À quel point les technologies d'impression 3D en métal sont-elles matures ?
[Crédit image :Laboratoire de recherche de l'armée CCDC]
L'impression 3D métal englobe un large éventail de technologies, chacune avec ses propres avantages et applications, ainsi que son propre niveau de maturité.
Lorsque vous cherchez à adopter une technologie d'impression 3D métallique spécifique pour la production, il est crucial de comprendre où se situent actuellement ses capacités et ses limites. Cependant, lorsqu'il s'agit d'impression 3D métal, les entreprises sont confrontées au défi de séparer la réalité du battage médiatique.
Pour aider les entreprises à évaluer plus facilement la maturité des technologies clés d'impression 3D métal, nous allons aujourd'hui examinant dans quelle mesure ils sont prêts pour la production de pièces finales, sur la base d'un système de niveau de préparation technologique (TRL), développé pour la première fois par la NASA.
Qu'est-ce que le niveau de maturité technologique (TRL) exactement ?
Développé pour la première fois par la NASA au début des années 1970, le « niveau de préparation technologique » est une approche utilisée pour évaluer si une technologie émergente est adaptée à l'exploration spatiale. Dans les années 1990, les TRL étaient appliqués dans de nombreuses agences gouvernementales américaines et sont maintenant d'usage courant dans de nombreuses industries.
Le système TRL mesure la maturité d'une technologie du niveau 1 (évaluation de concept) jusqu'au niveau 9 (déploiement réussi) . Chacun des neuf niveaux représente une étape importante dans le développement de la technologie.
Comment utiliser le TRL pour évaluer la maturité des technologies d'impression 3D métal ?
Nous avons appliqué cette approche pour évaluer la maturité des différentes technologies d'impression 3D. Pour identifier un TRL pour chaque technologie d'impression 3D métal, nous avons analysé son évolution, les industries qui l'adoptent, comment elle est utilisée aujourd'hui et les développements qui façonnent son avenir.
Notamment, dans certains cas, le TRL peut être spécifique à l'application. Par exemple, la technologie de dépôt direct d'énergie se situe à un TRL 8 pour les applications de production, tandis que ses applications pour la réparation ont atteint le niveau 9.
Sur la base de nos recherches, nous pensons que la majorité des métaux 3D les technologies d'impression ont franchi le TRL 7, qui fait référence aux tests dans un environnement opérationnel pour résoudre les problèmes de performances, et aux applications de prototypage fonctionnel et d'outillage.
Certaines ont également fait leurs preuves dans des conditions de fonctionnement normales (TRL 8) et se dirigent vers l'intégration dans l'écosystème de fabrication plus large (TRL 9).
Fusion laser sur lit de poudre

Niveau de maturité technologique : 8
La fusion laser sur lit de poudre (PBF) est l'une des technologies d'impression 3D métalliques les plus établies. Le processus PBF métallique consiste à appliquer sélectivement un laser puissant et affiné sur une couche de poudre métallique. De cette façon, les particules métalliques sont fusionnées couche par couche pour créer une pièce.
Les origines du métal PBF remontent à 1995, lorsque l'Institut Fraunhofer d'Aix-la-Chapelle, en Allemagne, a déposé le premier brevet pour la fusion laser des métaux. Depuis lors, de nombreuses entreprises, y compris des acteurs établis comme EOS, Concept Laser (acquis par GE) et SLM Solutions, sont entrées sur le marché du PBF avec leur vision de la technologie.
Au cours de la dernière décennie, les fabricants d'imprimantes 3D PBF métal ont travaillé dur pour optimiser la technologie de production. À cette fin, nous avons vu des acteurs clés du marché lancer des solutions de production automatisée et intégrée.
La majorité de ces solutions partagent des caractéristiques similaires :elles sont modulaires, configurables et offrent un haut niveau d'automatisation dans le but de maximiser l'efficacité et de réduire la quantité de travail manuel nécessaire.
