5 causes de panne d'équipement (et ce que vous pouvez faire pour l'éviter)
Cet article a été initialement écrit en tant que blog invité par Nicole Pontius de Camcode. Edité et mis à jour par l'équipe Fiix en juin 2019.
- 5 causes courantes de panne d'équipement
- Cause 1 :Opération incorrecte
- Cause 2 :Ne pas effectuer la maintenance préventive
- Cause 3 :Trop de maintenance préventive
- Cause 4 : échec de la surveillance continue de l'équipement
- Cause 5 :Mauvaise (ou pas !) culture de fiabilité
- Le résultat final
Une panne d'équipement se produit. L'impact de celui-ci peut aller de facilement résolu avec des pertes minimales à catastrophique, en fonction de facteurs tels que les coûts de réparation, le temps d'arrêt total, les implications pour la santé et la sécurité, et l'impact sur la production et la prestation de services.
Il existe plusieurs raisons courantes pour lesquelles l'équipement peut tomber en panne, et comprendre pourquoi votre équipement peut tomber en panne est votre première ligne de défense contre les conséquences graves d'un temps d'arrêt imprévu.
Utilisez ces sept secrets pour réduire les temps d'arrêt et vaincre l'échec
Vaincre la défaillance de l'équipement
5 causes courantes de panne d'équipement
Cause n°1 :Opération incorrecte
Il y a tout un tas de personnes qui peuvent se trouver dans et autour de l'équipement quotidiennement et qui pourraient avoir un impact significatif sur son état de fonctionnement général.
Les opérateurs d'équipement sont l'un de ces groupes. Ils reçoivent généralement une formation approfondie sur les procédures d'exploitation appropriées, le dépannage de base et les meilleures pratiques pour une utilisation sûre de l'équipement en rapport avec les machines avec lesquelles ils travailleront. Cependant, un jour pourrait arriver où un opérateur finira par travailler sur une machine pour laquelle il n'a pas été suffisamment formé. Parfois, cette situation survient à la suite d'un manque de personnel ou d'absences imprévues. D'autres fois, des urgences surviennent et nécessitent une remédiation rapide avec du personnel disponible qui n'a pas nécessairement le niveau d'expertise que vos opérateurs les plus expérimentés ont.
Une solution à ces problèmes est de s'assurer que vous avez suffisamment d'opérateurs formés pour permettre une certaine flexibilité et un plan d'urgence pour les urgences de pénurie de personnel. Si possible, tous vos opérateurs doivent avoir une formation sur chaque pièce d'équipement, même les actifs avec lesquels ils ne travaillent généralement pas.
Plus important encore, ne permettez jamais à un opérateur d'utiliser un équipement pour lequel il n'est pas qualifié. Non seulement cela contribuera à réduire les erreurs opérationnelles, mais dans certains secteurs, il est impératif de se conformer à la réglementation. L'Administration de la sécurité et de la santé au travail (OSHA) établit des règlements pour les exigences de formation des opérateurs pour certains types d'équipement et pour la sécurité au travail en général. C'est à vous, cependant, de connaître les réglementations applicables à votre secteur et de vous assurer que vous avez mis en place des procédures de conformité adéquates.
Cause n°2 :Ne pas effectuer la maintenance préventive
La plupart des équipements nécessitent un entretien régulier pour des performances optimales, mais trop souvent, la maintenance préventive est la première tâche à accomplir lorsque vous êtes à court de personnel et débordé. Il est facile d'écarter l'entretien régulier lorsque les choses semblent bien fonctionner, et de nombreuses entreprises partent du principe que les travailleurs expérimentés identifieront les problèmes imminents avant que l'équipement ne tombe complètement en panne.
Cela dit, bon nombre des signes subtils de ralentissement des performances ou des premiers stades d'échec ne sont pas facilement détectables et passent souvent inaperçus. Dans d'autres cas, les entreprises manquent simplement de méthodes de planification efficaces pour garantir que la maintenance continue est effectuée. Le suivi des équipements et des machines avec des étiquettes d'actifs peut aider à maintenir les calendriers de maintenance sur la bonne voie et à faire fonctionner les équipements avec une efficacité opérationnelle maximale.
