Insensibilité efficace de la résine de mélamine urée-formaldéhyde par polymérisation interfaciale sur des explosifs à la nitramine
Résumé
Pour améliorer la sécurité des explosifs au nitrate d'ammonium, la résine mélamine urée-formaldéhyde (résine MUF) a été sélectionnée pour la préparation de trois explosifs nitramine typiques (cyclotétraméthylènetétranitramine, HMX ; cryclo-triméthylènetrinitramine, RDX ; et polymère vert à base d'hexanitrohexaazaisowurtzitane, CL-20) -explosifs liés (GPBX) par polymérisation interfaciale. Parallèlement, les particules composites correspondantes préparées par des méthodes de mélange physique et de bain de séchage ont été étudiées et comparées. La morphologie des particules, la structure cristalline, la stabilité thermique et les performances de sécurité des particules composites résultantes ont été caractérisées par microscopie électronique à balayage (MEB), diffraction des rayons X sur poudre (XRD), spectres infrarouges à transformée de Fourier (FT-IR), calorimètre à balayage différentiel. (DSC) et test de sensibilité aux chocs, respectivement. Les résultats SEM ont montré que le MUF a été appliqué avec succès sur la surface des trois explosifs, et différentes particules composites préparées par la même méthode ont leurs propres caractéristiques uniques. Cet effet est attribué à la capacité de la résine à isoler et à tamponner les stimuli externes. Il est évident que la polymérisation interfaciale est une technique de désensibilisation efficace pour préparer des particules composites cœur-enveloppe pour explosifs.
Contexte
À mesure que la technologie et les systèmes d'armes continuent d'évoluer, les munitions doivent non seulement avoir une précision élevée, une puissance élevée et une longue portée pour le système de puissance de feu de l'arme, mais également pour maintenir une sécurité relativement élevée dans d'autres environnements. Cependant, les explosifs conventionnels comme l'hexahydro-1,3,5-trinitro-1,3,5-trizine (RDX), le 1,3,5,7-teranitro-1,3,5,7-tetrazocane (HMX) et Le 2,4,6,8,10,12-hexanitro-2,4,6,8,10,12-hexaazaiso-wurtzitane (CL-20) répond difficilement à ces exigences (structures moléculaires illustrées à la Fig. 1), et le développement d'explosifs brisants insensibles (IHE) est considéré comme un moyen souhaitable de satisfaire l'application des systèmes d'armes [1,2,3]. De nombreux chercheurs au pays et à l'étranger s'intéressent à la désensibilisation des explosifs à la nitramine, en utilisant généralement des techniques de raffinement [4, 5], de revêtement [6, 7] et d'eutectique [8, 9] pour atteindre l'objectif de réduire la sensibilité. La technologie de revêtement pour matériaux énergétiques est une méthode d'enveloppement du modificateur sur la surface de la poudre par un certain processus pour atteindre l'objectif d'insensibilité, comprenant principalement un revêtement physique et un revêtement chimique. Le revêtement physique fait principalement référence à la formation d'une certaine couche de revêtement à la surface de particules explosives solides par adsorption ou force externe. Et les méthodes de revêtement physiques courantes incluent la méthode de suspension aqueuse [10], la méthode de revêtement par cristallisation [11], la méthode de séchage par atomisation [12], la méthode supercritique [13] et la méthode de séparation de phases [14]. Le procédé de revêtement chimique fait référence à la formation d'une couche de revêtement sur la surface de particules solides par métathèse, réaction de polymérisation, traitement à haute énergie ou similaire dans un certain milieu. Il est bien connu que les indicateurs clés pour l'évaluation d'un matériau coeur-coquille sont le degré de couverture, la résistance mécanique et l'inhibition de l'auto-nucléation pour la coque de revêtement [15]. Par conséquent, l'exploration de nouvelles techniques de revêtement et la découverte de nouveaux matériaux de revêtement sont des moyens efficaces de garantir que les explosifs possèdent une bonne structure noyau-enveloppe et répondent aux exigences de sécurité. Notre recherche est basée sur les deux méthodes de revêtement décrites ci-dessus.

Structure moléculaire de RDX, HMX, CL-20 et MUF Binder. R-CH2OH est MF
Pendant des décennies, les liants « trialdéhydes » conventionnels ont fait l'objet de recherches pour les universitaires au pays et à l'étranger. Avec l'amélioration continue des performances globales, des rapports pertinents sur leurs applications ont commencé à apparaître dans le domaine des matériaux énergétiques. En 2015, Yang et al. [16] ont utilisé un monomère de résine mélamine-formaldéhyde (MF) à 3 % pour revêtir le CL-20, le HMX et le RDX. Les particules telles que préparées avaient une couche de revêtement de résine MF compacte et uniforme, et leur stabilité thermique et leurs propriétés de sécurité sont considérablement améliorées. Cet article présente des similitudes avec ce rapport car nous avons également découvert que la résine mélamine-urée-formaldéhyde est plus appropriée comme matériau liant explosif, par rapport à la résine mélamine-formaldéhyde. La résine MF a d'excellentes performances ; cependant, il est cassant et coûteux. Le plus important est que le produit en résine MF ne puisse pas être stocké longtemps. S'il est utilisé comme matériau de revêtement pour fabriquer des particules composites énergétiques avec une structure cœur-coquille, il est susceptible d'altérer les propriétés des particules. Li et al [17] ont préparé de la cyclotétraméthylènetétranitramine sur des microsphères énergétiques en élastomère polyester-éther thermoplastique (HMX @ TPEE) avec une distribution granulométrique allant de 50 à 200 m via une méthode d'évaporation de solvant en émulsion (ESV), et les particules résultantes avaient une sensibilité plus faible et plus élevée. stabilité thermique. Dans cet article, une méthode de bain de séchage améliorée a été proposée et les explosifs à liant polymère (PBX) avec d'excellentes performances globales ont été préparés en utilisant de la résine mélamine urée-formaldéhyde (résine MUF) comme matériau de coque et trois explosifs différents comme matériau de base. . Wang et al. [18] ont obtenu des nanocomposites 30 nm de cyclotétraméthylènetétranitramine/nitrocellulose (HMX/NC) avec une bonne propriété globale par une méthode sol-gel-supercritique améliorée. On peut voir que le choix du liant a une grande influence sur la morphologie, la taille des particules et les performances des PBX résultants.
