Comment créer un programme de maintenance électrique
Les systèmes de contrôle et de distribution électriques sont généralement des actifs complexes et coûteux qui doivent être entretenus efficacement afin qu'ils fonctionnent à des performances optimales tout au long de leur durée de vie. Il est courant de constater que des efforts importants ont été déployés pour gérer les actifs mécaniques, avec moins d'accent sur les équipements électriques.
Il existe de nombreuses raisons pour lesquelles c'est le cas, mais la réalité est que la façon dont les programmes de gestion des actifs sont développés doit être appliquée de manière égale aux composants électriques et mécaniques de l'actif.
Combien d'entre vous peuvent associer aux éléments suivants situations ?
-
Les jours d'arrêt et les arrêts ne sont pas inclus dans le calendrier de production.
-
Il y a peu de tâches électriques documentées, et souvent celles qui le sont étaient souvent une réaction « coup de poing » à un événement ponctuel.
-
Les pièces de rechange d'entretien électrique ne sont pas conservées dans le magasin. Souvent, ils sont enfermés dans des armoires et des tirages d'individus.
-
Il existe de nombreux planificateurs de maintenance mécanique et peu ou pas de planificateurs électriques.
-
Il n'y avait aucune norme suivie pour les dessins électriques et, par conséquent, la plupart des modifications se sont produites au mieux avec des croquis dessinés à la main.
-
Les informations techniques importantes ne sont pas centralisées ni gérées.
-
Il existe peu ou pas de nomenclatures pour les équipements électriques.
-
La panne était la principale stratégie pour tous les équipements électriques.
-
Il n'y avait pas de plan prévisionnel lié à la sécurité opérationnelle de l'équipement.
-
La GMAO n'est pas utilisée efficacement pour enregistrer l'historique des pannes.
-
De nombreux électriciens prennent du retard dans leur compréhension de la technologie.
Si vous êtes d'accord avec la plupart de ces commentaires, alors vous travaillez presque à 100 % de manière réactive et vous avez beaucoup de marge de progression.
Mais, par où commencer ? Vous pouvez développer votre propre plan, dire aux gens ce qu'ils vont faire maintenant et regarder tout cela se produire. Tort! Si vous ne gérez pas l'aspect humain de l'amélioration, il y a peu d'espoir d'amélioration durable.
Les problèmes de personnes
-
Reconnaître votre situation actuelle .
Vous devez croire qu'il existe une meilleure façon de faire les choses. Si plusieurs des points ci-dessus s'appliquent à vous, alors vous devez savoir que votre situation doit être améliorée. -
Développez une vision pour votre programme de maintenance électrique.
La vision est l'endroit où vous voulez être dans le futur. Un exemple d'une telle vision : -
Un planificateur électrique sera embauché dans les trois prochains mois.
-
Tous les équipements critiques auront des stratégies de maintenance développées dans les 12 mois.
-
Des stratégies pour les équipements moins critiques seront développées dans les 24 mois.
-
Un système de mise à niveau et de gestion des schémas électriques sera développé et mis en œuvre au cours des 12 prochains mois.
-
Toutes les stratégies maximiseront l'utilisation de la maintenance conditionnelle.
-
Les commerçants et autres personnels concernés seront formés afin qu'ils puissent appliquer efficacement les stratégies.
-
Mettre en place des jours d'arrêt pour les équipements électriques.
-
etc.
-
- Obtenez le soutien du groupe de travail électrique. Discutez de vos projets d'avenir avec votre groupe de travail. Après tout, ce sont eux qui connaissent le mieux la plante. Demandez-leur des idées à inclure dans la vision. C'est bien mieux pour le groupe de soutenir la vision et d'avoir un sentiment d'appartenance.
- Obtenez le soutien de votre direction. Si la direction n'est pas disposée à soutenir votre vision, alors il y a peu de chances de succès. Documentez votre vision, en mettant en avant les bénéfices et gains potentiels, et vos idées ! Soyez prêt à répondre à des questions difficiles et ayez confiance en votre jugement.
