Fabrication et caractérisation d'un nouveau support de catalyseur anodique en nanofibre de carbone composite Tio2 pour pile à combustible au méthanol direct via la méthode d'électrofilage
Résumé
Le platine (Pt) est le catalyseur couramment utilisé dans une pile à combustible à méthanol direct (DMFC). Cependant, le Pt peut conduire à un empoisonnement du catalyseur par des espèces carbonées, réduisant ainsi les performances du DMFC. Ainsi, cette étude porte sur la fabrication d'un nouveau composite TiO2 support de catalyseur anodique en nanofibre de carbone pour les piles à combustible au méthanol direct (DMFC) via une technique d'électrofilage. La distance entre la pointe et le collecteur (DTC) et le débit ont été examinés en tant que paramètres influençant la technique d'électrofilage. Pour garantir la fabrication du meilleur matériau catalytique, la nanofibre a subi plusieurs caractérisations et tests électrochimiques, notamment FTIR, XRD, FESEM, TEM et voltamétrie cyclique. Les résultats montrent que D18, fabriqué avec un débit de 0,1 mlh −1 et DTC de 18 cm, est une nanofibre ultrafine avec le plus petit diamètre moyen, 136,73 ± 39,56 nm. Il a présenté l'activité catalytique et la valeur de surface active électrochimique les plus élevées à 274,72 mAmg −1 et 226,75m 2 g −1 PtRu , respectivement, par rapport aux autres échantillons.
Contexte
La pile à combustible à méthanol direct (DMFC) est l'un des futurs systèmes de production d'énergie renouvelable et très respectueux de l'environnement. Le système génère de l'énergie électrique à l'aide d'un combustible liquide (méthanol) directement sans aucun dispositif supplémentaire ni processus de combustion. Les avantages des DMFC sont leur simplicité, leur énergie spécifique élevée, leur faible température de fonctionnement et leur démarrage facile avec un ravitaillement instantané [1]. Cependant, les systèmes DMFC souffrent encore de plusieurs limitations, telles que l'empoisonnement du catalyseur et une cinétique de réaction lente, qui conduisent à des performances et à une puissance de sortie faibles du système [2]. Ces deux limitations sont dues au catalyseur et au matériau utilisé dans ce système.
Le platine (Pt) est le catalyseur couramment utilisé dans le DMFC. Cependant, le Pt peut conduire à un empoisonnement du catalyseur par des espèces carbonées, réduisant ainsi les performances du DMFC. Plus tard, le platine-ruthénium (PtRu) est introduit pour augmenter la vitesse de réaction, mais le paramètre cinétique du catalyseur reste l'un des problèmes majeurs du DMFC. Par conséquent, l'altération vers ce catalyseur bimétallique commence à se placer dans le domaine du catalyseur DMFC. L'une des approches les plus attrayantes parmi les chercheurs consiste à introduire l'oxyde métallique et les nanomatériaux en tant que composant catalytique latéral. Dioxyde de titane (TiO2 ) est un oxyde métallique qui attire beaucoup d'attention de la part des développeurs de recherche. TiO2 possède diverses propriétés bénéfiques, qui sont non toxiques, ininflammables et très résistantes à la corrosion [1], peuvent augmenter la stabilité électrochimique et thermique [3] et affecter les propriétés électroniques et le mécanisme bifonctionnel des catalyseurs composites [4]. Ito et al. [5] ont développé PtRu/TiO2 -nanofibre de carbone intégrée (CNF) (PtRu/TECNF), et Ercelik et al. [6] ont présenté le PtRu/C-TiO2 comme électrocatalyseur dans l'application DMFC, et le résultat montre que les performances de ce nouvel électrocatalyseur composite sont supérieures à celles du catalyseur PtRu.
Le nanomatériau est l'une des nanotechnologies qui a fasciné dans un large éventail d'applications, y compris la conversion d'énergie. Il existe de nombreux types de nanomatériaux dans le domaine de la conversion d'énergie, qui sont des nanofibres, des nanotubes, des nanofils, des nanotiges et autres. Ce matériau devient la principale attraction dans la recherche sur les matériaux énergétiques en raison de la réduction dimensionnelle à l'échelle nanométrique qui peut affecter de nombreuses étapes élémentaires, y compris le transfert de charge et le réarrangement moléculaire, ainsi que les propriétés de surface pour fournir des fractions de volume interfacial élevées et des taux de réaction améliorés. sept]. Cette étude se concentre sur les structures de nanofibres pour les deux matériaux, TiO2 oxyde métallique et carbone. Cela est dû aux propriétés spéciales des nanofibres qui peuvent fournir des rapports surface/volume et d'aspect élevés [7], une conductivité électrique élevée, une bonne résistance mécanique et une dispersion uniforme du catalyseur, ce qui peut augmenter l'activité électrocatalytique [8].
Les nanofibres peuvent être produites par plusieurs procédés, notamment le soufflage par fusion, la polymérisation interfaciale, l'électrofilage et la précipitation de polymère induite par un antisolvant [9]. Récemment, l'électrofilage est le principal choix des chercheurs en raison du grand avantage de produire des structures de nanofibres ultrafines. L'électrofilage est un procédé unique pour la formation de fibres avec des diamètres submicroniques (de l'ordre du nanomètre au micromètre) en utilisant des solutions à base de polymères ou des fusions par des forces électrostatiques [10]. Il y a trois composants principaux pour l'électrofilage :une alimentation haute tension (plusieurs dizaines de kV), la filière (seringue avec une aiguille) et un collecteur mis à la terre (par exemple, une plaque ou un collecteur rotatif) [11, 12]. La figure 1 illustre le processus global et la configuration du processus d'électrofilage. Par conséquent, l'électrofilage est populaire en raison de sa procédure simple, polyvalente, à haut rendement, efficace et ayant un processus plus économique [7, 13].
