Guide du responsable de la maintenance pour la création et l'utilisation des AMDEC
Une attaque de ransomware vicieuse a frappé la ville d'Atlanta en mars 2018. Elle a fini par être l'une des violations les plus coûteuses de la dernière décennie. Les services publics ont été perturbés. Les ministères ont été obligés de remplir les documents essentiels à la main. Et cela a coûté 17 millions de dollars au gouvernement de la ville.
Lorsque la poussière est retombée, une chose était claire :la ville n'avait pas été préparée à ce désastre. Un audit effectué deux mois avant la violation a révélé 2 000 vulnérabilités dans le système informatique de la ville. C'était un bon pas, mais c'était trop peu, trop tard.
Ce qui s'est passé à Atlanta est une mise en garde avec une grande leçon :le risque ne peut jamais être éliminé, mais il peut être géré. C'est particulièrement vrai pour la maintenance. La défaillance de l'équipement est inévitable. Mais savoir comment réduire la probabilité d'échec et comment réagir lorsque cela se produit est essentiel au succès.
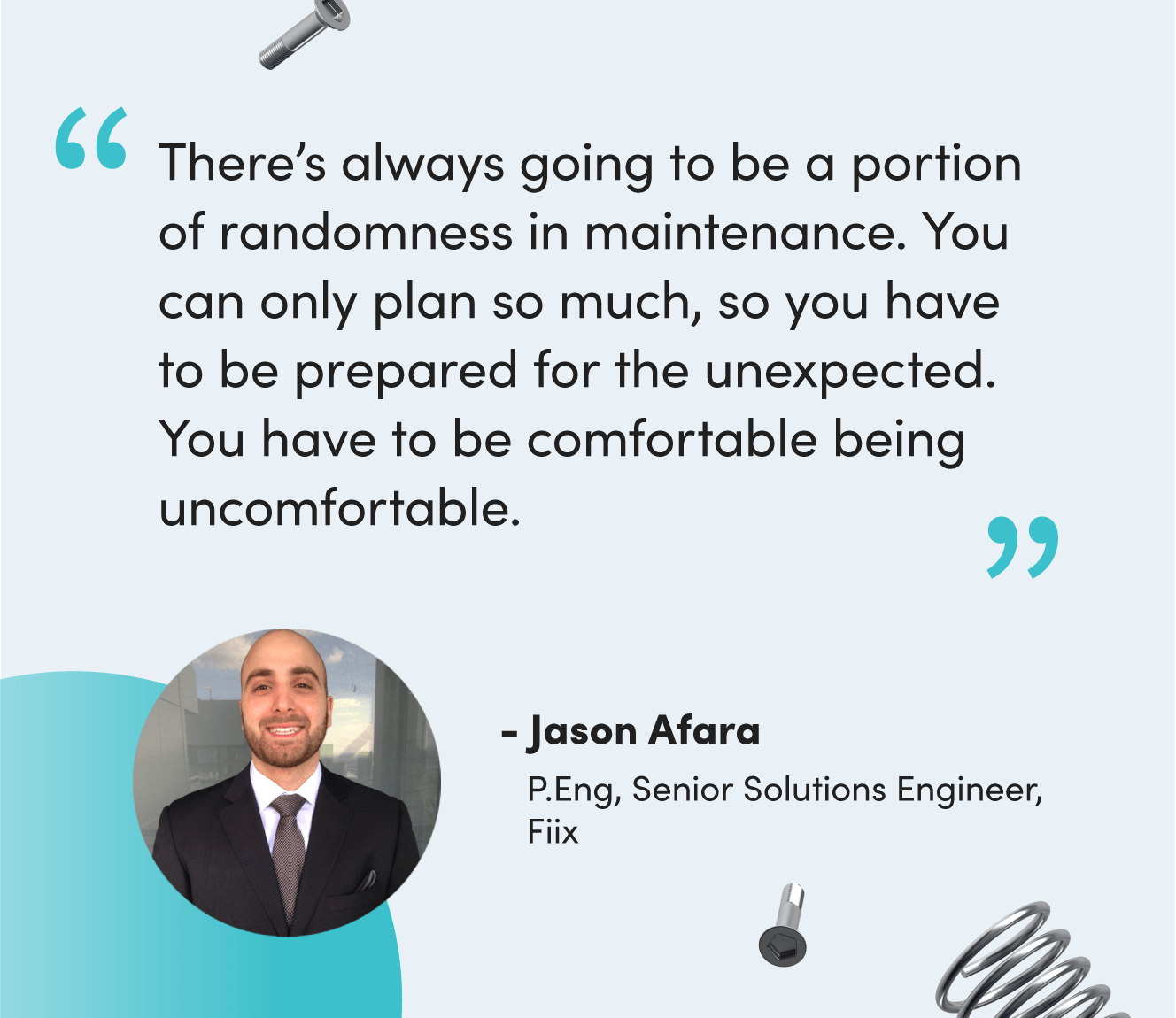
Une analyse des modes de défaillance et de leurs effets (AMDEC) est un outil pour comprendre et anticiper la défaillance afin de limiter son impact. Dans cet article, vous apprendrez :
- Qu'est-ce qu'une AMDEC
- Les différents types d'AMDEC
- Comment créer une AMDEC
- Et comment les équipes de maintenance peuvent utiliser une AMDEC
Qu'est-ce qu'une AMDEC ?
