Dépannage pour la maintenance :plus qu'un simple essai et erreur
Un guide complet de dépannage pour la maintenance et des conseils pour améliorer vos compétences de dépannage afin d'améliorer l'ensemble de vos opérations.
Table des matières
- Qu'est-ce que le dépannage ?
- Conseils de dépannage pour la maintenance
- Utiliser un logiciel de maintenance pour le dépannage
- Le résultat final
Le dépannage pour la maintenance peut être à la fois un art et une science. Le problème est que si l'art peut être beau, il n'est pas connu pour son efficacité. Lorsqu'il passe au niveau supérieur, le dépannage peut abandonner le surnom d'essais et d'erreurs et devenir une entreprise purement scientifique. Cela aide les techniciens à trouver plus rapidement les bons problèmes et les bonnes solutions. Lorsque le dépannage est effectué correctement, l'ensemble de votre opération de maintenance peut surmonter les problèmes de retard, de perte de production et de conformité beaucoup plus efficacement.
Voyons ce qu'est réellement le dépannage, pourquoi il est important pour les professionnels de la maintenance et comment votre équipe peut affiner son approche.
Qu'est-ce que le dépannage ?
Les systèmes tombent en panne, c'est juste une réalité de la vie. Qu'il s'agisse d'un tapis roulant ou d'une perceuse industrielle, nous avons tous rencontré un équipement qui ne répond pas, est défectueux ou agit de manière anormale sans aucune raison apparente. Cela peut être carrément frustrant.
Le dépannage est le processus d'identification de ce qui ne va pas avec ces systèmes défectueux lorsque le problème n'est pas immédiatement évident. Le dépannage suit généralement une approche systématique en quatre étapes; identifier le problème, planifier une réponse, tester la solution et résoudre le problème. Les étapes un à trois sont souvent répétées plusieurs fois avant qu'une résolution ne soit atteinte.
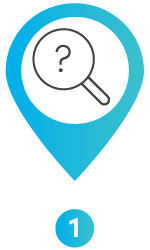
Identifier le problème
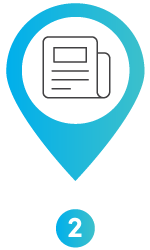
Planifier une réponse

Testez la solution
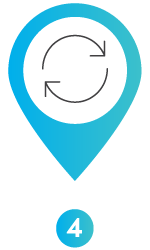
Répétez jusqu'à ce que le problème soit résolu
Pensez-y de cette façon :lorsqu'un tapis roulant tombe en panne, vous pouvez essayer différentes méthodes pour le réparer. Tout d'abord, vous identifiez quelle partie de la bande transporteuse ne fonctionne pas. Une fois que vous avez identifié la zone à problème, vous planifiez une réponse et la testez, comme le réalignement ou la lubrification d'une pièce. Si cela ne résout pas le problème, vous pouvez remplacer la pièce, ce qui permet à la bande transporteuse de fonctionner à nouveau. C'est un dépannage.
Comment le dépannage est-il généralement effectué en maintenance ?
Arrêtez-nous si vous avez déjà entendu cette histoire. Un actif tombe en panne et personne ne sait pourquoi. Vous parlez à l'opérateur, lisez certains manuels et vérifiez vos notes sur l'actif. Vous essayez plusieurs choses pour remettre la machine en marche sans succès. Avant de pouvoir essayer une troisième ou une quatrième solution possible, vous êtes appelé pour une autre urgence, l'actif étant toujours hors service.
C'est souvent ainsi que se déroule le processus lors du dépannage pour la maintenance, en particulier lorsqu'une installation s'appuie sur des enregistrements papier ou des feuilles de calcul Excel. Le processus est basé sur la collecte d'un maximum d'informations auprès d'autant de sources que possible afin d'identifier la cause la plus probable de la panne. Vous ne pouvez jamais vous tromper lorsque vous collectez des informations, mais c'est la façon dont les informations sont collectées qui peut transformer le dépannage d'une nécessité en un cauchemar.
