Impression 3D FDM :où en sommes-nous aujourd'hui ?
Les progrès de l'impression 3D par extrusion modifient la trajectoire de la technologie de fabrication de filaments fondus (FFF).
FFF, ou FDM (Fused Deposition Modelling) comme on l'appelle plus communément, est l'une des technologies d'impression 3D les plus couramment utilisées. Avec une adoption croissante dans tous les segments industriels, FDM était la technologie d'impression 3D la plus génératrice de revenus en 2017 et aurait la plus grande base installée (SmarTech).
Alors, qu'est-ce qui a stimulé la croissance et la maturité de la technologie ? Et comment l'impression 3D polymère basée sur l'extrusion évoluera-t-elle à l'avenir ?
Pour répondre à ces questions, cet article se penchera sur certains des développements clés qui façonnent la FDM et sur les prochaines étapes de cette technologie passionnante.
Éléments clés du développement de FDM
- 1989 :Scott et Lisa Crump font breveter une nouvelle méthode de fabrication additive, déposent la marque Fused Deposition Modeling (FDM) et fondent la société de matériel informatique Stratasys.
- 1991 :Stratasys commercialise pour la première fois l'impression 3D FDM.
- 2005 :marque le début du projet RepRap, qui permet de réduire le coût de l'impression 3D FDM.
- 2008 :Stratasys annonce qu'elle proposera l'ULTEM 9085 hautes performances pour ses machines FDM 900mc et 400mc — un grand pas en avant pour les matériaux FDM.
- 2009 :Les premiers brevets FDM expirent, permettant aux passionnés de développer et commercialiser leurs propres imprimantes 3D FDM DIY. Des entreprises comme MakerBot et Lulzbot connaissent un énorme succès avec leurs kits d'imprimantes DIY.
- 2011 :Création d'Ultimaker, l'un des principaux fabricants d'imprimantes 3D FDM de bureau.
- 2013 :Stratasys acquiert MakerBot, un fabricant d'imprimantes 3D de bureau.
- 2013 :Création de Markforged, un fabricant de matériel proposant la technologie d'impression 3D composite FDM.
- 2014 :Le fabricant d'imprimantes 3D FDM à grande échelle, BigRep, est fondé.
- 2015 :Voodoo Manufacturing démarre son activité d'impression 3D, qui deviendra une usine numérique avec plus de 200 machines FDM d'ici 2019.
- 2017 :Stratasys présente son Continuous 3D Build Demonstrator, une unité d'impression 3D modulaire pour les opérations à haut débit.
- 2018 :Essentium commercialise sa plateforme d'extrusion à grande vitesse, dotée de sa technologie FlashFuse qui utilise le chauffage électrique pour imprimer des pièces en 3D.
Les origines du FDM
L'émergence de l'impression 3D par extrusion remonte à la fin des années 1980, lorsque l'ingénieur et inventeur Scott Crump a développé une nouvelle méthode de prototypage rapide.
En 1989, Crump a breveté la nouvelle technologie, la nommant Fused Modélisation des dépôts. La même année, Scott et Lisa Crump ont cofondé Stratasys et livré leur première machine FDM, le modeleur 3D, deux ans plus tard.
Depuis lors, la technologie FDM n'a cessé de gagner en popularité, combler le vide dans les solutions de prototypage rapide à moindre coût.
Aujourd'hui, Stratasys reste l'une des plus grandes entreprises de matériel informatique au sein de l'industrie de l'impression 3D, proposant 9 modèles de ses machines FDM et plusieurs imprimantes 3D Polyjet.
Les imprimantes 3D FDM actuelles impliquent le même processus de fusion et d'extrusion de matériaux thermoplastiques par couches, que la première machine FDM il y a trente ans.
Cela dit, il serait faux de supposer que la technologie n'a pas évolué. De nombreux développements ont façonné l'impression 3D FDM, l'aidant à devenir l'une des technologies additives les plus largement utilisées.
L'essor du projet RepRap et du FDM low-cost
Le succès de la technologie FDM s'explique en partie par la montée en puissance du projet RepRap et l'expiration de plusieurs brevets FDM à la fin des années 2000.
