Types de moulage dans la fabrication
Dans cet article, nous découvrirons les types de moulage utilisés dans les industries manufacturières. Le moulage est un processus de fabrication majeur qui est principalement utilisé dans les industries lourdes. La plupart des composants tels que le carter extérieur de la turbine, le lit du tour, le carter de soupape, les aubes de turbine hydraulique, la roue Pelton, le coureur Francis et de nombreuses autres pièces des principales machines sont fabriqués par coulée. Le produit coulé a une faible résistance par rapport au forgeage, mais toutes les pièces difficiles peuvent être coulées par cette technologie.
Types de diffusion :
Le moulage est largement utilisé dans de nombreuses formes et matériaux différents. Il existe différentes méthodes de moulage disponibles qui sont utilisées pour différentes formes et matériaux. Le casting a les types suivants.
Moulage au sable :
Il est largement utilisé pour la coulée de différents processus. Le sable est facilement disponible et possède une propriété de réfectoire élevée, il est donc utilisé dans la coulée. Cela se fait en suivant les étapes.
- La conception est réalisée à l'aide d'un logiciel ou manuellement.
- Un motif en bois est créé dans la boutique de motifs. Généralement, les modèles sont divisés en deux moitiés et peuvent être augmentés en fonction de la complexité.
- Le motif est placé dans le flacon et un mélange de sable et d'argile avec de l'eau y est versé. Le système de glissière, de colonne montante, de noyau et de porte y est également intégré.
- Lorsque le moule devient dur, le motif est retiré du moule et le métal en fusion y est versé.
- Le métal est autorisé à se solidifier dans le moulage.
- Après la solidification, le moulage est retiré du moulage et envoyé à l'atelier d'usinage pour usinage.
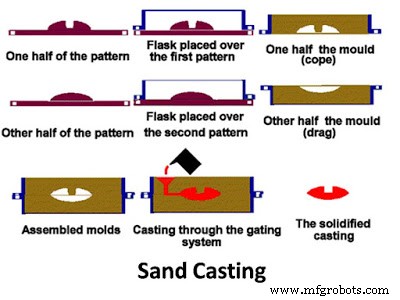
Mise en forme de coque :
C'est une autre méthode de coulée et utilisée pour couler des sections minces comme une aube de turbine, etc. Cette coulée est différente de la coulée au sable. Un motif métallique est utilisé dans ce type de moulage. Il consiste à suivre les étapes.
- Un motif métallique est d'abord coulé. Le métal utilisé pour la coulée est généralement de l'aluminium ou de la fonte
- Les motifs sont chauffés jusqu'à 250 degrés et mis dans un flacon.
- Le flacon est rempli d'un mélange de sable et de résine. La résine se solidifie immédiatement après le contact avec le motif chauffé.
- Après le sable, solidifiez le motif et retirez le sable supplémentaire. Maintenant, une coquille de cavité est créée. Cette coquille est encore chauffée dans le brûleur qui permet une bonne liaison.
- Le métal est coulé dans la coque et permet de se solidifier.
- Après la solidification, la fonte est retirée de la coque et envoyée pour usinage.
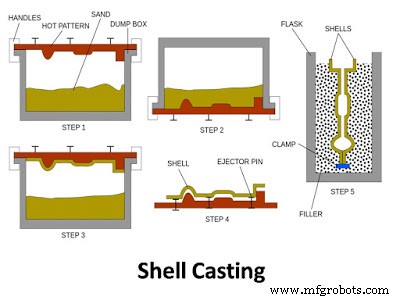
Casting d'investissement :
Dans ce type de processus, un modèle de cire est utilisé. Le motif est d'abord créé par de la cire trempée dans un matériau de réfectoire. Ce matériau de réfectoire fait un doit en dehors du modèle de cire. Après cela, le moule est chauffé, ce qui permet le cirage du moule. Maintenant, le métal en fusion est versé dans la cavité formée par celui-ci et permet de se solidifier. Le moulage est retiré après solidification appropriée du moulage et envoyé pour usinage. Le principal avantage de ce procédé est qu'il permet d'obtenir une précision et une finition de surface très élevées. Il est utilisé pour la production de formes complexes et de lots.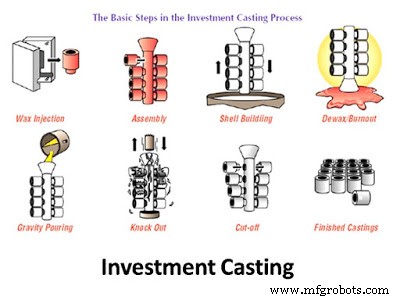
Moulage en plâtre :
