Fabrication de nanofibres hélicoïdales CA/TPU et son analyse de mécanisme
Résumé
Pour explorer le mécanisme de l'acétate de cellulose (CA)/polyuréthane thermoplastique (TPU) sur la fabrication de nanofibres hélicoïdales, une série d'expériences ont été menées pour trouver les conditions de filage optimales. Les résultats expérimentaux montrent que le système CA (14 % en poids, DMAc/acétone, rapport en volume 1/2)/TPU2 (18 % en poids, DMAc/acétone, rapport en volume 3/1) peut fabriquer efficacement des nanofibres hélicoïdales par co-électrofilage. Nous nous concentrons sur l'interaction interfaciale entre les composants polymères induits par la structure du polymère et les propriétés intrinsèques, y compris les propriétés de la solution, la liaison hydrogène et le comportement de miscibilité des deux solutions. La calorimétrie différentielle à balayage (DSC) et la spectroscopie infrarouge à transformée de Fourier (FTIR) sont utilisées pour étudier l'interaction interfaciale entre les deux phases du système polymère. Les résultats de l'analyse fournissent l'explication des résultats expérimentaux selon lesquels le système CA/TPU a le potentiel de produire efficacement des nanofibres hélicoïdales. Cette étude basée sur l'interaction interfaciale entre les composants polymères donne un aperçu du mécanisme de formation des fibres hélicoïdales CA/TPU et introduit un choix plus riche de matériaux pour l'application des fibres hélicoïdales.
Contexte
Les structures hélicoïdales avec un large spectre d'applications dans les domaines des capteurs nanométriques, des matériaux de filtration, des absorbants d'huile, des cellules solaires, etc. . L'introduction d'une structure hélicoïdale dans les micro/nanofibres peut améliorer la résilience et la flexibilité des fibres, et cette structure tridimensionnelle (3D) des hélices peut fournir au tapis de fibres une plus grande porosité [3]. Les structures hélicoïdales peuvent être trouvées dans de nombreux systèmes naturels tels que les vrilles végétales et la laine fine, qui sont considérées comme la conséquence de différents retraits (ou extensions) et entraînent un enroulement forcé de la structure [4]. Zhang et al. [5] se sont concentrés sur la formation, la structure et la fonction des nanoarchitectures chirales les plus courantes et ont exploré comment les molécules peuvent former des nanoarchitectures chirales hiérarchiques. Le mécanisme d'une telle déformation asymétrique doit également être utilisé pour générer une courbure des fibres. Le co-électrofilage, comparé aux autres méthodes, telles que le dépôt chimique en phase vapeur [6], le sol-gel [7] et l'hydrothermie [8], est une méthode simple et efficace pour générer des fibres composites avec des types de morphologies au niveau micro- et nanométriques.
À l'aide de la technique de co-électrofilage, plusieurs chercheurs ont réussi à préparer des nanofibres hélicoïdales tridimensionnelles à partir de solutions à deux composants. Lin et al. [9] ont obtenu des fibres de laine biomimétiques à l'échelle nanométrique par électrofilage de PAN et de TPU en utilisant un arrangement de co-électrofilage côte à côte. Chen et al. [10] ont utilisé trois types de filières de co-électrofilage pour produire des nanoressorts à partir de PU et de Nomex. En utilisant l'électrofilage côte à côte, Zhang et al. [11] ont rapporté la génération de fibres avec des morphologies bouclées et hélicoïdales à partir de poly(téréphtalate d'éthylène glycol) (HSPET) et de poly(téréphtalate d'éthylène propanediol) (PTT). Dans les recherches ci-dessus, les nanofibres hélicoïdales obtenues sont décrites comme des structures tridimensionnelles et en forme de ressort avec des diamètres d'hélice nano à micrométrique. Les auteurs ont attribué la génération de fibres hélicoïdales au fait que les deux composants impliqués dans le co-électrofilage présentent des retraits différents après l'électrofilage. Mais il n'y a pas d'analyse et d'explication détaillées du mécanisme de formation des fibres hélicoïdales. Sur la base du concept selon lequel un élastomère et un polymère rigide en co-électrofilage peuvent introduire une contrainte longitudinale et entraîner des formes enroulées des fibres bicomposantes, nos études précédentes [12] ont rapporté la fabrication de nanofibres hélicoïdales par co-électrofilage. Nous avons comparé trois systèmes de composants, Nomex/TPU, PAN/TPU et PS/TPU, qui représentent trois types d'arrangements de composition polymère dans le co-électrofilage, et avons exploré le rôle de la rigidité de la chaîne polymère, de la miscibilité et de la liaison hydrogène sur la formation de fibres hélicoïdales. Il a été vérifié expérimentalement que le système Nomex/TPU peut former de fines fibres hélicoïdales. Cependant, le Nomex est un polymère non hydrophile, ce qui a limité son application dans les tissus biologiques et la filtration par adsorption [13].