Comme nous le savons tous, l'assistance par ultrasons a été largement appliquée à la synthèse chimique et à la modification de matériaux fonctionnels [19, 20]. Dans notre étude, un liant MUF vert avec des performances globales supérieures a été préparé par une méthode de synthèse en deux étapes. Ensuite, le liant MUF tel que préparé a été utilisé comme matériau de coque, et HMX, RDX et CL-20 comme matériaux de noyau, respectivement. Tout d'abord, en utilisant une méthode de mélange physique simple, trois différents explosifs/particules MUF (avec une teneur en MUF de 5%) ont été fabriqués via une assistance ultrasonique. Par la suite, dans les mêmes conditions, les six autres particules énergétiques composites ont été préparées en utilisant respectivement une méthode améliorée de bain de séchage et une méthode de polymérisation interfaciale optimisée. En résumé, pour la première fois, neuf particules énergétiques composites différentes avec le même rapport MUF ont été fabriquées via une assistance ultrasonore par les trois méthodes différentes. Fait intéressant, grâce à différentes méthodes, nous avons obtenu des PBX avec différentes morphologies, telles que des formes apparentes de particules exposées (mélange physique), polygonales irrégulières (méthode du bain de séchage) et denses noyau-enveloppe (polymérisation interfaciale). Étonnamment, à mesure que l'aspect esthétique de la morphologie des particules augmentait, leur stabilité thermique et leurs performances de sécurité se sont améliorées. Grâce à la recherche et à l'analyse, les particules énergétiques composites préparées par polymérisation interfaciale sont optimales en termes de morphologie, de stabilité thermique et de performances de sécurité. Par conséquent, afin d'obtenir des particules énergétiques composites avec les meilleures performances globales, il est préférable d'envisager la méthode de polymérisation interfaciale pour préparer le GPBX après avoir déterminé le liant utilisé.
Méthodes
Matériaux
HMX, RDX et CL-20 ont été fournis par Gansu Yinguang Chemical Industry Group Co. Dans notre étude, les matières premières ont été sélectionnées dans le processus de bain de séchage. Lors de la préparation de composites explosifs/MUF par des méthodes de mélange physique et de polymérisation interfaciale, les matières premières ont été recristallisées selon la référence [21]. Le diméthylsulfoxyde a été obtenu auprès de l'usine de réactifs chimiques de Tianjin Fuchen. Tween 80 et Span 80 ont été mélangés comme émulsifiant composite pour explosifs avec du MTween 80 :MSpan80 de 0,57 :0,43. La triéthanolamine (TEOA, utilisée pour ajuster la valeur du pH pendant la réaction) provenait de Tianjin Sailboat Chemical Reagent Technology Co., Ltd. Urée, formaldéhyde, acide chlorhydrique (5% d'acide chlorhydrique dilué a été utilisé pour ajuster la valeur du pH dans la présente étude) , et le résorcinol (R-80) ont été fournis par Tianjin Tianli Chemical Reagent Co., Ltd. Le chlorure d'ammonium a été acheté auprès de Tianjin Guangfu Technology Development Co., Ltd. L'alcool polyvinylique 2488 (PVA) a été fourni par Qingdao Yousuo Chemical Technology Co., Ltd. L'eau pure a été obtenue à partir de l'approvisionnement en eau pure de Taiyuan Iron and Steel Co., Ltd.
Synthèse en deux étapes de la résine MUF
Le liant MUF avec d'excellentes propriétés globales a été préparé par un processus en deux étapes. Premièrement, la préparation du prépolymère de résine urée-formaldéhyde. 0,62 µg d'urée et 1,87 µg de solution de formaldéhyde (la concentration est de 37 %) ont été mélangés, puis l'urée a été suffisamment dissoute avec un agitateur magnétique. La valeur du pH du mélange a été ajustée à 8,5~9,5 avec de la triéthanolamine. La solution a été placée dans un bain d'eau à 65°C et agitée pendant 1 h jusqu'à ce qu'un prépolymère de résine urée-formaldéhyde transparent et visqueux soit obtenu. Après refroidissement, HCl a été ajouté goutte à goutte jusqu'à ce que le pH de la solution soit ajusté à environ 3,5, et mis de côté. Deuxièmement, la préparation du MUF. 1,87 g de prépolymère a été ajouté à 35 ml d'eau désionisée pour former une émulsion sous agitation uniforme. Par la suite, 8 % de PVA, 0,01 µg de mélamine, 0,125 µg de résorcinol et 0,06 µg de chlorure d'ammonium ont été successivement ajoutés et le pH a été ajusté à environ 3,5 avec de l'acide chlorhydrique dilué. Ensuite, le ballon à trois cols a été placé dans le bain-marie à 65 °C et mis à réagir pendant 3 à 4 h, suivi d'un refroidissement naturel et d'une filtration sous vide. La solution a été lavée avec de l'eau déminéralisée, donnant finalement une résine MUF de haute qualité. Après séchage, environ 0,3 g de MUF a été pesé.
Préparation de particules composites explosives/MUF par des méthodes de polymérisation interfaciale et de bain de séchage
La préparation de particules composites explosives/MUF par des méthodes de polymérisation interfaciale et de bain de séchage est tout à fait cohérente avec la préparation de prépolymère de résine urée-formaldéhyde dans la synthèse en deux étapes du liant MUF. Cependant, la deuxième étape est évidemment différente.
Dans la fabrication de particules composites explosives/MUF par polymérisation interfaciale, 6 g d'explosifs ont été ajoutés à 35 ml d'eau désionisée, et 0,01 g de span-80 a été ajouté goutte à goutte comme émulsifiant. Par la suite, le système a été émulsionné et cisaillé à une vitesse de 7 000 rad/min pendant 30 min jusqu'à ce qu'une émulsion explosive stable se forme. L'émulsion explosive a remplacé l'eau déminéralisée dans la synthèse en deux étapes de la résine MUF. Le schéma de synthèse est présenté en B sur la figure 2 ci-dessous.
