Directives de conception et de production essentielles pour le moulage par insertion
Le moulage par insertion est un processus de moulage par injection qui est lié au surmoulage, mais qui se distingue de quelques manières clés. Alors que le surmoulage consiste à injecter une deuxième résine sur un substrat en plastique plus ferme - ce qui permet aux équipes de produits de mouler des dispositifs ergonomiques, des poignées d'outils électriques et des joints en caoutchouc directement sur des pièces préexistantes sans créer de travail manuel supplémentaire - le moulage par insertion est la pratique consistant à charger un composant préformé (généralement en métal) dans un moule avant l'injection de la matière plastique.
La technique d'utilisation d'inserts dans le moulage par injection permet aux concepteurs et aux ingénieurs d'ajouter efficacement des inserts métalliques filetés aux pièces en plastique, d'intégrer des composants électriques métalliques dans des boîtiers de protection en plastique ou de créer des outils à main courants tels que des ciseaux et des tournevis.
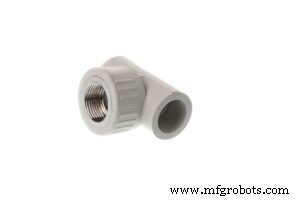
En tant que processus, le moulage par injection d'insert est plus facilement contrôlé et peut fournir de meilleurs résultats que d'autres méthodes d'encapsulation de composants métalliques dans des pièces en plastique. Les fabricants automobiles, médicaux et électriques, ainsi que ceux opérant dans les biens de consommation, la beauté et d'autres industries, tirent de plus en plus parti des technologies de moulage par insertion. Cependant, afin de maximiser les avantages du moulage par insertion, les équipes de produits doivent tenir compte de certaines considérations de conception et de processus.
Lignes directrices pour l'optimisation de la conception des moules d'insertion
Lors de la conception d'inserts moulés personnalisés, les équipes de produits doivent respecter les meilleures pratiques DFAM courantes, en incorporant un moletage arrondi, en évitant les angles vifs et en optimisant les angles de dépouille. Alors que les contre-dépouilles (également appelées verrous mécaniques) augmentent la complexité et le coût de toute pièce, l'incorporation d'une contre-dépouille dans la conception du moule d'insert offre à la pièce une plus grande résistance à l'arrachement.
Une bonne règle de base lors de la conception d'inserts est de s'assurer qu'ils restent petits par rapport à la pièce en plastique dans laquelle ils sont intégrés. D'une manière générale, l'insert doit s'étendre sur un minimum de 0,016 po (0,4 mm dans la cavité du moule) et, afin d'éviter les retassures dans le plastique, le moulage sous l'insert doit être d'au moins un sixième de l'insert. diamètre.
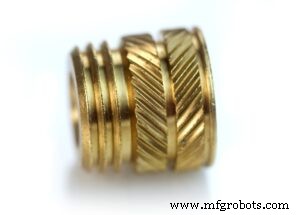
Un défaut de production courant associé à cette technique est la fissuration retardée dans le plastique entourant l'insert métallique. Si la contrainte de frette moulée de l'insert n'est pas prise en compte, les deux parties de la pièce peuvent facilement se séparer lorsque la résine injectée se contracte et se refroidit, et se ruine (en supposant que le plastique entourant l'insert subit une contrainte équivalente au retrait de moule). Il est conseillé d'utiliser des résines durcies et plus durables, car ces matériaux offrent de meilleures propriétés d'allongement et de résistance à la rupture.
La liaison des matériaux est une autre préoccupation commune à de nombreuses applications de moulage par insertion. Alors que les pièces surmoulées peuvent tirer parti des liaisons chimiques qui se forment entre les couches de différentes résines thermoplastiques, les inserts métalliques ne forment pas de liaisons chimiques avec les plastiques surmoulés. Les composants métalliques et plastiques doivent donc être conçus pour se lier mécaniquement entre eux.
