ?
La maintenance et les opérations ont travaillé ensemble pour définir les performances de pointe pour les fonctions de l'usine (par exemple, l'assemblage des anodes), les processus (déchargement du minerai), les résultats (ferraille) et les pièces d'équipement individuelles (four annulaire). En compilant ces informations, il a été déterminé que 8,3 millions de dollars d'économies annuelles étaient possibles grâce à la réalisation des objectifs de l'OEE.
Avec les informations de base, les états actuels ont été définis et les conditions cibles établies. Des activités – des projets de travail utilisant des outils de production au plus juste tels que le kaizen et l'amélioration continue – ont eu lieu. Les progrès ont été mesurés et analysés. Et des avantages tangibles ont été calculés.
En 2004, 2,4 millions de dollars d'améliorations étaient liés à des gains en TRS.
Le fait de chercher plus en profondeur et de prendre des mesures a également permis de réduire les dépenses d'entretien de la fonderie. Au cours de la première année suivant le début de l'initiative de fiabilité, les dépenses ont chuté de 1,9 million de dollars, passant d'un chiffre de référence de 32 millions de dollars à 30,1 millions de dollars. En 2004, le chiffre a encore baissé de 700 000 $. Le ratio des dépenses d'entretien par tonne métrique produite a également chuté à 109 $ en 2004.
Le plan sur « Planifié »
Un effort important a également été fait pour mieux définir les éléments de maintenance. Plus précisément, dans ce système de fiabilité dirigé par l'opérateur, « comment le travail est-il planifié ? » et "comment le travail se fait-il ?"
« Avec le recul, nous nous trompions en pensant que nous étions en bonne santé », explique le responsable de la maintenance Danny Reyes. « Beaucoup de nos anciennes mesures étaient déconnectées. Nous pensions que notre « pourcentage de travaux planifiés et planifiés » était de 85 % et notre « pourcentage d'achèvement de la MP » était de 90 %. »
LCE a informé l'usine qu'elle utilisait les mauvaises définitions.
« Le « pourcentage de travail planifié et planifié » n'était en réalité que « pourcentage planifié. » La planification était très limitée », explique Reyes. « C'était le respect des horaires. Probablement 10 % de ces travaux étaient planifiés. »
Un ratio de 35 pour 1 entre le personnel d'artisanat (140) et les planificateurs (quatre) était le nœud du problème.
« Cela n'a pas très bien fonctionné », déclare Larry McCubbins, planificateur de la maintenance. « Il y avait très peu de temps pour planifier. Vous êtes devenu un planificateur, et pas très bon pour ça. »
Un environnement réactif se développe dans ce cadre. « Nous appliquions l'approche de l'entretien de la maison », explique Keneipp. « C'est ainsi que vous et moi abordons les projets un samedi matin. C'est vraiment imprévu et inefficace."
L'usine a depuis ajouté trois planificateurs pour un total de sept, offrant un ratio plus gérable de 20 à 1.
"Cela permet à ces gars de mettre en place, d'organiser le travail, de le planifier, de le planifier avec les centres de production, de s'assurer que toutes les pièces sont là, de s'assurer que l'équipement est en panne et que le temps est alloué", explique le surintendant de la maintenance de la fonderie. Scott Deon.
Autres clés pour une meilleure planification :
-
Un document formel décrit maintenant les composants d'un travail planifié (voir l'encadré à la page 14). « Les quatre pauvres planificateurs que nous avions en train d'essayer de tout faire n'ont pas fait les choses de la même manière », explique Deon. « Ce nouveau format standardise désormais la façon d'effectuer le travail. »
-
Une zone formelle et sécurisée est maintenant utilisée par les planificateurs pour le kit de travail. Dans le passé, les pièces et les matériaux nécessaires étaient expédiés au coup par coup sur un chantier. La pile peut rester des semaines jusqu'à ce que tous les articles arrivent. Pendant le temps d'attente, il n'était pas rare que des pièces ou des outils soient déplacés, perdus ou utilisés pour un autre travail.
« Lorsque le planificateur planifie le travail, il commande tous les matériaux et les fait livrer ici », dit McCubbins. « Quand tout est là pour le travail, nous le rassemblons sur une palette ou deux. Les artisans viennent ensuite l'emporter sur le chantier et effectuent le travail. » -
Communication efficace.
