Comportement de frittage d'un SiC fritté par plasma d'étincelle avec des nanoparticules composites Si-SiC préparées par un procédé plasma thermique à courant continu
Résumé
La nanoparticule composite SiC revêtue de Si (Si-SiC) a été préparée par traitement au plasma thermique à arc non transféré de poudre de SiC synthétisée à l'état solide et a été utilisée comme additif de frittage pour la formation de céramique SiC. Une pastille de SiC frittée a été préparée par un procédé de frittage par plasma à étincelles (SPS), et l'effet de particules composites Si-SiC de taille nanométrique sur le comportement de frittage d'une poudre de SiC de taille micronique a été étudié. Le rapport de mélange de la nanoparticule composite Si-SiC au SiC de la taille d'un micron a été optimisé à 10 % en poids. La dureté et la densité relative de Vicker ont augmenté avec l'augmentation de la température de frittage et du temps de maintien. La densité relative et la dureté de Vicker ont été encore augmentées par la liaison réactionnelle utilisant du charbon actif supplémentaire au mélange de SiC de taille micronique et de Si-SiC de taille nanométrique. La densité relative maximale (97,1 %) et la dureté Vicker (31,4 GPa) ont été enregistrées à une température de frittage de 1800 °C pendant 1 min de temps de maintien, lorsque 0,2 % en poids de charbon actif supplémentaire a été ajouté au mélange de SiC/Si-SiC.
Contexte
Les céramiques en carbure de silicium (SiC) ont attiré une grande attention en raison de ses propriétés phénoménales, telles que la dureté à haute température, la résistance à l'usure, le faible coefficient de dilatation thermique, la conductivité thermique élevée, la forte résistance à la corrosion et la stabilité élevée dans un environnement agressif, et ont été appliqué à divers domaines tels que les aubes de turbine, les pièces de moteur diesel et les matériaux de réacteurs aérospatiaux et nucléaires [1,2,3,4,5,6]. Cependant, il est difficile de densifier le SiC sans additifs en raison de la nature covalente de la liaison Si-C et du faible coefficient d'autodiffusion [7, 8]. Les matériaux SiC massifs sont généralement préparés soit par le carbure de silicium fritté à l'état solide (SSS-SiC) soit par le carbure de silicium fritté en phase liquide (LPS-SiC) à partir des poudres cristallines SiC de départ [7, 8]. Dans le cas du SSS-SiC, aucun additif formant liquide, tel que le bore, l'aluminium, le carbone ou leurs composés, n'a été utilisé pour la densification du SiC par la réduction de l'énergie de surface des grains et la réaction entre la silice présente en surface et carbone. Cependant, ce processus nécessite une température supérieure à 2000 °C pour le frittage [7, 9, 10]. Le LPS-SiC est régi par la formation en phase liquide d'un additif d'oxyde métallique à la température de frittage et cette phase liquide agit comme un milieu de transport de masse pendant le frittage du SiC [8, 11, 12]. À l'exception de la magnésie et de l'alumine, l'yttria et d'autres oxydes de terres rares sont principalement utilisés comme additifs de frittage, et la température de frittage peut être abaissée jusqu'à 1850 °C, selon la combinaison d'additifs de frittage utilisée [11, 12]. Cependant, la présence du composé de silicate amorphe aux joints de grains et aux points triples entraîne une diminution de la dureté et de la résistance au fluage à haute température par rapport au SSS-SiC [12]. Mais les additifs utilisés pour améliorer le traitement deviennent invariablement une phase secondaire «faible» dans la céramique finale, ce qui abaisse généralement ses propriétés mécaniques à haute température [13]. Cet effet néfaste implique que la plus petite fraction d'additifs est souhaitable. De plus, l'efficacité des additifs dépend fortement de l'homogénéité de leur répartition [13]. Il existe également une autre approche pour la fabrication de SiC en vrac, appelé carbure de silicium lié par réaction (RB-SiC). Dans le RB-SiC, la réaction du silicium fondu avec la poudre de carbone entraîne la formation de SiC [13,14,15,16]. Bien que cette approche nécessite une température de frittage plus basse et qu'il n'y ait aucune limitation de la forme et de la taille du produit, la faible densité des corps est un inconvénient [17, 18]. Cependant, l'abaissement de la température de frittage est essentiel pour économiser l'énergie. Ces derniers temps, les économies d'énergie sont devenues la force motrice pour trouver d'autres méthodes adaptées à la préparation de céramiques SiC en vrac à basse température.
