3 conseils pour créer des pièces moulées par injection plus solides
Le moulage par injection est un processus de fabrication polyvalent qui consiste généralement à injecter de la résine plastique fondue dans des moules métalliques durables, ce qui permet la production de volumes élevés de pièces identiques. Alors que le moulage par injection peut être incroyablement rentable à grande échelle, les pièces en plastique passent généralement par des revues de conception, des impressions 3D, des simulations et des tests avant le moulage par injection d'un produit final. Voici quelques conseils à garder à l'esprit lorsque vous concevez des pièces moulées par injection de plastique qui contribueront à améliorer la résistance du produit final.
Sélection des matériaux :Fondamental pour créer des pièces solides
Tout d'abord, une note rapide sur la sélection des matériaux. Cela peut sembler évident à dire, mais les matériaux particuliers dont sont faits vos composants auront un impact significatif sur la durabilité, la résistance et la ténacité de la pièce ou de l'assemblage final. Un moyen simple d'améliorer la résistance de vos pièces et assemblages ? Utilisez des thermoplastiques plus résistants. Voici quelques matériaux de moulage par injection courants à prendre en compte si vous cherchez spécifiquement à améliorer la résistance de vos pièces moulées par injection.
ABS
L'acrylonitrile butadiène styrène (ABS) est un thermoplastique technique résistant aux chocs qui a des utilisations domestiques et industrielles - tout, des télécommandes et des boîtiers électroniques aux compresseurs et aux nébuliseurs de fabrication, peut être fabriqué à partir de cette résine abordable. Cependant, l'ABS est sensible aux intempéries et à la fissuration sous contrainte lorsqu'il est introduit dans certains produits chimiques.
Polycarbonate
Aussi connu sous le nom de PC, ce plastique offre une incroyable résistance aux chocs (encore plus que l'ABS) et peut être rendu transparent, ce qui en fait une alternative courante au verre. Les biens de consommation tels que les lunettes de protection, les écrans faciaux, la signalisation intérieure et extérieure et les fenêtres sont fabriqués à partir de cette résine, qui est également parfois utilisée pour protéger l'extérieur des bâtiments. Bien qu'il soit résistant aux chocs, le PC est sujet aux rayures et coûte cher à travailler.
Nylon
Les nylons sont une famille polyvalente de plastiques bien adaptés aux applications nécessitant un faible coefficient de frottement associé à une bonne résistance à l'usure, aux produits chimiques et à la chaleur. Alors que le nylon non chargé a tendance à avoir un certain degré de flexibilité et de rigidité, des stabilisants et des additifs peuvent être incorporés dans le matériau pour optimiser les propriétés spécifiques de la pièce. Les fibres de verre, par exemple, améliorent la résistance à la compression, la rigidité et la température de déflexion thermique du matériau tout en le rendant cassant. Le nylon a tendance à absorber l'humidité de son environnement et est facilement endommagé par la lumière UV sans l'utilisation de stabilisants.
Acétal
L'acétal est apprécié pour sa rigidité, son faible coefficient de frottement et sa résistance à l'abrasion, à l'eau et aux produits chimiques. L'acétal est couramment utilisé pour produire des composants électroniques, des fermetures à glissière et des engrenages, des composants automobiles, des pièces pour l'industrie alimentaire et de nombreuses autres applications. L'acétal n'est pas compatible avec les technologies de fabrication additive et a donc tendance à être moins utilisé pour le prototypage que le nylon. Il n'est pas non plus bien adapté aux pièces cosmétiques ou à celles qui nécessitent de la peinture ou de l'impression.
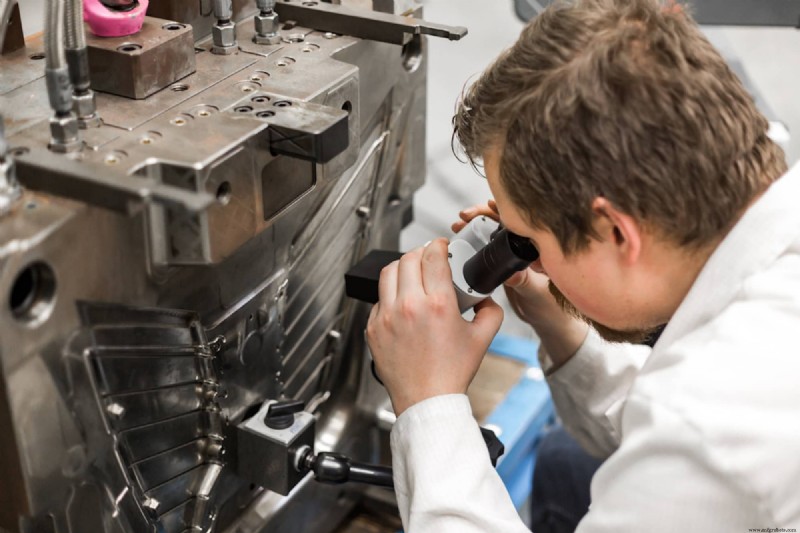
Conseils de conception pour construire des pièces plus solides
Éviter les sections épaisses
Le temps de refroidissement, généralement l'étape la plus longue du processus de moulage par injection, est déterminé par les sections les plus épaisses de la pièce. Un temps de refroidissement plus long signifie un temps de cycle plus long, ce qui augmente à son tour le coût de production. Des sections transversales plus épaisses augmentent également le risque que différentes sections de la pièce refroidissent à des vitesses différentes, ce qui peut entraîner des défauts tels que le gauchissement et les affaissements.