Dans le même temps, le choix de matériaux pour PBF s'est continuellement élargi. Par exemple, EOS a introduit le mois dernier quatre nouvelles poudres métalliques pour ses imprimantes 3D métalliques. Parmi eux figurent l'acier inoxydable CX, l'aluminium AlF357, le titane Ti64 grade 5 et le titane Ti64 grade 23.
Grâce à ces développements, le laser PBF a trouvé sa place dans de nombreuses industries et applications. L'aérospatiale est une industrie particulièrement enthousiaste à l'idée d'adopter le PBF métallique.
Aujourd'hui, les pièces métalliques imprimées en 3D PBF alimentent des systèmes essentiels d'avions et d'engins spatiaux comme les moteurs. C'est là que les capacités clés de la technologie - la production de pièces complexes avec un assemblage simplifié et moins de déchets de matériaux - brillent vraiment.
Désormais, la technologie laser PBF est capable de délivrer des pièces fonctionnelles de manière répétée. Cependant, cela nécessite encore quelques réglages et tests avant que les fabricants ne puissent s'engager dans une production à grande échelle. C'est pourquoi nous suggérons qu'il est actuellement au niveau de maturité technologique 8.
À l'avenir, la facilité d'utilisation et la fiabilité des systèmes PBF métalliques augmenteront, grâce à bien des égards aux progrès des logiciels et de l'ensemble flux de travail.
Un exemple soutenant cette tendance vient du fabricant d'imprimantes 3D métal basé en Californie, VELO3D.
En développant sa technologie laser PBF, appelée Intelligent Fusion, la société a mis l'accent sur l'intégration logicielle et matérielle. Le résultat est un système étroitement intégré qui peut imprimer des pièces avec moins de supports, une meilleure finition de surface et, apparemment, un taux de réussite plus élevé. Ceci, à son tour, conduit à une plus grande fiabilité, une production plus rapide et moins de post-traitement.
Le laser PBF reste le moteur de l'industrie de l'impression 3D métal. Les imprimantes 3D métal PBF ont la plus grande base installée parmi les autres technologies d'impression 3D métal. Et les fabricants d'imprimantes 3D PBF détiennent les plus grandes parts du marché de l'impression 3D métal par rapport aux entreprises produisant d'autres types d'imprimantes 3D métal.
Pour cette raison, un certain nombre de matériaux sont d'abord développés pour les technologies PBF métalliques. Cela signifie que l'évolution de cette technologie va se poursuivre, portée par la demande de pièces métalliques complexes et hautes performances imprimées en 3D.
Fusion par faisceau d'électrons
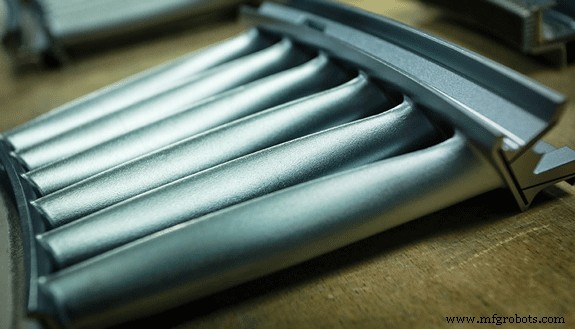
Niveau de maturité technologique : 8
La fusion par faisceau d'électrons, comme le laser PBF, appartient à la famille des technologies d'impression 3D par fusion sur lit de poudre. L'EBM fonctionne de manière similaire au laser PBF en ce sens que les poudres métalliques sont également fondues pour créer une pièce métallique entièrement dense.
La principale différence entre les deux technologies est la source d'énergie :au lieu d'un laser, les systèmes EBM utilisent un faisceau d'électrons de haute puissance comme source de chaleur pour faire fondre des couches de poudre métallique.
Depuis le brevetage de la technologie en 2000, la société suédoise Arcam est restée le principal fabricant d'imprimantes 3D EBM.
