Fabrication de fosses à l'échelle nanométrique avec un débit élevé sur une couche mince de polymère à l'aide de la lithographie dynamique à base de pointes AFM
Résumé
Nous montrons qu'une approche de lithographie de labour dynamique (DPL) basée sur la pointe d'un microscope à force atomique (AFM) peut être utilisée pour fabriquer des fosses à l'échelle nanométrique à haut débit. La méthode repose sur le grattage à une vitesse relativement grande sur une surface d'échantillon en mode tapotement, qui est responsable de la distance de séparation des puits adjacents. Des tests de grattage sont effectués sur un film mince de poly(méthacrylate de méthyle) (PMMA) à l'aide d'une pointe de revêtement en carbone de type diamant. Les résultats montrent que 100 μm/s est la valeur critique de la vitesse de grattage. Lorsque la vitesse de grattage est supérieure à 100 μm/s, des structures de fosse peuvent être générées. En revanche, les nanosillons peuvent être formés à des vitesses inférieures à la valeur critique. En raison de la difficulté de briser la chaîne moléculaire du polymère à l'état vitreux avec une charge à haute fréquence appliquée et une dissipation à faible énergie dans une interaction de la pointe et de l'échantillon, une fosse nécessite 65 à 80 pénétrations pour être réalisée. Par la suite, le processus de formation de la fosse est analysé en détail, comprenant trois phases :déformation élastique, déformation plastique et escalade sur l'empilement. En particulier, 4800-5800 puits peuvent être obtenus en 1 s en utilisant cette méthode proposée. Des expériences et des analyses théoriques sont présentées qui déterminent pleinement le potentiel de cette méthode proposée pour fabriquer des fosses efficacement.
Contexte
Le développement récent et rapide de la nanotechnologie a attiré une attention croissante sur l'application des nanostructures dans divers domaines, tels que les systèmes nanoélectromécaniques, les nanocapteurs et la nanophotonique. En particulier, les nanopoints, définis comme des nanostructures unidimensionnelles, sont largement utilisés dans les domaines du stockage haute densité et de la préparation de points quantiques [1]. Cependant, la fabrication efficace de nanodots est toujours confrontée à d'énormes défis. De nombreux chercheurs ont proposé diverses méthodes pour fabriquer des nanopoints sur une grande variété de matériaux. Parmi eux, la méthode de synthèse chimique est largement utilisée pour obtenir des nanodots pour la plupart des dispositifs de détection de propriétés et à l'échelle nanométrique [2]. Cependant, il est difficile de déterminer les dimensions et la distribution spatiale des nanodots en utilisant cette méthode. Cela se traduit par plus d'efforts requis pour la localisation et la manipulation dans les processus ultérieurs. Ainsi, de nombreux chercheurs ont consacré des ressources à l'exploration de méthodes plus contrôlables pour obtenir des structures de nanopoints avec des dimensions de plusieurs nanomètres, telles que la lithographie par faisceau d'ions focalisés [3], la lithographie par faisceau d'électrons [4] et la lithographie par nanoimpression [5]. Cependant, la complexité, les exigences environnementales strictes et/ou le coût élevé entravent grandement les applications de ces techniques.
Depuis que le microscope à force atomique (AFM) a été inventé en 1986, il a été couramment utilisé comme profileur de surface de haute précision [6]. Lorsque la force d'interaction entre la pointe de l'AFM et l'échantillon est agrandie à une valeur relativement grande, telle que plusieurs centaines de nanonewtons ou même plusieurs centaines de micronewtons, le matériau de l'échantillon peut être enlevé par la pointe pointue de manière plastique, similaire à un petit outil de coupe [7 ]. Des énergies chimiques et thermiques ont également été introduites dans le système AFM via l'oxydation locale [8] ou le chauffage de l'échantillon [9] pour faciliter l'élimination des matériaux de l'échantillon. Il en résulte donc de nouvelles méthodes de fabrication pour étendre la portée des méthodes existantes de nanolithographie à pointe AFM (TBN). Parmi toutes les méthodes TBN, l'approche par enlèvement mécanique est la plus simple et la plus flexible [10]. Cette méthode consiste d'abord en des actions d'indentation et de grattage subséquentes sur divers matériaux, dans lesquels l'interaction pointe-matériau dépend fortement du type de matériau, tels que les métaux [11], les semi-conducteurs [12, 13] et les polymères [14]. En contrôlant avec précision l'interaction pointe-matériau à l'échelle nanométrique, des nanostructures complexes et de haute précision, telles que des nanopoints, des nanosillons et même des nanostructures 3D, ont été fabriquées avec succès. En particulier, certains chercheurs ont effectué des processus de nanoindentation à base de pointes AFM sur la surface de matériaux semi-conducteurs pour obtenir des structures de nanopoints [15, 16]. Dans leurs études, les défauts cristallins causés par la nanoindentation ont été déterminés comme des sites de nucléation pour les nanostructures d'InAs. Cependant, la dureté relativement élevée des matériaux semi-conducteurs pourrait entraîner une usure importante de la pointe. Ainsi, certains chercheurs ont proposé d'effectuer le processus de nanoindentation sur des matériaux plus mous, tels que les polymères à couche mince, pour fabriquer d'abord des structures de nanopoints. Ces structures nanodot pourraient ensuite être transférées aux matériaux semi-conducteurs par gravure ionique réactive (RIE) ou par des procédés de gravure humide [17]. En raison de sa faible dureté et de son épaisseur ultra-mince, la couche de réserve pourrait être pénétrée avec une charge normale relativement faible. Certains chercheurs ont proposé une approche de grattage en deux étapes pour obtenir des réseaux de nanopoints sur une surface en polycarbonate [18]. Cette méthode repose sur les ondulations des matériaux formées par le processus de grattage constant à force de pointe AFM. Cependant, la distance d'espacement entre les nanopoints adjacents ne dépend que de la géométrie de la pointe de l'AFM, et le mécanisme de formation des nanopoints reste incertain.