La maintenance préventive est une fonction permanente qui ne devrait jamais être abandonnée. Prendre soin de votre équipement avec des mises au point régulières prolongera la durée de vie de votre équipement, vous donnant finalement plus pour chaque dollar. De plus, la maintenance préventive peut identifier les petits problèmes avec des solutions peu coûteuses avant qu'ils ne deviennent des pannes majeures et coûteuses. Lorsque vous utilisez des stratégies efficaces de contrôle des stocks pour vous assurer que vous disposez des bonnes pièces de rechange pour les tâches de maintenance et les dysfonctionnements les plus courants, les temps d'arrêt pour la maintenance et les réparations de routine sont minimes. En fait, le département américain de l'Énergie estime que la maintenance préventive entraîne :
- Jusqu'à 30 % de réduction des coûts d'énergie et de maintenance
- 35 % à 45 % de pannes en moins
- Réduction des temps d'arrêt jusqu'à 75 %
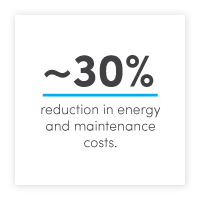
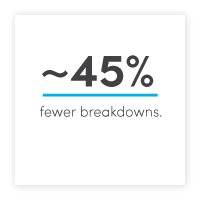
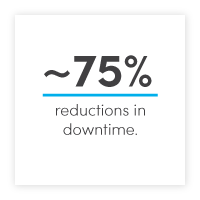
Arrêtez de combattre les incendies toute la journée avec ce modèle gratuit de calendrier de maintenance préventive
Cause n°3 :trop de maintenance préventive
"C'est sûrement une erreur", pensez-vous. « Vous venez de me dire que NE PAS faire de maintenance préventive entraînera des problèmes. » C'est vrai, il y a un peu une situation de Boucle d'or en ce qui concerne la maintenance préventive. Pas assez peut être problématique pour les raisons que nous avons décrites ci-dessus, mais trop est également une cause majeure de préoccupation.
Nous avons déjà écrit à ce sujet en profondeur, alors consultez ce blog si vous souhaitez approfondir le concept des pannes après maintenance. Mais voici les notes de Coles :chaque fois que vous entrez dans une machine pour l'entretenir, vous exposez cette pièce d'équipement à tout un ensemble de risques, et avec le temps, ces risques peuvent s'aggraver et conduire à une panne.
Pas assez de MP
Les signes d'échec précoce sont manqués
Les calendriers de maintenance souffrent
Efficacité réduite de l'équipement
La durée de vie des actifs diminue
Pannes et augmentation des temps d'arrêt
Les coûts montent en flèche
Juste assez de MP
Les coûts sont maîtrisés
La livraison juste à temps est atteinte
Les temps d'arrêt sont réduits
L'efficacité des techniciens est renforcée
La sécurité s'améliore
La productivité des actifs critiques est optimisée
Trop de MP
Les dépenses excessives augmentent
L'usure des actifs monte en flèche
Le temps des techniciens est perdu
L'inventaire inutile est utilisé
Des informations inexactes sont collectées
Assurez-vous de ne pas faire trop de MP avec ce modèle de journal de maintenance
Pensez-y en termes de chirurgie :un triple pontage est une opération qui sauve des vies. Mais vous ne voulez pas subir régulièrement une opération à cœur ouvert simplement parce que quelques années se sont écoulées ou que votre cœur a battu plusieurs millions de fois. Mais si souvent, c'est exactement ainsi que nous abordons la maintenance préventive. Cela se fait selon un calendrier prédéfini (généralement basé sur le temps ou l'utilisation) sans tenir compte de l'état de fonctionnement réel de l'actif.
Ce qui nous amène à…
Cause 4 : échec de la surveillance continue de l'équipement
Alors, comment trouver le bon équilibre entre maintenance préventive ? Le remède ici est simple dans son concept mais un peu plus complexe dans son exécution :la maintenance conditionnelle. Il s'agit d'une maintenance effectuée en fonction de l'état de fonctionnement d'une pièce d'équipement, au lieu d'un simple programme « réglez-le et oubliez-le ». Il prend beaucoup de choses en compte, de l'historique de l'équipement des informations du fabricant aux données en temps réel telles que l'analyse des vibrations.
La surveillance continue s'appuie sur les données des capteurs pour établir une base de référence pour le bon état de l'équipement afin de détecter les changements subtils, qui peuvent être utilisés pour prédire les pannes et les pannes. Cela laisse plus de temps pour la planification d'urgence et la planification des temps d'arrêt afin de minimiser les interruptions de production. Ce type de surveillance et les données collectées au cours du processus peuvent aider les entreprises à identifier les causes d'un stress accru sur les machines et à ajuster les charges de travail et les calendriers pour réduire la charge sur l'équipement en montrant des indicateurs précoces d'une défaillance imminente.
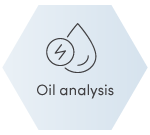
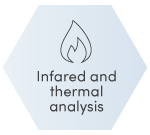
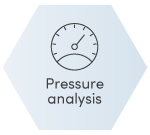
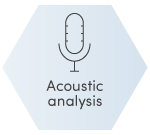
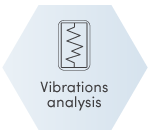
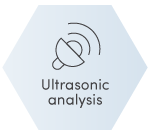
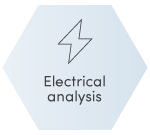
Préparez-vous à chaque panne de vos actifs critiques avec ce modèle AMDEC
Le hic, c'est que c'est en fait très difficile à faire si vous gérez la maintenance avec un stylo et du papier ou Excel. Si c'est là que vous souhaitez que vos opérations de maintenance se déroulent, il est peut-être temps d'envisager de passer à une solution de maintenance numérique.
