Entretien d'experts :vice-président des partenariats technologiques de VELO3D sur l'extension des capacités de l'impression 3D métal
L'impression 3D métal est peut-être une technologie innovante, mais elle n'est pas sans défis. C'est un processus qui nécessite des considérations de conception fastidieuses, un post-traitement et un certain nombre d'essais et d'erreurs pour obtenir une impression réussie. Dans le but de résoudre ces problèmes et d'autres, la société californienne VELO
3D
, a dévoilé l'année dernière son imprimante 3D métal Sapphire à laser.
Fruit de quatre années de développement, l'imprimante Sapphire possède deux éléments clés :sa technologie Intelligent Fusion™ et son logiciel de préparation d'impression Flow. Les deux fonctionnalités fonctionnent main dans la main pour permettre des avantages potentiellement révolutionnaires, comme une répétabilité améliorée et des impressions sans support. Ce dernier, en particulier, est possible grâce à la capacité de l'imprimante Sapphire à imprimer des surplombs extrêmes sans avoir besoin de structures de support.
Dans l'entretien d'experts de cette semaine, nous parlons avec Zachary Murphree, vice-président de la technologie Partenariats chez VELO
3D
, pour discuter de la valeur de sa technologie Intelligent Fusion™, de ses applications les plus intéressantes et de l'avenir du secteur de la FA métallique.
Pourriez-vous me parler un peu de VELO 3D ?
VELO
3D
a été fondée dans le but d'élargir les applications de la fabrication additive métallique.
Une partie de ce qui a motivé la fondation était la frustration autour de la fabrication additive que notre fondateur, Benny Buller, a éprouvée lorsqu'il a essayé de fabriquer des pièces pour la production. Metal AM ne tenait pas certaines des promesses qui avaient été faites, comme la complexité sans coût et l'accélération du processus de développement de produits.
Il y a de gros points de discussion autour de la FA métal qui ne sont pas tout à fait vrais. Une partie de notre objectif est d'éliminer cette frustration et d'élargir la gamme d'applications afin que la FA métallique tienne vraiment ses promesses.
Pour atteindre cet objectif, nous avons réexaminé le processus pour en comprendre la physique fondamentale. En comprenant parfaitement le processus, nous avons développé un système capable d'imprimer des choses qui étaient auparavant considérées comme non imprimables et d'élargir la gamme de géométries qui peuvent être considérées comme rentables pour la fabrication additive.
C'est ainsi que nous avons développé nos deux produits phares :l'imprimante métal Sapphire et le logiciel Flow. Ces deux produits constituent le système qui permet l'impression 3D de pièces qui ne peuvent être produites avec aucun autre système.
VELO 3D est sorti du mode furtif avec l'imprimante Sapphire l'année dernière, lançant l'entreprise publiquement au Salon international de la fabrication. Quelle valeur votre système apporte-t-il sur le marché ?