Par conséquent, dans cet article, basé sur les recherches précédentes, nous discutons plus en détail des conditions de co-électrofilage CA/TPU et analysons son mécanisme de formation de fibres hélicoïdales. Nous préparons les nanofibres hélicoïdales composites avec CA, le composant rigide et TPU, et le composant élastomère par technique de co-électrofilage. Dans la partie expérimentale, nous avons mené des expériences de simple filature de CA et TPU, respectivement. Différentes concentrations de solution de CA et systèmes de solvants (rapport de volume de DMAc à l'acétone) ont été appliqués pour trouver les conditions de traitement des fibres de CA fines. Et dans le système de filage TPU, nous avons essayé deux systèmes de solvants, TPU1 (DMAc/THF, rapport en volume 3/1) et TPU2 (DMAc/acétone, rapport en volume 3/1), qui permettent une tension interfaciale inférieure avec la solution CA. Ensuite, CA avec différentes concentrations de LiCl et TPU de différents systèmes de solvants ont été menées pour faire des expériences de co-électrofilage, respectivement. Dans la section de discussion, nous nous concentrons sur l'interaction interfaciale entre les composants CA et TPU induite par différentes structures polymères et propriétés intrinsèques, y compris les propriétés de la solution, la miscibilité et la liaison hydrogène des deux solutions. Des techniques thermiques et spectroscopiques, notamment DSC et FTIR, sont utilisées pour étudier le comportement d'interaction de la paire CA/TPU. Cette étude donne un aperçu de la formation des fibres hélicoïdales CA/TPU et présente un choix plus riche de matériaux pour l'application des fibres hélicoïdales.
Expérimental
Matériaux
Acétate de cellulose (CA, poudre blanche, M W = 100 W g/mol) a été acheté auprès d'Acros Organics. Le polyuréthane thermoplastique (TPU, Desmopan DP 2590A) provenait de Bayer Materials Science. N , N -diméthylacétamide (DMAc, 0,938-0,942 g/ml à 20 °C, tension superficielle 25,3 dyne/cm, tension de vapeur 0,17 kPa (20 °C)), acétone (0,788 g/ml à 20 °C, tension superficielle 18,8 dyne/ cm, pression de vapeur 24,64 kPa (20 °C)), tétrahydrofurane (THF, 0,887-0,889 g/ml à 20 °C, tension superficielle 28,8 dyne/cm, pression de vapeur 18,9 kPa (20 °C)) et chlorure de lithium anhydre (LiCl, M w =42,39 g/mol) ont tous été achetés auprès de Shanghai Chemical Reagents Co., Ltd., Chine. Tous ces matériaux ont été utilisés sans autre purification. Toutes les expériences ont été réalisées à environ 25 °C et 40 % ~ 50 % d'humidité relative.
Co-électrofilage
Une solution de CA avec différentes concentrations de CA et de LiCl a été préparée en dissolvant de la poudre de CA et du LiCl dans le mélange de solvants de DMAc et d'acétone. Une solution de TPU avec une concentration de 18 % en poids a été préparée en dissolvant des pastilles de TPU dans des mélanges de solvants de DMAc/THF (rapport en volume 3/1), appelés TPU1 et dans des mélanges de solvants de DMAc/acétone (rapport en volume 3/1), appelés comme TPU2. Toutes les solutions ont été agitées pendant 5 h à température ambiante et mises de côté pendant une nuit pour la préparation. Comme le montre la figure 1a, un système de co-électrofilage a été utilisé pour éjecter les solutions de polymère de noyau et d'enveloppe à travers une filière décentrée via des seringues et des pompes correspondantes. Une alimentation haute tension a été appliquée à la filière et au collecteur rotatif avec une vitesse linéaire de 14,24 cm/s. La figure 1b montre le mécanisme de formation des nanofibres hélicoïdales :le composant central impliqué dans la nanofibre présente un rétrécissement plus important que le composant de la coque, comme les vrilles végétales.