Récemment, le SiC de taille nanométrique a été largement étudié pour examiner leurs propriétés mécaniques, physiques et chimiques qui sont différentes de celles en vrac et souvent utiles [19,20,21]. Par exemple, les nanopoudres principalement en raison des surfaces spécifiques et des activités de surface plus élevées peuvent fournir la frittabilité à basse température du SiC de taille nanométrique dans le traitement de consolidation et l'amélioration des propriétés mécaniques en permettant d'atteindre des densités élevées [22]. Par conséquent, à l'heure actuelle, nous avons développé une nouvelle méthode pour préparer des nanoparticules de SiC revêtues de Si (Si-SiC) à appliquer comme additif de frittage en utilisant le traitement par plasma CC thermique non transféré de poudre de SiC synthétisée à l'état solide [23].
Dans cette étude, la particule composite Si-SiC de taille nanométrique en tant qu'additif de frittage a été appliquée pour préparer la céramique SiC en vrac par le procédé de frittage par plasma d'étincelle (SPS), et l'effet de l'ajout de la particule composite Si-SiC de taille nanométrique sur le frittage la température, la densité relative et la dureté de Vicker de la céramique SiC frittée ont été étudiées. De plus, pour augmenter encore la densité relative et la dureté du SiC fritté, la liaison réactionnelle entre le silicium libre de particules de Si-SiC nanométriques et le charbon actif qui a été ajouté en plus a été nouvellement introduite dans le processus de frittage du SiC. Le mécanisme de frittage de la céramique SiC produite avec un additif composite Si-SiC de taille nanométrique par le biais du processus SPS a également été discuté sur la base de l'effet de taille nanométrique et de l'effet de liaison par réaction. Cette étude fournit une nouvelle stratégie prometteuse pour pouvoir préparer la céramique SiC avec une densité et une dureté élevées à une température de frittage relativement basse.
Expérimental
La figure 1 montre les procédures de préparation d'une poudre de SiC de taille micrométrique par réaction solide-solide (calcination), d'une poudre de SiC de taille nanométrique par procédé de plasma thermique à arc non transféré et d'une pastille de SiC frittée par procédé SPS. Dans ce travail, des poudres de SiC de deux tailles différentes, une poudre de SiC de la taille d'un micron (en tant que matériau de frittage principal) et une nanopoudre composite Si-SiC de taille nanométrique (en tant qu'additif de frittage), ont été préparées respectivement par des procédés de calcination et de plasma.
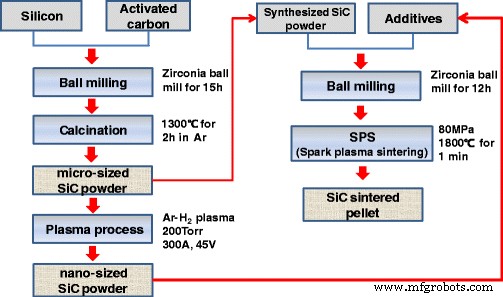
Procédure expérimentale de préparation de poudre de SiC micronique par calcination et de poudre composite Si-SiC nanométrique par plasma et de frittage de céramiques SiC par SPS
Préparation de poudre de SiC de la taille d'un micron
Le SiC de la taille du micron a été synthétisé en utilisant des poudres de Si avec une taille de particule moyenne de 25 μm (99,9 % ; Neoplant Co. LTD.) et du charbon actif avec une taille de particule moyenne de 32 μm (Sigma-Aldrich). Dans une procédure typique, un rapport molaire de 1:1,5 de Si et de carbone a été mélangé en utilisant un broyeur à boulets pendant 15 h. La poudre mélangée a été placée dans un four tubulaire vertical et chauffée à 1300 °C pendant 2 h avec une vitesse de chauffage de 10 °C/min en présence de gaz argon (1 L/min). Une fois la réaction terminée, la poudre obtenue a été broyée dans un mortier d'agate pour une caractérisation plus poussée.
