Fabrication de nanocomposites Yolk-Shell Cu@C en tant que catalyseurs hautes performances dans la carbonylation oxydative du méthanol en carbonate de diméthyle
Résumé
Un moyen facile a été développé pour fabriquer des composites jaune-coquille avec des noyaux de Cu accordables encapsulés dans des sphères de carbone creuses (Cu@C) avec un diamètre moyen d'environ 210 nm et une taille de cavité d'environ 80 nm. Au cours de la pyrolyse, le nanoespace confiné de la cavité creuse garantit que le processus de nucléation et de croissance des nanocristaux de Cu se déroule exclusivement à l'intérieur des cavités. La taille des noyaux de Cu peut être facilement ajustée de 30 à 55 nm en faisant varier la concentration en sel de cuivre. En créant délibérément une porosité de la coque par activation chimique KOH, à un rapport massique KOH/HCS optimisé de 1/4, les performances catalytiques pour la carbonylation oxydante du méthanol en carbonate de diméthyle (DMC) de l'échantillon activé sont remarquablement améliorées avec un TOF jusqu'à 8,6 h −1 à une conversion de méthanol de 17,1 %. Le catalyseur à coque jaune activé présente des propriétés catalytiques prometteuses impliquant la réutilisation avec une légère perte d'activité catalytique et une lixiviation négligeable des composants activés même après sept recyclages, ce qui est bénéfique pour la mise en œuvre d'une production propre pour le DMC chimique respectueux de l'environnement.
Contexte
Le carbonate de diméthyle (DMC) a attiré beaucoup d'attention en tant que bloc de construction largement utilisé en raison de son excellente biodégradabilité (par exemple, faible bioaccumulation et persistance) et de sa faible toxicité [1]. Les applications industrielles potentielles du DMC couvrent de nombreux domaines, tels que solvant non toxique, substitut alternatif du phosgène, additif pour carburant et intermédiaire pour la synthèse de polycarbonates et d'isocyanates [2,3,4,5]. Compte tenu des différentes méthodes de synthèse du DMC, la carbonylation oxydative du méthanol (MeOH) à l'aide de CO, O2 , et MeOH en tant que matières premières a représenté l'un des processus favorables proposés en raison du taux d'utilisation élevé de la source de carbone et des avantages environnementaux. Les catalyseurs utilisés dans cette réaction peuvent être principalement classés en deux types :les catalyseurs contenant du chlore et les catalyseurs sans chlore. Étant donné que certains problèmes, tels que de graves problèmes de corrosion, une détérioration de la qualité du produit et la désactivation du catalyseur, découlent de la perte de chlore des catalyseurs contenant du chlore, les catalyseurs sans chlore ont été largement étudiés [6, 7]. Le cuivre ou l'oxyde de cuivre supporté par du charbon actif (AC) a montré une activité catalytique prometteuse pour la synthèse de DMC [8,9,10], et les chercheurs ont suggéré que Cu est le centre actif de cette réaction [10,11,12,13]. Cependant, la désactivation des catalyseurs au cuivre supportés est généralement attribuée à l'agglomération de particules de cuivre, à la perte d'espèces actives et au changement d'état chimique du cuivre, parmi lesquels le premier est plus grave. Afin de surmonter ces inconvénients, la conception et la fabrication de nanoparticules encapsulées dans une enveloppe protectrice sont bénéfiques pour renforcer l'activité catalytique et la stabilité des centres réactifs dans la carbonylation oxydative du méthanol en DMC du point de vue technologique.
Le long de cette ligne, les nanostructures jaune-coquille (YSN) ou les nanocomposites de type hochet, dans lesquels les nanoparticules centrales (NP) sont encapsulées par une couche externe avec un espace libre interstitiel entre elles, ont été particulièrement populaires en raison de leurs nanostructures hiérarchiques/multiniveaux uniques. , et les propriétés optiques et électriques associées et un grand potentiel dans les applications catalytiques [14]. La coque de protection des YSN peut effectivement maintenir l'élément central stable même dans des conditions difficiles et exposer suffisamment sa surface active [15]. L'espace vide clos devrait être utile pour le stockage chimique, le compartimentage et le confinement des interactions hôte-invité, et plus important encore, fournir un environnement unique pour créer des actions concertées entre le noyau et une enveloppe perméable [16]. Ces caractéristiques de texture remarquables permettent aux YSN de fonctionner comme des candidats prometteurs pour satisfaire les exigences telles que la stabilité au frittage et la réutilisation pour les applications en catalyse. Parmi elles, les nanostructures de coque jaune-carbone ont immédiatement suscité un intérêt considérable en raison de la conductivité inhérente ainsi que de l'excellente stabilité chimique et thermique du revêtement de carbone [17,18,19,20,21].
