Étude de l'effet de la direction d'impact sur le processus de coupe nanométrique abrasif avec la dynamique moléculaire
Résumé
Le polissage par flux abrasif joue un rôle important dans l'usinage ultra-précis moderne. Les particules ultrafines en suspension dans le milieu du flux abrasif enlèvent le matériau à l'échelle nanométrique. Dans cet article, des simulations de dynamique moléculaire (MD) en trois dimensions sont effectuées pour étudier l'effet de la direction d'impact sur le processus de coupe abrasive pendant le polissage par flux abrasif. Le logiciel de simulation de dynamique moléculaire Lammps a été utilisé pour simuler la coupe de cuivre monocristallin avec des grains abrasifs SiC à différents angles de coupe (0 o –45 o ). A coefficient de frottement constant, nous avons trouvé une relation directe entre l'angle de coupe et la force de coupe, ce qui augmente finalement le nombre de dislocations lors de l'usinage par flux abrasif. Notre étude théorique révèle qu'un petit angle de coupe est bénéfique pour améliorer la qualité de surface et réduire les défauts internes de la pièce. Cependant, il n'y a pas de relation évidente entre l'angle de coupe et le coefficient de frottement.
Contexte
Dans l'usinage ultra-précis moderne, les technologies d'enlèvement de matière jouent un rôle important dans la fabrication d'éléments microélectroniques, micromécaniques et optiques. La demande de dispositifs miniaturisés avec une précision dimensionnelle élevée et une surface de qualité, faisant des processus d'ultra-précision le choix majeur dans le domaine mentionné [1]. De plus, les changements des composants de la surface et de la structure souterraine sont à l'échelle du nanomètre. La technologie de polissage par flux de particules abrasives joue un rôle important dans de nombreux domaines de l'usinage de précision et ressemble à d'autres technologies de finition non traditionnelles qui améliorent la qualité de surface. Cette technologie a attiré de nombreux chercheurs en raison de son rôle important. E. Uhlmann et d'autres chercheurs ont rapporté la simulation informatique de la surface céramique de polissage des grains abrasifs pour les expériences conçues pour vérifier le flux de fluide de broyage de divers facteurs de traitement sur l'effet des matériaux de coupe [2]. Sehijpal Singh et d'autres chercheurs utilisent la technologie de polissage par flux abrasif pour couper les matériaux en cuivre et en aluminium. À partir de l'analyse au microscope électronique à balayage, ils ont trouvé une surface de rainure profonde de leur pièce [3]. G. Venkatesh et d'autres chercheurs ont rapporté une technologie de polissage des grains abrasifs assistée par ultrasons pour l'engrenage conique sur la surface complexe du processus de finition. Dans cette technique, la vitesse des grains abrasifs est plus élevée que le flux de grains abrasifs conventionnel pour entrer en collision avec la surface de la pièce, ce qui peut améliorer l'efficacité du traitement. À partir de leurs méthodes expérimentales et théoriques, ils ont découvert que cette technologie est l'un des meilleurs choix pour la finition des lames d'engrenage [4, 5]. K. Kamal et al. ont étudié les propriétés rhéologiques du liquide abrasif dans la viscosité, le taux de cisaillement et le temps de fluage du fluide abrasif [6]. Cependant, la plupart des études de polissage par flux abrasif sont basées sur le niveau macro et une attention très rare a été accordée au niveau micro. Dans le processus de polissage par flux abrasif, les particules en suspension dans le support s'écouleront le long du support, à une certaine vitesse avec l'impact de la surface de la pièce de micro-coupe (Fig. 1).
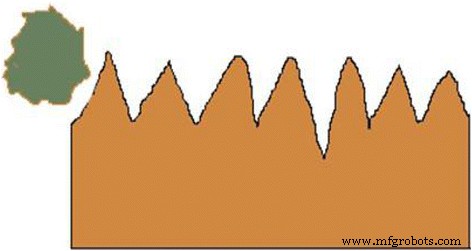
Croquis d'une pièce de coupe abrasive. Tous les chiffres concernent l'effet de la direction d'impact sur le processus de coupe nanométrique abrasif avec la dynamique moléculaire. La figure 1 est le croquis de la pièce de coupe abrasive. Dans le processus de polissage par flux abrasif, les particules en suspension dans le support s'écouleront le long du support à une certaine vitesse avec l'impact de la surface de la pièce de micro-coupe
Comme la forme des grains abrasifs n'est pas régulière, ayant certains bords et coins qui agissent sur la surface de la pièce, semblable à l'outil. Mais le processus de découpe est à l'échelle atomique, ce qui est évidemment différent du processus d'enlèvement de matière. Une découpe à l'échelle nanométrique implique quelques nanomètres ou moins de la surface du matériau, mais il est très difficile d'observer ce processus par des expériences. Par conséquent, la simulation MD en tant que méthode d'investigation théorique est très utile pour étudier le processus de coupe nanométrique. La dynamique moléculaire en tant que technique de simulation informatique, qui utilise une méthode de mécanique statistique basée sur le temps pour étudier l'interrelation des atomes pour la prédiction et l'analyse des conditions. C'est aussi un outil puissant pour simuler et comprendre les processus d'enlèvement de matière. Dans la littérature, il existe de nombreuses études concernant la DM en tant qu'outil pour étudier l'usinage de précision. Oluwajobi et Chen ont effectué des travaux approfondis sur la simulation MD de l'usinage nanométrique du cuivre [7]. Dans leurs études, ils ont étudié divers paramètres pour le nano-usinage tels que la profondeur de coupe minimale, la géométrie et le potentiel interatomique [8]. De plus, les résultats des simulations MD ont également été couronnés de succès dans le passé pour résoudre un certain nombre de problèmes concernant le processus de coupe nanométrique de matériaux fragiles tels que le silicium [9]. Komanduri et al. a mené une simulation MD pour le découpage nanométrique de monocristaux de silicium pur sans défaut, en utilisant le potentiel de Tersoff. Ils ont étudié les effets de l'angle de coupe, de la largeur de coupe, de la profondeur de coupe et de l'angle de dépouille sur l'enlèvement de matière et la génération de surface [10]. Goel et al. ont étudié les aspects atomistiques de la réponse ductile du SiC pendant le processus de coupe nanométrique. Ils ont découvert la présence d'une transition ordre-désordre sp3-sp2 qui a finalement abouti à la graphitisation du diamant [11]. Cai et al. utilisé MD pour étudier le découpage en mode ductile à l'échelle nanométrique du silicium. Ils ont rapporté le tranchant de l'outil et ses effets sur la contrainte de cisaillement dans le matériau de la pièce [12]. Arafin et al. a discuté de l'effet du rayon de l'arête de coupe dans la coupe en mode ductile à l'échelle nanométrique d'une plaquette de silicium [13]. Divers autres chercheurs ont également mis en évidence les différentes conditions de nano-usinage du silicium à l'aide de simulations MD. Ces investigations portent sur les forces de coupe, la profondeur de coupe, la température, la contrainte de cisaillement et d'autres paramètres. Cependant, il y a un manque de validations expérimentales adéquates dans ce domaine. Qihong Fang et al. ont étudié le mécanisme d'interaction des dislocations dans différents matériaux hétérogènes avec différentes échelles, et la dislocation et la relation entre la ténacité du matériau et les dommages à la rupture. Ils utilisent des simulations de dynamique moléculaire pour étudier la nanoindentation sur trois structures cristallines différentes, y compris le cuivre polycristallin monocristallin, polycristallin et nanojumelé. Avec l'augmentation du taux de rayure, la force de rayure et la température de la pièce augmentent continuellement en raison de la déformation plastique sévère et du grand volume de copeaux, ce qui entraîne un glissement de dislocation, un glissement GB et un jumelage/déjumelage [14, 15].
