10 technologies d'impression 3D passionnantes apparues au cours des 12 derniers mois
L'industrie de l'impression 3D se développe à un rythme étonnant. Au cours des 12 derniers mois, un certain nombre d'entreprises ont annoncé de nouvelles technologies et lancé de nouvelles machines, indiquant un avenir prometteur pour l'industrie.
Pour vous aider à vous tenir au courant des dernières nouveautés en matière d'impression 3D, voici notre liste des 10 technologies les plus intéressantes récemment annoncées.
Impression 3D Métal
1. Impression simultanée à plusieurs niveaux d'Aurora Labs
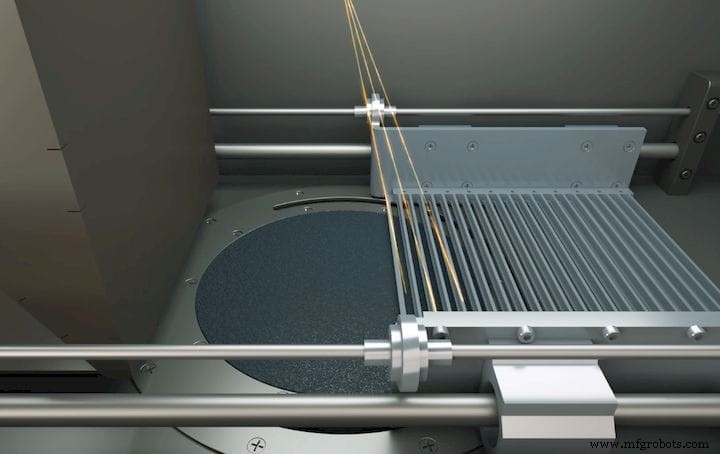
Alors que la perspective d'imprimer des pièces métalliques en 3D à la vitesse de 1 tonne de métal par jour peut sembler trop belle pour être vraie, le fabricant australien d'imprimantes 3D en métal, Aurora Labs, semble prêt à y parvenir.
Depuis 2014, Aurora Labs développe une nouvelle technologie d'impression 3D métal pour permettre l'impression 3D métal à des vitesses beaucoup plus rapides. Dévoilée pour la première fois lors de formnext 2018, la Multilevel Concurrent Printing (MCP™) est basée sur une technologie familière de fusion sur lit de poudre, mais présente une particularité.
Contrairement aux technologies traditionnelles de lit de poudre qui impriment une couche à la fois, MCP imprime plusieurs couches simultanément en un seul passage. Lors de formnext 2018, la société a déclaré qu'elle était en mesure d'imprimer environ 30 couches à la fois, dans le but d'augmenter ce nombre à 100 couches au cours des 12 prochains mois.
Comment ça marche ?
La technologie MCP comporte deux éléments clés :un mécanisme de recouvrement en forme de grille et de multiples faisceaux laser. Lorsque l'impression commence, le mécanisme de revêtement, qui comporte plusieurs trémies, glisse sur le lit d'impression, chaque trémie déposant différentes couches de poudre en un seul passage.
Lorsqu'une couche est déposée, elle est fusionnée par un laser, atteignant la poudre à travers les interstices spéciaux de la coucheuse. Au cours de ce même passage, les couches suivantes sont déposées et fusionnées successivement par des lasers.
Essentiellement, cela signifie que plusieurs couches peuvent être imprimées en un seul passage, ce qui réduit considérablement le temps d'impression.
En février de cette année, la société a annoncé qu'elle avait atteint une vitesse d'impression de 113 kilogrammes par jour. Pour illustrer ce jalon, Aurora Labs a imprimé en 3D une série de pièces hexagonales en titane de 10 mm de haut, ce qui n'a pris que 20 minutes.
Actuellement, Aurora Labs se prépare à lancer commercialement son système de fabrication rapide à la fin de l'année. Sera-t-il capable d'imprimer une tonne de métal par jour d'ici là ? Seul le temps nous le dira.
2. La technologie MELD de MELD Manufacturing
MELD Manufacturing Corporation a développé une nouvelle façon d'imprimer des métaux en 3D sans les faire fondre.
La technologie, qui est en développement depuis plus d'une décennie, a été dévoilée pour la première fois l'année dernière avec l'introduction de la technologie à grande échelle de MELD appareil B8.
Comment ça marche ?
La plus grande différence entre MELD et les autres techniques de FA métallique est qu'il s'agit d'un processus à l'état solide. Dans MELD, des poudres ou des fils métalliques sont passés à travers un outil rotatif creux, où la pression et le frottement déforment le métal et le mélangent dans le matériau en dessous.
Ce processus présente de nombreux avantages uniques. Premièrement, la technologie MELD crée des pièces entièrement denses, ce qui signifie qu'elles ne nécessitent pas de traitement thermique ultérieur.