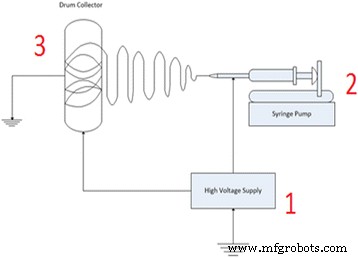
Installation d'électrofilage pour tous les composants principaux
Ce processus a plusieurs paramètres qui peuvent être ajustés afin d'obtenir les structures de nanofibres optimales, que ce soit pour le diamètre ou la morphologie de surface, et les paramètres d'influence sont différents pour chaque matériau. Les paramètres peuvent être divisés en trois catégories principales :paramètres de solution, ambiants et de processus. Cette étude est centrée sur les paramètres du procédé, et le débit de solution et la distance entre la pointe de l'aiguille et le collecteur (DTC) ont été choisis comme principaux paramètres d'influence pour obtenir le plus petit diamètre. Ceci est dû au faible nombre de recherches focalisées sur ces paramètres [14], même s'ils ont été considérés comme des variables principales pour l'obtention de nanofibres ultrafines [15,16,17,18].
Ainsi, cette étude présente le composite TiO2 nanofibre de carbone comme support de catalyseur sur l'électrode d'anode. Cette combinaison du composite devrait augmenter l'activité électrocatalytique et réduire l'empoisonnement du catalyseur afin d'améliorer les performances globales du DMFC. Les principaux objectifs de cette étude sont de fabriquer le plus petit diamètre possible de nanofibres pour augmenter la surface et fournir un point plus actif pour la réaction catalytique et améliorer les performances du DMFC. La fabrication de nanofibres implique plusieurs étapes, notamment des processus sol-gel, électrofilage, stabilisation et carbonisation. Pour obtenir les nanofibres de plus petit diamètre, les paramètres d'électrofilage du débit et du DTC sont pris comme variables principales dans cette étude. Les nanofibres préparées sont caractérisées par spectroscopie infrarouge à transformée de Fourier (FTIR), diffraction des rayons X (XRD) et microscopie électronique à balayage (FESEM). Tous les supports de catalyseur avec différents paramètres d'électrofilage sont déposés sur PtRu (PtRu/TiO2 -CNF) et évalués par analyse de la surface active électrochimique (ECSA) et voltamétrie cyclique (CV) pour évaluer les performances et déterminer leur potentiel en tant que supports de catalyseur dans les DMFC. Les résultats expérimentaux montrent l'effet des paramètres d'électrofilage sur le diamètre des nanofibres, ainsi que leur potentiel dans les applications DMFC.
Méthodes/Expérimental
Matériaux
Du poly(acétate de vinyle) (PVAc, Mw = 500 000), du diméthylformamide (DMF, 99,8 %), de l'isopropoxyde de titane (TiPP, teneur à 97 %), de l'acide acétique (99,7 %) et du précurseur Ru (teneur de 45 à 55 %) ont été obtenus de Sigma-Aldrich Co., Ltd., tandis que le précurseur de Pt (teneur de 40 %) et l'éthanol (99,8 %) ont été reçus de Merck, Allemagne et de R&M Chemical Reagents, respectivement. Tous les produits chimiques ont été utilisés sans autre purification. L'appareil principal, la machine d'électrofilage, porte la marque Nfiber N1000, Progene Link Sdn. Bhd., et le concasseur de cellules à ultrasons INS-650Y provient d'INS Equipments Trading Co., Ltd., Chine.
Préparation du TiO2 -Nanofibres CNF
La méthode sol-gel commence par la préparation d'une solution de polymère, où le PVAc (11,5 % en poids), en tant que source de carbone, a été dissous dans le solvant DMF. La solution de polymère a été agitée à 60 °C pendant 1 h, puis agitée pendant une nuit à température ambiante. Le TiO2 le précurseur, le TiPP et la solution de polymère ont été mélangés dans un rapport de 1:1, et une petite quantité d'acide acétique et d'éthanol a été ajoutée à la solution de polymère. Le mélange a été homogénéisé par un broyeur de cellules à ultrasons pendant 60 s. Ensuite, la solution a été transférée dans une seringue pour injection dans une unité d'électrofilage de nanofibres. La tension appliquée était de 16 kV, tandis que le débit et le DTC étaient manipulés dans la plage de 0,1 à 0,9 mLh −1 et 14-18 cm. Le débit a été fixé à 0,1, 0,5 , et 0,9 mLh −1 , notés F0.1, F0.5 et F0.9, respectivement. Les échantillons avec des valeurs DTC de 14, 16 et 18 cm sont respectivement notés D14, D16 et D18. La nanofibre fabriquée a été laissée au repos pendant 5 h à température ambiante avant d'être stabilisée pendant 8 h à 130 °C. La nanofibre stabilisée a été carbonisée à 600 °C pendant 2 h sous atmosphère d'azote à l'aide d'un four tubulaire, puis broyée au mortier et au pilon pendant 5 min avant d'être réutilisée dans cette étude. La charge de masse pour tous les échantillons est la même, qui est de 6,67 mgs −1 .
