Nanofils de silicium amorphe cultivés sur film d'oxyde de silicium par recuit
Résumé
Dans cet article, des nanofils de silicium amorphe (α-SiNWs) ont été synthétisés sur un substrat de Si (100) avec un film d'oxyde de silicium par un mécanisme solide-liquide-solide (SLS) piloté par un catalyseur de Cu pendant le processus de recuit (1080 °C pendant 30 min sous Ar /H2 atmosphère). La fabrication de micro-modèles en Cu a décidé si les α-SiNW peuvent croître ou non. Pendant ce temps, ces modèles Cu de taille micro ont également contrôlé la position et la densité des fils. Pendant le processus de recuit, le motif Cu a réagi avec SiO2 pour former du siliciure de Cu. Plus important encore, un canal de diffusion a été ouvert pour que les atomes de Si synthétisent des α-SiNW. De plus, la taille des α-SiNWs était simplement contrôlée par le temps de recuit. La longueur du fil a été augmentée avec le temps de recuit. Cependant, le diamètre a montré la tendance inverse. La résistivité à température ambiante du nanofil était d'environ 2,1 × 10 3 Ω·cm (84 nm de diamètre et 21 μm de longueur). Cette méthode de fabrication simple rend possible l'application des -SiNW.
Contexte
Parmi les différentes classes de nanostructures semi-conductrices unidimensionnelles, les nanofils de silicium (SiNW) ont été exposés à un brillant avenir dans les domaines de l'électronique, du solaire photovoltaïque, de la photonique, des batteries et des capteurs. [1,2,3,4,5,6] La méthode de fabrication SiNW comprend des approches descendantes et ascendantes. Le tableau 1 est le résumé des différentes méthodes de fabrication de SiNW. L'approche descendante est généralement réalisée par gravure ionique réactive (RIE) et gravure autocatalytique catalysée par un métal du silicium. Dans ces méthodes, le site du nanofil est contrôlé dans une approche descendante par des outils de nanofabrication tels que la lithographie par faisceau électronique, [7] la lithographie par nanoimpression [8], ou un modèle nanométrique tel que la sphère PS, [9] AAO mask [10]. Les outils de nanofabrication contrôlent bien le site, la taille, l'orientation et le nombre de fils avec un processus de fabrication complexe et coûteux. Le modèle nanométrique [9,10,11] est la méthode à faible coût, mais le processus de fabrication est plus complexe que la méthode de l'outil de nanofabrication pour le modèle qui doit être construit et retiré pendant tout le processus. Par conséquent, la méthode sans modèle montre un bon potentiel à l'avenir [12]. Une autre approche descendante utilise la technique MEMS pour fabriquer des SiNW contrôlables sur site [13], ce processus de fabrication permet de fabriquer facilement des dispositifs de capteur SiNW. Cependant, la technique MEMS apporte un processus de fabrication complexe avec un coût élevé.
Dans l'approche ascendante, le dépôt chimique en phase vapeur (CVD) est une approche importante pour la synthèse des SiNW avec un processus de fabrication simple et peu coûteux. Et cette approche peut facilement produire des SiNW de très petit diamètre et très longs (comme enregistré, le plus petit diamètre était de 1 nm et le plus long de millimètres) [14,15,16]. Les SiNW de bonne qualité sont toujours synthétisés par le mécanisme vapeur-liquide-solide (VLS) à l'aide d'Au ou d'autres métaux dans cette méthode [2]. Cependant, ces nouveaux matériaux sont interdits dans les salles blanches pour dégrader les propriétés électriques et optiques des semi-conducteurs.
Une méthode sans catalyseur est proposée pour résoudre le problème de pollution provoqué par de nouveaux catalyseurs dans une approche ascendante. La méthode de croissance assistée par oxyde (OAG) ne nécessite aucun catalyseur métallique [17]. Malheureusement, la compatibilité avec la technologie d'intégration basée sur Si est médiocre dans cette méthode. Et les produits sont toujours facilement affectés par d'autres impuretés résiduelles [18]. L'ablation laser à onde continue à température ambiante de Si est une autre façon de synthétiser des SiNW sans utiliser de catalyseur métallique [19]. Néanmoins, un vide poussé est nécessaire. Même dans la simple technique d'évaporation du SiO, une bonne contrôlabilité de la taille est toujours difficile à réaliser. De plus, la poudre de SiO est nocive pour la santé [20].