Méthodes/Expérimental
Dans l'expérience de polissage par flux abrasif, la pièce à usiner était généralement coupée avec un abrasif SiC. Après l'établissement du modèle de grains abrasifs SiC, la simulation de la dynamique moléculaire de la pièce a été réalisée par le logiciel Lammps. Le modèle de deux cuivre monocristal de coupe abrasive SiC avec des angles différents a été construit. Un modèle de simulation d'un crash de grains abrasifs SiC coupant du cuivre monocristallin est présenté sur la figure 2.
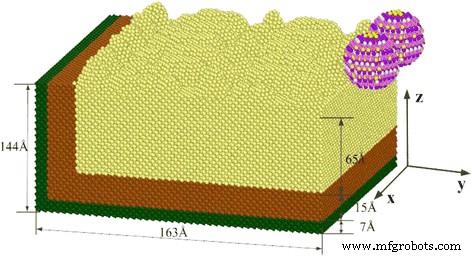
Modèle de simulation de cuivre monocristallin de coupe abrasive SiC. La figure 2 concerne le modèle de simulation de cuivre monocristallin de coupe abrasive SiC ; nous avons construit deux abrasifs SiC pour couper le cuivre monocristallin. Dans l'expérience de polissage par flux abrasif, la pièce à usiner était généralement coupée avec un abrasif SiC. Après la construction du modèle abrasif SiC, la simulation de la dynamique moléculaire de la pièce a été réalisée. Le modèle de deux cuivre monocristal de coupe abrasive SiC avec des angles différents a été construit
La taille du modèle est illustrée à la figure 2 alors que le nombre d'atomes simulés était de 159 020. Le rayon abrasif est de 15 , le nombre total d'atomes de C et d'atomes de Si dans les grains abrasifs est de 1406. Et le nombre d'atomes de carbone et de silicium était de 681 et 725, respectivement. Le nombre d'étapes de relaxation est fixé à 10 000 étapes pour l'ensemble d'équilibre simulé, les étapes de simulation de collision à 100 000 étapes de coupe, chaque étape de la simulation était de 0,001 ps, la simulation de coupe, les particules abrasives SiC dans la direction de coupe vitesse de 80 m/s. Les grains de valeur d'analyse AFM entrent en collision avec la pièce de micro-usinage pendant le polissage, les grains abrasifs SiC pour explorer le processus de coupe sous différents angles de la dynamique de collision moléculaire. Dans le processus de coupe par flux abrasif, la force de coupe augmente à mesure que la vitesse de coupe augmente et la taille de la force de coupe affecte directement l'effet de coupe. Par conséquent, le choix d'une vitesse de coupe raisonnable a un impact important sur la qualité de la coupe. Pour obtenir une coupe de haute qualité, nous avons choisi la vitesse de coupe de 80 m/s, car elle produit la force de coupe qui peut rapidement détruire l'interaction entre les atomes de la pièce [16].
Dans les simulations de dynamique moléculaire à faible vitesse de coupe telles que 10 m/s, les cartes de déplacement atomique et le motif de la variation de la force de coupe des particules abrasives de carbure de silicium et des angles de coupe avec la taille du pas de simulation, comme le montrent les Fig. 3 et 4. Étant donné que la vitesse de coupe est trop faible, la force de coupe est également insuffisante, ce qui entraîne beaucoup moins de déformation et de dislocation du réseau. Dans l'ensemble, l'efficacité de coupe est faible et la qualité de coupe est relativement médiocre. En revanche, lorsque la vitesse de coupe atteint 80 m/s dans une expérience microscopique, les liaisons chimiques entre les atomes de cuivre peuvent être rompues rapidement et efficacement, afin d'atteindre l'objectif d'une coupe instantanée de haute qualité. Par conséquent, après une analyse complète, une vitesse de coupe de 80 m/s est raisonnable pour la simulation.
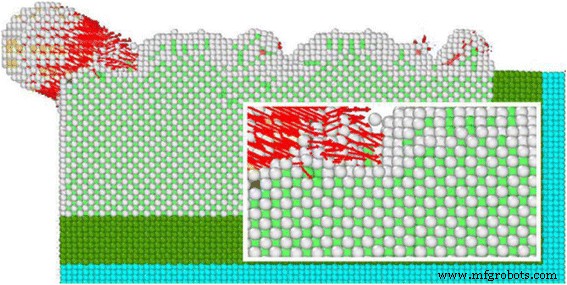
Déplacement atomique à faible vitesse
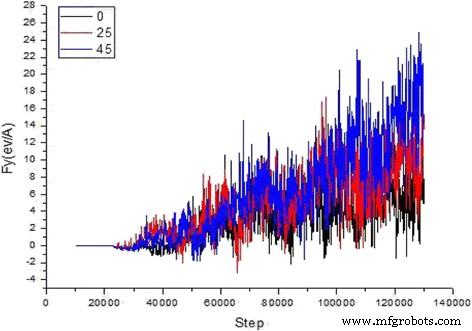
La relation entre la force de coupe, l'angle de coupe et l'étape de simulation
Afin de simuler la faisabilité et la crédibilité, nous choisissons une fonction de potentiel empirique raisonnable pour considérer les potentiels interatomiques des atomes. Selon les différents objets, nous pouvons diviser la fonction potentielle en fonction potentielle de paire et fonction potentielle à plusieurs corps. Les deux modèles entre le cuivre monocristallin et les grains abrasifs décrivent les potentiels interatomiques des atomes entre eux par le potentiel Morse [17], le potentiel EAM est utilisé pour décrire les potentiels interatomiques des atomes entre les atomes de cuivre [18,19,20], et le l'interaction entre les particules de SiC est décrite à l'aide du potentiel de Tersoff [21].