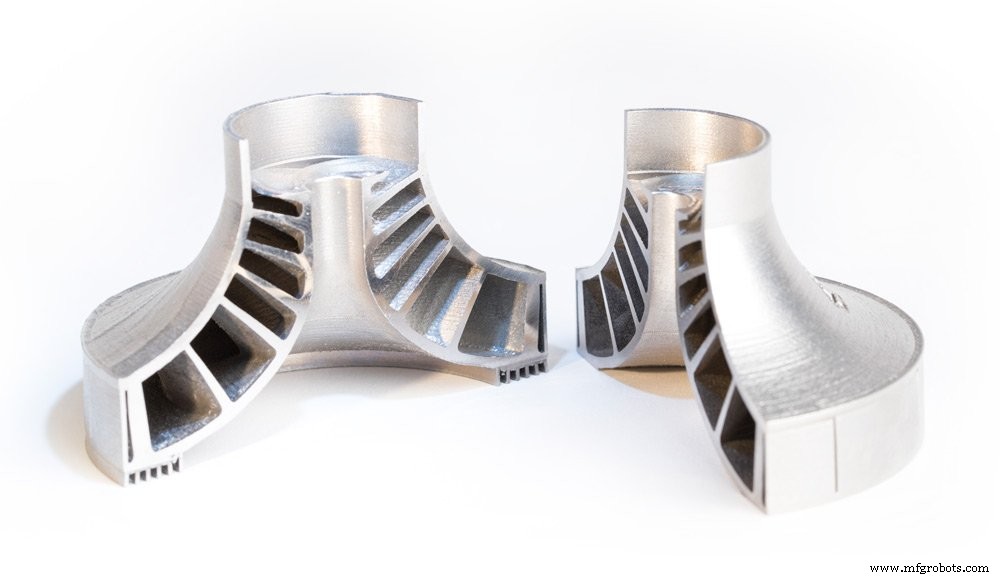
L'une des choses importantes que nous essayons de souligner est que notre technologie n'est pas seulement le matériel physique. L'imprimante Sapphire est la partie la plus visible de notre solution, mais ce n'est qu'un composant. Pour permettre au système de faire ce qu'il peut faire, il faut notre logiciel de préparation d'impression Flow. Le processus ne peut pas être exécuté sur d'autres systèmes ; nous avons vraiment dû développer le matériel à partir de zéro pour activer les processus que nous exécutons.
Cette combinaison nous permet d'accomplir une fabrication sans assistance, ce qui revient au contrôle des processus. VELO
3D
s'est concentré là-dessus dès le début. En contrôlant le processus et en l'exécutant dans une fenêtre très étroite, nous sommes en mesure d'imprimer des pièces à très faible angle de porte-à-faux sans supports.
Comment fonctionne la technologie ?
Le processus commence par la géométrie CAO. Nous travaillons avec la géométrie CAO sous-jacente et non avec des formats de fichiers tesselés comme un fichier STL. Le fichier CAO est d'abord importé dans notre logiciel de préparation d'impression Flow.
Le logiciel vous permet d'orienter la pièce et de placer les supports — un peu de la même manière que ce qui peut être fait avec certaines des solutions logicielles existantes. Mais ce qui est différent ici, c'est que notre logiciel Flow est très sensible aux processus. Le fait qu'il ait été co-développé avec le matériel signifie qu'il s'agit d'un système très étroitement intégré.
Le logiciel est également capable de prédire des facteurs tels que le moment où les pièces se déformeront ou le moment où des défaillances de support se produiront pendant la construction, et peut fournir des informations sur l'orientation et les supports avant même le début de l'impression.
Nous avons également une fonction de correction de déformation qui nous permet de pré-déformer la géométrie afin que la pièce que vous sortez de la machine à la fin de l'impression ait la bonne géométrie. Il s'agit d'un logiciel de simulation thermique.
La dernière partie du logiciel de préparation d'impression est le paramétrage. Ceci est, encore une fois, étroitement intégré au matériel afin que nous puissions définir les paramètres de la trajectoire de l'outil d'une manière très spécifique à la géométrie d'une pièce. Ces paramètres sont beaucoup plus nuancés que ce que vous obtenez de certains des systèmes conventionnels de fabrication additive métallique.
Tout cela ensemble vous donne un fichier d'impression qui inclut une grande partie de l'intelligence du processus. C'est pourquoi nous appelons notre technologie Intelligent Fusion.
L'imprimante Sapphire est conçue pour exécuter ces instructions de construction de manière très contrôlée. Une grande partie de notre succès repose non seulement sur le contrôle très étroit de l'atmosphère, de la chambre, du lit de poudre et du flux de gaz, mais également sur le processus lui-même.
L'une des choses que nous avons sur le système est un système de contrôle du bassin de fusion en boucle fermée qui nous permet d'atteindre les températures cibles pour que le processus réussisse. Nous avons également une coucheuse sans contact qui nous permet de fabriquer des pièces d'une manière qui ne peut pas être réalisée sur d'autres systèmes.
Pourriez-vous développer les défis spécifiques que votre technologie résout ?