De nouveaux catalyseurs tels que l'aluminium et le cuivre sont recherchés pour ouvrir la porte de la technologie des semi-conducteurs à oxyde métallique complémentaire (CMOS) aux SiNW [21]. L'aluminium est utilisé pour réduire les impuretés profondes; il peut également s'agir d'un dopant de type p produisant un accepteur peu profond en Si. Cependant, la grande sensibilité à l'oxydation rend l'utilisation de l'aluminium comme méthode de catalyseur peu pratique. Le cuivre est un bon conducteur de chaleur et d'électricité et a été largement utilisé dans les circuits intégrés (CI) et le traitement CMOS. Ainsi, le cuivre est considéré comme le catalyseur approprié pour la croissance du SiNW. La taille et l'emplacement des fils de Si étaient bien contrôlés par le catalyseur au cuivre dans Kayes et al. travail [22]. Dans les travaux où le cuivre a été utilisé comme catalyseur pour synthétiser les SiNW, SiH4 , Si2 H6 , ou SiCl4 les gaz ont été utilisés comme précurseur de Si [22,23,24].
Dans cet article, nous présentons une méthode simple et efficace pour synthétiser des SiNW sur SiO2 films par le mécanisme SLS entraîné par un catalyseur de Cu pendant le processus de recuit sans utiliser de gaz précurseurs toxiques. Cette méthode présente deux avantages. Premièrement, la contamination métallique des SiNWs a été diminuée. Deuxièmement, aucun gaz précurseur toxique n'a été utilisé.
Méthodes
Fabrication de puces
Tout d'abord, 300 nm de SiO2 Le film a été développé sur des plaquettes de silicium de type n polies sur une seule face (100) par oxydation thermique (Fig. 1a). Ensuite, un film de cuivre de 400 nm a été déposé sur SiO2 par pulvérisation cathodique magnétron. Après un processus de photolithographie et une solution de persulfate d'ammonium (1:100 d'eau), des matrices de motifs en Cu ont été fabriquées sur SiO2 surface dans la zone cible (Fig. 1b). Par la suite, la plaquette a été découpée en puces. Et ces puces ont été nettoyées par ultrasons à l'éthanol et à l'acétone pendant 10 min. Ensuite, de l'eau DI a été utilisée pour le dernier processus de nettoyage avant le séchage par N2 .
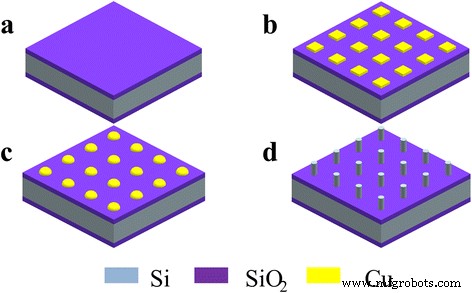
Représentation schématique du processus de fabrication. un Oxydation thermique. b Fabrication de matrices de motifs de taille micron Cu. c Les motifs de cuivre se sont transformés en hémisphères. d Croissance des nanofils
Croissance α-SiNW
Un millier de centimètres cubes standard par minute d'Ar a été utilisé pour exclure l'air dans le tube pendant 10 minutes après que les copeaux aient été placés sur une nacelle en quartz et transférés au centre du four horizontal.