Récemment, Lu et ses collègues ont rapporté la préparation de sphères creuses par assemblage induit par une interaction acide-base faible avec l'utilisation d'acide oléique comme modèle mou et d'acide dihydroxybenzoïque fonctionnel (DA) comme précurseur [22]. Ici, nous étendons leur travail pour développer une approche facile vers les YSN avec une taille de noyau de Cu accordable encapsulée à l'intérieur de sphères de carbone creuses (HCS) (Cu@C) en utilisant une stratégie de livraison en bouteille. La porosité de la coquille des catalyseurs hétérogènes Cu@C peut être ajustée par activation KOH, et ses effets sur les performances catalytiques et la stabilité dans la synthèse de DMC sont également étudiés.
Méthodes
Produits chimiques
L'acide 2,4-dihydroxybenzoïque (DA) a été obtenu auprès de J&K Scientific Ltd. Acide oléique, solution d'ammoniaque (25 %), formaldéhyde, nitrate de cuivre (Cu(NO3 )2 ·3H2 O), l'hydroxyde de potassium (KOH) et le méthanol (MeOH) ont été obtenus auprès de Sinopharm Chemical Reagent Co. Ltd. Tous les produits chimiques étaient de qualité analytique et utilisés sans autre purification. De l'eau déminéralisée obtenue à partir du système Milli-Q (Millipore, Bedford, MA) a été utilisée dans toutes les expériences. O2 (> 99,99 %) et le CO (> 99,99 %) ont été fournis par Beijing ZG Special Gases Science &Technology Co. Ltd.
Synthèse de sphères de carbone creuses (HCS)
Les sphères creuses en polymère (HPS) avec un noyau creux et une enveloppe en polymère ont d'abord été préparées en utilisant de l'acide oléique comme matrice molle et de la résine phénolique comme précurseur de carbone suivant la procédure rapportée par Lu et al. [22]. Dans une procédure typique, 2,5 mmol d'acide 2,4-dihydroxybenzoïque et 7,5 mmol de formaldéhyde ont été dissous dans 95 ml d'eau désionisée. Un volume de 5 ml d'une solution aqueuse contenant 56 μL d'acide oléique et 180 μL de solution d'ammoniac (25 %) a été ajouté à la solution préparée ci-dessus à 30 °C sous agitation lente pendant 30 min. Ensuite, le mélange a été transféré dans un autoclave vieilli hydrothermiquement pendant 4 h à 140 °C. Après centrifugation, lavé avec de l'eau déminéralisée et de l'éthanol, séché à 50 °C pendant une nuit, puis pyrolysé à 700 °C pendant 2 h sous flux d'azote, le HCS a été obtenu.
Synthèse de matériaux nanocomposites Cu@C
En règle générale, 0,3 g du HCS tel que préparé a d'abord été dispersé dans 30 mL de solution de nitrate de cuivre avec une plage de concentration différente de 0,03 à 0,24 M. Ensuite, le mélange a été transféré dans un autoclave pour subir une imprégnation hydrothermale à 100 °C pendant 10 h. L'échantillon imprégné résultant, noté HCS-Cu 2+ , a été récupéré par la même méthode que HPS. Après calcination à 400 °C pendant 2 h sous H2 /N2 (10 %/90 %), enfin, les nanocomposites jaune-coquille Cu@C-X (X = 0,03, 0,06, 0,12, 0,24) ont été obtenus.
Synthèse du catalyseur Cu@A-HCS avec la sphère de charbon actif KOH comme support
Le traitement du HCS avec du KOH est tenté, dans le but de modifier les caractères du support carboné et d'affecter davantage les performances du catalyseur Cu. Typiquement, 0,3 g de HCS ont été mélangés avec 0,15 g de KOH physiquement en l'absence d'eau. Après le prétraitement, l'échantillon a été chauffé dans un flux d'azote de 80 mL/min avec une vitesse de rampe de 10 °C/min jusqu'à 700 °C pendant 2 h, puis refroidi à température ambiante. Les charbons KOH post-traités ont été lavés à plusieurs reprises avec du HCl dilué puis avec de l'eau distillée jusqu'à ce qu'aucun ion chlore ne soit détecté (AgNO3 test). Après séchage à 60 °C pendant la nuit, une solution de nitrate de cuivre 0,12 M a été utilisée pendant l'imprégnation hydrothermale et d'autres procédures étaient identiques à celle de Cu@C-0,12, donnant finalement les échantillons modifiés désignés par Cu@A-HCS.
