Décryptage de l'évolution morphologique et de la cinétique de gravure de nanofils de silicium poreux lors d'une gravure chimique assistée par métal
Résumé
De nombreuses applications potentielles des nanofils de silicium poreux (SiNW) fabriqués avec une gravure chimique assistée par métal dépendent fortement du contrôle précis de la morphologie pour l'optimisation du dispositif. Cependant, les effets des principaux paramètres de gravure, tels que la quantité de catalyseur métallique déposé, le rapport molaire HF-oxydant (χ ), et la concentration de solvant, sur la morphologie et la cinétique de gravure des SiNWs n'ont pas encore été complètement explorées. Ici, les changements dans la nanostructure et la vitesse de gravure du silicium de type p dégénéré dopé dans un HF-H2 O2 –H2 Les systèmes de gravure O avec catalyseur à l'argent déposé sans courant sont systématiquement étudiés. La morphologie de la surface évolue d'une structure microporeuse et cratérisée à un réseau uniforme de SiNW à χ suffisamment élevé valeurs. Les taux de gravure à la base et à la pointe de la nanostructure sont corrélés avec la gravure primaire induite par Ag et la gravure secondaire induite par les ions métalliques et les trous diffusés, respectivement. Le H2 La concentration en O affecte également le χ fenêtre où se forment les SiNW et les vitesses de gravure, principalement en modulant la dilution des réactifs et la vitesse de diffusion. En contrôlant la gravure secondaire et la diffusion des réactifs via χ et H2 La concentration en O, respectivement, la fabrication de SiNW hautement dopés avec un contrôle indépendant de la porosité à partir de la longueur est démontrée avec succès, ce qui peut être potentiellement utilisé pour améliorer les performances des dispositifs à base de SiNW.
Contexte
Malgré les avancées de la recherche sur divers nouveaux matériaux, le silicium reste l'un des substrats les plus attrayants pour la fabrication de nanostructures en raison de son abondance dans la nature et de l'existence de techniques bien développées pour l'intégration de dispositifs. Ces dernières années, les nanostructures de silicium unidimensionnelles, telles que les nanofils de silicium (SiNWs) et les nanopiliers, ont continué à attirer l'attention dans un large éventail d'applications, telles que le photovoltaïque [1, 2], la thermoélectrique [3, 4], le stockage d'énergie [5,6,7], électronique flexible [8], détection biochimique [9] et interfaçage biologique [10]. Outre les propriétés électriques, optiques, thermiques et mécaniques uniques de ces nanostructures, le développement de nouvelles techniques de fabrication qui permettent une formation facile des nanostructures tout en maintenant un excellent contrôle sur la morphologie et les propriétés physiques est l'un des principaux facteurs de leur attrait durable. Parmi les différentes techniques de fabrication, la gravure chimique assistée par métal (MACE) se distingue d'un point de vue industriel par sa simplicité, son faible coût et sa flexibilité [11, 12]. En utilisant MACE, des SiNW sans défaut à l'échelle d'une plaquette avec une longueur, une porosité, une conductivité, un niveau de dopage et une orientation cristalline définis peuvent être obtenus en sélectionnant simplement la plaquette de Si, la composition de gravure, la température de réaction et le temps de réaction [13,14, 15,16,17,18,19,20,21,22,23]. Le contrôle du diamètre, de la section transversale et du pas du réseau SiNW peut également être obtenu grâce à des techniques de modélisation de catalyseur, telles que la lithographie à nanosphères [24], la lithographie par interférence [25] et la lithographie à blocs de copolymères [26]. Cela contraste avec d'autres techniques de fabrication, telles que la gravure ionique réactive et les méthodes vapeur-liquide-solide, qui nécessitent un équipement coûteux et peuvent produire des nanofils avec des défauts de surface, des orientations cristallographiques incontrôlées et des formes de section transversale limitées [11].
Au cours de la dernière décennie, la fabrication de SiNW à partir de plaquettes de Si hautement dopées à l'aide de MACE a suscité un intérêt particulier en raison des SiNW poreux résultants de haute qualité cristalline [14, 17, 19]. La structure poreuse permet aux nanofils d'acquérir des propriétés hautement souhaitables, telles que la photoluminescence accordable [15], une faible conductivité thermique [27] et une surface spécifique élevée [28], ce qui en fait des matériaux prometteurs pour l'optoélectronique [14, 16], la thermoélectrique [ 3, 27], la photocatalyse [28, 29] et le stockage d'énergie [5]. En combinaison avec leur photoluminescence et leur surface spécifique élevée, la biocompatibilité et la biodégradabilité des SiNW poreux dans des environnements physiologiques en font également des candidats appropriés pour le bioétiquetage [15] et les applications d'administration de médicaments [30]. Bien que des SiNW relativement poreux puissent être obtenus avec des plaquettes de Si faiblement dopées en utilisant des concentrations élevées d'oxydant dans le décapant [15], l'utilisation de Si hautement dopé est avantageuse lorsqu'une conductivité électrique élevée est nécessaire car elle évite le besoin d'un dopage post-gravure. étape. Cela est particulièrement vrai dans les applications thermoélectriques des SiNW poreux où l'augmentation de la figure de mérite est due à la diminution de la conductivité thermique sans dégradation significative de la conductivité électrique [27]. D'un autre côté, il a été rapporté que la résistance des SiNW poreux est plutôt grande par rapport à celle des SiNW solides [14], ce qui implique un compromis entre le degré de porosité et la conductivité électrique.
