Inspection des soudures pour les assemblages critiques pour la sécurité
Les enjeux sont importants pour les constructeurs produisant des pièces automobiles. Les conducteurs et les passagers d'automobiles comptent sur la qualité de la soudure pour résister aux conditions pour lesquelles elle a été conçue. Une erreur non détectée au cours du processus de fabrication pourrait rendre une entreprise vulnérable ou pire, en particulier lorsque la pièce en question est "critique pour la sécurité" d'un assemblage.
Les sièges automobiles, par exemple, sont en contact direct avec les passagers; par conséquent, les soudures du siège sont considérées comme critiques pour la sécurité. Cette classification dicte un protocole particulier avant la production. Bien que les exigences OEM varient, elles ont tendance à être cohérentes avec les pratiques de l'industrie et sont mises en œuvre avec des différences mineures en fonction de la pièce, de l'usine et de l'équipement industriel utilisés. Voici les éléments de base d'un protocole :
Protocole de pré-production
- Configuration des paramètres - Établir les paramètres de soudage et vérifier leur acceptabilité. Cela peut être fait en coupant et en gravant des sections de soudure pour vérifier la pénétration de la soudure (15-20 %).
- Processus de publication - Un processus défini pour lancer ou approuver la production une fois que les éléments ci-dessus ont été vérifiés.
- Gestion du changement - Les changements de variables essentielles au-delà de certaines limites nécessitent une nouvelle validation via des tests de coupe et de gravure.
- Assurance qualité - Des pièces aléatoires peuvent être sélectionnées à partir de la production pour être coupées et gravées à une fréquence dictée par l'OEM.
Le soudage robotisé a permis d'améliorer considérablement la qualité des pièces en plaçant toujours les soudures au même endroit avec des paramètres de soudage programmés. Le respect des procédures ci-dessus aide à produire un produit soudé de qualité. Les équipementiers automobiles se sont concentrés sur les soudures critiques pour la sécurité, ce qui a entraîné la révision de certains éléments clés :
Protocole de fabrication
- Sécurité - Vérifiez que le personnel qualifié a accès à l'équipement et qu'aucune modification n'est apportée pour affecter négativement la qualité.
- Surveillance d'arc - La mise en place d'un système de surveillance d'arc peut aider à vérifier que le processus est sous contrôle et peut permettre de réduire la fréquence des essais destructifs. La surveillance de l'arc vérifie que les paramètres de soudage respectent les limites établies. Les soudures en dehors des limites sont signalées pour une inspection plus approfondie.
- Traçabilité - Suivez les modifications et les résultats de soudage, et conservez la possibilité d'enregistrer la date, l'heure et le numéro de série où les modifications de pièces ont eu lieu.
Chez Yaskawa Motoman, nous prenons le temps de nous renseigner sur les exigences de fabrication et de traçabilité de nos clients. Au fil des ans, nous avons développé plusieurs logiciels et améliorations d'E/S pour nos contrôleurs qui permettent aux fabricants d'effectuer des inspections de soudure fiables et traçables.
Fonctions de sécurité
Fonction de mot de passe
Le système de sécurité standard d'un mot de passe global à différents niveaux est pratique pour que plusieurs techniciens maintiennent plusieurs cellules robotisées dans une usine. Cependant, les mots de passe globaux risquent d'être partagés entre le personnel de l'usine, sans aucun contrôle sur ce qui est modifié et par qui.
La fonction de mot de passe du contrôleur DX de Yaskawa crée une base de données d'utilisateurs avec des mots de passe et des autorisations de niveau de sécurité. Les utilisateurs doivent se connecter pour faire fonctionner le robot ; la fonction de journalisation enregistrera le nom d'utilisateur et les modifications apportées.
Un logiciel a été ajouté au contrôleur DX200 pour permettre le contrôle à distance du mot de passe par PLC. Les ingénieurs de contrôle peuvent implémenter une logique pour utiliser des contrôles basés sur l'usine/la cellule pour administrer à distance les utilisateurs et les connexions en fonction de leurs badges d'employés internes ou de leur système de sécurité.