Pendant le processus de polissage, la direction de collision des grains abrasifs dans le milieu est aléatoire; leurs trajectoires ne sont pas exactement le long de la surface de la pièce. Pendant le processus de micro-découpe, la direction de coupe des grains abrasifs n'est pas toujours orthogonale au matériau de la pièce. L'angle de coupe fait référence au degré de l'angle entre la direction de coupe du grain abrasif et le plan horizontal. Il est positif lorsque les particules s'approchent de la surface de la pièce. Le croquis de l'angle de coupe est illustré à la Fig. 5.
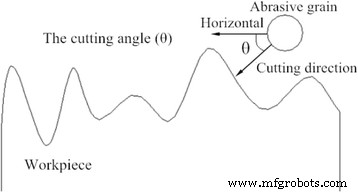
Le croquis de l'angle de coupe. La figure 5 est le croquis des différents angles de coupe lorsque les grains abrasifs sont coupés. Grain abrasif de différentes directions coupant le matériau de la pièce, le matériau aura les performances et la qualité de traitement sera différente
Dans cette étude, la simulation MD est utilisée pour simuler des multi-abrasifs avec différentes directions d'impact du cuivre monocristallin coupé. Comme le montre la figure 5, l'angle de coupe est compris entre 0° et 45° alors que la surface de la pièce en cuivre est rugueuse.
Résultats et discussion
Analyse de collision mécanique de coupe abrasive SiC
L'impact de l'abrasif en carbure de silicium sur la coupe du matériau en cuivre monocristallin est obtenu en détruisant la structure en treillis du monocristal du matériau en cuivre. Au cours de la rupture, les interactions entre les atomes de cuivre, la contrainte de cisaillement imposée par les atomes de C, Si des particules abrasives SiC sur les atomes de Cu du matériau de la pièce a été identifiée comme étant la force de coupe, qui est un paramètre physique important pour le fait que la force de coupe reflète profondément le processus d'élimination du matériau de la pièce en cuivre monocristallin. Comme indiqué précédemment, il existe une grande différence entre la force de coupe micro et macro. Généralement, la force de macro-coupe est la somme de la force de coupe et de meulage, tandis qu'en micro-coupe, la force de coupe est générée par les interactions entre les grains abrasifs et les atomes de la pièce.
Sur la figure 6, nous avons montré les changements de contrainte de cisaillement des grains abrasifs dans différentes directions, l'effet de la contrainte de cisaillement avec différentes directions et la répartition des forces de coupe le long de différents angles de coupe.
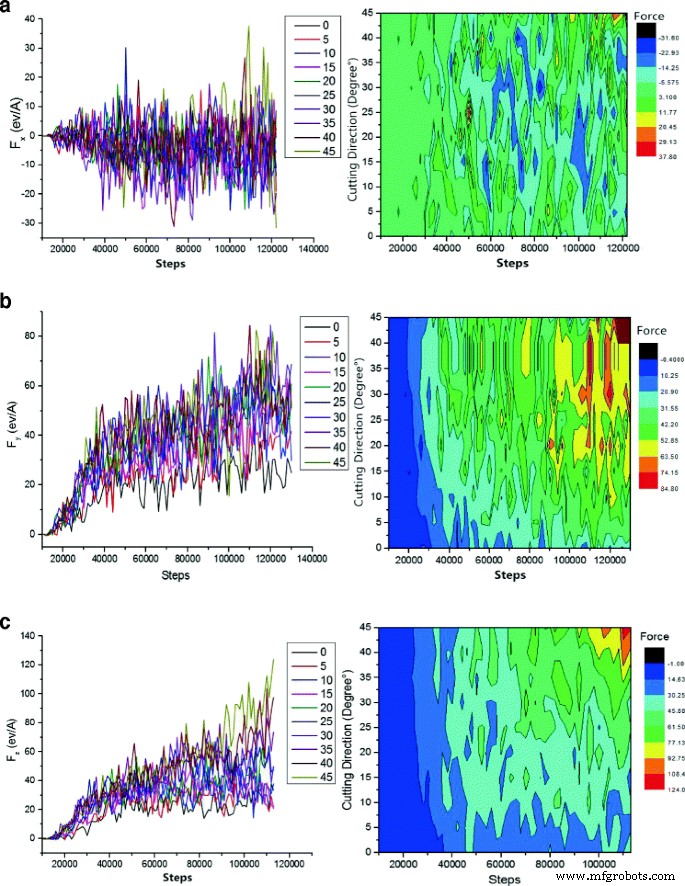
Comment l'angle de coupe et la taille du pas de simulation affectent la force de coupe. La figure 6 montre la force de coupe abrasive SiC et l'angle de coupe et le diagramme d'étape de simulation, avec l'augmentation de la profondeur de coupe, le nombre de la structure cristalline de destruction augmente, la valeur maximale de la fluctuation de la force de coupe devient également plus grande. un [100] direction de la force de coupe. b [010] direction de l'effort de coupe. c [001] direction de la force de coupe
Les grains abrasifs de carbure de silicium coupés et impactés sur un matériau de cuivre monocristallin dans différents angles de bord tels que [010] et [100]. Les forces de coupe suivant les directions [001] et [010] étaient des forces de cisaillement. Lors d'une simulation ultérieure, la profondeur de coupe a progressivement augmenté, ce qui a augmenté de manière persistante les forces de coupe le long des directions [001] et [010]. Cependant, jusqu'à une certaine limite, ces forces ont fluctué comme on peut le voir sur la figure 6. Lorsque des particules abrasives se sont déplacées vers les matériaux de la pièce, cela a totalement modifié l'interaction (de l'attraction à la répulsion) entre les atomes de cuivre les plus externes et les atomes de SiC (Si et C). Initialement, lors du meulage du matériau de la pièce, les forces de coupe étaient insuffisantes en raison de la présence de forces de répulsion des atomes de cuivre. Pour le processus de finition, les forces de coupe doivent être suffisamment élevées pour que les grains abrasifs puissent facilement rompre les liaisons chimiques des atomes de cuivre pour se déplacer librement. De plus, l'incrément de profondeur de coupe a des relations directes avec les interactions atomiques. Lorsque les atomes ont commencé à s'accumuler, la force de coupe augmente constamment jusqu'à ce que les particules abrasives pénètrent dans la pièce, ce qui nécessite une force de coupe stable. Dans cette étape relativement stable, la fluctuation de la force de coupe a été soumise au degré de déformation du réseau, à la reconstruction du réseau, au changement de phase amorphe et à la génération de copeaux. Au fur et à mesure que les grains abrasifs marchaient le long de la direction de coupe, une force externe a été appliquée à l'atome de cuivre dans le réseau FCC, ce qui a entraîné des déplacements des atomes de cuivre. Ce déplacement effondre le réseau FCC et le transforme en une nouvelle structure de réseau présentant une dislocation. Une situation similaire est également observée dans la force de coupe. Il n'y a pas de corrélation linéaire positive entre la force de coupe le