Le projet RepRap a promu le concept d'imprimantes 3D open source et auto-réplicables. Le concept a d'abord été adopté par la communauté des bricoleurs. Mais à la suite de l'expiration des principaux brevets FDM détenus par Stratasys à la fin des années 2000, de nombreuses entreprises ont vu le jour en cherchant à commercialiser des imprimantes 3D FDM basées sur RepRep.
Cela a donné naissance à une vague d'imprimantes 3D de bureau FDM à un coût nettement inférieur, faisant de cette technologie un excellent point d'entrée pour les entreprises qui découvrent la technologie.
Les années 2010 :une nouvelle génération de FDM
L'essor du mouvement RepRap et l'expiration des principaux brevets FDM ont considérablement accéléré le développement de la technologie au cours de la dernière décennie. Un certain nombre d'entreprises prometteuses ont émergé, cherchant à faire progresser l'impression 3D FDM.
Pionnier de l'impression 3D en fibre de carbone continue
En 2014, une petite startup, Markforged, a fait sensation avec sa technologie d'impression 3D Continuous Filament Fabrication (CFF). La société serait la première à permettre l'impression 3D à fibre continue, ouvrant de nouvelles opportunités industrielles pour la technologie FDM.
Alimentées par CFF, les imprimantes 3D compactes et de bureau de Markforged utilisent deux têtes d'impression :une pour extruder un filament à base de nylon et l'autre pour poser des brins continus de fibres à haute résistance, y compris la fibre de carbone, le Kevlar et la fibre de verre .
Les fibres de renforcement forment la « colonne vertébrale » de la pièce imprimée, produisant des pièces rigides, solides et durables.
Par exemple, la machine X7 de qualité industrielle de Markforged, la dernière des six imprimantes 3D polymères de Markforged, imprimerait des pièces plus résistantes et 40 % plus légères que l'aluminium 6061.
Au prix de 70 000 $, le X7 présente un volume de construction de 330 x 270 x 200 mm et une hauteur de couche de 50 microns. Pour une machine à prix relativement bas, ces spécifications sont tout à fait correctes, sans parler de la capacité du X7 à imprimer des outils durables ainsi que des pièces de rechange et d'utilisation finale fonctionnelles.
En offrant la possibilité d'imprimer avec des matériaux renforcés, Markforged a puisé dans un marché très rentable. Rien qu'en 2018, la société aurait expédié plus de 2 500 imprimantes 3D industrielles. Avec une telle hyper-croissance, Markforge est en passe de devenir l'une des plus grandes sociétés de FA du secteur.
La nouvelle référence pour l'impression FDM grand format ?
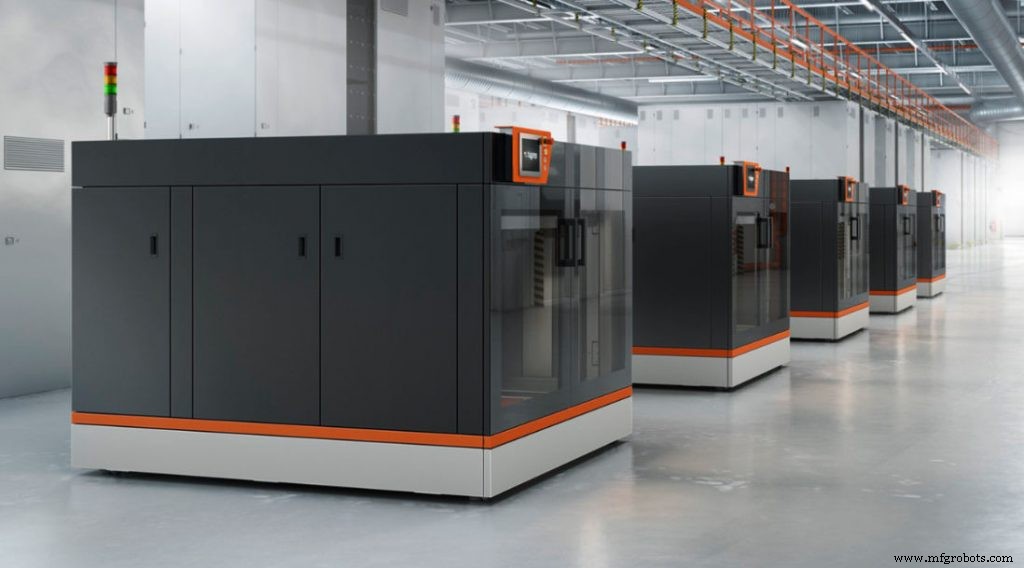
L'impression 3D grand format a le potentiel de résoudre de nombreux défis auxquels les fabricants sont confrontés lors du prototypage et de la production de pièces plus grandes.
