Assurez-vous que les conceptions de moulage par injection sont prêtes pour la production grâce à cette liste de contrôle
Le moulage par injection permet la production en grand volume de pièces identiques à un prix par pièce peu élevé. Le processus consiste à injecter du matériau fondu dans des moules métalliques durables à travers une buse sous pression, à éjecter la pièce une fois que le matériau a durci et à répéter. Une large gamme d'articles de tous les jours, y compris des bouteilles d'eau, des jouets en plastique et des boîtiers électroniques, est fabriquée par moulage par injection. Bien que les thermoplastiques et les thermodurcissables soient les matériaux les plus couramment utilisés dans le moulage par injection, le métal peut également être moulé par injection.
Lorsque vous fabriquez une pièce par moulage par injection, vous devez tenir compte d'un certain nombre de variables qui ont un impact sur la qualité et la fonctionnalité du produit final. Une pièce moulée par injection peut échouer de plusieurs manières, y compris les lignes d'écoulement, les retassures et le gauchissement, mais vous pouvez éviter la plupart des problèmes en suivant quelques principes de conception clés.
Chez Fast Radius, nous travaillons chaque jour avec nos clients sur leurs pièces moulées par injection. Les ingénieurs viennent souvent nous voir avec de superbes conceptions de pièces qui doivent être ajustées avant de pouvoir être fabriquées efficacement. Nos experts en conception pour la fabrication (DFM) ont évalué et ajusté des milliers de conceptions de pièces, et ils ont identifié et compilé les problèmes les plus courants qu'ils rencontrent. La correction de ces erreurs courantes dans votre conception peut éviter des erreurs coûteuses et vous faire gagner beaucoup de temps dans les révisions de conception.
Avant de soumettre votre conception de pièce à mouler par injection, vérifiez-la par rapport à cette liste de règles de conception :
Utilisez des angles de dépouille appropriés
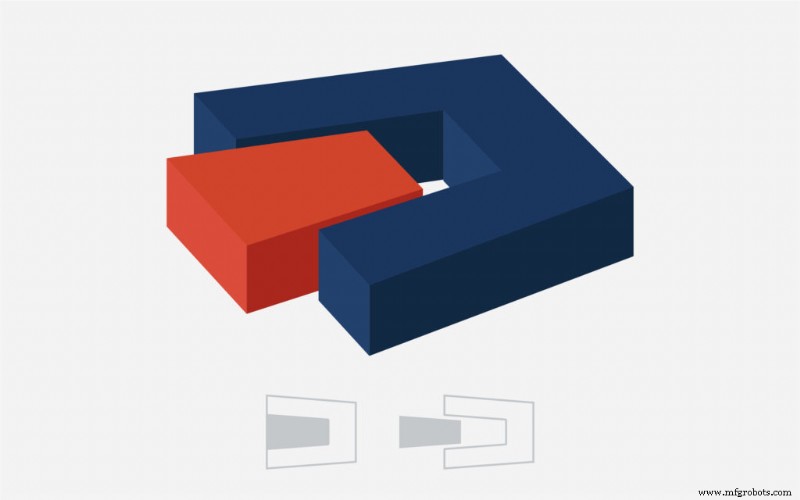
Un tirant d'eau de 1,5 à 2 degrés est généralement un minimum sûr pour la plupart des pièces.
Les angles de dépouille font référence à la légère conicité ajoutée aux surfaces d'une pièce moulée par injection qui s'alignent avec la direction de traction, permettant à la pièce d'être retirée du moule sans être endommagée par le frottement ou l'aspiration.
L'angle de dépouille requis pour une pièce dépend de quelques facteurs, notamment l'épaisseur de la paroi, le taux de retrait du matériau de la pièce, la profondeur d'étirage et si la pièce nécessitera une finition de surface ou une texturation pendant la post-production. Alors que le tirant d'eau moyen devrait augmenter de 1 degré pour chaque pouce supplémentaire de profondeur de pièce, un tirant d'eau de 1,5 à 2 degrés est généralement un minimum sûr pour la plupart des pièces.