D'autre part, le faible débit est un facteur critique entravant le développement de méthodes de nanofabrication basées sur la pointe AFM. Il a été démontré que le processus de nanoindentation basé sur la pointe AFM prend du temps pour obtenir des structures de nanopoints à grande échelle [19]. Pour résoudre ce problème, Vettiger et al. a présenté le concept de « mille-pattes », qui utilise de grands réseaux de micro-cantilevers fonctionnant en parallèle pour obtenir une capacité d'usinage à ultra-haute densité [20]. Compte tenu de l'usure importante de la pointe après un processus de grattage sur une grande surface, certains chercheurs ont proposé un nouveau fonctionnement en mode de contact intermittent pour réduire la force d'interaction pointe-échantillon, diminuant ainsi l'usure de la pointe [21, 22]. Cependant, les grands réseaux de micro-cantilevers utilisés dans cette approche nécessitent des processus de conception et de production compliqués, et un processus fastidieux est nécessaire pour ajuster la position de toutes les pointes sur une sonde afin de garantir le contact avec l'échantillon. Par conséquent, certains chercheurs ont modifié le système AFM commercial, y compris le matériel et les logiciels, pour promouvoir la capacité d'usinage à grande vitesse [23,24,25]. Dans ces méthodes, des pointes avec un porte-à-faux ont été utilisées. Cependant, seules les nanorainures peuvent être fabriquées en utilisant ces approches de manière efficace, et les rayures à grande vitesse pourraient également entraîner une usure importante de la pointe. En plus du traitement statique avec une pointe AFM, la lithographie de labour dynamique (DPL) basée sur la pointe AFM a également attiré de plus en plus d'attention récemment ; ce processus est effectué avec le mode de taraudage du système AFM. Lors de l'augmentation de l'amplitude d'entraînement du cantilever, la pointe de l'AFM peut pénétrer la surface de l'échantillon pour réaliser le processus d'usinage [26,27,28]. En raison du contact intermittent entre la pointe et l'échantillon dans l'approche DPL, l'usure de la pointe pourrait être réduite, de la même manière que les méthodes proposées dans les réfs. [21, 22]. La profondeur usinée obtenue par la méthode DPL est généralement de l'ordre de quelques nanomètres, ce qui convient à la fabrication de nanostructures sur un film mince, telles que les résines polymères à couche mince et les matériaux bidimensionnels [29]. De plus, dans la méthode DPL, le porte-à-faux de la pointe de l'AFM pourrait être amené à osciller à plusieurs milliers de hertz, ce qui entraînerait une interaction de la pointe avec la surface de l'échantillon plusieurs fois sur une courte période. Ainsi, la méthode DPL pourrait être une approche potentielle pour fabriquer efficacement des structures de puits à l'échelle nanométrique sur une surface d'échantillon à couche mince.
Dans cette étude, une méthode de nanolithographie à balayage rapide (FSN) est présentée sur la base de l'approche de fabrication DPL et en utilisant un système AFM commercial. La figure 1a montre un schéma du processus de nano-grattage avec une pointe de revêtement en carbone de type diamant, qui illustre une vue de la pointe en contact avec un film mince de poly(méthacrylate de méthyle) (PMMA) sur un substrat de silicium. Le cantilever est entraîné près de sa fréquence de résonance pour générer un contact intermittent entre la pointe et la surface de l'échantillon. L'amplitude d'entraînement de la pointe est maintenue à une valeur constante par le système de contrôle (AM-AFM). Le module Nanoman équipé du système AFM est utilisé pour tous les processus d'usinage, et la direction de grattage est choisie parallèle à l'axe long du porte-à-faux. L'effet de la vitesse de grattage sur les nanostructures usinées est étudié. De plus, le mécanisme de formation de la structure de la fosse est également étudié.
