Une meilleure planification de la maintenance est la solution miracle de MillerCoors
Tim Davison, planificateur de MillerCoors Asset CARE
La planification n'est pas sexy. Tom Clancy n'écrira pas un thriller d'espionnage intitulé "The Maintenance Planner".
Vous ne mettrez pas vos copains sur le bord de leurs tabourets de bar en leur racontant le temps où vous avez pris toutes les mesures appropriées et vous êtes assuré que le projet de refonte se déroulerait sans heurts. (« Mec, alors qu'est-ce qui s'est passé ? ! »)
Il n'y a pas de paillettes, de flash ou de friandises pour les yeux.
« Lorsqu'un service de maintenance cherche à s'améliorer, l'accent est généralement mis sur la présentation des victoires et la prise de photos avant et après - des trucs « wow » », déclare Dan Roberts, directeur de la fiabilité d'Asset CARE pour Miller Coors à Golden, Colorado.
« La maintenance prédictive est sexy. Avec la thermographie infrarouge, vous prenez un instantané et dites :« Regardez ce que j'ai trouvé ». mais il y a du bon travail en cours au cœur. Ce n'est juste pas sexy. Comment montrez-vous les résultats d'une planification et d'un ordonnancement efficaces ? Vous ne pouvez pas le faire avec des photos avant-après. »
Tranquillement et secrètement, l'organisation de maintenance et de fiabilité de MillerCoors utilise la planification et la planification comme outil d'amélioration. Il assure l'équilibre dans un environnement où le déséquilibre a des conséquences majeures.
Entretenir la chaîne
MillerCoors, le troisième brasseur américain, a ciblé des améliorations d'entretien depuis plus d'une décennie, et pour cause. La brasserie Golden fonctionne 24 heures sur 24, sept jours sur sept, pour brasser 217 millions d'onces de bière chaque jour.
"Il y a peut-être deux jours dans l'année où nous ne produisons pas", explique Tim Davison, un planificateur Asset CARE dans la partie brasserie du grand complexe de plusieurs usines de Golden.
Le processus de fabrication de la bière - des matières premières aux marchandises emballées et expédiées - s'exécute dans une chaîne étroitement liée, et de nombreux composants du processus comportent des pièces de machines non redondantes. En cas de panne mécanique, le transfert du travail vers un équipement similaire peut ne pas être une option. Dans ces cas, le processus s'arrête.
« Lorsqu'il y a une panne, c'est généralement un gros problème », explique Ron Kerr, responsable Asset CARE pour les services publics. « Cela affecte presque tout le monde en amont et en aval. »
L'opérateur de presse Craig Doebele travaille les commandes le long de la ligne de production
à Rocky Mountain Metal Container, la coentreprise MillerCoors/Ball.
L'objectif est de faire fonctionner les machines sans interruption pendant des mois d'affilée, en particulier pendant la haute saison estivale, jusqu'à ce qu'une brève fenêtre de maintenance puisse être programmée.
La structure unique des unités commerciales de Golden ajoute du stress à la chaîne. Bien que MillerCoors soit propriétaire de la brasserie, elle est un partenaire conjoint dans les unités de fabrication de canettes (avec Ball Corporation) et de fabrication de bouteilles (Owens-Illinois). Faire en sorte que tout le monde tire dans la même direction est nécessaire, mais cela demande de la patience.
L'ingrédient manquant
Le rythme de l'amélioration de la maintenance, lent et régulier pendant des années, s'est accéléré à la fin des années 90 après que le joueur de premier plan Anheuser Busch a annoncé des baisses de prix. Pour rester compétitif, MillerCoors a cherché à réinvestir dans le front-end de l'entreprise.
« Le coût de nos marchandises a dû baisser considérablement », explique Roberts. « Nous devions nous attaquer à un certain nombre d'éléments, les opérations étant l'un d'entre eux. L'opportunité et l'objectif étaient de devenir l'opération la plus fiable possible. »
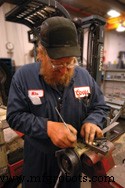
Asset CARE (acronyme de Capability, Availability, Reliability and Enhancement) est devenu le cri de ralliement. Des outils de maintenance centrée sur la fiabilité (RCM), d'analyse des causes de défaillance (RCFA) et de maintenance prédictive (PdM) ont été utilisés. Même avec ces avancées positives, il manquait quelque chose.