Cette méthode utilise un moule en plâtre pour la coulée. Le premier moule en plâtre est créé à l'aide de modèles. Après enlèvement du motif, le moule en plâtre laisse sécher dans une étuve. Après séchage, le métal en fusion y est versé et permet la solidification. Après solidification complète, la fonte est poncée à l'atelier d'usinage. Le zinc et l'aluminium sont principalement utilisés comme métal en fusion. Ce moulage est utilisé pour créer un prototype.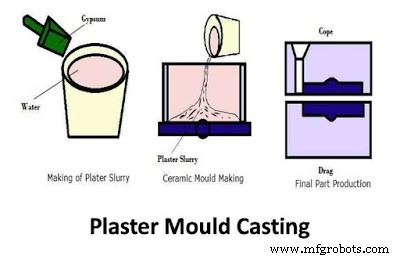
Moulage en céramique
La coulée de moules en céramique est la même que la coulée de précision mais elle n'utilise pas de modèle de cire. La suspension de céramique et de liant liquide est versée sur un motif qui se solidifie facilement. Aucun modèle de cire n'est utilisé, il n'y a donc aucune limitation de taille de moulage. Ce type de moulage est principalement utilisé pour couler des composants lourds tels que des corps de vannes, des équipements militaires, etc.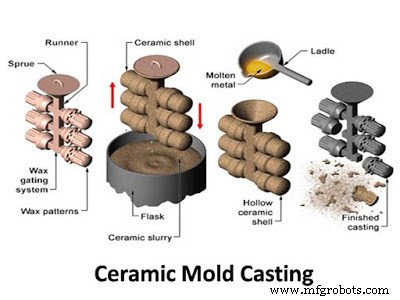
Moulage sous pression :
Cette coulée est principalement utilisée pour couler de l'aluminium, du plomb, etc. Dans cette coulée, un métal liquide est pompé à haute pression dans une matrice métallique et permet de se solidifier. Le métal est autorisé à s'y solidifier et à sortir après solidification. La matrice est à nouveau utilisée pour la coulée suivante. Il convient bien à la production par lots de coulée de métal à bas point de fusion. Il ne convient pas aux métaux à haute température de fusion. Le coût de l'outillage est également élevé.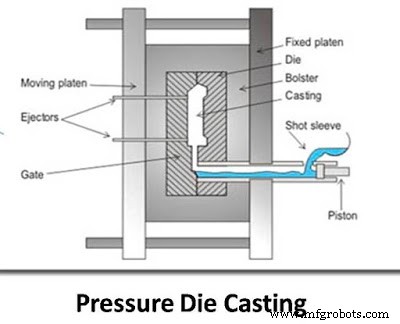
Coulée centrifuge :
C'est l'un des procédés de coulée les plus appropriés pour couler des composants cylindriques symétriques. Dans ce processus, un métal liquide est versé au centre d'une matrice rotative. La filière tourne et une force centrifuge agit sur le métal en fusion qui le force à se rapprocher de la circonférence. Il est utilisé pour créer une forme creuse. Les impuretés légères s'entassent près du centre et sont éliminées à la machine. Ce processus élimine l'utilisation d'un noyau et d'un système de porte. Ce type de moulage est utilisé pour fabriquer des tuyaux, etc.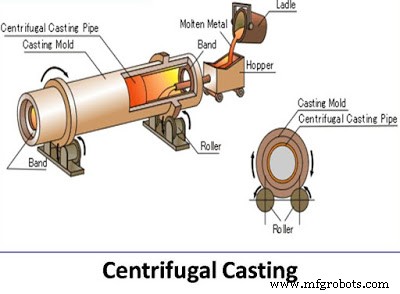
Diffusion continue :
Il s'agit d'un processus de coulée différent qui est utilisé pour créer une coulée continue. Dans ce processus, nous n'utilisons pas de moule ou de copeaux et de traînée. C'est différent dans le principe. Dans ce processus, le métal en fusion est versé dans une poubelle qui est reliée à un tuyau en cuivre. Le tuyau en cuivre est entouré d'eau de refroidissement. Le métal est directement ou immédiatement refroidi après avoir traversé le tuyau. Le produit coulé sort de l'autre côté. Ce processus fonctionne en continu et le métal en fusion y est versé en continu. Il est utilisé pour créer un bloc simple de forme carrée ou autre qui est ensuite utilisé pour le laminage ou un autre processus.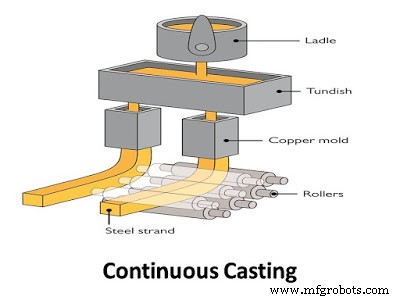
Ce sont tous les principaux types de casting. Si vous avez un doute concernant cet article, demandez en commentant. Si vous aimez cet article, n’oubliez pas de le partager sur les réseaux sociaux. Abonnez-vous à notre site Web pour plus d'articles informatifs. Merci de l'avoir lu.
Processus de fabrication
- Types de colorants utilisés dans les textiles
- 6 types courants de rivets utilisés dans l'industrie manufacturière
- 10 différents types de modèles de moulage
- Types de marteaux
- Types d'équipement de moulage au sable
- Types d'alliages de titane utilisés dans le moulage de précision
- Types de méthodes de contrôle qualité utilisées pour les pièces coulées au sable
- Quels sont les 4 types de processus de fabrication ?
- Avantages des fournisseurs de fonte en tant que processus de fabrication