Dépôt de catalyseur
Le TiO2 -Des nanofibres de CNF ont été ajoutées dans un mélange d'alcool isopropylique (IPA) et d'eau déminéralisée (eau DI) et soniquées dans un bain à ultrasons pendant 20 min. Le précurseur du catalyseur au platine et au ruthénium (20 % en poids avec un rapport 1:1) a été mélangé à la solution et agité pendant 20 min. Ensuite, le pH de la solution mélangée a été ajusté avec une solution de NaOH jusqu'à atteindre pH 8. La température a été augmentée à 80 °C et 25 ml de NaBH 0,2 M4 a été ajouté goutte à goutte dans la solution mélangée. La solution a été agitée pendant encore 1 h. Le mélange a ensuite été refroidi, filtré et lavé à plusieurs reprises. La poudre de catalyseur a été séchée à 120 °C pendant 3 h et finalement broyée à l'aide d'un mortier et d'un pilon pour obtenir une poudre de catalyseur fine qui était prête à être utilisée dans les tests de performance.
Caractérisation du catalyseur
Le composé chimique dans le support du catalyseur a été identifié à l'aide de la spectroscopie infrarouge à transformée de Fourier (FTIR, PerkinElmer) et la diffraction des rayons X (XRD, D8 Advance/Bruker AXS, Allemagne) a été utilisée pour analyser le motif et la structure cristalline des échantillons. La morphologie et la distribution des tailles des échantillons ont été analysées par microscopie électronique à balayage à émission de champ (FESEM, SUPRA 55VP). La microscopie électronique à transmission (MET, Tecnai G2 F20 X-Twin) a été utilisée pour observer la structure détaillée et la distribution élémentaire des nanofibres.
Évaluation de la mesure électrochimique
Les performances ont été mesurées pour tous les catalyseurs fabriqués avec différents paramètres. Le catalyseur PtRu a été déposé sur le TiO2 -Support de catalyseur CNF pour évaluation par mesures électrochimiques. Ces mesures ont été obtenues à l'aide d'un système de cellule à trois électrodes, qui utilise la voltamétrie cyclique (CV) pour examiner l'activité du catalyseur dans la réaction d'oxydation du méthanol (MOR) à l'aide d'un poste de travail électrochimique Autolab. Le système de cellule à trois électrodes fonctionnait à température ambiante et impliquait une électrode de Pt, d'argent/chlorure d'argent (Ag/AgCl) et de carbone vitreux (GCE, 3 mm de diamètre) comme compteur, référence et électrode de travail. Avant de commencer la mesure, le GCE a été nettoyé avec de l'alumine et du papier à polir, en traçant plusieurs fois un motif arrondi ressemblant au nombre « huit ». Ensuite, le GCE a été rincé avec de l'eau DI et soniqué pendant 30 s avant utilisation. L'encre catalytique pour le GCE a été préparée en dispersant 15 mg de catalyseur dans un mélange de 400 ul d'eau DI, 400 ul d'IPA et 125 ul de solution de Nafion (5 % en poids) pendant 30 min. Ensuite, 2,5 μl d'encre catalytique ont été appliqués sur le GCE à l'aide d'une micropipette et séchés pendant 1 h à température ambiante avant d'être chauffés à 80 °C pendant 30 min supplémentaires. L'électrolyte était une solution de 0,5 M H2 SO4 dans 2 M de méthanol, et il a été barboté pendant 20 min avec de l'azote gazeux pour éliminer tout oxygène. La mesure du CV a été effectuée sur une plage de potentiel de − 0,1 à 1,1 V par rapport à Ag/AgCl à une vitesse de balayage de 50 mVs −1 .
Résultats et discussion
Caractérisation structurelle
Effet du débit
La spectroscopie FTIR a été réalisée sur le TiO2 -Échantillons CNF pour identifier les composés chimiques présents. Les spectres IR des échantillons produits à différents débits sont illustrés à la Fig. 2. Les spectres ont révélé des signaux de liaison chimique représentatifs de TiO2 et carbone. Les pics moyens et larges à 3 200-3 600 cm −1 représentent des groupes fonctionnels O-H, tandis que la bande d'absorption C=O nette et forte était située dans la région de 1550 à 1850 cm −1 [19]. Les pics pour les alcanes (groupes C-H) sont faibles et larges et situés dans les régions de 1 300 à 1 450 cm −1 . Cependant, les groupes C-C apparaissent à des nombres d'onde très faibles, inférieurs à 500 cm −1 [19] et n'existent pas dans les spectres en raison de la faible plage de nombre d'onde (4000 cm −1 < nombre d'onde > 50 cm −1 ) produit par le spectre. Les bandes moyennes et nettes dans la région de 650 à 900 cm −1 appartiennent à des groupes Ti-O, comme suggéré par Ding et al. [20]. Les spectres IR présentent tous les groupes fonctionnels du TiO2 -Échantillons CNF. Tous les échantillons ont des nombres d'onde et des pics similaires, ce qui indique que le débit de la solution de polymère pendant l'électrofilage n'affecte pas les composés chimiques de l'échantillon.