Par la suite, cinq étapes ont été utilisées pour synthétiser les SiNW. Les conditions détaillées du traitement de recuit sont indiquées sur la figure 2. Dans l'étape I, la température a été augmentée de la température ambiante à 400 °C en 1 h avec le même flux d'Ar qui est utilisé pour exclure l'air. Au stade II, le débit d'Ar a été ajusté à 100 sccm et 20 sccm H2 était ajouté. Il a fallu 2 h pour atteindre 1080 °C. À ce stade, les motifs de cuivre se sont transformés en hémisphères (Fig. 1c). Ensuite, la température a été maintenue pendant 30 min avec 1000 sccm Ar et 40 sccm H2 au stade III. Après avoir éteint le four, le processus de refroidissement rapide de seulement 10 min a été considéré comme l'étape IV et le débit a été ajusté à 500 et 20 sccm respectivement. Dans la dernière étape, un refroidissement lent utilisé pour réduire la température du four à la température ambiante avec 100 sccm Ar et 20 sccm H2 . Après les cinq étapes, les -SiNW ont été cultivés sur la position des motifs de Cu, comme le montre la figure 1d.
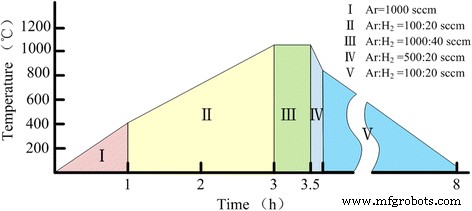
Conditions de traitement thermique pour la synthèse de SiNW à l'aide d'un four horizontal. Au stade I, la température a été augmentée de la température ambiante à 400 °C en 1 h avec le même flux d'Ar qui excluait l'air. Au stade II, le débit d'Ar a été ajusté à 100 sccm et 20 sccm H2 était ajouté. Il a fallu 2 h pour atteindre 1080 °C. À ce stade, les motifs de cuivre se sont transformés en hémisphères. Ensuite, la température a été maintenue pendant 30 min avec 1000 sccm Ar et 40 sccm H2 au stade III. Après avoir éteint le four, le processus de refroidissement rapide n'a pris que 10 minutes comme étape IV et le débit a été ajusté à 500 et 20 sccm respectivement. Dans la dernière étape, un refroidissement lent utilisé pour réduire la température du four à la température ambiante avec 100 sccm Ar et 20 sccm H2
Caractérisation
La microscopie électronique à balayage (SEM, Hitachi S-4800) et la microscopie électronique à transmission haute résolution (TEM, JEM-2100F fonctionnant à 200 Kv) équipées d'un spectromètre à dispersion d'énergie (EDS) ont été utilisées pour analyser la morphologie et la composition des nanofils. Pour les mesures TEM, la grille Mo a été utilisée pour supporter les nanofils. Pour la gravure FIB de la racine du fil, une fine couche d'Au a été évaporée en surface pour protéger le fil par dépôt induit par faisceau d'électrons (EBID). Un dispositif à deux bornes a été utilisé pour mesurer la résistivité du nanofil [25]. Le fil a été retiré mécaniquement du substrat par un nano-opérateur équipé d'un faisceau d'ions focalisé (FIB) (FEI, QUANTA3D 600FIB System). Ensuite, le nanofil a été soudé sur les deux électrodes par du Pt déposé par faisceau d'électrons assisté. Enfin, la résistivité du nanofil a été mesurée par la station de sonde Cascade Semi-automatique HP 4156.
Résultats et discussion
La figure 3 présente les photos SEM de deux échantillons avant et après le recuit (échantillon I, le film de Cu épais est de 400 nm, l'échantillon II est les matrices de motifs Cu avec une taille de 400 nm d'épaisseur et 1,9 m de diamètre, et un pas de centre à centre est de 10 μm). Il est évident que les résultats des deux échantillons étaient assez différents après recuit à 1080 °C pendant 30 min. Pour le film de Cu, illustré à la Fig. 3b, seules des billes de Cu ont été dispersées au hasard sur la surface de SiO2 . La figure insérée dans la figure 3b était les distributions de diamètre des billes de Cu, et le diamètre moyen de la bille était de 4,4 μm. Le nanofil en combinaison est apparu dans l'échantillon II après recuit sur la figure 3d. La longueur du nanofil peut atteindre 20 μm et le diamètre du nanofil est d'environ 57 nm, comme le montre l'image insérée de la figure 3d. Il est clair que chaque motif a fait croître un nanofil et la distance centre à centre est égale à la valeur des motifs Cu. Cela signifie que la densité des nanofils peut être contrôlée simplement par le nombre de motifs Cu. Le phénomène de la figure 3 démontre que la taille micro des motifs de Cu est adaptée à la croissance de nanofils (dans notre cas, la taille du motif de Cu était de 400 nm d'épaisseur et de 1,9 μm de diamètre). Pour le film Cu, l'effet de démouillage s'est produit à haute température. Afin de réduire l'énergie de surface du film de Cu, des billes de Cu ont été agrégées de manière aléatoire (fig. 3b).
