Un Turn-Mill doit-il tourner ?
LeanWerks a développé un processus combinant outil de coupe, serrage et des technologies de test de pièces pour permettre à son usine de tournage d'usiner cinq faces de cette pièce de moulage à la cire perdue en une seule configuration. Crédits photos :LeanWerks
Il y a quelques années, la baisse des conditions commerciales dans les champs pétrolifères a incité les LeanWerks d'Ogden, dans l'Utah, à poursuivre des travaux dans d'autres secteurs (y compris l'aérospatiale et l'automatisation à grande vitesse) pour établir une clientèle plus équilibrée et un flux de travail plus stable. L'atelier sous contrat, désormais enregistré selon la norme aérospatiale AS9100C, a également commencé à adapter une partie de sa capacité d'usinage existante pour mieux répondre aux travaux d'usinage qu'il rencontrerait dans ces nouvelles industries.
Reid Leland, président et cofondateur de l'entreprise, donne un exemple :un moulage de précision en aluminium pour un boîtier de filtre à carburant de moteur à réaction. Au moment où LeanWerks a été initié à ce travail, son client de fonderie aérospatiale avait près d'un an de retard sur le calendrier de livraison car son processus d'usinage interne, donc son taux de production, était lent. En conséquence, son client - l'OEM du moteur à réaction sur lequel ce boîtier est installé - perdait patience, et l'arriéré causé par les retards de ce travail décevait les autres clients. Par conséquent, dans le but d'alléger une partie de la charge sur ses ressources d'usinage internes, la fonderie a contacté LeanWerks pour envisager de prendre en charge l'usinage de ces pièces moulées.
Bien que de nombreux ingénieurs spécifient des moulages de précision pour leurs conceptions de pièces car ils offrent une complexité de forme avec une bonne précision dimensionnelle par rapport à d'autres processus de moulage, ces composants nécessitent toujours un usinage pour obtenir un ajustement et une fonction précis dans des assemblages hautes performances. Cependant, la variabilité de ces types de pièces brutes de fonderie et leurs exigences de serrage délicates associées font que certains ateliers évitent d'entreprendre ce type de travail d'usinage.
Par exemple, le boîtier du filtre à carburant nécessite plusieurs opérations d'usinage, y compris le fraisage de trous profonds, l'alésage, le surfaçage, le perçage, le taraudage, le rainurage du diamètre intérieur et le contournage 3D. À l'origine, LeanWerks pensait pouvoir terminer le travail en utilisant plusieurs configurations sur une fraiseuse à trois axes et une configuration sur un centre de tournage. Il a finalement décidé que ce n'était pas la meilleure stratégie, car les tolérances de position serrées de la pièce avec un schéma de référence compliqué ne seraient pas réalisables en raison des multiples configurations.
Au lieu de cela, LeanWerks a réfléchi à la manière dont il pourrait tirer parti de la capacité de fraisage de son tournage-fraisage Mazak Integrex i200S pour minimiser le nombre de fois que la pièce est touchée pendant l'usinage. L'atelier utilisait principalement cette machine pour produire des inserts de vannes à boisseau conique pour les opérations de pompage à haute pression dans l'industrie pétrolière et gazière, telles que celles requises pour les applications de fracturation hydraulique et de tubes enroulés. L'Integrex était bien adapté à la pièce d'insert de soupape car il pouvait à la fois tourner le diamètre extérieur conique de la pièce et fraiser ses alésages d'écoulement à axe transversal interne. La machine pouvait également fraiser le joint torique associé à l'alésage, ce qui nécessitait une opération de contournage sur cinq axes en raison de la surface conique de l'alésage.
Cela dit, l'usinage de la partie du boîtier du filtre à carburant sur le tournage-fraisage, un travail qui ne nécessitait aucun tournage, présentait une variété de défis. Par exemple, l'aluminium coulé de qualité aéronautique A356.0 a une teneur élevée en silice et peut être dur pour les outils de coupe. De plus, la géométrie de la pièce présente de multiples caractéristiques à plusieurs angles sur toutes les faces (y compris un raccord critique à l'intérieur du fond de la pièce moulée de 13 pouces de profondeur) et les zones à parois minces créent des problèmes de vibration lors de l'usinage. De plus, la pièce avec une structure de référence complexe nécessite des tolérances serrées, y compris une tolérance de position réelle de 0,25 mm sur certaines caractéristiques largement séparées, et des tolérances de taille de ± 0,01 mm et des tolérances de position réelle de 0,05 mm pour d'autres caractéristiques moins séparées.
En conséquence, LeanWerks a essentiellement suivi trois étapes pour permettre à son usine de tournage d'usiner efficacement cinq faces du moulage à la cire perdue en une seule configuration. La première étape consistait à concevoir un montage pour maintenir la pièce moulée afin de permettre l'usinage à effectuer sur les cinq côtés de la pièce. Un élément clé de cette conception de luminaire est un berceau qui s'engage dans le corps principal de la pièce moulée tout en offrant un accès aux caractéristiques entre et le long des pieds du berceau. Pour fixer le moulage au berceau, un mécanisme de chaîne et de poulie a été installé entre les pieds du berceau pour fournir une force de serrage uniformément répartie.
Étant donné que le tournage-fraisage n'offrait pas une course suffisante sur l'axe Y pour atteindre toutes les fonctionnalités, une glissière à queue d'aronde Setco a été incorporée dans le dispositif pour permettre au berceau et à la pièce d'être glissés et resserrés dans une position accessible sans refixer complètement la pièce. Pour assurer la rigidité, le berceau a été monté et renforcé sur une plaque de base en acier avec des goujons et des soudures. Cette plaque de base se monte sur la selle coulissante en queue d'aronde, et la base de la glissière se monte sur les mors principaux du mandrin à trois mors existant de la machine.