-
Les problèmes pratiques
-
Des ressources seront nécessaires pour mettre en œuvre efficacement les changements. Dans le cadre de votre vision présentée à la direction, il aurait dû être clair que des ressources sont nécessaires pour apporter des améliorations significatives à votre programme de maintenance électrique. Cela ne signifie pas nécessairement que vous avez besoin de plus de gens. Le redéploiement de la main-d'œuvre interne ou l'embauche d'entrepreneurs à temps partiel est généralement plus logique. Au fur et à mesure que votre programme commence à prendre effet, les gains d'efficacité compenseront la perte de main-d'œuvre sur le sol.
-
Comprendre la criticité de vos actifs électriques. Vous pouvez utiliser un outil de classement de criticité pour cela, mais si vos actifs existent depuis un certain temps, vos employés en auront généralement une compréhension assez claire. Les actifs les plus critiques seront votre point de départ.
-
Rassemblez l'historique des échecs. Dans les entreprises établies, il existe deux domaines pour rechercher ces données :auprès de la GMAO et auprès des opérateurs et artisans expérimentés. Ce que vous essayez de faire, c'est de comprendre quelles défaillances vous devez atténuer en appliquant une stratégie de maintenance.
-
Comprendre les autres causes potentielles d'échec. Pour les actifs nouveaux ou très critiques, il est souvent intéressant d'effectuer une analyse des modes de défaillance et de leurs effets ou un processus de maintenance centrée sur la fiabilité. Ces outils détermineront « ce qui pourrait échouer et quels en seraient les effets ». Cela permet de prendre des décisions judicieuses en fonction de la criticité de l'effet.
-
Développez des inspections de maintenance préventive et des listes de tâches qui minimisent les modes de défaillance connus et hypothétiques. Avant de générer de nouveaux MP, un examen des documents actuels doit être effectué. Vous constaterez que certains PM sont adéquats pour le résultat requis. Mais s'ils n'ont pas été révisés pendant un certain temps, ils auront des lacunes. L'exemple du tableau ci-dessous montre que pour les 10 actions requises, seules quatre ont été considérées comme ayant des MP qui traitent de manière adéquate les modes de défaillance identifiés. Trois étaient des travaux moyens et requis, tandis que les PM n'existaient pas pour trois actions critiques. Votre point de départ dans ce cas est de développer les nouveaux MP pour les trois qui manquent.
-
Les actions développées dans les nouvelles MP doivent être quantitatives si possible - par exemple, mesurer la longueur de la brosse et la remplacer si elle mesure moins de 40 millimètres de long. La thermographie (où elle peut être appliquée en toute sécurité) est toujours la meilleure option pour détecter les joints chauds dans les équipements de contrôle et de distribution.
Pour les composants électriques, rappelez-vous les bases de PROPRE, REFROIDIR et SEC .Les joints chauds sont la cause de temps d'arrêt importants.
- Assurez-vous que tous les documents de stratégie sont capturés dans la GMAO et programmés pendant les temps d'arrêt planifiés. L'élaboration de stratégies, y compris leur saisie dans une GMAO, est un processus très chronophage. Des ressources doivent être mises à disposition pour que cela soit fait en temps opportun. Ne pas mettre en œuvre les améliorations de la stratégie en temps opportun sera perçu comme négatif par votre client (production, gestion, etc.).
- Démarrez le processus de nomenclature. Pour que le travail planifié se déroule sans heurts, les matériaux doivent être répertoriés dans la hiérarchie des équipements afin qu'ils puissent être facilement identifiés et commandés. L'équipement critique peut devoir être conservé en stock en fonction du délai d'exécution et de la conséquence de ne pas avoir la pièce de rechange. Avec les équipements électriques, il y a toujours eu le dilemme de la suppression des équipements dans des délais très courts, et cela est souvent utilisé comme une raison pour ne pas démarrer. Le BOMing doit faire partie d'un processus global de révision de la stratégie. Si un nouvel équipement est en cours d'installation, demandez une liste de pièces à l'équipe d'ingénierie chargée de l'installation avant la fin du projet. Idéalement, le catalogage et la nomenclature des équipements devraient faire partie du projet global.
- Gérez vos schémas électriques et votre documentation. Combien de fois une machine n'a-t-elle pas été réparée dans un délai adéquat en raison des inexactitudes dans les schémas ? Avez-vous des schémas dessinés à la main comme celui ci-dessous?