Les performances catalytiques de Cu@C-X (X = 0,03, 0,06, 0,12, 0,24) et Cu@A-HCS
La carbonylation oxydative du méthanol a été réalisée dans un autoclave en acier inoxydable de 25 mL revêtu de Téflon et équipé d'un agitateur magnétique. Dans une expérience typique, 0,2 g de catalyseur et 10 mL de méthanol ont été chargés dans l'autoclave, qui a ensuite été scellé hermétiquement, purgé trois fois avec du CO et ensuite mis sous pression à 3,0 MPa avec du CO et de l'O2 (PCO :PO2 = 2 :1) à température ambiante. La réaction s'est déroulée à 120 °C sous agitation continue à 750 tr/min pendant 1,5 h. Après la réaction, le réacteur a été refroidi à la température ambiante et dépressurisé. Les catalyseurs ont été séparés par filtration. Les concentrations de produits dans le filtrat ont été déterminées par chromatographie en phase gazeuse (GC) à l'aide d'un détecteur FID. La recyclabilité du catalyseur usé a été étudiée en effectuant une série d'essais consécutifs.
La principale réaction de la carbonylation oxydative du méthanol en carbonate de diméthyle a été illustrée ci-dessous :
2CH3 OH + 1/2 CO + O2 =(CH3 O)2 CO + H2 O.
La concentration de cuivre, conversion MeOH (CMeOH ), sélectivité DMC (SDMC ) et la fréquence de rotation (TOF) ont été calculés par les équations suivantes :
La concentration de cuivre (CCu , mmol/g) = teneur en Cu (% en poids)/63,55 × 1000.
Conversion MeOH (CMeOH , %) = méthanol ayant réagi/méthanol introduit × 100 %.
Sélectivité DMC (SDMC , %) = 2 DMC produit/méthanol ayant réagi × 100 %.
Fréquence de rotation = DMC produit/(la quantité molaire de cuivre × temps de réaction).
Caractérisation
Les diagrammes de diffraction des rayons X (XRD) ont été enregistrés sur un diffractomètre Rigaku D-Max 2500, en utilisant Cu K rayonnement (λ = 0,154 nm) à 40 kV et 100 mA, avec une vitesse de balayage de 4 ° min −1 à 2θ de 5° à 85°. L'analyse par microscopie électronique à transmission (MET) a été réalisée sur un microscope électronique à transmission à émission de champ JEM 2100F (JEOL, Tokyo, Japon) fonctionnant à 200 KeV. Les échantillons MET ont été préparés en immergeant des grilles de Cu revêtues de C dans des solutions d'éthanol d'échantillons et en les séchant à température ambiante. L'analyse thermogravimétrique (TG) a été réalisée sur un analyseur thermogravimétrique, STA 449 F3 Jupiter (NETZSCH), avec un N2 ou débit d'air de 50 mL/min. Les surfaces et les volumes des pores ont été déterminés à partir d'isothermes d'adsorption d'azote à 77 K en utilisant l'analyseur de surface 3H-2000PS2 (Beishide). Les surfaces spécifiques de Brunauer-Emmett-Teller (BET) ont été calculées à l'aide de données d'adsorption dans une plage de pression relative de P /P 0 =0,04-0,3. Les courbes de distribution de la taille des pores des mésopores ont été calculées par la méthode BJH (Barrett-Joyner-Halenda) à partir de la branche d'adsorption. Les volumes poreux totaux ont été estimés à partir de la quantité d'azote adsorbé à une pression relative (P /P 0 ) de 0,99. La teneur en cuivre est déterminée en dissolvant le catalyseur dans un mélange d'acide fort suivi d'une analyse par spectrométrie d'adsorption atomique (AAS) à l'aide d'un équipement SpectrAA-220 AAS. L'analyse du produit de réaction a été réalisée par chromatographie en phase gazeuse (GC; Agilent 6890) à l'aide d'un détecteur FID.