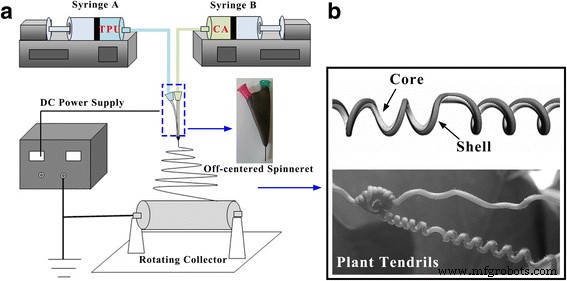
un Schéma du système de co-électrofilage décentré. b Mécanisme de formation des nanofibres hélicoïdales
Caractérisations
morphologie de la fibre
La morphologie des fibres noyau-coque résultantes a été observée au microscope électronique à balayage (MEB) (JSM-5600LV, Japon) après revêtement en or.
DSC
Les températures de transition vitreuse des mélanges ont été effectuées en utilisant un DSC de DSC-4000 dans une atmosphère d'azote avec température. La mesure a été effectuée à l'aide d'un échantillon de 5 à 10 mg sur une cellule d'échantillon DSC après que l'échantillon ait été rapidement refroidi à - 80 °C à partir de la masse fondue du premier balayage. La température de transition vitreuse a été obtenue en tant que point d'inflexion de la capacité thermique de saut avec une vitesse de balayage de 10 °C/min et une plage de températures de − 80~300 °C.
FTIR
Les spectres infrarouges ont été enregistrés sur un spectrophotomètre FTIR Bruker Vector 33, et 32 scans ont été collectés avec une résolution spectrale de 1 cm −1 . Le film utilisé dans cette étude était suffisamment mince pour obéir à la loi de Beer-Lambert. Les spectres IR enregistrés à des températures élevées ont été obtenus en utilisant une cellule montée à l'intérieur du compartiment à température contrôlée du spectromètre.
Les propriétés de la solution sont présentées dans le tableau 1. Des mélanges avec différentes paires de composants ont été préparés en mélangeant des solutions. Les mélanges ont été agités pendant 8 h et laissés s'évaporer lentement à température ambiante pendant 2 jours. Les films des mélanges ont ensuite été séchés à 90 °C pendant 1 jour pour assurer l'élimination totale des solvants.
Résultats expérimentaux
Pour explorer le mécanisme des fibres hélicoïdales CA/TPU et le rôle des effets de solvant, nous avons conçu des expériences en deux parties :la première partie a été réalisée pour sélectionner les paramètres de filage simples appropriés, et dans la seconde partie, l'expérience combinatoire :deux systèmes de composition polymère, CA/TPU1 et CA/TPU2, ont été étudiées.
La figure 2 montre les résultats des expériences d'électrofilage CA unique avec différentes concentrations de solution et systèmes de solvants dans les conditions de traitement d'une tension appliquée de 15 kV, d'une distance de travail de 10 cm et d'un débit de 0,2 ml/h. Le x -axis montre la concentration de la solution CA, et y -L'axe désigne le rapport volumique du DMAc à l'acétone. Nous avons constaté que sous la même concentration de solution CA, avec l'augmentation de la proportion d'acétone dans la solution CA, moins de billes se formaient sur les nanofibres CA. Cependant, au cours du processus expérimental, le CA formera un coagulum facilement apparu sur la pointe de l'aiguille, ce qui a entraîné une finesse de fibre inégale car la pression de vapeur (environ 24,64 kPa (20 °C)) de l'acétone est trop élevée. Au fur et à mesure que la concentration en CA augmente, les billes de filage se transforment en fibres homogènes, mais lorsque la concentration est trop élevée, des fuseaux commencent à apparaître sur les fibres. Compte tenu du processus de filage relativement stable, nous avons choisi une concentration de solution CA de 14 % en poids dissous dans le rapport volumique de l'acétone au DMAc de 2. Une autre note qui doit être soulignée est, afin de répondre aux exigences du filage de fibres hélicoïdales plus tard , lorsque nous avons ajouté du LiCl dans la solution CA, les fibres de filage uniques émergent sous forme de faisceaux et le processus de filage ne peut pas être effectué en raison de la conductivité élevée.