Afin de réaliser le potentiel des SiNW poreux dans les applications mentionnées ci-dessus, il est impératif de bien comprendre les effets de divers paramètres de gravure au cours du MACE de Si fortement dopé. Un certain nombre d'études [13,14,15,16,17, 19,20,21, 23] ont réussi à fabriquer des SiNW hautement dopés avec différentes longueurs et porosités en utilisant MACE en HF–H2 O2 graver. Leurs enquêtes ont mis en lumière l'effet de H2 O2 concentration [14,15,16,17, 20, 21, 23], concentration HF [21], HF–H2 O2 rapport volumique [19], durée de gravure [14, 16, 17, 19,20,21, 23] et température de gravure [19,20,21, 23] sur la porosité [14, 16, 17, 19, 20] , la longueur [16, 17, 19, 20, 21, 23], le taux de gravure [15] et la morphologie globale [15, 16, 21] des tableaux SiNW. Néanmoins, des études systématiques sur l'effet du mordançage HF–H2 O2 rapport molaire, défini comme χ = [HF]/([HF] + [H2 O2 ]), et H2 Les concentrations en O sur la formation de nanostructures de Si fortement dopées sont limitées. Ceci malgré le fait que χ est un paramètre clé pour déterminer la morphologie et la vitesse de gravure des nanostructures de Si [18, 31], tandis que [H2 O] est essentiel dans la formation de SiNW dans les zones à micro-motifs [18]. À ce jour, seuls Chiappini et al. [15] et Balasundaram et al. [19] ont utilisé un large éventail de χ valeurs (0,4-0,98 et 0,7-0,99, respectivement) dans la fabrication de SiNW hautement dopés, alors qu'aucun n'a pleinement exploré l'effet de l'attaque [H2 O]. De plus, malgré un certain nombre d'études élucidant le mécanisme de l'évolution morphologique, de la porosification et de l'effilage des SiNW légèrement et fortement dopés fabriqués avec du MACE [15, 17, 32], le mécanisme de l'évolution de la longueur en raison des effets concurrents du métal déposé la gravure, la gravure de métal renucléé, la diffusion de trous et la diffusion de réactifs n'ont pas été complètement étudiées. Dans cette étude, MACE [33] en deux étapes sur des plaquettes de Si de type p dégénérées en utilisant un catalyseur Ag déposé sans courant et H2 O2 oxydant a été effectué. Par rapport au MACE utilisant un catalyseur Au à motifs, le dépôt autocatalytique ne peut former que des SiNW distribués de manière aléatoire avec des diamètres variés [13], tandis que Ag peut limiter les rapports d'aspect SiNW réalisables en raison de sa dissolution plus rapide que l'Au [11]. Néanmoins, l'utilisation d'un dépôt autocatalytique et d'un catalyseur Ag dans MACE est considérée comme le moyen le plus simple et le moins cher de former des nanostructures de Si, y compris les SiNW. Afin d'explorer les effets de la composition de l'agent de gravure sur les nanostructures et les taux de gravure résultants, des agents de gravure avec une gamme relativement large de χ et [H2 Les valeurs O] ont été utilisées. En déterminant la cinétique de gravure à la pointe et à la base des nanostructures de Si, un aperçu des effets de l'injection de trous et des taux de dissolution du Si, de la gravure secondaire induite par les ions métalliques dissous et les trous diffusés, et le taux de diffusion des réactifs sur la morphologie et la longueur résultantes de les nanostructures sont fournies. Des SiNW hautement dopés de même longueur ont également été fabriqués à l'aide d'agents de gravure composés de différents χ et [H2 O], montrant ainsi que la porosité peut être ajustée efficacement par la composition de l'agent de gravure malgré des durées de gravure variables.
Méthodes
Des plaquettes de Si (100) de type p polies et dopées au bore avec une résistivité de 0,001 à 0,005 Ω cm et une couche d'oxyde thermique de 50 nm sur la face polie ont été utilisées comme matériau de départ. Les plaquettes ont été soigneusement nettoyées avec de l'eau déminéralisée (DI), de l'acétone et de l'éthanol, et l'oxyde thermique a été éliminé avec du HF dilué, ce qui a donné des surfaces de Si à terminaison H. Pour limiter la gravure sur la surface de Si polie, la face arrière des plaquettes de Si a été recouverte de résine photosensible (AZ5214). Les échantillons de Si pour les expériences MACE ont été obtenus en clivant les plaquettes en 1 × 1 cm 2 pièces. Des échantillons de Si provenant de la même plaquette ont été utilisés pour chaque série d'expériences.
MACE a été réalisée à l'aide d'un processus de gravure en deux étapes consistant en un dépôt autocatalytique de catalyseur Ag, puis une gravure dans HF–H2 O2 solutions, comme le montre schématiquement la figure 1. Les morceaux de Si ont d'abord été immergés dans 5 % de HF pendant 3 min. Le dépôt autocatalytique de nanoparticules d'Ag (AgNPs) sur le substrat de Si a ensuite été effectué dans une solution aqueuse contenant 4,8 M de HF et 0,005 M d'AgNO3 pour des durées différentes (Fig. 1a). Après un rinçage doux avec de l'eau déminéralisée, les échantillons de Si revêtus d'AgNP ont été gravés dans du HF-H2 aqueux O2 solutions avec différents χ et [H2 O] (voir Fichier complémentaire 1 :Tableau S1) pour différentes durées (Fig. 1b). Les échantillons de Si gravés ont été soigneusement rincés avec de l'eau DI puis immergés dans 1:1 (v /v ) HNO3 pendant 10 min pour dissoudre les AgNPs. Après un autre rinçage approfondi à l'eau DI, les échantillons de Si ont été trempés dans du HF à 5 % pendant 3 min pour éliminer toute couche d'oxyde formée, puis rincés à nouveau avec de l'eau DI plusieurs fois. Dépôt d'Ag et HF–H2 O2 la gravure a été effectuée dans l'obscurité. Tous les échantillons ont été traités à température ambiante (22-23 °C) dans des béchers en plastique séparés contenant 15 ml de la solution requise.
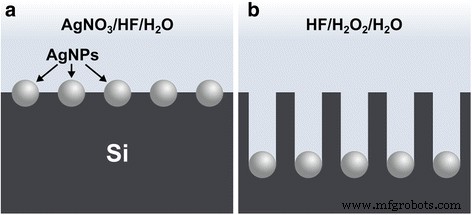
Vue schématique en coupe transversale de la fabrication de nanostructures de Si à l'aide de MACE en deux étapes. un Dans la première étape, les AgNPs sont déposés sans courant sur la surface de Si dans une solution aqueuse contenant AgNO3 et HF. b Dans la deuxième étape, les AgNPs catalysent la gravure du substrat Si dans une solution composée de HF, H2 O2 , et H2 O, conduisant à la formation de nanostructures de Si
Les surfaces de Si gravées ont été caractérisées par microscopie électronique à balayage (SEM, Phenom Pro ou FEI/Philips XL-30) et microscopie électronique à transmission (TEM, Philips CM20). Pour préparer les échantillons pour l'observation SEM, la résine photosensible à l'arrière a été retirée par de l'acétone. Les échantillons de Si ont ensuite été rincés à l'éthanol et séchés sur une plaque chauffante pour minimiser l'agglomération de SiNW due à l'évaporation de l'eau [19].