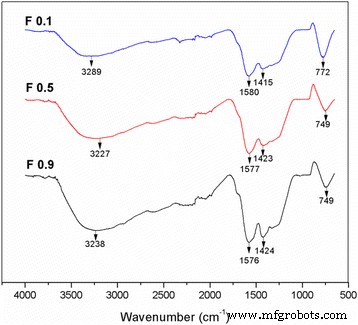
Les spectres IR pour le TiO2 -Échantillon CNF avec différents paramètres de débit dans la plage de 650 à 4000 cm −1 numéro d'onde
Le TiO2 -Échantillons CNF fabriqués à des débits de 0,1, 0,5 , et 0,9 mlh −1 sont notés respectivement F0.1, F0.5 et F0.9. La figure 3 montre les modèles XRD du TiO2 -Supports de catalyseurs CNF fabriqués avec différents débits. La figure 3a est un échantillon individuel pour le support de catalyseur, qui est un échantillon F0.1, pour regarder le modèle XRD en gros plan avec tout le matériau de pic dans TiO2 -CNF, tandis que la Fig. 3b est l'échantillon de débit entier impliqué. L'existence de TiO2 et le carbone dans l'échantillon est présenté. Le TiO2 se compose de deux structures, l'anatase et le rutile, car la température de carbonisation convertit une petite quantité d'anatase TiO2 en rutile TiO2 . Les pics de diffraction pour l'anatase TiO2 sont 25° (101), 38° (112), 48° (200), 53,9° (105), 62° (213) et 68° (116), tandis que ceux pour le rutile, TiO2 sont 27° (110), 36° (101), 41° (111) et 54° (211). La source de carbone est indiquée par plusieurs pics de diffraction, dont ceux à 30° (110) et 55° (211). Le TiO2 anatase et rutile formaient une structure tétragonale, tandis que le carbone était dans la structure cristallographique cubique à faces centrées.
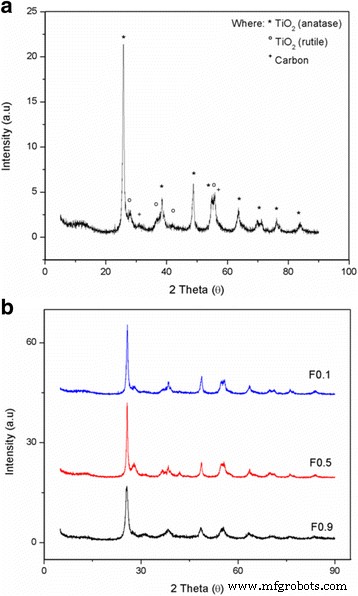
Diagrammes de diffraction des rayons X de a TiO individuel2 -Échantillon CNF et b échantillon de débit différent
Le débit dans la technique d'électrofilage s'est avéré affecter le diamètre des nanofibres, qui a été calculé à l'aide de l'analyse FESEM. L'image FESEM est présentée sur la figure 4, tandis que les résultats de la distribution des tailles et du diamètre sont présentés sur la figure 5 et le tableau 1. L'image confirme que la structure des nanofibres s'est formée à tous les débits étudiés. Les nanofibres F0.1 ont montré une morphologie lisse en raison du débit plus lent, ce qui donne suffisamment de temps pour que le solvant s'évapore, aidant à produire la structure lisse. Le diamètre moyen des nanofibres à partir de 100 mesures est de 161,18 ± 26,08 nm, qui est le plus petit diamètre parmi les échantillons produits à différents débits. Cependant, l'image FESEM de F0,5 montre la formation de rubans plats sur les nanofibres en raison du manque d'évaporation du noyau, c'est-à-dire que le solvant est piégé dans le noyau et diffuse dans l'atmosphère ambiante pour provoquer la structure du ruban plat [ 21]. F0.9 montre des nanofibres plus rugueuses avec des diamètres non uniformes, et plusieurs billes formées sur la morphologie des nanofibres. Cela se produit lorsque le débit est très supérieur à la valeur optimale, ce qui réduit le temps de séchage avant que la fibre n'atteigne le collecteur. Les diamètres moyens des nanofibres de F0,5 et F0.9 étaient supérieurs à ceux de F0.1, qui étaient respectivement de 220,28 ± 38,01 et 286,33 ± 50,83 nm. L'image FESEM révèle que le diamètre des nanofibres augmente à mesure que le débit augmente pendant l'électrofilage. F0.1, qui a un débit de 0,1 mLhr −1 , a été utilisé pour une analyse plus approfondie de l'effet du DTC sur le diamètre des nanofibres.
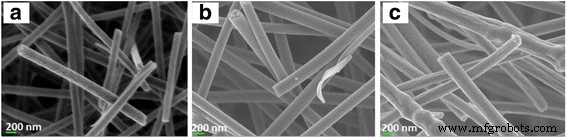
Image FESEM de a TiO2 -CNF (F0.1), b TiO2 -CNF (F0.5), et c TiO2 -CNF (F0.9) au grossissement ×30 000
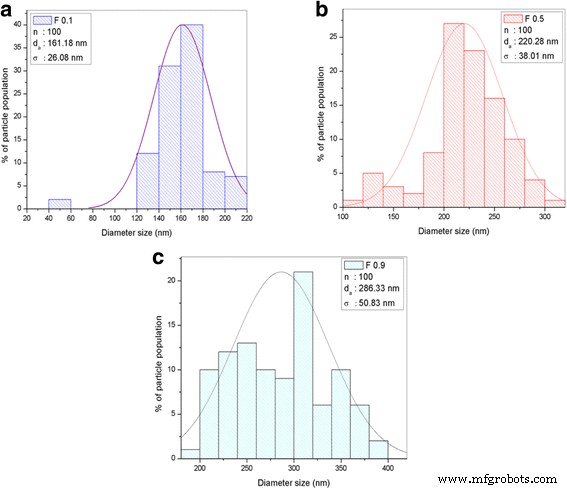
Données d'histogramme de distribution de taille de diamètre avec le paramètre de n, da , et . un TiO2 -CNF (F0.1). b TiO2 -CNF (F0.5). c TiO2 -CNF (F0.9)
Effet de la distance entre la pointe et le collecteur
Le TiO2 synthétisé -Les supports de catalyseur CNF ont été analysés par FTIR pour évaluer la liaison chimique dans les échantillons, et les spectres IR des échantillons sont illustrés sur la figure 6. Les spectres IR montrent trois échantillons avec différents paramètres DTC après le processus de carbonisation. Tous les échantillons synthétisés montrent l'existence de liaisons O-Ti-O et d'ions carbonate, où les pics et les nombres d'onde dans les spectres étaient dans la même plage que ceux des échantillons F0.1, F0.5 et F0.9 dans le section précédente. Les nombres d'onde étaient suffisamment proches pour indiquer la similitude des échantillons, y compris les échantillons produits à différents débits sur la figure 2. Cependant, l'échantillon D14 montre l'existence d'un nouveau pic autour de 2 300 à 2 400 cm −1 , qui indiquent les vibrations d'étirement N-H. Ce pic peut être classé comme pic de sels d'amines tertiaires, où la liaison N-H est faible et sans valeur pratique pouvant être négligée [19]. La présence de cette liaison pourrait être due à l'élimination incomplète du composé solvant pendant le processus de carbonisation. Cette observation montre que les paramètres d'électrofilage du débit et du DTC n'influencent pas la liaison chimique dans les échantillons.