Résultats et discussion
Paramètres de texture et stabilité thermique du support tel que préparé
La surface BET et le volume des pores des échantillons impliqués dans les différentes étapes de préparation sont résumés dans le tableau 1. Comme le montrent la figure 1a et le tableau 1, le HPS obtenu a de faibles surfaces BET (~23 m 2 g −1 ). Ainsi, il est difficile de poursuivre l'introduction des précurseurs de catalyseur par la méthode d'imprégnation classique. Ainsi, nous utilisons un processus d'imprégnation hydrothermale pour améliorer la capacité de diffusion afin que le précurseur de cuivre puisse être aspiré avec succès dans la cavité du HPS. La surface BET du HPS et du HPS-Cu est passée de 23 à 15 m 2 g −1 certifié la déclaration. De plus, les images MET de la figure 2 confirment davantage les nanoparticules de Cu formées exclusivement dans les limites de la coque de carbone.
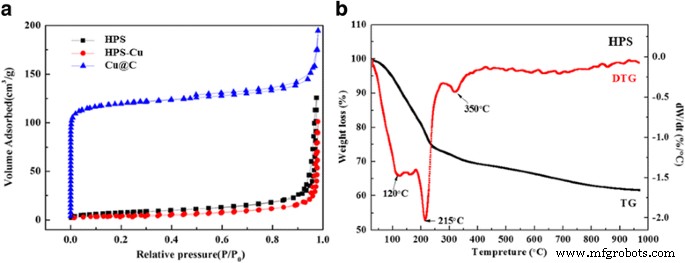
un N2 isotherme d'adsorption-désorption des produits obtenus après chaque étape :HPS, HPS-Cu 2+ , et Cu@C. b Profils TG-DTG de HPS
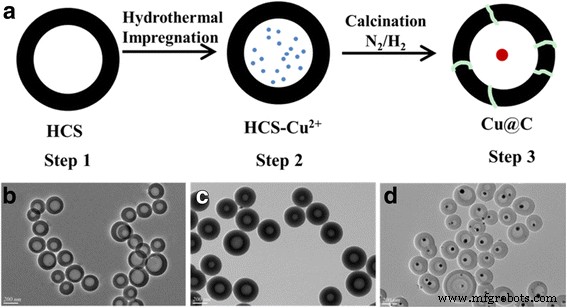
un Illustration schématique de la synthèse de nanocomposites Cu@C en condition d'imprégnation hydrothermale. Images MET des produits obtenus après chaque étape :b HCS, c HCS-Cu 2+ , et d Cu@C
Le processus de carbonisation du HPS est étudié par TG. La figure 1b montre le résultat de TG-DTG dans N2 . Tout au long de cet intervalle, la perte majeure de HPS apparaît vers 215 °C et est complète vers 350 °C. Cela peut être attribué à la décomposition de l'acide oléique incorporé à l'intérieur du HPS et à la carbonisation de la charpente polymère [22]. Ainsi, par rapport aux courbes TG des catalyseurs Cu@C (voir Fig. 5b), pour assurer la carbonatation complète du HPS et empêcher l'agrégation des nanoparticules de Cu, 400 °C a été déterminé comme température de préparation optimale.
Propriétés structurelles des nanocomposites Cu@C
En prenant comme exemple le nanocomposite jaune-enveloppe [email protected], la procédure de synthèse pour la préparation de structures jaune-enveloppe avec des NP de Cu encapsulées par une coque de carbone, suivant une stratégie d'expédition dans une bouteille, est illustrée à la figure 2a. La figure 2b, c montre des images TEM typiques du produit résultant obtenu à chaque étape. Comme on le voit, des HCS avec une taille uniforme d'environ 210 nm ont été synthétisés avec succès (Fig. 2b). Au cours du processus d'imprégnation hydrothermale, aucune différence évidente ne peut être observée entre les HCS et les HCS-Cu 2+ (Fig. 2c). Cependant, après calcination, la morphologie creuse est maintenue, mais des NP de Cu peuvent être observées en raison de la décomposition des sels de cuivre. Enfin, le Cu@C à structure vitelline (Fig. 2d) avec un diamètre d'environ 200 nm et une taille de cavité d'environ 80 nm est obtenu. La microscopie électronique à transmission à haute résolution (HRTEM) (Fig. 3b) montre que les particules centrales ont un espace de 0,18 nm indexé sur le plan Cu (2 0 0). Ceci est cohérent avec les résultats de XRD (Fig. 3c), où la diffraction culmine à 2θ = 43,3°, 50,4° et 74,1° sont devenus observables car Cu 2+ espèces sur le précurseur (HCS-Cu 2+ ) sont réduits en métal Cu sous atmosphère réductrice, correspondant respectivement aux plans cristallins spécifiques (1 1 1), (2 0 0) et (2 2 0) de Cu, qui sont basés sur la carte JCPDS 04-0836 . Le N2 -l'isotherme d'adsorption-désorption du [email protected] résultant présente une isotherme de type I, démontrant qu'il y a des micropores abondants sur les coquilles de carbone de [email protected] (Fig. 3d). Cet échantillon a une surface BET de 365 m 2 /g accompagné d'un volume poreux de 0,23 cm 3 /g. Une faible surface spécifique ainsi qu'une microporosité étroite sont généralement signalés comme les principaux inconvénients, limitant leurs applications, qui seront discutées ci-dessous. Les paramètres de texture détaillés des échantillons sont résumés dans le tableau 2.
