Rockwell compte toutes les façons dont le "voyage" numérique a porté ses fruits
Tom O'Reilly, vice-président du développement commercial mondial chez Rockwell Automation, s'entretient avec le magazine Smart Manufacturing.
Tom, parlez-nous du plan quinquennal de Rockwell Automation pour restructurer vos installations et vos réseaux de fournisseurs, et arriver à "l'entreprise connectée".
Ce voyage a commencé il y a plus de cinq ans. Au cours de ce processus, nous avons tracé un processus en six étapes qui, je pense, illustre ce que nous avons fait et comment nous faisons ces choses maintenant, ainsi que la façon dont nous parlons aux clients. La première étape consiste à comprendre les besoins de l'entreprise. La deuxième étape consiste à déterminer où se situent les principales lacunes de la chaîne d'approvisionnement. Ensuite, déterminez également votre état de préparation :évaluez l'état actuel de votre installation de fabrication et de vos processus. Quatrièmement, l'élaboration de plans de mise en œuvre, puis la gestion du projet au fur et à mesure que vous exécutez les plans de mise en œuvre, puis une phase d'amélioration continue.
Vous aviez 20 usines différentes à coordonner. Quelles leçons l'entreprise a-t-elle apprises qu'elle applique désormais à ses clients ?
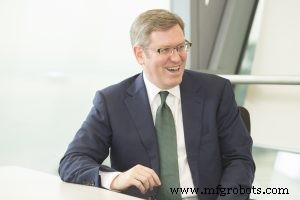
Le plus gros problème que nous avons découvert était le manque de connectivité, en particulier entre le système ERP et l'usine pour nos systèmes d'automatisation. Dans de nombreux cas, nous n'avions pas les bonnes données. Dans certains cas, il n'y avait pas de données. Et dans certains cas, il y avait de mauvaises données. Lorsque vous examinez ces données et que vous les analysez, et qu'elles sont incorrectes ou pas assez solides, cela peut vous conduire à de mauvaises décisions. L'un des éléments clés, dans la phase de détermination de l'état de préparation, consiste à évaluer les capacités de votre infrastructure. C'était une leçon clé apprise. Et nous en avons parlé à nos clients.
La deuxième chose qui est vraiment importante pour les entreprises qui envisagent de se lancer dans la fabrication intelligente est que vous devez d'abord trouver la valeur. En examinant les besoins de l'entreprise, quels sont les véritables moteurs de valeur ? Quels sont les vrais gros problèmes que vous devez résoudre et qui offrent le meilleur rapport qualité-prix ? Parfois, les gens ne s'intéressent qu'à la technologie.
J'ai entendu dire que Rockwell attribue une amélioration annuelle de la productivité de 4 à 5 % grâce à ce changement. Comment est-ce possible? Et pensez-vous que la plupart des fabricants peuvent s'attendre à cela ?
Pour la plupart des fabricants, je dirais oui. Mais cela dépend de votre industrie et de votre état actuel. Difficile donc de généraliser. Si vous regardez comment nous l'avons fait, voici quelques exemples :les jours d'inventaire sont passés de 120 à 82. Nous avons réduit nos CAPEX, ce que nous appelons l'évitement des CAPEX, de 30 % par an. Notre livraison au sein de notre chaîne d'approvisionnement est passée de 80 % à 96 %. Nos délais ont en fait été réduits de 50 %. Et puis, pour le service client, notre délai de livraison au client est passé de 82 % à 98 %. Et en ce qui concerne la qualité, nous avons réduit notre PPM (parties par million) de 50 %. Vous savez, tout cela ne se produit pas le premier jour. Vous devez donc continuer à vous concentrer sur les zones et continuer à les chasser au fil du temps. Nous pensons que nous pouvons continuellement réduire les coûts de quatre à cinq pour cent.
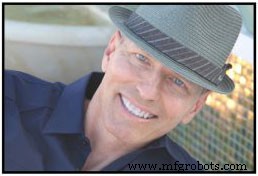
Dans votre pratique MES, vous' re travailler avec FANUC sur des opportunités à travers le monde. Quel est le principal problème qui se pose dans ce type de collaboration ?
Nous avons un excellent partenariat avec FANUC qui a commencé il y a environ sept ans. Ce n'est pas seulement autour du MES. Nous nous concentrons principalement avec FANUC sur le domaine du groupe motopropulseur dans l'industrie automobile. Le plus gros problème auquel nos clients étaient confrontés, et l'un des moteurs du partenariat, était l'intégration entre les systèmes d'automatisation et leur CNC ou leurs robots. Donc, pour aider nos clients à résoudre ce problème, nous avons aidé le FANUC à adopter EtherNet/IP pour les communications. Nous nous appuyons sur ce que nous appelons des profils complémentaires dans notre programmation. Fondamentalement, ce sont des écrans qui s'affichent pour que vous puissiez configurer automatiquement les communications dans la CNC. Nous avons donc rendu l'intégration transparente et pré-construite afin qu'il soit très facile d'intégrer à la fois les CNC ou les robots à notre système d'automatisation.