Pourquoi le dépannage est-il important dans la maintenance ?
Une panne d'équipement inattendue est la seule raison pour laquelle le dépannage existe. Si les actifs ne tombaient jamais en panne sans aucun signe clair de défaillance imminente, il ne serait pas nécessaire de résoudre le problème. Mais nous savons que ce n'est tout simplement pas le cas.
La défaillance des actifs ne suit pas toujours un modèle prévisible. Oui, les équipes de maintenance peuvent utiliser la maintenance préventive et la maintenance conditionnelle pour réduire la probabilité de temps d'arrêt imprévus. Cependant, vous ne pouvez jamais l'éliminer complètement. Ce que vous pouvez faire, c'est mettre en place des processus pour réduire autant que possible les défaillances et les corriger dès que possible lorsqu'elles se produisent. C'est là que de solides techniques de dépannage s'avèrent utiles.
Étant donné que le dépannage fera toujours partie de l'équation de maintenance, les humains auront également toujours un rôle à jouer. La technologie de maintenance n'efface pas le besoin d'une touche humaine dans le dépannage ; cela rend simplement le processus beaucoup plus efficace. Lorsque le dépannage n'est pas affiné, cela peut entraîner une perte de temps à rechercher des informations, une perte de production substantielle, un environnement de travail dangereux et des pannes plus fréquentes. En bref, connaître certaines bonnes pratiques de dépannage pourrait faire la différence entre un arriéré écrasant et un programme de maintenance stable.
Conseils de dépannage pour la maintenance
Voici quelques façons dont votre exploitation peut améliorer ses capacités de dépannage pour vaincre le chaos et prendre le contrôle de sa maintenance.
Quantifier les performances des actifs et comprendre comment utiliser les résultats
Cela va probablement de soi, mais plus vous connaissez un atout en profondeur, mieux vous serez équipé pour diagnostiquer un problème. Des années de travail avec un certain actif peuvent vous aider à reconnaître quand cela ne fonctionne pas tout à fait correctement. Mais un dépannage exceptionnel ne consiste pas seulement à connaître les sons, les vitesses ou les odeurs normaux d'une machine particulière. Au lieu de cela, il s'agit de savoir comment analyser les performances des actifs à un niveau plus profond, c'est là que les rapports avancés entrent en ligne de compte.
Obtenir les meilleures pratiques pour le suivi et l'utilisation des données d'actifs
Lire la suite
Lorsque les opérateurs et les techniciens se fient uniquement à leur propre expérience passée avec un équipement, cela leur laisse d'énormes lacunes dans les connaissances qui nuisent au processus de dépannage. Par exemple, cela laisse trop de place au biais de récence pour affecter la prise de décision, ce qui signifie que les techniciens sont plus susceptibles d'essayer la dernière chose qui a résolu un problème particulier sans envisager d'autres options ou approfondir la cause première. De plus, si le dépannage repose sur les connaissances exclusives de quelques techniciens, cela signifie que les réparations devront attendre que ce personnel particulier soit disponible.
Le personnel de maintenance doit avoir le savoir-faire pour effectuer une analyse approfondie des performances d'un actif. Par exemple, les techniciens doivent savoir comment exécuter des rapports et comprendre les KPI pour les équipements critiques, tels que le temps moyen entre la panne et l'efficacité globale de l'équipement. Si vous utilisez la maintenance conditionnelle, l'équipe de maintenance doit également connaître la courbe P-F pour chaque actif et la signification des différentes lectures des capteurs. Lorsque les techniciens sont dotés d'une compréhension plus approfondie d'un actif, il leur sera plus facile de déterminer où un problème s'est produit et comment le résoudre, à court et à long terme.