Traitement au plasma de poudres SiC synthétisées
Le traitement au plasma a été effectué par un réacteur à plasma thermique à arc non transféré comme indiqué dans nos travaux précédents [21, 23]. La poudre de SiC broyée a été introduite dans l'arc plasma via le pipeline d'alimentation interne de 2 mm de diamètre intérieur dans la torche à plasma à l'aide d'un alimentateur de poudre spécialement conçu. Le système d'alimentation en poudre se composait d'un conteneur d'échantillon, d'un vibrateur et d'une conduite de gaz vecteur. Les poudres ont été alimentées par un alimentateur vibrant à 70 V avec un taux d'alimentation de 1 g/min. Des expériences de synthèse typiques ont été effectuées à des pressions du système de 200 Torr, avec des débits de gaz plasma Ar de 30 L/min, H2 débits de gaz d'environ 3 L/min et courant continu de 300 A (à 45 V). Après l'allumage du plasma, une poudre de SiC de la taille du micron a été fournie par l'alimentateur. Les nanopoudres synthétisées ont été collectées à partir de la paroi du réacteur et du fond du système de réacteur à plasma. Le rendement était d'environ 80 à 85 %.
Préparation de pastilles SiC frittées
La pastille de SiC frittée a été préparée par le procédé SPS (comme le montre la figure 1). Les deux matériaux SiC, c'est-à-dire la poudre de SiC de la taille du micron synthétisée par procédé de calcination et la poudre de Si-SiC de taille nanométrique obtenue à partir du procédé plasma, ont été utilisés sans additifs supplémentaires. La teneur en mélange des nanoparticules de Si-SiC dans une poudre de SiC de la taille d'un micron est passée de 5 à 15 % en poids.
Les poudres mélangées ont été placées dans une matrice en graphite (20 mm de diamètre) et frittées avec un système SPS sous vide (10 −2 Torr). La vitesse de chauffage a été fixée à 600 °C/min, et la pression appliquée était de 80 MPa. La température de frittage a été modifiée de 1600 à 1800 °C. Le temps de maintien à la température cible a varié de 0 à 1 min à 1800 °C. Après frittage, les surfaces des échantillons ont été rectifiées pour éliminer la couche de graphite, puis polies par une pâte diamantée. La densité des échantillons frittés a été mesurée par la méthode d'Archimède dans de l'eau déminéralisée comme milieu d'immersion.
Caractérisation de l'échantillon
Les structures cristallographiques des échantillons solides ont été déterminées à l'aide d'un XRD (D/Max 2005 Rigaku) équipé d'un rayonnement Cu-Kα1 de haute intensité monochromaté graphite (λ = 1,5405 Å). Les modèles XRD ont été enregistrés de 20° à 80° (2θ ) avec une vitesse de balayage de 0,04°/s. La taille et la morphologie des particules ont été étudiées au microscope électronique à balayage (SEM ; JSM-5900, JEOL) et au microscope électronique à transmission (TEM ; JEM-2010, JEOL).
Résultats et discussion
La figure 2 montre le motif XRD et l'image FESEM de SiC synthétisé par une méthode à l'état solide utilisant un mélange de Si et de C dans des rapports molaires de 1:1,5. Le motif XRD confirme la formation de -SiC avec une petite quantité de α-SiC, comme le montre la figure 2a. Il n'y avait pas d'autres phases d'impuretés, telles que le silicium libre et le SiO2 . L'image FESEM a montré la formation de particules de SiC de la taille d'un micron et la taille des particules variait de 2 à 5 μm, comme le montre la figure 2b.
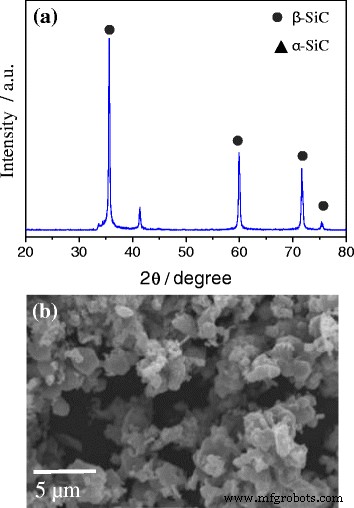
Profil XRD (a ) et image FESEM (b ) de SiC micrométrique synthétisé par la méthode à l'état solide
Une poudre de SiC de taille nanométrique a été préparée à partir de cette poudre de SiC de la taille d'un micron à l'aide d'un traitement au plasma thermique, comme le montre la figure 3. Les figures 3a, b étaient une image FESEM et une image TEM, respectivement. Ces photographies confirment la formation de particules Si-SiC de taille nanométrique, et la taille des particules variait de 20 à 70 nm. La figure 3c est une image HRTEM de particules SiC de taille nanométrique, qui confirme la formation de particules composites Si-SiC de taille nanométrique sous la forme de franges de réseau claires des deux matériaux (Si et SiC). La surface de la poudre de SiC de taille nanométrique était de 69 m 2 /g.