Une analyse des modes de défaillance et de leurs effets, ou AMDEC, identifie et documente toutes les manières dont un équipement peut tomber en panne et l'impact potentiel de ces défaillances. Il décrit :
- Modes de défaillance pour les composants individuels
- Les conséquences d'un échec sur la productivité et la sécurité
- Un plan pour prévenir ou réagir à ces problèmes
La création d'AMDEC est un élément clé de la maintenance centrée sur la fiabilité (RCM).
Une AMDEC a trois objectifs principaux :
- Prévenir les pannes futures en réduisant la probabilité de pannes courantes et critiques grâce à la maintenance planifiée et aux procédures d'exploitation standard
- Réduire les temps de réponse, les temps d'arrêt et améliorer la santé et la sécurité en cas de défaillance d'un élément
- Prioriser la maintenance préventive et corrective dans les situations non urgentes
Quels sont les différents types d'AMDEC ?
Les AMDEC peuvent être classées en sous-types en fonction du type de risque qu'elles évaluent et de l'impact qu'elles ont. Voici un aperçu rapide de chaque type d'AMDEC :
- FFMEA (analyse des modes et effets de défaillance fonctionnelle) :Une FFMEA analyse les risques qui affectent le fonctionnement d'un système. L'objectif d'un FFMEA (parfois appelé analyse du mode de défaillance du système et de ses effets) est de prévenir ces défaillances avant qu'elles ne surviennent.
- DFMEA (analyse des modes de défaillance et des effets de la conception) :Un DFMEA évalue les risques d'un actif au stade de la conception. L'objectif de cette analyse est de détecter et de corriger les problèmes potentiels d'un actif avant son déploiement afin d'augmenter sa fiabilité, de réduire la maintenance nécessaire et de prolonger le cycle de vie de l'actif.