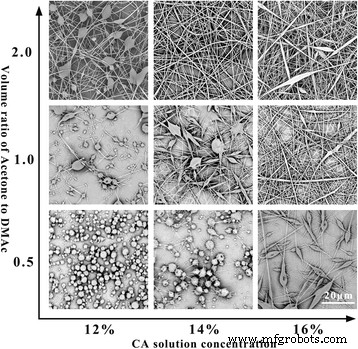
Images SEM d'expériences d'électrofilage unique CA de x -axe :concentration de la solution CA, de y -axe :rapport volumique du DMAc à l'acétone. La tension appliquée est de 15 kV, la distance de travail est de 10 cm et le débit est de 0,15 ml/h
La figure 3 montre les résultats des expériences d'électrofilage uniques de TPU1 et TPU2. Comme nous le savons tous, dans des champs électriques suffisamment puissants, des jets se produisent à la pointe des gouttelettes composées, auquel cas l'entraînement du fluide central entraîne la formation de fibres composées [14]. Ainsi, dans le co-électrofilage, la solution de coque agit comme une couche protectrice et entoure la couche centrale. Par conséquent, la solution de coque électrofilable est critique pour la formation de la structure bicouche, alors qu'il apparaît que les exigences pour la filabilité de la couche centrale en elle-même ne sont pas aussi critiques que les couches de coque. Dans cette étude, nous avons essayé une variété de concentrations de solution de TPU dans le processus expérimental. En raison de la solution TPU en tant que couche centrale avec une faible demande de filabilité et du co-filage approprié suivant requis, nous montrons ici uniquement la concentration de 18 % en poids d'images TPU à titre de référence. Dans notre étude précédente [15], nous avons utilisé le DMAc :THF = 3:1 comme solvant TPU1 pour filer des fibres hélicoïdales, comme le montre la figure 3a. On peut voir qu'il y a beaucoup de billes sur les fibres, bien que la morphologie de base des fibres puisse être facilement distinguée. Dans cette étude, nous avons utilisé le DMAc :acétone = 3:1 comme solvant du TPU2 à titre de comparaison. La figure 3b montre le filage unique de TPU2 ; comme nous pouvons le voir, il y a une forte adhérence des fibres entre les couches et presque aucune fibre ne se forme.
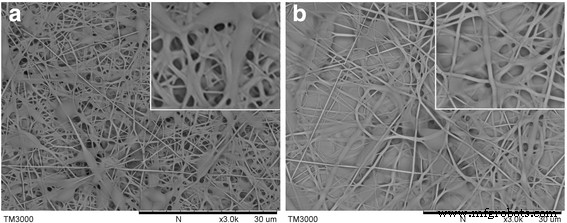
Images SEM des expériences d'électrofilage uniques de a 18 % en poids de TPU1 dans un rapport DMAc/THF de 3/1 en volume b 18 % en poids de TPU2 dans DMAc/acétone de rapport en volume 3/1. La tension appliquée est de 15 kV, la distance de travail est de 10 cm et le débit est de 0,15 ml/h
Dans la prochaine partie, nous allons co-spin CA ajouté avec un contenu différent de LiCl et TPU (inclus TPU1 et TPU2), respectivement. Ainsi, deux systèmes de composants, CA/TPU1 et CA/TPU2, ont été choisis dans le co-électrofilage. Bien que les résultats du TPU à filage unique ne soient pas satisfaisants, en tant que couche centrale du co-filage, il montrera une autre situation.
La figure 4 montre les résultats de 14% en poids de CA dissous par rapport en volume de DMAc à l'acétone de 0,5, avec une concentration de LiCl différente comme couche d'enveloppe et les deux solutions de TPU comme couche centrale. Comme nous pouvons le voir, lorsqu'il n'y a pas de LiCl ajouté dans la solution de CA, il n'y a pas de fibres hélicoïdales formées dans les deux combinaisons de TPU. Les fibres CA/TPU1 contiennent même quelques billes, tandis que la fibre CA/TPU2 est relativement uniforme, sans billes ni adhérence apparues entre les couches de fibres. Avec l'augmentation de la concentration de LiCl dans le CA, les deux systèmes TPU commencent à apparaître des fibres hélicoïdales. Lorsque la concentration en LiCl est faible (0,5 % en poids), les fibres de co-filage CA/TPU1 se présentent comme des faisceaux de diamètres non uniformes. Au fur et à mesure que la concentration de LiCl augmentait, le phénomène de groupage a disparu, mais il n'y a toujours pas autant de fibres hélicoïdales apparues. Lorsque la concentration de LiCl a atteint 2 % en poids, les fibres CA/TPU1 présentent un peu de fibres hélicoïdales, mais en raison de la conductivité élevée de la solution, la finesse des fibres n'est pas aussi uniforme. En revanche, les performances CA/TPU2 sont bien meilleures. Lorsque la concentration de LiCl est de 0,5 % en poids, les fibres CA/TPU2 deviennent pliées à partir de fibres droites. Lorsque la concentration de LiCl a atteint 1 % en poids, une quantité considérable de fibres hélicoïdales est observée dans la nappe de fibres CA/TPU2. Lorsque la concentration de LiCl a augmenté à 2 % en poids, les fibres hélicoïdales ont été étirées en raison de la conductivité excessive de la solution.