Deuxièmement, le processus peut être utilisé non seulement pour fabriquer des pièces, mais aussi pour réparer et revêtir des composants existants ou créer des alliages métalliques personnalisés. Comme le souligne Nanci Hardwick, PDG de MELD Manufacturing :
« Nous sommes la seule technologie capable de faire évoluer et de fabriquer ou de réparer de très grandes pièces. Une autre capacité unique est que vous pouvez prendre une pièce existante, la placer dans la machine et ajouter du matériau supplémentaire, que vous souhaitiez un revêtement résistant à l'usure sur un matériau très léger ou que vous souhaitiez ajouter le matériau pour réparer une surface usée. "
L'imprimante 3D de MELD ne nécessite pas de boîtier et le processus se déroule dans un environnement ouvert. Cela signifie qu'il y a beaucoup de liberté pour créer des pièces plus grandes.
Cependant, la technologie a quelques limites. L'un est le défi de l'impression des surplombs. La technologie nécessite également des investissements importants, sa machine B8 coûtant 800 000 $. Mais avant de s'engager dans l'investissement, les clients peuvent essayer la technologie via le service d'impression proposé par MELD Manufacturing.
3. VELO 3D la fusion intelligente
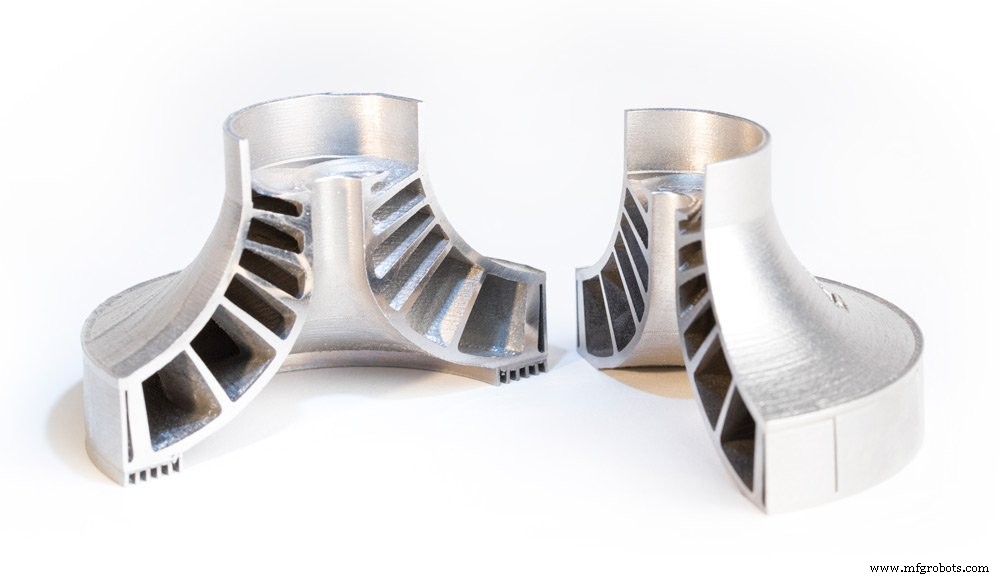
Le manque de répétabilité et la nécessité d'imprimer des structures de support sont deux des plus grands défis de l'impression 3D métal. VELO
3D
basé en Californie vise à résoudre ces défis avec sa technologie Intelligent Fusion.
Tandis que VELO
3D
a été fondée en 2014, la société est apparue pour la première fois sur le radar à l'automne dernier lorsqu'elle a dévoilé son imprimante 3D Sapphire à base de laser. Intelligent Fusion™ constitue l'épine dorsale de l'imprimante 3D et de VELO
3D
le logiciel de préparation d'impression de Flow™. En termes simples, Intelligent Fusion™ permet une intégration étroite entre le matériel, les logiciels et le processus.
Comment ça marche ?
Le système et le logiciel ont été co-développés pour réaliser un processus étroitement intégré qui contient des fonctionnalités assez intéressantes.
L'imprimante 3D Sapphire est basée sur un procédé de fusion sur lit de poudre, où un faisceau laser fond et fusionne couche par couche la poudre métallique pour former une pièce. Le système est largement équipé de capteurs, permettant le contrôle du bain de fusion en boucle fermée et améliorant ainsi la cohérence des pièces.
Côté logiciel, VELO
3D
a développé son logiciel Flow pour utiliser des fichiers CAO au lieu de fichiers STL. Cette décision a deux implications. Premièrement, étant donné que le format STL se rapproche de la surface d'un modèle CAO avec des triangles, l'utilisation de la CAO dès le départ permet d'obtenir une plus grande précision.
Deuxièmement, la taille des fichiers STL peut être très importante, rendant le traitement des fichiers lourd. Le passage à la CAO comme format de fichier initial rend ainsi le flux de préparation de l'impression plus simple et plus rapide.