Résultats et discussion
Dépôt de catalyseur d'argent et formation de SiNW poreux
L'effet de la durée du dépôt d'Ag (10 s à 15 min) dans une solution de 0,005 M AgNO3 et 4,8 M de HF sur la formation de SiNW hautement dopés ont été étudiés. Lorsque les échantillons chargés en Ag ont été gravés dans une solution contenant 4,8 M H2 O et χ =0,95 pendant 30 min, des temps de dépôt courts (≤2 min) ont donné lieu à un réseau dense de pores verticaux avec quelques piqûres latérales, comme le montre la figure 2a. Cependant, les pores n'étaient pas assez denses pour former des structures de nanofils bien séparées si le temps de dépôt est ≤ 1 min. D'autre part, des SiNW qui ne présentaient presque aucun défaut ont été obtenus avec un temps de dépôt d'Ag de 4 min (Fig. 2b), avec des temps de dépôt plus élevés résultant en des SiNW sans piqûres. Outre les changements dans la morphologie du SiNW, une variation non monotone de la vitesse de gravure du SiNW par rapport au temps de dépôt d'Ag a également été observée, comme le montre la figure 2c (symboles en diamant). La vitesse de gravure du SiNW a augmenté d'un temps de dépôt de 10 s à 4 min, mais a diminué de manière inattendue entre 4 min et 6 min. Par la suite, la vitesse de gravure a de nouveau augmenté jusqu'à 15 minutes, bien qu'avec des valeurs de vitesse de gravure relativement plus faibles.
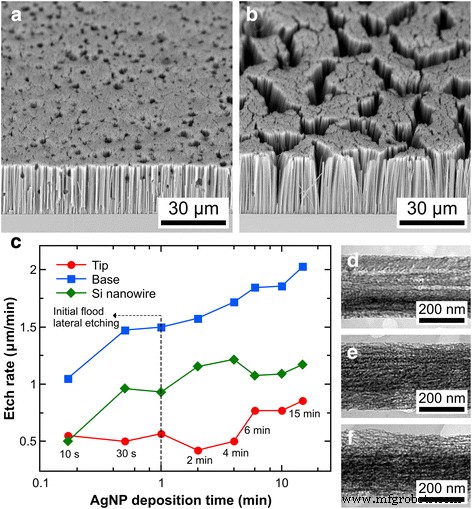
SiNWs fabriqués à l'aide d'une solution de dépôt d'Ag contenant 0,005 M AgNO3 et 4,8 M HF et une solution de gravure composée de 48 M H2 O et 0,95 HF–H2 O2 rapport molaire. Images SEM des SiNW pour les temps de dépôt d'Ag de a 30 s et b 4 minutes c Taux de gravure des SiNW pour différents temps de dépôt d'Ag. Images MET de la section médiane des SiNW pour des temps de dépôt d'Ag de d 4, e 10, et f 15 montrant le degré de porosité. La durée de gravure pour tous les échantillons était de 30 minutes
Afin de tenir compte de la tendance particulière de la vitesse de gravure du SiNW, les taux de gravure à la pointe et à la base des SiNW ont également été déterminés à partir des images SEM en coupe transversale en alignant la micrographie d'un échantillon de Si gravé avec celle d'un Si non gravé échantillon de la même plaquette à l'arrière (voir Fichier supplémentaire 1 :Figure S1). À partir de la figure 2c, on peut voir que la vitesse de gravure à la base SiNW (symboles carrés) augmente de manière monotone avec le temps de dépôt d'AgNP. D'autre part, trois domaines peuvent être observés à partir de la ligne de tendance de la vitesse de gravure de la pointe SiNW (symboles circulaires) :(a) ≤1 min, où la vitesse de gravure est relativement élevée ; (b) entre 1 et 6 min, lorsque la vitesse de gravure est relativement faible ; et (c) ≥6 min, où la vitesse de gravure est la plus élevée. Ainsi, l'augmentation initiale de la vitesse de gravure SiNW du temps de dépôt de 10 s à 1 min était due à l'augmentation constante de la vitesse de gravure à la base, tandis que l'augmentation ultérieure de la vitesse de gravure aux temps de dépôt de 2 et 4 min était due à les taux de gravure relativement faibles aux extrémités. Pendant ce temps, la baisse de la vitesse de gravure du SiNW au moment du dépôt de 6 min et les vitesses de gravure relativement faibles dans les temps de dépôt suivants ont été causées par l'augmentation de la vitesse de gravure au niveau des pointes.
Étant donné que la couverture de surface des AgNPs est directement liée au temps de dépôt d'Ag [22, 34, 35], les piqûres latérales pour les temps de dépôt faibles peuvent être attribuées à un réseau d'Ag clairsemé [18, 34, 36] avec quelques AgNPs isolés se déplaçant dans directions aléatoires <100> en raison de leur forme irrégulière [37]. Le taux de gravure du SiNW à la base devrait augmenter avec le temps de dépôt d'Ag en raison de l'augmentation de la quantité de catalyseur Ag, qui fournit plus de surface pour l'injection de trous par H2 O2 . De plus, une plus grande quantité d'Ag signifie également plus d'Ag oxydé par H2 O2 [15, 17], ce qui entraîne une concentration plus élevée d'Ag + des ions pouvant contribuer à la dissolution du Si via une réaction de déplacement galvanique [31]. D'autre part, les taux de gravure relativement élevés aux extrémités pour des temps de dépôt d'Ag ≤ 1 min peuvent être expliqués par une gravure latérale initiale causée par des AgNPs de forme irrégulière provenant du réseau d'Ag clairsemé. Les augmentations ultérieures de la vitesse de gravure des pointes avec l'augmentation du temps de dépôt d'Ag peuvent être attribuées à l'augmentation des taux de renucléation du métal [17, 38] aux pointes et, dans une moindre mesure, à la diffusion des trous [31, 39].