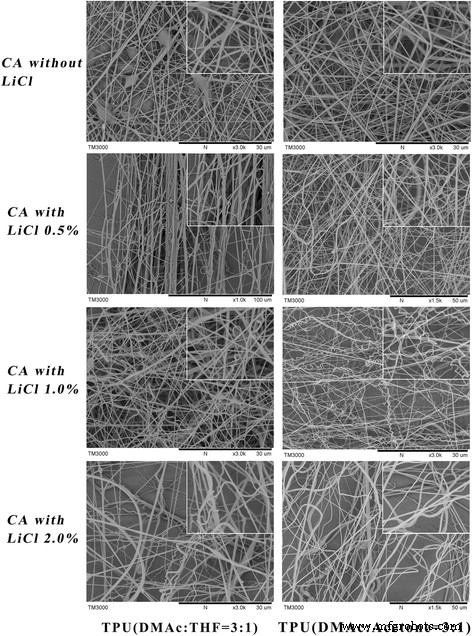
Images SEM de systèmes à deux composants de CA/TPU1 et CA/TPU2, dans lesquels le LiCl ajouté dans la solution CA est de zéro à 2 % en poids. La condition de traitement est d'une tension appliquée de 20 kV, d'une distance de travail de 15 cm et d'un débit de 0,15 ml/h pour les deux solutions de composants
Nous avons essayé diverses conditions de traitement pour les systèmes à deux composants, et les expériences montrent des résultats similaires selon lesquels les fibres CA/TPU2 peuvent fabriquer des structures hélicoïdales plus efficacement par rapport au système CA/TPU1. Seules quelques fibres présentent des structures hélicoïdales dans la nappe fibreuse CA/TPU1. Ces expériences démontrent que la concentration de LiCl et les systèmes de solvants jouent un rôle crucial dans la génération de fibres hélicoïdales. Dans cette étude, nous analysons en outre les résultats expérimentaux à travers les trois aspects ci-dessous pour expliquer le mécanisme de la formation des fibres hélicoïdales.
Résultats et discussion
Dans cet article, nous essayons d'explorer le mécanisme de filage hélicoïdal des fibres CA/TPU et de discuter de la manière dont les propriétés de la solution, la miscibilité et la liaison hydrogène des deux solutions affectent la morphologie des fibres résultantes.
Mécanisme des fibres hélicoïdales CA/TPU
Certains chercheurs ont signalé la solubilité de l'AC dans le système solvant LiCl/DMAc [16, 17]. Le mécanisme que nous pensons être opérationnel pour la dissolution de l'AC est illustré à la Fig. 5a. Le lithium-ion est associé au DMAc pour former une structure complexe de macrocations. Les ions chlorure sont associés aux hydrogènes hydroxyles du CA par des liaisons hydrogène. Par conséquent, on peut constater qu'après dissolution, les ions chlorure chargés négativement sont combinés avec les chaînes polymères de CA. Cela peut être utilisé pour illustrer le phénomène de la figure 4. Lorsqu'il n'y a pas de LiCl dans la solution CA, il n'y a pas de fibre hélicoïdale formée, mais avec l'augmentation de la concentration de LiCl, le système CA/TPU pourrait former des fibres hélicoïdales. Ici, l'additif LiCl n'augmente pas seulement la conductivité de la solution, mais permet également d'étirer efficacement la chaîne CA en raison des ions chlorure chargés négativement [18]. L'orientation étirée de la chaîne moléculaire est bénéfique pour augmenter la rigidité du segment de chaîne dure, ce qui augmente la différence de rigidité dans le segment mou, et est en outre bénéfique pour la formation de fibres hélicoïdales. Comme le montre la figure 5b, dans la solution CA, la force d'attraction générée entre les charges positives à la surface de la solution et les charges négatives portées par les ions chlorure dans la chaîne CA aide à la formation du jet composite CA/TPU et est censée être bénéfique pour le processus de co-électrofilage.