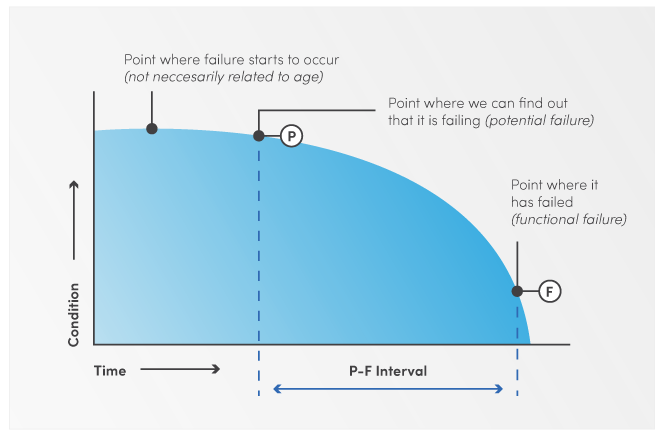
Créer des historiques d'actifs détaillés
L'information est le carburant qui alimente un dépannage exceptionnel pour la maintenance. Savoir comment un actif particulier a fonctionné et a échoué pour des centaines d'autres est un bon endroit pour commencer une réparation. C'est pourquoi les manuels sont un outil utile lors du dépannage. Cependant, chaque actif, installation et opération est différent, ce qui signifie que la défaillance d'un actif ne suit pas toujours le script. Des notes détaillées sur l'historique d'un actif peuvent ouvrir une impasse et vous conduire à une solution beaucoup plus rapidement.
Un historique détaillé des actifs peut vous donner un avantage dans le dépannage de diverses manières. Il offre une méthode simple pour croiser les symptômes du problème actuel avec des éléments de problèmes passés. Par exemple, un technicien peut voir si un certain type de matériau était manipulé par une machine ou s'il y avait des signes avant-coureurs identifiés pour une défaillance précédente. Plus une situation actuelle s'aligne sur un scénario passé, plus il est probable qu'elle ait besoin de la même solution. Les solutions peuvent être hiérarchisées de cette façon, ce qui entraîne moins d'incidents, moins de temps d'arrêt, moins de pièces de rechange inutiles utilisées, et plus encore.
Lorsque le dépannage est effectué correctement, l'ensemble de votre opération de maintenance peut surmonter les problèmes de retard, de perte de production et de conformité beaucoup plus efficacement.
Lors de la création d'historiques détaillés des actifs pour faciliter le dépannage (ainsi que la maintenance préventive), il est important d'inclure autant d'informations que possible. Assurez-vous d'enregistrer l'heure et les dates de toute action notable prise sur un actif ou une pièce d'équipement. Cela peut inclure des pannes, des MP, des inspections, des remplacements de pièces, des calendriers de production et des comportements anormaux, tels que de la fumée ou des sons inhabituels. Ensuite, documentez les mesures prises pendant la maintenance, y compris les MP ou les réparations. Enfin, mettez en évidence la solution réussie et ce qui était nécessaire pour l'accomplir, comme les pièces nécessaires, la main-d'œuvre et l'équipement de sécurité. Assurez-vous également d'ajouter toutes les métriques et rapports pertinents à l'historique des actifs.
Une façon de capturer toutes ces informations en un seul endroit consiste à créer un journal de maintenance de l'équipement bien construit, comme celui-ci :
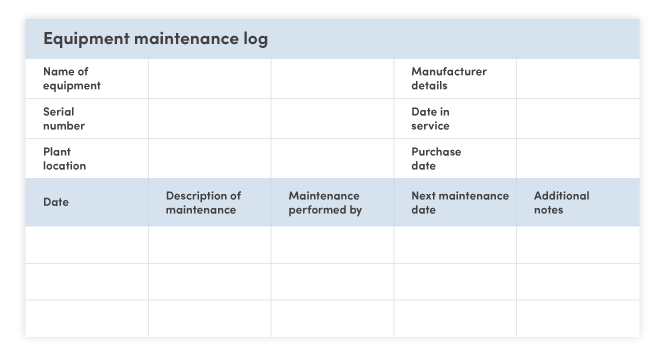
Téléchargez votre propre modèle de journal de maintenance de l'équipement ici
Utilisez l'analyse des causes profondes et les codes d'échec
Un dépannage efficace pour la maintenance commence par l'élimination des ambiguïtés et des solutions à court terme. Trouver rapidement la racine d'un problème, le résoudre efficacement et s'assurer qu'il reste résolu est une formule gagnante. L'analyse des causes profondes et les codes de défaillance sont quelques outils qui vous aideront à atteindre cet objectif.