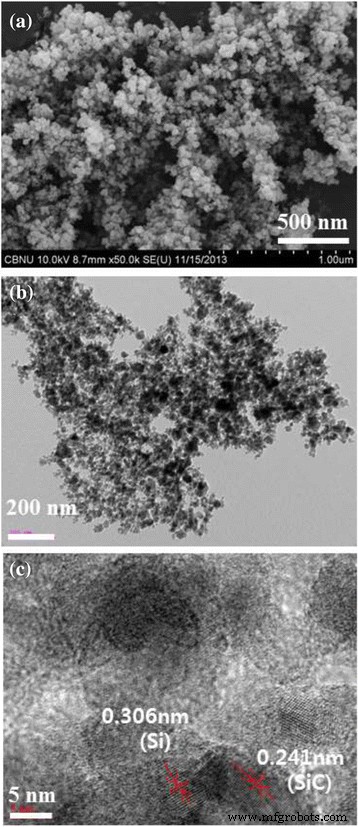
Images EM de particules composites Si-SiC préparées par un procédé de plasma thermique à arc non transféré :a FESEM, b TEM, et c RH-TEMP
La phase et la structure des particules de SiC de taille nanométrique ont été analysées par XRD et illustrées à la figure 4. Semblable au SiC de la taille d'un micron, il montre également la formation de -SiC avec une petite quantité de α-SiC. Cependant, le SiC de taille nanométrique présentait du Si libre et du SiO2 pics. L'apparition du pic de silicium était liée à la décomposition partielle du SiC lors du traitement par plasma thermique. L'origine de SiO2 Le pic était peut-être lié à l'oxydation partielle de la surface du SiC lors de l'exposition à l'air après le traitement au plasma. Une pastille de céramique SiC frittée a été préparée à partir de ces deux types de SiC, c'est-à-dire le SiC de taille micronique et les composites Si-SiC de taille nanométrique. Le mélange a été fritté par procédé SPS en utilisant diverses compositions de SiC de taille micronique et de Si-SiC de taille nanométrique, et la température de frittage, le temps de maintien à la température de frittage et la pression comprimée ont varié comme indiqué dans le tableau 1.
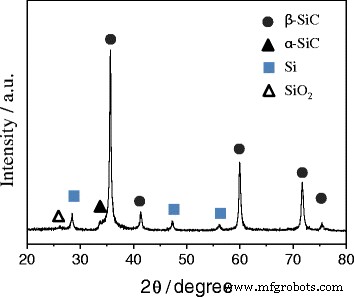
Profil XRD de nanoparticules composites Si-SiC préparées par procédé de plasma thermique à arc non transféré
Les changements de densité relative et de dureté Vicker du SiC fritté en fonction de la température de frittage et du temps de maintien à la température de frittage cible sont également indiqués dans le tableau 1. La densité relative et la dureté augmentent avec l'augmentation de la température de frittage, et la densité relative (87,4 %) et la dureté les plus élevées (18,6 GPa) ont été enregistrés à 1800 °C. La densité relative et la dureté ont encore été augmentées à 88,2 % et 21,2 GPa, respectivement, avec une augmentation du temps de maintien de 0 à 1 min à une température de frittage de 1800 °C. Cela suggère que la densité relative et la dureté augmentent avec l'augmentation du temps de maintien ; Malheureusement, le temps de maintien à 1800 °C n'a pas pu être augmenté davantage en raison de la limitation du système SPS.
La figure 5 montre les images FESEM d'une surface SiC frittée avec une température de frittage et un temps de maintien variables. La taille des grains de SiC a augmenté avec l'augmentation de la température de frittage, comme le montre la figure 5a–c. La forme et la taille des particules de SiC de la taille du micron étaient presque maintenues jusqu'à 1600 °C (Fig. 5a), et la croissance des grains de SiC a commencé à partir de 1700 °C, ce qui a entraîné une augmentation de la densité relative et de la dureté jusqu'à 86,1 % et 14,8 GPa, respectivement (Fig. 5b). À 1800 °C de température de frittage, la taille des grains de SiC était de 2 à 4 μm et la texture cristalline était plus densifiée (Fig. 4c). La densité relative et la dureté à 1800 °C étaient respectivement de 87,4 % et 18,6 GPa. La croissance des grains a été en outre enregistrée lorsque l'échantillon a été maintenu pendant 1 min à une température de frittage de 1800 °C, ce qui est évident d'après l'augmentation de la densité relative et de la dureté à 88,2 % et 21,2 GPa, respectivement (Fig. 5d).