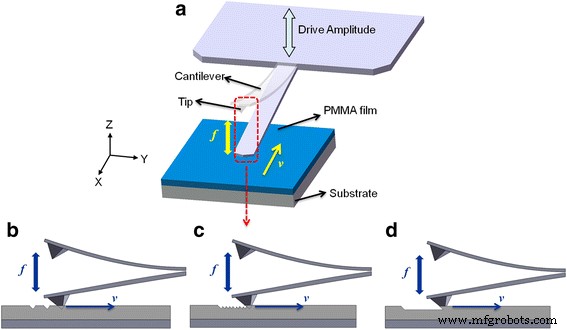
un Schéma du processus de grattage de ligne sur une surface de film PMMA avec la méthode FSN. Le cantilever oscille à sa fréquence de résonance f dans le sens vertical. La vitesse de grattage v est modifié le long de la direction de balayage rapide. Diverses plages de vitesse de grattage sont représentées :b vitesse de grattage élevée, c vitesse de grattage moyenne, et d faible vitesse de grattage
Méthodes
La concentration de la solution de PMMA est de 1,25 % en poids, préparée en dissolvant la poudre de PMMA de poids moléculaire Mw = 120 000 dans du chlorobenzène. Les films de PMMA sont préparés en faisant tourner la solution sur un morceau de substrat de Si monocristallin, qui est nettoyé par des bains à ultrasons successifs dans l'acétone et l'alcool pendant environ 10 min. La vitesse de filage est choisie pour être de 6000 tr/min dans les expériences pour générer des films avec des épaisseurs de plusieurs dizaines de nanomètres. Après le processus de revêtement, les films PMMA sont post-cuits à 125 °C, ce qui est proche de la température de transition vitreuse du PMMA, pendant 30 min.
Les expériences sont conduites avec un AFM commercial (Dimension Icon; Bruker Corporation, USA). Une pointe en silicium est sélectionnée avec une constante de ressort nominale de 42 N/m et une fréquence de résonance de 320 kHz, fournies par le fabricant (TESPD ; Bruker Corporation, États-Unis). Le côté pointe du cantilever est durci avec un revêtement en carbone de type diamant (DLC) pour une durée de vie prolongée de la pointe. La mesure des nanostructures sur la surface du PMMA est réglée en mode tapotement avec une fréquence de balayage de 1 Hz et une ligne de balayage de 256. Le système en porte-à-faux doit être réglé lors de l'utilisation de sondes différentes. Le point de réglage est réglé autour de 300 mV dans cette étude. Les images sont traitées par aplatissement du premier ordre à l'aide du logiciel d'analyse Nanoscope fourni par la société Bruker.
Le module Nanoman équipé du système AFM est utilisé pour le processus de grattage dans cette étude, qui est largement adopté pour concevoir la trajectoire de la pointe afin d'obtenir des structures souhaitables, telles que des rectangles ou des cercles, sur la surface de l'échantillon. Pour modifier la surface, la valeur d'amplitude d'entraînement de la pointe doit être augmentée à V w (écriture), où l'interaction entre la pointe et le film PMMA est favorisée pour garantir que la pointe pénètre la surface de l'échantillon. Après le processus de grattage, la valeur d'amplitude d'entraînement de la pointe est immédiatement plongée à V r (lecture) sans changer le porte-à-faux. Par rapport à la méthode de lithographie par labour statique, l'usure de la pointe s'avère très faible avec le DPL et peut donc être négligée. En évitant de changer de sonde et de rechercher l'emplacement de la nanostructure, cette méthode d'imagerie in situ peut améliorer l'efficacité du processus de grattage. Toutes les expériences sont effectuées à température ambiante.
Résultats et discussion
Compte tenu de la limitation de vitesse de l'AFM PZT, des vitesses de grattage comprises entre 0,1 et 1 000 μm/s sont sélectionnées dans les tests expérimentaux. La figure 1 montre un schéma du processus de nano-usinage, y compris trois plages de vitesse. Lors du grattage à une vitesse relativement élevée (environ plusieurs centaines de micromètres par seconde), des creux séparés peuvent se former, comme le montre la figure 1b. Lorsque la vitesse de grattage ralentit à une valeur moyenne (environ 100 μm/s), les creux peuvent se chevaucher, comme le montre la figure 1c. Comme le montre la figure 1d, lorsque la vitesse de grattage atteint une valeur relativement faible (des dizaines de micromètres par seconde), les creux peuvent être transformés en nanosillons. Ce résultat indique que la distance entre les deux fosses fabriquées dépend de la vitesse de grattage, qui a une grande influence sur les nanomotifs fabriqués.
Dans cette étude, quatre directions de grattage typiques sont choisies, comme le montre la figure 2a. V 1 et V 3 représentent le grattage le long du grand axe du porte-à-faux ; V 2 et V 4 sont définis comme des rayures perpendiculaires au grand axe du porte-à-faux. Les trajectoires de pointe sont obtenues en pilotant l'AFM PZT. La figure 3 montre des images AFM de nanostructures à lignes carrées fabriquées avec différentes vitesses de grattage et les sections transversales correspondantes des nanostructures grattées avec la direction V 1 , lorsque la fréquence de résonance du cantilever est de 380 kHz. Avec une vitesse de grattage relativement élevée de 200 μm/s, des piqûres continues peuvent se former, comme le montre la figure 3a. Pour quatre directions de grattage définies à l'avance, des creux se formeraient immédiatement bien moins de 1 s, même si la vitesse de grattage s'éloigne au point de retournement des deux directions. Avec une vitesse de grattage moyenne (100 μm/s), aucune fosse évidente ne peut être trouvée le long de la trajectoire d'usinage et des nanostructures fluctuantes se forment, comme le montre la figure 3b. Une seule fosse avec une profondeur beaucoup plus grande peut être observée à l'intersection des deux chemins de grattage adjacents, ce qui peut s'expliquer comme suit. Pendant la période de transformation entre les deux chemins de grattage adjacents, la vitesse de grattage devrait ralentir jusqu'à 0 et la pointe peut s'enfoncer plus souvent dans la surface de l'échantillon que dans le cas du grattage, ce qui peut être la raison possible pour générer une plus grande profondeur de fosse. La vitesse de grattage de 100 μm/s peut être considérée comme une valeur critique pour la fabrication de piqûres continues sur un film mince de PMMA. La figure 3c montre les nanosillons usinés avec une vitesse de rayage de 50 μm/s. À partir de la section transversale du nanosillon usiné, on peut observer que le fond du nanosillon est relativement plat et qu'une profondeur évidente du nanosillon peut être formée. De plus, comme le montre la figure 3, du fait que la pointe laboure le film de PMMA, il n'y a pas de copeaux formés lors de la rayure et seuls des empilements peuvent se former, d'un côté ou des deux côtés de la rainure. De plus, les profils des différents côtés des nanostructures obtenues sont incohérents lors du grattage dans différentes directions, ce qui est similaire aux résultats obtenus en utilisant la lithographie statique avec une pointe asymétrique. Pour d'autres matériaux de réserve tels que le SU-8 ou le polystyrène (PS), les valeurs seuils de la vitesse de rayure seront différentes de celles du film PMMA, en raison du module de relaxation des contraintes différent. Cependant, leurs valeurs seuils peuvent être obtenues grâce à l'expérience de grattage en suivant la même approche de cette étude.