Quand utiliser la surveillance basée sur les conditions
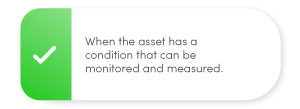
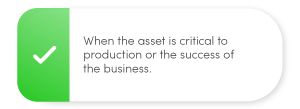
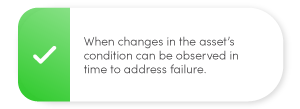
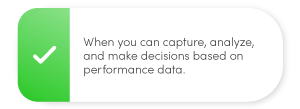
Cause n°5 :Culture de fiabilité mauvaise (ou pas !)
Tout le monde a été là - une pression importante du sommet signifie qu'il n'y a pas une seconde à perdre si vous avez le moindre espoir d'atteindre vos objectifs de production. Dans ces circonstances, il peut être si tentant (et si facile) pour un opérateur ou un préposé à l'entretien de remarquer que quelque chose ne fonctionne pas à 100 %, d'appliquer une solution de fortune dessus et de dire :« Je trouverai ça quand les choses se calmeront. vers le bas". Le problème est que, de manière réaliste, les choses ne se calment jamais au point où vous aurez le temps de revoir ce travail. Ce qui signifie que la solution de pansement devient une solution semi-permanente jusqu'à ce qu'elle cesse de fonctionner et devienne un échec à part entière.
Boeing en est un très bon exemple. Vous connaissez probablement les deux accidents mortels impliquant l'avion 737 Max de l'entreprise, qui ont soulevé la question de savoir si la précipitation de Boeing pour mettre l'avion en production a conduit l'entreprise à prendre des risques pour la sécurité qui ont finalement abouti aux accidents.
Mais l'histoire la plus discrète concerne un autre modèle d'avion, le 787 Dreamliner. Plusieurs dénonciateurs se sont manifestés pour tirer la sonnette d'alarme au sujet des Dreamliners, qui ont été fabriqués en 2009 dans une nouvelle usine près de Charleston, en Caroline du Sud. Dès le début, la production bâclée était un problème qui a été constamment balayé sous le tapis en faveur de calendriers de production agressifs.
Si vous voulez l'histoire complète, consultez l'article complet du New York Times ici (ou le podcast connexe du Daily si vous êtes plutôt une personne audio). Mais pour faire court, les problèmes de Boeing sont un très bon exemple de pression concurrentielle aux plus hauts niveaux d'une entreprise ayant un effet d'entraînement tout au long de la chaîne de commandement, jusqu'à l'usine. Une mauvaise culture au sommet crée une mentalité « faites-le rapidement » qui peut entraîner des oublis dévastateurs, des solutions de fortune et des erreurs.
Et si la mauvaise culture était à l'origine de la panne de votre équipement ? Que pouvez-vous faire? Nous avons abordé le sujet de la mise en place d'une culture axée sur la fiabilité, alors allez-y et consultez l'un (ou tous !) De ces éléments pour vous donner une base solide en matière de fiabilité.
Résumé : des opérateurs formés, un calendrier de PM solide et une concentration sur la culture de la fiabilité sont vos billets pour un avenir sans panne (ou au moins moins de pannes)
L'équipement peut être imprévisible et une panne survient. Les gens font des erreurs, les pièces vieillissent et parfois la maintenance préventive n'est qu'une chose de trop dans une journée déjà bien remplie. Mais en assurant une formation adéquate des opérateurs, en exécutant une maintenance préventive ou basée sur l'état au bon moment et en travaillant vers une meilleure culture globale, vous aurez une bien meilleure chance de maintenir votre équipement en parfait état de fonctionnement.
Entretien et réparation d'équipement
- Maintenance autonome :qu'est-ce que c'est et pourquoi c'est important
- Qu'est-ce que la fiabilité et la gestion des actifs ?
- La mort du service de maintenance et ce que nous pouvons y faire
- Que pouvez-vous faire pour améliorer la maintenance et la fiabilité ?
- Principales causes de panne de machine et comment les prévenir
- Qu'est-ce qu'une chute de pression et comment la prévenir ?
- 4 conseils de maintenance pour prolonger la durée de vie et le retour sur investissement de l'équipement
- Qu'est-ce que l'exécution jusqu'à l'échec ? RTF est-il toujours mauvais ?
- Maintenance des installations et industrielle