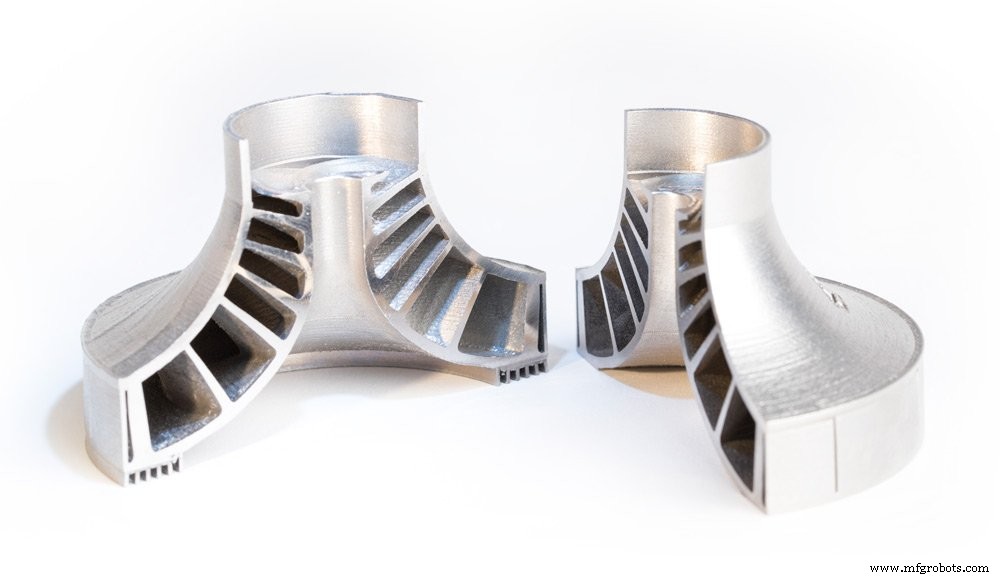
En discutant avec des clients, j'ai définitivement vu que les ingénieurs sont désireux d'utiliser la FA métallique comme technique de fabrication.
Mais malgré une industrie vieille de trente ans, il reste encore beaucoup d'immaturité dans la façon dont les pièces sont fabriquées, en particulier lorsque vous la comparez aux méthodes de fabrication établies.
Lorsque vous imprimez des pièces, il est souvent difficile de les rendre imprimables en premier lieu. Cela se résume en grande partie aux restrictions géométriques. Le plus grand exemple de ceci est la règle standard des 45 degrés, lorsque vous ne pouvez pas imprimer des surplombs non pris en charge qui sont inférieurs à 45 degrés par rapport à l'horizontale. Bien que ce soit la norme, les gens l'ont poussé un peu plus bas. Selon le matériau et la machine, vous pouvez atteindre 40 ou 35 degrés.
Bien qu'il y ait eu quelques innovations, il s'agit toujours d'une restriction assez fondamentale. Cela signifie qu'il faut souvent mettre des supports à des endroits où il sera très difficile, voire impossible, de les retirer par la suite.
Si vous regardez une volute pour un carter de pompe ou un carter de turbo, qui est une pièce de forme toroïdale et creuse en forme de beignet, les supports à l'intérieur signifient que ce n'est pas un bon candidat pour le métal UN M.
Les roues carénées sont un autre défi. Pendant longtemps, les gens ont voulu, mais ont vraiment lutté, pour imprimer ces pièces.
Dans le domaine des turbines à gaz, vous avez des aubes, des aubes et des veines de stator qui sont tous de bons candidats pour l'additif, mais la quantité de supports que vous devez ajouter pour les imprimer avec succès fait de la FA pas un idéal Solution. Sinon, ces pièces seraient un très bon candidat pour l'impression 3D car elles sont assez difficiles à fabriquer avec d'autres méthodes.
Donc en repoussant les limites du design avec la possibilité d'imprimer jusqu'à 5 -10 degrés sans aucun support avec une bonne finition de surface, nous permettons de nombreuses applications différentes.
Comment positionnez-vous votre technologie aux côtés d'autres technologies d'impression 3D métal ?