L'analyse des causes profondes est une technique qui vous permet d'identifier la raison d'un échec. La méthode consiste à demander « pourquoi » jusqu'à ce que vous arriviez au cœur du problème. Par exemple :
- Pourquoi l'équipement est-il tombé en panne ? :parce qu'un roulement s'est usé
- Pourquoi le roulement s'est-il usé ? :parce qu'un accouplement était mal aligné
- Pourquoi l'accouplement n'était-il pas aligné ? :parce qu'il n'a pas été entretenu récemment.
- Pourquoi l'accouplement n'a-t-il pas été entretenu ? : car l'entretien n'a pas été planifié.
- Pourquoi la maintenance n'a-t-elle pas été planifiée ? :parce que nous ne savions pas à quelle fréquence elle devait être planifiée.
Réalisez votre prochaine analyse des causes profondes avec ce modèle RCA
Ce processus présente deux avantages lors du dépannage pour la maintenance. Tout d'abord, il vous permet d'identifier la cause immédiate de la panne et de la réparer rapidement. Deuxièmement, cela vous amène au cœur du problème et à une solution à long terme. Dans l'exemple ci-dessus, il est clair qu'un meilleur programme de maintenance préventive est nécessaire pour améliorer la gestion des actifs et réduire les temps d'arrêt imprévus.
Les codes d'échec fournissent une méthode cohérente pour décrire pourquoi un actif a échoué. Les codes de défaillance sont construits sur trois actions : Répertorier tous les problèmes possibles, toutes les causes possibles et toutes les solutions possibles. Ce processus enregistre les aspects clés d'une défaillance selon des catégories prédéfinies, comme le désalignement ou la corrosion.
Les codes de panne sont utiles lors du dépannage pour la maintenance, car les techniciens peuvent immédiatement voir les codes de panne courants, déterminer la meilleure solution et la mettre en œuvre rapidement. Les codes de défaillance peuvent également être utilisés pour découvrir un problème commun parmi un groupe d'actifs et déterminer une solution à long terme.
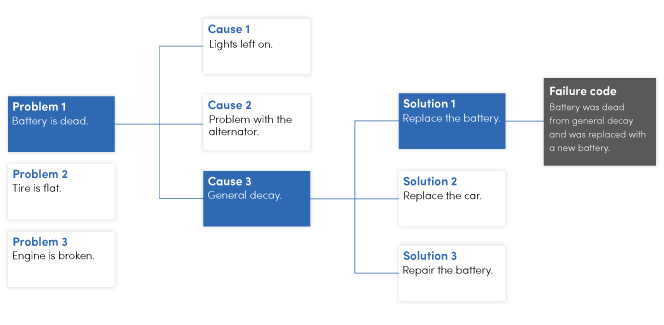
Créez des codes d'échec impressionnants avec ce modèle FMEA gratuit
Créer des listes de tâches détaillées
Un dépannage exceptionnel nécessite une planification et une prévoyance solides. Des processus clairs fournissent un modèle aux techniciens afin qu'ils puissent rapidement identifier les problèmes et mettre en œuvre des solutions plus efficaces. La création de listes de tâches détaillées est un moyen de renforcer votre planification et d'éviter les maux de tête en cours de route.