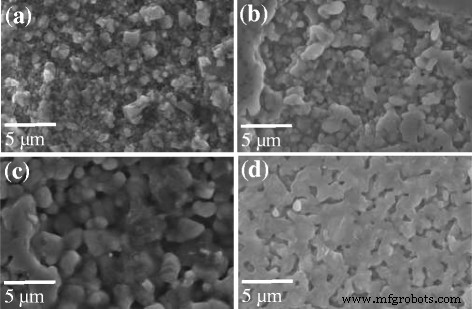
Images FESEM du SiC fritté avec des particules composites Si-SiC de taille nanométrique par procédé SPS à a 1600 °C, b 1700 °C, c Température de frittage de 1800 °C avec 0 min de temps de maintien, et d 1800 °C température de frittage à 1 min de temps de maintien à la température cible
Afin d'augmenter la densité relative, la quantité ajoutée de Si-SiC de taille nanométrique dans une poudre de SiC de taille micrométrique a été modifiée de 5 à 15 % en poids. De plus, du charbon actif supplémentaire a également été ajouté à ce mélange pour augmenter la densité relative grâce à la liaison réactionnelle (RB) avec du silicium libre de Si-SiC de taille nanométrique. La densité relative et la dureté de Vicker du SiC fritté en fonction des différentes compositions de SiC micronique, de Si-SiC nanométrique et de charbon actif sont résumées dans le tableau 2.
La température de frittage (1800 °C), le temps de maintien (1 min) et la pression (80 MPa) ont été maintenus constants tout au long de l'expérience. En l'absence de carbone ajouté, la densité relative et la dureté augmentent avec l'augmentation de la teneur en SiC nanométrique jusqu'à 10 % en poids, puis diminuent. Par exemple, la densité relative et la dureté étaient de 85,9 % et 21,1 GPa, lorsque la teneur en Si-SiC de taille nanométrique était de 5 % en poids. La densité relative et la dureté ont augmenté à 88,2 % et 21,2 GPa, respectivement à 10 % en poids du Si-SiC de taille nanométrique. Alors que lorsque la teneur était de 15 % en poids, la dureté a diminué de manière remarquable jusqu'à 16,6 GPa bien que la densité relative indiquait encore 85,6%. Ceci est principalement dû au fait que les particules de Si-SiC de taille nanométrique excessivement ajoutées peuvent fournir une grande quantité de pores dans le SiC fritté. Pour une augmentation supplémentaire de la densité relative et de la dureté, du charbon actif a été ajouté en plus. L'ajout de 0,1 % en poids de charbon actif a entraîné une augmentation remarquable de la densité relative (93,1 %) et de la dureté (25,2 GPa). La densité relative et la dureté ont encore été augmentées à 97,1 % et 31,4 GPa, respectivement, avec une augmentation de la teneur en charbon actif jusqu'à 0,2 % en poids. L'analyse XRD de ces pastilles de SiC frittées avec différentes compositions a été réalisée et montrée sur la Fig. 6. Il n'y a eu aucun changement dans la structure cristalline même après frittage, à l'exception d'un faible pic de silicium enregistré à 29°, qui est peut-être dû à l'ajout de particules composites Si-SiC de taille nanométrique.