Il y avait une augmentation globale de la porosité des SiNW fabriqués à mesure que le temps de dépôt d'Ag augmentait, comme le montre la figure 2d–f. (Voir le fichier supplémentaire 1 :Figure S2a–c pour des images MET supplémentaires.) De telles augmentations de la porosification sont attendues en raison de concentrations plus élevées d'Ag + ions, qui entraînent un métal renucléé et une gravure induite par des ions [15, 17, 38]. De plus, des taux plus élevés d'injection de trous pourraient également avoir entraîné des trous plus diffus, ce qui peut contribuer à la formation de pores [19, 39]. La structure poreuse des SiNW semble se présenter sous la forme d'une coque poreuse dans la plupart des nanofils, similaire à ce qui a été observé dans des études précédentes [14, 17]. Pour certains SiNW avec un temps de dépôt d'Ag de 15 min, les parois latérales apparaissent considérablement plus rugueuses avec des taches sombres relativement grandes (≈20 nm de diamètre), probablement dues à des particules d'Ag renucléées plus grosses. Cependant, la distribution de la porosité n'est pas claire :certains SiNW avec un temps de dépôt d'Ag de 4 min ont presque la même porosité que celle des SiNW avec un temps de dépôt d'Ag de 10 min ; il en va de même pour les SiNW avec des temps de dépôt d'Ag de 10 et 15 min. Cela était probablement dû aux SiNW obtenus à partir de différentes zones de l'échantillon, qui ont connu des taux de porosification légèrement différents en fonction de la quantité réelle d'AgNPs déposés (ou renucléés) et de la concentration d'agent de gravure n'ayant pas réagi, qui devrait être plus élevée vers les côtés. de l'échantillon. Néanmoins, la tendance générale observée ici indique que la quantité globale d'Ag déposé offre un autre degré de liberté dans le contrôle de la porosité des SiNW.
Le degré de porosité augmente de la base à la pointe des SiNW (voir Fichier complémentaire 1 :Figure S2d–l), similaire à celui des études précédentes [16, 19]. Ceci est attendu de l'exposition plus longue des régions supérieures des nanofils à l'agent de gravure [19]. D'autre part, la majorité des SiNW ont un profil longitudinal effilé, caractéristique des SiNW hautement dopés fabriqués à l'aide d'Ag-MACE en raison de la dissolution continue des AgNP à la base du SiNW et de la renucléation sur d'autres sites [15, 17 ]. Néanmoins, il y avait quelques SiNW ayant un profil légèrement biconique ou en sablier, c'est-à-dire que la section transversale médiane est respectivement plus grande ou plus petite que les sections transversales supérieure et inférieure. Cela suggère que le mobile Ag + les ions pourraient se redéposer non seulement sur les sections supérieures des nanofils, mais aussi sur les AgNP voisins à la base.
Composition d'attaque et évolution morphologique des nanostructures de silicium
La morphologie des nanostructures résultantes dans Si dopé dégénéré a été déterminée en utilisant χ valeurs de 0,7 à 0,99 et H2 Concentrations en O de 46, 48 et 50 M. Le dépôt autocatalytique d'AgNPs a été effectué dans une solution de 0,005 AgNO3 et 4,8 M HF pendant 4 min, tout en gravant en HF–H2 O2 –H2 O solutions a été réalisée pendant 30 min. La figure 3 montre la morphologie de la surface de Si vue au MEB. Pour [H2 O] = 46 M et 48 M, les caractéristiques sur le Si gravé évoluent à partir de Si microporeux avec des cratères (χ = 0,7 et 0,75, Fig. 3d, e), aux macropores à pores profonds (χ = 0,75 et 0,80, Fig. 3f), puis aux SiNWs (χ ≥ 0.85). Pour [H2 O] = 50 M, l'évolution de la surface du Si est légèrement différente :à partir du Si poli (χ = 0.7), aux macropores à pores profonds (χ = 0,75), au Si microporeux avec cratères (χ = 0,8–0,85), puis à SiNWs (χ 0.9). Contrairement aux travaux de Chiappini et al. [15], SiNWs sur un film de Si poreux pour 0,7 < χ < 0.95 n'ont pas été observés, et des structures uniquement SiNW ont été obtenues dans un plus grand χ plage (χ ≥ 0.85 au lieu de χ> 0.95). Ces différences étaient très probablement dues aux variations de la quantité d'AgNP déposés, du temps de gravure, de H2 Concentrations en O et HNO3 et traitements post-mordançage HF.
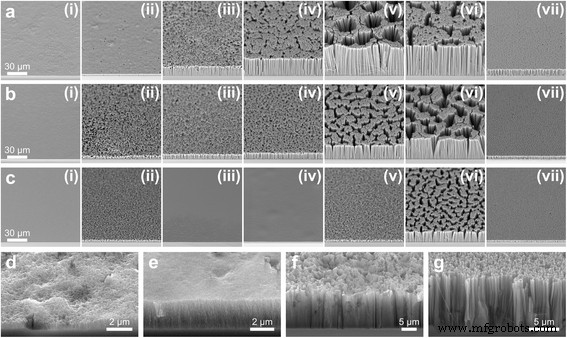
Images SEM de la surface Si gravée dans des solutions avec H2 O concentrations de a 46 H, b 48 M, et c 50 M et HF–H2 O2 rapports molaires de (i) 0.7, (ii) 0,75, (iii) 0.8, (iv) 0,85, (v) 0.9, (vi) 0,95, et (vii) 0,99. d –g Images SEM à fort grossissement des échantillons dans a (i) , (ii ), (iii ), et (vii ), respectivement. Les échantillons ont été gravés en HF–H2 O2 pendant 30 minutes
Les morphologies Si obtenues peuvent être expliquées en termes de densité de courant à l'interface Ag-Si et Ag + gravure induite par des ions [15, 17, 31, 38]. La formation de SiNWs à haute χ les valeurs (≥0,85 ou 0,9) peuvent être attribuées à la formation de Si microporeux à de faibles densités de courant avec dissolution ultérieure du Si microporeux par polissage [31, 38]. Un mécanisme similaire était très probablement responsable de la formation de Si macroporeux avec des pores profonds à χ inférieur valeurs, sauf que les densités de courant plus élevées à l'extrémité des pores ont entraîné la formation d'oxyde et la diffusion subséquente des trous [31], entraînant des macropores peu profonds à la surface supérieure. Une telle diffusion de trous devrait être particulièrement importante pour le Si de type p hautement dopé en raison de la hauteur de barrière de Schottky positive qui éloigne les trous injectés de l'interface métal-Si [40]. Il est également possible que le [H2 relativement élevé O2 ] à [HF] a conduit à une dissolution d'Ag significative, qui à son tour a entraîné la faible densité de pores profonds dans le substrat de Si. D'autre part, l'apparition de Si microporeux avec des cratères à χ = 0,7-0,85 indique l'apparition de faibles densités de courant dans ce χ gamme, ce qui est cohérent avec l'observation de Chartier et al. [31] De plus, la porosification concomitante du Si par Ag + ions devrait également se produire dans ce régime. La formation de SiNWs à un χ plus élevé valeur pour le mordançage le plus dilué (50 M H2 O) est cohérent avec l'observation de Chiappini et al. [15] que des concentrations d'éthanol plus élevées favorisent la formation de Si poreux et poli plutôt que de SiNW. Ces résultats pourraient être dus à la diffusion lente des réactifs vers la base de la nanostructure due aux faibles HF et H2 O2 gradients de concentration le long de la profondeur de la nanostructure de Si. Dans ce cas, l'impact de la gravure au niveau des pointes devient relativement important et des pores profonds ne pourraient pas être formés par les particules métalliques.
