8 procédures de sécurité critiques que les gestionnaires d'entrepôt doivent suivre
Un entrepôt qui fonctionne bien est très organisé et les opérations modernes deviennent de jour en jour plus efficaces. Une bonne gestion de la sécurité va bien au-delà des dangers de base connus et anticipe les défaillances potentielles dans n'importe quelle zone de l'entrepôt et à chaque opération. Le taux de décès dans les environnements d'entrepôt est près du double de la moyenne nationale basée sur les données de ces dernières années, et c'est certainement un domaine qui mérite le respect et la gestion avec un programme de sécurité robuste.
Selon l'OSHA, certaines des principales défaillances dans un environnement d'entrepôt qui ont entraîné des blessures étaient dues à des procédures inappropriées, à l'utilisation dangereuse de chariots élévateurs, à un empilement inapproprié des palettes, à une mauvaise conception de l'agencement de l'entrepôt et à des blessures causées par des mouvements répétitifs. Voici huit procédures de sécurité critiques que tout responsable d'entrepôt peut revoir et améliorer avec les meilleures pratiques pour se protéger contre ces zones de risque.
Protocoles de déplacement des véhicules sur le quai de chargement 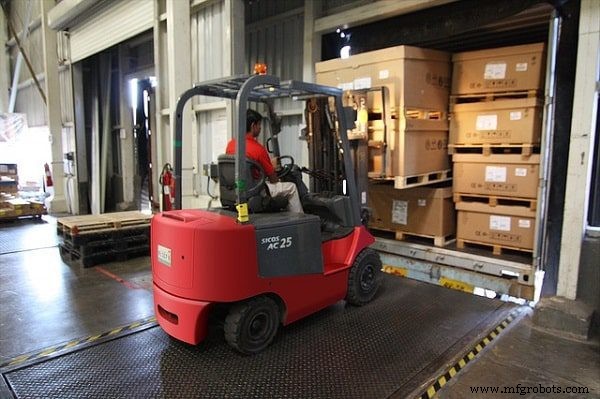
Le quai de chargement est une zone à fort trafic dans l'entrepôt qui voit beaucoup d'activité chaque jour avec des camions chargés et déchargés et des matériaux mis en scène pour l'expédition. Les travailleurs de la zone doivent être vigilants face à ces activités, car être coincé entre un chariot élévateur ou un camion et le quai de chargement pourrait être dévastateur. Les procédures suivies par vos opérateurs de chariots élévateurs pour la préparation, la réception et le chargement des matériaux sont essentielles pour garantir que les mouvements sont prévisibles et faciles à surveiller. Des limites de vitesse strictement appliquées, des panneaux d'avertissement clairs et le dégagement du quai et de la zone environnante devraient faire partie de toute formation.
Opération de chariot élévateur et risques de chute
Tout entrepôt respectable aura des procédures claires définies pour la conduite des chariots élévateurs et les opérations de base dans tout l'entrepôt. Mais un danger potentiellement négligé dans tout entrepôt concerne la panne des palettes pour exécuter les commandes. Cela peut être fait au niveau du sol, mais dans certains cas, il est plus facile d'amener un travailleur jusqu'à la palette avec un chariot élévateur ou avec des passerelles. Une protection adéquate contre les chutes comprend une plate-forme de chariot élévateur appropriée pour une personne si nécessaire, une couverture pour toute mezzanine et passerelles, et des rails adéquats sans espaces exposés inutiles.
Procédures de verrouillage et d'étiquetage des convoyeurs
L'automatisation dans l'entrepôt devient un élément standard de l'exécution des commandes et s'accompagne d'un certain nombre de pièces mobiles. Les tapis roulants, en particulier, peuvent avoir un impact incroyable sur l'efficacité et aider à déplacer les stocks dans l'ensemble de l'installation rapidement et de manière prévisible. Étant donné que les convoyeurs présentent un certain nombre de points de pincement potentiels et un risque de chute d'objets, il est important que des protections appropriées soient en place entre les travailleurs et l'équipement. De plus, les procédures de verrouillage et d'étiquetage utilisées par les employés pour la maintenance doivent être très robustes pour éviter tout contact inutile avec les convoyeurs en mouvement.
Stockage de palettes et rayonnages 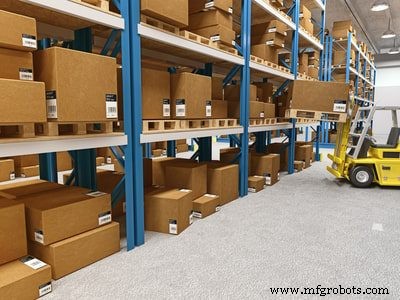
L'emballage et le stockage des palettes est une opération hautement manuelle qui nécessite beaucoup d'interaction entre le personnel, les palettes et les rayonnages. Il est possible d'éviter les risques de sécurité liés à la chute d'objets en s'assurant que vos procédures d'emballage de palettes tiennent compte des problèmes courants. Le personnel doit être formé pour emballer et sécuriser correctement les palettes, porter un équipement de protection individuelle (EPI), utiliser un modèle d'empilage recommandé et suivre les directives du fabricant pour une hauteur d'empilage et une capacité de poids sûres. Avoir des procédures qui demandent également aux employés d'inspecter les palettes pour des clous lâches ou d'autres problèmes et les dirige correctement pour éviter de marcher sur des rayonnages ou d'autres zones qui peuvent causer des dommages peut ajouter des niveaux de sécurité supplémentaires.