long de la direction de [010] et l'angle de collision des particules. Dans la collision avec 0°, 5°, 10° et au-delà, la force dans la direction [010] était plus petite et moins fluctuante que celles dans les autres directions de coupe. En coupant à un angle plus petit, éliminez essentiellement les bavures car la bavure peut être définie dans une plage de hauteur de 3,5 ~ 15 Å. En comparant ces directions entre elles, si la profondeur de coupe est relativement plus petite, les dommages et la déformation de la structure cristalline seront modérés. Par conséquent, dans l'ensemble du processus de coupe, la force de cisaillement le long de la direction [010] a été maintenue plus petite, comme le montre le graphique de courbe de la figure 6b. Dans la dernière étape de la simulation, la force de coupe a atteint le minimum de 0°. On constate également que la force de coupe a une relation directe avec l'angle, comme le montre la figure 6c, ce qui peut être attribué au fait que lorsque la vitesse des particules atteint 80 m/s, un angle de coupe plus grand est obtenu. D'autre part, à la même étape de simulation, plus la vitesse du composant le long de la direction [001] est grande, plus l'angle est élevé, plus les particules sont coupées plus profondément et plus les réseaux atomiques sont détruits. Cependant, il y avait une corrélation positive entre l'angle de coupe et la force de coupe. Lorsque les grains se déplaçaient dans la direction [100], les frictions entre les atomes de C, Si et Cu étaient la source de la force de coupe. Ainsi, la force de coupe n'a pas montré une tendance à la hausse progressive. Cependant, lors d'une simulation plus poussée, la force de coupe a augmenté et fluctué, ce qui était étroitement lié à la déformation et à la reconstruction du réseau ainsi qu'à la génération d'une transition de phase structurelle amorphe. Avant que les particules abrasives ne puissent détruire, l'interaction entre les atomes de la pièce est réalisée pour éliminer le matériau, ce qui a finalement augmenté la force de coupe de manière cohérente. En augmentant la force de coupe abrasive, au-delà de la valeur critique (force de liaison atomique), le réseau atomique s'endommage et les liaisons se dissocient, ce qui donne une structure amorphe. En réalisant cela, la force de coupe est tombée à une valeur relativement faible. Les fluctuations de la force de coupe sont apparues en continu pendant tout le processus d'usinage par flux abrasif, ce qui est dû à l'augmentation de la profondeur de coupe, et une plus grande destruction de la structure cristalline a eu lieu. Ainsi, il est conclu qu'à ce stade, la valeur maximale de la fluctuation de la force de coupe était plus grande. Comme le montre la figure 6b, la région rouge a occupé une plus grande surface au cours de la dernière étape de la simulation, ce qui indique que la force de coupe a été nettement augmentée. Dans le même temps de simulation, la force de coupe était plus petite lorsque l'angle de coupe était inférieur à 15°, ce qui signifie qu'une petite partie du réseau cristallin a été détruite.
Analyse énergétique pour le processus de coupe par impact abrasif SiC
L'énergie totale thermodynamique est la somme de l'énergie potentielle totale et de l'énergie cinétique totale dans un système, ce qui révèle l'effet du travail effectué sur la pièce par les grains abrasifs. L'influence de l'angle de coupe sur l'abrasif en carbure de silicium sur le changement d'énergie du système est illustrée à la Fig. 7. Au cours du processus de coupe, des matériaux de pièce en cuivre monocristallin avec des grains abrasifs en carbure de silicium, le travail effectué par les grains abrasifs sur le matériau de la pièce agit de deux façons; une partie est convertie en énergie cinétique qui augmente la chaleur des atomes de cuivre monocristallins en contact avec les particules de carbure de silicium fonctionnant au polissage, l'autre partie est convertie en énergie potentielle qui permet des changements dans la structure interne de la pièce en cuivre monocristallin, la déformation du réseau et la libération d'énergie du réseau.
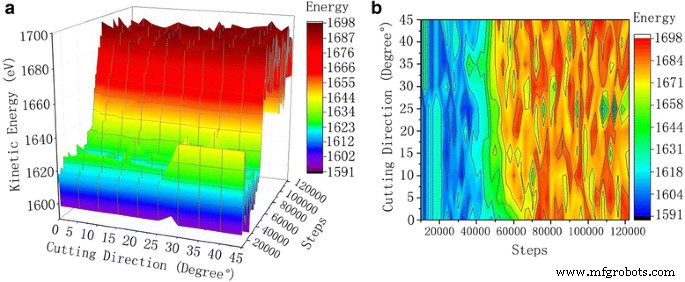
Courbe d'énergie cinétique des atomes de la pièce. La figure 7 est la courbe d'énergie cinétique des différents angles de coupe pendant le processus de coupe. Avec l'augmentation du nombre d'étapes de simulation, l'énergie cinétique des atomes fluctue dans une plage basse, puis dans une plage plus élevée au sein des fluctuations. un courbe 3D. b Contours
Dans le processus de coupe des grains abrasifs d'une pièce en cuivre monocristallin, l'énergie cinétique du système est étroitement liée au travail effectué sur le matériau de la pièce par les abrasifs SiC. En calculant la vitesse des particules dans le système à chaque instant, l'énergie cinétique totale du système peut être calculée :
$$ K=\sum \limits_{i=1}^N\frac{1}{2}{m}_i\left({v}_{\mathrm{ix}}^2+{v}_{\ mathrm{iy}}^2+{v}_{\mathrm{iz}}^2\right) $$ (1)Dans la formule, \( {v}_{\mathrm{ix}}^2 \), \( {v}_{\mathrm{iy}}^2 \) et \( {v}_{\mathrm {iz}}^2 \) représentent la composante de vitesse x , y , z atomes de direction, respectivement.