De plus, le logiciel Flow a été développé pour être très sensible aux processus. Cela signifie, par exemple, qu'il peut exécuter une simulation avant le démarrage d'une impression, ainsi que prévoir et prévenir les défaillances avant qu'elles ne surviennent.
Combinez cela avec les capacités de contrôle en boucle fermée de Sapphire, et vous obtenez un processus très intelligent qui devrait fournir une fiabilité extrême.
Intelligent Fusion serait capable d'atteindre des taux de réussite de première impression allant jusqu'à 90 % tout en réduisant de trois à cinq fois le nombre de structures de support.
Alors que VELO3D continue pour améliorer sa technologie et acquérir de nouveaux clients, nous attendons avec impatience d'autres études de cas mettant en évidence les capacités uniques de VELO
3D
la fusion intelligente.
4. Jet métallique de HP
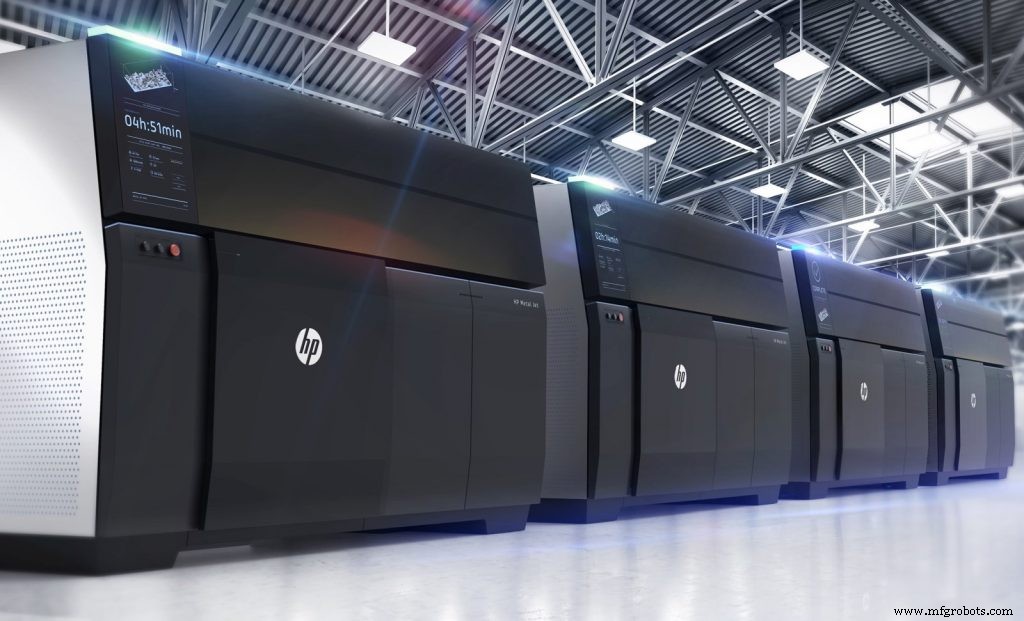
Dans le monde de l'impression 2D, les imprimantes HP sont synonymes de haute précision et de vitesse. En 2016, l'entreprise a dévoilé publiquement son passage à l'impression 3D, avec le lancement de son imprimante 3D polymère - Multi Jet Fusion.
Après s'être imposé du côté des polymères de l'impression 3D, HP est maintenant entré dans l'arène du métal, en annonçant l'année dernière son imprimante 3D Metal Jet. Le système a été développé pour être compétitif avec d'autres méthodes de production.
La technologie qui le permet est le Binder Jetting.
Comment ça marche ?
Dans le Binder Jetting, une fine couche de poudre métallique est déposée sur le lit d'impression. Une ligne de têtes d'impression se déplace au-dessus du lit d'impression, projetant de minuscules gouttes d'un liant - essentiellement de la colle - là où du métal solide est nécessaire. Lorsqu'une couche est terminée, une nouvelle couche de poudre est déposée suivie d'un autre passage du liant.
Après impression, la pièce finale reste dans un état « vert » et doit subir une opération de chauffage (appelée frittage) pour griller le liant et créer une pièce dense.
Ce procédé présente plusieurs avantages. D'abord, c'est rapide. Avec deux fois plus de têtes d'impression que les systèmes existants, HP affirme que ses imprimantes à jet de métal sont jusqu'à 50 fois plus productives que les machines à relier et de frittage laser comparables sur le marché aujourd'hui.
Deuxièmement, le processus utilise moins de liant, ce qui rend le processus de frittage plus rapide et moins cher.
