Défauts de moulage sous pression : types, causes et comment les prévenir
Le processus de moulage sous pression consiste à appliquer une haute pression sur le métal en fusion, un processus similaire au moulage par injection de plastique. Cependant, le moulage sous pression est complexe et de nombreux facteurs peuvent compromettre la qualité des produits moulés sous pression. Les défauts de moulage sous pression sont désormais des préoccupations majeures en raison d'un contrôle lâche des matières premières, d'une planification inadéquate des processus et de la production, etc.
Par conséquent, une incapacité à résoudre correctement ces défauts de moulage affectera la qualité des produits finaux. Cependant, une chose essentielle à noter est que vous ne pourrez peut-être pas éviter tous les défauts pendant le processus de moulage sous pression . Dans de tels cas, les concepteurs peuvent être amenés à modifier la conception du moule.
Par conséquent, nous discuterons des différents types de défauts de boîtier de matrice dans cet article, en détaillant leurs causes, leurs solutions et comment les prévenir. Allons-y !
Défaut de moulage sous pression s :types, Causes , et solution s
Ici, nous couvrirons les différents défauts de moulage sous pression et les remèdes. Ces défauts surviennent souvent en raison de mauvais remplissages ou d'une phase de solidification inadéquate, et il existe deux grandes catégories :
Interne Défauts de moulage sous pression
Ces types de défauts de coulée sont difficiles à trouver et ils affaiblissent la résistance structurelle des composants. Les deux principaux défauts internes de moulage sont :
1. Porosité au gaz
Cela implique la formation de bulles dans le moulage après refroidissement. Vous verrez des porosités de gaz sous forme de structures rondes ou ovales sur le corps des pièces moulées sous pression, et elles ont également des surfaces lisses, blanches ou jaunes brillantes.
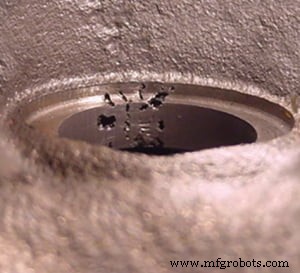
La plupart des métaux solides ne peuvent pas contenir une grande quantité de gaz dissous, mais les métaux liquides le peuvent. En conséquence, le gaz dans le métal solide forme des vides ou des bulles dans la fonte en refroidissant. Cela se produit souvent pendant la phase de solidification et vous remarquerez peut-être des trous dans le moulage. Selon la gravité de la porosité du gaz, cela peut entraîner d'autres types de défauts et augmenter les taux de rebut.
Causes :
- Libération d'hydrogène à partir d'alliages métalliques en fusion – Des températures de fusion plus élevées entraînent souvent une plus grande solubilité de l'hydrogène dans les alliages métalliques en fusion. Le refroidissement et la solidification impliqués dans le moulage sous pression réduisent la solubilité de l'hydrogène et le libèrent du métal fondu. En conséquence, des porosités de gaz se produisent.
- Gaz impliqués dans le processus de remplissage des alliages métalliques - Le processus de coulée sous pression consiste à remplir un alliage métallique fondu dans des matrices à haute vitesse et à haute pression. Par conséquent, des turbulences peuvent se produire si l'alliage liquide ne peut pas s'écouler de manière stable et ordonnée, ce qui entraîne des porosités de gaz.
- Gaz provenant des agents de démoulage – Les agents de démoulage se décomposent généralement et libèrent des gaz lors du chauffage par l'alliage métallique en fusion. Par conséquent, une volatilisation des gaz peut se produire en raison de l'utilisation excessive d'agents de démoulage.
Solution :
- Contrôler le processus de fusion en faisant fondre la matière première sous vide sous flux ou autour d'un gaz à faible solubilité pour empêcher l'air d'atteindre le métal en fusion.
- Assurez-vous d'avoir un lingot d'alliage métallique propre et sec.
- Utilisez des paramètres de moulage sous pression discernables, y compris la vitesse d'injection.
- Une longueur de cheminée et de canaux suffisante aidera l'alliage fondu à s'écouler de manière stable et à évacuer facilement les gaz.