De telles pièces ont généralement des délais de livraison plus longs, car l'assemblage est nécessaire. Ils nécessitent également la production d'outils plus gros, ce qui entraîne souvent des dépenses importantes.
Une entreprise aidant à surmonter ces défis est BigRep. Fondée en 2014, BigRep se positionne comme le fabricant des plus grandes imprimantes 3D d'extrusion du marché, avec des volumes d'impression de ses machines dépassant 1m³.
Alors que l'impression 3D de gros objets a ses avantages, il y a aussi une limitation clé :la vitesse. L'impression de pièces plus volumineuses peut prendre des jours, voire des semaines, avec un risque accru d'échec d'impression.
BigRep vise à résoudre ce problème de plusieurs manières.
Dans le passé, BigRep a introduit des buses plus grandes pour pouvoir extruder une plus grande quantité de plastique plus rapidement et a également introduit des bobines de filament de gros poids pour correspondre.
En 2017 , la société a commencé à produire son filament « haute vitesse », qui permet de réduire les temps d'impression jusqu'à 50 %.
Mais peut-être l'une des avancées les plus intéressantes a été la technologie d'extrusion de mesure de BigRep (MXT ).
Lors de formnext 2018, BigRep a présenté deux nouvelles imprimantes 3D pilotées par MXT :la BigRep PRO et la BigRep EDGE. Développé en partenariat avec Bosch Rexroth, le système d'extrusion MXT possède plusieurs caractéristiques clés qui le distinguent des extrudeuses standard.
Il dispose d'un réservoir spécial où le matériau en fusion est retenu. Une roue à engrenages, alimentée par un moteur pas à pas, prélève une quantité spécifiée de matériau de ce réservoir et la pousse dans la buse.
Cette approche permet un contrôle total sur la vitesse et la quantité de matériau déposé. Selon BigRep, le système MXT rend ses nouvelles imprimantes cinq fois plus rapides que les machines d'extrusion actuelles et permet d'obtenir une précision beaucoup plus grande.
Le système MXT actuel n'est que la première itération du concept MXT, mais, avec tous ses avantages, il sera passionnant de voir comment cette technologie évoluera à l'avenir.
Infusé de force isotrope
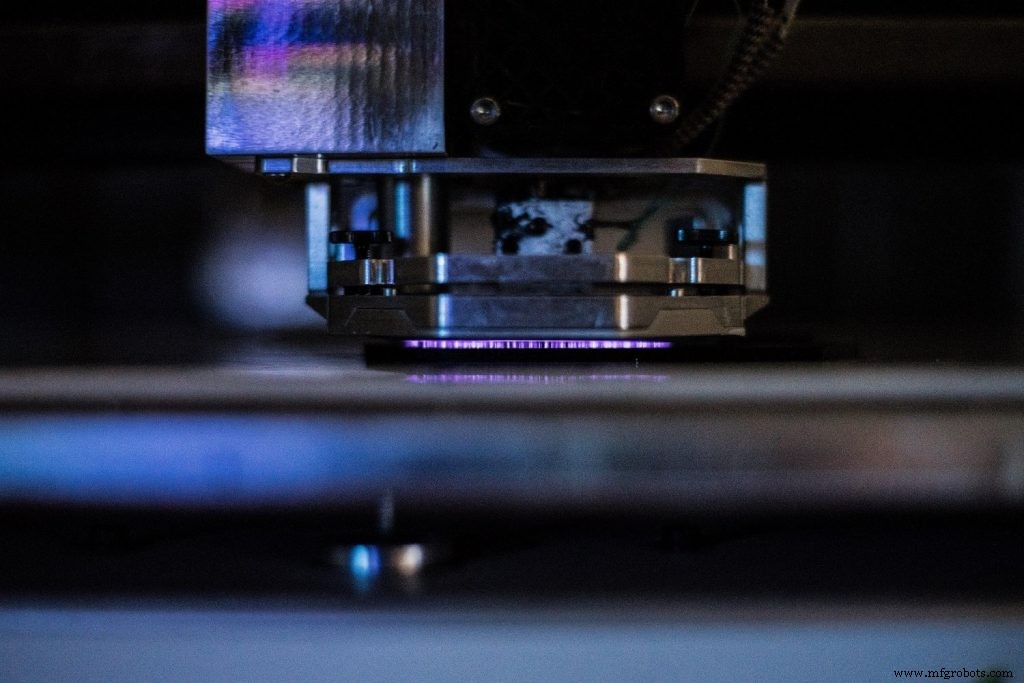
En plus des limitations de vitesse, les pièces anisotropes sont un autre problème courant dans l'impression 3D FDM, en raison de la nature par couches du processus d'impression.
