Les 4 plus grosses erreurs de conception pour le moulage par injection
De nombreuses entreprises se tournent vers les services de moulage par injection pour produire de manière rentable un volume élevé de pièces identiques. Le moulage par injection de plastique consiste à faire fondre des thermoplastiques dans un baril chauffé avant d'injecter le matériau fondu dans un moule métallique durable et précis via une buse sous pression. Une fois que le matériau a refroidi et durci, la pièce est éjectée et le processus est répété. Les entreprises utilisent ce processus de fabrication pour tout produire, des boîtiers électroniques aux bouteilles d'eau.
Le moulage par injection est un processus complexe, et une seule erreur peut entraîner des défauts esthétiques, compromettre l'intégrité du produit et entraîner des refontes coûteuses. La bonne nouvelle est que la plupart de ces problèmes sont évitables tant que vous suivez les meilleures pratiques de conception. Voici 4 des erreurs les plus courantes auxquelles vous devez faire attention lorsque vous concevez une pièce pour le moulage par injection.
4 des erreurs de moulage par injection les plus courantes et comment les résoudre
1. Concevoir avec des contre-dépouilles
Une contre-dépouille est une surface en retrait, une saillie, une rainure, un porte-à-faux, un filetage, un encliquetage ou toute autre caractéristique qui empêche l'éjection d'une pièce de son moule. Les contre-dépouilles peuvent entraîner une augmentation des coûts de fabrication, de la complexité des pièces et des exigences de maintenance des moules. Il est donc préférable d'éliminer toute contre-dépouille potentielle dans la mesure du possible.
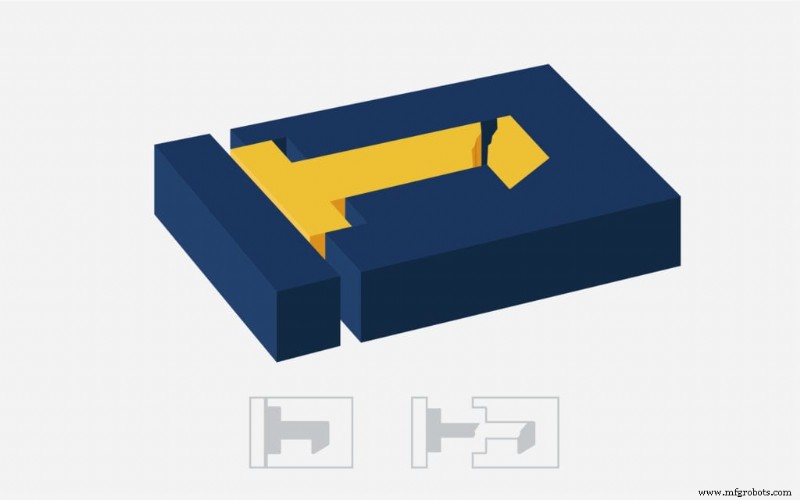
Si vous avez une contre-dépouille essentielle à la conception de votre pièce, il existe plusieurs façons d'améliorer l'éjection de la pièce. Réorienter les éléments problématiques afin qu'ils soient parallèles à la ligne de tracé est une solution rentable. Cela permet à la pièce de s'éjecter sans subir de dommages, éliminant ainsi la contre-dépouille. Si vous avez des pièces avec des contre-dépouilles internes ou des faces sans angles de dépouille, vous pouvez également utiliser des élévateurs pour faciliter le processus d'éjection. Vous pourrez peut-être former des fonctions de contre-dépouille en concevant intelligemment des trous et des fentes dans la pièce, ce que nos ingénieurs Fast Radius peuvent vous guider.
2. Avoir une épaisseur de paroi non uniforme
Le fait d'avoir une épaisseur de paroi uniforme aide le plastique fondu à s'écouler à travers la cavité du moule dans une seule direction, permettant au matériau de remplir la cavité plus précisément. Cependant, étant donné que les parois plus minces refroidissent plus rapidement que les parois plus épaisses, les variations d'épaisseur de paroi peuvent provoquer un affaissement, une déformation, des tirs courts, etc.