Roberts cite l'exemple d'un ventilateur qui a connu trois pannes dynamiques au cours d'une période de 18 mois. Après le premier échec, RCFA a identifié la lubrification comme cause principale. Un système de lubrification automatique a été installé. Après le deuxième échec, les graisseurs automobiles ont été jugés problématiques. Après le troisième échec, les responsables de la maintenance ont pris du recul.
« Nous participons maintenant à des exercices de cartographie des causes qui nous amènent à explorer plusieurs causes profondes », explique Roberts. "RCFA ne dit pas qu'il y a une cause fondamentale, mais cela conduit les gens dans cette direction."
En allant plus loin, la planification et l'ordonnancement ont émergé comme un contributeur au problème.
Un mois avant la troisième défaillance, l'analyse vibratoire avait identifié des anomalies. Cependant, aucune mesure appropriée n'a été prise pour planifier la maintenance et en faire une priorité avant que la panne ne se produise. La leçon :des gains substantiels sont peu probables si la planification et la programmation de base ne sont pas en place.
« Avant nos efforts concentrés, nous n'étions pas en train de planifier et d'ordonnancer en soi », explique Roberts. « Les planificateurs ont examiné les bons de travail dans le système informatique, les ont imprimés, les ont remis à un superviseur et ont attendu que le superviseur les remette à l'équipe. Peu d'efforts ont été déployés pour s'asseoir chaque semaine avec les opérations et examiner ce qui se préparait, déterminer les priorités et identifier les ressources. »
Les usines fonctionnaient en mode de maintenance réactive. Les planificateurs ont consacré un temps considérable à la recherche, au stockage et à la distribution des pièces de rechange.
« Si notre organisation est avant-gardiste, nous trouvons les éléments à corriger, rédigeons le bon de travail, planifions le bon de travail et exécutons le travail. Si c'est réactionnaire, nous achetons des sièges de première classe dans des avions pour expédier un moteur », explique Bobby McCall, responsable de la maintenance pour les opérations d'emballage.
Le travail réactif a eu ses récompenses – des tapes dans le dos et des remerciements de la production. Un trophée itinérant était remis chaque année au planificateur responsable du plus grand nombre de livraisons de nuit.
Ensuite, MillerCoors a trouvé une meilleure façon d'identifier les composants essentiels d'une planification de maintenance efficace. Ceux-ci maximisent les ressources, minimisent les coûts et augmentent la fiabilité globale de l'équipement. Les sections qui suivent décrivent plusieurs de ces composants.
Dan Roberts est le directeur Asset CARE de
la fiabilité pour MillerCoors Brewing Entreprise à
Golden, Colorado. Bien que les usines de l'entreprise
aient fait des progrès importants,
il admet que « nous n'y sommes pas encore ».
Vraiment dévoué
Comme dans tout effort, le dévouement est la clé du succès. Chez MillerCoors, la maintenance avant-gardiste commence par des planificateurs et des ressources dédiés.
Une organisation de planification a besoin du nombre approprié de planificateurs. Chaque planificateur doit avoir un domaine de responsabilité qui est :
• raisonnable en taille géographique ;
• raisonnable en nombre d'artisans représentés; ou,
• raisonnable en nombre d'équipements.
Sans de telles limites, comment le planificateur peut-il consacrer le temps et les ressources nécessaires pour entretenir efficacement cette zone ?
Davison dit qu'avec une zone trop grande, un planificateur ne peut pas se concentrer sur l'ensemble de la portée, mais uniquement sur les mauvais acteurs et les situations d'urgence qui surviennent. Lorsqu'un planificateur se concentre sur les mauvais acteurs et les échecs, il ne permet pas la planification prédictive et proactive nécessaire.
« Deux personnes ne peuvent pas planifier 4 000 pièces d'équipement », explique Davison. "Tout ce qu'ils auront le temps, c'est de commander des pièces."
Le mécanicien de chariot élévateur Jerry Mitchell enlève une roue dans
afin d'exposer un roulement pour les travaux de maintenance préventive.