Après l'acquisition de la société par GE en 2016, la technologie EBM a continué d'évoluer. En 2018, Arcam a lancé sa prochaine génération de machines EBM, les Spectra H.
Le « H » signifie « métal chaud », ce qui signifie qu'il peut traiter des matériaux à haute température et sujets aux fissures tels que l'aluminure de titane. (TiAl) à des températures atteignant 1000°C.
Arcam EBM Spectra H possède un certain nombre de nouvelles fonctionnalités visant à augmenter la productivité et à réduire les coûts globaux.
Par exemple, l'EBM Spectra H est équipé d'une puissance HV de 6 kW unité, qui permet de réduire les étapes de pré- et post-chauffage de 50% par rapport aux autres machines EBM actuellement sur le marché.
De plus, le processus de stratification a été amélioré pour réduire les températures élevées. Cela permet aux fabricants d'économiser jusqu'à cinq heures sur une construction pleine hauteur et d'augmenter les vitesses d'impression jusqu'à 50 % par rapport aux autres machines EBM.
L'entreprise GE Aviation, Avio Aero, aurait utilisé 35 Arcam. machines :31 machines Arcam A2X et 4 machines Arcam EBM Spectra H. Chez Avio Aero, les imprimantes 3D sont utilisées pour produire des aubes TiAl pour les turbines basse pression du nouveau gros moteur GE9X.
En plus de l'aérospatiale, l'industrie médicale utilise largement la technologie pour produire des implants médicaux . La première utilisation de l'EBM pour cette application remonte à 2007.
Soutenue par les ressources et l'expertise de GE en FA métal, la technologie EBM est en voie d'industrialisation. La technologie est appliquée dans des environnements de production au sein d'industries hautement réglementées comme l'aérospatiale et le médical. Compte tenu de ces applications, EBM a atteint le TRL 8.
Dépôt d'énergie direct
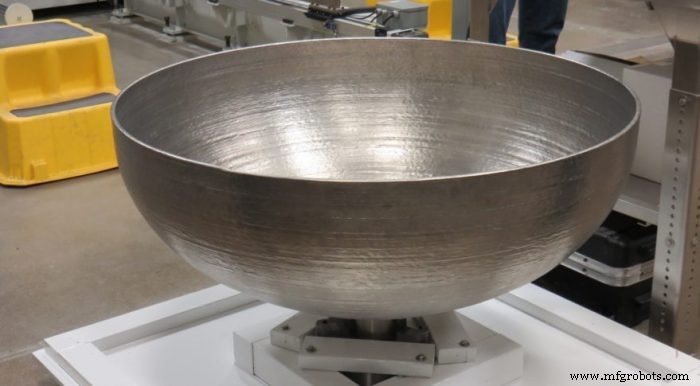
Niveau de maturité technologique : 8
Issu des procédés de soudage, le dépôt direct d'énergie (DED) consiste à faire fondre du métal à l'aide d'un laser ou d'un faisceau d'électrons tandis que le matériau est poussé à travers une buse sur une plate-forme de fabrication.
Les systèmes DED utilisent du fil ou de la poudre comme matière première. La plupart des systèmes utilisent des matériaux du commerce développés pour le soudage ou la métallurgie des poudres. L'utilisation de matériaux standard présente de nombreux avantages, notamment une sélection de matériaux plus large, une qualité supérieure et un prix inférieur.
L'une des premières et des plus réussies applications du DED a été la réparation de composants endommagés. La technologie est utilisée pour ajouter de la matière aux pièces endommagées comme les aubes de turbine et les inserts de moule d'injection. En réparant les pièces usées, DED contribue à réduire les temps d'arrêt et les coûts associés au remplacement d'une pièce, tout en prolongeant la durée de vie de la pièce.
Pour permettre l'utilisation du DED au-delà des applications de réparation, les fabricants de systèmes DED ont développé et optimisé des solutions pour la production de pièces métalliques fonctionnelles.