« Avec le moulage par injection de métal, vous avez généralement plus de 10 % en poids de liant qui doit être brûlé. Dans notre cas, nous avons moins de 1%, ce qui est un ordre de grandeur inférieur, ce qui le rend plus rapide, moins coûteux et beaucoup plus simple à fritter », déclare Tim Weber, Global Head of Metals de HP, s'exprimant dans une interview avec AMFG. .
Fait intéressant, Metal Jet ressemble quelque peu à la technologie et à la proposition de valeur derrière le système de production de Desktop Metal. Les deux machines basées sur le jet de liant cherchent à perturber la fabrication traditionnelle en permettant une plus grande vitesse et une plus grande évolutivité. Par exemple, Desktop Metal affirme que son système est plus de 4 fois plus rapide que les autres machines à jet de liant.
Alors que le système de production de Desktop Metal a été publié plus tôt cette année, la technologie de HP est prévue pour une version 2020 et actuellement disponible uniquement via le service de production HP Metal Jet.
Une fois Metal Jet sorti, il sera passionnant de voir comment les deux systèmes se compareront dans la transition vers la production AM en série.
Impression 3D polymère
5. LaserProFusion d'EOS
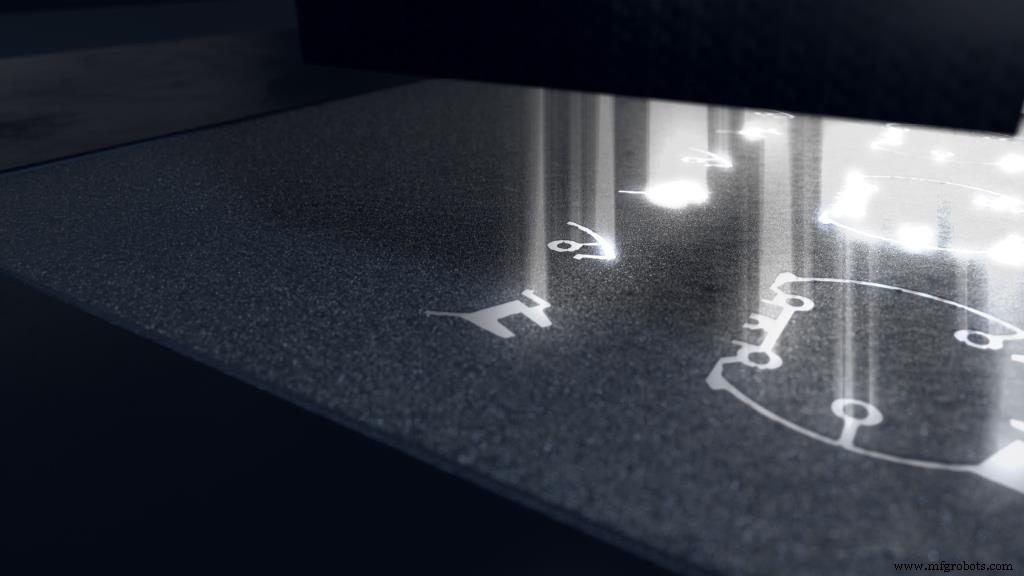
LaserProFusion est peut-être l'une des technologies d'impression 3D polymères les plus attendues. Créé à Formnext 2018, LaserProFusion est un futur système d'impression 3D polymère d'EOS qui promet de rendre la production 3D polymère 10 fois plus rapide grâce à l'inclusion d'un million de lasers à diodes.
EOS a une longue histoire dans impression 3D polymère, notamment avec le Frittage Laser Sélectif (SLS). Dans SLS, une couche de poudre, généralement du nylon, est déposée sur un lit d'impression et un laser contourne ensuite la section transversale d'une pièce, fusionnant les particules de poudre ensemble.
Alors que les machines SLS actuelles utilisent un ou quelques lasers CO₂, la technologie LaserProFusion pourra utiliser jusqu'à un million de lasers à diodes. Cela permettra à son système de créer des pièces non seulement avec une résolution élevée, mais également à une vitesse d'impression beaucoup plus élevée, rivalisant potentiellement avec le moulage par injection.
Cependant, la technologie, qui serait en développement depuis 8 ans, ne sortira pas plus tôt qu'en 2021. Il sera passionnant de voir quel impact LaserProFusion aura lorsqu'il le trouvera. dans le marché.