- PFMEA (analyse des modes de défaillance et des effets du procédé) :Une PFMEA recherche les défaillances possibles au sein d'un processus. La différence entre une PFMEA et d'autres types de FMEA est qu'elle se concentre sur ce qui peut mal tourner pendant l'exploitation et la maintenance d'un système.
- AMDEC (analyse du mode de défaillance, des effets et de la criticité) :Une AMDEC (ou analyse de criticité) analyse à la fois les modes de défaillance et le niveau de risque associé à ces modes de défaillance.
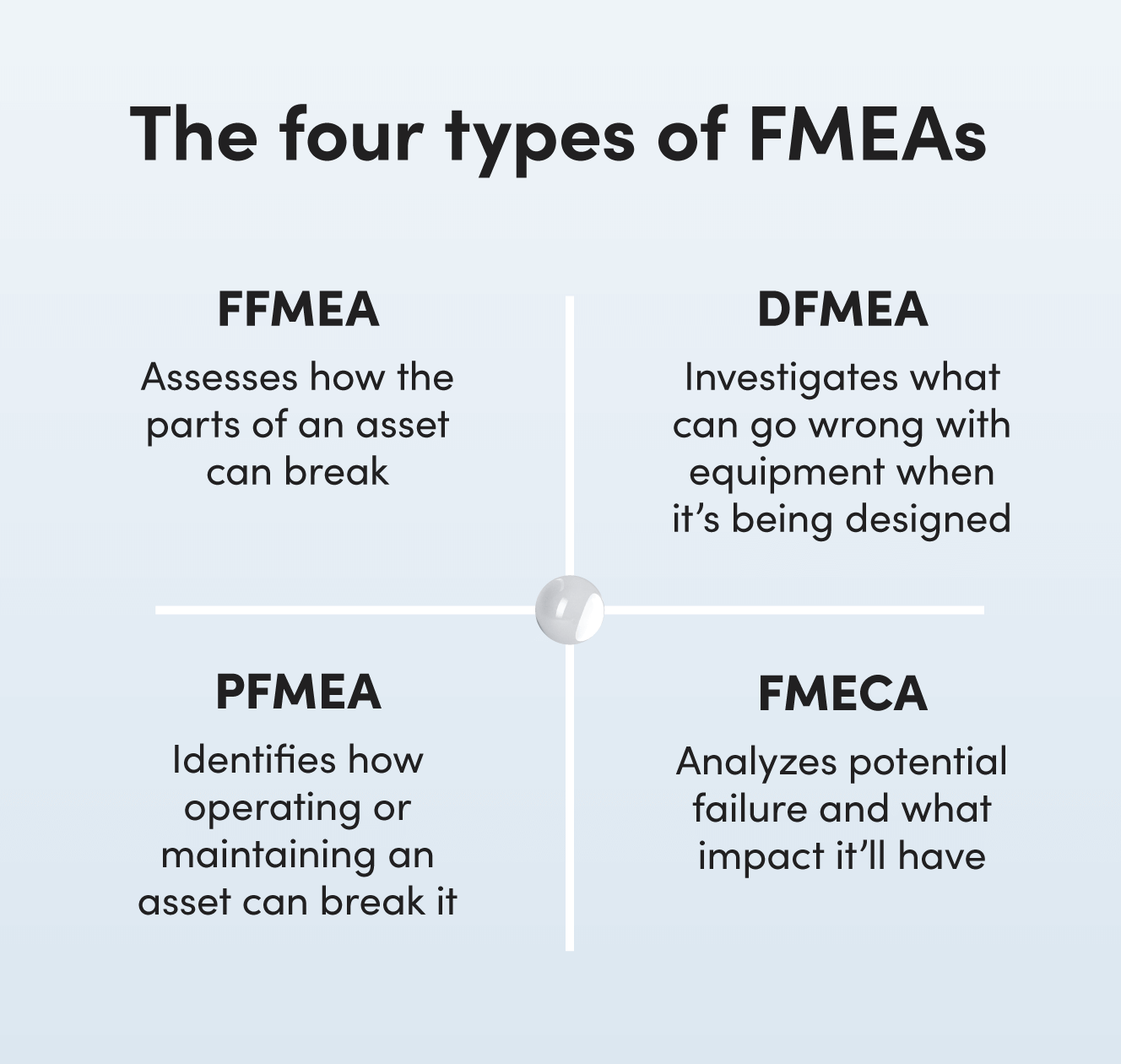
Quelle est la différence entre un mode de défaillance et un code de défaillance ?
Un mode de défaillance est une erreur ou un défaut qui provoque un dysfonctionnement d'un système. Un exemple de mode de défaillance sur un convoyeur de transfert à vitesse variable pourrait être un grippage de roulement. Un roulement cassé entraînera un ralentissement ou un arrêt du fonctionnement du convoyeur.
Un code de défaillance est un mode de défaillance représenté par une balise alphanumérique. Les codes de défaillance sont souvent utilisés dans les logiciels de GMAO comme moyen de transmettre rapidement des informations et de trier ou de signaler les défaillances. Les codes d'échec sont généralement pris en charge par trois informations contextuelles. Un exemple de code d'échec ressemble à ceci :
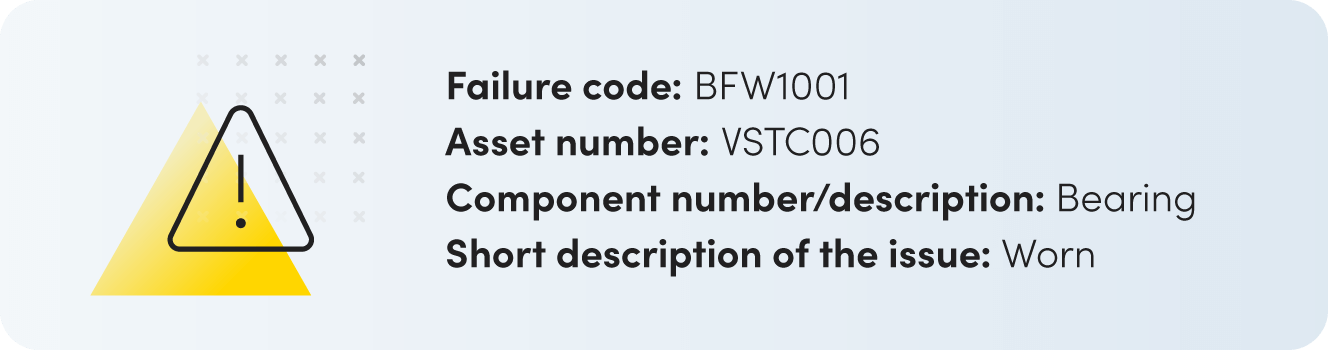
Quelle est la différence entre AMDEC et FRACAS ?
Une analyse du mode de défaillance et de ses effets décrit une défaillance possible, ses causes et son impact. C'est un processus qui répertorie les incidents futurs possibles et leurs causes probables. C'est une mesure proactive.