Cela dépend de ce que vous faites. Il existe des applications qui connaissent désormais un certain succès dans la FA métal. Peut-être qu'il y aurait un avantage à utiliser VELO
3D
technologie sans support pour accélérer la production. Mais en fin de compte, il y a des gens qui impriment de très bonnes pièces sur d'autres systèmes.
Donc je pense qu'en termes d'additif, il y a définitivement de la place à la table pour beaucoup de joueurs différents. Lorsque vous comparez la taille de l'industrie de la fabrication additive avec la taille de l'industrie manufacturière traditionnelle, nous avons beaucoup de place pour nous développer avant qu'elle ne devienne un monde de chiens mangeurs de chiens.
Même si nous pensons que notre technologie peut remplacer une grande partie des technologies actuelles, cela ne veut pas dire qu'il n'y a pas de place pour d'autres.
Dans quels secteurs voyez-vous les plus grandes opportunités de croissance pour VELO 3D ?
Sans surprise, l'aérospatiale est une industrie clé car elle a été l'un des premiers à adopter l'impression 3D. Le raisonnement est assez clair :ils font de la fabrication à haute valeur ajoutée, ils ont des pièces qui sont chères à fabriquer et ont beaucoup de complexités géométriques afin qu'ils puissent bénéficier de la FA métallique.
Et l'industrie aérospatiale est vaste. Il y a la propulsion, que vous pouvez décomposer en turbines à gaz ou en applications non respirantes comme les moteurs de fusée, qui est une autre très bonne application. Ensuite, vous avez des aérostructures - des composants structurels réels - dans l'aviation et des structures satellitaires dans l'espace
Les applications sont également nombreuses du côté de l'électronique, notamment autour des boîtiers et des composants radiofréquences. Les échangeurs de chaleur sont un autre composant qui peut être difficile à fabriquer traditionnellement, selon la géométrie. Donc, dans l'aérospatiale, il y a beaucoup à chasser.
Ensuite, il existe une opportunité pour la FA métallique dans les applications industrielles, principalement parce qu'elle est quelque peu similaire à l'aérospatiale. Bien que de moindre valeur, les applications peuvent inclure des composants hydrauliques ou d'autres types de pièces de pompe, de collecteur et d'échangeur de chaleur.
Quels sont les principaux problèmes que vous constatez lorsque les clients vous contactent ?
Les plus grands défis se situent autour des géométries qui peuvent être imprimées.
Une autre grande chose que l'industrie doit aborder pour être plus largement acceptée est la variation de pièce à pièce. Si vous êtes un ingénieur qui conçoit des pièces pour la fabrication additive métallique et qu'il s'agit de composants critiques, vous devez considérablement réduire vos autorisations de conception pour pouvoir utiliser des additifs métalliques.
La raison en est est que la consistance du matériel qui sort du système n'est pas nécessairement ce que vous voulez qu'il soit. Vous devez concevoir pour la partie la plus faible que vous pourriez obtenir, ce qui signifie que vous n'exploitez pas pleinement certaines des capacités de la FA, en particulier en ce qui concerne l'allègement ou l'amélioration des performances. Vous devez avoir beaucoup de marges intégrées dans votre partie.
L'une des choses que nous essayons également d'aborder avec notre système, et avec de nombreuses capacités de métrologie intégrées, est la partie à la partie, le build-to-build et variation machine à machine, ainsi que les propriétés mécaniques de la pièce finale.
C'est quelque chose qui va ouvrir beaucoup de portes car il y a encore des hésitations à utiliser la FA métal, et les gens ne sont pas sûrs à 100% de ce qu'ils vont sortir à la fin du jour.
Quels conseils donneriez-vous aux entreprises souhaitant adopter la technologie de FA métal, mais ne sachant pas par où commencer ?
Il y a différentes motivations derrière l'adoption de la technologie AM. Certaines personnes ont une volonté d'entreprise d'adopter simplement la FA métal. Mais ce n'est pas nécessairement quelque chose qui conduit à des arguments convaincants pour l'additif métallique.