Il convient de noter que pour des valeurs relativement faibles de χ (≤0,8), la morphologie sur toute la surface de Si n'était pas uniforme (voir Fichier supplémentaire 1 :Figure S3). Pour [H2 O] = 50 M, une gravure non uniforme s'est également produite pour χ = 0.85. Dans tous les cas, une surface gravée uniformément n'a été obtenue que lorsque des SiNW ont été formés. Pour les surfaces gravées de manière non uniforme, les sections avec des morphologies homologues ont tendance à se produire à peu près au même emplacement général à partir du centre de l'échantillon. La dynamique de gravure non uniforme dans différentes zones de l'échantillon peut s'expliquer par l'augmentation de la concentration d'ions catalyseurs dissous dans la solution et leur diffusion ultérieure et renucléation sur d'autres zones de l'échantillon. Cela a été facilité dans une certaine mesure par la diffusion externe simultanée de H2 bulles lors de la gravure du Si.
À un χ très élevé (0,99), un réseau très dense de SiNW fins a été obtenu, conduisant à une surface d'échantillon noire (voir Fichier supplémentaire 1 :Figure S3a–c(vii)). Cependant, bon nombre de ces SiNW avaient des parois latérales inclinées et quelques creux latéraux, qui se produisent tous deux près de la base (Fig. 3g) et à des temps de gravure longs (Fichier supplémentaire 1 :Figure S4d). Un certain nombre de bosses où la formation de nanofils s'est terminée prématurément peuvent également être observées. De telles caractéristiques ont probablement été causées par l'épuisement de H2 O2 dans la solution de gravure qui a conduit à des taux différents d'enfoncement de diverses parties du film AgNP. Au fur et à mesure que le réseau Ag se désintégrait, certaines sections d'AgNP ou de petites pellicules Ag ont commencé à graver dans des directions <100> horizontales.
Cinétique de gravure de nanostructures de silicium pendant MACE
La variation du taux de gravure avec χ pour différents [H2 Les valeurs de O] sont indiquées sur la figure 4. La vitesse de gravure apparente des nanostructures augmente généralement avec χ et culmine à χ =0,95, après quoi les taux de gravure chutent de manière significative. Cette tendance est vraie quel que soit le [H2 O] et la morphologie de la nanostructure de Si. Cependant, [H2 O] peut être vu comme ayant considérablement affecté l'amplitude des taux de gravure, l'amplitude augmentant pour diminuer [H2 O] (c'est-à-dire des agents de gravure plus concentrés). La figure 4b montre que le taux de gravure à la pointe a considérablement diminué après χ = 0.85 pour [H2 O] = 46 et 48 M et après χ = 0.9 pour [H2 O] = 50 M. Par contre, la Fig. 4c montre que la vitesse de gravure à la base augmente considérablement à χ = 0.85 et 0.9 pour le 46 M H2 O etchant mais seulement légèrement pour les 48 et 50 M H2 graveurs. Le taux de gravure à la base est resté élevé à χ = 0,95 mais diminue significativement à χ = 0.99.
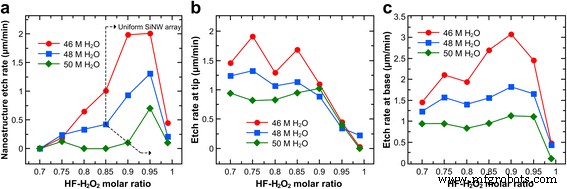
Taux de gravure apparents observés après 30 min de gravure dans des solutions composées de différents HF–H2 O2 rapports molaires et H2 O concentrations. un Taux de gravure des nanostructures de Si basé sur la longueur résultante. b , c Taux de gravure du Si massif par rapport à la pointe et à la base des nanostructures de Si, respectivement
D'après les tendances des taux de gravure à la pointe et à la base des nanostructures de Si, il peut être déterminé que l'augmentation de la longueur SiNW pour [H2 O] = 46 M était principalement dû à l'accélération de la gravure à la base, tandis que l'allongement des SiNWs pour [H2 O] = 48 et 50 M étaient principalement dictés par la suppression de la gravure aux extrémités. De plus, la tendance de la vitesse de gravure globale des nanostructures n'est pas exactement la même que la tendance de la vitesse de gravure à la base. En particulier, le χ valeur où se produit le taux de gravure de pointe à la base et le χ la valeur où la plus grande hauteur de nanostructure est atteinte n'est pas la même (0,9 contre 0,95, respectivement) en raison de l'effet concurrent de la vitesse de gravure de la pointe.