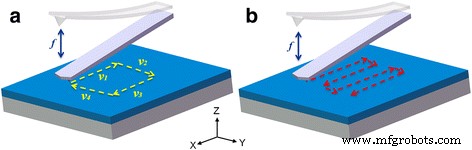
un Quatre directions de grattage typiques (V 1 , V 2 , V 3 , et V 4 ) sont choisis pour la fabrication par nano-usinage dans cette étude. b La trajectoire de la pointe avec l'avance pour les motifs de grande surface
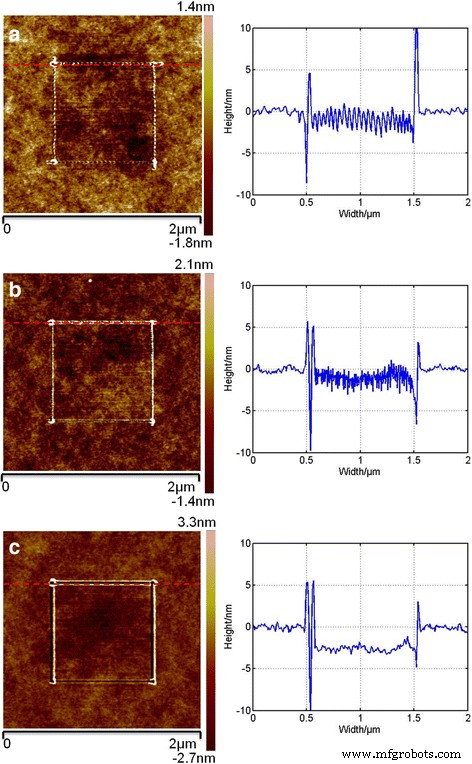
Images AFM de trois types de nanostructures et de leur section transversale avec des vitesses de grattage de a 200 μm/s, b 100 μm/s et c 50 μm/s
Avec des vitesses de grattage inférieures à 100 μm/s, des nanosillons de bonne qualité peuvent être obtenus. La figure 4 montre la relation entre la profondeur usinée du nanosillon et la vitesse de grattage avec les différentes directions de grattage illustrées à la figure 2a. Pour chaque nanosillon, la profondeur expérimentale est calculée par la moyenne de cinq valeurs de profondeur à cinq emplacements différents. Les distances de grattage pour toutes les directions de grattage sont les mêmes :1 μm dans cette étude. On peut observer que la profondeur usinée diminue avec l'augmentation de la vitesse de grattage pour toutes les directions de grattage. Une raison possible peut être expliquée comme suit. Pour une distance de grattage de 1 μm sélectionnée dans cette étude, le nombre d'opérations de presse à des vitesses de grattage de 100 μm/s et 1 μm/s sera respectivement de 3870 et 387 000. Pour la même distance de grattage, un grand nombre d'opérations de presse par la pointe AFM peut conduire à un pourcentage relativement important de chevauchement entre les opérations de presse adjacentes, ce qui peut entraîner une plus grande profondeur usinée du nanosillon. De plus, comme le montre la figure 4, les profondeurs des nanosillons rayés dans toutes les directions sont cohérentes lorsque la vitesse de rayage est inférieure à 5 μm/s, tandis que la profondeur du nanosillon usiné dans la direction V 3 devient beaucoup plus petite que les profondeurs usinées obtenues par d'autres directions avec des vitesses de rayage supérieures à 5 μm/s. De plus, les barres d'erreur des profondeurs usinées obtenues dans la direction V 3 sont beaucoup plus importantes lorsque la vitesse de grattage est inférieure à 5 μm/s que pour les autres. Une raison possible peut être expliquée comme suit. La sonde AFM géométrique utilisée dans cette étude est asymétrique, et une inclinaison de la sonde causée par la pente en porte-à-faux typique de 12°, utilisée pour garantir que seule la pointe de l'AFM touchera la surface de l'échantillon, peut entraîner une différence de la zone de contact entre la pointe et la surface de l'échantillon avec différentes directions de grattage. Pour une vitesse de grattage inférieure à 5 μm/s, la zone de chevauchement des opérations de presse adjacentes est très grande. Ainsi, la zone de contact entre la pointe et la surface de l'échantillon est également extrêmement grande. L'influence du sens de grattage sur la profondeur usinée peut donc être négligeable. Cependant, l'empilement formé le long de la surface de la pointe dépend également de la direction du grattage, qui est similaire au processus de grattage statique. Par conséquent, l'empilement ne peut pas être formé de façon constante dans le V 3 sens de grattage. Les chiffres insérés dans les Fig. 4a, b sont les sections transversales de nanorainures typiques usinées avec des vitesses de rayage de 0,5 et 50 μm/s, respectivement. À partir de la section transversale du nanosillon usinée avec une vitesse de grattage de 0,5 μm/s, le fond du nanosillon est fluctuant lors du grattage dans le V 3 direction, ce qui peut entraîner une barre d'erreur relativement grande pour la profondeur usinée. Pour le grattage avec une vitesse supérieure à 5 μm/s, la zone de chevauchement avec les opérations de presse adjacentes devient petite. Ainsi, la direction de grattage joue un rôle important, ce qui peut se traduire par une profondeur usinée relativement faible obtenue dans le V 3 sens de grattage.