Maintenir une épaisseur de paroi uniforme, si possible
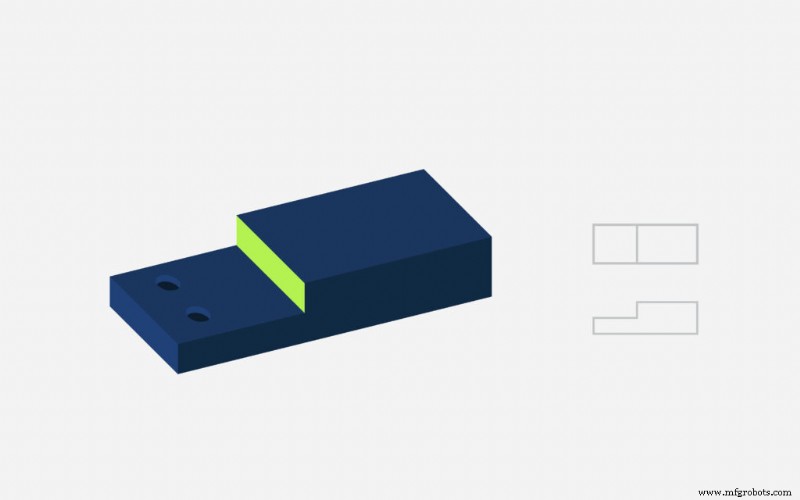
Si possible, les composants moulés par injection doivent avoir une épaisseur de paroi uniforme sur toute la pièce. Les variations d'épaisseur de paroi peuvent entraîner le refroidissement du matériau injecté à des vitesses différentes, ce qui peut entraîner des retassures, des vides et un gauchissement.
Généralement, des épaisseurs de paroi comprises entre 1,2 mm et 3 mm sont idéales (bien que certaines variations puissent être attendues en fonction du matériau). L'épaisseur de paroi doit presque toujours rester inférieure à 5 mm, car des parois plus épaisses augmentent les temps de cycle de production et peuvent également avoir un impact négatif sur les propriétés mécaniques de la pièce.
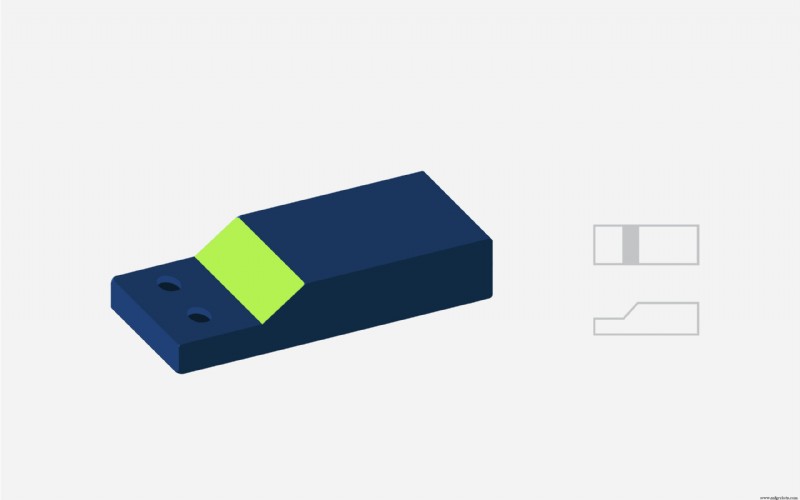
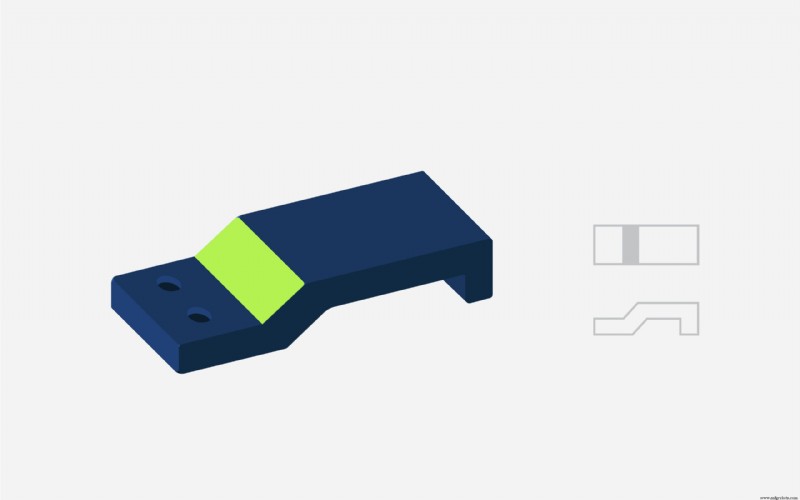
Si une pièce nécessite des variations d'épaisseur de paroi, vous devez rendre la transition entre les sections aussi progressive que possible. Vous pouvez le faire en incorporant des chanfreins (coins ou bords inclinés) ou des filets (coins ou bords arrondis) dans la conception de la pièce, ce qui permet de s'assurer que le jet de plastique fondu remplit complètement le moule, refroidit complètement et uniformément, et empêche le gauchissement ou non. -retrait uniforme.