Un système de rapport de défaillance, d'analyse et d'action corrective (FRACAS) est un système de rapport en boucle fermée qui analyse les défaillances qui se sont déjà produites. Il examine les échecs passés pour découvrir pourquoi ils se sont produits et quel impact ils ont eu afin qu'ils puissent être évités à l'avenir. C'est une mesure réactive.
La création d'AMDEC pour la maintenance est un élément clé de la construction d'un FRACAS. En fait, c'est la première étape du processus. Une AMDEC est une référence pour l'échec ainsi que la performance de l'équipe et de l'équipement. Vous pouvez baser des décisions, telles que les rapports à créer ou les échecs à cibler, sur la base de ces informations.
Comment utiliser les AMDEC pour la maintenance
Il existe trois manières principales pour les équipes de maintenance d'utiliser une analyse des modes de défaillance et des effets :
- Pour créer un programme de maintenance préventive qui réduit la probabilité de défaillance des actifs et optimise les ressources
- Pour se préparer à la maintenance d'urgence afin que les actifs puissent être réparés rapidement et que les temps d'arrêt puissent être minimisés
- Pour prioriser la maintenance corrective et le backlog de maintenance
Utilisation des AMDEC pour établir un calendrier de maintenance préventive
Il existe trois façons d'utiliser les AMDEC pour exécuter un programme de maintenance préventive de classe mondiale :
- Créer de nouvelles tâches de maintenance préventive
- Prioriser la maintenance préventive
- Optimiser la maintenance préventive
Téléchargez ce modèle pour créer un programme de maintenance préventive
La première étape de la création d'un programme de maintenance préventive consiste à comprendre quelles pannes peuvent survenir et à quelle fréquence elles se produisent. Une AMDEC décrit ces informations. Par exemple, si un nouvel actif est en cours de conception, une AMDEC vous permet de déterminer quelles MP sont nécessaires pour éviter les modes de défaillance possibles et à quelle fréquence elles doivent être effectuées. Cela vous permettra de cartographier les entrées qui entrent dans la création de nouveaux MP, y compris qui sera affecté au travail, ce qui déclenchera le travail, ce que cela coûtera et combien de temps cela prendra.
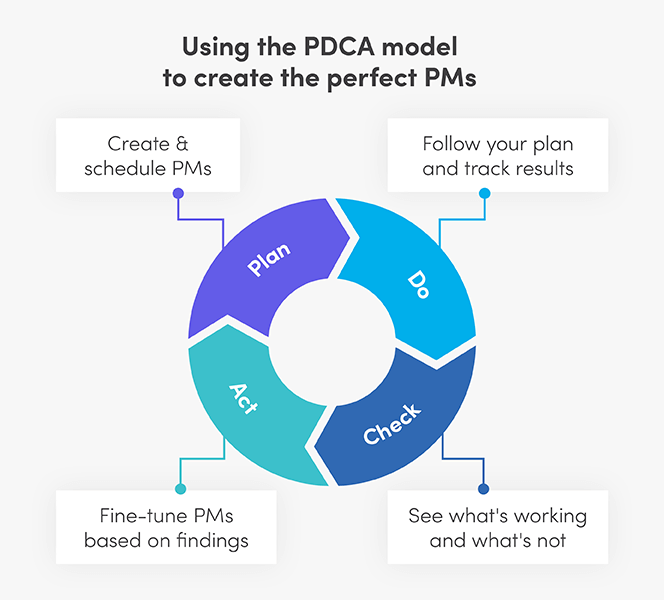
Le succès de votre programme de maintenance préventive dépend à la fois du nombre de pannes détectées et arrêtées et de l'impact de ces pannes. Si vous évitez 100 petites pannes, mais n'attrapez pas les cinq ou six pannes qui ont coûté des millions de dollars à votre entreprise, votre programme est défectueux. Une AMDEC dispose de toutes les informations dont vous avez besoin pour hiérarchiser les MP et cibler les pannes les plus probables et les plus perturbatrices.
Alors que les AMDEC vous donnent une base pour créer un programme de maintenance préventive, vos plans ne dureront pas éternellement. Votre opération change tout le temps. Votre horaire PM doit changer avec lui. L'utilisation des historiques des bons de travail et des réparations pour mettre à jour les AMDEC vous aide à optimiser votre emploi du temps et à suivre le rythme des autres changements. Par exemple, un mode de défaillance peut ne pas se produire aussi fréquemment que vous l'aviez prévu. Ces données peuvent vous amener à réduire la fréquence des MP destinées à éviter ce mode de défaillance. Vous pouvez ensuite affecter ces ressources à une autre tâche de maintenance.