Le moulage par injection en tant que processus est généralement stable et cohérent lorsqu'il est utilisé pour produire des pièces avec des épaisseurs de paroi allant de 0,040" (1,016 mm) à 0,140" (3,556 mm), mais l'épaisseur de paroi nominale idéale varie selon le matériau. Les pièces dont l'épaisseur de paroi est supérieure à 0,120 po (3 mm) sont généralement moulables, mais nécessitent souvent une attention supplémentaire pour s'assurer que la cavité du moule se remplit à chaque cycle. Autour de 0,150" (3,8 mm), les sections transversales deviennent susceptibles de développer des puits, ce qui rend nécessaires des processus ou un support supplémentaires afin de maintenir la viabilité de la pièce.
Renforcer les murs ou les bossages avec des nervures
Les murs et les bossages sont deux caractéristiques qui dépassent souvent les directives d'épaisseur de paroi maximale ci-dessus, en partie parce qu'ils doivent être suffisamment solides pour fonctionner correctement. Les nervures renforcent les zones clés qui nécessitent une épaisseur de paroi supérieure à la valeur nominale, des éléments en relief et des murs hauts, le tout sans impact sur le temps de cycle. Dans certains cas, l'incorporation de plus de nervures dans la conception de la pièce peut réduire l'utilisation de matériau.
Pour minimiser le risque de dépressions ou de vides lors du refroidissement de la pièce, l'épaisseur de paroi d'un bossage doit être de 40 à 60 % de l'épaisseur de paroi nominale du composant. Les bossages doivent être fixés en place avec des nervures ou des filets pour minimiser le gauchissement. Les patrons peuvent introduire des points de contrainte supplémentaires, mais ils peuvent en fait renforcer les points de contrainte dans la conception d'une pièce s'ils sont correctement intégrés.
Utilisez des congés et des rayons pour renforcer les coins
Les angles vifs ne sont l'ami de personne dans la fabrication, en particulier pour les pièces moulées par injection. La solution pour contourner les virages ? Rayons de congé et rayons ronds. Les deux sont similaires - les rayons de congé étant l'arrondi d'un coin interne et les rayons arrondis l'arrondi des coins externes d'une pièce.
Arrondir les coins intérieurs offre un certain nombre d'avantages, notamment l'amélioration de la résistance à la charge de la pièce tout en aidant à atténuer la concentration des contraintes. Cela garantit également un remplissage plus uniforme de la cavité pendant la production, ce qui aide à empêcher le matériau d'angle de se dilater et de fissurer la qualité de la pièce. Des rayons de congé peuvent être ajoutés entre les bossages et les nervures, les reliant aux murs voisins pour une résistance supplémentaire. Arrondir un coin extérieur contribue à augmenter la résistance à la charge, réduit le risque de fractures et supprime les coins difficiles à remplir de la conception de la pièce, ce qui permet de garantir plus facilement des remplissages de moule plus cohérents.
Améliorez la résistance de vos pièces moulées par injection avec un expert qualifié
La durabilité et la ténacité ne sont pas les seules propriétés matérielles recherchées par les équipes produit. Il est essentiel de trouver le bon équilibre entre résistance, fonction, prix abordable et autres caractéristiques matérielles souhaitées. Sinon, vous risquez de vous retrouver avec une pièce trop souple ou trop cassante.
Travailler avec un partenaire de fabrication expérimenté comme Fast Radius signifie que vous vous reposez tranquillement. Notre équipe travaille dur pour aider chacun de nos clients à optimiser leurs conceptions et fournir les informations nécessaires pour garantir que chaque pièce que nous produisons avec vous dépasse les attentes en matière de résistance, de calendrier de production et de coût. Prêt à commencer? Contactez-nous dès aujourd'hui pour en savoir plus sur nos services de moulage par injection.
Technologie industrielle
- Cinq conseils pour créer un processus d'intégration de fournisseur efficace
- Moulage par injection robotisé pour composites fonctionnalisés
- Matériaux pour le moulage par injection-réaction (RIM)
- Conseils de conception pour le moulage par coulée
- Outillage souple ou dur pour le moulage par injection
- Angle de dépouille pour le moulage par injection :Guide de conception et meilleures pratiques
- Le moulage par injection et l'impression 3D se combinent pour créer des pièces "impossibles"
- Options matérielles pour le moulage par injection
- Conseils de conception pour le moulage par injection