En règle générale, la longueur de la transition entre les sections avec des épaisseurs de paroi différentes doit être de 3 x le changement d'épaisseur de paroi (par exemple, si l'épaisseur de paroi diminue de 1 mm, la transition doit se produire sur 3 mm).
Éviter les contre-dépouilles
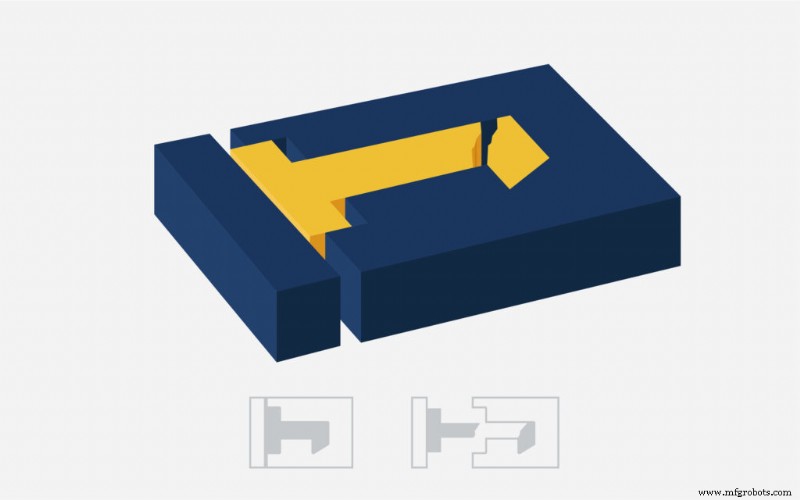
Les contre-dépouilles sont des surfaces ou des caractéristiques en retrait ou en surplomb, telles que des filetages, des rainures ou des encliquetages, qui empêchent une pièce d'être éjectée du moule en une seule traction unidirectionnelle sans dommage. Il est possible d'éviter les contre-dépouilles en orientant les éléments parallèlement à la ligne de tracé ou en incorporant des actions dans la conception de votre moule.
Arrondissez les arêtes vives et les coins
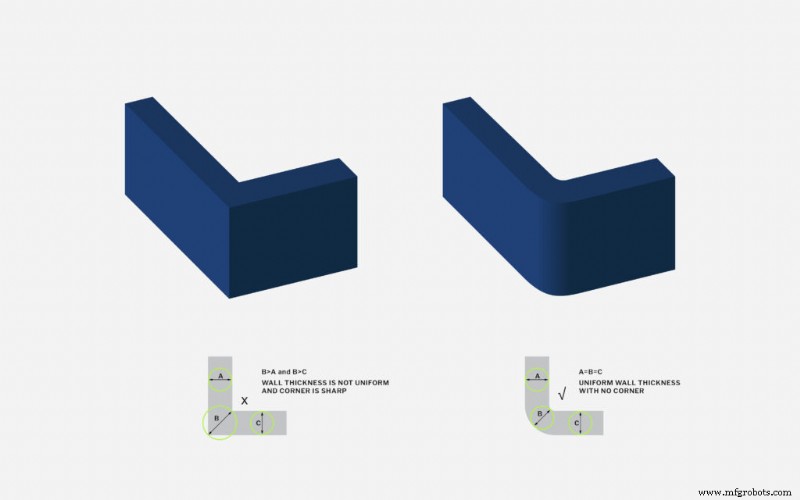
Dans la mesure du possible, les concepteurs et les ingénieurs doivent opter pour des éléments ronds plutôt que des arêtes et des angles vifs. Les bords nécessitent une pression supplémentaire pour se remplir, ce qui rend plus difficile l'écoulement efficace et uniforme d'une grenaille dans le moule. Les arêtes vives ont également tendance à s'accrocher au moule lors de l'éjection, ce qui augmente le risque d'endommagement et de défauts des pièces. Vous pouvez éviter ces deux problèmes avec des coins internes et externes arrondis.
Les coins internes, ou ceux où les murs partiels rencontrent le sol, doivent avoir un rayon d'au moins 50 % de l'épaisseur du mur adjacent. Les coins externes, ou ceux situés en haut des murs partiels, doivent avoir un rayon de 150 % du mur adjacent pour permettre au plastique de s'écouler plus efficacement. Cela permet également de minimiser les contraintes résiduelles et les fissures.
La base de toutes les fonctions verticales d'une pièce (comme les bossages, les nervures ou les ajustements par encliquetage) doit également être arrondie. Les rayons de bossage doivent être de 25 % du mur adjacent, avec un rayon minimum de 0,015" (ou 0,381 mm).