« Avant, je pensais que je savais ce que les gens voulaient. Ce processus m'a appris que je ne l'ai pas fait », explique McCubbins. « Je ne savais pas ce qu'ils voulaient et ce qui leur convenait. Dans le passé, je planifiais le travail et ne posais pas de questions. »
Deon ajoute :« Avec la responsabilité partagée avec la production, nous savons maintenant quel travail vient en premier. La personne qui possède l'équipement doit savoir quelle est la chose la plus critique. Avant, je ne pense pas que nous devinions. Mais étions-nous à 100 % ? Probablement pas." -
Réunions hebdomadaires ciblées et efficaces.
« Les propriétaires d'actifs président les réunions et les planificateurs/planificateurs de l'entretien de la zone sont des facilitateurs », explique Keneipp. « S’il s’agit d’une réunion de planification, nous discutons de la manière dont nous allons procéder. S'il s'agit d'une réunion de planification, nous établissons le calendrier. »
En ce qui concerne également la manière dont le travail est effectué, l'usine a pris des mesures pour documenter l'historique de l'équipement et normaliser les instructions des tâches de maintenance.
«Au début, vous pouviez obtenir des enregistrements, mais la documentation s'est ensuite arrêtée», explique Dan Decastra, ingénieur en énergie de la station de redressement. « Donc, nous avons créé un emplacement sur le serveur et avons commencé à documenter. Pour cette station, nous avons créé une liste de « bad boy ». Nous avons sélectionné les grands problèmes et avons commencé par là. Maintenant, vous pouvez remonter à 2001 et voir un historique sur les commutateurs pneumatiques, les contacts, les transformateurs et les patins. »
L'ingénieur en fiabilité Jonathan Fulton ajoute :« Peut-être qu'un tiers de notre personnel de maintenance pourrait prendre sa retraite demain s'il le souhaitait. C'est une énorme responsabilité potentielle pour nous. Et, il est difficile d'obtenir un artisan de qualité de l'extérieur. Pour y remédier, nous normalisons les processus de travail et développons l'historique des équipements. En faisant cela, nous pouvons rapidement mettre à niveau les personnes ayant une expertise technique. »
Notes de berceau
Un dernier exemple d'amélioration est la façon dont l'usine a mieux défini qui achète les produits d'entretien et comment l'argent est dépensé pour les outils et les matériaux de type consommable.
Dans le passé, divers membres du personnel d'entretien de la fonderie achetaient les outils à main, les outils électriques, les produits de sécurité, les nettoyants, les produits de manutention et une centaine d'autres articles nécessaires. Les produits achetés étaient stockés dans des huches à outils décentralisées autour de l'installation et dans une multitude de lieux de détention non officiels (casiers, coffres et casiers).
« Au fur et à mesure que l'usine s'agrandissait, des zones ont été ajoutées. Ils avaient un petit groupe et quelqu'un s'occupait de la commande et ils mettaient en commun leurs fournitures ici et là », explique le mécanicien général Dick Day. « Nous dépensions beaucoup d'argent pour essayer d'alimenter ces berceaux satellites. Ils n'étaient pas gérés. Les gens achetaient des trucs, mais ce n'était pas vraiment accessible."
Si un mécanicien avait besoin d'un outil particulier, il le cherchait. C'était quelque part dans le coin. S'il ne le trouvait pas, il en commandait un. Cet outil acheté pourrait disparaître avant qu'il ne l'atteigne. Cela a conduit à des dépenses inutiles et redondantes.
Pour résoudre ce problème, un berceau centralisé a été construit et tous les éléments du berceau satellite et du casier ont été amenés dans cette zone sécurisée et fermée.
L'inutile est entré.
"Nous avons réalisé que nous avions beaucoup de choses obsolètes - quelque chose pour un équipement que nous avons peut-être retiré il y a 10 ans", explique Keneipp.
Et, est venu le précieux.
« C'était incroyable tout ce qui sortait du bois. Quelqu'un a apporté une armoire contenant plus de 38 000 $ de pompes et de vérins », explique Day, qui est devenu le préposé principal du berceau central. « Nous avons commencé à utiliser ce que nous avions. Pour certains matériaux, nous n'avons rien eu à commander pendant un an. »
Aujourd'hui, Day est responsable de l'achat de ces produits liés à la maintenance. Il réceptionne les achats, stocke les articles et les distribue au besoin.
« Nous savons ce que nous avons et où il se trouve », dit-il.
Day a également créé un système minimum/maximum pour une variété de produits et s'est lancé dans des efforts pour normaliser les marques d'outils électriques et de fournitures de soudage.