Le χ La valeur où la longueur du pic SiNW s'est produite (0,95) est proche de celle obtenue par Qi et al. [21] (χ =0,91) pour un substrat Si de type n fortement dopé. La diminution initiale du taux de gravure de la pointe se produit près de χ = 0,85 est cohérent avec l'évolution morphologique observée de la surface de Si dans laquelle la faible diffusion des trous et la renucléation de l'Ag ont permis la formation de SiNW à χ 0.85. La baisse presque simultanée du taux de gravure de pointe et le saut du taux de gravure de base à environ χ = 0.85 signifie que les trous et Ag + ions qui diffusaient auparavant loin du front de gravure à χ inférieur les valeurs étaient maintenant limitées à la base en raison de l'inhibition de la formation d'oxydes à l'interface Ag-Si. Dans le même temps, l'augmentation de [HF] à χ plus élevé les valeurs ont accéléré la dissolution du Si, conduisant à une augmentation du taux de pénétration de l'Ag. Étant donné que [HF] et [H2 O2 ] diminue lorsque [H2 O] augmente pour un χ donné (voir Fichier complémentaire 1 :Tableau S1), la diminution de la vitesse de gravure aux pointes et la base pour les [H2 plus élevés O] est attendue. Les plus petites augmentations du taux de gravure de base entre χ = 0.85 et 0.95 pour [H2 O] = 48 et 50 M sont dus à la diffusion plus lente des réactifs à travers la longueur SiNW pour les mordançages plus dilués.
À χ = 0.9, le taux de gravure à la base est maximal en raison des taux optimaux d'injection de trous par H2 O2 et dissolution de Si par HF. En dessous de cette valeur, [HF] est le facteur déterminant la vitesse car la dissolution du Si oxydé n'est pas assez rapide; au dessus de cette valeur, [H2 O2 ] détermine la vitesse de réaction car le nombre de trous injectés est trop faible. Cet épuisement de H2 O2 dans la solution explique pourquoi le taux de gravure à la base commence à diminuer à χ = 0.95 et chute fortement à χ = 0.99. Une telle dépendance du taux de gravure à la fois sur [HF] et [H2 O2 ] a été observé précédemment [21] et implique que les deux concentrations de réactifs doivent être prises en compte dans toute expression de la vitesse de réaction du MACE de Si. En revanche, une valeur maximale pour χ n'est pas évident d'après le taux de gravure de la pointe. Au lieu de cela, le taux de gravure de pointe est principalement déterminé par [H2 O2 ]. Étant donné que la gravure à la pointe des nanostructures de Si peut être principalement attribuée à la renucléation des ions métalliques et à la diffusion des trous, cette corrélation est raisonnable car plus élevée [H2 O2 ] par rapport à [HF] conduisent à des concentrations plus élevées d'Ag + mobile ions [15, 17] et trous injectés [31, 32].
Évolution de la longueur SiNW avec le temps pour différentes compositions de gravure
La longueur des SiNW est un paramètre important dans les applications photovoltaïques [2], de stockage d'énergie [6], de détection [41] et thermoélectriques [4]. Afin de fabriquer des SiNW d'une longueur spécifiée, la variation temporelle de la longueur de SiNW a été déterminée pour les mordants avec χ = 0,9, 0,92, 0,95 et 0,98 et [H2 O] =46, 48 et 50 M. Pour ces expériences, le temps de dépôt d'AgNP a été augmenté à 10 min pour minimiser les piqûres latérales dans les SiNW fabriqués avec de longs temps de gravure (voir Fichier supplémentaire 1 :Figure S4a-c). De même, le plus élevé χ la valeur utilisée était de 0,98 car des SiNW avec des parois latérales inclinées et des fosses latérales ont été obtenus pour χ = 0.99 même avec un temps de dépôt AgNP de 10 min (voir Fichier supplémentaire 1 :Figure S4d).
La figure 5a montre que la longueur des SiNW formés augmente avec le temps de réaction du MACE, ce qui est cohérent avec les observations d'études précédentes [14, 16, 17, 18, 19, 21, 23]. Cependant, on peut voir que l'augmentation de la longueur du SiNW diminue avec le temps, c'est-à-dire que le taux de gravure diminue (voir Fichier supplémentaire 1 :Figure S5a), ce qui pourrait être dû à l'augmentation des taux de gravure aux pointes SiNW ou à la diminution des taux de gravure à la base ou les deux. La figure 5d montre l'augmentation des taux de gravure des pointes au fil du temps pour χ = 0,92 et 0,95, l'augmentation étant plus prononcée dans le premier (voir Fiche complémentaire 1 :Figure S5b). Cela indique une quantité croissante d'Ag renucléé aux extrémités SiNW, ce qui devrait être plus important pour les χ inférieurs valeurs. D'autre part, la figure 5e montre qu'à des temps de gravure supérieurs à 5 min, la vitesse de gravure à la base SiNW était presque constante pour χ = 0.9 et 0.92 mais décroissant pour χ = 0.95 and 0.98 (see Additional file 1:Figure S5c). The latter was probably due to impeded diffusion of reactants to the SiNW base caused by the longer diffusion lengths (SiNW lengths were longer for χ = 0.95 and 0.98) and depletion of H2 O2 in the etching solution.
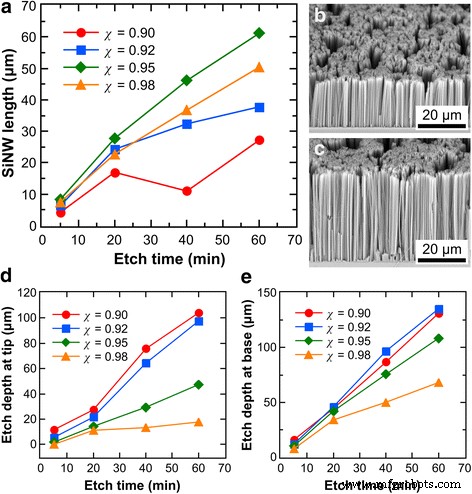
Evolution of SiNW length with time for different HF–H2 O2 molar ratios at 48 M H2 O. a Effect of etch time on SiNW length. b , c SEM images of SiNWs after etching for 1 h in a solution composed of 48 M H2 O and HF–H2 O2 molar ratios of 0.9 and 0.98, respectively. d , e Etched bulk Si thickness with respect to the tip and base of the SiNWs over time
It should be noted from Fig. 5 that at χ = 0.9, the evolution of length with time is erratic because of the non-monotonic trend of the etch rate at the tip (see Additional file 1:Figure S5b). This may be due to differing amounts of re-nucleated Ag as more mobile Ag + ions were generated. Nevertheless, lower χ values have the advantage of forming defect-free SiNWs (Fig. 5b) as higher χ may result in some lateral pits, as shown in Fig. 5c for χ = 0.98. The trend of the overall etch rates and etch rates at the tip and base of the SiNWs with respect to χ mirrors those observed in Fig. 4. However, it can be seen in Fig. 5e that χ = 0.92, which is not included in Fig. 4, actually results in a higher base etch rate than χ = 0.9.