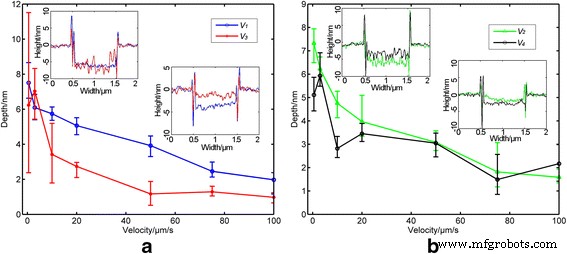
Dépendance de la profondeur de la rainure sur la vitesse de grattage dans les directions de grattage typiques :a V 1 et V 3 , parallèle au grand axe du porte-à-faux ; b V 2 et V 4 , perpendiculaire au grand axe du porte-à-faux. Les encarts montrent la section transversale des nanosillons pour des vitesses de rayage de 0,5 et 50 μm/s
Un film mince de PMMA est une sorte de matériau viscoélastique et dépendant du temps. Ainsi, la charge périodique appliquée par la pointe de l'AFM peut avoir une influence sur le module de Young de l'échantillon. La représentation générale du module de relaxation des contraintes G est défini par G 1 et G 2 [30] :
$$ G\left(\omega \right)={G}_1\left(\omega \right)+{iG}_2\left(\omega \right) $$ (1) $$ {G}_1\left (\omega \right)=\left[{G}_r\right]+{\int}_{-\infty}^{+\infty}\frac{H\left(\tau \right){\omega} ^2{\tau}^2}{1+{\omega}^2{\tau}^2}d\left(\ln \tau \right) $$ (2) $$ {G}_2\left( \omega \right)={\int}_{-\infty}^{+\infty}\frac{H\left(\tau \right)\omega \tau}{1+{\omega}^2{\ tau}^2}d\gauche(\ln \tau \right) $$ (3)où G r est une constante et ω est lié à la fréquence. H (τ ) est le spectre de temps de relaxation contribué à la relaxation de contrainte, qui a une relation avec les temps de relaxation entre lnτ et lnτ + d (lnτ ). Lorsque la fréquence d'excitation est réglée sur une valeur proche de la fréquence de résonance du cantilever, qui est de 387 kHz, le module peut atteindre une valeur élevée. D'après le calcul utilisant les équations mentionnées ci-dessus, le film mince de PMMA se présente comme un état vitreux avec une charge à haute fréquence appliquée [30]. Étant donné que le mode de taraudage est utilisé dans l'ensemble du processus d'usinage, la force d'interaction et la dissipation d'énergie entre la pointe de l'AFM et la surface de l'échantillon pendant le processus de grattage sont relativement faibles, et même l'amplitude d'entraînement V w /V r est réglé sur une valeur relativement élevée, allant de 10 à 20. Dans ces conditions d'usinage, en raison de la propriété vitreuse du film mince de PMMA et d'une charge appliquée relativement faible par la pointe de l'AFM, les chaînes entre les molécules de polymère ne peuvent pas être il est difficile de générer une déformation cassée et plastique pour modifier la surface de l'échantillon par un cycle de l'opération de presse. Cependant, la pointe a une énergie suffisante (> 1~2 eV) pour accomplir cela pendant les 20 à 30 premières fois de l'opération de presse [27]. Ainsi, les liaisons en chaîne entre les molécules de polymère peuvent être coupées pour générer une déformation plastique sur la surface du film mince.