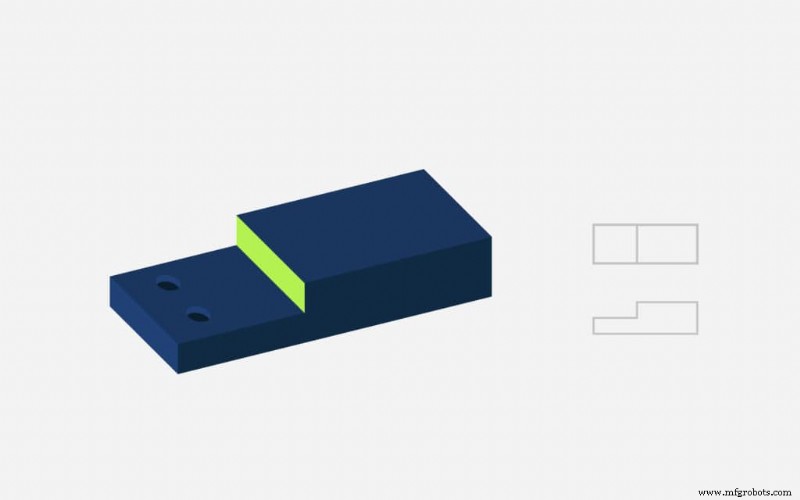
Pour éviter ces problèmes et vous assurer que toutes les zones de votre pièce refroidissent au même rythme, utilisez des épaisseurs de paroi constantes. Les épaisseurs de paroi comprises entre 1,2 mm et 3 mm sont les meilleures dans la plupart des cas. Si vous devez avoir des murs d'épaisseurs variables, vous devez :
- Faites en sorte que la transition entre les sections minces et épaisses soit aussi progressive que possible — La meilleure pratique de conception consiste à utiliser des noyaux et des nervures au lieu de modifier l'épaisseur de paroi ou de minimiser les modifications lorsqu'elles sont nécessaires.
- Utiliser la bonne épaisseur de nervure et de bossage — Les nervures et les bossages ne doivent pas dépasser 40 à 80 % de l'épaisseur de la paroi de base avec un rayon de base de 25 à 40 % de l'épaisseur de la paroi.
- Retirez le plastique des zones les plus épaisses - C'est ce qu'on appelle le carottage, et cela peut aider à garder vos sections de mur uniformes.
3. Oublier les angles de dépouille
L'ajout d'un courant d'air, une légère conicité à chaque surface verticale de la pièce, est essentiel pour une éjection en douceur. Une pièce conçue sans dépouille peut coller au moule, et un manque de dépouille peut également provoquer des traînées disgracieuses si les parois verticales de la pièce frottent contre le moule métallique lors de l'éjection. En ajoutant une légère conicité, vous pouvez protéger votre pièce contre les frottements, assurer une finition uniforme et réduire l'usure, la déchirure et la déformation lors de l'éjection.
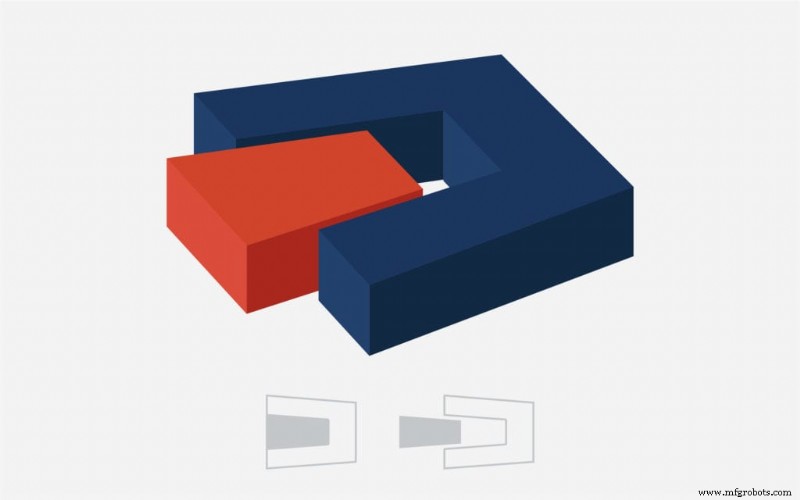
Les degrés d'angle de dépouille dépendent de plusieurs facteurs, de l'épaisseur de la paroi à la texture de la surface. Vous devrez tenir compte du taux de retrait du matériau, de la fonction d'utilisation finale de la pièce et de la profondeur d'étirage pour déterminer le bon angle de dépouille. Il est donc préférable de vous connecter avec un partenaire de fabrication expérimenté pour obtenir une évaluation précise. En règle générale, vous devez utiliser au moins 1,5 à 2 degrés de tirant d'eau et ajouter 1 degré pour chaque pouce de profondeur de cavité. Si votre pièce a une surface fortement texturée, vous aurez peut-être besoin d'angles de dépouille de 5 degrés pour éviter les lignes de traînée.
