La formation d'un leader de l'industrie du thermoformage.
Hytech fournit des solutions pour le thermoformage, le gaufrage et le rognage des plastiques à couches minces. Ils se concentrent principalement sur les pièces en plastique à couche mince nécessitant un repérage graphique précis. Il existe également des applications non graphiques où les procédés de formage Hytech offrent des avantages par rapport aux autres procédés de formage traditionnels. Leurs technologies brevetées sont utilisées par les équipementiers des secteurs automobile, électroménager, médical, aérospatial et militaire.
Développer des procédés brevetés et faire progresser le thermoformage et faire correspondre les matrices de garniture métallique
Aujourd'hui, Hytech dispose d'installations de fabrication offrant des services de production et d'outillage aux États-Unis et en Europe et fournit le développement de processus et l'équipement depuis son siège américain à Phoenix AZ.
Hytech a demandé à Rogers pourquoi le dôme n'était pas en plastique. Ils ont découvert que personne ne fabriquait le dôme en plastique. Ainsi, la première chose qu'ils ont faite a été d'inventer une technologie de thermoformage spécialisée pour gaufrer un dôme en polyester et a vendu des millions de ces dômes à Rogers Corporation, puis a vendu des dizaines de millions d'entre eux à Hewlett Packard pour leur gamme de produits financiers. ou des calculatrices scientifiques. Les avantages de production (par rapport aux dômes métalliques) sur des pièces telles que les interrupteurs à membrane sont que vous pouviez poser 100 dômes en plastique sur une seule feuille, alors qu'avec les dômes métalliques, vous deviez choisir et placer les 100 dans l'emplacement.
Lorsque Hytech a commencé à vendre ces couches de dôme aux fabricants d'interrupteurs à membrane, les fabricants d'interrupteurs à membrane ont déclaré :"C'est vraiment génial, mais j'ai des problèmes pour gaufrer mes superpositions pour passer par-dessus vos dômes." Ainsi, les fondateurs de Hytech ont inventé une autre technologie de formage appelée hydroformage où ils ont gaufré les superpositions. À ce stade, ils disposaient d'une technologie pour gaufrer la superposition d'un interrupteur à membrane et ils avaient une technologie pour gaufrer la couche tactile qui se trouve sous la superposition.
Match Metal Trim Die Process :le développement et l'avancement continus de la technologie brevetée de Hytech en ont fait un expert mondial du tridimensionnel
assortissez les matrices de garniture en métal pour le plastique à couche mince.
Au milieu des années 90, la technologie de la décoration dans le moule (IMD) ou de l'étiquetage dans le moule (IML) ou du moulage par insertion de film (FIM) est apparue qui prend un plastique plat sérigraphié (généralement du polycarbonate) et le forme dans la forme 3D d'un moule à injection. Le film décoratif est placé dans le moule, le moule est injecté et lorsque le moule s'ouvre, la pièce est décorée.
Cela a coïncidé avec l'époque où Hytech disposait des procédés d'hydroformage et de polydôme. Les clients sont venus les voir et leur ont demandé de gaufrer du plastique pour cette nouvelle technologie de moulage par insertion de film. Ils ont rapidement découvert qu'aucun de leurs processus n'était adapté pour faire quoi que ce soit de plus profond que 1 mm. L'avantage de la décoration dans le moule est que vous pouvez créer des pièces 3D complexes avec des graphiques enregistrés. Ainsi, les fondateurs, avec un autre ingénieur nouvellement embauché, ont développé Accuform - une technologie de formation d'air à haute pression qui leur permet de faire jusqu'à 50 mm de profondeur d'étirage avec des graphiques enregistrés. Désormais, ils peuvent conserver la position, l'emplacement et la taille de différents graphiques sur des surfaces tridimensionnelles complexes.