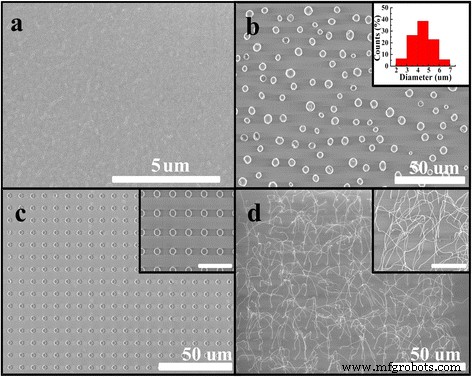
Images SEM pour les deux échantillons sur 300 nm SiO2 surface avant et après 30 min recuit en Ar/H2 atmosphère à une température de 1080 °C. un Image SEM pré-recuite de l'échantillon I avec un nanofilm de Cu (400 nm d'épaisseur). b Images SEM de l'échantillon I avec un film de Cu après recuit. Photo en médaillon était la distribution de diamètre des particules de Cu après SEM. c Image SEM pré-recuite de l'échantillon II avec matrice de motifs Cu (taille du motif Cu, épaisseur 400 nm et diamètre 1,9 μm). Photo en médaillon était l'image agrandie du tableau de motifs Cu. d Image SEM de la croissance des nanofils sur l'échantillon II après recuit. Photo en médaillon était l'image agrandie des nanofils. Les barres d'échelle dans les encarts sont de 10 μm
L'image de microscopie électronique à transmission (MET) à haute résolution de la figure 4a révèle que le nanofil a une morphologie lisse à un diamètre de 50 nm dans l'échantillon II. Le motif annulaire hautement diffusif (en médaillon) de la zone sélectionnée de diffraction électronique (SAED) démontre que le nanofil était totalement amorphe (sur la figure 4). Les résultats du spectromètre à dispersion d'énergie (EDS) de la figure 4 indiquent que le fil est constitué de Si et d'O avec un rapport atomique de 4, ce qui est loin du rapport du dioxyde de Si et suggère qu'une trace d'oxygène existe dans les SiNW. Pour l'atmosphère de réduction qui était composée d'Ar et H2 est maintenue pendant le processus de croissance des nanofils, de sorte que l'oxydation légère ne s'est produite que pendant l'exposition de l'échantillon à l'air après la fabrication.