La distance d'espacement entre les opérations de presse adjacentes est un paramètre critique qui a une relation avec la vitesse de grattage et la fréquence d'oscillation de la pointe. La distance d'une ligne des stands (L ) peut être obtenu par le temps utilisé pour une ligne des stands (t ) multiplié par la vitesse de grattage (v ). Le nombre total d'oscillations de pointe de l'AFM dans une ligne de fosse (N ) peut être calculé en utilisant la fréquence d'oscillation du cantilever (f ) multiplié par le temps (t ). Ainsi, la distance d'espacement entre les opérations de presse adjacentes (D ) peut être obtenu par l'équation. 4.
$$ D=\frac{L}{N}=\frac{v}{f} $$ (4)La fréquence de vibration naturelle du cantilever sélectionné dans cette étude est d'environ 387 kHz. La fréquence d'entraînement du système AFM est choisie pour être proche de cette valeur. Comme mentionné ci-dessus, la vitesse de grattage doit être sélectionnée dans la plage de 200 à 900 μm/s pour garantir la formation des piqûres. Ainsi, la distance d'espacement entre les opérations de presse adjacentes (D e ) pendant le processus de grattage peut être calculé dans la plage de 0,52 à 2,33 nm, qui est désignée par la courbe rouge sur la figure 5a. La courbe bleue de la Fig. 5a représente la relation entre la distance d'espacement entre les fosses adjacentes (D ) obtenu à partir des expériences et de la vitesse de grattage. Les images AFM en médaillon sont obtenues pour des puits usinés avec trois vitesses de rayage typiques de 400, 600 et 800 μm/s. Par conséquent, le nombre d'opérations de presse pour une formation de fosse peut être calculé comme le rapport de D à D e illustré à la figure 5b. En supposant que la vitesse de grattage est une valeur constante, 4 800 à 5 800 piqûres peuvent être générées sur un film mince de PMMA en 1 s, calculée à partir de la longueur de grattage (L ) et la distance d'espacement (D ). À partir de la figure 5b, on peut observer que le nombre d'opérations de presse pour une formation de fosse augmente avec l'augmentation de la vitesse de grattage et se situe principalement dans la plage de 65 à 80. Considérant que le terrain plat entre les deux fosses est presque égal aux dimensions de fosses, seules environ 32 à 40 opérations de presse sont nécessaires pour briser les chaînes polymères et générer une déformation plastique de la surface de l'échantillon, ce qui est cohérent avec la conclusion de Cappella [27]. De plus, on peut conclure qu'il est plus facile de casser les chaînes polymères lors du grattage avec une vitesse relativement faible. Dans cette étude, la constante d'élasticité du cantilever est identique. Un porte-à-faux plus rigide pourrait être utilisé pour la fabrication de fosses, ce qui entraînerait une force appliquée plus importante et une fréquence de résonance plus élevée. Si une force plus importante est appliquée à la surface de l'échantillon, l'apport d'énergie est augmenté à chaque cycle. Une plus grande dissipation d'énergie est ainsi contribuée à la déformation du film de PMMA. Une fosse peut donc être générée avec des cycles réduits. Cependant, si la fréquence de résonance est augmentée pour le système d'oscillation, le cycle de l'opération de presse entre la surface de l'échantillon et la pointe est ainsi augmenté. De plus, la dissipation d'énergie serait augmentée en un cycle, en raison du point de réglage diminué dans les expériences. La vitesse critique peut être déterminée par la valeur du point de réglage. Sur la base des discussions ci-dessus, la valeur seuil de la vitesse pourrait être influencée par la force appliquée, la fréquence de résonance du système en porte-à-faux et le point de réglage, qui feront l'objet d'enquêtes futures.
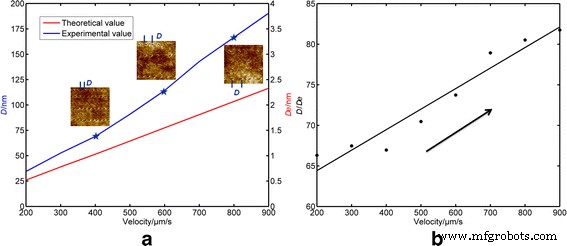
un Variante de D et D e avec vitesse de grattage (200-900 μm/s) ; les médaillons montrent les résultats de fabrication pour diverses vitesses de grattage. b Rapport de D à D e
Le processus de formation de la fosse est illustré sur la figure 6, comprenant trois phases :la déformation élastique, la déformation plastique et l'escalade sur l'empilement. Selon la discussion ci-dessus, pendant le grattage de la pointe sur la distance des figures 6a, b, le nombre d'opérations de presse n'est pas assez grand pour casser les chaînes polymères du film mince de PMMA et générer une déformation plastique de la surface de l'échantillon. Il a été démontré que la pointe oscillante pénètre progressivement dans l'échantillon de polymère au cours des 40 à 50 premières opérations [27]. Par rapport au processus d'indentation de la Réf. [27], le pressage avec une vitesse latérale pourrait générer une distance entre deux pénétrations adjacentes. Cependant, la distance entre deux pénétrations adjacentes (de l'ordre de 0,52 à 2,33 nm) est beaucoup plus petite que le rayon de la pointe de l'AFM (environ 15 nm). Ainsi, la situation dans cette étude est similaire au cas du processus d'indentation. En raison d'un manque d'accumulation d'énergie au cours des 30 à 40 pénétrations initiales, aucune déformation plastique évidente ne peut être trouvée dans la zone d'usinage. Ce résultat indique que le mécanisme dominant de dissipation d'énergie est la déformation élastique dans la première étape du grattage. Ainsi, la pointe de l'AFM glisse en contact continu avec la surface de l'échantillon pendant la période de temps entre les Fig. 6a, b. Lorsque le nombre de pénétrations effectuées par la pointe AFM atteint une valeur critique (40 fois dans cette étude), les chaînes polymères commencent à se briser et une déformation plastique se produit, comme le montre la figure 6c. Dans le même temps, une contrainte normale et de cisaillement se produirait à la surface d'interaction entre la face avant de la pointe de l'AFM et le matériau de l'échantillon ; ainsi, un empilement peut être généré devant la face avant de la pointe AFM. Une déformation (Δ) se produirait, attribuée au mouvement latéral de la pointe contre l'empilement. Il en résulterait une contrainte à l'intérieur du film polymère, qui pourrait être libérée par la propagation de la fissure [31]. Le taux de libération d'énergie de déformation V s peut être décrit comme :[32].