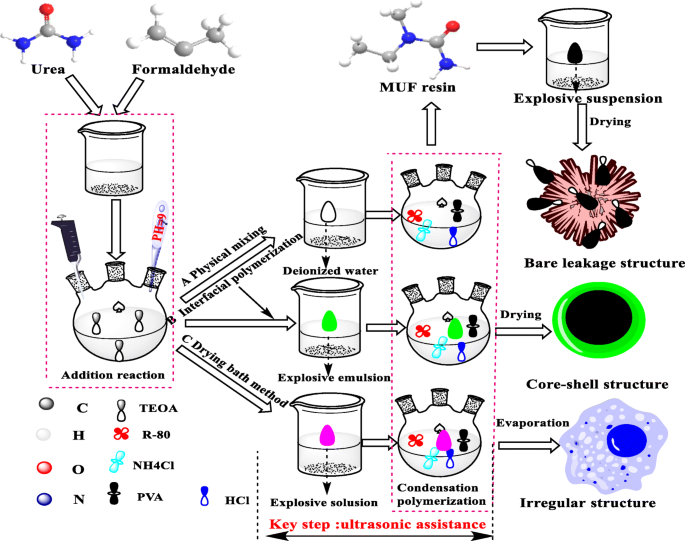
Schéma de principe des différentes méthodes de préparation de HMX/MUF, RDX/MUF et CL-20/MUF
Lors de la préparation de particules composites explosives/MUF par la méthode du bain de séchage, 6 µg d'explosif ont été dissous dans 35 µml de DMSO à 65°C pour former une solution explosive. La solution explosive a remplacé l'eau déminéralisée dans la synthèse en deux étapes de la résine MUF. Après 3 à 4 h de réaction, un mélange laiteux explosif/MUF stable s'est formé. Ensuite, l'émulsion a été placée dans un four et séchée à 70 °C pendant 48 h, donnant finalement des particules composites explosives/MUF. Le schéma de synthèse est représenté en C sur la figure 2 ci-dessous (bain de séchage). Il est à noter qu'après l'ajout de l'émulsion explosive, une assistance ultrasonore doit être effectuée afin d'éviter l'agglomération du liant et de l'explosif.
Préparation de particules composites explosives/MUF par mélange physique
Afin de comparer avec les particules explosives/MUF préparées par les deux premières méthodes, nous avons également préparé des particules explosives/MUF en utilisant une méthode de mélange physique simple. Le liant MUF, préparé par la synthèse en deux étapes, a été mélangé avec 6 g d'explosif dans 35 ml d'eau désionisée, puis, la solution mélangée a été agitée dans le bain-marie à 65 °C pendant 2 h. Après cela, le mélange a été laissé au repos, suivi d'une filtration et d'un séchage; des particules composites explosives/MUF ont été obtenues. Le schéma de préparation est représenté en A sur la Fig. 2 (Mélange physique).
Nous avons étiqueté les échantillons préparés par la méthode de polymérisation interfaciale, la méthode du bain de séchage et la méthode de mélange physique, en tant qu'échantillon 1, échantillon 2 et échantillon 3, respectivement.
Caractérisation
Des images de microscopie électronique à balayage à émission de champ (FESEM) ont été prises sur un MIRA3 LMH SEM (Tescan) à 10 k; Les diagrammes de diffraction des rayons X (XRD) ont été obtenus à l'aide d'un diffractomètre à rayons X DX-2700 (Dandong Haoyuan Corporation, Liao ning, Chine) avec un rayonnement Cu-Kα (40 kV, 30 mA) à λ = 1.5418 Å. Tous les échantillons ont été scannés de 5° à 50° avec des pas de 0,03 et 6 s de temps de comptage ; Les spectres infrarouges à transformée de Fourier (FT-IR) ont été caractérisés par un Nicolet FT-IR 8700 Thermo (Waltham, MA, USA) avec une résolution du nombre d'onde de 4 cm −1 et une moyenne unique de 32 balayages à la température du nombre ; l'analyse thermique a été effectuée sur un calorimètre à balayage différentiel (DSC-131, France Setaram Corporation, Shanghai, Chine) à une vitesse de chauffage de 10 °C/min. L'appareil à marteaux-pilons ; la hauteur spéciale (H 50 ) représente la hauteur à partir de laquelle le marteau-pilon de 2,500 ± 0,002 kg provoquera un événement explosif dans 50 % des essais. Dans chaque détermination, 25 tests de chute ont été effectués pour calculer le H 50 . Et la masse de l'échantillon est de 30 mg. La sensibilité au frottement des échantillons a été testée avec un instrument à friction WM-1. Dans chaque détermination, 25 échantillons ont été testés, et une probabilité d'explosion (P , %) a été obtenu. Et la masse de l'échantillon est de 20 mg. La taille des particules testée par l'analyseur de particules dynamique QICPIC (SYMPATEC Co., Ltd., Allemagne) et son environnement de travail sont de 5 à 35 °C ; l'humidité relative est inférieure à 85 % ; le type de source lumineuse est le laser He-Ne ; la puissance est de 2,0 mW ; et la longueur d'onde est de 0,6328 μm.
Résultats et discussion
Morphologie des échantillons
La morphologie et la structure des RDX, HMX et CL-20 bruts ; le classeur MUF synthétisé (Fichier complémentaire 1 :Section S1) ; et les particules composites explosives/MUF préparées par les trois méthodes ont été mesurées, respectivement. L'image SEM montre que les explosifs à la nitramine brute présentent une forme polygonale et une distribution de taille inégale. L'apparence du liant MUF d'origine est sphérique ; cependant, on peut clairement voir que les particules ne sont pas pleines car son intérieur peut être vide ou partiellement en eau.