Mettre en place un système de numérotation des emplacements d'entrepôt
Un système de numérotation des emplacements d'entrepôt permet d'éviter la congestion inutile des allées en fournissant des indications claires pour diriger les associés vers les zones appropriées. En réduisant l'encombrement des allées, les associés ont un accès plus facile aux racks et autres zones de stockage, ce qui réduit également les accidents. Utilisez des panneaux de signalisation et des étiquettes d'entrepôt pour vous assurer que toutes les zones sont clairement marquées, y compris des panneaux et des étiquettes rétroréfléchissants pour les applications de numérisation à longue portée. Si vous ne savez pas quels panneaux et étiquettes d'entrepôt conviennent à vos diverses applications d'entrepôt, consultez notre guide en trois étapes pour choisir les bonnes étiquettes d'entrepôt. Pour obtenir des conseils sur la sélection des meilleures solutions de signalisation de haut niveau, consultez notre guide d'achat des panneaux d'entrepôt.
Utilisation appropriée des bornes de recharge
Les bornes de recharge pour chariots élévateurs utilisées dans la plupart des entrepôts semblent assez simples et, en ce qui concerne l'équipement, sont extrêmement sûres. La plupart des risques dans ces domaines proviennent de l'activité des employés dans la préparation de la charge et de l'entretien de la batterie. Interdire de fumer dans la zone est un contrôle de sécurité évident, mais il est également essentiel d'avoir une ventilation adéquate dans la zone et de positionner et d'appliquer correctement les freins aux ascenseurs avant de charger. Les procédures d'entretien des batteries doivent également être bien documentées et indiquer l'utilisation de l'EPI approprié, contenir un équipement adéquat pour l'entretien des batteries et fournir des instructions pour l'utilisation des installations de quasi-urgence telles que les douches oculaires en cas d'exposition à l'acide de la batterie.
Un plan HazCom approfondi et engageant
Les procédures qui traitent correctement des dangers potentiels sont moins utiles si elles ne font pas partie d'un plan global de communication des dangers (HazCom). Avoir un plan HazCom écrit est une exigence de l'OSHA, et il devrait inclure des informations de sécurité sur les étiquettes et les avertissements, les fiches de données de sécurité, la formation des employés et une liste des produits chimiques dangereux présents dans l'entrepôt. Bien que la création du plan soit une exigence de base, la meilleure pratique consiste à s'assurer qu'il est régulièrement examiné, tenu à jour et intégré à un programme de formation à la sécurité qui tient les employés informés.
Procédures et formation ergonomiques appropriées
Toute opération manuelle, du levage d'objets au fonctionnement des affichages numériques pour les équipements automatisés, peut entraîner un risque pour la sécurité ergonomique. Des procédures appropriées doivent indiquer clairement la charge de travail maximale de sécurité (SWL) de tout équipement et les limites de poids de manutention manuelle pour tout levage manuel. Éviter le besoin d'opérations manuelles grâce à l'automatisation et à l'assistance de l'équipement peut aider à réduire considérablement les risques ergonomiques, et maintenir l'équipement dans des paramètres de fonctionnement sûrs permet d'éviter les contraintes inappropriées et d'éviter les pannes dangereuses.
La sécurité fait partie du travail de chaque employé, et la direction de l'entrepôt a un rôle particulièrement important avec sa supervision des procédures qui dictent le travail dans tous les domaines. La prise en compte des risques majeurs et mineurs dans vos procédures donne à votre exploitation le meilleur potentiel pour éviter les accidents du travail et assurer la sécurité de votre personnel.
Technologie industrielle
- 10 règles de codage de la NASA pour la rédaction d'un programme de sécurité critique
- Équipement et politiques de sécurité dont aucun entrepôt ne devrait se passer
- Comment garantir la préparation aux urgences dans l'entrepôt
- 5 conseils de sécurité pour le levage par grue que tout grutier devrait suivre
- 7 indicateurs d'inventaire que les gestionnaires d'entrepôt devraient suivre
- Créer des procédures de sécurité pour les travailleurs et les techniciens
- Guide de sécurité des travailleurs pour l'industrie manufacturière
- 7 stratégies des grands responsables de la sécurité
- Considérations sur la sécurité incendie des machines CNC pour les responsables EHS