Des schémas précis sont une partie essentielle de votre programme de maintenance électrique. Un examen schématique de la précision doit commencer sur la base de l'évaluation de la criticité de votre usine. (Les actifs les plus critiques en premier.) Le meilleur endroit pour commencer est de rassembler toutes les copies papier des schémas d'un seul équipement et de demander à votre personnel électrique le plus expérimenté de vérifier ce qui est correct. À partir de là, développez une copie annotée du schéma et stockez-la électroniquement sous forme de fichier CAO ou image (.jpg,. tif, .pgn, etc.). Vous avez maintenant un schéma mis à jour auquel vous pouvez accéder facilement. Pour la plupart des entreprises, ce sera un énorme travail au départ, mais le résultat en vaut la peine. Et une fois que votre système est en ordre, il est beaucoup plus facile à gérer. En fin de compte, le processus de modification des schémas doit être procédural et contrôlé.
- Formez votre personnel électrique. Développez une matrice de formation pour vos électriciens. La matrice doit inclure un aperçu des technologies et des compétences spécifiques et génériques requises de votre personnel. Un exemple d'une compétence spécifique serait :Accéder et surveiller les API Allen-Bradley. Une compétence générique serait :Entretien des moteurs à courant continu. Vous pouvez également inclure le besoin de comprendre les processus de production ou simplement de vous familiariser avec un domaine spécifique de l'usine.
- Assurez-vous d'avoir un processus documenté pour gérer efficacement la charge de travail. La plupart des services de maintenance électrique, qu'il s'agisse d'un seul homme ou de dizaines, doivent prioriser leur travail. La hiérarchisation ne doit pas être fondée sur « qui crie le plus fort » et doit être fondée sur l'importance et l'urgence. L'importance équivaut à la valeur pour l'entreprise, où l'urgence équivaut aux limitations de temps appliquées à une tâche. Ricky Smith, co-auteur de « Lean Maintenance » et « Rules of Thumb for Maintenance Practices » déclare : « Les meilleures entreprises ont développé un modèle de flux de travail proactif qui est compris et suivi par tous les niveaux de l'organisation. » Le modèle de « flux de travail » Ricky fait référence aux besoins d'inclure un processus de gestion des pannes, un processus de planification, un processus de planification des tâches planifiées, un processus de gestion du travail qui brisera un calendrier fixe et une méthode pour capturer les améliorations qui peuvent être introduit dans le système.
Le modèle Allied Reliability Workflow.
- Fermez la boucle d'amélioration. Il vaut la peine de lire sur le cycle Planifier, Faire, Vérifier, Agir. Il y a une infinité de références à cela sur Internet. Toutes les choses discutées jusqu'au point 13 étaient liées à la planification et à l'action. Lorsqu'un programme de maintenance préventive est développé, il est peu probable qu'il soit à 100 pour cent à l'avance. Viser 80 pour cent est un bon début. Le réglage fin se fera à partir des commentaires des gars sur le terrain. Assurez-vous que ces commentaires sont capturés et renvoyés dans votre système. Il n'y a rien de pire qu'une personne soulignant où les choses peuvent être améliorées, puis rien ne se passe à ce sujet et aucun retour n'est donné. N'oubliez pas que vous pouvez avoir d'excellents systèmes, mais si personne ne les suit, vous ne réussirez aucune initiative d'amélioration.
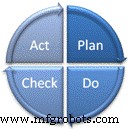
À propos de l'auteur :
Mark Brunner est titulaire d'une maîtrise en gestion de la maintenance et d'un certificat en génie électrique. Lui et Rod O'Connor ont développé la feuille de route de la fiabilité des actifs. L'objectif est de contribuer à simplifier le chemin vers l'excellence en gestion d'actifs. Pour plus d'informations, contactez Mark à [email protected].
Entretien et réparation d'équipement
- Comment un programme PM aide-t-il à éliminer les défaillances de composants ?
- Comment conserver la maintenance en mode proactif
- Mesure du succès du programme de maintenance prédictive
- Réponses aux questions de maintenance prédictive
- Comment démarrer un programme de fiabilité
- Comment les responsables de maintenance peuvent améliorer leur programme de santé et de sécurité
- Comment concevoir un programme de maintenance préventive pour votre équipement
- Comment construire un programme de maintenance électrique
- Qu'est-ce que l'arriéré de maintenance ? Comment le surmonter ?