En ce qui concerne la couverture du planificateur à l'artisanat, Roberts dit que son objectif actuel est d'un planificateur pour 15 à 18 artisans. La règle générale est qu'au fur et à mesure que vous progressez vers la classe mondiale, vous pouvez avoir plus d'artisans par planificateur. Si vous êtes sur les échelons inférieurs de l'échelle, un plus grand pourcentage de planificateurs est approprié.
L'objectif du brasseur est de limiter spécifiquement ses planificateurs aux tâches qui relèvent de la fiabilité et du maintien du domaine de responsabilité défini. Sinon, il est facile pour les planificateurs de se laisser distraire par un travail qui ne relève pas de leur rôle et de leur fonction.
"La production peut considérer le planificateur comme un 'go-fer' ou un Wal-Mart, là pour répondre à tous leurs besoins et désirs", explique Brad Simpkins, un responsable Asset CARE en charge de l'équipement mobile.
La gestion de l'usine et du service peut également gêner les planificateurs dans leurs tâches administratives, de reporting et de saisie de données.
"Sans la possibilité d'avoir une réelle concentration, la planification devient réactive", ajoute Simpkins.
Tout aussi important, ces planificateurs nécessitent également des ressources dédiées (temps et main-d'œuvre) pour accomplir les travaux planifiés et programmés. Cela peut être une pilule amère pour certains travailleurs de la maintenance et de la production.
« Certains mécaniciens horaires ont dit : « Nous aimons ce que nous faisons maintenant. » Ils aiment venir sur le cheval blanc et sauver la situation », explique Jay Johnson, responsable de la maintenance pour les opérations de traitement. «Mais ils ont vu que la direction était derrière ces 100 pour cent. Cela n'allait pas disparaître."
Les directeurs de production et les opérateurs hésitaient également à mettre le cheval blanc au pâturage.
Dans l'organisation d'emballage de MillerCoors, l'équipe de maintenance était répartie à parts égales entre trois équipes. « Leur objectif était de réparer les machines et de les faire fonctionner », explique Kerr.
Puis, les premiers changements d'horaire sont arrivés. Un pourcentage important d'artisans travaillant la nuit et le week-end ont été transférés pour effectuer le travail prévu sur le quart de jour.
« La production nous a dit : « Vous ne supportez pas nos pannes ! » », déclare Kerr. "Vous avez raison. Je ne vais pas supporter vos pannes. Je vais soutenir le travail proactif. Les amener à accepter cela a demandé un acte de foi. »
Parmi les départements fonctionnels au sein de MillerCoors, l'emballage est actuellement le pionnier en poussant les ressources dédiées à un travail proactif et planifié.
« Nous allons planifier 100 % des heures disponibles pour les travaux de maintenance planifiés », déclare McCall. « Nous entendons toujours : « Vous ne pouvez pas faire ça ; il faut prévoir les pannes.’ Non, nous n’allons pas prévoir les pannes. Nous prévoyons de faire les travaux planifiés. Nous traiterons les pannes si elles se produisent. »
À tous les niveaux, l'organisation doit se rendre compte que les opérateurs et le personnel artisanal existent dans une installation de fabrication parce qu'il existe un processus à exploiter et à entretenir. Les planificateurs existent pour maximiser l'efficacité des opérateurs et des mainteneurs. Lorsque tous les niveaux de l'opération commencent à travailler ensemble en équipe, pour un objectif commun d'amélioration de la fiabilité et des performances opérationnelles, l'accent n'est plus mis sur les « victoires du cheval blanc », mais sur les gains durables à long terme.
Gestion du temps
Une autre clé du succès de la planification de MillerCoors est de tirer le meilleur parti du temps.
Comme indiqué dans la section précédente, la production était un peu sceptique. Si la maintenance devait soulager les douleurs de la production, ces « avant-gardistes » allaient devoir faire leurs preuves. N'oubliez pas qu'une machine hors ligne peut avoir d'énormes implications.
Un défi consistait à faire en sorte que la production comprenne qu'arrêter une machine pendant 40 minutes pour une maintenance préventive pendant une heure et un jour prédéterminés était mieux qu'une panne de trois heures suite à une panne à une heure et un jour inconnus. Le défi supplémentaire consistait à faire croire à la production que son temps précieux ne serait pas perdu.