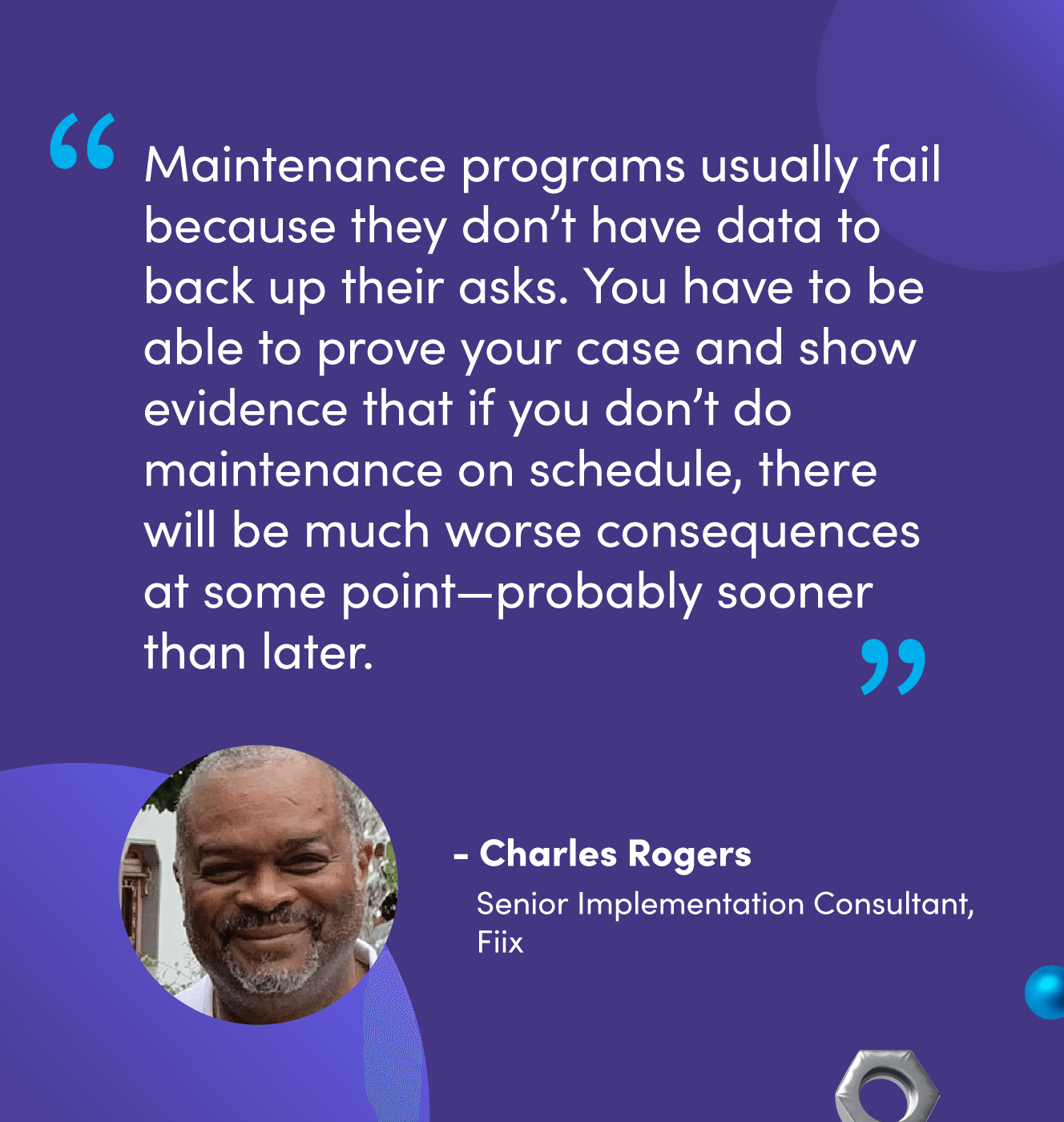
Utilisation des AMDEC pour préparer la maintenance d'urgence
Aucun entretien n'éliminera totalement les pannes. Le mieux que vous puissiez faire est de planifier les pannes à haut risque et à fort impact afin que votre équipe puisse les réparer en une heure au lieu de deux. Une AMDEC est un outil précieux pour mettre en place ces mesures d'urgence.
Commencez par examiner les échecs qui ont le plus d'impact et qui se produisent le plus souvent. Dans cette liste, sélectionnez les modes de défaillance difficiles à détecter. Vous vous retrouverez avec des modes de défaillance difficiles à repérer et qui causeront le plus gros gâchis. Élaborez un plan d'intervention d'urgence pour ces pannes.