Par rapport aux explosifs non revêtus (Figs. 3a, 4a et 5a), la morphologie des particules composites explosif/MUF préparées par différentes méthodes est assez différente, tandis que la morphologie des différentes particules composites explosif/MUF préparées par la même méthode a des caractéristiques similaires . Les particules composites préparées par la méthode de mélange physique présentent un phénomène d'exposition aux particules évident, montrant un effet de revêtement médiocre (Fig. 3d, 4d et 5d). En effet, il est difficile de répartir uniformément le liant sur la surface de l'explosif uniquement par action mécanique. Le processus de dispersion de l'agitation mécanique seul est réversible. Après la collision, les gouttelettes se regrouperont à nouveau, atteignant finalement un équilibre dynamique qui maintient une certaine granularité. Une liaison mutuelle incontrôlable se produit lors de la collision de gouttelettes, ce qui est hors de contrôle.
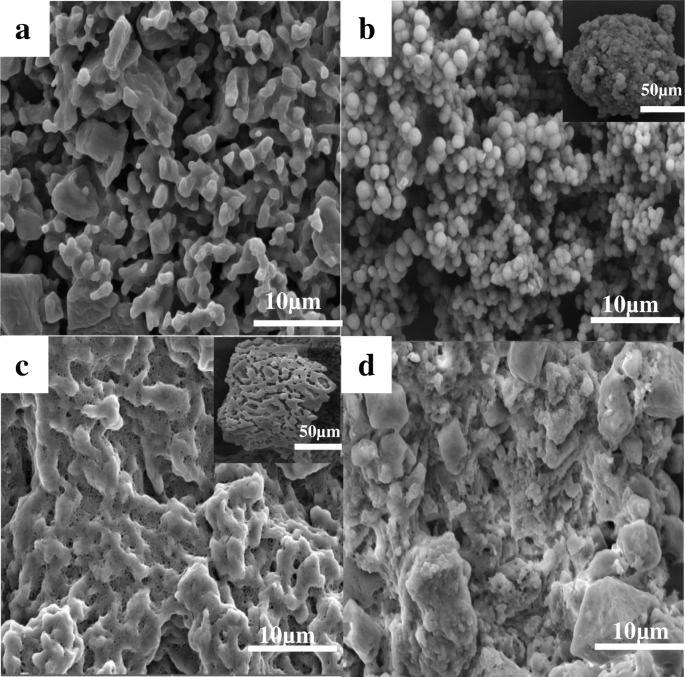
Images SEM du HMX non couché (a ), HMX/MUF-1 (b ), HMX/MUF-2 (c ) et HMX/MUF-3 (d ); les images correspondantes à faible grossissement sont insérées
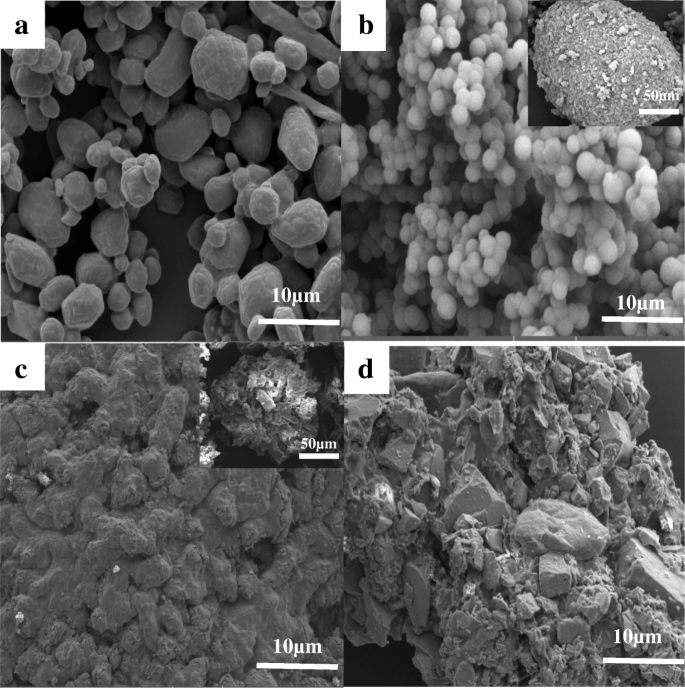
Images SEM du RDX non couché (a ), RDX/MUF-1 (b ), RDX/MUF-2 (c ), et RDX/MUF-3 (d ); les images correspondantes à faible grossissement sont insérées
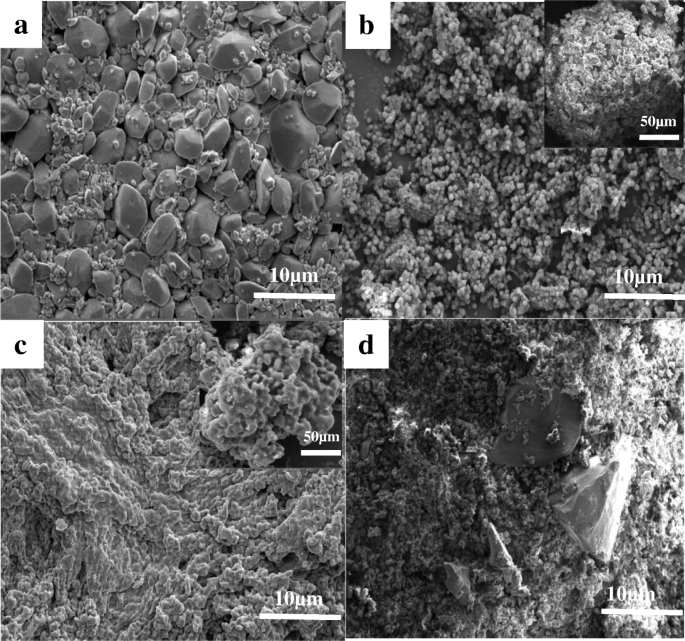
Images SEM du CL-20 non couché (a ), CL-20/MUF-1 (b ), CL-20/MUF-2 (c ), et CL-20/MUF-3 (d ); les images correspondantes à faible grossissement sont insérées
Les particules composites préparées par la méthode du bain de séchage ont des couches de revêtement distinctement denses. Étonnamment, une fois que le MUF a complètement encapsulé les particules explosives, il est difficile de former une sphère complète, dont la plupart apparaît sous forme de particules denses mais irrégulières (comme le montrent les figures 3c, 4c et 5c). Et ce phénomène peut être expliqué par la théorie de base de la chimie des interfaces [22]. Pendant le processus d'élimination du solvant, la viscosité de l'explosif/MUF augmente progressivement à mesure que le solvant s'évapore, et les particules dispersées ont tendance à se réagréger ensemble. D'autre part, étant donné que la solubilité du dispersant PVA dans le DMSO est faible, lorsque les liants MUF entrent en collision les uns avec les autres, il n'y a pas une bonne force de dispersion, ce qui les fait coller les uns aux autres, formant finalement une forme irrégulière. De plus, la théorie de la croissance cristalline [23] peut également servir de support puissant pour expliquer cette morphologie irrégulière. La méthode du bain de séchage amène l'explosif à subir un processus de croissance et de développement de "l'embryon de cristal-noyau-cristal". Étant donné que le système MUF est dans une phase fluide métastable et que le système contient une variété de surfaces externes, les particules explosives dissoutes nucléent sur ces surfaces, ce qui peut réduire la barrière de nucléation causée par l'augmentation de l'énergie de surface de MUF et diminuer efficacement l'énergie de surface barrière lors de la nucléation des explosifs. La nucléation explosive est préférentiellement formée à cette irrégularité, c'est-à-dire qu'une nucléation non uniforme est également une cause de morphologie irrégulière des particules. D'après l'illustration de la figure 3d, nous pouvons voir que la morphologie globale des particules HMX/MUF est en « nid d'abeille », ce qui est lié à l'énergie de liaison plus faible entre MUF et HMX (Fichier supplémentaire 1 :Section S2). Au fur et à mesure que l'évaporation progresse, le liant MUF se rétracte progressivement. Une énergie de liaison trop faible entre eux rend le MUF incapable d'encapsuler complètement le HMX et génère une forte contrainte interne, formant finalement la forme en « nid d'abeille » [24].