Situer les lignes de séparation stratégiquement
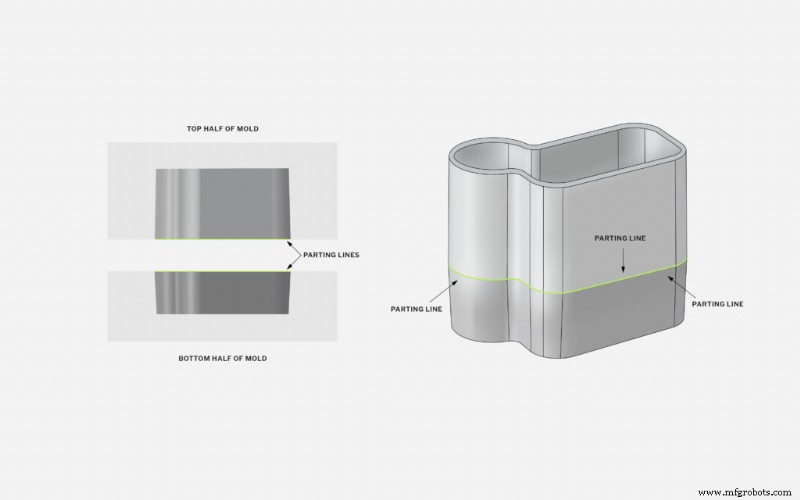
Une marque physique, connue sous le nom de ligne de séparation, apparaîtra à l'endroit où les deux moitiés d'un moule se rencontrent. Dans de nombreux cas, les lignes de séparation peuvent être facilement vues et ressenties, mais c'est plus qu'un problème esthétique. Le placement de la ligne de séparation dicte la façon dont le moule s'ouvre (et donc la direction dans laquelle vous devez ajouter une dépouille aux fonctions de la pièce), et il peut influencer à la fois le coût de l'outillage du moule et tout post-traitement requis.
Vous pouvez souvent améliorer l'apparence et la fonctionnalité d'une pièce en plaçant la séparation le long d'un bord plutôt que sur une surface plane. Cela aide à masquer le joint et réduit également les risques de flash (matériau excessif autour de l'endroit où le moule se rejoint).
Pensez au placement de la broche d'éjection
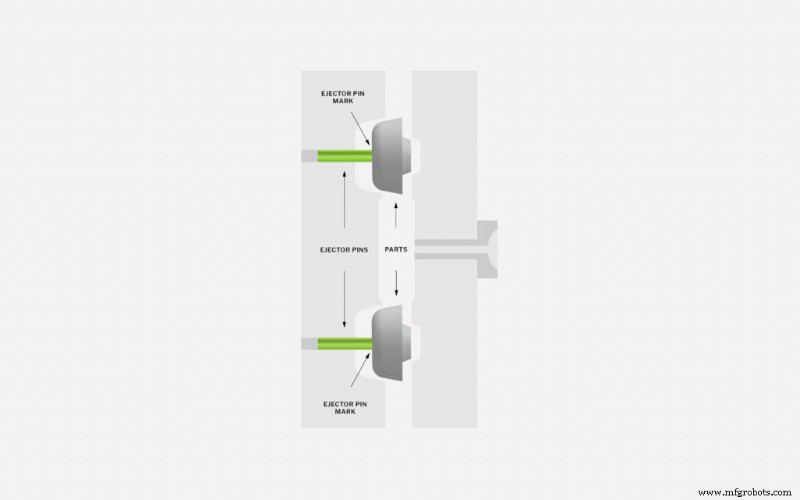
Pour fonctionner correctement, les éjecteurs nécessitent des surfaces planes, ou des tampons, placés perpendiculairement à la direction du mouvement de la broche. L'emplacement et le nombre de goupilles doivent être informés par la forme de la pièce, les angles de dépouille, la texture de la paroi latérale et la profondeur de la paroi, qui influencent tous la façon dont une pièce s'accrochera aux parois du moule.
Le choix du matériau doit également être pris en compte dans le placement ou la taille des broches. Les résines plus collantes, par exemple, ont tendance à nécessiter plus de force pour être éjectées. De même, les plastiques plus souples auront probablement besoin d'un plus grand nombre de broches ou de broches plus larges afin de répartir efficacement la force d'éjection et d'éviter d'endommager la pièce.
Optimiser la taille des nervures de support
Les nervures sont souvent utilisées pour renforcer les parois partielles dans des situations où deux parois partielles se rencontrent à un angle de 90 degrés, ou lorsque la longueur d'une section particulière est affaiblie par l'épaisseur de paroi de la section.