Par exemple, Sciaky, l'un des pionniers de la technologie DED, a introduit le contrôle en boucle fermée dans ses systèmes de fabrication additive par faisceau d'électrons. Le système de surveillance des processus de Sciaky combine l'imagerie optique en temps réel avec la vision industrielle pour mesurer la taille, la forme et la température du bain de fusion.
Sur la base des données obtenues à partir de l'image, un système de contrôle en boucle fermée a ensuite donne des commandes de réglage au logiciel contrôlant la puissance du faisceau, la vitesse d'avance du fil et le mouvement de la machine. Grâce à cela, la répétabilité du processus peut être considérablement améliorée.
La technologie DED a déjà été appliquée dans de nombreuses applications aérospatiales et de défense. Les exemples incluent les dômes de réservoirs de carburant en titane pour les satellites, les pièces structurelles en titane pour le Boeing 787 Dreamliner et les pièces de rechange pour les véhicules militaires.
La technologie s'est imposée comme une solution de maintenance facilement disponible. Avec cette application, DED est à TRL 9.
En ce qui concerne les applications de production, DED peut également être utilisé comme outil de fabrication. Cependant, des développements supplémentaires sont nécessaires en termes d'avancement du contrôle en cours et d'amélioration de la résolution d'impression.
À l'heure actuelle, la technologie produit des formes proches du filet, qui nécessitent un usinage important pour obtenir des spécifications de pièce et une bonne finition de surface. L'amélioration de la résolution d'impression permettra aux fabricants de réduire le temps et les coûts nécessaires à l'usinage secondaire.
Jet de liant métallique
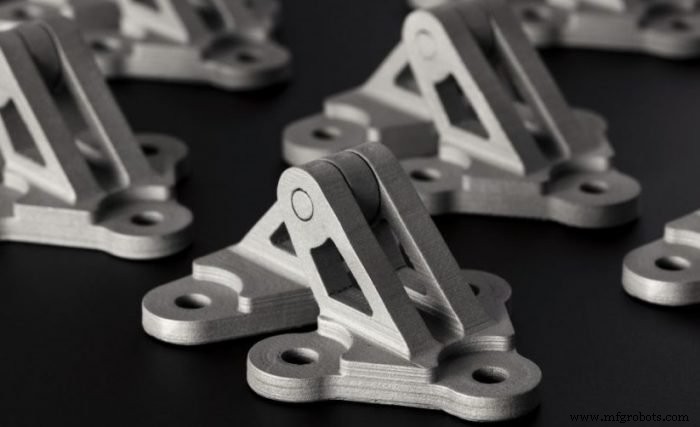
Niveau de maturité technologique :variable
Le jet de liant métallique évolue rapidement vers une technologie de fabrication très prometteuse. Cependant, le niveau de préparation technologique varie considérablement parmi les technologies de projection de liant métallique sur le marché aujourd'hui.
Le jet de liant métallique a été développé pour la première fois en 1993 au MIT. Le processus d'impression commence par l'étalement d'une fine couche de poudre, les têtes d'impression déposant stratégiquement des gouttelettes de liant dans le lit de poudre. Le processus se répète couche par couche jusqu'à ce que la pièce soit terminée, avec de la poudre inutilisée (environ 95%) recyclée.
ExOne, qui licencie la technologie du MIT depuis 1996, est restée la seule entreprise à proposer du métal services et systèmes de jet de liant jusqu'au début des années 2010. Les systèmes de projection de liant métallique d'ExOne ont été largement utilisés pour créer des prototypes et des outillages métalliques.
Cependant, alors que les brevets sur le jet de liant métallique commençaient à expirer, la concurrence s'est intensifiée, encourageant l'entreprise à commencer le développement de solutions au niveau de la production. La dernière en date, l'imprimante 3D X1 25PRO, a été lancée commercialement il y a quelques mois.