- Sélectionnez des agents de démoulage de haute qualité et utilisez-en une quantité raisonnable.
2. Porosité de retrait
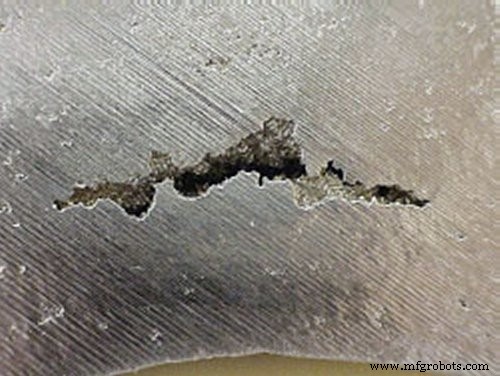
La porosité de retrait se forme pendant le processus de refroidissement et de solidification de la coulée, et les alliages métalliques rétrécissent lors du refroidissement. Par conséquent, il y a une forte possibilité que ce défaut se produise sans précautions adéquates. Cependant, cela devient un défaut lorsqu'un rétrécissement irrégulier déforme la forme ou crée des trous dans le moulage.
La porosité de retrait peut se produire sous forme de retrait ouvert, de gauchissement et de retrait fermé, affectant la contrainte du métal. Vous verriez ce défaut comme des bords anguleux, et ils peuvent également être accompagnés de fissures ou de fractures dendritiques.
Causes :
- Conception déraisonnable du système de refroidissement.
- Ouverture du moule trop tôt.
- Utilisation d'une température de coulée extrêmement élevée.
Solution :
- Améliorer la structure globale de la coulée.
- Reconcevoir le système de fonctionnement (porte) pour avoir des colonnes montantes qui permettent un flux continu de métal en fusion.
- Insérez des refroidisseurs internes, des serpentins de refroidissement ou des nervures pour augmenter la dissipation de la chaleur.
- Ajustez la température de coulée pour réduire les déficits de volume totaux.
3. Inclusions
Ce sont des trous de forme irrégulière à l'intérieur du moulage ou sur sa surface. Avec les inclusions, il y a des particules indésirables de sable, de matériau, d'écume ou de produit de désoxydation dans la coulée de métal. Les inclusions peuvent affecter les fonctions mécaniques de la coulée de métal et peuvent être identifiées par rayons X ou UT.
Causes :
- Impuretés du métal dues à une mauvaise purification ou à la pollution par les ordures.
- Faible pureté de la charge du four.
- Interaction du métal avec l'atmosphère environnante ou avec la surface du moule.
- Inclusion de trop de graphite dans les agents de démoulage.
Solution :
- Assurez-vous que la charge du four est pure.
- Purification appropriée du liquide métallique avec élimination complète des scories.
- Nettoyez correctement la cavité de la matrice et les louches.
- Si les agents de démoulage contiennent du graphite, assurez-vous que le mélange et l'agitation sont uniformes.
Superficiel Mourir Diffusion Défauts
Ces types de défauts de coulée sont souvent visibles et détruisent la surface du composant et sa qualité esthétique. Ils incluent :
1. Fissures
Les fissures se produisent lorsque le matériau se brise en raison de contraintes à l'intérieur et à l'extérieur du matériau. Ils apparaissent sous forme de motifs irréguliers ou linéaires sur les surfaces de moulage sous pression. La première fissure se produit pendant le processus de refroidissement et de solidification.
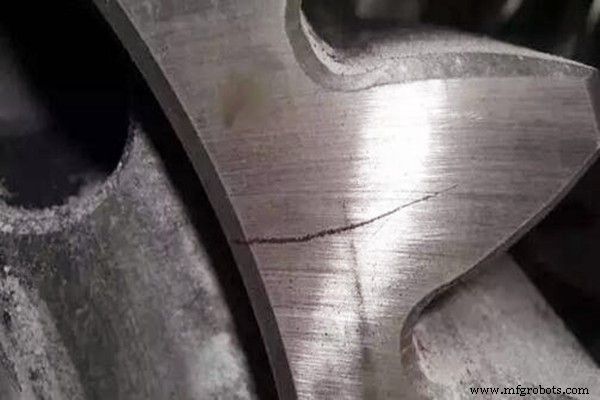
Cela se produit parce que les matériaux à géométrie de cavité ne peuvent pas rétrécir dans leur état naturel. Par conséquent, les contraintes résiduelles génèrent des fissures ou des déformations dans le moule. La deuxième forme de fissure se produit en raison d'une force externe sur le composant. Les efforts proviennent de la phase de coupe ou du moule lors de l'éjection de la pièce.