Votre plan d'intervention d'urgence doit inclure toute information qui réduit les délais d'intervention et de réparation. Il doit également tenir compte de la santé et de la sécurité. Cela peut inclure les éléments suivants :
- Kit de pièces pour réduire le temps passé à récupérer les pièces de rechange critiques et les équipements de protection individuelle (télécharger un modèle de kit de pièces)
- Créer une liste de tâches détaillée ou des conseils de dépannage
- Joindre des diagrammes, des manuels, des photos et d'autres aides visuelles aux bons de travail
- Décrire une liste de techniciens ou d'entrepreneurs pouvant effectuer la réparation
- Établir un moyen de communiquer rapidement avec les techniciens, comme un logiciel de GMAO
Utilisation des AMDEC pour hiérarchiser la maintenance corrective et le backlog de maintenance
La détection précoce des défaillances est utile, mais cela ne signifie rien si vous n'avez pas de processus pour corriger ces défaillances rapidement et efficacement. Une AMDEC vous aide à construire ce processus.
La première étape consiste à identifier les modes de défaillance avec un score de gravité élevé (c'est-à-dire les actifs qui coûteront le plus cher à votre entreprise s'ils tombent en panne). Des mesures correctives doivent être prises sur cet équipement dès que possible. Cette liste vous permettra de créer du matériel de formation et des plans de réponse afin que chacun sache comment réagir en cas d'échec.
Vous pouvez utiliser une approche similaire lors de la priorisation du backlog de maintenance, à l'exception d'une étape supplémentaire. Après avoir classé le travail différé par gravité, examinez le travail restant par fréquence de défaillance. Comparez cela à la façon dont le travail est en retard. Si un mode de défaillance a un taux de fréquence supérieur au nombre d'inspections manquées, ce travail doit être prioritaire car la probabilité de défaillance est plus élevée.
Ce modèle gratuit vous aidera à hiérarchiser votre arriéré de maintenance
Comment créer une AMDEC
Le modèle AMDEC ci-dessous vous aidera à repérer les risques dans votre exploitation et à prendre des mesures pour les prévenir.
Téléchargez votre propre modèle AMDEC ici
Mais d'abord, voici comment obtenir des données pour votre AMDEC
De bonnes AMDEC dépendent de bonnes données. Sans données, vous construirez votre programme de maintenance sur des hypothèses et des hypothèses. Mais comment trouver les informations nécessaires pour une AMDEC ? Les trois sources ci-dessous vous donnent une excellente base :
- Consignes OEM :il s'agit de votre point de départ. Ces directives vous donnent une base pour remplir une AMDEC si vous n'avez pas d'autres données.
- Entretiens avec des opérateurs et des techniciens :tirez parti de l'expérience de ceux qui travaillent quotidiennement avec des équipements. Ils vous donneront des informations que vous ne trouverez nulle part ailleurs, par exemple si un composant a besoin de deux fois plus de lubrification que suggéré ou si la fréquence d'une panne a augmenté en raison de l'évolution des spécifications de la machine.
- Données des bons de travail :vos bons de travail révèlent les performances de l'équipement et constituent une excellente source d'informations pour peaufiner et améliorer vos AMDEC. Recherchez les pannes courantes, les mesures prises pour trouver et corriger la cause première, ce qui a retardé une réparation et la facilité avec laquelle il a été de détecter une panne.
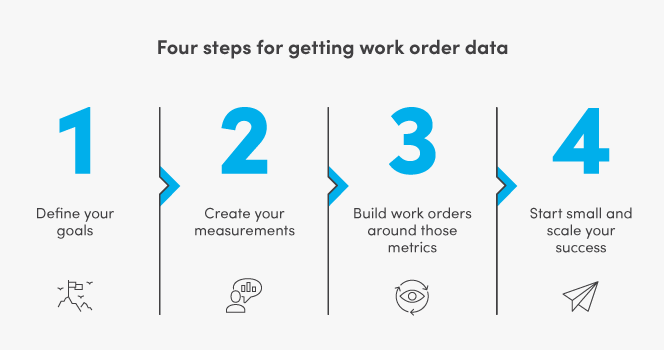
Aucune de ces sources ne fonctionne seule. Combinez-les pour obtenir une image complète du fonctionnement de votre équipement, de la façon dont il peut tomber en panne, de l'impact d'une panne et de ce qu'il faut faire pour y remédier.
Un modèle AMDEC
1. Identifier les composants de l'actif
Documentez chaque composant d'actif qui peut se casser ou se dégrader. Par exemple, les composants d'une ligne d'embouteillage peuvent inclure des boîtes de vitesses, des moteurs, des pignons, des roulements et des buses.
Commencez par votre équipement le plus critique et travaillez à partir de là. C'est le moment idéal pour créer des conventions de nommage claires et une hiérarchie d'actifs si vous ne les avez pas déjà.
2. Identifier les modes de défaillance potentiels
Il est temps d'identifier comment ces composants peuvent échouer. Si un seul composant a plusieurs modes de défaillance, répertoriez chaque mode de défaillance en conséquence. Par exemple, les modes de défaillance d'un roulement peuvent inclure un désalignement, de la corrosion ou une contamination.