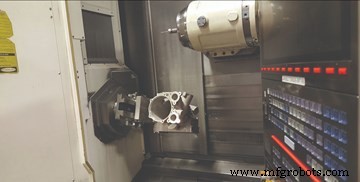
En raison de la taille de cette pièce, le la course de l'axe Y du tournage-fraisage ne permet pas à sa broche d'atteindre toutes les zones de la pièce à usiner. Pour atténuer cela, le luminaire développé par LeanWerks utilise une glissière à queue d'aronde pour permettre à la pièce fixée d'être glissée et re-serrée dans une position accessible. Les routines de palpage suivantes déterminent la position réelle de la pièce repositionnée.
Ensuite, l'atelier a intégré un système de palpage à déclenchement par contact. Le palpage tactile était nécessaire car la forme de chaque pièce brute de coulée varie légèrement et le dispositif coulissant utilisé pour atténuer le problème de déplacement de l'axe Y modifie l'emplacement de la pièce. Le palpage a permis de définir avec précision la nouvelle position de la pièce après le décalage et d'adapter au mieux les trajectoires d'outil suivantes à l'emplacement réel de la pièce.
En fait, l'atelier s'est rendu compte qu'il avait besoin d'une sonde de longueur standard ainsi que d'une sonde à portée étendue pour accéder aux fonctions situées profondément à l'intérieur de la pièce. Étant donné que le tournage-fraisage ne comportait qu'un seul canal de palpage, LeanWerks a équipé la machine d'un récepteur radio Renishaw RMI-Q et a installé une carte de contrôleur logique programmable (PLC) dans le panneau de commande principal de la machine pour gérer un deuxième signal de palpage. La sonde courte utilise un stylet de 25 mm de long, tandis que la sonde longue utilise un stylet de 50 mm de long monté sur une rallonge de 200 mm. Les deux utilisent un corps de palpeur Renishaw RMP-60.
Les routines de palpage ont été programmées à l'aide du logiciel Inspection Plus de Renishaw, et le code résultant a été ajouté au programme de la machine aux emplacements appropriés. La routine de sondage initiale mesure des points sur l'orifice inférieur à l'intérieur du boîtier et l'ouverture à l'avant du boîtier pour définir l'axe central de la pièce. Les autres caractéristiques sondées incluent l'un des petits orifices près de la face pour définir l'orientation de rotation de la pièce et une paroi à l'intérieur de la bride latérale principale pour définir l'emplacement de l'axe Z de la pièce. Le module logiciel de compensation d'erreur de position de travail (WPEC) de Mazak permet aux écarts détectés par des calculs de position réelle dérivés de la routine de palpage initiale de se déplacer avec la pièce à travers les mouvements d'indexation de la broche. Après les routines de sondage initiales, un sondage supplémentaire est effectué pour confirmer l'emplacement des fonctions associées et des surfaces post-usinées.
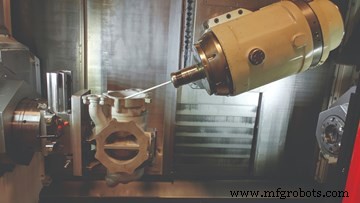
Pour sonder les fonctionnalités au plus profond du boîtier, LeanWerks utilise un stylet de 50 mm de long monté sur une rallonge de 200 mm.
Enfin, les opérations d'usinage en profondeur requises pour cette pièce et le matériau abrasif en aluminium ont conduit l'atelier à utiliser une technologie avancée d'outils de coupe. Pour ce travail, l'atelier utilise le système de porte-outils Rego-Fix powRgrip. Une alternative à l'ajustement par frettage, le powRgrip est un système mécanique à ajustement serré qui se compose d'un porte-outil, d'une pince de précision et d'une unité de serrage hydraulique de table compacte utilisée pour insérer la pince et l'outil dans le support. Selon Rego-Fix, le système est capable de générer des forces de serrage élevées tout en maintenant une lecture totale de l'indicateur inférieure à 0,0001 pouce. La rigidité de ce système améliore la durée de vie de l'outil et la précision de coupe.
Les outils de coupe utilisés pour ce travail doivent avoir des angles de coupe positifs élevés et fonctionner à des vitesses très élevées avec de faibles profondeurs de coupe. Des fraises en bout Garr Alumistar sont utilisées ainsi qu'une petite fraise à surfacer avec des plaquettes non revêtues, hautement polies et hautement positives.
LeanWerks prérégle également les outils pour ce travail à l'aide d'un prérégleur Speroni STP Magis 400 disponible auprès de Big Kaiser. Le préréglage permet non seulement le réglage externe des outils mais, plus important encore, aide à la qualification et au dépannage car il facilite l'inspection de l'arête de coupe, la validation de la forme des outils de forme et la mesure du faux-rond.
Tournant
Le processus développé par LeanWerks pour usiner ce travail de fonderie de précision sur son laminoir a amélioré le taux de production de 10 heures par pièce à moins de deux heures par pièce. En conséquence, l'atelier continue d'envisager d'autres moyens de maximiser les capacités de sa capacité existante de la même manière, tout en poursuivant des travaux dans diverses nouvelles industries.
Équipement industriel
- Qu'est-ce que l'usinage par jet abrasif et comment fonctionne-t-il ?
- Facteurs qui affectent le coût d'usinage CNC
- Les centres à deux broches tournent les deux extrémités des pièces en une seule configuration
- Limites de taille dans l'usinage CNC
- Produits de moulage et d'usinage intérieurs (Partie 3)
- Produits de moulage et d'usinage intérieurs (Partie 2)
- Comment réduire le coût des pièces d'usinage CNC ?
- Que signifie l'usinage CNC 5 axes ?
- Besoin d'une machine VMC 5 axes ?