Cela a abouti à des pièces de construction Hytech pour l'industrie IMD. Ils ont rapidement découvert que même s'ils pouvaient facilement et continuellement construire les outils de forme, ils avaient du mal à construire des matrices de garniture en métal assorti. À l'époque, personne au monde ne fabriquait d'outils de coupe tridimensionnels en métal assorti pour les plastiques à couches minces. Hytech a donc dû développer cette technologie elle-même.
Au début, ils sous-traitaient les composants en acier trempé à des fournisseurs qui les produisaient avec des électroérosions à enfonçage. Cela a amené Hytech à croire qu'ils devaient investir dans un électroérosion par enfonçage et faire le travail en interne. Ainsi, en plus de l'électroérosion par enfonçage, ils ont également investi dans une électroérosion à fil et dans un tout nouveau logiciel et ont commencé à construire leurs propres outils de découpe. Aussi bons qu'ils aient réussi le processus, ils savaient que ce serait bien mieux s'ils pouvaient enlever un autre dixième du périmètre de l'acier trempé. Ils savaient qu'ils ne pouvaient pas le faire sur leurs centres d'usinage actuels car ils ne pouvaient pas tenir ce genre de tolérance. Le PDG de Hytech, Fred Himmelein, explique :"Au fil des ans, nous nous sommes améliorés de plus en plus, puis nous avons atteint notre maximum. Nous ne pouvions tout simplement pas obtenir la précision, les dixièmes que nous voulions. Nous voulions avoir un jeu entre les composants en acier trempé de +/- 0,0003", mais nous ne pouvions tout simplement pas y arriver avec l'équipement d'EDM et de VMC par enfonçage que nous avions. C'est ce qui nous a conduits à DATRON."
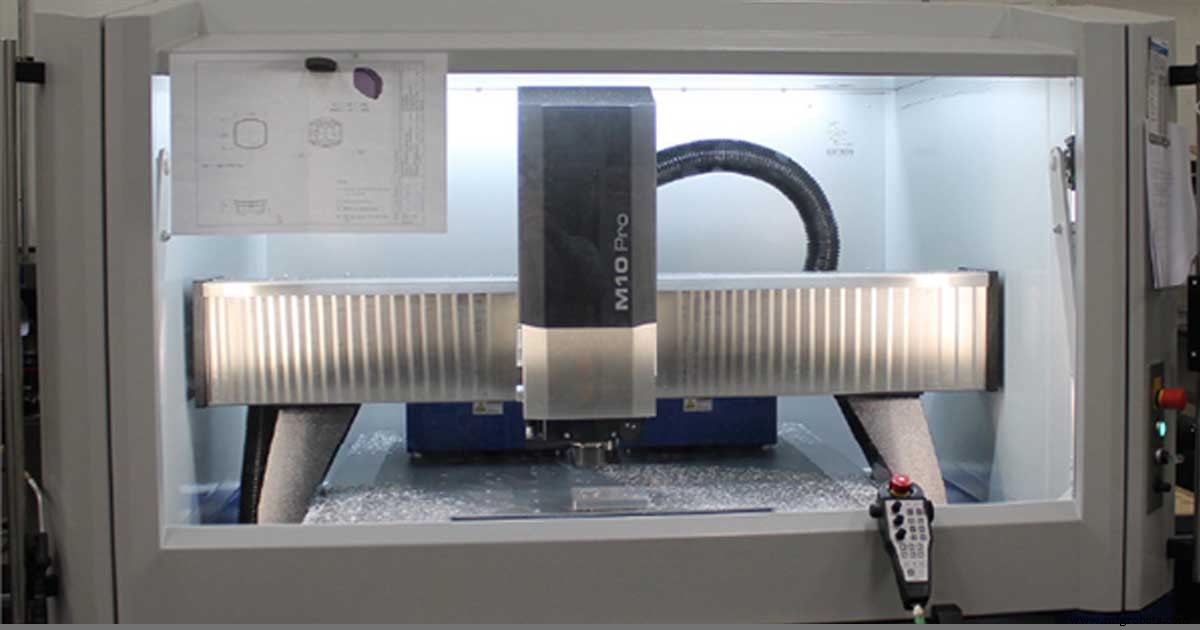
Recherche de technologies avancées pour le thermoformage et la finition de surface parfaite
Le chef de l'atelier d'outillage de Hytech, Dave Blandino, a fait des recherches et des analyses très approfondies des centres d'usinage disponibles et a présenté plusieurs solutions différentes à la pointe de l'industrie à l'équipe de direction. Finalement, il a été décidé d'acheter un centre d'usinage à grande vitesse DATRON M10 Pro. Himmelein explique, "Pour une combinaison de raisons telles que la précision, le logiciel de contrôle (programmation CN), le coût de la maintenance de la broche, le support et l'emplacement du support, Dave l'a décomposé en une matrice d'environ 10 ou 12 éléments, et cela nous a clairement montré que DATRON était le bon choix.”