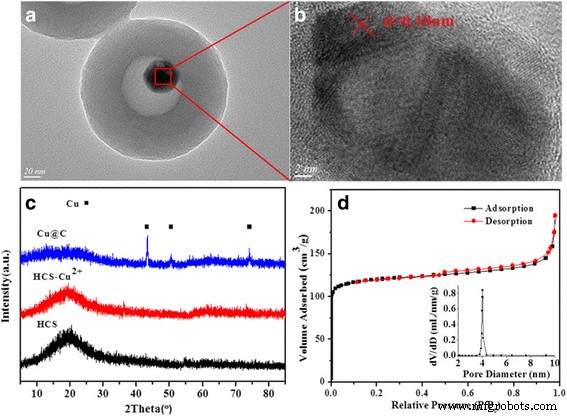
un , b Images MET d'un noyau de cuivre dans [email protected]. c Schémas XRD des produits obtenus après chaque étape :HCS, HCS-Cu 2+ , et [email protected]. d N2 isotherme d'adsorption-désorption et distribution de la taille des pores de [email protected]
La voie mécanistique pour la formation d'un seul Cu NPs dans la coquille de carbone peut être expliquée par le processus confiné de nucléation et de croissance. Au cours de la progression de la pyrolyse, de nombreux minuscules noyaux de CuO initiaux se sont formés et se sont complètement distribués dans la cavité creuse en raison de la décomposition du Cu(NO3 incorporé )2 molécules. Lorsque l'agent réducteur H2 diffuse dans la cavité, les noyaux CuO formés sont encore réduits en noyaux Cu métalliques, qui ont tendance à migrer et à s'agréger pour former des particules plus grosses. Une fois les plus grosses formées, les noyaux de Cu restants dans la cavité seront successivement absorbés à la surface des particules préformées, ce qui entraînera la croissance du nanocristal de Cu. Un mécanisme similaire a également été proposé ailleurs [23]. Sur la base du processus de nucléation et de croissance, on pourrait déduire que la taille du noyau de Cu résultant peut être contrôlée en ajustant la quantité de précurseur de sel de cuivre logé dans la cavité confinée.
Contrôle de la taille du noyau Cu
En faisant varier Cu(NO3 )2 des concentrations de 0,03 à 0,24 M, une série de nanocomposites vitellines, désignées par Cu@C-X (X = 0,03, 0,06, 0,12, 0,24), ont été obtenues. La morphologie et la taille des produits ont été examinées par MET. Comme le montre la figure 4a–d, presque toutes les nanosphères creuses sont constituées d'une seule particule à l'intérieur. Cependant, la taille du noyau de Cu des nanosphères résultantes augmente de 30 ± 1,3 à 55 ± 2,5 nm (Fig. 4e–h) avec une augmentation de Cu(NO3 )2 concentrations, déterminées à partir d'images MET en prenant en compte au moins 150 particules. Notamment, une fraction des sphères creuses de carbone (HCS) coexistent avec les YSN pour les faibles Cu(NO3 )2 concentration (Fig. 4a). En outre, quelques petites NP de Cu décorées sur la surface externe de la coque de carbone (Fig. 4d), qui pourraient être causées par la décomposition et l'agrégation du Cu(NO3 résiduel )2 à l'extérieur de la coquille.