Digital Metal est un autre acteur important sur le marché du jet de liant métallique. Ses imprimantes 3D DM P2500, introduites pour la première fois en 2017, auraient produit plus de 300 000 composants dans diverses industries, notamment l'aérospatiale, les produits de luxe, les outils dentaires et les équipements industriels.
Il y a aussi quelques nouveaux venus dans le domaine du jet de liant métallique, notamment HP et Desktop Metal.
Après avoir dévoilé sa technologie Multi Jet Fusion pour les pièces en polymère en 2016, HP a présenté la prochaine extension de ses offres d'additifs en 2018 :un système d'impression 3D Metal Jet. Avec un nouveau système, HP cherche à intégrer la technologie dans un environnement de production à haut volume.
Pour y parvenir, l'entreprise a équipé son système de plusieurs buses et introduit un liant innovant. Combinés, ces progrès sont censés rendre le processus d'impression plus rapide et plus simple.
La technologie derrière l'imprimante 3D de Desktop Metal est ce que l'entreprise appelle le Single Pass Jetting (SPJ), une version plus rapide du processus typique de jet de liant. L'entreprise affirme que son système peut imprimer jusqu'à 12 000 cm3/h, ce qui se traduit par plus de 60 kg de pièces métalliques par heure.
Il est intéressant de noter que le système HP Metal Jet et le système de production Desktop Metal partagent une valeur quelque peu similaire proposition. Les deux machines basées sur le jet de liant cherchent à perturber la fabrication traditionnelle en permettant une plus grande vitesse et une plus grande évolutivité.
Alors que le système de production de Desktop Metal a été publié plus tôt cette année, la technologie de HP est prévue pour une version 2020 et est actuellement disponible uniquement via le service de production HP Metal Jet.
Certes, de nombreuses technologies de projection de liant métallique ne sont apparues que récemment. Cela signifie qu'ils auront besoin d'un certain temps pour prouver qu'ils sont prêts pour les applications de production en série grâce à des tests supplémentaires, soit en interne, soit sur le site du client.
Avec des antécédents dans les applications de production, les technologies plus anciennes, comme celles de Digital Metal et ExOne, se situent entre les niveaux de maturité technologique 7 et 8. Nous nous attendons à ce que les technologies de jet de liant métallique les plus récentes atteignent et dépassent le TRL. 8 dans les prochaines années.
Les systèmes de projection de liant métallique continueront d'évoluer dans le but de répondre aux marchés difficiles à pénétrer pour d'autres technologies d'impression 3D métalliques, y compris la production de biens automobiles et industriels en plus grand volume. Cela crée de nombreuses opportunités de croissance intéressantes pour cette technologie à l'avenir.
Dépôt de métal lié
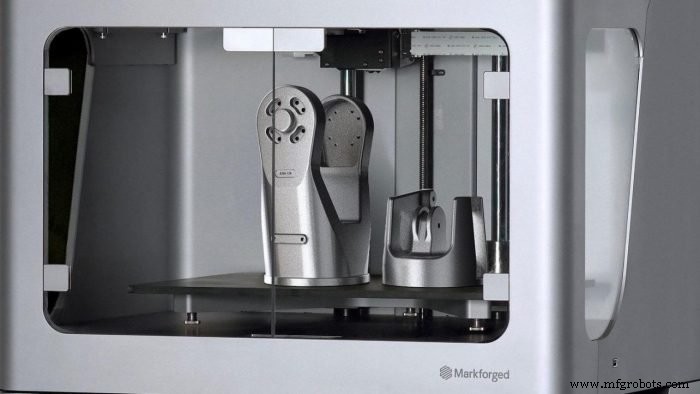
Niveau de maturité technologique : 7
Bound Metal Deposition est un nouveau venu passionnant dans le domaine de la fabrication additive métallique. La technologie fonctionne de manière similaire à la fabrication de filaments fondus (FFF), où un filament est chauffé et extrudé à travers une buse, créant une pièce couche par couche. Cependant, contrairement aux filaments plastiques utilisés dans le FDM, l'extrusion métallique utilise des filaments constitués de poudres ou de pastilles métalliques enrobées de liants plastiques.