La courbe cinétique de la figure 7 nous a amenés à conclure que lors de l'incrémentation des étapes de simulation, l'énergie cinétique des atomes fluctue initialement dans une plage basse puis dans une plage plus élevée. Avec le mouvement des grains abrasifs, une interaction répulsive à longue distance se trouve entre les atomes de cuivre les plus externes et les atomes de Si, C (SiC). Les atomes de cuivre dans la pièce commencent à recevoir de l'énergie cinétique et à se déplacer. Lorsque les particules de carbure de silicium entrent en contact avec le monocristal de cuivre, la température atomique de la région de contact augmente, ce qui augmente le mouvement thermique atomique. Lorsque la coupe est stable, l'énergie cinétique des atomes de cuivre dans le matériau se transporte et se transforme en un modèle d'équilibre dynamique, et l'énergie cinétique des atomes fluctue dans une plage élevée.
L'analyse de l'énergie cinétique nous a amenés à conclure que pendant le processus de coupe, lorsque les particules commencent à entrer en contact avec la pièce, les atomes de la région extrudée subissent une déformation du réseau, les coordonnées atomiques changent et le déplacement change avec l'énergie cinétique. Lorsque les particules abrasives pénètrent dans le cuivre monocristallin, la valeur maximale de l'énergie cinétique de la pièce en cuivre monocristallin apparaît lorsque la pièce pénètre complètement dans la pièce. Parce que l'énergie cinétique et l'énergie potentielle des particules abrasives ne font que se transformer mutuellement. Cependant, l'énergie de l'ensemble du système ne changera pas, à l'exception des particules en mouvement qui pénètrent dans la pièce. De plus, le mouvement des particules de carbure de silicium force les atomes de la pièce à se déplacer simultanément avec elles. La chaleur générée lors du frottement atomique est libérée par l'énergie cinétique et l'énergie de déformation libérée en raison du mouvement de dislocation.
La conversion entre la chaleur et l'énergie cinétique est calculée par la formule suivante :
$$ \frac{1}{2}{\sum}_i{m}_i{v}_i^2=\frac{3}{2}{nk}_B{T}_i $$ (2)Dans la formule, n est le nombre d'atomes; vi représente la vitesse instantanée; k B est la constante de Boltzmann, et T i est la température des atomes.
La force de coupe augmente la température atomique de la zone où l'abrasif entre en contact avec le matériau de la pièce. En considérant le mouvement thermique de l'atome et l'énergie cinétique des atomes, l'énergie cinétique des atomes de cuivre augmente partiellement. Le système simulé est réglé sur l'ensemble canonique; la température globale du système fluctue dans une certaine plage. La chaleur produite lors de la coupe des particules abrasives est rapidement transférée à la couche d'atomes à température constante, de sorte que l'énergie cinétique globale du système change très peu.
Comme on peut le voir sur la courbe d'énergie potentielle de la figure 8, lors de l'augmentation du nombre d'étapes de simulation, l'énergie potentielle parmi le monocristal d'atomes de cuivre dans la pièce a également tendance à augmenter. Lorsque l'abrasif en carbure de silicium entre en contact avec le monocristal de la pièce de cuivre du début à la coupe entièrement stable, le matériau de la pièce s'est progressivement déformé et les atomes de cuivre se déplacent, ce qui conduit à la distorsion du réseau cristallin dans le cristal. Il en résulte également un champ de contrainte élastique, où l'énergie de déformation augmente. Lorsque l'énergie de déformation n'est pas suffisante pour réarranger les atomes matériels, la dislocation des atomes se produit, ce qui augmente l'énergie totale du système. Contrairement aux courbes de potentiel de 0° à 45°, on constate une constance du mouvement thermique des atomes à température constante. Il n'y a pas de relation significative entre l'énergie cinétique atomique et l'angle de coupe des grains abrasifs SiC. L'énergie cinétique des atomes est étroitement liée au mouvement thermique des atomes. Cependant, le changement d'énergie potentielle et d'énergie totale est évidemment lié à l'angle de coupe des particules abrasives de SiC. L'amplitude de l'énergie potentielle atomique augmente avec l'augmentation de l'angle de coupe. Lorsque l'angle de coupe est compris entre 0° et 20°, un changement évident d'énergie potentielle est observé. Cependant, lorsque l'angle de coupe est compris entre 25° et 45°, l'énergie potentielle reste telle quelle, et les courbes d'énergie potentielle globale sont de 0° à 20° d'angle de coupe. Comme le montre la figure 9, la tendance de l'énergie totale est similaire à celle de la courbe d'énergie potentielle. Les valeurs énergétiques totales de tous les angles de coupe sont très proches les unes des autres. En effet, l'énergie totale est égale à l'énergie potentielle et à l'énergie cinétique du système, tandis que l'énergie cinétique ne change pas en fonction de l'angle de coupe, pendant le processus de coupe. Le changement d'énergie cinétique de la pièce est très faible avec différents angles de coupe. Par conséquent, la courbe de changement de l'énergie potentielle est similaire à la courbe de l'énergie totale. En comparant les diagrammes de déplacement atomique de la figure 9, on peut constater que dans les mêmes conditions de coupe, la profondeur de coupe dans la pièce en cuivre monocristallin est plus grande lorsque l'angle de coupe est compris entre 25° et 45°, ce qui peut être attribué à l'augmentation du déplacement d'atomes de cuivre. Le long de la direction [001] des particules de SiC, davantage de dommages atomiques dans le réseau et de dislocations sont générés. L'énergie de déformation produite pendant ce temps est plus élevée, ce qui entraîne une courbe de changement d'énergie potentielle élevée et une courbe de changement d'énergie totale des atomes de la pièce.