3. Lister les effets potentiels d'un échec
Décrivez le résultat d'une défaillance et son impact sur la production et la sécurité du personnel. Par exemple, un roulement mal aligné arrêtera une ligne jusqu'à ce qu'elle puisse être remplacée (environ trois heures), avec une perte potentielle de 1 800 unités.
4. Score de gravité
Il s'agit d'une mesure de l'impact d'une défaillance sur la production et la sécurité. Il est noté sur une échelle de 1 à 10, 1 étant un événement à faible impact et 10 un événement à fort impact. Tenir compte de l'état de l'actif lors de la notation. Par exemple, une voiture dont le pneu éclate à basse vitesse connaîtra des problèmes de direction mineurs, mais une éclatement à grande vitesse est bien plus dangereux.
Commencez à calculer le score de gravité d'un actif avec ce modèle d'analyse de criticité
5. Lister les causes potentielles
Énumérez toutes les raisons possibles pour lesquelles un échec peut s'être produit. Aller au-delà d'une cause directe. Par exemple, un roulement corrodé peut se produire parce que les fournitures ont été mal étiquetées ou que les instructions ne sont pas claires, ce qui entraîne une mauvaise lubrification.
Allez au fond des échecs avec ce modèle d'analyse des causes profondes pratique (et gratuit !)
6. Score de fréquence attendu
Il s'agit d'une mesure de la fréquence d'un mode de défaillance. Il est noté sur une échelle de 1 à 10, où 1 représente un événement qui se produit rarement et 10 représente un événement qui se produit très fréquemment.
7. Répertorier les contrôles de processus actuels
Documentez toutes les mesures en place pour prévenir ou détecter une défaillance. Les contrôles de processus peuvent inclure des inspections de maintenance préventive hebdomadaires, des remplacements de pièces mensuels et l'utilisation de capteurs pour détecter des niveaux de vibration dangereusement élevés.
8. Score de détection
Ce nombre détermine à quel point il est facile de détecter un problème avant qu'il ne provoque un échec total. Il est noté sur une échelle de 1 à 10. Un score de 1 est attribué à un événement qui ne peut jamais être détecté. Un score de 10 est attribué à un événement qui peut être détecté presque à chaque fois. Par exemple, un pneu crevé peut parfois être détecté à ses débuts, il obtiendrait donc un 5. Un pare-brise ébréché est souvent causé par des événements imprévisibles, ce qui signifie qu'il est difficile à détecter et obtiendrait un 9.
9. Numéro de priorité du risque
Le numéro de priorité du risque calcule les modes de défaillance qui ont l'impact le plus élevé et sont les plus évitables. Pour trouver le RPN, multipliez les scores de gravité, de fréquence et de détection. Par exemple, si un mode de défaillance a un score de gravité de 8, un score de fréquence de 5 et un score de détection de 10, le RPN serait de 400. Plus le nombre est élevé, plus de ressources doivent être consacrées à la prévention de cette défaillance.
10. Déterminer l'action recommandée
Établissez un plan pour réduire la probabilité d'échec ou augmenter les chances de détection précoce. Cela peut inclure l'augmentation de la fréquence des MP sur un composant ou l'investissement dans un équipement de surveillance de l'état.
Comment gérer les AMDEC
Les AMDEC sont des documents vivants qui doivent être régulièrement revus et mis à jour. Voici quelques événements qui pourraient déclencher un examen d'une AMDEC :
- Un nouvel élément est conçu ou installé dans votre établissement
- Un nouveau technicien ou opérateur rejoint l'équipe
- Une modification est apportée au mode de fonctionnement d'une machine (c'est-à-dire qu'elle est exécutée plus souvent ou que les spécifications changent)
- Un mode de défaillance se produit plus fréquemment
- Une nouvelle technologie est mise en œuvre pour vous aider à détecter ou à prévenir plus facilement les pannes
- Vous trouvez un nouveau mode de défaillance ou la raison d'une défaillance existante
- L'impact des changements de défaillance (c'est-à-dire qu'un nouveau produit utilisant un matériau plus cher est en cours de production)
Le personnel de maintenance et d'exploitation doit être impliqué dans la modification et l'ajout d'une analyse des modes de défaillance et des effets. La diversité des perspectives et des expériences avec les équipements permet d'éviter les lacunes dans vos AMDEC.