Les deux entreprises les plus importantes travaillant dans ce domaine sont Markforged et Desktop Metal. Les deux sociétés ont dévoilé pour la première fois leurs systèmes d'impression 3D métalliques (Markforged's Metal X et Desktop Metal's Studio System) en 2017.
Actuellement, la technologie est largement utilisée pour créer des prototypes et des outillages métalliques plus rapidement et à moindre coût.
Un exemple est Dixon Valve &Coupling Company, un fabricant et fournisseur d'accessoires pour les industries de transfert de fluides. La société a utilisé les mâchoires de préhension Metal X de Markforged pour imprimer en 3D. Ces outils sont essentiellement des pinces, qui sont montées sur un bras robotisé qui ajoute des bagues d'étanchéité aux raccords en acier.
La production de tels outils prend 14 jours et coûte 355 $. À titre de comparaison, l'impression 3D d'une pince en métal coûte 7 $ et nécessite 1,25 jour, soit une réduction de plus de 90 % pour le coût et le délai.
Alors que la technologie de dépôt lié fait de grands progrès en termes de coûts. prototypage efficace et rapidité de mise sur le marché, son utilisation côté production reste limitée. D'une part, ces systèmes sont positionnés comme des imprimantes 3D métalliques compactes, qui peuvent être difficiles à mettre à l'échelle.
Cependant, à mesure que de plus en plus d'entreprises adoptent la technologie, en particulier pour les emplacements éloignés comme les plates-formes pétrolières, nous pouvons voir plus d'exemples de pièces de rechange et d'utilisation finale créées par dépôt de métal lié dans les années à venir.
Innover avec l'impression 3D métal
La majorité des technologies d'impression 3D métalliques ont atteint des niveaux de préparation technologique assez élevés, ce qui signifie qu'elles sont adaptées aux applications de production.
De toute évidence, beaucoup de travail reste à faire, notamment sur l'amélioration de la rentabilité et de la rapidité des technologies d'impression 3D métal. Actuellement, les procédés sur lit de poudre, le DED et le jet de liant métallique sont considérablement plus coûteux que les systèmes de fabrication conventionnels.
Les systèmes de dépôt de poudre liée à faible coût apportent une certaine accessibilité à l'impression 3D métal et pourraient offrir un bon point d'entrée pour les petites entreprises.
En fin de compte, faire progresser la technologie elle-même n'est qu'une pièce du puzzle. Il est tout aussi crucial pour que l'écosystème autour de l'impression 3D métal continue d'évoluer. Cela peut impliquer le développement d'une solution logicielle mieux intégrée et plus facile à utiliser, l'automatisation des opérations de post-traitement et la création de flux de travail rationalisés.
Ce n'est qu'en assemblant toutes les pièces qu'il existe un moyen de parvenir à une innovation significative en matière de processus et de produits avec l'impression 3D en métal.
impression en 3D
- Comment les modèles d'objets sont conçus pour l'impression 3D
- Comment les ponts sont utilisés dans l'impression 3D
- Comment l'impression 3D peut-elle profiter à la fonte des métaux ? Voici 3 façons
- Impression 3D métal :où en sommes-nous aujourd'hui ?
- Dans quelle mesure votre industrie est-elle mature dans son adoption de l'impression 3D ? [Infographie]
- 10 technologies d'impression 3D passionnantes apparues au cours des 12 derniers mois
- Comment les imprimantes 3D de bureau transforment l'impression 3D
- AM dans le monde :quelle est la maturité de l'impression 3D dans la région Asie-Pacifique ?
- Évolution du marché du matériel d'impression 3D en 2020