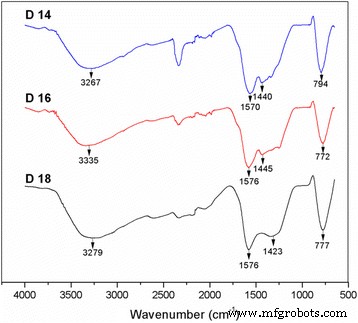
Le spectre IR pour le TiO2 -Échantillon CNF avec différents paramètres DTC dans la plage de 650 à 4000 cm −1 numéro d'onde
La cristallinité du TiO2 -Les supports de catalyseur CNF ont été analysés. Les modèles XRD sont illustrés à la figure 7a pour l'échantillon individuel et à la figure 7b pour le DTC. L'échantillon individuel de la figure 7a indique le modèle XRD en gros plan pour le DTC 18 afin de voir le pic d'existence pour tout le matériel impliqué. Les matériaux impliqués dans le support du catalyseur, TiO2 et le carbone, existent dans chaque échantillon. Les pics de diffraction ont été examinés sur une plage de 2θ de 5° à 90°, et les pics à 31° (110) et 55° (211) indiquent que du carbone avec une structure cristallographique FCC est présent dans le support de catalyseur. Le pic de diffraction pointu à 25° (101) a été attribué au TiO2 sous forme anatase, et il existe plusieurs autres pics pour l'anatase TiO2 , y compris ceux à 38° (004), 48° (200), 53° (105), 55° (211), 63° (204) et 69° (116). Les quatre autres pics de diffraction à 27° (110), 36° (101), 41° (111) et 54° (211) appartiennent au rutile TiO2 . TiO2 anatase et rutile ont une structure cristallographique tétragonale.
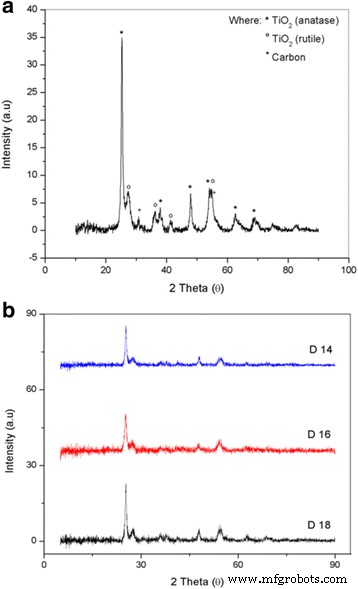
Diagrammes de diffraction des rayons X de a TiO individuel2 -Échantillon CNF et b échantillon DTC différent
TiO2 -Les nanofibres CNF ont été fabriquées par électrofilage avec différentes valeurs DTC, notées D14, D16 et D18. Le DTC a été varié à 14, 16 et 18 cm. Le diamètre de la nanofibre a été calculé en utilisant l'analyse FESEM. La figure 8 montre les images FESEM des échantillons avec différentes valeurs DTC à un grossissement de × 30 000. L'effet de la variation du DTC sur le diamètre des nanofibres a été estimé à l'aide de la distribution granulométrique (diamètre), comme illustré sur la figure 9, et les valeurs sont présentées dans le tableau 2. La distribution du diamètre comprend plusieurs paramètres, n (nanoparticules population), da (taille moyenne arithmétique des particules) et (écart type) [22].