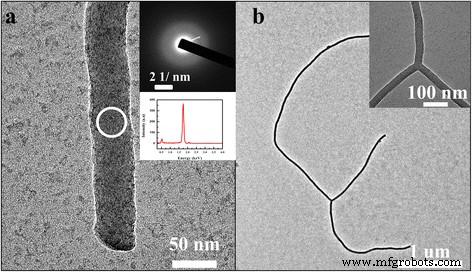
Images MET de nanofils. un Image MET de la pointe du nanofil. Photos en médaillon étaient respectivement la diffraction électronique à zone sélectionnée (SAED) du nanofil et le spectre EDS. Le motif SAED a été obtenu à partir du milieu du fil (cercle blanc ) sur la figure 4, et l'ouverture pour SAED était de 200 nm. b Image MET d'un nanofil. L'image insérée était la photo détaillée du nanofil sur la figure 4b
Après la gravure FIB de la partie racine du fil et du substrat, la section transversale de la racine du fil a été caractérisée par SEM avec un porte-échantillon tourné à 45°. Il est intéressant de constater que le nanofil s'est développé à partir de la frontière entre Si et SiO2 dans la Fig. 5. Un long gap Si se trouve également au niveau du Si /SiO2 interface. Ces observations démontrent que le substrat était la seule source de Si pour le fil. Pendant ce temps, aucune particule métallique n'est trouvée à la pointe du fil. D'après ces résultats, une illustration schématique possible de la croissance de α-SiNW est présentée sur la figure 6 sur la base d'un mécanisme solide-liquide-solide. Au cours du processus de recuit, les motifs Cu (Fig. 6a) mouillent jusqu'au centre du motif (Fig. 6b) et réagissent avec SiO2 pour former du siliciure de Cu (Fig. 6c). Ensuite, les atomes de Si pénètrent dans le siliciure de Cu. Au cours de ce processus, la vitesse de diffusion différente des atomes de Si dans le substrat, causée par le défaut du substrat, peut induire la formation d'un trou de Si. Lorsque les atomes de Si en dissolution dans le siliciure ont atteint la saturation, le Si commence à précipiter pour synthétiser des α-SiNW (Fig. 6d).
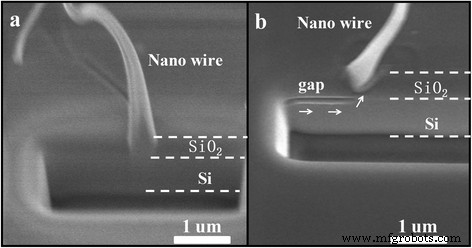
Images SEM de la racine α-SiNW. un , b Les images SEM de la partie radiculaire α-SiNW à une inclinaison de 45° après gravure FIB. Un long gap Si se trouve au niveau du Si /SiO2 interface dans (b )
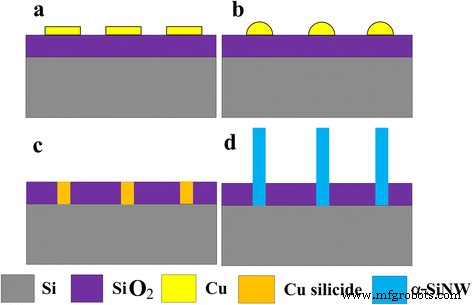
Illustration schématique de la croissance de α-SiNW. Pendant le processus de recuit, les motifs Cu (a ) mouiller au centre du motif (b ), et réagir avec SiO2 pour former du siliciure de Cu (c ). Ensuite, les atomes de Si pénètrent dans le siliciure de Cu. Au cours de ce processus, la vitesse de diffusion différente des atomes de Si dans le substrat, causée par le défaut du substrat, peut induire la formation d'un trou de Si. Lorsque les atomes de Si en dissolution dans le siliciure ont atteint la saturation, Si commence à précipiter pour synthétiser des α-SiNWs (d )
Il est clair que Cu a joué un rôle très important dans notre étude. Quelque chose comme une particule noire peut être trouvée à l'extrémité du fil, bien que dans la plupart des fils, cette particule n'existe pas. Les résultats de la cartographie (Fig. 7) montrent qu'aucune particule métallique n'existe à l'extrémité du fil. La particule semble être le malentendu par l'angle entre le fil et le support, qu'il ne convenait pas d'observer. Malheureusement, on ne trouve pas de cuivre à la racine du fil (Fig. 5). Cu diffusé dans des substrats de Si est la voie possible qui peut donner lieu à ce résultat surprenant. Il est bien connu que la diffusion rapide des atomes de Cu dans Si a été testée à haute température [26]. Ainsi, les atomes de Cu pourraient diffuser dans le substrat Si en quelques minutes après la fenêtre en SiO2 a été ouvert à haute température.