The SiNW length also increases with etch duration for more concentrated (46 M H2 O) and dilute (50 M H2 O) etchants, as shown in Fig. 6a. Likewise, the etch rate decreases with etch time for all H2 O concentrations used (see Additional file 1:Figure S6a). Figure 5d, e show that, while the etch depth at the tip and base of the SiNWs both increase with time, the amount of increase at the tip is almost constant but that at the base is decreasing (see Additional file 1:Figure S6b, c). These trends are consistent with those observed for χ = 0.95 in Fig. 5 and Additional file 1:Figure S5. Hence, for χ = 0.95, the increase in the amount of re-nucleated Ag at the SiNW tips with time is negligible, while the increasing SiNW lengths progressively hampers reactant diffusion to the SiNW base. Figure 6 also shows that regardless of the etching time point, lower [H2 O] generally results in more etched Si, similar to what was observed in Fig. 4. However, Fig. 6b, c show that low [H2 O] solutions may result in some lateral pitting in the SiNWs whereas high [H2 O] solutions do not. This could be due to fast etching at sites with re-nucleated Ag particles for low [H2 O] etchants.
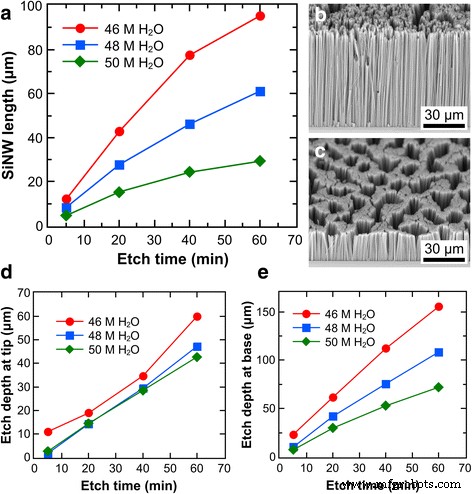
Evolution of SiNW length with time for different H2 O concentrations at a fixed HF–H2 O2 molar ratio of 0.95. un Effect of etch time on SiNW length. b , c SEM images of SiNWs after etching for 1 h in a solution composed of HF–H2 O2 molar ratios of 0.95 and H2 O concentrations of 46 and 50 M, respectively. d , e Etched bulk Si thickness with respect to the tip and base of the SiNWs over time
Fabrication of Highly Doped SiNWs with Controlled Porosity
SiNW porosity is another key parameter in SiNW-based devices [5, 16, 27, 29], making its controlled formation during SiNW fabrication highly important. The degree of porosity of SiNWs fabricated using two-step MACE is directly related to the H2 O2 concentration [14,15,16,17, 20], etching time [14, 16, 17, 20], and temperature [20] and inversely related to the HF–H2 O2 volume ratio [19] and wafer resistivity [17]. In our Ag deposition experiment, SiNW porosity was also found to be directly related to the amount of deposited Ag. However, the extent of SiNW porosification cannot be easily tuned without affecting other parameters. For example, length and porosity are expected to vary together if one of them is adjusted using either [H2 O2 ], etch time, or temperature. If a SiNW of a specific length needs to have higher porosity, the [H2 O2 ] can be increased, but the etch duration needs to be decreased as higher [H2 O2 ] may have a higher etch rate. This raises the question of whether the desired porosity can still be achieved given the shorter etch time.
Here, the extent of SiNW porosification caused independently by χ and [H2 O] was compared for χ = 0.92, 0.95, and 0.98 ([H2 O] fixed at 48 M) and [H2 O] = 46, 48, and 50 M (χ fixed at 0.95). The SiNW length was fixed at 20 μm by using different etch durations based on the etch rate of the respective etchant composition (see Additional file 1:Table S2). The porosity, in general, was found to be inversely related to χ and directly related to [H2 O], as shown in Fig. 7a–c and Fig. 7d, b, e, respectively. (The trends are more apparent in Additional file 1:Figure S7 where more samples are shown.) Comparing the SiNWs for χ = 0.95 and χ = 0.98 (Fig. 7b, c), the samples for χ = 0.95 appear to have a higher pore density and most are surrounded by a thin porous shell [14, 17]. Meanwhile, for χ = 0.98, some SiNWs appear to be rough and solid rather than porous, which indicates a much lesser degree of porosification. On the other hand, the overall porosity obtained for χ = 0.92 (Fig. 7a and Additional file 1:Figure S7a) appears to depart from the expected trend. While some SiNWs have a porous shell, others seem to be only roughened although to a higher extent compared with those for χ = 0.98. In contrast, the increase of porosity with [H2 O] is more consistent. Although no rough solid SiNWs were obtained for [H2 O] = 46 M, highly porous SiNWs were formed for [H2 O] = 50 M unlike in the case of χ = 0.92.