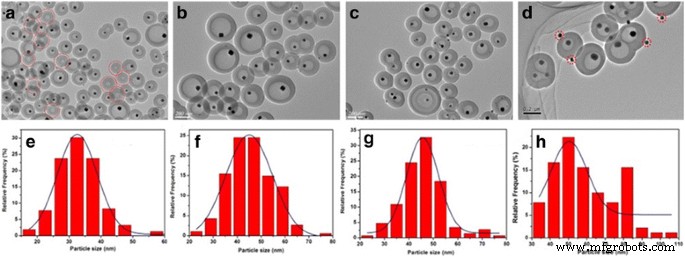
Images MET et histogrammes de distribution de taille correspondants des NP de Cu dans les échantillons :a , e [email protected], b , f [email protected], c , g [email protected], et d , h [email protected]
La figure 5a montre les modèles XRD de Cu@C-X tel que préparé (X = 0,03, 0,06, 0,12, 0,24). Tous les échantillons présentent trois pics de réflexion typiques indexés sur des cristaux de Cu (JCPDS Card No. 04-0836). À mesure que la concentration en sel de cuivre augmente, les pics de diffraction sont beaucoup plus forts et plus nets, tandis que la taille de Cu NP augmente de 26,6 à 52,2 nm en utilisant l'équation de Scherrer basée sur le pic le plus fort des motifs, ce qui est en bon accord avec les résultats MET . En outre, une analyse TG a été menée pour déterminer la teneur en Cu des nanosphères de la figure 5b. En supposant que les résidus sont entièrement constitués de CuO, les quantités de charge de Cu de Cu@CX (X = 0,03, 0,06, 0,12, 0,24) sont calculées à environ 5,9, 7,5, 8,0 et 9,9 % en poids, respectivement, ce qui est identique à les valeurs déterminées à partir de l'analyse AAS.
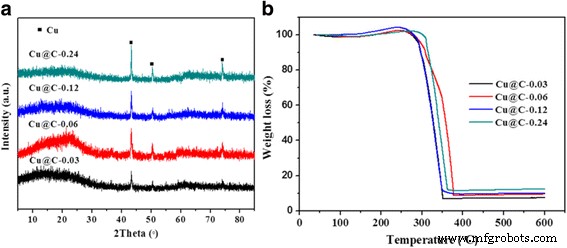
un Modèles XRD et b Courbes TG des échantillons :[email protected], [email protected], [email protected], [email protected]
Performances catalytiques de Cu@C-X (X = 0,03, 0,06, 0,12, 0,24)
Le catalyseur Cu@C tel que préparé a été testé pour la carbonylation oxydante en phase liquide du méthanol en DMC (tableau 2). De manière inattendue, bien qu'étant meilleur que les autres, le catalyseur Cu@C-0,12 n'a donné qu'une conversion de méthanol extrêmement inefficace de 0,82 %. La faible activité catalytique pourrait être associée au manque de porosité suffisante et au grand volume de pores dans la coque. A notre connaissance, les pores situés sur la coque agissent comme des canaux reliant le vide des sphères avec l'environnement extérieur [24]. Bien que l'épaisseur de la coque de Cu@C-0,12 soit d'environ 15 nm, le manque de porosité suffisante (le volume des pores structurels est de 0,23 cm 3 /g avec une faible surface spécifique de 365 m 2 /g) contraint la quantité de molécules réactives à diffuser dans les cavités et à entrer en contact avec le composant actif enterré des noyaux de Cu. Ainsi, il est essentiel de créer plus de porosité dans les coques pour faciliter le transport de masse. Comme on le sait, l'activation de KOH est une méthode bien établie pour ajuster la porosité des matériaux carbonés [25,26,27]. Avec cette méthode, des micropores et des mésopores peuvent être introduits dans le carbone, avec une augmentation significative de la surface spécifique et du volume des pores [28]. Au cours de la procédure d'activation, la quantité de KOH est généralement considérée comme un facteur critique pour influencer la structure poreuse ; ainsi, différents rapports massiques de KOH/HCS ont été réalisés pour optimiser le [email protected] activé.