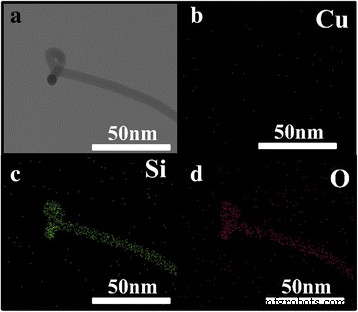
Images cartographiques TEM et EDS de la pointe du nanofil. un montre l'image TEM de la pointe du fil qui ressemble à une particule de métal, b –d localisation des différents éléments illustrés par cartographie EDS avec variation de contraste lumineux :cuivre (b ), silicium (c ) et l'oxygène (d )
Pour démontrer la contrôlabilité de notre méthode, différents temps de recuit sont effectués dans nos expériences. Le SEM de nanofils synthétisés dans différents temps de recuit avec la même taille de motif Cu (400 nm d'épaisseur et 1,9 um de diamètre) et le même SiO2 L'épaisseur (300 nm) est illustrée à la figure 8. La plupart des nanofils ont un diamètre uniforme. Il est intéressant de constater que le diamètre diminue lorsque la direction du fil change. Comme le montre la flèche rouge sur la figure 8c, le diamètre de la pointe est de 76 nm et la partie de la racine n'est que de 49 nm. Cette énorme différence de diamètre dans le même fil peut être causée par la variation de l'énergie par unité de surface pour le noyau [27]. Et ce phénomène est rarement visible. Une autre découverte intéressante est que le diamètre de la partie racine était la partie la plus grande de l'ensemble du fil et la partie pointe était plus petite (flèches rouges montrées en d–f). En comparaison avec l'ensemble du fil, la longueur de la partie non uniforme est très courte. Ce résultat montre que a-SiNW avait un diamètre non uniforme.
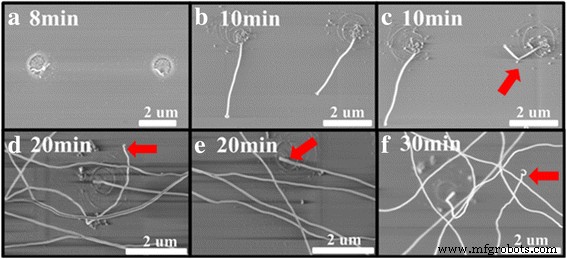
un –f Les images SEM de α-SiNW cultivées dans différents temps de recuit
Après SEM, la longueur et le diamètre de la partie racine des α-SiNW sont calculés. Les résultats de la figure 9 montrent que la longueur de α-SiNW a augmenté avec le temps de recuit, en fonction du temps de recuit. Le temps de diffusion des atomes de Si est augmenté offrant plus d'atomes pour synthétiser des nanofils. La longueur de α-SiNW augmente jusqu'à 24 μm tandis que le temps de recuit augmente jusqu'à 30 min. Le taux de croissance moyen des nanofils est d'environ 1,1 μm/min, ce qui était similaire au taux de croissance par recuit avec une source de Si bloc [28]. La vitesse de croissance rapide ne laisse pas le temps aux atomes de Si de s'empiler dans un ordre cristallin. Enfin, des nanofils amorphes au lieu de cristallins sont synthétisés.
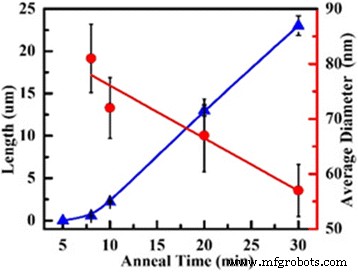
Le diamètre et la longueur du nanofil en fonction du temps de recuit. Triangles bleus et cercles rouges dans la figure sont la date pour la longueur et le diamètre du nanofil dans l'expérience, et bleu et lignes rouges dans la figure étaient la ligne d'ajustement selon les dates d'expérience
Le diamètre du α-SiNW est réduit de 81 à 57 nm dans le processus d'augmentation du temps de recuit. Habituellement, la longueur des SiNW dépend de leur diamètre pour l'effet Gibbs-Thomson dans la croissance vapeur-liquide-solide utilisant le silane comme source gazeuse et l'or comme catalyseur. La longueur de SiNW augmente lorsque le diamètre augmente pour les nanofils d'un diamètre inférieur à 100 nm. Néanmoins, le résultat de notre expérience montre la conclusion inverse que le diamètre diminue avec la longueur. Le recuit de longue durée donne plus de temps aux atomes de Cu diffusés dans le substrat de Si, et le volume de catalyseur de siliciure est également diminué. Pendant ce temps, le processus de diffusion des atomes de Si se poursuit, ce qui entraîne une croissance constante du α-SiNW avec le changement de la taille des particules du catalyseur. Par conséquent, le diamètre du α-SiNW diminue avec le temps de recuit.