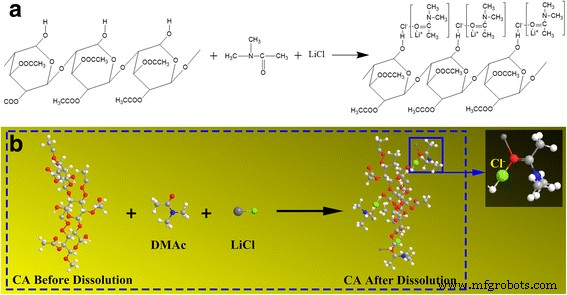
Mécanisme proposé pour la dissolution du CA dans le système solvant DMAc/LiCl :a formule moléculaire et b Structure moléculaire 3D
Propriétés de la solution
Comme nous le savons tous, les paramètres de solution du co-filage incluent la viscosité de la solution, la pression de vapeur du solvant, la tension interfaciale et la conductivité de la solution. Comme le montre la figure 2, lorsque l'on change le solvant THF par de l'acétone dans du TPU, le phénomène d'adhésion des fibres est réduit. Il convient de noter que les solvants utilisés par les différents types de TPU sont très importants. Les propriétés de la solution sont présentées dans le tableau 1. Comme indiqué, les solvants du TPU1 sont le DMAc et le THF (rapport en volume 3/1), tandis que les solvants du TPU2 sont le DMAc et l'acétone (rapport en volume 3/1), ce qui entraîne le propriétés de solution différentes. Comme nous pouvons le voir, la tension superficielle du TPU1 est d'environ 34,45 N m − 1 , tandis que le TPU2 est d'environ 25,34 N m − 1 , qui est beaucoup plus gros que le TPU2. La tension superficielle du THF est de 28,8 dyne/cm et la pression de vapeur est d'environ 18,9 (20 °C), tandis que la tension superficielle de l'acétone est de 18,8 dyne/cm et la pression de vapeur est d'environ 24,64 (20 °C). Si la pression de vapeur de la solution est trop élevée, le solvant s'évaporera trop rapidement et la solution ne pourra pas former un cône de Taylor, tandis que si elle est trop basse, les fibres atteindront la plaque de collecte humides et fusionneront pour former un film. Dans le filage coaxial, il est généralement avantageux d'utiliser des solvants (ou des mélanges de solvants) avec des pressions de vapeur différentes pour éviter l'effondrement des fibres [19].
En outre, la miscibilité de la solution entre le noyau et la coque est un autre facteur important. Comme le montre la littérature [20], lorsqu'il est utilisé avec le même solvant dans la solution de noyau et d'enveloppe, il permet une tension interfaciale inférieure, ce qui est important pour que le polymère ne précipite pas à l'interface fluide près de la buse. Comme le montre le tableau 1, les solvants de la solution CA sont le DMAc et l'acétone (rapport en volume 1/2), qui sont similaires au solvant de TPU2 et ont entraîné une tension interfaciale similaire entre les interfaces de la solution CA/TPU2. Cela explique également les résultats selon lesquels les fibres CA/TPU2 peuvent fabriquer des structures hélicoïdales plus efficacement que le système CA/TPU1 de la figure 4. En général, la propriété de solvant entraînera un changement considérable dans les propriétés de la solution de filage, affectant ainsi le composite. morphologie des fibres. Cependant, outre la propriété de solution, les performances du matériau polymère ont également une influence importante sur la formation de fibres hélicoïdales.
Liaison hydrogène dans les mélanges
Dans nos recherches précédentes, nous avons constaté qu'aucun composant polymère avec une rigidité différentielle ne peut former des fibres hélicoïdales, par exemple, les systèmes PAN/TPU et PS/TPU ne peuvent pas former de fibres hélicoïdales, alors que le système Nomex/TPU le pourrait. L'une des raisons importantes est que les liaisons hydrogène entre les systèmes Nomex/TPU contribuent à augmenter l'interaction de l'interface de solution.