"Avec les outils électriques, nous avons principalement standardisé sur DeWalt, et nous nous intéressons beaucoup à leurs outils sans fil", dit-il. « Pour les fournitures de soudage, nous avons standardisé nos pistolets dévidoirs et les pièces de rechange pour ces pistolets. »
Il fait ses devoirs et trouve des moyens innovants de réduire les coûts.
Voici quelques exemples :
Gants :« Nous avions l'habitude d'acheter une marque de gants avec une petite languette dessus pour 12 $ la paire. C'est ce que tout le monde « devait avoir », dit-il. « Vous pouvez acheter les mêmes gants avec un peu d'élastique pour 2,67 $ la paire. Les gens les ont aimés."
Huile hydraulique :« Nous l'avons acheté au gallon à 8 $ la pop. En l'achetant en gros, nous économisons maintenant 3 $ par gallon. Je verse l'huile dans des cruches réutilisables qui coûtent 57 cents pièce. »
Tuyau d'acétylène :« Avant, on l'achetait préemballé en bobine. Maintenant, nous l'achetons sur un rouleau de 500 pieds et coupons ce dont la personne a besoin. Nous économisons 25 %. »
Day dit que c'est du bon sens.
«Je le considère comme mon argent», dit-il. "Si c'est mon entreprise, c'est comme ça que je la dirigerais."
Les faire suer
Grâce au travail acharné, au partenariat, à la propriété et à une réflexion innovante, cette fonderie d'Alcoa est devenue plus stable, plus légère, plus prévisible, plus fiable et plus compétitive.
Les coûts-avantages de l'OEE s'élèvent à 4,4 millions de dollars annualisés pour le cumul annuel de 2005 par rapport au chiffre de référence de 2003.
Les dépenses de maintenance depuis le début de l'année 2005 s'élèvent à 27,1 millions de dollars annualisés et reflètent une diminution de 4,9 millions de dollars par rapport au nombre de référence de 2003.
Les coûts de maintenance pour le deuxième trimestre de 2005 étaient de 96 $ par tonne métrique produite et les objectifs sont fixés pour atteindre 87 $ dans un proche avenir.
Une évaluation de suivi LCE a placé l'usine dans la catégorie « conditions proactives » et des travaux sont en cours pour l'élever dans la catégorie « excellence ».
Il y a de l'optimisme et de l'élan.
"Quand j'ai été embauché il y a 15 ans, nous avons dit:" Nous sommes une vieille technologie. Nous ne pouvons pas rivaliser avec certaines des installations les plus modernes », déclare Fulton. « Pour moi, la récompense est de nous voir rivaliser et avoir une plus grande efficacité. Nous produisons mieux avec notre technologie vieille de 40 ou 50 ans que sur des sites construits il y a 10 ou 20 ans. »
Bien que la chaleur ne disparaisse jamais complètement pour cette plante, elle fait ce qu'elle peut pour faire transpirer la concurrence.
Quelles sont les caractéristiques d'un travail planifié ?
-
Il existe une estimation précise du temps pour le travail, de sorte que le superviseur aurait une attente raisonnable quant au moment où il pourrait attribuer la tâche.
-
Il existe une estimation précise des ressources nécessaires en termes de personnel d'artisanat, de pièces de réparation/remplacement, d'outils, d'équipement de soutien, etc.
-
Toutes les informations nécessaires (plans, permis, sécurité, etc.) sont obtenues.
-
La séquence des étapes de travail, les procédures et les instructions pour accomplir le travail sont établies.
-
Toutes les pièces et tous les matériaux nécessaires sont fournis.
-
En tant que contrôle intégré pour assurer un travail planifié de qualité, discutez périodiquement de la nature du travail avec un superviseur et/ou l'artisan désigné pour terminer le travail. S'assurer qu'il y a une compréhension complète de la portée du travail et que le package de travail en kit est complet.
Entretien et réparation d'équipement
- Qu'est-ce que la culture de la fiabilité ?
- Quel est le rôle de l'ingénieur fiabilité ?
- Une révolution de la fiabilité du tourbillon
- Meilleurs performances en maintenance et fiabilité
- Comment l'excellence en matière de fiabilité accélère-t-elle les avantages du Lean ?
- Fiabilité orientée famille
- Gestion de la chaîne d'approvisionnement :aller au-delà de l'excellence en matière de fiabilité
- Pourquoi l'excellence en matière de fiabilité est impérative pour la sécurité
- La fiabilité est une initiative verte