La chose la plus intéressante est que les particules composites explosives/MUF préparées par le procédé de polymérisation interfaciale possèdent toutes une structure sphéroïdale et que la surface des particules résultantes est dense et lisse (comme le montrent les figures 3b, 4b et 5b). Ceci est probablement dû au fait que l'ajout du dispersant PVA diminue la tension superficielle de l'eau et améliore la mouillabilité, augmentant ainsi l'affinité entre les molécules explosives et la solution de liant. La constante de Hamaker est diminuée simultanément et l'énergie d'attraction entre les particules est réduite, formant un encombrement stérique efficace. Plus important encore, l'énergie répulsive entre les particules composites augmente, ce qui améliore considérablement la dispersibilité entre l'explosif/MUF [25]. Comme représenté dans l'insert des Fig. 4b et 5b, de nombreuses particules composites RDX/MUF et CL-20/MUF présentent une morphologie sphérique super solide, avec des surfaces denses et lisses. Étonnamment, la morphologie des particules HMX/MUF illustrées sur la figure 3b est également sphérique, mais pas aussi complète que les particules composites RDX/MUF et CL-20/MUF, ce qui est attribué à l'énergie de liaison minimale entre HMX et MUF. Une énergie de liaison trop faible rend le système mixte trop stable, ce qui entraîne une tendance évidente de la surface MUF à rétrécir automatiquement. Par conséquent, bien que les particules HMX/MUF aient tendance à être sphéroïdisées, elles ne sont pas pleines.
Structure cristalline des échantillons
Pour déterminer si la transformation de phase du HMX et du CL-20 s'est produite, une analyse XRD est utilisée et les résultats sont présentés sur la figure 6. Grâce à l'analyse, on peut voir si la structure cristalline a changé pendant la préparation de l'explosif/MUF particules composites. Plus important encore, l'analyse par diffraction des rayons X a confirmé de côté que le MUF avait été appliqué avec succès sur la surface de l'explosif. D'après la figure 6a, HMX/MUF-1, HMX/MUF-2 et HMX/MUF-3 contiennent presque tous les pics de diffraction du HMX brut. Et des phénomènes similaires apparaissent également dans les diagrammes de diffraction des particules composites RDX et CL-20, comme le montre la figure 6c, e. Cela indique que la structure cristalline de l'explosif ne change pas pendant toute la préparation du MUF/explosif par les méthodes de mélange physique, de bain de séchage et de polymérisation interfaciale. De plus, nous avons remarqué un phénomène similaire parmi les trois particules composites explosif/MUF, c'est-à-dire que les principaux pics de diffraction des particules composites explosif/MUF sont affaiblis et élargis par rapport aux matières premières. Par exemple, dans les diagrammes de diffraction HMX/MUF, RDX/MUF et CL-20/MUF, les pics de diffraction principaux à 2θ = 16,39°, 12,58° et 13,29° montrent le phénomène d'affaiblissement et d'élargissement le plus évident. Cela peut être attribué aux propriétés physiques « isotropes » du MUF amorphe, ce qui entraîne une disposition irrégulière des particules explosives/MUF résultantes dans la distribution spatiale. Un tel arrangement périodique affaiblit l'intensité de diffraction de l'explosif [26]. Plus important encore, le pic de diffraction de MUF est également présent dans le pic de diffraction des particules composites explosif/MUF. Par exemple, dans les diagrammes de diffraction HMX/MUF, RDX/MUF et CL-20/MUF, la diffraction culmine à 2θ = 26,71°, 26,78° et 26,99° sont beaucoup plus élevés que le pic de diffraction à la même position des matières premières. Évidemment, c'est parce que le pic de diffraction autour de 2θ = 27° est l'un des pics caractéristiques de diffraction les plus dominants de la MUF. Étant donné que la teneur en MUF ne représente que 5 % de l'explosif, les pics de diffraction discrets présents dans le MUF lui-même sont moins prononcés dans les particules composites. Comme illustré dans la vue agrandie du pic de diffraction inséré dans chaque image, par rapport aux explosifs d'origine, de nouveaux pics de diffraction apparaissent dans les trois particules composites explosives, comme à 2θ = 41,30° dans le diagramme de diffraction de l'échantillon HMX, 2θ = 39,45° dans le diagramme de diffraction de l'échantillon RDX et 2θ = 35,93° dans le diagramme de diffraction de l'échantillon CL-20, ce qui confirme effectivement l'existence d'un liant MUF dans les particules composites explosif/MUF.