« Nous avons eu de mauvais antécédents en matière de planification et d'ordonnancement. Nous devions prouver que si vous nous en donnez le temps, nous réaliserons le travail planifié et proactif », déclare Davison. «Ils ont fait tomber la ligne. Ils perdent de l'argent. Vous devez tirer le meilleur parti de cette fenêtre. »
La maximisation du temps passe par une planification et une programmation efficaces.
Premièrement, une fenêtre de maintenance doit être clairement définie (heure prévue, date, étendue et durée) et acceptée par les planificateurs de maintenance et les responsables de la production. À partir de là, le planificateur commande toutes les pièces et tous les matériaux nécessaires et s'assure que la quantité appropriée de ressources est disponible pour gérer le travail. Le planificateur veille à ce qu'aucune surprise ou, pire, annulation ne se produise lorsque la fenêtre s'ouvre. Le travail de maintenance échoué ou non productif a un impact direct sur les coûts de l'entreprise.
L'implication ne s'arrête pas là. Pendant la fenêtre, le planificateur observe, assiste et évalue le travail afin d'acquérir une connaissance complète du travail. Ces connaissances sont appliquées pour mieux planifier et programmer des tâches similaires à l'avenir. Il ou elle gagne également une mesure de respect et d'appréciation de la part des artisans qui travaillent sur le tas. Ceci est essentiel lorsque des conseils techniques et des questions surviennent ultérieurement.
Bien qu'il s'agisse de la méthode conventionnelle de planification au fur et à mesure de l'exécution chez MillerCoors, des méthodes spécialisées de planification et d'ordonnancement existent également.
L'usine de fabrication de canettes, qui doit fonctionner en permanence pour satisfaire les besoins de la brasserie (12 millions de canettes par jour), utilise un plan d'arrêt de 12 mois qui est mutuellement développé par les responsables des opérations, de la maintenance, de l'ingénierie, du contrôle des processus, de la qualité, de l'entrepôt et de la planification.
Le plan 2005 répertorie les dates, les emplacements, les activités de maintenance et les détails du projet pour 1 655 heures d'arrêt programmé. Le plan 2006 a été élaboré en septembre.
« Nous mettons 20 personnes dans une pièce et le calculons en équipe », explique David Miller, directeur des services techniques de Rocky Mountain Metal Container (la coentreprise MillerCoors/Ball). « Nous avons tout planifié et exploré, que pouvons-nous faire d'autre pendant cette panne ? Comment pouvons-nous maximiser ce temps? On ne peut pas avoir de surprises dans l'année. Nous devons avoir une longueur d'avance. Par conséquent, le plan de temps d'arrêt est notre document directeur pour assurer la fiabilité de l'équipement et la livraison des canettes en aluminium pour répondre aux exigences de la brasserie. »
L'usine de fabrication de bouteilles, qui produit 3 millions de bouteilles par jour, utilise une réflexion prospective pour les arrêts programmés d'une seule machine et de l'ensemble de l'usine.
« Auparavant, nous fonctionnions toute l'année, puis nous fermions à Noël pour des travaux de maintenance préventive (MP) », explique Tim Hood, directeur des services d'ingénierie chez Rocky Mountain Bottle Company (la coentreprise MillerCoors/Owens-Illinois). "Pour le reste de l'année, vous traiteriez les échecs au fur et à mesure qu'ils se produisaient parce que nous n'avions prévu aucun autre temps d'arrêt."
Aujourd'hui, les planificateurs et les responsables de la maintenance et de la production de cette usine planifient des sessions de temps d'arrêt appelées « maxi arrêts au stand ». Semblable au plan de temps d'arrêt de l'usine de conserves, ces arrêts pour les MP et les révisions sont définis bien à l'avance.
« Nous programmons différentes machines à différents moments », explique Hood. « De cette façon, vous n’avez pas tout votre équipement en panne en même temps. Nous déplaçons les ressources pour compenser les temps d'arrêt. »
Un arrêt annuel de l'usine, dirigé par un seul planificateur, a lieu en septembre.