Une liste de tâches décrit une série de tâches qui doivent être accomplies pour terminer un travail plus important. Ils garantissent que des étapes cruciales ne sont pas manquées lors de la réalisation d'inspections, d'audits ou de MP. Par exemple, la tâche la plus importante peut consister à effectuer une inspection de routine des défibrillateurs de votre établissement. Ce travail est divisé en une liste de tâches plus petites, telles que « Vérifier l'installation de la batterie » et « Inspecter les composants extérieurs à la recherche de fissures ».
La technologie de maintenance n'efface pas le besoin d'une touche humaine dans le dépannage ; cela rend simplement le processus beaucoup plus efficace.
Les listes de tâches détaillées sont extrêmement importantes lors du dépannage pour la maintenance. Ils servent de guide lors du test des solutions possibles afin que les techniciens puissent soit résoudre le problème, soit disqualifier un diagnostic le plus rapidement possible. Plus la liste des tâches est explicite, plus le travail est approfondi et moins un technicien risque de se tromper. Des listes de tâches complètes peuvent également offrir des données précieuses en cas d'échec. Ils donnent un aperçu du type de travail récemment effectué sur un actif afin que vous puissiez déterminer si des actions ont été manquées et si cela était la source du problème.
Il existe quelques bonnes pratiques pour créer des listes de tâches détaillées. Tout d'abord, incluez toutes les actions individuelles qui composent une tâche. Par exemple, au lieu de demander à quelqu'un « Inspecter le ventilateur de refroidissement », incluez les étapes qui composent cette inspection, telles que « Vérifier toute fissure visible » et « Inspecter les pièces desserrées ». Organisez toutes les étapes dans l'ordre où elles doivent être effectuées. Enfin, incluez toute information supplémentaire qui peut être utile pour effectuer les tâches, y compris les fournitures nécessaires, les ressources (c'est-à-dire les manuels) et les EPI.
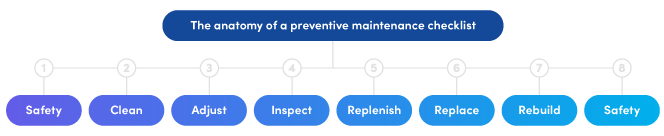
Créez des listes de contrôle PM de classe mondiale avec ce modèle gratuit
Rendre les informations supplémentaires accessibles
Nous l'avons déjà dit et nous le répéterons; un excellent dépannage est souvent le résultat d'une excellente information. Cependant, si ces informations sont difficiles d'accès, vous perdrez tout avantage qu'elles offrent. C'est pourquoi il est crucial pour votre exploitation non seulement de créer un grand centre de ressources, mais aussi de le rendre très accessible. Cela augmentera vos capacités de dépannage et remettra vos actifs en ligne plus rapidement en cas d'indisponibilité imprévue.
Commençons par les éléments d'un grand centre d'information. Nous avons parlé de l'importance des rapports, des historiques d'actifs, des codes de panne et des listes de tâches lors du dépannage pour la maintenance. Certaines autres ressources clés incluent des diagrammes, des procédures opérationnelles standard (SOP), des vidéos de formation et des manuels. Ceux-ci devraient tous être inclus et organisés par actif. Si un technicien se trouve dans une impasse lors du dépannage d'un problème, ces outils peuvent offrir une solution qui a peut-être été manquée lors de l'analyse initiale.