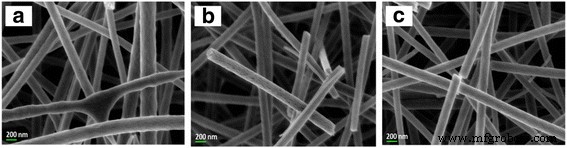
Image FESEM de a TiO2 -CNF (D14), b TiO2 -CNF (D16), et c TiO2 -CNF (D18) au grossissement ×30 000
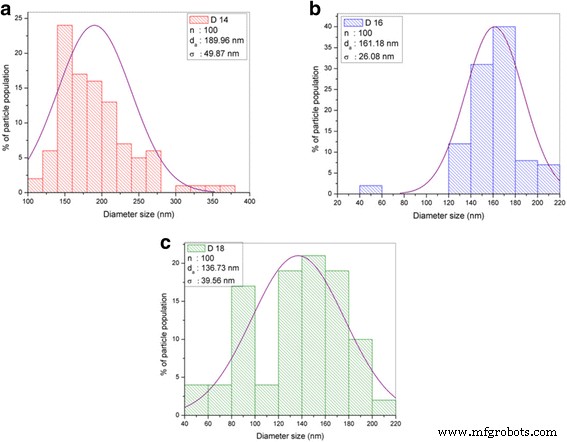
Données d'histogramme de distribution de taille de diamètre avec le paramètre de n, da , et . un TiO2 -CNF (D14). b TiO2 -CNF (D16). c TiO2 -CNF (D18)
Le plus petit diamètre moyen était de 136,73 ± 39,56 nm (90-170 nm), appartenant à D18, suivi de D16 et D14 avec des diamètres de 161,18 ± 26,08 et 189,96 ± 49,87 nm, respectivement. Plus les distances pointe-collecteur sont longues, plus le diamètre des nanofibres est petit. Ce comportement est dû au temps de dépôt et à l'intervalle d'instabilité de fouettage pendant le processus d'électrofilage. La distance plus longue fournit un temps de dépôt plus long, et pendant cette période, le phénomène d'instabilité de fouettage se produit, également connu sous le nom de mécanisme d'amincissement et de division. Ce phénomène est dû aux interactions entre les ions chargés et le champ électrique [17]. Lorsque la force électrique appliquée à la pointe de la buse atteint une valeur critique, la densité hautement chargée et la force viscoélastique divisent les jets en jets plus petits, créant un chemin courbé, sinueux et en spirale vers le collecteur. Lorsque le DTC est plus long, la division du jet se produit à plusieurs reprises, ce qui entraîne des fibres ultrafines et de plus petit diamètre. Par conséquent, le plus petit diamètre appartient à l'échantillon D18 avec un débit de 0,1 mLh −1 et DTC de 18.
Le diamètre des nanofibres fabriquées, TiO2 -CNF, est comparé à l'étude précédente du diamètre des nanofibres pour TiO2 -à base de nanofibres, et cette comparaison est présentée dans le tableau 3. Les résultats montrent que le TiO2 -CNF a le plus petit diamètre de nanofibre avec 136,73 ± 39,56 nm. Cela est dû au paramètre optimal utilisé pendant la méthode d'électrofilage ; qui est faible en débit et valeur élevée de DTC. Ainsi, avec un débit plus petit et une valeur DTC plus élevée, le plus petit diamètre d'une nanofibre est produit. Cela montre que les paramètres d'électrofilage donnent le plus grand effet au diamètre de la nanofibre. Même si un DTC plus long et un débit plus petit sont préférables, il existe des valeurs optimales pour ces paramètres, car ces paramètres peuvent entraîner une perte de poids. Cela se produit en raison d'une évaporation excessive, dans laquelle la nanofibre se forme avant d'atteindre le collecteur, permettant à la nanofibre de se déplacer librement vers des régions indésirables.
L'échantillon D18 avec un débit de 0,1 mLh −1 et le DTC de 18 a été sélectionné pour l'analyse MET afin d'examiner la morphologie et d'obtenir la taille du diamètre. L'image TEM et la cartographie élémentaire du TiO2 -Le support du catalyseur CNF est illustré à la Fig. 10. L'image TEM montre que TiO2 -Le CNF donne des nanofibres lisses et soyeuses d'un diamètre de 135,38 nm. Le diamètre est dans la même plage (90-170 nm) que celui obtenu à partir de l'analyse FESEM. La cartographie est utilisée pour examiner la distribution de TiO2 et carbone sur nanofibre. Les résultats reflètent que TiO2 et du carbone formé uniformément dans la structure des nanofibres, en raison de la répartition homogène de la solution de polymère et du TiO2 précurseur lors de la méthode sol-gel. Cette cartographie montre également l'emplacement des matériaux, dans lesquels TiO2 et le carbone sont situés sur toute la surface des nanofibres, ce qui favorise la création de zones de réaction actives lors de la catalyse. Les autres échantillons de nanofibres devraient avoir la même distribution uniforme de TiO2 et carbone. La taille des particules de TiO2 et le carbone dans les échantillons de nanofibres et leur effet sur le MOR est discuté dans la section suivante.