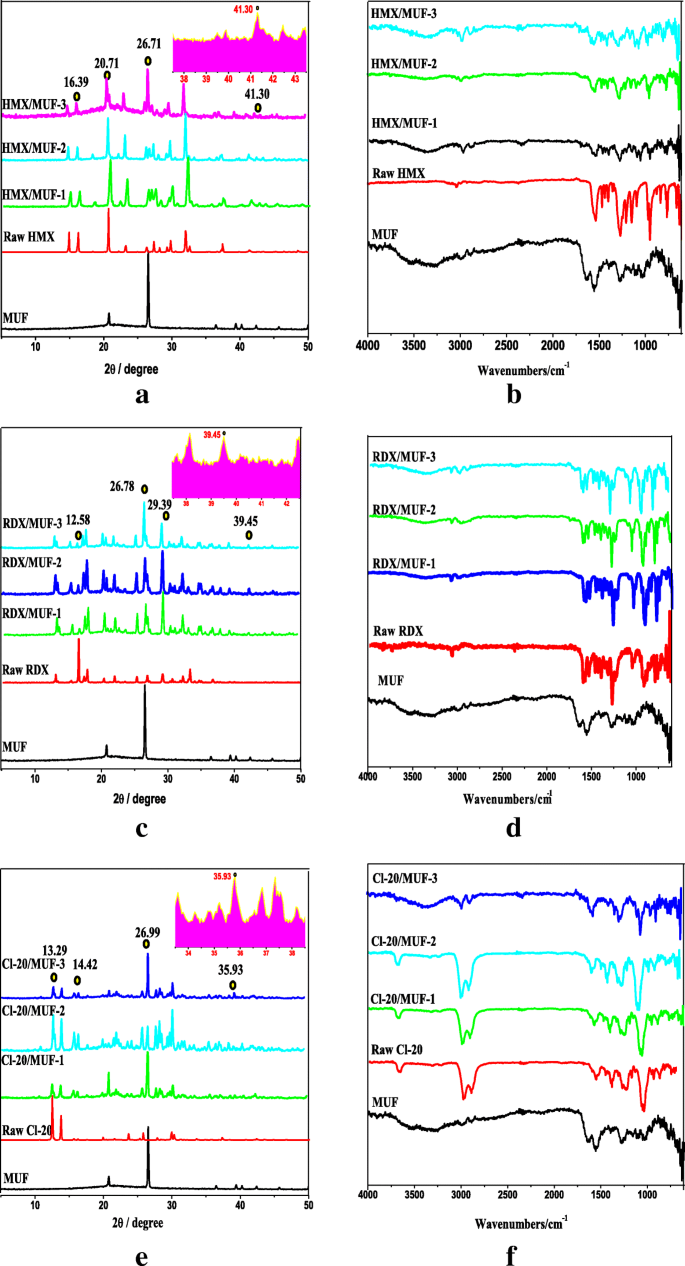
un –f Échantillons de spectre XRD et FI-IR
Une analyse FI-IR a été réalisée pour identifier la structure moléculaire des échantillons. Dans l'ensemble, les particules composites préparées par les trois techniques différentes contiennent la quasi-totalité des pics de vibration d'étirement du liant et de l'explosif. Les résultats de mesure ont confirmé de côté que la résine MUF a formé avec succès une couche protectrice sur la surface de l'explosif, correspondant aux résultats du test XRD. Il est bien connu que le HMX possède quatre structures cristallines différentes, trois phases cristallines pures (α-HMX, -HMX et -HMX) et une phase hydratée (γ-HMX). Et le β-HMX est généralement considéré comme la phase la plus stable avec une énergie explosive élevée, une grande densité et une faible sensibilité, ce qui est bien sûr lié à la structure spatiale de sa monoclinique P21/c [27]. Dans le spectre infrarouge de la MUF, il y a –C=O pic d'absorption des vibrations d'étirement à 1735 cm −1 . Dans le spectre infrarouge de HMX, –NO2 et –CH2 les pics d'absorption des vibrations d'étirement apparaissent près de 1560 cm −1 et 2980 cm −1 , respectivement (comme le montre la figure 3b). On peut remarquer que des pics d'absorption des vibrations d'étirement similaires apparaissent dans les positions correspondantes dans la bande caractéristique de HMX/MUF, ce qui signifie que la structure cristalline de HMX ne sera pas modifiée pendant la préparation via des méthodes de mélange physique, de bain de séchage et de polymérisation interfaciale. . De plus, une situation similaire se retrouve également dans le spectre infrarouge des particules CL-20 (Fig. 6f), en particulier le pic de vibration d'étirement des particules CL-20 dans la région des empreintes digitales 760 cm −1 démontre que la structure cristalline Ɛ-CL-20 n'a pas changé tout au long de l'expérience [28].
Propriétés thermiques
Sonder le processus de décomposition thermique est très important pour les matériaux énergétiques [29]. Dans nos recherches, des courbes DSC collectées à une vitesse de chauffe de 10 °C/min sont obtenues sur la Fig. 7. Nous avons trouvé des phénomènes intéressants sur la décomposition thermique de ces trois explosifs à base de nitramine. Dans l'ensemble, le HMX et le CL-20 ont des caractéristiques de décomposition thermique similaires (il existe un pic endothermique de transformation cristalline lors de la décomposition thermique) ; cependant, le phénomène d'auto-échauffement du CL-20 est plus important que celui du HMX. Cela est dû au fait qu'en tant qu'explosif au nitrate d'ammonium de type cage, le clivage du squelette moléculaire et la "réaction en phase condensée hétérogène" de la phase condensée existent simultanément et s'exacerbent, tandis que le HMX est un type de "décomposition-fusion". matériau, et son processus de fusion est affecté par le processus de décomposition thermique. En pratique, HMX et RDX ont également des comportements thermiques similaires, car tous deux ont les mêmes chaînes ramifiées. La différence est que HMX libère de la chaleur rapidement pendant la décomposition thermique, et sa courbe DSC montre un pic abrupt et pointu (Fig. 7a). Parce que la décomposition du HMX est un processus hétérogène où la réaction solide-liquide se déroule simultanément, alors que la décomposition du RDX est un processus homogène à l'état fondu après la fin de la fusion. La réaction accélérée provoquée par le changement de phase simultané lors de la décomposition rend la décomposition du HMX plus sévère que celle du RDX [30].