Mais le choix d'acheter le DATRON ne s'est pas uniquement basé sur cette matrice. Il y avait également un processus de ruissellement ou d'analyse comparative que chaque fabricant de machines devait compléter - chacun produisant exactement la même pièce pour une comparaison concurrentielle. Alors que la capacité à fraiser les applications IMD de l'acier était l'un des paramètres, la finition de surface pour le côté formage de leur activité était d'une importance primordiale dans ce test. C'est parce que leur technologie de formage à haute pression est si précise que toutes les marques d'outils seront visibles sur la feuille de forme même si elles ont été sablées. Himmelein explique :"Vous pouvez regarder un noyau de forme sur lequel nous allons former, il a été sablé et il est magnifique et la finition est superbe, mais lorsque nous le formons, vous verrez une marque d'outil qui vous ne pouvez pas croire." À l'époque, une grande partie du travail qu'ils effectuaient consistait à créer des logos d'entreprise tridimensionnels très précis sur le dessus d'une pièce formée. De toute évidence, l'apparence de chaque logo était d'une grande importance pour le client qui les engageait pour le travail. Himmelein élabore, "Cela la pièce de forme est l'insert qui va dans le moule d'injection. Il s'agit d'un appliqué ou d'un film formé qui entre dans le moule d'injection et qui est à nouveau moulé de sorte que lorsque le moule s'ouvre, la pièce est décorée. Les cosmétiques de ces pièces sont absolument critiques et c'est une exigence cosmétique aussi stricte que celle qui existe dans la fabrication. »
Le directeur de l'outillage Hytech, Dave Blandino, explique plus en détail son expérience avec les fournisseurs de CNC et le test d'analyse comparative :"Nous avons effectué des recherches approfondies et donné à plusieurs fabricants de CNC l'occasion de découper une pièce pour nous. Je leur ai demandé de mettre une pièce devant moi qui vendrait leur machine et personne ne s'est approché de la pièce produite par DATRON. J'ai reçu des pièces d'autres fabricants de machines-outils et la qualité n'a pas répondu à mes attentes. Mais dans les 2 semaines suivant l'envoi du modèle à DATRON, je me suis envolé pour l'Allemagne, et non seulement l'hospitalité était excellente, mais DATRON a mis devant moi une partie à laquelle je ne m'attendais vraiment pas compte tenu du court délai. C'était de loin le meilleur de ce que tous les fournisseurs de CNC produisaient. Quand je suis revenu aux États-Unis et que j'ai montré l'échantillon DATRON aux autres vendeurs, ils ont dit :"Oh, ils ont peaufiné ça." et j'ai dit :"Non, ils ne l'ont pas fait, c'est juste sur la machine !", mais ils ne l'ont pas fait. Crois moi. Le fait est que nous avons méticuleusement inspecté chaque pièce sur un comparateur optique RAM avec un grossissement de 200+, donc ce n'est pas seulement ce que vous voyez avec vos yeux ou une loupe. Notre processus montre tout et n'importe quoi. Dans le thermoformage, si vous avez la moindre marque d'outil, elle apparaîtra dans le film. Il est donc extrêmement important d'avoir la finition de surface que nous offre le DATRON. »
Outre la qualité, il existe des économies de coûts correspondantes associées à l'élimination des opérations secondaires telles que le travail manuel, le ponçage et le polissage et Himmelein attribue à DATRON une réduction de 90 % du temps passé à la main. Il y a aussi des limites au ponçage comme l'explique Blandino, "Vous pouvez toujours faire du travail manuel avec du papier de verre, mais quand vous avez un outil qui est multiple cavité, vous n'allez pas poncer la pièce deux fois de la même manière. Si vous avez 15 à 20 cavités, vous allez avoir des variations et ces variations se traduisent par le formage, la coupe et le moulage. Ce que nous faisons essentiellement, c'est retirer la pièce du DATRON et nous ne la touchons pas et c'est notre objectif. Les pièces sont prêtes à être assemblées dans nos assemblages d'outillage dès la sortie de la machine. Parfois, une texture de grenaillage léger est une exigence du client, mais aucun ponçage ou polissage n'est nécessaire."