Il est important de noter que des côtes plus épaisses ne signifient pas nécessairement un meilleur soutien - en fait, des côtes trop épaisses entraînent souvent des marques d'évier. L'épaisseur de base des nervures de support doit être au maximum égale aux deux tiers de l'épaisseur du mur adjacent.
Soyez conscient de l'épaisseur de la paroi du moule
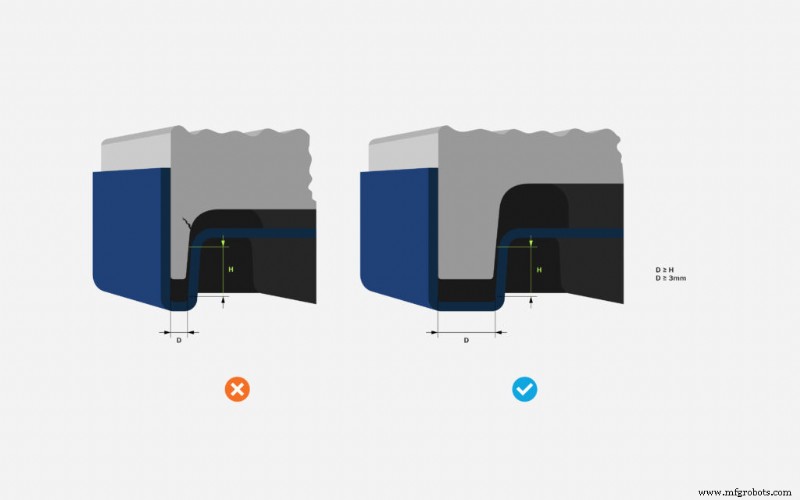
L'épaisseur des parois du moule est une autre considération importante - et qui sera principalement déterminée par l'espace entre les caractéristiques de la pièce. Assurez-vous que les éléments verticaux tels que les nervures et les bossages ne sont pas trop proches les uns des autres, ne séparent pas les murs ou les zones minces, car cela complique le processus de refroidissement.
L'épaisseur de la paroi du moule peut également avoir un impact sur les coûts d'outillage. La majorité des moules à injection sont créés par usinage CNC et les parois métalliques plus minces dans le moule sont plus difficiles à usiner correctement. Des parois plus minces entraînent également des cycles de vie de moule plus courts.
Bien que l'épaisseur minimale autorisée de la paroi du moule soit dictée par les qualités physiques et mécaniques du matériau de la pièce, un jeu de 3 mm entre les caractéristiques de la pièce est généralement acceptable.
Concevoir des pièces moulées par injection de manière efficace et efficiente
Les erreurs de conception coûtent cher. Recouper un outil pour corriger une erreur de conception pourrait faire reculer les équipes produit de plusieurs semaines et coûter des milliers de dollars. Un bon partenaire de fabrication vous aidera à éviter des révisions coûteuses avec DFM, mais ce processus ajoute également à votre calendrier. Vérifier votre conception pour les problèmes mentionnés dans ce guide avant de la soumettre à un partenaire de fabrication vous aidera à obtenir de meilleures pièces plus rapidement.
Il y a beaucoup de choses qui peuvent mal tourner dans le moulage par injection, vous devez donc trouver un partenaire en qui vous pouvez avoir confiance pour obtenir vos pièces correctement. Chez Fast Radius, nous sommes là pour vous faciliter la tâche et nous nous investissons dans la réussite de votre projet. Contactez-nous dès aujourd'hui pour commencer votre prochain projet de moulage par injection.
Pour en savoir plus sur le moulage par injection - de la sélection des matériaux aux différences entre les moules à cavité unique et à cavités multiples, en passant par la manière dont nous avons exploité le processus pour fabriquer des masques faciaux qui combattent la propagation du COVID-19 - visitez le centre d'apprentissage Fast Radius .
Prêt à fabriquer vos pièces avec Fast Radius ?
Commencez votre devisTechnologie industrielle
- Moulage par injection avec la technologie PolyJet
- Robots d'interface à six axes avec presses de moulage par injection
- Comment les meilleures entreprises de moulage par injection génèrent plus d'opportunités grâce au marketing numérique
- Que sont les défauts de moulage par injection et comment les prévenir :10 défauts de pièces en plastique
- Micro moulage avec des polyuréthanes
- Qu'est-ce que le moulage par injection de réaction
- Moulage vs moulage par injection
- Moulage par injection vs moulage par injection de réaction (RIM)
- Moulage par coulée vs moulage par injection de réaction