TEM images of fabricated SiNWs with a length of ≈20 μm showing the variation of porosity at the middle section with a –c HF–H2 O2 molar ratio and d , b , c H2 O concentration. un –c HF–H2 O2 molar ratio of the etchant was 0.92, 0.95, and 0.98, respectively, with [H2 O] = 48 M. d , b , c H2 O concentration of the etchant was 46, 48, and 50 M, respectively, with HF–H2 O2 molar ratio = 0.95. TEM images of SiNWs with f –h low and i –k high porosity corresponding to those shown in c and e , respectively, but including the f , i top et h , k bottom sections. The scale bar in e and k also applies to the images in a –d et f –j , respectively
The higher SiNW porosity obtained for χ = 0.95 than χ = 0.98 is consistent with the fact that metal re-nucleation, metal ion-induced etching, and hole diffusion are higher for lower χ values. It also shows that the longer etch time utilized for χ = 0.98 to obtain 20-μm long SiNWs did not overcome the porosification caused by the etchant χ value. The seemingly lesser degree of porosification for χ = 0.92 could not have been due to the difference in etch time as a longer etching period was utilized for it than for χ = 0.95. It is possible that more porous SiNWs were actually obtained for χ = 0.92; however, due to the very high porosity, HF–H2 O2 etching of porous Si both at the surface and inside the pore walls resulted, leading to the rapid collapse of the porous shells [42] and subsequent exposure of the less porous Si surface underneath. That more porous SiNWs were obtained for higher [H2 O] values confirms that etch duration has a significant effect on porosity [14, 16, 17, 20]. (Note the large differences in etch times in Additional file 1:Table S2 for different [H2 O] values.) The high degree of porosity obtained for 50 M H2 O without the collapse of the porous shell could be due to minimized HF–H2 O2 etching inside the pore walls because of the lower diffusion rate of reactants in dilute etchants.
Examination of the surface roughness along the length of the SiNWs reveals the characteristic increase in porosity from the base to the tip of highly doped SiNWs fabricated with MACE [16, 19], as shown in Fig. 7f–k (also in Additional file 1:Figure S8). The increase in porosity towards the tip of the SiNWs is due to the longer exposure time of these portions in the etchant solution [19]. Figure 6f–k and Additional file 1:Figure S8 also show that the SiNWs are tapered, with the tapering being more severe in SiNWs which are more porous (Fig. 7i–k and Additional file 1:Figure S8a–c). This is expected considering that porosification is directly related to the amount of dissolution of the metal catalyst at the SiNW base [15, 17]. However, a closer look at the SiNWs reveals that some nanowires exhibit a slightly biconic or hourglass longitudinal profile, which seems to occur more often among those with higher porosity. Likewise, more porous SiNWs generally have larger diameters than the less porous ones (see Additional file 1:Figure S7). In order to achieve highly porous SiNWs with smaller diameters, it might be necessary to use a more inert catalyst like Au [32].
Based on the results obtained here, porosity control in highly doped SiNWs of a given length is possible through the use of the appropriate etchant composition. To achieve low porosity, it is best to use high χ values as rough solid nanowires could be obtained. To achieve highly porous SiNWs, on the other hand, the use of dilute etchants with moderate χ values (≈0.95) is advisable as this avoids the disintegration of the porous shell which occurs in etchants with low χ values. It is conceivable that lower porosities could be achieved using an etchant of both high χ and low [H2 O] values and higher porosities using an etchant of both (slightly) lower χ and high [H2 O] values. In the case of low-porosity SiNWs, the maximum χ and minimum [H2 O] values would probably be dictated by the values where considerable lateral pitting occurs. On the other hand, for high-porosity SiNWs, the minimum χ and maximum [H2 O] values would be determined by the values where the porous shell dissolves and the SiNW structures are lost, respectively. These methods can be combined with our earlier finding of porosity control via the amount deposited Ag in order to obtain a wide range of SiNW porosities.
Conclusions
Porous SiNWs were fabricated from degenerately doped p-type Si substrates using metal-assisted chemical etching in HF–H2 O2 with electrolessly deposited Ag catalyst. The effect of Ag deposition time, etchant HF–H2 O2 molar ratio, and etchant H2 O concentration on the morphology and etch rate of the Si nanostructures was systematically studied. It was shown that there is an optimal amount of deposited Ag particles necessary to form damage-free SiNWs. Furthermore, the amount of deposited Ag particles affects the SiNW etch rate in a non-monotonic manner and provides an additional mechanism to control the porosity of the resulting nanowires. Likewise, the etchant composition has a significant effect on the resulting nanostructures. There is an appropriate χ window within which uniform SiNW arrays can be formed. For H2 O concentrations between 46 and 48 M, this χ range is 0.85–0.98; more dilute etchants increase the minimum χ due to sluggish etching at the SiNW base. The formation of Si nanostructures during Ag-catalyzed chemical etching is a result of the competing effects of different factors, namely, deposited Ag-catalyzed Si dissolution, re-nucleated Ag-catalyzed Si dissolution, hole diffusion, and reactant diffusion through etched pores, as reflected by the etching kinetics at the tip and base of the Si nanostructures. These factors result in a gradually decreasing etch rate over time, with re-nucleated Ag-catalyzed etching being dominant for low χ values and impeded diffusion being more pronounced for high χ values. These mechanisms can be exploited to control the porosity of SiNWs of the same length fabricated with different etch times. In particular, suppressing Ag re-nucleation and hole diffusion using higher χ values can effectively decrease pore density, while more controlled porosification can be achieved using dilute etchants owing to slower reactant diffusion and longer etch times. Since the general mechanism of Ag- and Au-catalyzed MACE of Si is similar [11, 33, 35], the findings of this study may also apply to porous SiNWs fabricated with Au metal catalyst, except that metal ion-induced etching is expected to be greatly suppressed and hole diffusion acts as the main mechanism of porosification and tip etching.
Abréviations
- AgNP:
-
Ag nanoparticle
- DI:
-
Deionized
- MACE:
-
Metal-assisted chemical etching
- SEM :
-
Microscopie électronique à balayage
- SiNW:
-
Silicon nanowire
- TEM :
-
Microscopie électronique à transmission
- χ :
-
HF–oxidant molar ratio
Nanomatériaux
- Heroes in Silicon Valley (et à la réunion du groupe d'utilisateurs RTI)
- Évolution du marché des matériaux d'impression 3D :tendances et opportunités en 2019
- L'évolution du SLS :nouvelles technologies, matériaux et applications
- Instrumentation de surveillance du benzène pour les industries chimiques, pharmaceutiques et pétrochimiques
- Démêler les complexités des lois anti-corruption
- L'évolution et l'avenir de la livraison en bordure de rue au détail
- L'incroyable évolution de l'impression 3D dans l'aérospatiale et la défense
- Systèmes de maintenance préventive et logiciel GMAO :l'évolution
- L'acier inoxydable et l'évolution des montagnes russes