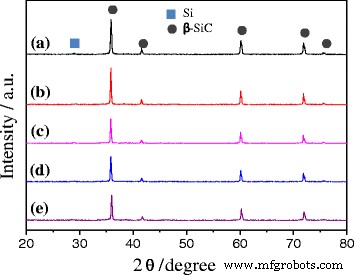
Profils XRD de pastilles SiC frittées avec des particules composites Si-SiC nanométriques et du charbon actif par procédé SPS (les détails de a, b, c, d et e sont donnés dans le tableau 2)
La figure 7 montre des images FESEM de la surface des pastilles de SiC frittées avec différentes compositions de SiC de taille micronique et de Si-SiC de taille nanométrique. La taille des grains de SiC était de 2 à 3 μm avec des pores plus gros, lorsque la teneur en Si-SiC de taille nanométrique était de 5 % en poids (Fig. 7a). La taille des grains a augmenté avec l'augmentation de la teneur en Si-SiC de taille nanométrique, comme indiqué sur les Fig. 7b, c. La taille des grains des pastilles de SiC avec 10 et 15 % en poids de Si-SiC était d'environ 3 à 5 et 4 à 6 μm, respectivement. La figure 7d, e présente les images FESEM d'une pastille de SiC frittée après ajout de charbon actif. Lorsque 0,1 % en poids de charbon actif a été ajouté, des grains géants commencent à apparaître, ce qui suggère que la densification de la texture SiC a progressé par liaison réactionnelle entre le silicium et le charbon actif. Une augmentation supplémentaire du charbon actif jusqu'à 0,2 % en poids a entraîné une densification complète de la texture SiC, comme le montre la figure 7e.
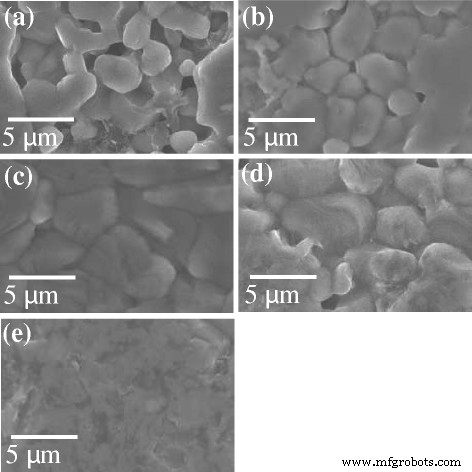
Images FESEM de pastilles de SiC frittées avec des nanoparticules composites Si-SiC nanométriques et du charbon actif par procédé SPS (détails de a , b , c , d , et e sont donnés dans le tableau 2)
La figure 8 présente les déplacements de retrait d'échantillons de SiC fritté avec différentes compositions à différentes températures de frittage. Une expansion a été enregistrée pour tous les échantillons jusqu'à 1500 °C, ce qui est principalement dû à l'expansion des gaz présents dans le mélange SiC (Fig. 8a–e). Il peut également être observé par une augmentation de 1,0 à 1,28 mm de la hauteur du moule en graphite ayant un mélange de poudre de SiC après le frittage par rapport à l'étape de frittage initiale. Une augmentation supplémentaire de la température de frittage a entraîné un rétrécissement de tous les échantillons en raison de l'effet de frittage des nanoparticules de Si-SiC de taille nanométrique. L'augmentation du temps de maintien de l'échantillon à la température de frittage de 0 à 1 min a également entraîné une augmentation du retrait des échantillons. L'ajout de charbon actif supplémentaire au mélange de SiC et Si-SiC a montré un déplacement de retrait plus élevé après 1500 °C par rapport aux mélanges SiC/Si-SiC sans charbon actif (Fig. 8d, e). De plus, le déplacement de retrait augmente avec l'augmentation de la quantité ajoutée de charbon actif supplémentaire. Par exemple, le déplacement de retrait a été augmenté de 1,11 à 1,61 mm, lorsque la quantité de charbon actif ajouté a été augmentée de 0,1 à 0,2 % en poids, respectivement, comme le montre la figure 8d, e. Cela est dû à l'effet de liaison par réaction du silicium libre des nanoparticules composites Si-SiC et du charbon actif. La nature exothermique de cette réaction se traduit par une augmentation de la température réelle à l'intérieur de la pastille de SiC lors du frittage. Ainsi, ces résultats confirment clairement que l'effet de liaison par réaction du silicium et du charbon actif peut augmenter la densité relative et la dureté des céramiques SiC.