Le dépôt de matériau couche par couche entraîne une faiblesse partielle de l'axe Z (direction dans laquelle les couches sont déposées). Ainsi, alors qu'une pièce moulée par injection peut être presque 100 % isotrope (également résistante dans toutes les directions), les pièces FDM perdent généralement de la résistance dans l'axe Z.
Certaines machines industrielles résolvent ce problème en utilisant une enceinte pour chauffer l'ensemble de la zone du bâtiment. Bien que cette solution contribue à améliorer la liaison entre les couches, elle a tendance à être trop énergivore.
La société d'impression 3D, Essentium, a développé une nouvelle technologie FDM prometteuse pour améliorer la résistance mécanique des pièces imprimées en 3D.
Connue sous le nom de FlashFuse, la technologie implique le dépôt d'un filament sensible à l'énergie et l'application d'un courant électrique. Ce courant chauffe la pièce, moulant efficacement les couches ensemble.
Cette approche présente deux avantages.
Premièrement, les pièces imprimées en 3D à l'aide de la technologie FlashFuse atteignent une résistance comparable à celle des pièces moulées par injection. Deuxièmement, il empêche la déformation des pièces, comme le gauchissement, car la température reste stable pendant le processus d'impression.
Cette technologie alimente désormais l'imprimante 3D à extrusion haute vitesse (HSE) 180-S d'Essentium, au prix de 75 000 $.
Surmonter certains des principaux obstacles à l'impression 3D FDM a aidé l'entreprise à lever 22 millions de dollars dans un tour de table de série A dirigé par BASF Venture Capital. Avec le récent financement, Essentium cherche à pousser sa technologie pour les applications de production, établissant une nouvelle référence pour l'impression 3D FDM.
Matériaux FDM de qualité industrielle
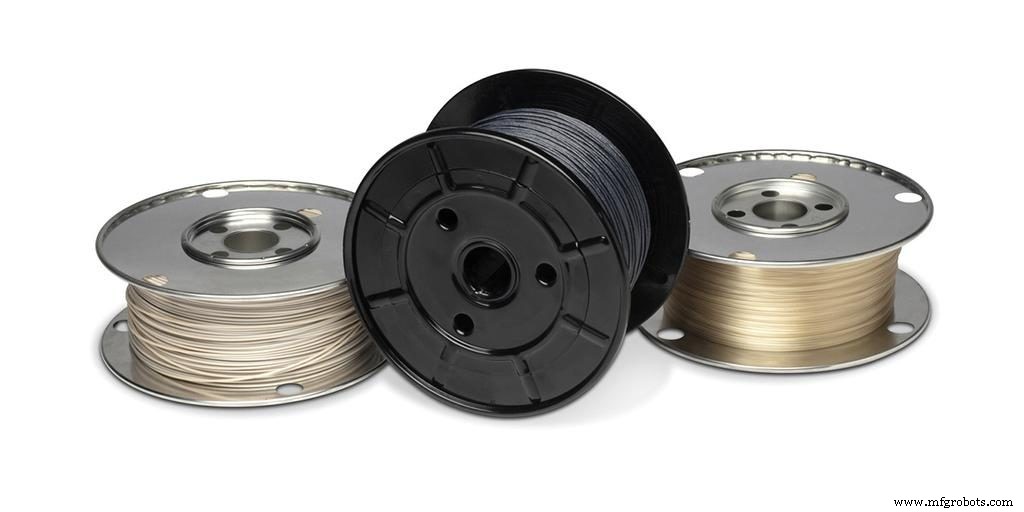
Bien que le marché des matériaux FDM soit encore jeune, il a considérablement évolué au fil des ans, poussant la science des matériaux au-delà des filaments PLA et ABS standard.