Je pense qu'il est vraiment important d'avoir une raison impérieuse d'avoir besoin d'additifs métalliques. Souvent, les entreprises diront :« Et si nous fabriquions exactement la même pièce avec un additif métallique ? Comment faisons-nous des comparaisons de coûts? Mettons-nous tout cela dans une matrice et trouvons-nous ce qui est le plus rentable ? » Cela ne profite pas nécessairement à toutes les offres d'additifs métalliques.
En fin de compte, la FA métallique est un autre outil dans la boîte à outils de fabrication. Vous devez avoir la douleur de faire la transition. Vous devez donc avoir une pièce que vous devez fabriquer, ou que vous avez des difficultés à fabriquer avec une autre technique de fabrication, ou vous avez besoin de plus de fonctionnalités du produit final qui vous obligent à concevoir de nouvelles fonctionnalités et de nouvelles géométries.
Comment décririez-vous l'état actuel de l'industrie de la FA et comment la voyez-vous évoluer au cours des cinq prochaines années ?
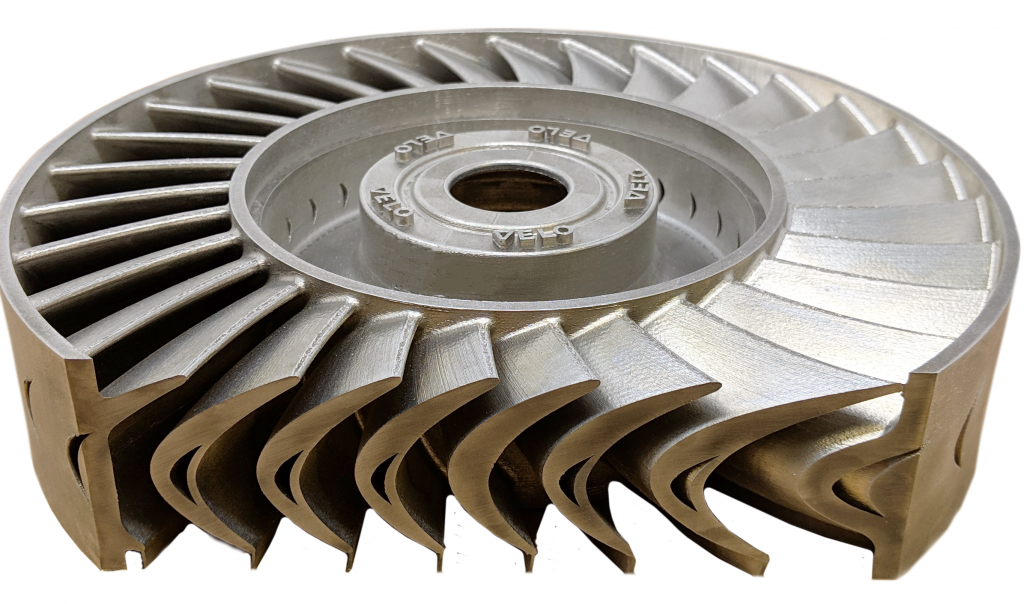
Metal AM arrive à maturité. Il existe des cas évidents d'entreprises qui se lancent avec succès dans la production. Nous atteignons un point d'inflexion et le nombre de pièces qui entrent réellement en production augmente.
Dans cinq ans, vous verrez de nombreux sous-traitants qui se sont considérablement développés et ont des centaines de ces systèmes dans leur usine, produisant des pièces avec des contrats de production à long terme. L'industrie y travaille depuis longtemps.
Les gens font confiance aux additifs métalliques comme solution. VELO
3D
's la technologie y jouera un grand rôle car notre objectif est d'accélérer la production et de donner confiance aux gens dans la qualité d'une pièce qui sort à la fin de l'impression.
Avec ces deux éléments combinés, vous pouvez commencer à attirer un certain nombre de candidatures supplémentaires qui peuvent être discutables aujourd'hui mais pourraient vraiment être de bons candidats pour AM.
Y a-t-il des tendances particulières qui vous passionnent ?
Nous voyons pas mal de tendances passionnantes.
Un domaine qui me passionne particulièrement est le marché spatial, en particulier autour des fusées et des petits satellites.