4. Y compris les angles vifs
Non seulement les arêtes vives et les coins nécessitent plus de pression pour se remplir, mais ils font souvent coller les pièces au moule lors de l'éjection. Étant donné que les angles vifs rendent également plus difficile le passage des grenailles à travers les moules, ils peuvent entraîner des vides sous vide ou des zones où les bulles d'air sont piégées. Ceux-ci peuvent causer des dommages esthétiques, augmenter la concentration de contraintes et entraîner une défaillance des pièces. Il est donc important d'arrondir vos bords et coins internes et externes dans la mesure du possible.
Lors de la conception des coins, n'oubliez pas de modéliser vos coins pour avoir une épaisseur de paroi constante. Cela signifie que les angles internes sont arrondis à 50 % de l'épaisseur de la paroi et les angles externes à 150 %.
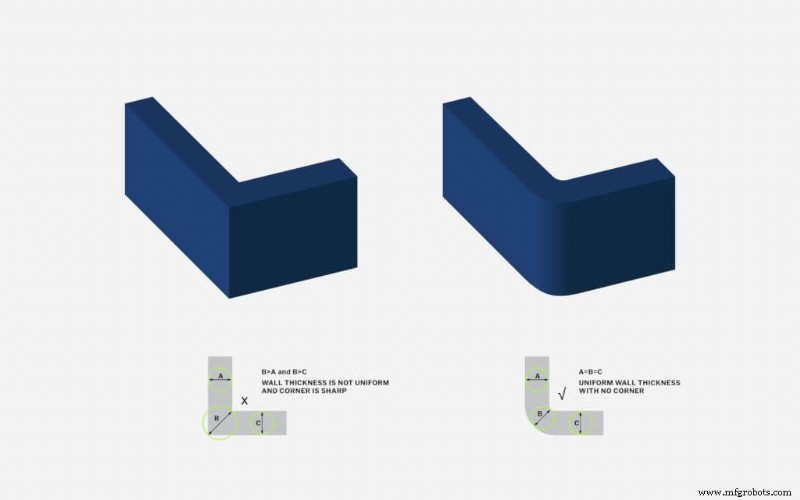
Prévenir les défauts sur les pièces moulées par injection avec Fast Radius
Les erreurs de conception du moulage par injection peuvent retarder la production de plusieurs semaines, augmenter les coûts et entraîner des pièces de qualité inférieure ou même inutilisables. Prendre le temps de prendre des décisions de conception réfléchies au début de votre projet est essentiel et vous fera économiser du temps et de l'argent à long terme. Cependant, il y a beaucoup de choses à garder à l'esprit, donc travailler avec un partenaire expérimenté en moulage par injection comme Fast Radius peut vous aider à obtenir la bonne conception du premier coup.
Lorsque vous vous associez à Fast Radius, vous aurez accès à notre équipe d'ingénieurs, de conseillers et d'experts en conception qui peuvent vous aider tout au long du processus de fabrication. Que vous ayez besoin d'aide pour incorporer subtilement une ébauche dans votre conception ou pour décider d'une épaisseur de paroi appropriée, Fast Radius peut vous aider à concevoir la meilleure pièce possible. Contactez-nous dès aujourd'hui pour commencer la conception de votre prochain projet de moulage par injection.
Vous voulez en savoir plus ? Consultez notre centre de ressources pour en savoir plus sur la sélection des matériaux, quand utiliser un moule à cavité unique ou à plusieurs cavités, et plus encore.
Prêt à fabriquer vos pièces avec Fast Radius ?
Commencez votre devisTechnologie industrielle
- Quelles sont les erreurs courantes à éviter lors de la conception pour la fabrication ?
- Pourquoi la conception de l'angle de dépouille est-elle essentielle pour le moulage par injection ?
- Matériaux pour le moulage par injection-réaction (RIM)
- Conseils de conception pour le moulage par coulée
- Conception de la porte de moulage par injection :un guide ultime pour la fabrication de plastique
- Angle de dépouille pour le moulage par injection :Guide de conception et meilleures pratiques
- L'importance d'une épaisseur de paroi uniforme dans le moulage par injection [Guide]
- Pourquoi avez-vous besoin de la conception pour la fabrication dans le moulage par injection
- Les limites du moulage par injection à faible volume