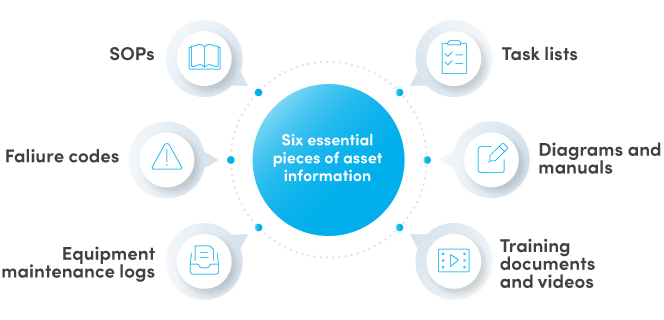
Maintenant que vous avez rassemblé tous vos documents, il est temps de les rendre facilement accessibles à toute l'équipe de maintenance. Si des ressources sont piégées dans un classeur, sur une feuille de calcul ou dans l'esprit d'une seule personne, elles ne font pas grand-chose pour le technicien. Ils peuvent être perdus, égarés et difficiles à trouver, sans parler de l'inefficacité liée au fait de devoir marcher d'un actif au bureau juste pour récupérer un manuel. Une façon de contourner cet obstacle est de créer un pôle de connaissances numériques avec un logiciel de maintenance. En mettant toutes vos ressources à disposition via un appareil mobile, les techniciens peuvent accéder à tous les outils dont ils ont besoin pour résoudre un problème. Au lieu de passer au crible des fichiers papier pour trouver un historique ou un diagramme des actifs, ils peuvent accéder aux mêmes informations n'importe où, n'importe quand.
Tout ce que vous devez savoir sur les métriques de maintenance
Lire la suite
Utilisation d'un logiciel de maintenance pour le dépannage
Si cela semble beaucoup de travail pour rassembler, organiser, analyser et diffuser toutes les informations nécessaires pour réussir le dépannage, vous n'avez pas tort. Sans les outils appropriés, ce processus peut être un fardeau pour les équipes de maintenance débordées. Le logiciel de maintenance est un outil qui peut aider à alléger la charge à chaque étape du processus. Une plate-forme numérique, telle qu'une GMAO, s'occupe de calculer les chiffres, d'organiser les données et de les rendre disponibles n'importe où et n'importe quand, afin que vous puissiez vous concentrer sur l'utilisation de ces informations pour prendre de bonnes décisions et résoudre les problèmes plus efficacement.
Par exemple, lors de la création d'un historique détaillé des actifs, il est important de documenter chaque rencontre avec un équipement. C'est beaucoup de travail pour un technicien qui se précipite d'un travail à un autre et difficile à suivre après coup. Un investissement dans un logiciel de maintenance vous aidera à surmonter ces obstacles. Pour ce faire, les techniciens peuvent utiliser un ensemble de questions prédéterminé pour prendre et récupérer des notes en temps réel en quelques clics.
Il en va de même pour les codes de panne. La clé pour les utiliser efficacement est une organisation et une accessibilité appropriées. Sans ces deux ingrédients clés, les codes d'échec deviennent plus un obstacle qu'une aide. Une façon d'y parvenir est d'utiliser un logiciel de maintenance. Une plate-forme numérique peut mieux organiser les codes de panne que n'importe quel classeur ou tableur Excel et permettre aux techniciens de les trier rapidement et d'identifier ceux qui sont pertinents à partir du site de la panne.
Le résultat final
Le dépannage existera toujours en maintenance. Vous ne serez jamais sûr à 100 % 100 % du temps lors du diagnostic de la cause de l'échec. Ce que vous pouvez faire, c'est prendre des mesures vers un processus de dépannage plus efficace pour vous assurer que l'équipement est réparé rapidement et efficacement. En combinant une bonne compréhension des métriques de maintenance avec des historiques d'actifs détaillés, des codes de panne, des listes de tâches et d'autres ressources d'actifs, et en rendant toutes ces informations accessibles, vous pouvez déplacer votre dépannage au-delà des essais et des erreurs vers une approche plus scientifique.
Entretien et réparation d'équipement
- Maintenance mobile :Plus qu'une simple tendance du secteur (PODCAST)
- Une leçon de conduite pour les opérations et la maintenance
- Un nouveau livre aide à transformer la fabrication et la maintenance
- Stratégie et solutions de l'armée pour la maintenance conditionnelle
- L'effort multi-compétences pour la maintenance
- 5 règles d'exploitation et de maintenance en partenariat
- L'amélioration de la disponibilité va bien au-delà de la maintenance
- Plages de contrôle pour les planificateurs de maintenance et autres
- Stratégies pour des composants de transmission d'énergie plus fiables