$$ {V}_s=E\frac{h}{2}{\gauche(\frac{\varDelta }{L}\right)}^2 $$ (5)où E est le module de Young du matériau polymère et L est la longueur du défaut interne. h représente la profondeur de pénétration totale jusqu'à la surface libre de l'échantillon. Le terme d'énergie de surface W contrôle le processus de défaut interne, qui est égal au taux de libération d'énergie de déformation à travers l'équilibre thermodynamique. Le terme d'énergie de surface dépend de la vitesse de propagation du défaut interne (v L ), qui est donné par [33].
$$ W={W}_0\left(1+\alpha {v}_L^n\right) $$ (6)où v L est égal à dL /dt et α est une valeur constante liée au matériau de l'échantillon. n est également un paramètre lié au matériau. Une force tangentielle appliquée sur l'apex de la pointe pourrait être générée par l'énergie élastique stockée dans le substrat polymère, qui peut être exprimée par [32] :
$$ {F}_t=\frac{Eah}{2}\frac{\varDelta }{L} $$ (7)où un représente le rayon de la zone de contact entre la pointe et l'échantillon. Parce que la rigidité de la sonde est beaucoup plus grande que la rigidité de l'échantillon, le matériau a pu être retiré du trou formé [31]. Cependant, Mindlin a défini une valeur critique de la force qui pourrait entraîner le glissement de la pointe sur la surface du substrat [34]. La force tangentielle critique (F tc ) pour le mouvement de glissement pourrait être déterminé comme une fonction de la force d'adhérence et de la charge normale, exprimée par [35,36,37,38] :
$$ {F}_{tc}=\mu \left(P+3\pi RW+\sqrt{6\pi RW P+{\left(3\pi RW\right)}^2}\right) $$ ( 8)où μ est le coefficient de frottement. P est la normale, et R représente le rayon de la pointe de l'AFM. Lorsque F t atteint la valeur critique F tc , la pointe de l'AFM glisserait sur l'empilement du matériau au lieu de pousser le matériau hors du trou produit par la pointe. Le contact se rompt à chaque cycle, et ainsi, le glissement peut ainsi se produire plus facilement à chaque cycle en mode taraudage. Although the setting point is not close to 100% of the tip oscillation reduction, a period of contact time could occur during one cycle and the stick may occur during this period of time.
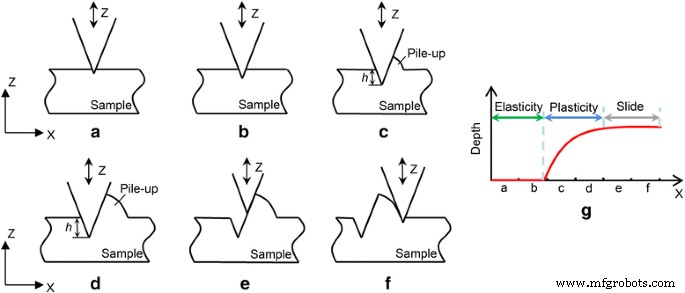
Schematic of pit formation with a , b elasticity stage, c , d plasticity stage, e , f slide stage, and g precedence diagram of pit formation
As shown in Fig. 6d, in this study, the depth that the AFM tip penetrated into the sample surface becomes larger because of the decrease of the tip-sample contact area when the AFM tip undergoes a lateral velocity. The height of the pile-up is also increased. This could contribute to balancing the normal load applied by the AFM tip. At the same time, the tangential force applied on the tip apex described in Eq. 7 could also be increased. With an increasing penetration depth, the tangential force could reach the critical value F tc given in Eq. 8. The AFM tip starts to slide on the formed pile-up without modifying the material. Because of the characteristics of the tracking sample surface of the AFM system, the AFM tip would rise to climb over the pile-up, as shown in Fig. 6e. After the AFM tip moved over the pile-up, one pit could be achieved and another pit would be fabricated by repeating the above steps. The corresponding deformation mechanism of each stage of pit formation can be found in Fig. 6g.