Les fissures sont le résultat d'éléments d'alliage inappropriés contenus dans l'alliage de moulage. Ainsi, vous souhaitez utiliser les éléments d'alliage corrects lors de la fusion. De plus, l'optimisation de la structure du composant et l'assurance d'une épaisseur de paroi uniforme empêcheront ce défaut. Une éjection équilibrée des pièces moulées sous pression est également une bonne solution à ce défaut de moulage.
2. Fermeture à froid
Ici, il y a des lignes linéaires irrégulières sur la surface du plâtre. Les lignes sont étroites et petites, avec des bords lisses qui peuvent s'étendre avec des forces externes. Les défauts de fermeture à froid dans le moulage sous pression se produisent lorsqu'il y a une fusion incorrecte de deux fronts de métal liquide dans la cavité de la matrice. Par conséquent, il reste un point faible sur le composant.
Une faible température de fusion, une faible vitesse d'injection, une conception déraisonnable du système d'injection et une mauvaise fluidité de l'alliage sont quelques-unes des causes de la fermeture à froid. Des inspections visuelles vous aideront à découvrir ce défaut. Un bon moyen d'éviter la fermeture à froid consiste à augmenter les températures du moule et du métal en fusion. Vous pouvez également modifier la taille et la position du jeu tout en augmentant la vitesse du piston.
3. Cracks réseau
Les fissures du réseau apparaissent sous forme de dépressions et de saillies en forme de cheveux ou de filets à la surface de la pièce moulée sous pression. La saillie de la matrice s'étend avec une augmentation des temps de moulage sous pression. Cela peut se produire en raison d'une cavité de matrice rugueuse, d'une température de remplissage élevée, d'un matériau de coulée inapproprié et de traitements thermiques inappropriés.
Votre matériau de moulage sous pression et votre processus de traitement thermique doivent être adéquats pour éviter ce défaut. De plus, vous devez assurer un chauffage uniforme et suffisant du moule pour éliminer les contraintes internes. L'équilibre thermique de la cavité de la matrice doit être assuré par des méthodes de refroidissement appropriées. Vous voulez un bon niveau de rugosité pour le processus de moulage sous pression. Par conséquent, vous devez polir régulièrement la cavité de la matrice et le système de déclenchement.
4. Traces et soudure
Les traînées sont des défauts qui se produisent parallèlement à la direction de l'ouverture de la matrice. Ils apparaissent comme des rayures en forme de bandes sur la surface des composants de moulage. La soudure résulte d'un collage anormal de la cavité de la matrice et de l'alliage métallique. Il apparaît comme des matériaux excédentaires ou manquants sur certaines zones du composant.
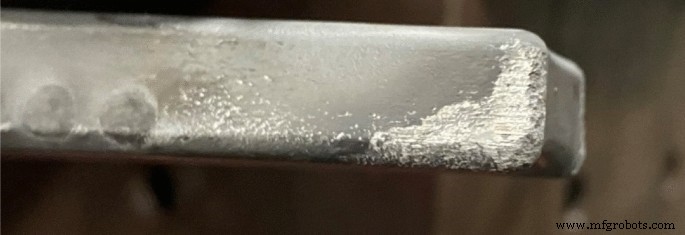
Ces défauts de moulage sous pression sont causés par un alliage fondu surchauffé, des dommages à la surface de la cavité de la matrice ou des angles de dépouille insuffisants. Un mécanisme d'injection déraisonnable et une mauvaise qualité de l'agent de démoulage peuvent également être à l'origine de ces défauts.