6. La technologie de vol de Farsoon
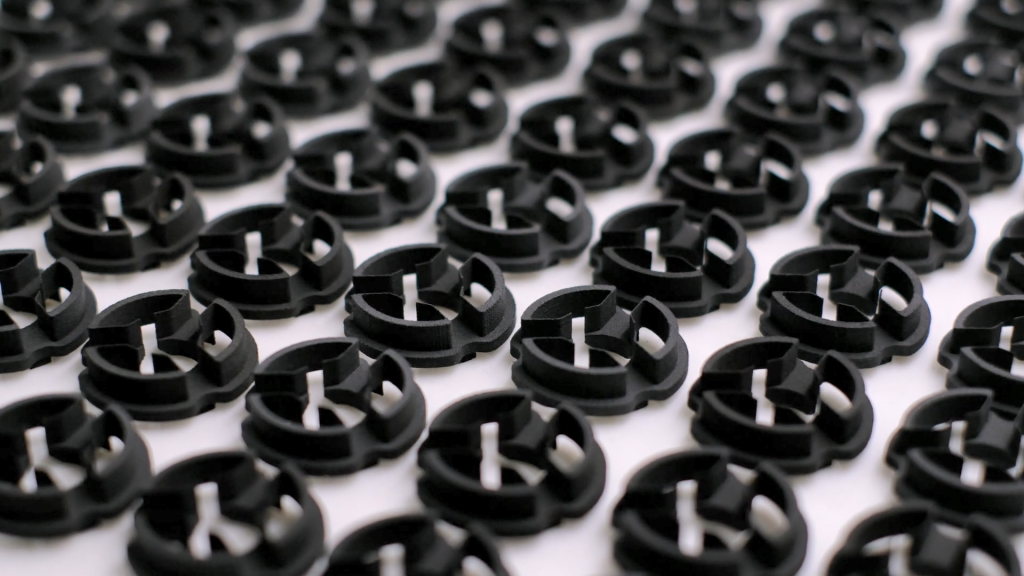
Une autre entreprise qui cherche à révolutionner la technologie SLS est Farsoon. Pour rendre le SLS encore plus rapide et précis, Farsoon exploite la puissance d'un laser à fibre dans sa nouvelle technologie de vol.
Comment ça marche ?
En SLS, une couche de poudre est étalée sur une plate-forme de fabrication, puis un laser trace les contours d'une couche d'une pièce, frittant la poudre ensemble.
Pour améliorer ce processus, le fabricant chinois d'imprimantes 3D a développé un nouveau système de numérisation et, surtout, a remplacé le laser CO₂ standard par un laser à fibre.
Un laser à fibre Le système est capable de fournir plus de puissance au lit de poudre et d'améliorer la distribution d'énergie au matériau. C'est parce que le faisceau laser à fibre permet une taille de spot laser plus petite. Cela se traduit par une densité de puissance plus élevée, permettant à la poudre d'être frittée plus rapidement.
Lorsqu'ils sont combinés, ces avantages se traduisent par une vitesse de numérisation de plus de 20 m/s, soit environ quatre fois celle des technologies comparables. De plus, la puissance ajoutée d'un laser rend les détails des caractéristiques aussi petits que 0,3 mm possible.
Conçue pour favoriser l'adoption de l'impression 3D pour la production à haut volume, Flight Technology est certainement un pas en avant dans cette direction.
7. Extrusion à grande vitesse d'Essentium
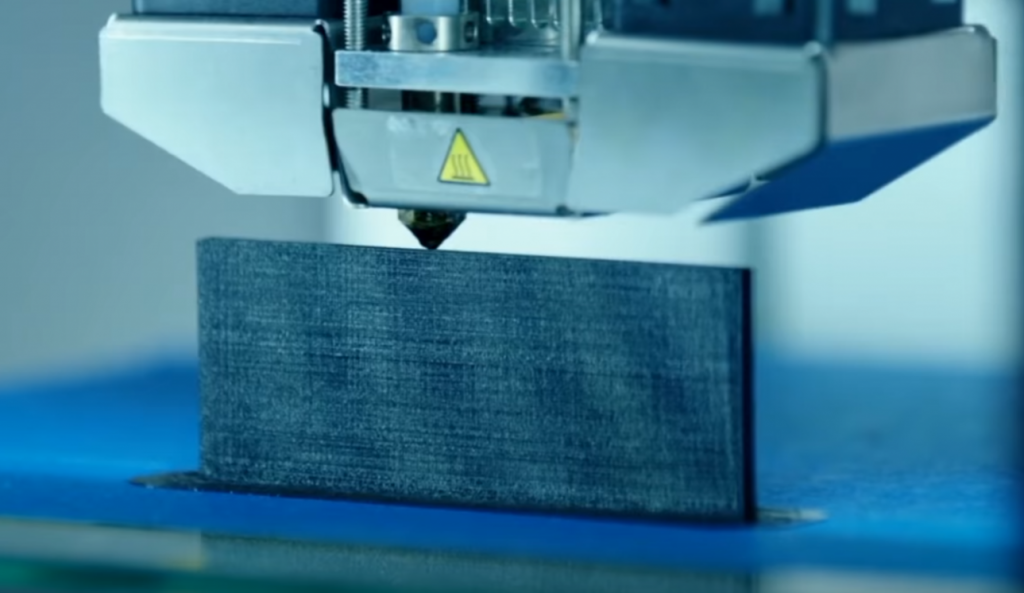
Le fabricant américain d'imprimantes 3D, Essentium, affirme avoir développé l'imprimante 3D par extrusion la plus rapide.