La figure 6 montre des spectres infrarouges compris entre 500 et 4 000 cm −1 du système CA/TPU. La figure 6a montre une bande nette centrée à 1 250 cm −1 pour le coagulum CA pur, correspondant au –O– lié à l'éther, ce qui confirme l'existence de l'hétérocycle CA. Quant au cas du groupe ester, il montre une bande forte centrée à 1100 cm −1 pour le CA pur, et en même temps, la vibration d'étirement intermédiaire du groupe carbonyle -C=O montre une bande centrée à 1650 cm −1 . Alors que dans le mélange CA/TPU, la bande 1650 cm −1 disparu et une bande centrée à 3400 cm −1 significativement augmenté, indiquant la formation d'une nouvelle liaison hydrogène entre le -NH dans le TPU et l'oxygène dans le CA. Ces données de la figure 6 suggèrent que le CA est partiellement miscible avec le TPU en raison de la formation de liaisons hydrogène entre leurs chaînes polymères, et l'étendue de la miscibilité a sans aucun doute joué un rôle important dans la formation de fibres hélicoïdales [21].

FTIR du système de composants CA/TPU comprenant les polymères purs et les mélanges :a Coagulation TPU, b CA coagulum, et c Caillot CA/TPU
La formation de liaisons hydrogène entre CA et TPU peut être illustrée plus en détail sur la figure 7. Le co-électrofilage implique deux solutions de polymère qui introduisent une interface entre les deux solutions. Lorsqu'il est étiré par le champ électrique, une contrainte, qui provoque un cisaillement à l'interface des deux solutions, est générée. On s'attend à ce que l'étendue de la « contrainte », considérée comme la traînée visqueuse [22], et dans les mélanges, soit généralement nécessaire pour s'assurer qu'une liaison hydrogène existe entre les deux composants de base. Comme indiqué dans le système CA/TPU, les hydrogènes amides -NH dans la chaîne polymère TPU sont représentés en liaison hydrogène avec les oxygènes dans CA. On croyait que dans le système CA/TPU, les liaisons hydrogène augmentent la traînée visqueuse aux interfaces des jets composites lorsqu'ils sont étirés dans les champs électriques. Au cours du processus de co-électrofilage, la traînée visqueuse aide le noyau et la couche de coque à se lier, ce qui est la base de la génération de fibres hélicoïdales à deux composants, car ce type de liaison intermoléculaire contribue à augmenter l'interaction d'interface entre les deux couches [23]. Par conséquent, le système CA/TPU a tendance à générer efficacement des structures hélicoïdales en raison des interactions d'interface intensifiées.
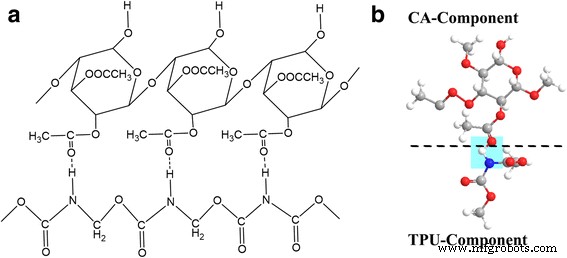
un , b Liaison hydrogène entre les chaînes polymères du composant CA et du composant TPU
Comportement de miscibilité dans les mélanges
Outre la miscibilité dans les mélanges, la contrainte de compression longitudinale résultant de l'élasticité du composant flexible (c'est-à-dire TPU) et de la rigidité du composant rigide (c'est-à-dire CA) est fondamentale pour la formation de structures hélicoïdales. La température de transition vitreuse d'un polymère, Tg, est une propriété intrinsèque importante qui influence à la fois les propriétés physiques et mécaniques, notamment la résistance, la ténacité et la rigidité. Typiquement, les polymères avec une rigidité de chaîne élevée ont une Tg plus élevée [24, 25]. L'analyse DSC est l'une des méthodes pratiques pour déterminer la température de transition vitreuse du polymère et la miscibilité des mélanges de polymères. La figure 8 montre les thermogrammes DSC des systèmes TPU, CA et CA/TPU. On peut constater que le TPU a une Tg d'environ - 31,24 °C, indiquant une chaîne polymère assez flexible de TPU (Fig. 8a), et CA a une Tg plus élevée (environ 193,74 °C) que le TPU, indiquant la plus grande rigidité de la chaîne de CA. La figure 8c illustre que dans le mélange CA/TPU, il y a deux Tg (61,24 et 157,75 °C) situées entre les Tg des deux polymères individuels (− 31,24 °C pour le TPU pur et 193,74 °C pour le CA pur), ce qui donne une indication de miscibilité partielle dans le mélange.