« Il est impliqué dans l'ensemble du plan, essayant de déterminer quels travaux doivent être effectués pendant la panne », explique Hood. « Nous nettoyons à la vapeur les machines et préparons tous les équipements de distribution électrique pendant cette période. C'est une entreprise énorme. Lorsque nous terminons un arrêt, le planificateur prépare déjà le plan pour le suivant. »
Le processus de brassage commence par le maltage de l'orge.
L'orge est trempés dans l'eau et encouragés à germer.
Après quatre à cinq jours, le « malt » est chauffé pour arrêter la nouvelle
croissance. Le malt est ensuite craqué par des rouleaux en acier pour
exposer son contenu.
Informations utiles
Le succès de la planification de MillerCoors est également lié à l'exploitation optimale des informations. Cela commence par quelque chose d'aussi basique que de fournir des informations précises sur les ressources disponibles pour un quart de travail donné.
"Qui est là? Combien de temps sont-ils ici ? De combien de ressources les planificateurs doivent-ils tenir compte ? Avant, comme dans toute organisation réactive, c'était nébuleux », explique McCall. « Dans SAP, nous le déterminons. Les planificateurs voient que « j'ai une fenêtre de huit heures et 10 gars. Je peux planifier 80 heures de travail. Voici 80 heures de travail à consacrer à ce plan.' »
Une autre ancienne zone grise était les ordres de travail. Comme dans la plupart des usines, un ordre de travail est créé lorsque le travail est identifié. Mais quelles informations sont incluses sur ce bon de travail ?
Tirant les leçons du passé, les responsables de la maintenance de MillerCoors affirment désormais qu'un ordre de travail doit être capable de saisir le code de charge d'équipement approprié, tout l'historique de l'équipement, le coût de la main-d'œuvre et des matériaux et les exigences de service contractuel. Pour suivre avec précision les défaillances de l'équipement, une description de travail détaillée est saisie lors de la création de la commande et une description précise de ce qui a été fait pour corriger la défaillance est saisie à la fin de la commande de travail. Si cela n'est pas fait, l'historique d'un équipement particulier est déformé et peut ne pas tenir compte avec précision des pannes ou des pannes. De plus, le bon numéro d'équipement est inscrit sur le bon de travail. Sans cela, les mesures vitales de suivi de l'historique telles que le matériel utilisé et les heures de travail facturées sont liées à la mauvaise pièce d'équipement ou sont totalement manquantes.
"Dans le passé, de mauvaises décisions étaient prises parce que nous n'avions pas d'informations précises sur les bons de travail", explique Davison.
Lorsqu'un ordre de travail est créé chez MillerCoors, des notes sont prises pour aider à identifier :
• toutes les pièces, compétences ou ressources externes nécessaires pour terminer le travail ;
• tous les outils, équipements ou ressources spécialisés potentiellement nécessaires ; et,
• tout problème potentiel de sécurité ou d'environnement.
Avec ces informations initiales, le planificateur recherche les pièces et les matériaux nécessaires, rassemble les ressources requises et planifie et programme avec précision le travail. Cela augmente le temps de clé.
Lorsque le travail est terminé, un artisan saisit des informations détaillées pour fermer correctement le bon de travail. Dans le système d'ordre de travail SAP de l'entreprise, il ou elle saisit avec précision un code de cause, un code d'échec et une partie objet dans la partie historique finale de la notification. Une description détaillée et longue du travail effectué est documentée avec tous les problèmes ou écarts.
Mais toutes ces étapes ne valent rien si vous n'utilisez pas les informations.
Les travaux d'entretien sont répétitifs. Ce que l'on apprend sur une machine aujourd'hui s'avère utile lorsque la même machine ou une machine similaire nécessite une maintenance à l'avenir. Les historiques identifient les tendances et aident à élaborer des stratégies de fiabilité efficaces.