Comment ça marche ?
Dévoilée pour la première fois à Formnext 2018, la plate-forme d'extrusion à grande vitesse (HSE) d'Essentium est basée sur la technologie de fabrication de filaments fondus (FFF). Dans FFF, un filament thermoplastique est fondu et poussé à travers une buse, imprimant les pièces couche par couche. Un temps d'impression long, en particulier pour les objets plus volumineux, et a été l'une des principales limitations de FFF.
Pour surmonter ce défi, le HSE d'Essentium intègre un certain nombre de fonctionnalités de conception qui pourraient potentiellement en faire l'un des le plus rapide disponible.
Par exemple, le HSE utilise tous les moteurs linéaires, ce qui signifie que la tête d'impression peut se déplacer à une vitesse beaucoup plus grande (1 m/sec) et avec une plus grande précision. Apparemment, le système de mouvement est précis jusqu'à 30 microns de positionnement, ce qui est assez incroyable à de telles vitesses. Pour correspondre à la vitesse du système de mouvement, Essentium a également incorporé de puissants servomoteurs au lieu de moteurs pas à pas.
Un autre élément qui rend ce système tout à fait unique est la buse propriétaire d'Essentium, le HSE Hozzle™, qui peut chauffer de 20 °C à 500 °C en 3 secondes.
En plus de la technologie HSE, Essentium a également développé sa technologie FlashFuse pour surmonter la faiblesse des pièces dans l'axe Z (la direction dans laquelle les couches sont déposées), un problème courant avec les pièces imprimées en 3D .
La technologie implique le dépôt d'un filament sensible à l'énergie et l'application d'un courant électrique. Ce courant chauffe la pièce, moulant efficacement les couches ensemble et créant des pièces également solides dans toutes les directions.
Prévu pour une sortie plus tard cette année, Essentium combinera sa technologie FlashFuse et HSE en une seule plate-forme, nommée HSE 180•S.
En optimisant les mouvements, l'extrusion, la température et, enfin, la résistance des pièces, Essentium est en bonne voie pour établir une nouvelle référence pour l'impression 3D par extrusion.
8. L'ÉTAPE d'Evolve Additive Solutions
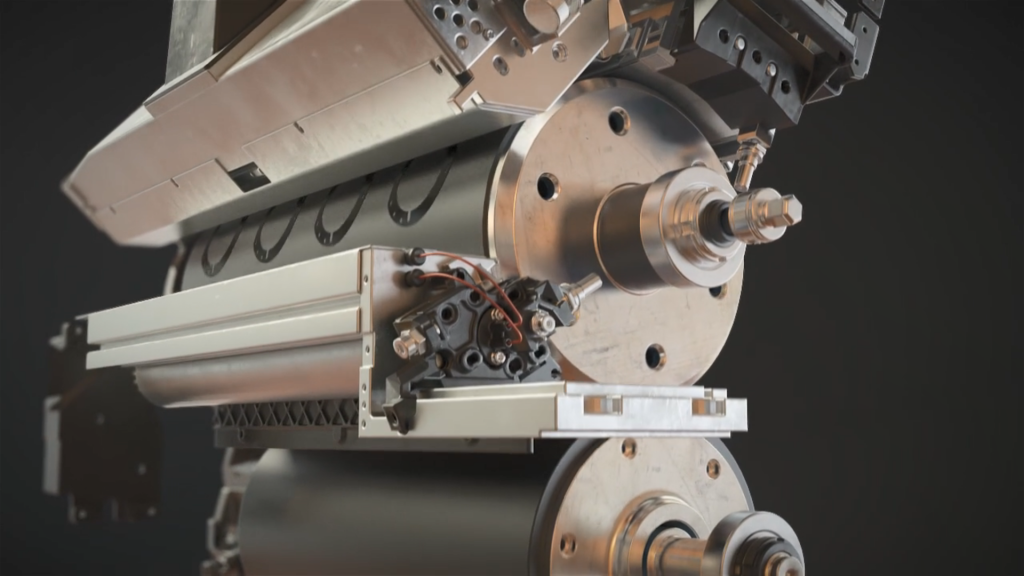
Le virage vers la production et la capacité de rivaliser avec la fabrication traditionnelle est un thème commun pour de nombreux fabricants d'imprimantes 3D. Evolve Additive Solutions, spin-off de Stratasys, ne fait pas exception.
Evolve est apparu pour la première fois sur la scène de l'impression 3D l'année dernière avec son procédé électrophotographique sélectif de toner (STEP) — une technologie que la société développe depuis près de dix ans.
Comment ça marche ?