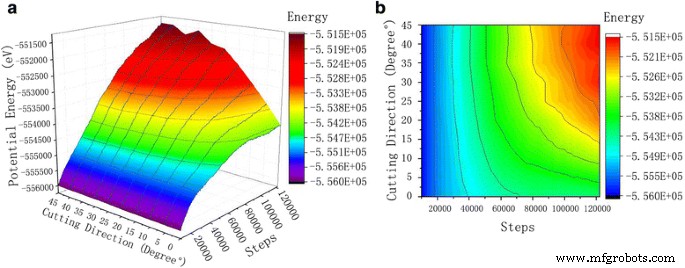
Courbe d'énergie potentielle de la pièce. La figure 8 est un graphique des variations d'énergie potentielle à différents angles de coupe pendant le processus de coupe. Avec l'augmentation du nombre d'étapes pour la simulation, le potentiel entre les atomes de cuivre monocristallins présentent une pièce à usiner a tendance à augmenter. un courbe 3D. b Contours
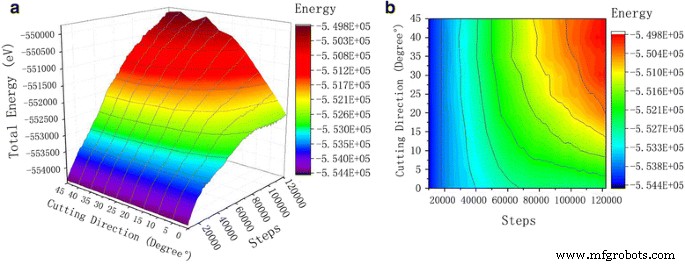
Courbe d'énergie totale. La figure 9 montre la courbe d'énergie totale. Au cours du processus de découpe SiC de la pièce en cuivre monocristallin, l'effet des grains abrasifs sur la pièce se manifeste sous deux formes :dont une partie est convertie en énergie cinétique, la chaleur atomique est augmentée et l'énergie cinétique locale devient plus importante lors du polissage la zone de jonction de la pièce en cuivre monocristallin et des particules SIC ; l'autre partie est convertie en énergie potentielle, la structure interne de la pièce en cuivre monocristallin est modifiée, le réseau est déformé et l'énergie du réseau est libérée et transformée en énergie potentielle. un courbe 3D. b Contours
Analyse du déplacement atomique dans le processus de coupe par collision de particules abrasives SiC
Lors du processus de coupe du matériau de la pièce sous différents angles, les grains abrasifs se déplacent dans la direction de coupe, forçant les atomes de cuivre dans la pièce à se déplacer. À partir de l'analyse de la direction de déplacement de la pièce, l'effet des grains abrasifs sur le matériau de la pièce, la façon dont la forme des copeaux et l'enlèvement de matière sont complètement clarifiés. Selon la méthode d'analyse de l'angle de liaison, proposée par Ackland-Jones, différentes structures de réseau atomique sont marquées par des couleurs diversifiées, à des fins d'observation et d'analyse. Le plan ZOY est sélectionné pour observer le processus de coupe d'une particule de SiC individuelle, et le diagramme de déplacement atomique de la zone de coupe est agrandi, comme le montre la figure 10.
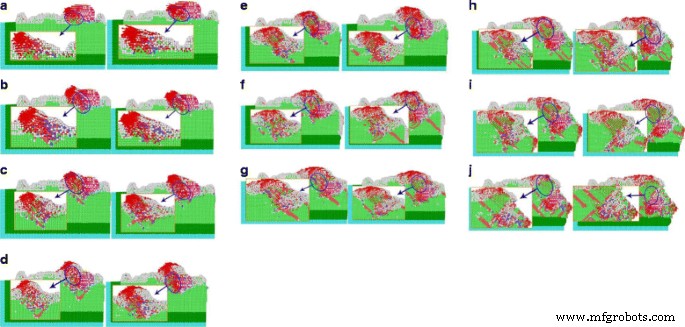
Des angles de coupe différents provoquent des déplacements atomiques. La figure 10 décrit les déplacements atomiques de différents angles de coupe. Lorsque les particules abrasives monocristallines SiC entrent en collision avec la pièce coupant le cuivre dans différentes directions, avec des grains abrasifs SiC coupés, la profondeur de coupe augmente, puisque la vitesse de la direction de coupe est à 80 m/s, la direction [001] La vitesse de déplacement est v z = 0.8 ∗ sin θ , avec l'augmentation de la profondeur de coupe de l'angle de coupe, [001] dans le même angle de coupe augmente les étapes de simulation, la profondeur de coupe est grande en même temps. un 0° de déplacement. b 5° déplacements. c 10° de déplacement. d 15° de déplacement. e 20° de déplacement. f 25° de déplacement. g 30° de déplacement. h 35° de déplacement. je 40° de déplacement. j Déplacement de 45°. (couleur atomique : Structure HCP,
Structure BCC,
Configuration FCC en tant que structure amorphe blanche)
Lorsque les particules abrasives monocristallines SiC entrent en collision avec la pièce coupant le cuivre dans différentes directions, la profondeur de coupe augmente tout au long du processus. La vitesse de la direction de coupe est de 80 m/s, où la vitesse du composant dans la direction [001] est v z = 0.8 ∗ sin θ . At the same simulation step, cutting depth increases with increasing the cutting angle. As shown in Fig. 10, there is an atomic position shift in both of the surface and interior of the workpiece material, contacting with the abrasive grains, where atoms of different lattice types are arranged and doped with each other. Due to the movement of these abrasive particles, the copper atoms accumulated at the tip of the abrasive grains, which results no cracks during abrasive particles cutting. It can be seen that the material removal mode of the abrasive particles is plastic deformation. At the same time, due to abrasive cutting, the atoms displacement in single crystal copper increases from 15° to 45°.
The number of the workpiece atoms along the abrasive grain motion direction also increases, and the atomic displacement is perpendicular to the direction of abrasive cutting. This part of the atomic displacement is due to that of the abrasive particles, change the cutting action to the extrusion upon the workpiece atoms. At cutting angle, the abrasive particles is between 0° and 10°, while the cutting depth is smaller than those of the 15° to 45°. Abrasive particles are performing mainly the cutting function, the extrusion of the workpiece atoms is marginal, and the number of atoms is small whose displacement direction is perpendicular to the direction of the abrasive grain motion. With the repeated cutting on the workpiece surface by numerous abrasive particles, the abrasive particles having large cutting angle produce deep pits on the workpiece material during the whole cutting process, while ones following smaller cutting angles will continue cutting along the cutting mark produced by the former. Under the combined action, the workpiece material is cut to a certain depth (micro-cutting) followed by whole abrasive flow polishing.
Dislocation Collision Analysis for SiC Abrasive Cutting
Dislocation is a special arrangement of atoms in crystal along certain crystal surface and crystal direction, or a boundary between the slip zone and the non-slip zone on the slip surface. Dislocation can be divided into edge dislocation, spiral dislocation, and mixed dislocation, among which mixed dislocation is most common. In the process of abrasive particle cutting, the single crystal copper workpiece is plastically deformed, the atoms move, and the crystal lattice breaks and reconstructs, which results in a large number of dislocations. The analysis for dislocation and bond angles at different incidence angles is shown in Fig. 10. In the simulation model of abrasive flow simulation, two abrasive particles are used for cutting the workpiece material. For ease of analysis, the generation and change of different dislocation lines in single crystal copper material, during cutting process and the different lattice structures in the cutting part are analyzed in the view of one single SiC particle on the YOZ surface, as shown in Fig. 11.