Il existe des innovations entreprises qui itèrent rapidement et ont des cycles de développement rapides. Ils recherchent des pièces finales de grande valeur bien alignées avec les capacités de VELO
3D
's Système saphir. C'est un marché qui est rapide à adopter et qui devrait croître de manière assez considérable.
L'autre avantage est que le marché a beaucoup de contiguïtés et alimente également le marché plus traditionnel de l'aérospatiale. Ces entreprises plus petites et plus rapides peuvent mettre au point certaines des choses au cours des cinq prochaines années qui attireront les principaux sous-traitants de la défense et les entreprises aérospatiales.
À quoi ressemble le développement des matériaux chez VELO 3D ? Prévoyez-vous d'élargir davantage votre portefeuille de matériaux ?
En ce moment, nous imprimons en Inconel 718 et Ti64. Nous essayons d'être axés sur le client, donc notre futur développement de matériel sera guidé par des analyses de rentabilisation solides.
Il existe de solides analyses de rentabilisation autour d'autres titanes et aluminium, mais pas nécessairement les mêmes matériaux que les offres communes d'autres fabricants de métaux AM. Nous voulons répondre aux besoins spécifiques des clients et être réactifs aux demandes du marché plutôt qu'à ce qui est nécessairement possible aujourd'hui.
VELO 3D s'est récemment associé à Praxair. Que signifie ce partenariat pour vous ?
Nous avons eu une très bonne relation avec Praxair Surface Technologies. C'est l'un de nos fournisseurs de poudre certifiés.
Nous essayons de nous assurer que nos clients ont accès à des matières premières de haute qualité et Praxair en est absolument un fournisseur. Avec eux, nous travaillons au développement de nouveaux alliages et veillons à ce que nos clients soient satisfaits des alliages qu'ils obtiennent de leurs fournisseurs.
Quelle a été la réaction de vos clients depuis votre lancement ?
C'est positif. J'ai vraiment l'impression que nos clients sont enthousiasmés lorsqu'ils voient toute l'étendue de ce que nous entreprenons ici, et comment nous avons entrepris de résoudre de nombreux problèmes qui existent avec les logiciels et le matériel autour de la FA métallique. . Cela montre qu'il s'agit d'une entreprise axée sur le client :comprendre les défis auxquels nos clients sont confrontés et développer des solutions pour améliorer leur vie.
En général, j'aime donner des visites ici à VELO
3D
, car la réponse est toujours aussi enthousiaste, et les gens semblent très enthousiastes à l'idée de commencer à utiliser la technologie et de l'intégrer en interne.
Enfin, à quoi ressemble 2019 pour VELO 3D ?
2019 va être une année vraiment excitante pour VELO
3D
. Nous commençons à nous lancer sur le marché et les gens prennent de plus en plus conscience de notre entreprise et de nos capacités. Nous le constatons à la fois dans la demande pour le système et pour les pièces imprimées sur le système et pour le système lui-même.
Pour nous, ce sera l'année de la technologie sans support, quand nous vraiment commencer à amener les gens à concevoir VELO
3D
dans leur produit final.
Pour en savoir plus sur Velo
3D
, visitez :www.velo3d.com
impression en 3D
- Poudres métalliques réfractaires VS Technologie d'impression 3D
- Entretien avec un expert :Dr Alvaro Goyanes de FabRx
- Considération de ce que signifie la nouvelle technologie d'impression sur métal pour la FA
- Entretien avec un expert :Dr Bastian Rapp de NeptunLab
- Stéréolithographie — la technologie d'impression 3D originale
- Entretien d'experts :Duncan McCallum, PDG de Digital Alloys, sur l'impression Joule et l'avenir de l'impression 3D sur métal
- Entretien d'experts :Guillaume de Calan, PDG de Nanoe, sur l'avenir de l'impression 3D céramique
- Entretien d'experts :John Kawola, président d'Ultimaker, sur l'avenir de l'impression 3D
- Entretien d'experts :Simon Fried, cofondateur de Nano Dimension, sur l'essor de l'impression 3D pour l'électronique