STEP ne ressemble à aucun autre procédé d'impression 3D polymère connu sur le marché aujourd'hui, en ce sens qu'il n'utilise pas de laser et n'extrude pas de filaments plastiques. Au lieu de cela, il est basé sur la même technologie d'impression électrophotographique que l'on trouve dans de nombreuses imprimantes de bureau.
Le processus STEP commence par charger électrostatiquement un rouleau, qui passe ensuite sur le matériau en poudre, appelé toner. La couche de toner adhère au rouleau et est ensuite transférée sur une bande transporteuse.
Sur la bande transporteuse, la partie en croissance passe dans une unité de chauffage, où une nouvelle couche est fondue sur la précédente avant que la couche de matériau suivante ne soit déposée.
Cette technologie peut potentiellement permettre des débits très élevés, ce qui la rend rentable pour l'impression 3D de production en série. directions. Cela est dû en partie au fait que la machine Evolve préchauffe non seulement la pièce mais aussi la couche suivante, ce qui se traduit par une liaison supérieure entre les couches.
La technologie d'Evolve ne devrait pas être commercialisée avant 2020. Mais quand ce sera le cas, cela pourrait fournir une toute nouvelle façon d'imprimer en 3D des pièces en polymère.
9. La technologie Fluxprint de Fortify
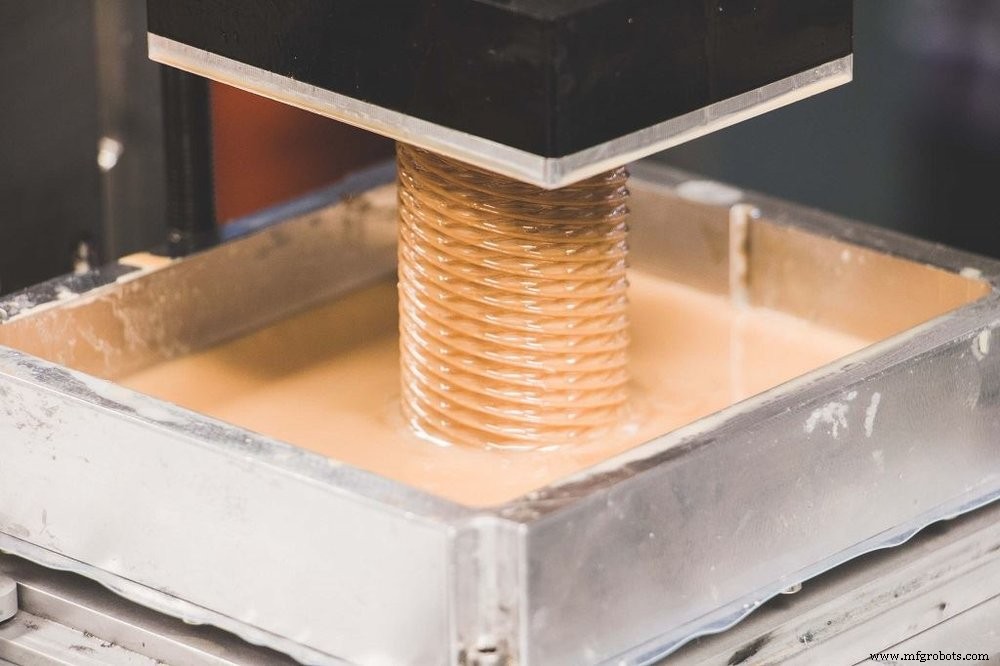
La startup basée à Boston, Fortify, a récemment émergé avec sa méthode unique d'impression 3D de pièces remplies de fibres extrêmement résistantes. Cette nouvelle méthode est activée par la technologie Fluxprint de Fortify, qui utilise des champs magnétiques pour contrôler l'alignement des fibres dans une pièce.
Comment ça marche ?
L'imprimante 3D Fortify est basée sur la technique de traitement numérique de la lumière, où un écran de projecteur de lumière numérique est appliqué pour solidifier les polymères sensibles à la lumière. Avec le procédé Fluxprint, les polymères sont mélangés à des fibres coupées, qui sont traitées avec un revêtement métallique.
Un champ magnétique est ensuite appliqué aux fibres les obligeant à s'orienter en fonction des forces magnétiques.
À l'étape suivante, l'imprimeur applique de la lumière pour polymériser une couche d'une pièce. Le processus se répète, couche par couche, pour terminer l'impression.
En contrôlant l'orientation des fibres sur chaque couche, Fluxprint peut créer des pièces très rigides et résistantes. Cette technologie pourrait être particulièrement utile pour produire des moules d'injection et des outils automobiles.
Fortify envisage de lancer sa première imprimante 3D commerciale dans les 8 à 12 prochains mois. Nous sommes ravis de voir cette technologie prendre forme et nous entendrons certainement beaucoup plus parler de Fortify à l'avenir.