« Si les données ne sont pas exactes pour cet équipement, vous n'obtenez pas une image complète et vous ferez des erreurs dans l'entretien de cet équipement », explique Davison. « Si ce n'est pas enregistré dans le système, vous n'avez aucune donnée à analyser. Les planificateurs en ont besoin pour décider comment le planifier la prochaine fois, le faire mieux et l'utiliser à des fins de cause première. »
Avec des informations de bon de travail correctement saisies, le personnel de MillerCoors peut accéder au bon de travail et à l'historique des coûts pour une pièce d'équipement individuelle, un service, un centre de coûts ou une installation entière. Avec ces données, les planificateurs déterminent les pourcentages d'achèvement de la MP, le délai d'exécution des bons de travail, le temps moyen de réparation et le temps moyen entre les pannes. Ils accèdent également à la combinaison en pourcentage d'ordres de travail PM, correctifs, de panne et de projet pour une période donnée. Ces rapports leur donnent les outils pour ajuster les fréquences PM en fonction des commandes générées et du MTBF.
« Sur certains équipements, nous avons constaté que nos fréquences PM étaient trop élevées », explique McCall. « Nos planificateurs examinent régulièrement les PM. Ils s'assurent que le bon MP, avec la bonne fréquence, est en place. L'idée est que le travail que nous planifions est le travail qui devrait être fait. Nous voulons utiliser au mieux notre temps et notre argent et rechercher les bonnes choses. »
Les gestionnaires d'Asset CARE Bobby McCall (à gauche) et Ron Kerr
discutent moteurs et réducteurs sur la ligne de conditionnement de la brasserie.
Résultats en or
Les améliorations de la planification et les prouesses en matière de planification ont eu un impact chez MillerCoors.
« Nous avons toujours eu des gens formidables désireux de faire les bonnes choses », déclare l'ingénieur d'usine Mike Fognani. « La planification et la planification nous permettent de combiner ces personnes formidables avec les outils, les matériaux et le temps nécessaires pour réussir. »
Les travaux planifiés et programmés dans de nombreuses zones du site représentent désormais plus de 60 % de la charge de travail de maintenance ; dans un passé récent, ce chiffre était inférieur à 30 %.
Le travail de PM terminé a considérablement augmenté. Dans le domaine des chariots élévateurs, par exemple, Simpkins affirme que le taux d'achèvement est passé de 31 % à 82 % en moins de 18 mois.
La disponibilité, la productivité et la disponibilité des équipements ont toutes augmenté. Tout cela a conduit à des coûts de maintenance réduits.
"Auparavant, c'était" la maintenance ne peut pas le faire fonctionner ", " vous n'êtes pas fiable " et " vous dépensez trop d'argent " ", explique McCall. « Depuis que nous nous sommes stabilisés et que nous sommes plus proactifs, nos coûts de maintenance ont baissé. »
De nombreuses opportunités existent encore.
« Dans de nombreux domaines, nous faisons ce que nous devons faire et obtenons les résultats que nous recherchons », déclare Roberts. « Nous sommes sur la bonne voie, mais nous n'y sommes pas encore. Nous avons encore des poches d'opportunités avec la planification et la planification, et nous nous concentrons sur les moyens d'apporter des changements par étape, même dans le sillage de l'excellent travail déjà en cours. "
Coûts réduits. Fiabilité accrue. De meilleures décisions. Une plus grande stabilité.
MillerCoors a peut-être trouvé un moyen de rendre la planification sexy.
Juste les faits Site :usines MillerCoors à Golden, Colorado (comprend la brasserie et les zones de soutien à la production connexes), et Rocky Mountain Metal Container et Rocky Mountain Bottle Company (deux usines en coentreprise).Emploi :Près de 2 000 employés dans les usines de fabrication de Golden.
Taille du site :Situé principalement dans une vallée de cinq milles de long à Golden.
Produits :Près d'une dizaine de marques de bières, dont Coors, Coors Light, George Killian's Irish Red Lager, Aspen Edge et Keystone. Aussi, les boissons maltées de marque Zima.
Volume de production :Plus de 20 millions de barils de bière brassés à Golden chaque année.
Entretien et réparation d'équipement
- Obtenez plus de travaux de maintenance avec une planification appropriée
- Comment réaliser une planification de maintenance efficace
- Réunions du matin :planification et planification de la maintenance
- En maintenance, deux plus deux peuvent égaler huit
- Planification de la maintenance :qu'est-ce que cela vous apporte ?
- Travail d'équipe, planification et planification
- Plages de contrôle pour les planificateurs de maintenance et autres
- Boeing s'engage à améliorer les processus de planification de la maintenance
- La maintenance préventive ou la maintenance prédictive sont-elles meilleures ?