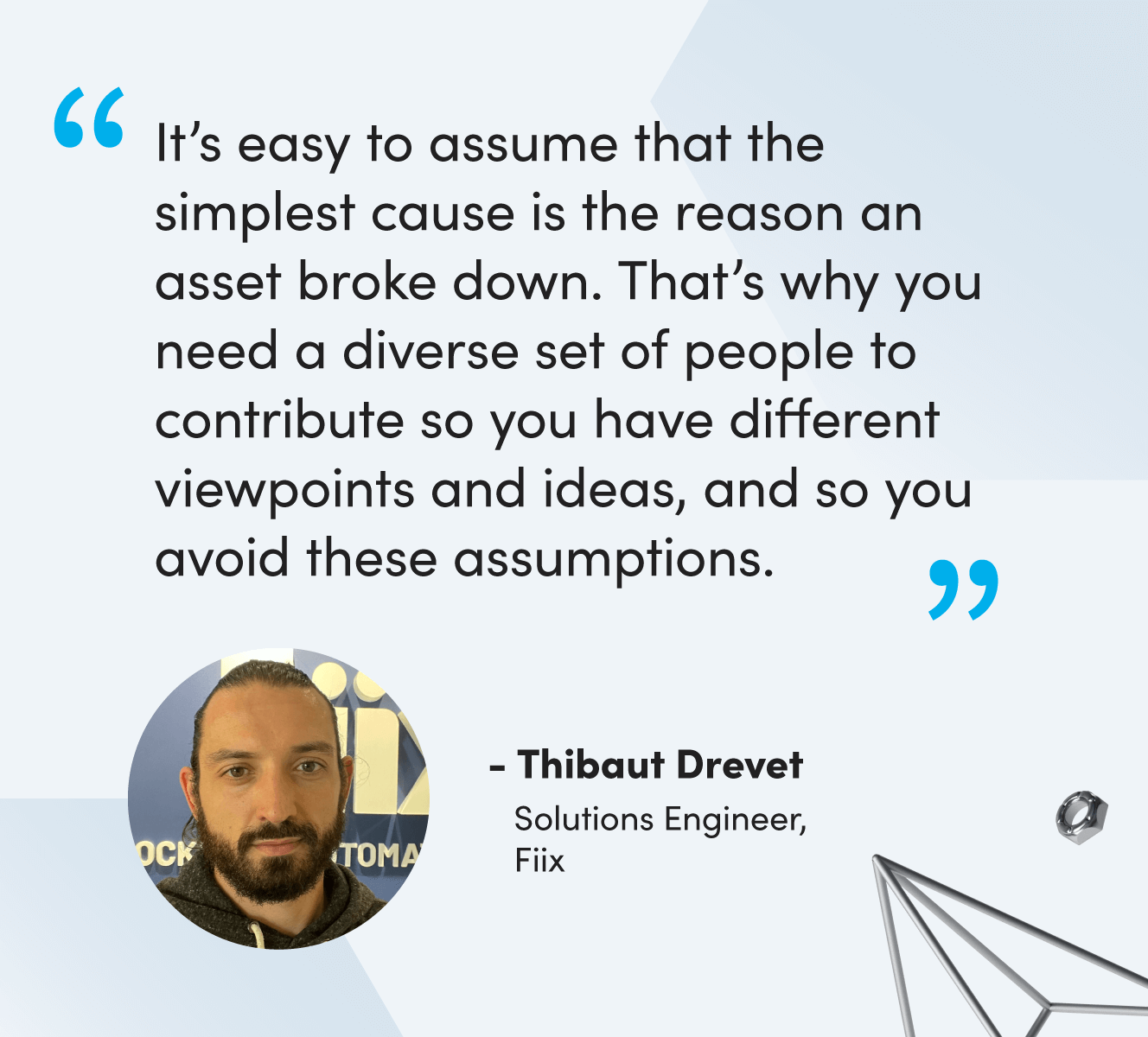
Les AMDEC sont un investissement à long terme dans la réussite
Une analyse des modes de défaillance et des effets n'est pas une solution de fortune ou un outil de dépannage. Il s'agit d'une activité continue dans le but de prévenir l'échec lorsque cela est possible et d'atténuer ses effets lorsqu'il ne l'est pas. C'est une ressource de planification et une protection contre les pertes financières et les risques de sécurité.
Bien que la création d'AMDEC implique un investissement de temps considérable, cela vous rapportera à long terme en vous aidant à planifier à l'avance, à empêcher la maintenance réactive et à suivre le succès de l'équipe.
Entretien et réparation d'équipement
- Comment conserver la maintenance en mode proactif
- Guide rapide sur le développement et l'exécution de PM
- Meilleurs performances en maintenance et fiabilité
- Les détails comptent pour la maintenance et la fiabilité
- Garder la maintenance simple :utilisez vos sens et votre sensibilité
- 5 causes de panne d'équipement (et ce que vous pouvez faire pour l'éviter)
- Le temps, c'est de l'argent :astuces pour utiliser un logiciel de maintenance pour gagner du temps et dépenser plus efficacement
- Simplifier les rapports d'échec dans la maintenance
- Guide d'entretien et de pièces des remontées mécaniques