Aujourd'hui, les utilisateurs de FDM peuvent acheter des matériaux composites, nylon, flexibles, biocompatibles et de qualité technique, entre autres.
La possibilité d'imprimer avec des matériaux hautes performances comme l'ULTEM et le PEEK est particulièrement intéressante.
Ces thermoplastiques sont particulièrement difficiles à travailler en raison de leurs températures de fusion élevées. Cependant, de nombreuses machines FDM actuelles sont équipées d'extrudeuses à haute température, faisant de FDM l'une des quelques technologies additives capables de gérer ces thermoplastiques hautes performances.
De nombreuses avancées dans les matériaux FDM ont été rendues possibles grâce au nombre croissant d'entreprises chimiques rejoignant l'industrie, dans le but de faire progresser l'utilisation industrielle de l'impression 3D. Il s'agit notamment de BASF, SABIC, Verbatim (Mitsubishi Chemical Group), Evonik et Solvay, pour n'en nommer que quelques-uns.
Par exemple, Solvay a récemment lancé les filaments PEEK et PPSU. Les deux matériaux ont des propriétés exceptionnelles :le PEEK est bien connu pour son excellent rapport résistance/poids, tandis que le PPSU possède une résistance élevée à la chaleur, aux produits chimiques et aux chocs.
La disponibilité de tels thermoplastiques de qualité de production permet des applications clés telles que les pièces d'avion, les roulements automobiles, les composants pétroliers et gaziers et les dispositifs médicaux.
Il existe encore beaucoup plus de thermoplastiques FDM encore à développer. Mais la demande croissante contribuera à stimuler leur développement, permettant de nouvelles applications pour l'impression 3D.
Fermes d'impression 3D :l'avenir du FDM ?
Certains défis ont limité l'utilisation de l'impression 3D FDM dans les applications de production, notamment les pièces faibles et les vitesses d'impression lentes.
Cependant, les développements récents de la technologie FDM aident à lever les barrières de la vitesse et de la force. Mais pour que la technologie FDM décolle véritablement en tant que technologie de production, elle doit devenir plus évolutive.
Une des solutions réside peut-être dans les fermes d'impression 3D dites FDM. De telles fermes impliquent un réseau d'une douzaine d'imprimantes 3D ou plus pour permettre une production 24 heures sur 24. Voodoo Manufacturing est un exemple d'entreprise mettant cette approche en pratique.
L'entreprise abrite plus de 200 imprimantes 3D FDM et utilise un logiciel avancé pour attribuer automatiquement les travaux d'impression 3D aux machines disponibles. Grâce à sa ferme d'impression 3D, Voodoo Manufacturing est en mesure de répondre à des centaines voire des milliers de commandes au prix du moulage par injection.
Les fabricants d'imprimantes 3D ont également commencé à s'appuyer sur ce concept. En 2017, Stratasys a présenté son Continuous Build 3D Demonstrator, une unité modulaire comportant plusieurs « cellules » d'imprimante 3D FDM, chacune fonctionnant simultanément et contrôlée par une architecture centrale basée sur le cloud.
Stratasys n'a pas encore annoncé la disponibilité commerciale de la plateforme Continuous Build. Cependant, la société pense que cette approche pourrait réaliser le rêve de l'impression 3D pour la production.
À la lumière de son évolution vers des matériaux plus robustes et de nouvelles stratégies de fabrication, FDM est prêt pour la prochaine vague d'adoption. Des pièces plus solides et plus grandes et un processus d'impression 3D plus rapide et plus évolutif ouvriront de nouveaux marchés pour les machines basées sur l'extrusion, faisant de la technologie FDM une énorme opportunité de fabrication.
impression en 3D
- Nettoyage sans stress pour l'impression FDM
- Développement de normes pour l'impression 3D :où en sommes-nous aujourd'hui ? (Mise à jour 2020)
- Impression 3D métal :où en sommes-nous aujourd'hui ?
- Stéréolithographie et traitement numérique de la lumière :où en sommes-nous aujourd'hui ?
- Comment les imprimantes 3D de bureau transforment l'impression 3D
- Vérification des faits pour l'industrie 4.0 :où en sommes-nous aujourd'hui ?
- Nouvelles avancées dans FDM de Stratasys
- Comparaison des technologies 3D :SLA et FDM
- Impression 3D FDM :de bureau ou industrielle