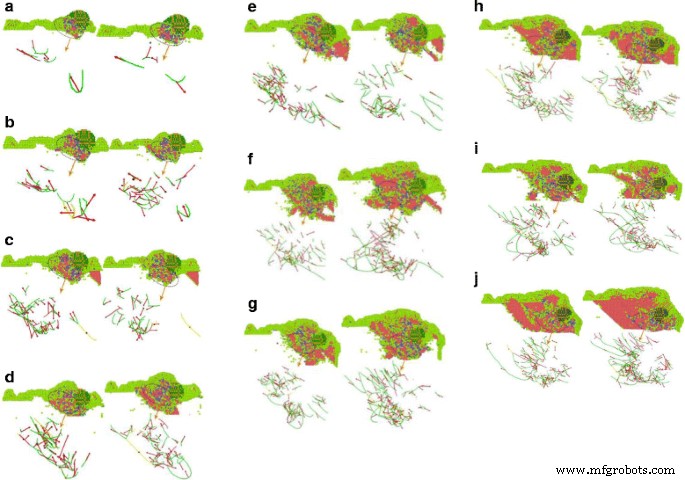
Different angles-bond angle dislocation line charts. Figure 11 represents the cutting dislocation line and the bond angle. As the repeated cuttings on the workpiece surface are done by the numerous abrasive particles during the polishing process, in the entire cutting process, the abrasive particles with larger cutting angle produce bigger pits, while the following abrasive particles with smaller cutting angles continue to polish along the cutting trace. Therefore, certain depth is done on the workpiece material and the whole micro-cutting of abrasive flow polishing is achieved. un Dislocation lines with 0° cutting angles. b Dislocation lines with 5° cutting angles. c Dislocation lines with 10° cutting angles. d Dislocation lines with 15° cutting angles. e Dislocation lines with 20° cutting angles. f Dislocation lines with 25° cutting angles. g Dislocation lines with 30° cutting angles. h Dislocation lines with 35° cutting angles. je Dislocation lines with 40° cutting angles. j Dislocation lines with 45° cutting angles. (Note:the upper part of the key angle analysis, the figure in the atomic color: HCP
BCC
Amorphous structure
Abrasive grain; the lower part of the dislocation line diagram, the figure dislocation line color:
Stair-rod,
Shockley,
Hirth,
Perect,
Frank,
Burgers vectors)
Key angle analysis diagram of each cutting angle is shown in Fig. 11, where the sample from the interior workpiece simulation at time 60 and 70 ps, the atoms are colored individually according to different arrangement of atoms through BAD technology. To facilitate the analysis of the lattice changes in the cutting part, atoms of the FCC structure in the workpiece material are removed. By DXA techniques, different types of dislocations are marked in diverse colors:red arrow indicates the Burgers vector (Burgers vectors), green for Shockley partial dislocations (Shockley), light blue for the Frank partial dislocations (Frank), pink pole position for the pressure error (Stair-rod), and blue for the whole dislocation (Perfect).
As can be observed from the analysis of the bond angle portion in Fig. 11, a large number of dislocations and lattice deformations occurred under the impact of external cutting forces. The bond angle analysis shows that the internal HCP structure of the workpiece appears more clearly with increasing of cutting angle. On further simulations, the structure of HCP increases gradually. The silicon carbide particles continuously cut and squeeze the workpiece material at 80 m/s speed, resulting in a phase transition from the FCC structure to the HCP structure. During this phase transition, the atomic strain of the workpiece continues to increase. However, when the stress state of atoms of the workpiece has exceeded the threshold of thermodynamic phase transition, it turns to metastable state. As the strain increases, the HCP phase begins to nucleate and grow spontaneously, and the FCC lattice of copper undergoes absolute destabilization, which induces a sudden change in mechanical quantities. As the kinetic energy of the atom is directly related to the atomic temperature (formula 1), there is a saltatory augment in the kinetic energy change curve, as can be seen from Fig. 7. This is due to high strain energy, accumulated in the single crystal copper workpiece before the nucleation of HCP. The HCP structure increases the system temperature through metastable nucleation and partial stress release. Due to the abrasive cutting and extrusion, bonds of copper atoms in workpiece material break down which results in disorder. The original regular lattice structure is broken, where the partial copper atoms gradually change into disorder and form an amorphous structure. It can be seen from the bond angle analysis diagram that (Fig. 11) atoms with relatively disordered displacement tend to form amorphous structures at 60 and 70 ps, which is because of silicon carbide abrasive particles. At the same time, many atoms with the same displacement direction are transformed into HCP structures. Meanwhile, the particles shear downward and the atomic structure is rearranged due to the displacement of atoms in the original amorphous structure, results an amorphous structure of HCP. Atoms that have already been transformed into HCP structures, even before the next cut stage, change back into amorphous structure. As the cutting depth increases, the number of amorphous atoms near the abrasive particles also increases.
When the FCC crystal structure undergoes cutting by abrasive particles, a shear stress generates in atoms, which results in the displacement of atoms in the lattice and the arrangement of various lattice structures. In moving the atoms of workpiece, the rigid displacements of the atoms produce dislocations, also called as dislocation lines (Fig. 11). Dislocation line can be termed as the boundary between the slip zone and the non-slip zone, on the slip surface. According to the relation between the dislocation and the PATS vector, dislocation is parallel to the PATS vector, called the screw dislocations. The vertical ones are edge dislocations, and the mixed dislocations are neither parallel nor vertical. In Fig. 11, most of the dislocation lines are neither parallel nor vertical to PATS vectors, which are typical mixed dislocations. In the cutting process of abrasive particles, the dislocation line changes, moves and grows around the abrasive particles. The closer the particle, the greater the density of the dislocation line. Dislocation lines are also very dense, when the arrangement of atoms is complicated. The abrasive particles marked as orange, produce a large amount of HCP, BCC, and amorphous structures around them, which interlace and blend with each other to form dislocations that increases the internal energy of the crystals. When atoms arrange their self just like shown in Fig. 12b, possess maximum potential energy. While for the arrangement, shown in Fig. 12a–b, the atoms situate at the lowest potential energy position. The number of dislocation lines is directly related to the magnitude of strain energy of the crystal. The total strain energy of the unit length dislocation can be measured with the given formula:
$$ W=\alpha {Gb}^2 $$ (3)
Schematic view of dislocation changes. Dislocation is a special arrangement of atoms in crystals. It is the crystal in the atomic arrangement along a certain crystal face and crystal orientation occurred in a certain wrong line, and it is the boundary of the slip surface within the area where the slip has occurred and the area with no slip has occurred. In Fig. 12a –c , the relative displacement of the rigidity of the upper atom and the underlying atom produce dislocations, the upper atom belongs to the sliding region, and the lower atoms belong to the non-slip region, they are in the slip surface of the intersection line which is called dislocation line, that is, dislocation. Figure 12 is the process of dislocation generation and development
Where, α is the geometric factor (type dislocations, dislocation density) parameter related to, and generally 0.5 ~ 1.0; G is the shear modulus, and b is the slippage distance.