Ainsi, il serait préférable d'utiliser des agents de démoulage de haute qualité et d'optimiser votre mécanisme d'éjection. S'il y a des dommages sur la surface de la cavité de la matrice, assurez-vous d'effectuer les réparations appropriées. Vous pouvez également ajuster la direction de la porte pour maintenir les noyaux de matrice dans le bon état.
5. Clignote
Ce défaut de moulage sous pression donne des formes de tôle minces et irrégulières sur la pièce moulée sous pression. Certaines de ses causes incluent une vitesse d'injection élevée, une température de limage élevée, des déchets sales sur la surface de séparation et une force de serrage insuffisante de la matrice. Par conséquent, vous devez utiliser les paramètres de traitement corrects et assurer un entretien régulier des matrices pour éviter ce défaut.
6. Blister s
Le moulage sous pression consiste à comprimer l'air dans la machine et à éjecter la pièce du moulage avec une soupape à vide, un trop-plein ou un évent. L'air laissé à l'intérieur se dissoudra dans le métal fondu avec une distribution uniforme. Les turbulences concentrent l'air, provoquant une cavité à haute pression - des cloques.
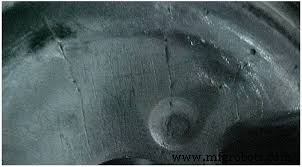
Ce défaut de moulage sous pression reste caché si la température du composant est basse, réduisant ainsi la résistance du composant. Dans un cas où la température est élevée, vous remarquez des bulles à la surface. Par conséquent, vos paramètres de moulage sous pression doivent être adéquats. Vous devez également optimiser votre système de fermeture pour assurer une bonne performance de ventilation.
7. Déformation
Cela se produit lorsque la forme de la pièce finale ne correspond pas au dessin. La déformation se produit en raison d'un retrait incorrect de la porte, d'une mauvaise conception de la coulée, d'une ouverture prématurée du moule, de mécanismes d'éjection inadéquats et de traînées lors de l'éjection de la coulée.
Par conséquent, vous devez vous assurer de choisir un mécanisme de retrait de porte approprié. De plus, ajustez le temps d'ouverture du moule pour assurer la rigidité. L'optimisation des conceptions de moulage structurel et la suppression des facteurs de démoulage défavorables aident également à prévenir ce défaut.
8. Marques de flux
Ce sont des rayures et des lignes non directionnelles sur la surface de la pièce moulée sous pression qui diffèrent en couleur de la base du moulage. Le métal liquide pénétrant dans la cavité forme souvent une fine couche incomplète qui peut être remplie de métal en fusion. Ce remplissage laisse des traces sur le composant.
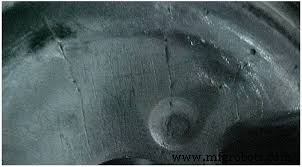
D'autres causes de marques d'écoulement comprennent une faible température de matrice, une faible pression de remplissage, un excès de lubrifiant ou d'agent de démoulage et une petite section transversale. Par conséquent, vous devez augmenter la température de la matrice, régler la vitesse d'injection, la section transversale et d'autres paramètres de coulée.
9. Remplissage court
Dans ce défaut de moulage sous pression, certains matériaux peuvent manquer sur la surface du moulage. Cela se produit en raison d'une mauvaise fluidité de l'alliage métallique, d'une faible température de remplissage, d'une faible pression d'injection, de mauvaises conditions de remplissage et d'une utilisation excessive de lubrifiants.
Un bon moyen d'éviter un remplissage trop court consiste à choisir le bon alliage métallique. Il serait utile d'augmenter également la température de la filière et de remplissage ainsi que la vitesse et la pression d'injection. L'amélioration de la conception du système d'obturation et de la déviation du flux de liquide métallique contribuera également à éviter les remplissages trop courts.
10. Laminage s
Les stratifications proviennent du chevauchement de deux couches séparées lors du processus de remplissage. Ces défauts du moulage sous pression sont difficiles à détecter. Ils apparaissent après des opérations de pré-finition comme le sablage et le culbutage.