Propriétés physicochimiques du Cu@A-HCS
L'image MET (Fig. 6a) montre que l'échantillon Cu@A-HCS activé maintient la morphologie sphérique au rapport de masse inférieur de KOH/HCS (1/4), mais partiellement ou gravement gravé avec un rapport de masse KOH/HCS supérieur à 1 /2 (Voir les informations complémentaires Fig. 2a, b). Ce résultat est en bon accord avec les rapports précédents selon lesquels une quantité excessive de KOH entraînera une combustion plus importante du carbone et détruira la morphologie [29]. Fait intéressant pour les nanocomposites Cu@A-HCS, après activation, des particules de cuivre hautement dispersées sont majoritairement incrustées dans l'enveloppe des sphères creuses, qui coexistent avec plusieurs encapsulées dans les cavités. Par rapport à [email protected], les NP de Cu insèrent la coquille affichent la taille de particule relativement plus petite centrée à 18 ± 2 nm (Fig. 6b) car la matrice de la coquille empêche les petits amas de Cu de grossir. L'existence de points blancs dans la coquille suggère l'existence de microspores désordonnées. La figure 6c montre le N2 -les isothermes d'adsorption-désorption du Cu@C-HCS, qui présentent des courbes représentatives de type IV associées à la fonction mésoporeuse, révélant que les échantillons activés possèdent des structures hiérarchiquement micro−/mésoporeuses. En outre, on peut constater qu'après activation de KOH à 700 °C pendant 2 h, la surface spécifique de l'A-HCS est passée de 471 à 989 m 2 /g, encore plus gros que le charbon actif (812 m 2 /g), et le volume microporeux (Vmic ), le volume des mésopores (Vmes ), et le volume total (VT ) a également augmenté, mais le rapport de Vmic à VT tend à diminuer. Ce résultat indique que plus de mésopores sont créés après l'activation de KOH, ce qui est peut-être lié à l'élargissement des micropores ou à la création de mésopores par la présence de KOH [30]. La grande surface typique et la porosité développée des catalyseurs Cu@A-HCS favorisent la dispersion de la phase active sur le support, garantissent le transfert rapide de matière entre le catalyseur confiné et l'environnement extérieur (réactifs), et augmentent sa résistance au frittage à forte charge métallique [31]. Comme le confirme le modèle XRD sur la figure 6d de Cu@A-HCS, tous les pics peuvent être indexés sans conteste sur le Cu cubique (JCPDS 04-0836) ; quant à lui, l'élargissement des pics caractéristiques implique la formation des Cu NPs de petite taille. En fait, la taille moyenne des Cu NPs dans Cu@A-HCS est estimée à 15 nm selon l'équation de Scherrer, ce qui est en accord avec le résultat obtenu par MET. Comme prévu, les catalyseurs Cu@A-HCS avec 11 % en poids de Cu déterminés par AAS ont été obtenus en utilisant la même méthode, supérieur à Cu@C-0,12. Plus important encore, au cours du processus d'activation, des groupes fonctionnels contenant de l'oxygène pouvant provenir de l'activation de KOH sont inévitablement introduits dans les HCS [27]. Dans l'ensemble, la génération de groupes de surface, l'augmentation de la surface et du volume des pores, entraînent de manière synergique la forte dispersion des Cu NPs, ce qui est bénéfique pour la promotion de l'activité catalytique [32,33,34]. Les propriétés texturales détaillées sont résumées dans le tableau 3.
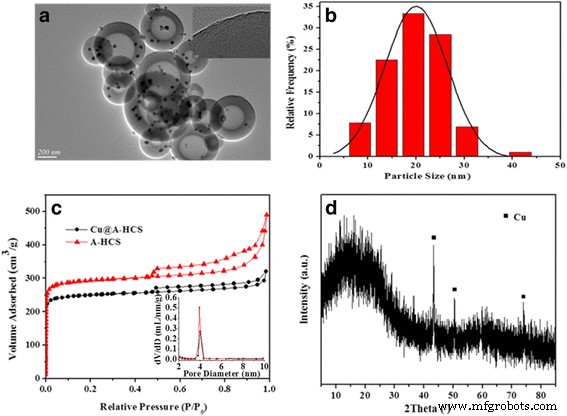
un Image MET de Cu@A-HCS et b sa taille de particule de Cu correspondante. c N2 isothermes d'adsorption-désorption et distributions de la taille des pores de A-HCS et Cu@A-HCS. d Schémas XRD du catalyseur Cu@A-HCS
Performances catalytiques de Cu@A-HCS
Les performances catalytiques de l'A-HCS et du Cu@A-HCS sont résumées dans le tableau 4. Comme le montre le tableau 4, il est clair que le support A-HCS n'a présenté aucune activité catalytique lors de la synthèse de DMC. Comme prévu, les propriétés catalytiques de l'échantillon activé se sont considérablement améliorées par rapport à celles non activées. Il est à noter que par rapport à 2,04 h −1 et 4,38 % pour Cu@C-0,12, l'activité naissante de Cu@A-HCS présente une multiplication par quatre du TOF de 8,6 h −1 accompagnée d'une augmentation correspondante de CMeOH de 17,1 %, respectivement dans les mêmes conditions. Ces résultats remarquables sont raisonnables si l'on considère