10. Photopolymérisation programmable d'Origin
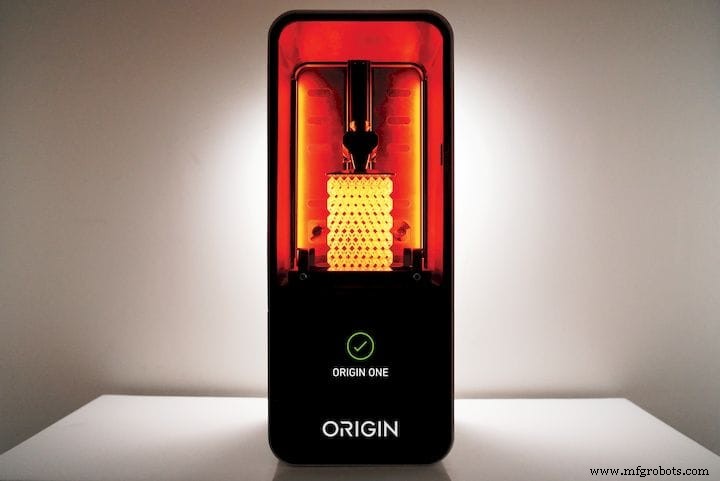
La startup américaine Origin est sortie de l'ombre lors de formnext 2018 avec l'ambition de permettre la production de masse avec l'impression 3D. Au salon RAPID le mois dernier, Origin a fait un pas vers la réalisation de sa promesse et a présenté l'imprimante 3D Origin One.
À première vue, vous seriez pardonné de penser que l'Origin One est tout simplement encore. une autre imprimante 3D en résine. Cependant, le secret de l'Origin One réside à l'intérieur de la machine. La société a développé une technologie de photopolymérisation programmable (P3), qui permet un débit élevé, un post-traitement réduit et une gamme beaucoup plus large de matériaux à imprimer.
Comment ça marche ?
Contrairement aux imprimantes 3D à résine actuelles, P3 est sans oxygène. L'imprimante 3D d'Origin utilise un gaz inerte, permettant au lit d'impression de se retirer pour construire la couche suivante avec extrêmement peu de force. En réduisant la force, la machine peut atteindre un débit plus élevé.
De plus, Origin affirme avoir été en mesure de réduire considérablement le temps de post-traitement requis en intégrant le processus de durcissement à l'intérieur de son imprimante 3D. Avec d'autres imprimantes 3D à résine, le durcissement a généralement lieu dans une unité spécialisée, prenant parfois jusqu'à plusieurs heures.
Avec P3, les pièces atteignent 99 % de leurs propriétés finales lors de l'impression. Par la suite, ils sont simplement nettoyés et rapidement passés à travers un système de convoyeur de durcissement UV final qui utilise une puissante lampe de fusion à micro-ondes. On dit que le processus ne prend pas plus de cinq minutes, ce qui est assez remarquable.
Actuellement, Origin dispose d'une cinquantaine de matériaux validés optimisés pour son processus P3. Ceci a été réalisé grâce à l'approche des matériaux ouverts d'Origin, qui s'appuie sur des experts en chimie pour élargir le choix de matériaux disponibles pour les utilisateurs.
Bien que l'entreprise ne fasse que commencer son voyage pour transformer la fabrication, la récente vague d'Origin des partenariats avec de grandes entreprises de matériaux et le fabricant de chaussures ECCO suggèrent qu'ils ont un avenir très prometteur devant eux.
Libérer le potentiel de l'impression 3D
Malgré leur diversité, toutes les technologies de notre liste partagent un objectif commun :faire passer l'impression 3D de ses origines de prototypage à la production industrielle à part entière. Pour y parvenir, les technologies sont développées pour être plus rapides, plus précises et plus fiables.
De toute évidence, il faudra du temps pour que ces promesses se réalisent. Cela dit, les technologies émergentes jettent les bases pour pousser l'impression 3D au-delà de ses limites actuelles vers un avenir radieux.
impression en 3D
- Scalmalloy :le dernier matériau hautes performances pour l'impression 3D sur métal
- Impression 3D en 2018 :7 tendances qui ont façonné l'industrie
- 10 utilisations intéressantes de l'impression 3D dans l'industrie des biens de consommation
- Entretien d'experts :vice-président des partenariats technologiques de VELO3D sur l'extension des capacités de l'impression 3D métal
- 10 exemples passionnants d'impression 3D dans l'industrie automobile en 2021
- À quel point les technologies d'impression 3D en métal sont-elles matures ?
- Évolution du marché du matériel d'impression 3D en 2020
- 9 entreprises du Fortune 500 pionnières dans l'utilisation de l'impression 3D industrielle
- 4 facteurs qui influent sur le coût de la fabrication métallique