L'impact entre la coulée et les inserts lors de ces phases provoque le soulèvement des couches de zinc. En conséquence, la saleté et les fluides peuvent être cachés au milieu de ces couches. Les substances cachées peuvent apparaître sur la surface pendant les processus de finition de surface comme la galvanisation et la peinture, ce qui aggrave le résultat.
11. Éviers
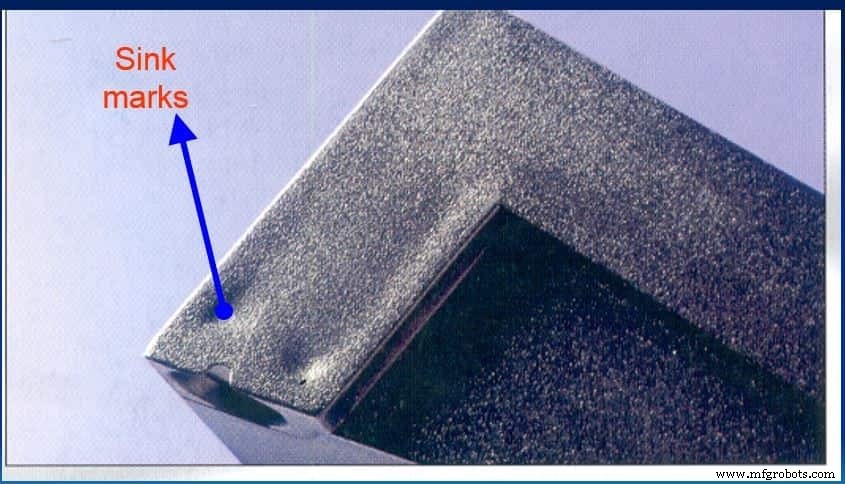
Ce sont des dépressions à la surface de la pièce coulée ainsi que les zones à parois épaisses. Les puits sont causés par la faible pression de l'injection, l'épaisseur inégale de la paroi coulée, la surchauffe partielle de la matrice et les temps de maintien de la pression courts.
Vous pouvez garantir une épaisseur de paroi uniforme en optimisant les conceptions de moulage. De plus, vous pouvez éviter les puits en améliorant les performances de ventilation de la cavité de la matrice et en augmentant la pression d'injection. L'augmentation du temps de maintien de la pression est également une méthode efficace.
Conseils pour éviter Défauts de moulage sous pression
Les défauts de moulage sous pression se produisent pour diverses raisons. Un bon guide de conception de moulures sera efficace. Cependant, les conseils de "premier principe" suivants vous aideront à éviter ces défauts :
Un système de notation efficace
Un système de notation efficace vous indiquerait si vous réduisez les défauts ou si la situation empire. Le système de notation vous aidera à savoir si vous avez besoin de corrections. Ceci est important car vous voulez vous attaquer au défaut avant qu'il n'atteigne le niveau d'apogée.
La porosité au gaz, les retraits et les inclusions sont des défauts majeurs du moulage sous pression qui nécessitent un jugement pour connaître leur gravité. Comme vous ne pouvez pas améliorer quelque chose sans le mesurer, vous avez besoin d'un système de notation efficace pour éviter ces défauts.
Épaisseur de paroi correcte
L'épaisseur de la paroi joue un rôle important dans les défauts de moulage, différentes parois produisant des résultats différents. Une paroi mince fera geler l'alliage métallique, augmentant la déformation. L'épaisseur de paroi minimale pour le magnésium et l'aluminium est de 1,5 à 2,5 mm et de 1,0 mm pour le zinc.