Niveaux de sécurité
- Niveau opérationnel - Par défaut, ce niveau de base permet à quiconque de se déplacer ou de parcourir un programme, mais pas de modifier les points ou les paramètres de soudure.
- Modifier le niveau - Permet à l'utilisateur de créer des programmes et de modifier les paramètres de soudage, mais n'autorise pas l'accès aux paramètres ou aux données de niveau supérieur.
- Mode de gestion - Fournit un accès complet aux paramètres et aux fonctions de maintenance.
- Niveau de sécurité - Permet d'accéder à la configuration et à l'administration des limites logicielles fiables de contrôle et de la logique de sécurité implémentée dans les contrôleurs DX (unité de sécurité fonctionnelle - FSU).
Ce que ces niveaux permettent aux utilisateurs de faire et d'accéder est défini par le système. Le niveau auquel la direction contrôle l'accès varie selon l'emplacement de l'usine.
Fonction de journalisation
De nombreux contrôleurs de robots plus récents sont livrés avec une fonction de journalisation standard qui garde une trace des modifications apportées au système par date et heure. Par exemple, un opérateur de l'équipe de jour peut voir si quelqu'un de l'équipe de nuit a effectué un changement. Le robot conserve un fichier local de la dernière série de modifications, de sorte qu'une sauvegarde de routine des données peut conserver un historique de l'activité de l'utilisateur. Le robot peut également utiliser la sécurité par mot de passe, obligeant les utilisateurs à se connecter pour apporter des modifications. Les noms d'utilisateurs sont également notés lorsque des modifications sont apportées.
Fonction d'édition de réapprentissage de sécurité
Le niveau d'exploitation ne permet pas aux utilisateurs de modifier les points du programme, mais certaines entreprises permettent aux opérateurs ou aux techniciens de premier niveau d'apporter des modifications mineures pour la variation de pièces. Safety Re-Teach permet aux utilisateurs du niveau de fonctionnement de modifier les points programmés dans une plage 3D définie par le mode de gestion. Ceci est normalement réglé sur quelques millimètres, et un gestionnaire peut limiter la quantité de changement d'angle pour la torche ou l'axe externe. Les utilisateurs du niveau opération ne peuvent pas modifier les paramètres de soudage, de sorte que les variables de soudage essentielles ne sont pas modifiées. Cela évite les tests destructifs répétitifs. Safety Re-Teach peut être activé par paramètre en mode de gestion sur n'importe quel contrôleur DX.
Surveillance des arcs
En tant que fournisseur de robots qui intègre des systèmes de soudage et s'appuie sur une coentreprise historique avec une entreprise de soudage, Yaskawa Motoman possède une expérience complète de la surveillance de l'arc. Nous avons conçu nos interfaces de soudage pour prendre en charge la capacité de surveillance de l'arc que les fabricants de sources d'alimentation peuvent avoir intégrée.
Les fonctions intégrées de Miller Insight Centerpoint™ et de Lincoln Electric Production Monitoring™ sont accessibles depuis le pendentif d'apprentissage du robot. WeldCube, de Fronius, communique directement avec la ou les sources d'alimentation. Yaskawa et Fronius travaillent pour que le résultat du moniteur soit signalé dans les bits d'état du soudeur.
Le défi de répondre aux mandats "critiques pour la sécurité" implique également de présenter clairement les résultats de soudage de la surveillance de l'arc de la source d'alimentation dans un format utile. Le meilleur format consiste à mettre en surbrillance les résultats du moniteur sur un schéma de pièce sur une IHM de cellule robotisée. De cette façon, les opérateurs du poste de soudage peuvent facilement repérer les irrégularités et réagir rapidement. Les opérateurs doivent inspecter visuellement les soudures signalées par le système, avec des résultats de surveillance hors plage, pour déterminer si les soudures sont conformes ou non conformes.