Alors, diriez-vous que l'intégration est un jeu d'enfant tout le temps ou est-ce toujours difficile dans certaines circonstances ?
Cela dépend de ce que vous essayez de faire. Mais c'est certainement beaucoup plus facile qu'avant. Et ce n'est pas seulement Rockwell qui le dit. Ce sont nos clients, comme General Motors, qui nous le disent. Leur intégration, puis le flux d'informations des deux systèmes, qu'il s'agisse de FANUC ou de notre système, jusqu'au système MES, puis en continuant vers l'ERP, est beaucoup plus facile. Donc je ne sais pas s'ils diraient que c'est un jeu d'enfant, mais ils diraient que c'est beaucoup plus facile.
Ce travail commun est-il principalement automobile ? Quels autres marchés sont importants dans cette relation? Et pouvez-vous nous dire où vous travaillez avec eux dans le monde ?
Le partenariat est né du besoin d'intégration entre la robotique CNC et les systèmes d'automatisation dans l'automobile. Donc, à ce jour, la plupart du travail a été automobile. L'un des domaines de croissance les plus rapides de la robotique se trouve dans les industries des produits de consommation. Nous collaborons donc un peu avec FANUC à travers le monde, principalement pour la robotique et les produits de consommation, en Amérique du Nord et en Europe. Maintenant, le travail que nous avons fait avec FANUC, je dirais que les principaux marchés seraient l'Amérique du Nord, la Chine, l'Europe, le Japon et la Corée. C'est parce que ce sont des centres automobiles où les décisions sont prises et/ou les machines sont construites.
Quel type de produits de consommation ?
Des aliments et boissons ou des produits emballés.
Et sont-ils dans différents pays ?
Il s'agit principalement des marchés les plus développés, où ils envisagent de plus grandes réductions de coûts, une plus grande efficacité, peut-être même un meilleur débit sans avoir des dépenses en capital plus importantes :l'Europe occidentale et l'Amérique du Nord.
Quels pays sont sûrs d'être de grands marchés de croissance dans votre pratique MES ?
L'Amérique du Nord en est une. Il existe de nombreuses initiatives de fabrication de pointe. Et pour être compétitif, vous devez commencer à exécuter la connectivité et avoir la convergence entre IT et OT. (Nous disons l'entreprise connectée.) Le MES est un catalyseur clé pour cela. Nous voyons également certains marchés émergents comme la Chine ou l'Inde qui sont plus précoces dans leur développement du point de vue de la maturité de fabrication. Mais ils reconnaissent que pour rester compétitifs à l'échelle mondiale, ils doivent presque sauter leur développement pour devenir compétitifs à l'échelle mondiale.
Parlons de la plate-forme FactoryTalk Cloud Gateway, qui consiste à extraire des informations des installations de fabrication qui utilisent votre automatisation, à les intégrer dans une structure de données cloud où elles peuvent être combinées avec d'autres données tierces et des données ERP, par exemple, puis en plaçant l'intelligence d'affaires au sommet pour effectuer des analyses pour vos clients afin de leur donner de nouvelles informations commerciales.
Avec FactoryTalk Cloud Gateway, nous nous associons à Microsoft. Nous le basons sur le cloud Microsoft Azure. Mais le logiciel s'appuie sur nos années d'expérience dans les déploiements sur site, tirant parti de la modélisation d'usine de notre FactoryTalk VantagePoint avec d'autres technologies Web et cloud modernes. L'avantage de la plate-forme FactoryTalk Cloud Gateway est que nous pouvons diffuser des données à partir de plusieurs systèmes industriels et commerciaux. Et puis, une fois combinés, nous pouvons les contextualiser, donner un sens aux données, puis les présenter dans des tableaux de bord et des rapports très conviviaux, afin que les non-scientifiques des données puissent interpréter les tendances du processus et prendre des mesures pour les optimiser.
Quelle est l'importance des solutions cloud telles que FactoryTalk Cloud lorsque vous travaillez avec des entreprises en dehors des États-Unis ? Votre mise à jour de cette plate-forme cloud l'automne dernier a-t-elle aidé vos partenaires et/ou clients internationaux ?
Nous mettons à jour notre plate-forme cloud plus rapidement que nos produits logiciels traditionnels. Beaucoup de nos clients mondiaux s'intéressent à l'emplacement géographique de leurs données, au stockage de données, et l'infrastructure de Microsoft Azure est la mieux liée à la transparence et à la conformité des données cloud. L'acceptation de la plate-forme cloud par une clientèle mondiale est donc étonnamment élevée.
Que faites-vous pour inciter les fabricants à adopter FactoryTalk Cloud ?
Nous essayons de vous faciliter la tâche. Par exemple, la configuration des tableaux de bord et la connectivité à notre passerelle est vraiment facile. En quelques étapes simples, vous pouvez connecter la passerelle au système de contrôle. Les données seront automatiquement transférées dans le cloud, puis vous pourrez immédiatement configurer vos tableaux de bord.