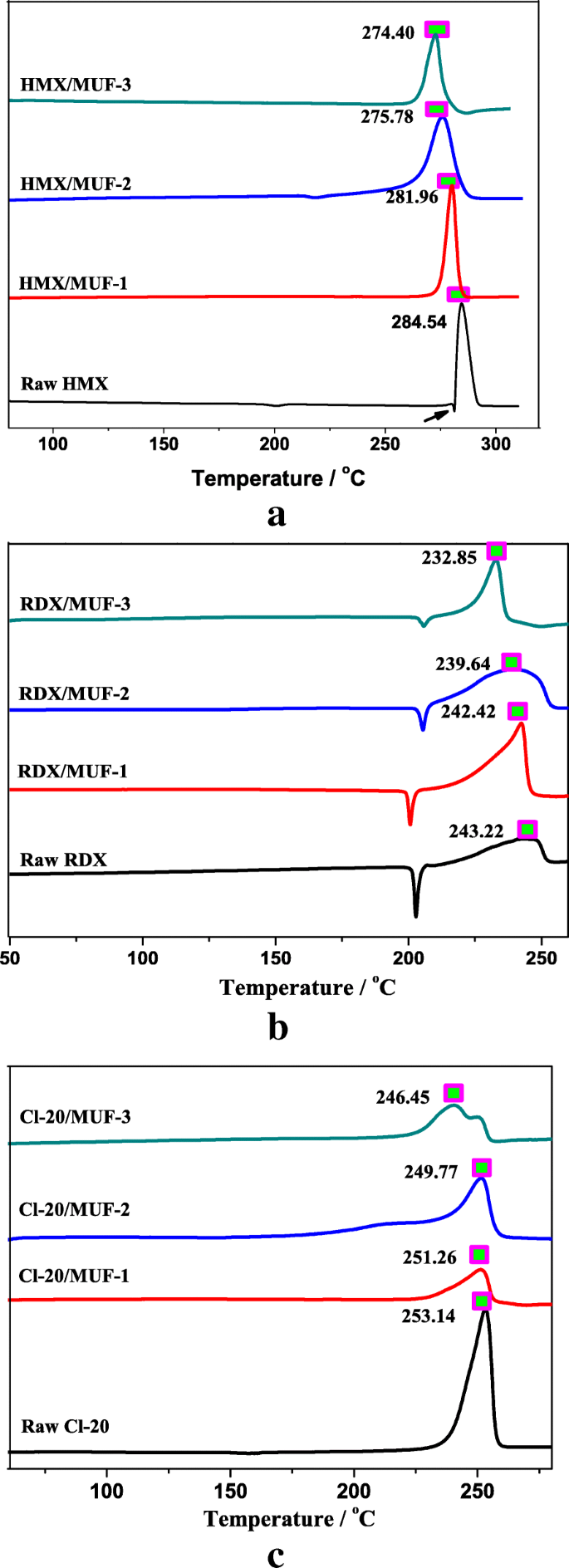
un –c Courbes DSC des échantillons prélevés à une vitesse de chauffe de 10 °C/min
Pour le HMX, la courbe DSC montre un pic endothermique à 279,2 °C, puis un pic exothermique à 284,54 °C (Fig. 7a), attribué respectivement à la transition de phase de fusion et au pic caractéristique de la décomposition thermique du HMX [31] . Par rapport au HMX brut, les températures de décomposition thermique de HMX/MUF-1, HMX/MUF-2 et HMX/MUF-3 ont toutes diminué. Et la température des particules composites préparées par polymérisation interfaciale, bain de séchage et méthodes de mélange physique réduite de 2,58 °C, 8,76 °C et 10,14 °C, respectivement. Des résultats similaires ont été rapportés comme un abaissement de la température de décomposition du HMX lorsqu'il était recouvert d'un liant [32, 33]. Sous la prémisse de contenir 5 % de MUF, le degré décroissant est assez différent pour les températures maximales de décomposition des particules composites à base de HMX fabriquées par différentes méthodes ; de toute évidence, l'effet de la polymérisation interfaciale sur les performances de décomposition thermique du HMX est minime. Des situations similaires peuvent également être observées dans les particules composites RDX/MUF et CL-20/MUF (comme observé sur la figure 7c). Cela peut être pertinent pour la morphologie et la compacité du revêtement de HMX/MUF, et le revêtement uniforme contribue à la stabilité du processus de décomposition thermique des particules composites. Par conséquent, afin d'améliorer la stabilité thermique des particules composites, c'est un moyen efficace de sélectionner un matériau de revêtement avec d'excellentes propriétés thermiques. De plus, dans le cadre du choix d'un liant particulier, cela peut être un bon moyen d'envisager l'utilisation d'une méthode de polymérisation interfaciale pour préparer des particules composites.