Alors que le contrôleur du robot peut signaler l'état du moniteur d'arc localement sur une IHM, les fabricants de sources d'alimentation proposent également un logiciel conçu pour rapporter les résultats du moniteur d'arc à distance, via un ordinateur personnel ou un logiciel basé sur le cloud.
Point central Miller Insight
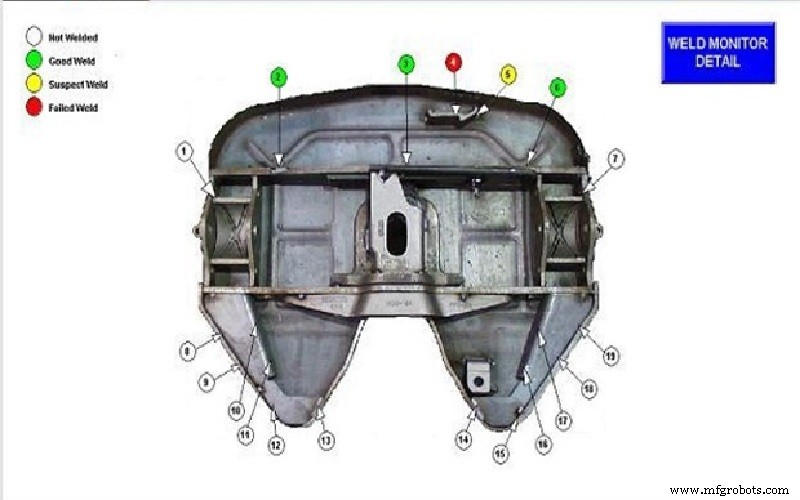
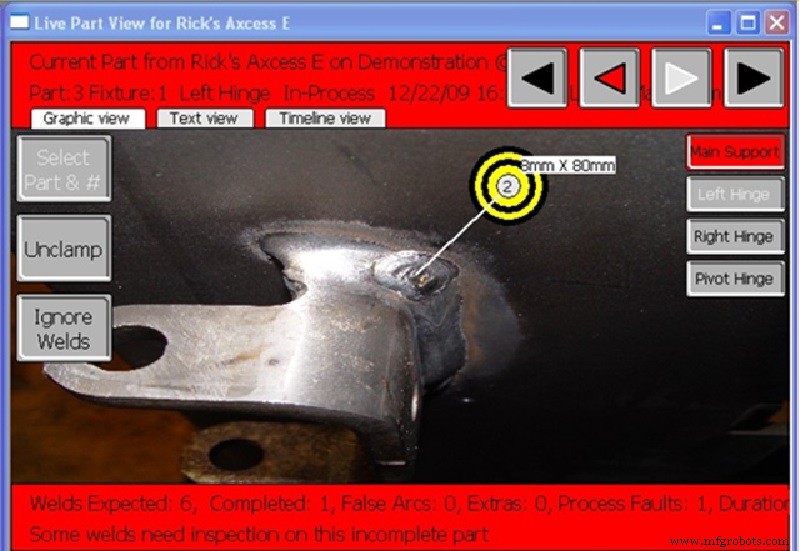
Traçabilité
Les équipementiers automobiles ne demandent pas seulement à leurs fournisseurs de fabriquer de bonnes pièces, ils leur demandent de mettre en place des systèmes de qualité pour fournir une "traçabilité" qui associera les résultats de soudage d'une pièce à son numéro de série. L'objectif est de pouvoir remonter jusqu'à un point de la production où les pièces étaient connues pour être conformes si une pièce non conforme est détectée.
Pour aider les fabricants à respecter la traçabilité, les données de surveillance de l'arc provenant de la source d'alimentation de soudage et du contrôleur de robot, ainsi que toutes les données spécifiques à la pièce qui doivent être accessibles à distance et finalement enregistrées dans l'automate, doivent être capturées et associées au numéro de série de la pièce. La façon d'harmoniser ce mashup de données - et la difficulté à le faire - dépend de ce qu'un fabricant est capable d'intégrer dès le départ, sans compromettre les protocoles de sécurité internes.