L'un des principaux avantages du moulage d'inserts filetés dans des composants en plastique est que cela peut améliorer les qualités mécaniques de la pièce. Le métal augmente la résistance et la durabilité de l'ensemble de la pièce, par exemple, ce qui est utile pour les coques d'appareils et les boîtiers électroniques. Les composants d'accouplement peuvent également être équipés de douilles ou de manchons métalliques pour augmenter la résistance à l'abrasion et prolonger la durée de vie de la pièce.
Lignes directrices pour optimiser le processus de production de moulage par insertion
De bonnes habitudes de prototypage sont essentielles pour un moulage d'inserts rentable. C'est pourquoi les équipes de produits doivent tester leurs conceptions tôt. Le prototypage est essentiel pour identifier les problèmes de conception et de performances, ainsi que pour anticiper les défauts potentiels qui pourraient se développer au fil du temps. Un programme de test d'utilisation finale bien conçu comprend, par exemple, le test de la performance des composants d'une pièce dans les températures et les conditions environnementales prévues pour leur utilisation finale. La détection et la résolution des erreurs avant le début de la production permettent également de raccourcir les cycles de production et d'accélérer la mise sur le marché.
Il est essentiel que l'outillage utilisé pour fabriquer le moule respecte des tolérances précises, ce qui permet de garantir que l'insert est placé ou suspendu avec précision dans le moule lorsque le matériau fondu entre.
La plupart des moulages par insertion sont effectués dans une presse verticale car il est plus facile de charger le matériel sans qu'il ne tombe à sa place. Si le volume de production est suffisamment élevé, il peut être intéressant d'investir dans un système robotisé ou automatisé pour charger les inserts dans les moules, mais la plupart des travaux de volume faible à moyen nécessitent de placer manuellement les inserts dans le moule. Cela augmente le coût unitaire et le temps de travail, mais c'est généralement l'option la plus économique pour les cycles de production de ces tailles.
Rendez de nouvelles choses possibles grâce aux technologies de moulage par insertion de pointe
Le moulage par insertion élimine finalement la complexité de la fixation des composants ensemble pour créer des pièces solides sans avoir besoin d'assemblage ou d'étapes secondaires qui pourraient augmenter les coûts de production. Bien que similaire au surmoulage à bien des égards, le moulage par insertion est compatible avec un plus large éventail d'options de matériaux et d'applications d'utilisation finale. En fait, il est souvent utilisé pour créer les boîtiers d'appareils médicaux critiques tels que les stimulateurs cardiaques et d'autres implants.
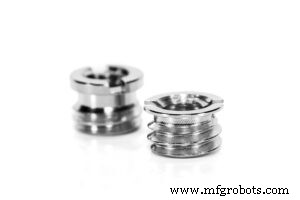
Cela dit, le moulage par insertion peut être une entreprise délicate. C'est pourquoi s'associer à un partenaire de fabrication expérimenté comme Fast Radius est le moyen le plus fiable de s'assurer que les pièces respectent les principaux seuils de matériaux, de performances et de tolérance sans allonger les délais de production ni se ruiner. Contactez-nous dès aujourd'hui pour en savoir plus sur nos services de moulage par insertion.
En savoir plus sur le moulage par injection, le surmoulage et notre gamme complète de capacités de fabrication à la demande en visitant notre centre de formation.
Prêt à fabriquer vos pièces avec Fast Radius ?
Commencez votre devisTechnologie industrielle
- Fabrication additive et moulage par injection — une nouvelle vision des cycles de production
- Demande de proposition – Photographie et production vidéo
- Directives de conception pour la manufacturabilité – Partie 2
- Lignes directrices pour la conception RF et micro-ondes
- Matériaux et conception de PCB pour haute tension
- L'industrie 4.0 et la fabrication distribuée permettent une production plus durable
- Conseils essentiels au processus de conception technique pour une production réussie
- Directives importantes de conception pour la fabrication et l'assemblage de PCB - Partie I
- Directives importantes de conception pour la fabrication et l'assemblage de PCB - Partie II