Sensibilités
Pour étudier les performances de sécurité des échantillons, des tests de sensibilité aux chocs et au frottement ont été effectués, et les résultats sont présentés sur la figure 8. Comme on peut le voir, parmi les traitements de désensibilisation effectués sur HMX, RDX et CL-20, MUF a l'effet désensibilisant le plus significatif sur les particules composites préparées par le procédé de polymérisation interfaciale. Par rapport aux bruts HMX, RDX et CL-20, la hauteur caractéristique H 50 augmenté de 21,6 cm, 31,8 cm et 15,3 cm à 73,4 cm, 85,6 cm et 64,03 cm, respectivement (Fig. 8a), améliorant ainsi considérablement les performances de sécurité. En outre, on peut voir à partir de la figure 8b que la sensibilité au frottement du GPBX fabriqué par ces trois méthodes différentes est inférieure à celle des composés explosifs non enrobés. Fait intéressant, les trois échantillons préparés par la polymérisation interfaciale présentent la plus faible sensibilité au frottement. Plus important encore, par rapport aux rapports précédents [7, 18, 26], les performances de sécurité du GPBX fabriqué par polymérisation interfaciale sont optimales. L'effet de désensibilisation est incroyable. Ceci peut être expliqué par la théorie du hotspot [34]. Le MUF est appliqué avec succès sur la surface du HMX, ce qui peut produire un certain effet tampon sous un stimulus mécanique externe, ralentissant efficacement la formation de points chauds. Schematic diagram of desensitization effect of composite particles prepared by three different techniques can be seen from Fig. 9. Obviously, with the same proportion of MUF binder, the composite particles fabricated by interfacial polymerization possess the most distinct desensitization effect, attributing to more uniform particle morphology. The uniform, small particle size distribution between the particles increases the gap between themselves, and the force area of the same quality composite particles increases, which reduces the stress concentration between the particles and effectively prevents the formation of local hot spots.
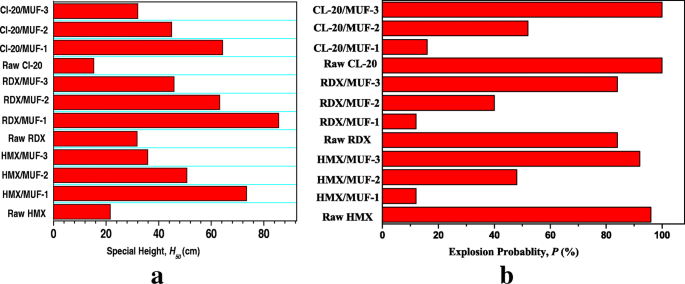
Impact sensitivity of samples:a impact sensitivity and b friction sensitivity
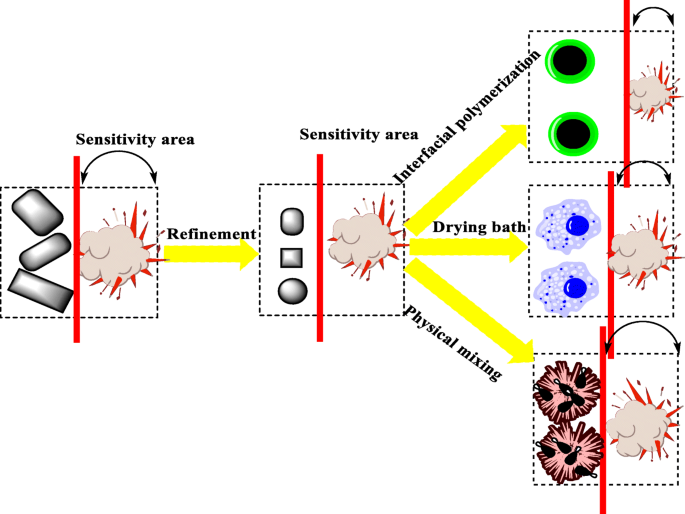
Schematic diagram of sensitivity
Conclusions
Via ultrasonic assistance, nine different composite particles were fabricated by a simple physical mixing method, an improved drying bath method, and an optimized interfacial polymerization method. XRD and FT-IR analysis did not show any change in the crystal structure before and after the preparation of HMX and CL-20, still maintaining β-HMX and Ɛ-CL-20, respectively. Compared with the raw explosives, the thermal decomposition peak temperature of the composite energetic particles after adding MUF was reduced; however, the reduction effect of the thermal decomposition peak temperature of the sample 3 was not significant. The characteristic height H50 of the composite particles prepared by interfacial polymerization method increased by three to four times, most obviously improving the safety performance. In short, HMX/MUF, RDX/MUF, and CL-20/MUF particles prepared by each method have similarities in morphology, particle size, and even performance. In particular, the three composite particles fabricated by interfacial polymerization method possess better thermal stability and safety performance with smooth surfaces, dense and uniform coating layers. Therefore, in order to improve the thermal stability of the composite particles, it is an effective approach to select a coating material with excellent thermal performance. And under the premise of choosing a specific binder, it may be effective to prioritize the use of interfacial polymerization method to prepare composite particles. This study provides certain reference for the application of high-energy and low-sensitivity ammunition in weapon firepower and rocket systems.
Abréviations
- CL-20:
-
Hexanitrohexaazaisowurtzitane
- DSC :
-
Calorimétrie différentielle à balayage
- ESV:
-
Emulsion solvent evaporation
- FI-IR:
-
Fourier-transform infrared spectra
- GPBX:
-
Green polymer-bonded explosives
- HMX:
-
Cyclotetramethylenetetranitramine
- IHEs:
-
Insensitive high explosives
- MF:
-
Melamine formaldehyde
- MUF:
-
Melamine-modified urea-formaldehyde
- NC:
-
Nitrocellulose
- PF:
-
Phenolic resin
- RDX:
-
Cyclotrimethylenetrinitramine
- SEM :
-
Microscopie électronique à balayage
- UF:
-
Urea formaldehyde
- XRD :
-
Diffraction des rayons X
Nanomatériaux
- Nano revêtement pour plusieurs couleurs
- Contrôle complet de la polarisation térahertz avec bande passante élargie via des métasurfaces diélectriques
- Effets de la co-adsorption sur le transfert de charge interfaciale dans un composite quantum dot@dye
- Réponse des ostéoblastes aux revêtements microporeux dopés au cuivre sur du titane pour une meilleure intégration osseuse
- Synthèse de points quantiques de carbone co-dopés en pyridinique N, S en tant qu'imitateurs d'enzymes efficaces
- Réglage de la chimie de surface du polyétheréthercétone par revêtement d'or et traitement au plasma
- Réglage des morphologies de surface et des propriétés des films de ZnO par la conception de la couche interfaciale
- Amélioration de l'efficacité antitumorale et de la pharmacocinétique de la bufaline via les liposomes pégylés
- Chase Plastics s'associe à Interfacial sur des solutions de résine