Variables de chaîne
Une astuce consiste à utiliser une fonction de création de variable de chaîne à partir du contrôleur du robot pour créer des identifiants uniques en tant que mécanisme de traçage. Il existe un mélange de variables utilisées pour stocker des nombres ou même des positions, et ces variables diffèrent en fonction du format et du nombre de chiffres. Les variables de chaîne peuvent être une combinaison de caractères ou de nombres jusqu'à 32 caractères. Ceux-ci peuvent être appelés pour afficher un message sur le pendentif ou pour d'autres usages.
Dans le cas de la production automobile, nous les avons utilisés pour contenir des informations sur le numéro de série de la pièce en cours de production. Les ingénieurs de contrôle peuvent utiliser la communication Ethernet pour "lire" les valeurs d'un automate ou d'un lecteur de code-barres et nous pouvons les transmettre à d'autres appareils.
E/S simultanées
Yaskawa Motoman utilise des E/S simultanées (CIO) pour effectuer un contrôle logique programmable et communiquer des données entre le robot et la source d'alimentation. Bien qu'il soit utilisé pour les réglages de soudage, il peut également être utilisé pour transmettre les résultats de la surveillance de l'arc entre la source d'alimentation et le robot. Pour la traçabilité, nous l'avons utilisé pour concaténer les résultats de soudure pour chaque emplacement de soudure et l'envoyer, avec le numéro de série de la pièce, à l'automate de l'usine pour un enregistrement de pièce. Nous prenons également le numéro de série de la pièce et l'envoyons à une poinçonneuse qui grave le numéro de série sur les pièces qui passent le moniteur de soudure.
Récemment, nous avons livré un système qui prendra les données d'inspection des soudures de Lincoln Electric Production Monitor et les présentera à l'opérateur dans une représentation graphique de la pièce. Il mettra en surbrillance, en vert ou en rouge, les résultats du moniteur à chaque emplacement de soudure - selon qu'ils se trouvent dans ou en dehors des limites. La surveillance CheckPoint™ (un logiciel externe) est conçue pour stocker les données dans le Cloud. Le CIO a permis un accès immédiat aux résultats du moniteur de production afin qu'ils puissent être présentés à l'opérateur pendant la production de la pièce.
Mise en œuvre
Le traitement des données de surveillance des soudures doit tenir compte du contrôle de la production, ainsi que des exigences de journalisation historique et de traçabilité. Les données capturées en cours de route sont utilisées différemment dans l'organisation, et ces besoins doivent être pris en compte pour chaque rôle à chaque étape.
Alors que l'utilisation des données de surveillance des soudures devrait permettre aux opérateurs sur le terrain de vérifier facilement la qualité des pièces, les données historiques peuvent être utilisées par le personnel de supervision pour administrer les plans de qualité et résoudre les problèmes. Les fonctions de sécurité rendent presque impossible de s'écarter des protocoles et paramètres établis, et la surveillance de l'arc fournit des indications graphiques en temps réel des soudures qui nécessitent une inspection plus approfondie.
Avec l'API comme destination ultime, les données de soudage spécifiques aux pièces sont enregistrées, stockées et traçables. L'harmonisation complète des données peut nécessiter une quantité considérable de travail initial; cependant, les résultats sont des clients confiants et une qualité améliorée qui peuvent également contribuer à assurer l'avenir de votre exploitation.
Robot industriel
- Température critique pour les supraconducteurs
- Pourquoi l'excellence en matière de fiabilité est impérative pour la sécurité
- 10 règles de codage de la NASA pour la rédaction d'un programme de sécurité critique
- Conseils de sécurité sur le lieu de travail pour les machinistes CNC
- Développer une nouvelle ère pour une sécurité alimentaire plus intelligente
- Un cas pour la mise à niveau des camions vieillissants
- Stratégies pour une bonne préparation de la soudure
- 5 conseils de sécurité pour la préparation d'équipement lourd
- Conseils de sécurité pour le soudage des réservoirs de carburant