La figure 10 montre le courant (I ) en fonction de la tension (V ) courbe d'ajustement avec un comportement quasi ohmique. I–V la mesure montre la résistivité à température ambiante ; le nanofil de la figure 3 est de 2,15 × 10 3 Ω·cm, mesuré par la méthode à deux sondes. En comparaison avec les travaux de M. Lieber [29], la résistivité du α-SiNW dans ce travail est dix fois supérieure à celle des fils de silicium monocristallin sans dopage. La conductivité électrique significativement plus élevée des nanofils est probablement due à l'effet de taille.
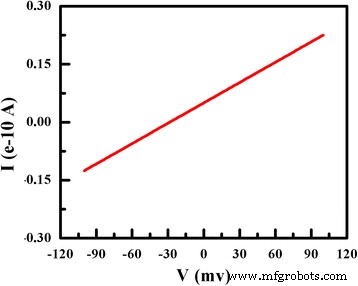
La mesure du transport électrique du α-SiNW sur la figure 3. Un dispositif à deux bornes a été utilisé pour mesurer la résistivité du nanofil [25]. Le fil a été retiré mécaniquement du substrat par un nano-opérateur équipé d'un faisceau d'ions focalisé (FIB) (FEI, QUANTA3D 600FIB System). Ensuite, le nanofil a été soudé sur les deux électrodes par du Pt déposé par faisceau d'électrons assisté. La résistivité du nanofil a été mesurée par la station de sonde semi-automatique Cascade HP 4156. Enfin, la résistivité à température ambiante du nanofil de la figure 3 est de 2,15 × 10 3 Ω·cm, mesuré par la méthode à deux sondes
Conclusions
En conclusion, les α-SiNW sont cultivés directement sur SiO2 surface pendant le processus de recuit dans Ar/H2 l'atmosphère via le mécanisme SLS sans aucun gaz précurseur toxique. La fabrication de motifs en Cu est la condition nécessaire à la croissance de α-SiNW. Pendant ce temps, les motifs Cu sont utilisés pour contrôler la densité et le site des -SiNW. De plus, le temps de recuit est un paramètre réglable pour contrôler le diamètre et la longueur du fil α-SiNWs. La résistivité à température ambiante du nanofil est de 2,15 × 10 3 ·cm. Cette nouvelle méthode de croissance fait du α-SiNW un candidat pour des applications potentielles à l'avenir.
Nanomatériaux
- Materials Part 1 :Que peut faire le recuit pour votre processus
- Décryptage de l'évolution morphologique et de la cinétique de gravure de nanofils de silicium poreux lors d'une gravure chimique assistée par métal
- Réalisation d'une couverture complète d'un film pérovskite stable par un processus anti-solvant modifié
- Caractéristiques optiques et électriques des nanofils de silicium préparés par gravure autocatalytique
- Film WS2 de grande surface avec de grands domaines uniques cultivés par dépôt chimique en phase vapeur
- Contrôle de la croissance des nanofils de séléniure d'indium à haute uniformité (In2Se3) via le processus de recuit thermique rapide à basse température
- Qu'est-ce que le recuit ? - Définition, processus et étapes
- 4 méthodes de processus courantes de galvanoplastie partielle
- Comprendre la mise en solution, le recuit, la nitruration