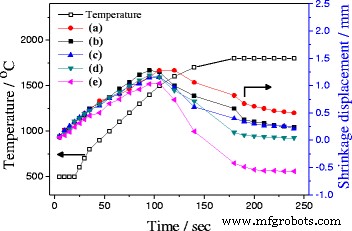
Modification du déplacement de retrait des pastilles de SiC frittées avec des nanoparticules composites Si-SiC nanométriques pendant le processus SPS (les détails de a, b, c, d et e sont donnés dans le tableau 2)
À partir des résultats expérimentaux ci-dessus, nous pouvons résumer un mécanisme de frittage d'une poudre de SiC de la taille d'un micron avec une poudre composite Si-SiC de taille nanométrique et du charbon actif comme suit. Il a été déterminé dans le tableau 1 que le frittage d'une poudre de SiC de la taille d'un micron avec 10 % en poids de poudre composite Si-SiC de taille nanométrique a commencé à 1600 °C, et la réaction de frittage a été accélérée avec l'augmentation de la température de frittage et du temps de maintien. À partir de ce résultat, nous avons confirmé l'effet nanométrique des nanoparticules composites Si-SiC sur le frittage de la poudre de SiC micronique. Ici, si du charbon actif est ajouté au mélange de SiC de taille micronique et de poudre composite Si-SiC de taille nanométrique, la liaison réactionnelle, qui provient de la réaction exothermique entre le silicium libre des nanoparticules composites Si-SiC, peut être induite dans le processus de frittage comme illustré schématiquement à la Fig. 9. Par conséquent, il a pu être constaté que le mécanisme de frittage d'une poudre de SiC de taille micronique avec une poudre composite Si-SiC de taille nanométrique et du charbon actif comme additifs de frittage repose sur les deux effets, le nano- effet de taille et l'effet de liaison par réaction, qui ont été introduits à partir de la poudre composite Si-SiC de taille nanométrique.
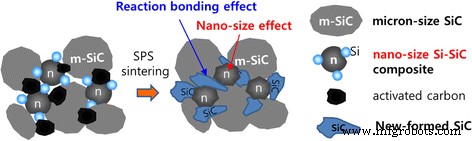
Schéma du mécanisme de frittage pour une poudre de SiC de taille micronique avec une poudre composite Si-SiC de taille nanométrique et du charbon actif comme additifs de frittage
Conclusions
Une poudre de SiC de la taille d'un micron (2-5 μm) a été synthétisée par une méthode à l'état solide en utilisant de la poudre de Si et des sources de charbon actif. Une poudre composite Si-SiC de taille nanométrique, ayant une taille de particule de 20 à 70 nm, a été préparée par un procédé de plasma thermique à arc non transféré. Des pastilles de SiC frittées ont été préparées par le procédé SPS en utilisant le mélange avec un rapport différent de poudre de SiC de taille micronique et de particules composites Si-SiC de taille nanométrique comme additif de frittage. À un rapport fixe de SiC de taille micronique et de Si-SiC de taille nanométrique (90:10), la densité relative et la dureté de Vicker ont augmenté avec l'augmentation de la température de frittage et du temps de maintien. La densité relative maximale (88,2 %) et la dureté Vicker (21,2) ont été enregistrées à une température de frittage de 1800 °C pendant 1 min de temps de maintien. La densité relative et la dureté de Vicker ont encore été augmentées par l'ajout de charbon actif supplémentaire au mélange de SiC de taille micronique et de Si-SiC de taille nanométrique. La densité relative et la dureté de Vicker ont été augmentées à 97,1 % et 31,4 GPa, respectivement, avec l'ajout de 0,2 % en poids de charbon actif supplémentaire au mélange SiC/Si-SiC. Il a été constaté que l'effet nanométrique des particules composites Si-SiC et la nature exothermique de la réaction de liaison silicium-carbone étaient responsables de l'augmentation de la densité et de la dureté relatives. Par conséquent, il a été suggéré que la particule composite Si-SiC de taille nanométrique pourrait être un additif prometteur pour le frittage des céramiques SiC.
Nanomatériaux
- Processus de frittage d'alliage réfractaire
- Grande amélioration de la conductivité thermique du composite de silicone avec des nanofils de cuivre ultra-longs
- Nanofibres polymères électrofilées décorées de nanoparticules de métaux nobles pour la détection chimique
- Membranes composites contenant des nanoparticules d'échangeurs d'ions inorganiques pour le dessalement électrodialytique du glycérol
- Synthèse facile de composite CuSCN coloré et conducteur revêtu de nanoparticules CuS
- Cibler les cellules endothéliales avec des nanoparticules GaN/Fe multifonctionnelles
- Propriétés électriques des matériaux composites avec alignement assisté par champ électrique des charges de nanocarbone
- Effets synergiques des nanoparticules d'Ag/BiV1-xMoxO4 avec une activité photocatalytique améliorée
- Étude de l'effet de la direction d'impact sur le processus de coupe nanométrique abrasif avec la dynamique moléculaire