Temps de remplissage correct
Le temps de remplissage commence lorsque l'alliage atteint la porte et se termine lorsque la cavité est remplie. Voici un guide du temps de remplissage maximum pour la plupart des castings :
Alliage | Parois fines <2 mm | Mur moyen >2 mm |
Aluminium Environ 2 kg | 0,09 seconde | .1 seconde |
Zinc Environ 1,4 kg | 0,03 seconde | 0,05 seconde |
Magnésium Environ 1 kg | .02 secondes | .03 secondes |
Vous pouvez prédire le bon temps de remplissage en utilisant le calcul PQ2. Le calcul prédit les changements de vitesse de porte et remplit le temps en modifiant l'un de ces éléments :
- Zone du portail
- Taille du piston
- Pression hydraulique machine
- Réglage de la vitesse du piston
Modèle de flux de métal droit
Le facteur clé dans la conception des vannes est le flux de métal, qui est fonction des normes de conception. Ces étapes simples vous aideront à utiliser le bon modèle de flux de métal :
- Utilisez le calcul PQ2 pour déterminer la taille de la porte et le piston, assurez-vous d'utiliser le temps de remplissage, la vitesse de la porte et la pression de la cavité corrects
- Divisez ensuite le casting en zones
- Divisez les portes pour que chaque zine soit rempli en même temps
- Flux à travers le casting
- Évitez de mélanger les défauts de moulage
La bonne température de matrice
Il faut utiliser la bonne température pour éviter les défauts de coulée. Les basses températures refroidissent le métal liquide et peuvent affecter la surface en augmentant la partie solidifiée. Un pourcentage élevé de métal solide rend le flux rigide et ne se mélange pas bien. En conséquence, il peut y avoir un écoulement à froid, entraînant des défauts.
Travailler avec RapidDirect à Éviter Défauts de moulage sous pression
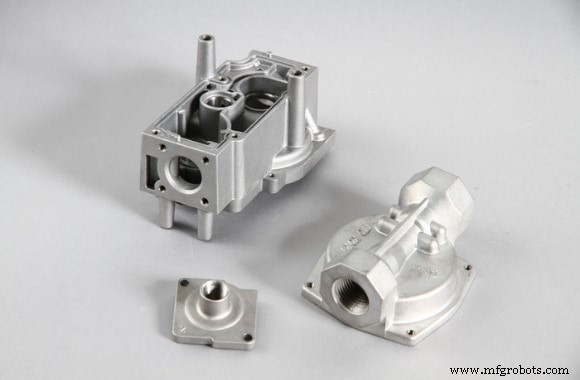
Comprendre les défauts de moulage sous pression et leur cause est essentiel pour garantir la qualité des pièces. Cependant, il y a beaucoup plus à savoir, il est donc préférable de s'associer à un expert en moulage sous pression. RapidDirect offre les meilleurs services de moulage sous pression personnalisés avec un matériel de premier ordre, des techniciens professionnels et des processus de pointe.
Nous abordons votre projet dans le but d'assurer la meilleure qualité. Nos machinistes surveillent également en permanence le processus. Ainsi, nous sommes en mesure d'éliminer les processus inefficaces et d'utiliser uniquement des techniques de haute qualité. Téléchargez votre fichier de conception aujourd'hui et obtenez un devis instantané.
FAQ
Comment pouvez-vous réduire les défauts de casting ?Vous pouvez éviter les défauts de diffusion en utilisant un système de notation efficace. Utiliser la bonne épaisseur de paroi. la température de la matrice et le modèle d'écoulement du métal sont également des solutions efficaces.
À quoi sert le moulage sous pression ?Le processus de moulage sous pression est populaire pour la fabrication de composants dans l'industrie automobile. Les concepteurs et les fabricants utilisent également ce processus pour fabriquer de la quincaillerie décorative et d'autres composants plus petits.
Comment supprimer la porosité des pièces moulées ?Une bonne conception de moule vous aidera à vous débarrasser de la porosité des gaz. Vous pouvez également éliminer ce défaut en ajoutant de l'azote au métal d'aluminium avant de couler. Une longueur de cheminée et de canal suffisante assurera un flux d'alliage stable pour évacuer facilement les gaz.
Technologie industrielle
- Les 4 principaux défis de la fabrication aux États-Unis et comment les surmonter
- 7 défis de la numérisation de la fabrication et comment les surmonter
- Sept défis de livraison du dernier kilomètre et comment les résoudre
- Quatre types de cyberattaques et comment les prévenir
- 4 principales causes de défaillance d'appareillage de commutation et comment les éviter
- Défauts de fonderie :types, causes et remèdes
- Comment prévenir les défauts non mouillants
- Principales causes de panne de machine et comment les prévenir
- Les pièges de la protection des machines et comment les éviter