When the workpiece material is being cut, particles break the atomic arrangement and the lattice reconstructs, which constitutes, macroscopically, the plastic deformation of the workpiece material. In the process of plastic deformation, the dislocation was supposed to escape from the crystal and decrease the dislocation density. However, this dislocation density increases due to dislocation propagation. There are many ways of dislocation multiplication and the main one is the Frank–Reed dislocation source theory, of which the growth mechanism is shown in Fig. 11. As illustrated in Fig. 11, the density of the dislocation line increases markedly from 60 to 70 ps when the cutting simulation proceeds, change both the number and shape of dislocation lines in accordance with Frank–Reed dislocation source theory. At simulation time of 60 ps, there are many long Shockley dislocations. But after another 10 ps simulating, the long Shockley dislocation line becomes less and shorter. The original straight dislocation lines turn into bent, which is especially evident near the abrasive grains. From formula 3, the strain energy of the dislocation is proportional to b 2 . From the viewpoint of energy, the dislocations with the smallest b in the crystal should be most stable with low energy; however, dislocations with larger b will break down into ones. In addition, the energy of the dislocation is valued by the unit length of the dislocation line. Given the shortest line between two points is the straight, the strain energy of straight dislocation is lower than that of the bent one, means straight dislocations are more stable. Frank–Reed dislocation source theory argued that the long dislocation line becomes shorter and breaks down into smaller dislocations, thus decreasing the strain energy of the crystal.
Analysis for Friction Coefficient Between Workpiece Surface and Abrasive Particles
To quantitatively disclose mechanical properties and surface effect of SiC abrasive cutting single crystal copper material, the tangential force ([010] direction) and normal force ([001]direction) on the cutting surface are further analyzed. The friction coefficient can be defined as the ratio of the tangential force to the normal force, with the formula below:
$$ f=\frac{F_y}{F_z} $$ (4)Figure 13 shows the variation of friction coefficient along different cutting angles during abrasive cutting. The change of friction coefficient can be divided into two periods. Period I, when the cutting distance is less than half of the size of the abrasive particle, the friction coefficient fluctuates violently in certain range due to surface effect of the material; while in period II, all the friction coefficients fluctuate in very small range, and the friction coefficients remains steady state at different angles. However, at cutting angle of 5°, there is a small amount of abnormal fluctuation at the end of simulation. Moreover, in period I, abrasive particles contact the workpiece atoms to the abrasive grains enter into the workpiece of half abrasive diameter (shown in Fig. 13b), the cutting movement distance reaches 7.5 Å. In Fig. 6, the cutting force change curve shows that the tangential force and normal force are in an oscillating phase during period I. Since the friction coefficient can be characterized as the adhesion among atoms in the contact surface and is related to the two atoms contacting with each other, regardless of the cutting mode, which can interpret the phenomenon that change of cutting angle does not cause significant change of friction coefficient, as shown in Fig. 13a.
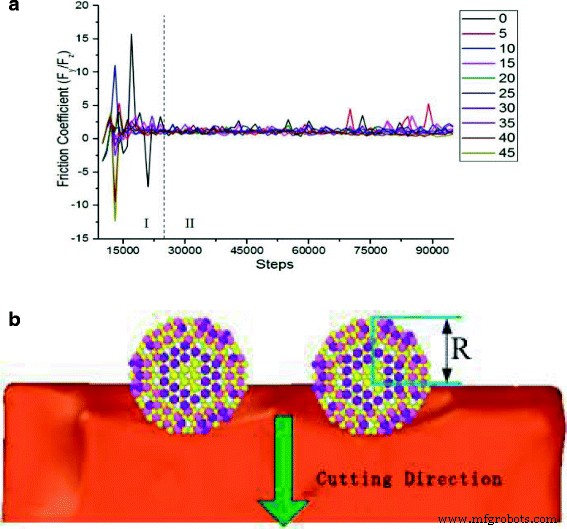
Friction coefficients of different cutting angles. Figure 13 is the changes of the frictional coefficients during SIC particles cutting single crystal copper from different angles. The change in cutting angle did not cause significant changes in friction coefficient. It described two kinds of coefficient of friction in contact with the relevant atoms in the cutting process, regardless of the cutting mode. un Friction coefficient variation curve with cutting angle. b Instantaneous structure when SiC abrasive grains move 7.5 Å
Conclusions
The micro cutting simulation of single crystal copper by SiC abrasive particles is achieved during abrasive flow polishing. Comprehensive analysis of the SiC abrasive cutting reveals that when SiC abrasive particles cut at angle from 0° to 15°, cutting forces in along Y and Z direction are relatively small and tend to stay steady. A larger cutting angle results more dislocations, which brings about larger grooves damaging of the workpiece material. In the process of cutting, it is necessary to avoid more dislocations, which has an immediate adverse effect on the performance of all aspects of crystal material. Therefore, a cutting angle of 0° is better than other angles. Considering the amount of dislocation produced, or the change of cutting force and energy in the cutting process; cutting with small or medium angles is not only beneficial for improving surface quality but reduce the internal defects.
Nanomatériaux
- Effet de surface sur le transport du pétrole dans les nanocanaux :une étude de dynamique moléculaire
- Modélisation et simulation de dynamique moléculaire de la coupe de diamant de cérium
- Toxicité des nanoparticules de CoFe2O4 enrobées de PEG avec effet thérapeutique de la curcumine
- Étude des comportements de frottement à l'échelle nanométrique du graphène sur des substrats d'or à l'aide de la dynamique moléculaire
- Dépendances de la température et de la pression des propriétés élastiques des monocristaux de tantale sous charge de traction <100> :une étude de dynamique moléculaire
- Synthèse et étude in vitro d'une sonde bimode ciblant l'intégrine αvβ3
- Usinage et découpe au jet d'eau abrasif
- Avantages du processus de découpe au laser
- Avantages et inconvénients de la coupe abrasive