According to the previous experimental results, the scratching velocity should be set to larger than 100 μm/s. As shown in Fig. 2b, scratching directions V 1 and V 3 are selected and a feed perpendicular to the scratching direction is conducted to achieve pit arrays with a large dimension of 5 μm. Figure 7a shows the pit arrays obtained with a scratching velocity of 400 μm/s. Figure 7b, c shows the local and 3D AFM images of the machined pits, respectively. Because the scratching velocity slows down to 0 near the transition point of two different scratching directions, the depths of the first and last pits of one horizontal scratching path are much larger than the pits in the middle. One possible reason is explained above. As shown in Fig. 7b, c, the pits in the middle of the scratching path are distributed evenly, which may result from the constant velocity. Moreover, it can be observed from the cross-section of the pits shown in Fig. 7d that the depths of the pits are approximately 2.5 nm. In addition, because of the opposite scratching directions of the adjacent paths, the geometries of the pits in adjacent lines are different. As shown in Fig. 8a, with a scratching velocity of 200 μm/s, the spacing distance between the adjacent pits is relatively small and the geometries of the pits are close to circular. From the fast Fourier transform (FFT) image of the pits, high-density pits can be obtained with a scratching velocity of 200 μm/s. When scratching with a velocity of 900 μm/s, as shown in Fig. 8b, the spacing distance is nearly 100 nm and differences between pits obtained with different scratching directions can be clearly observed. Also from the FFT image of the pits, with a scratching velocity of 900 μm/s, only low-density pits can be achieved.
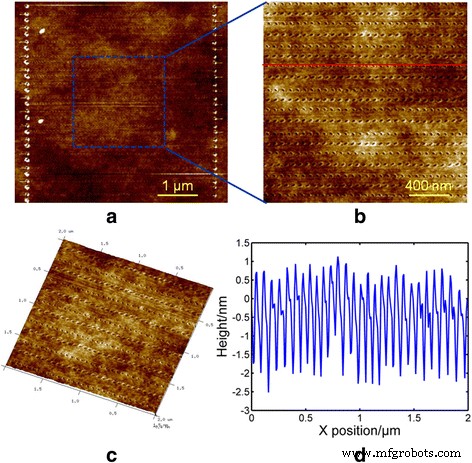
AFM images of an array of pits with a scratching velocity of 400 μm/s, a a dimension of 5 μm, b a portion of a with a dimension of 2 μm, c a 3D AFM image of b , and d a cross-section of pits for the red line in b
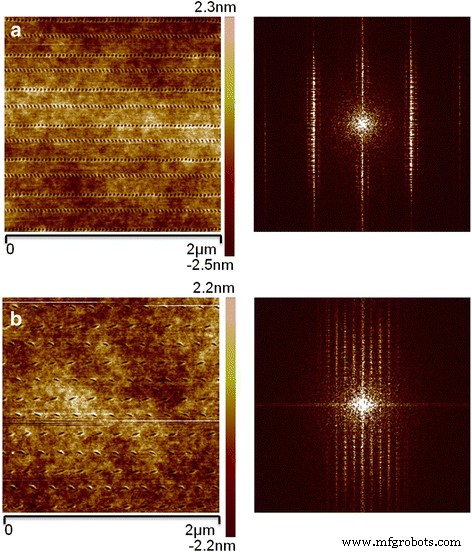
AFM image of pit arrary with a dimension of 2 μm and FFT image of the morphology. The scratching velocities are a 200 μm/s and b 900 μm/s
Conclusions
To improve the fabrication efficiency with the tip-based DPL method, a scratching velocity that ranges from 0.1 to 1000 μm/s is investigated and demonstrated based on the commercial AFM tapping mode. In the present study, results demonstrate that 100 μm/s is the critical value of the scratching velocity for the formation of pits. Nanogrooves with a pile-up can be obtained with scratching velocities less than the critical value. With scratching velocities greater than 5 μm/s, the machined depths are consistent in all typical directions except the V 3 direction, in which the machined depth becomes much smaller. In contrast, the depth is independent of the scratching direction. Separate pits can be generated with scratching velocities larger than the critical value of 100 μm/s. The total number of fabricated pits can reach nearly 4800–5800 in 1 s, when the scratching velocity is a constant value ranging from 200 to 900 μm/s. According to the stress relaxation modulus theory, the polymer surface is in the condition of a glass state when applying a high-frequency load. The energy applied on the sample surface is not large enough to break PMMA molecular chains during one penetration of the AFM tip. To form one pit, 65 to 80 penetrations are required. For the initial stage of penetration, elastic deformation is the dominant material removal mechanism. When the number of penetrations reaches 40 times, the polymer chains start to break and plastic deformation occurs. With increasing penetration depth, the height of the material accumulated beside the machined pit becomes larger, which will lead to an increase in the tangential force applied on the tip apex. This is the possible reason for the AFM tip sliding over the pile-up, after which one pit is created. Finally, pit arrays with dimensions of 5 μm, spacing distance of 70 nm, and machined depth of 2.5 nm are achieved successfully. FFT images are used to reveal the relationship between the density of pits and the scratching velocity.
Nanomatériaux
- Pionniers de l'AFM récompensés par le prix Kavli
- Fabrication par lots de microlentilles planes métalliques à large bande et de leurs réseaux associant l'auto-assemblage de nanosphères à la photolithographie conventionnelle
- Fabrication de nanomotifs ordonnés à l'aide d'un copolymère tribloc ABC avec du sel dans du toluène
- Fabrication à haut débit de nanofibres de qualité à l'aide d'un électrofilage à surface libre modifiée
- Fabrication de motifs de commutation optique avec des microfibres colorées structurelles
- Lithographie par diffraction par masque en une étape pour la fabrication de structures suspendues 3D
- Une référence de tension sans résistance à faible puissance à l'échelle nanométrique avec un PSRR élevé
- PMOSFET Ge à haute mobilité avec passivation Si amorphe :impact de l'orientation de la surface
- Encre polymère stable à haute conductivité