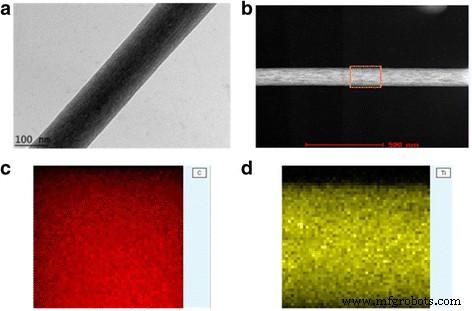
TiO2 -Support catalyseur CNF a Image TEM (échelle 100 nm), b Image TEM pour TiO2 et C cartographie des nanofibres, c cartographie pour la nanofibre C, et d cartographie pour TiO2 nanofibre
Caractérisation électrochimique de la réaction d'oxydation du méthanol
La caractérisation électrochimique comprend trois étapes principales, qui sont la caractérisation de l'activité électrochimique, les performances électrocatalytiques, ainsi que la stabilité et la durabilité à long terme. L'activité électrochimique et les performances électrocatalytiques ont été analysées par CV en utilisant un système à trois électrodes pour acquérir des informations qualitatives et quantitatives sur la réaction impliquée [23]. La figure 11a, b montre l'image MET du catalyseur PtRu déposé à la surface des F0.1 et D18 TiO2 -CNF prend en charge, respectivement. Le catalyseur PtRu était uniformément réparti sur la surface des nanofibres dans les deux F0.1 et D18. La figure 11c montre le modèle XRD de D18 PtRu/TiO2 -CNF, tandis que le tableau 4 donne les données pour le diamètre des nanofibres, obtenues à partir de FESEM, et la taille des cristallites des particules dans les échantillons, obtenues à partir de XRD. Le tableau 4 montre que les échantillons de la série F (F0.1, F0.5 et F0.9) avec catalyseur ajouté ont un TiO2 (anatase) taille des cristallites d'environ 20 à 22 nm. Le changement de diamètre des nanofibres a peu d'effet sur la taille des cristallites de TiO2 , tandis que la taille des cristallites du carbone change à mesure que le diamètre des nanofibres augmente de 15,9 nm dans F0.1 à 25,8 nm dans F0.9. La taille des cristallites de Pt a également tendance à augmenter avec la taille des cristallites de carbone. La taille des cristallites de Pt supportée sur F0.1, F0.5 et F0.9 est de 5,67, 8,04 et 9,75 nm, respectivement. Les changements dans la taille des cristallites de Pt sont dus aux propriétés de surface de la nanofibre. Le tableau 4 montre également la taille des cristallites de PtRu pris en charge sur les échantillons de la série D. Le diamètre des nanofibres diminue en valeur de D14 à D16 à D18. Contrairement aux échantillons de la série F, la taille des cristallites de TiO2 (anatase) dans les échantillons de la série D diminue à mesure que le diamètre des nanofibres diminue. Le TiO2 la taille des cristallites est de 23,40, 21,50 et 18,60 nm pour D14, D16 et D18, respectivement. La taille des cristallites du carbone et du Pt diminue également avec une diminution du diamètre des nanofibres. La taille des cristallites de carbone diminue de 17,3 nm dans D14 à 14,4 nm dans D18, tandis que la taille des cristallites de Pt supportée sur D14, D16 et D18 est de 5,44, 5,67 et 4,64 nm, respectivement. A partir de ces données, les changements dans les tailles des cristallites de TiO2 et le carbone dans la nanofibre entraînent des modifications des propriétés de surface de la nanofibre, entraînant des modifications de la taille des cristallites des particules de Pt déposées à la surface de la nanofibre.
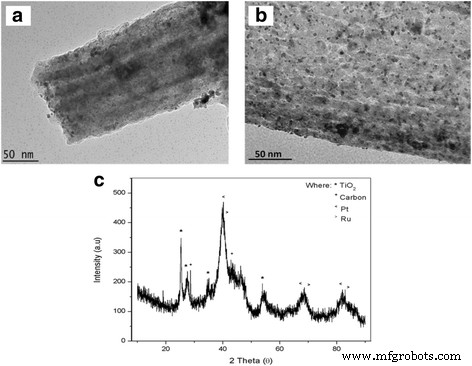
Image de PtRu déposé sur TiO2 -CNF a Image MET de PtRu/TiO2 -CNF en F0.1, b Image MET de PtRu/TiO2 -CNF en D18, et c Modèle XRD de PtRu/TiO2 -CNF de D18
La figure 12 montre les profils de CV du PtRu/TiO2 -CNF electrocatalysts with different catalyst supports in 0.5 M H2 SO4 Solution. The CV curve for F0.1, F0.5, and F0.9 are shown in Fig. 12a, while D14, D16, and D18 are shown in Fig. 12b. Hydrogen adsorption-desorption by Pt occurs around − 0.2 to 0.1 V vs. Ag/AgCl. The mass loading for all the electrocatalyst in this profile is the same that as 0.57 mgcm −2 . The PtRu/TiO2 -CNF supported on D18 exhibits a steep current peak for hydrogen adsorption in comparison in the other D series samples, while F0.1 has a steep peak in comparison with the F series samples. The peak indicates that the active surface area on the PtRu/TiO2 -CNF electrocatalyst and the ECSA can be calculated from the equation:ECSA = Q /(Γ .W Pt ). Where, Q is the integral of the hydrogen adsorption area, Γ is the constant for the charge required to reduce the proton monolayer on the Pt (2.1 CmPt −2 ), and W Pt is the mass loading of Pt. Table 5 shows the ECSA of all the catalyst samples in units of m 2 g −1 with mass loadings according to the mass of PtRu. From Table 5, the ECSA for PtRu supported on F0.1, F0.5, and F0.9 is 131.29, 65.05, and 25.03 m 2 g −1 , respectively. The ECSA value decreases with increasing Pt crystallite size in the catalyst samples. The catalyst supported on D14, D16, and D18 has an ECSA value of 21.48, 131.29, and 226.75 m 2 g −1 , respectively. As shown previously, the value of the Pt crystallite size in the D series samples decreases from D14 to D18, and thus, the ECSA increases according to Pt crystallite size. Smaller size particles lead to an increase in the active surface area of the catalyst. Overall, the electrospinning parameters clearly show big influence towards the diameter and surface properties (surface morphology) of nanofibers.