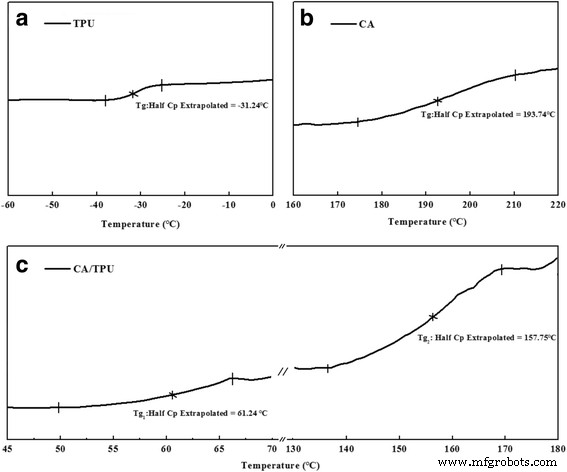
Thermogrammes DSC du système de composants CA/TPU comprenant les polymères purs et les mélanges :a Coagulation TPU, b CA coagulum, et c Caillot de mélange CA/TPU
On peut prédire que plus le différentiel de rigidité des deux composants est important, plus le système de composants a le potentiel de générer des structures hélicoïdales lors du co-électrofilage en raison de la plus grande contrainte interfaciale entre les composants. En analysant la miscibilité des systèmes CA/TPU, nous pensons que le système CA/TPU partiellement miscible a tendance à générer des structures hélicoïdales en raison de l'interaction interfaciale intensifiée attribuée à la liaison hydrogène.
Conclusions
Les résultats expérimentaux montrent que le système CA/TPU2 pourrait former efficacement des nanofibres hélicoïdales car la solution TPU2 permet une tension interfaciale inférieure avec la solution CA. Sur la base de l'interaction interfaciale induite par la structure et les propriétés intrinsèques du polymère, nous explorons le mécanisme des structures hélicoïdales CA/TPU sous trois aspects :propriétés de la solution, liaison hydrogène et comportement de miscibilité des deux solutions. Lorsque les solutions sont chargées, une force d'attraction entre les ions chlorure contenus dans les molécules CA et les charges libres à la surface de la solution conduit à une interaction interfaciale longitudinale dans le système CA/TPU. Le grand différentiel de rigidité des chaînes polymères de CA et TPU conduit à une grande interaction interfaciale entre eux. Dans le même temps, les liaisons hydrogène entre les chaînes polymères permettent d'obtenir un mélange partiellement miscible du CA et du TPU et par conséquent d'augmenter l'interaction interfaciale entre ces deux composants. Cette étude donne un aperçu du mécanisme de formation des fibres hélicoïdales CA/TPU et présente un choix plus riche de matériaux pour l'application des fibres hélicoïdales.
Abréviations
- CA :
-
Acétate de cellulose
- DMAc :
-
N,N-diméthylacétamide
- DSC :
-
Calorimétrie différentielle à balayage
- HSPET :
-
Poly(téréphtalate d'éthylène glycol)
- LiCl :
-
Chlorure de lithium
- Nomex :
-
Poly(m-phénylène isophtalamide)
- PAN :
-
Polyacrylonitrile
- PS :
-
Polystyrène
- PTT :
-
Poly(éthylène propanediol téréphtalate)
- PU :
-
Polyuréthane
- THF :
-
Tétrahydrofurane
- TPU :
-
Polyuréthane thermoplastique
- TPU1 :
-
TPU dissous dans DMAc/THF, rapport volumique 3/1
- TPU2 :
-
TPU dissous dans DMAc/acétone, rapport volumique 3/1
- FTIR :
-
Spectroscopie infrarouge à transformée de Fourier
Nanomatériaux
- Exemples de circuits et de listes d'interconnexions
- Qu'est-ce que l'analyse de maillage :procédure et ses exemples
- Nanofibres et filaments pour une administration améliorée des médicaments
- Dévoilement de la structure atomique et électronique des nanofibres de carbone empilées
- Fabrication à haut débit de nanofibres de qualité à l'aide d'un électrofilage à surface libre modifiée
- Fabrication de couches minces SrGe2 sur des substrats Ge (100), (110) et (111)
- Une étude sur les nanofibres de carbone et le charbon actif en tant que supercondensateur symétrique dans l'électrolyte aqueux :une étude comparative
- Fabrication et caractérisation de nano-clips de ZnO par le procédé à médiation par polyol
- La découpe au jet d'eau et ses nombreuses utilisations dans l'usinage et la fabrication