Avec qui avez-vous travaillé pour créer la passerelle ?
Le logiciel de passerelle est notre propre développement, mais il est conçu pour être très extensible avec des adaptateurs et des applications personnalisés. Nous proposerons bientôt ces API à l'ensemble de notre communauté de partenaires.
Quelles autres plates-formes et applications proposez-vous ou créez-vous pour générer de la valeur pour vos clients à l'étranger ?
Au salon de l'automatisation en novembre dernier, nous avons annoncé FactoryTalk Analytics for Machines, FactoryTalk Analytics for Devices, l'application FactoryTalk TeamONE, et nombre d'entre elles sont des applications conçues à cet effet. Très évolutif, facile à utiliser, facile à mettre en œuvre. Nous espérons qu'en produisant ces applications modulaires très rentables, les gens pourront adopter une approche étape par étape, au lieu d'essayer de manger l'éléphant en une bouchée.
Lorsque vous utilisez ce logiciel pour repérer et éliminer les pannes, quelles sont les deux ou trois pannes les plus courantes qu'il détecte et élimine ?
L'un des principaux avantages que nous avons constatés est que les clients découvrent des problèmes inconnus. En règle générale, dans une usine de fabrication, l'opérateur ou les personnes chargées de la technologie opérationnelle savent où ils ont des problèmes liés aux performances, à la qualité ou au débit. Une fois que les clients ont installé le système et commencé à résoudre ces problèmes, ils trouvent souvent d'autres problèmes dont ils n'étaient pas conscients. Ils pourraient avoir des goulots d'étranglement dans les processus de fabrication en amont ou en aval, par exemple.
Comme tout le monde, les clients de Rockwell ont été prudents quant à l'adoption du cloud. Que faites-vous pour les convaincre que c'est le bon moment pour le présenter ? Et les attaques de rançongiciels de cette semaine vont-elles compliquer les efforts pour promouvoir l'adoption du cloud ?
Tout d'abord, la fiabilité et la capacité des solutions cloud se sont considérablement améliorées. (De plus, nos clients n'ont pas à maintenir leur propre infrastructure, et cela devient de plus en plus important pour nombre de nos clients.) Deuxièmement, l'évolutivité des services cloud est presque impossible à reproduire avec des capacités sur site. Nos clients peuvent commencer petit et le faire évoluer beaucoup plus rapidement que s'ils le construisaient et l'entretenaient eux-mêmes. La sécurité des solutions cloud est probablement bien meilleure qu'avec les solutions sur site. Et cela, je pense, joue dans le deuxième point. Les services cloud sont mis à jour beaucoup plus fréquemment.
Nous pensons qu'une grande partie des rançongiciels actuels [ont eu un impact] sur ce que les gens appelleraient les actifs informatiques non gérés de nos clients, lorsqu'ils ne les ont pas tenus à jour ou ne l'ont pas fait avoir la bonne sécurité en place. C'était soit le point d'entrée, soit le début. Les services cloud seraient potentiellement une plus grande prévention pour cela. C'est notre première pensée. De toute évidence, les gens auraient peur de sortir de cela et d'essayer de comprendre ce qui s'est passé. Mais notre idée initiale est que cela pourrait en fait inciter davantage de nos clients à utiliser davantage le cloud.
Lorsque Rockwell a dû construire des usines à Singapour et au Mexique, comment avez-vous transféré les connaissances tribales des processus de fabrication chez Rockwell à ces marchés ?
Nous avons fait les installations de Singapour et du Mexique plus tard dans notre voyage, nous avions donc développé notre processus en six étapes pour mettre en œuvre l'entreprise connectée dans l'une de nos installations et l'avons exécuté dans au moins 10 usines. Il est important d'avoir les meilleurs experts en la matière sur des aspects spécifiques du processus qui étaient complexes ou uniques ou très critiques. Nous avons amené ces experts en la matière dans chaque usine pour veiller à ce que ces processus soient mis à niveau de la bonne manière. Enfin, nous avons déterminé qu'il était très important de disposer de systèmes et d'architectures standardisés avant de commencer le voyage.
Système de contrôle d'automatisation
- Cinq façons dont la technologie Digital Twin aide les entreprises à traverser la pandémie
- Dans le nouveau paysage logistique, il n'y a pas de retour aux anciennes méthodes
- Des clients depuis la Norvège jusqu'à notre usine de routeurs CNC
- GE Digital :un parcours continu de transformation numérique
- Comment le COVID-19 a-t-il modifié la transformation numérique ?
- Censornet :assurer l'avenir de l'industrie manufacturière
- L'impact démesuré de l'industrie 4.0 sur le back-office
- CS Ellis :quatre façons de numériser la chaîne d'approvisionnement
- L'essor des plateformes numériques dans le secteur manufacturier