l'augmentation de la surface et les volumes de pores des enveloppes de carbone peuvent adsorber positivement plus de molécules réactives de la solution en vrac, faciliter les vitesses de diffusion à travers les canaux de manière significative et les enrichir dans l'espace vide de la catalyseurs, résultant en une concentration de réactif plus élevée pour une catalyse confinée accessible. Un catalyseur avec une durée de vie raisonnablement longue est essentiel à son application dans l'industrie. Le catalyseur choisi est un échantillon de Cu@A-HCS activé avec une activité prometteuse pour tester la durabilité dans un système discontinu décrit ci-dessus. Les catalyseurs hétérogènes souffrent souvent d'une diminution de l'activité sous forme d'une lixiviation extensive d'espèces métalliques actives au cours des réactions [35]. Et tout aussi importante est la stabilité contre la coalescence pour le catalyseur à base de nanocristaux [36]. Dans notre cas, comme résumé dans le tableau 3, le catalyseur Cu@A-HCS récupéré (séparé par filtration) maintient une activité catalytique beaucoup plus élevée que CuCl même après sept essais (entrées 2-8) et la lixiviation moyenne de Cu, qui est le constituant actif du catalyseur, est d'environ 0,004%, restant presque le même que le frais. Pendant ce temps, la structure cristalline et la morphologie des catalyseurs n'ont pratiquement pas changé après des cycles successifs (Fichier supplémentaire 1 :Figure S2). Apparemment, la présence de l'enveloppe de carbone poreuse est suffisante pour stabiliser les espèces métalliques actives en empêchant leur agrégation et leur lixiviation; en même temps, les coques sont suffisamment perméables pour que les surfaces catalytiques restent accessibles et avantageuses pour les réactifs et les produits [12]. Par conséquent, les catalyseurs YSN sont des systèmes catalytiques efficaces et non corrosifs, où les NP de Cu en tant que matériaux de noyau encapsulés dans la cavité des HCS fournissent des centres réactifs, et la coque de carbone poreuse empêche le noyau de s'agréger et de se lessiver dans des conditions de réaction.
Conclusions
En résumé, nous avons présenté une stratégie de navire-dans-une-bouteille facile pour la fabrication de nanostructures de coquille jaune-carbone composées de Cu NPs avec une taille adaptée dans des distributions étroites en ajustant la concentration de sels de cuivre. Comme démontré, les propriétés catalytiques de ce système de type hochet dans la carbonylation oxydative du méthanol en DMC dépendent fortement de la porosité. L'échantillon activé avec une surface spécifique extrêmement élevée permet la création de nanoréacteurs confinés très efficaces pour des réactions catalytiques avec une conversion considérablement plus élevée (17,1 %) et un TOF (8,6 h −1 ), une longue durée de vie et une lixiviation négligeable à chaque cycle, qui satisfont incontestablement la production propre de DMC chimique vert. De plus, la voie de synthèse décrite dans cet article peut ouvrir de nouvelles opportunités pour la préparation de nanostructures jaune-coquille avec diverses compositions confinées dans la coquille de carbone.
Nanomatériaux
- Les nanocups peuvent courber la lumière
- Synthèse facile de WS2/Bi2MoO6 hétérostructurés en tant que photocatalyseurs hautes performances basés sur la lumière visible
- Nouveaux nanocomposites de polystyrène avec polyaniline dopé à l'acide lauryl sulfurique
- Fabrication à haut débit de nanofibres de qualité à l'aide d'un électrofilage à surface libre modifiée
- Performances photocatalytiques induites par la lumière visible des nanocomposites ZnO/g-C3N4 dopés N
- Fabrication et caractérisation d'un nouveau support de catalyseur anodique en nanofibre de carbone composite Tio2 pour pile à combustible au méthanol direct via la méthode d'électrofilage
- Nanocomposites de poly(N-isopropylacrylamide) magnétique :effet de la méthode de préparation sur les propriétés antibactériennes
- Fabrication, caractérisation et cytotoxicité de nanoparticules de carbonate de calcium dérivées de coquilles d'or conjuguées de forme sphérique pour des applications biomédicales
- La fabrication et les performances d'absorption des ondes électromagnétiques à haute efficacité des nanocomposites structurés CoFe/C Core-Shell