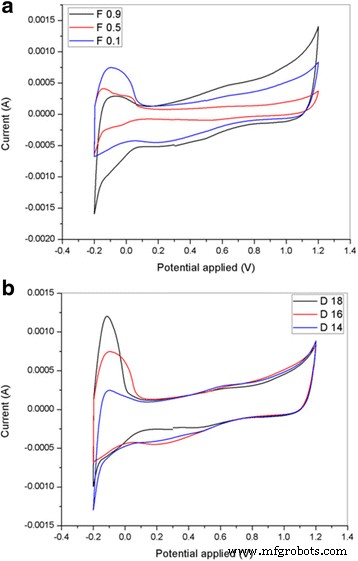
Cyclic voltammetry profiles of the PtRu/TiO2 -CNF with a different flow rate, F0.1, F0.5, F0.9, and b different DTC, D14, D16, and D18, in 0.5 M H2 SO4 solution at the scan rate of 50 mVs −1
The electrocatalytic performance of PtRu supported on the different F and D series nanofibers is tabulated and plotted in Table 5 and Fig. 13. The CV curve was measured in 2 M methanol and 0.5 M H2 SO4 solution saturated with N2 gas at room temperature. The mass loading for all the electrocatalyst is the same which is 0.57 mgcm −2 . Figure 13 shows multiple CV curves over a potential range of − 0.1 to 1.1 V vs. Ag/AgCl. Figure 13a shows the CV graphs for PtRu supported on the F series nanofiber samples. As the diameter of the nanofiber decreases from sample F0.9 to F0.1, the current density in MOR increases, and the oxidation peak and onset potential of MOR shift towards positive values. On the other hand, in the D series nanofiber samples, the oxidation peak potential of the catalyst supported on D14, D16, and D18 is 0.754, 0.771, and 0.732 V (vs. Ag/AgCl), respectively. There is no pattern in the oxidation peak potential in the D series samples, and the onset potential is almost the same for each sample, at 0.36 V vs. Ag/AgCl. However, the peak current density at the oxidation peak potential of MOR increases in accordance to the catalyst support on D14, D16, and D18. The peak current density for D14, D16, and D18 is 201.45, 249.58, and 274.72 mAmg −1 PtRu , respectively. It can be clearly seen that the increase in the current density matches the patterns in the diameter, from FESEM analysis, and ECSA value. This shows that a smaller diameter size produces high surface area and increases the number of active sites on the electrocatalyst surface. The higher peak current for the composite electrocatalyst may result from the supporting material (TiO2 -CNF), where changes in the structure and the combination of materials can be very effective in producing positive effects on the metal-support interaction [5, 24].
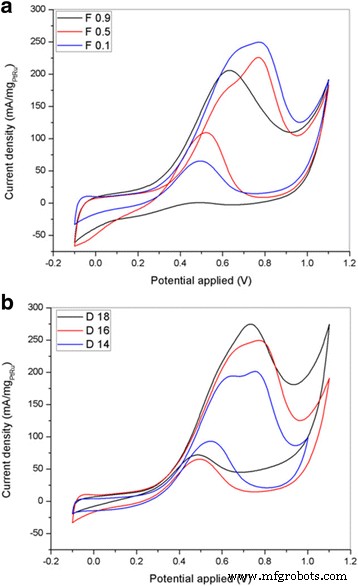
Cyclic voltammograms for PtRu/TiO2 -CNF with different a flow rate and b DTC of the catalyst support in 2 M methanol and 0.5 M H2 SO4 at the scan rate of 50 mVs −1
The reverse scan in the CV curve shows a small oxidation peak at a potential of approximately 0.49–0.55 V vs. Ag/AgCl. This second oxidation peak appeared due to the incomplete removal of oxidized carbonaceous species in the forward scan [25]. However, the ratio between the forward (If ) and reversed (Ib ) oxidation peak for PtRu/TiO2 -CNF (D18) exceeded 3.8, which means that the electrocatalyst has high tolerance towards carbonaceous species, reducing the potential for catalyst poisoning. This result shows that the combination of metal oxide and carbon nanofibers has a good potential for use in fuel cell applications.
Conclusion
TiO2 -CNF nanofibers can be fabricated via electrospinning, which is the main technique, and several other methods. The nanofibers are influenced by the flow rate and the DTC, which were examined as electrospinning process parameters, with three different samples for each parameter, denoted F0.1, F0.5, F0.9, D14, D16, and D18. The results showed that the TiO2 -CNF (D18) sample produced the smallest average diameter of 136.73 ± 39.56 nm. TiO2 -CNF was mixed with PtRu to form the composite catalyst, and its CV performance was examined. The current density of the PtRu/TiO2 -CNF (D18) sample is 1.4 times higher than that of PtRu/TiO2 -CNF (D14), while the ECSA of PtRu/TiO2 -CNF (D18) is 10 times higher than that of the other samples. Thus, the flow rate and DTC highly affect the diameter, morphology, and performance of the nanofibers. The nanofiber performance increased with decreasing nanofiber diameter, which shows the capability of the composite nanofiber catalyst to be an upcoming anode catalyst for DMFCs.
Nanomatériaux
- La méthode de fabrication de molécules artificielles remporte le prix du meilleur poster
- Composites de graphène et polymères pour applications de supercondensateurs :une revue
- Conception de matériaux de nanotubes de carbone soignés et composites par caractérisation porosimétrique
- Performances améliorées d'un nouveau catalyseur anodique PdAu/VGCNF pour l'électro-oxydation dans une pile à combustible au glycérol
- Fabrication, caractérisation et cytotoxicité de nanoparticules de carbonate de calcium dérivées de coquilles d'or conjuguées de forme sphérique pour des applications biomédicales
- Composite aérogel/soufre de charbon actif revêtu de polyaniline pour batterie lithium-soufre hautes performances
- Fabrication et caractérisation de nano-clips de ZnO par le procédé à médiation par polyol
- Nouveaux catalyseurs anodiques pour la pile à combustible à méthanol direct :caractérisations et performances des cellules individuelles
- Une méthode facile pour charger des nanoparticules de CeO2 sur des matrices de nanotubes de TiO2 anodiques