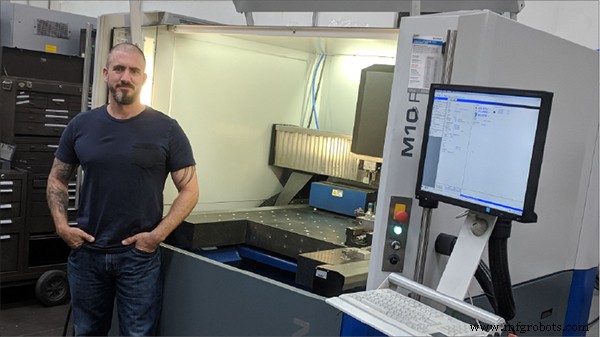
Haute tolérance requise pour la production de matrices de garnitures métalliques assorties (matrices d'estampage)
Alors maintenant, Hytech utilise son électroérosion à fil pour fabriquer le composant en acier trempé côté A qui représente sa tolérance fixe. Ensuite, ils fabriquent le composant en acier trempé du côté B qui est le composant d'accouplement avec la pièce du côté A. Ils laissent généralement le noyau de la matrice entre 0,0005" et 0,0008" et utilisent le DATRON M10 Pro pour prendre un dixième à la fois jusqu'à ce qu'il s'adapte. Himmelein dit :"C'est là que le DATRON brille vraiment parce que nous pouvons faire un dixième à la fois assez rapidement, ouvrir la porte en laissant tout monté et tester notre ajustement et si ce n'est pas là, nous fermons la porte et courons un autre dixième ."
La combinaison de l'électroérosion à fil et de la machine DATRON a vraiment fait la différence pour Hytech Forming et ils sont devenus l'expert mondial des matrices de garnitures métalliques en 3 dimensions pour les plastiques à couches minces.
Blandino explique : « Avant, nous devions sous-traiter ces composants à des ateliers qui disposaient de l'équipement pour pouvoir gérer cela et depuis que nous avons acheté le DATRON, nous avons fait tout ce travail en interne. Nous effectuons des passes de finition légères pour maintenir des tolérances serrées sur nos pièces en acier A2 traitées thermiquement. Ces pièces sont des composants d'outillage que nous concevons et fabriquons ici. L'une des visions de notre entreprise est le rognage. Nous sommes dans le thermoformage de plastiques à couches minces, mais l'autre côté de cela est que nous devons couper le plastique une fois qu'il est formé et ces formes coupées doivent s'adapter exactement au moule avec des tolérances serrées de +/- quelques millièmes de un pouce. Mais, pour que la coupe se produise réellement, les tolérances des composants que nous usinons doivent être de +/- quelques dixièmes de pouce. Ce sont les composants que nous utilisons pour construire nos matrices de garniture."
Blandino attribue également à la technologie DATRON l'ajout de flexibilité à leur processus de conception. "Cela nous a également permis de concevoir nos outils beaucoup plus efficacement. Avant, le seul équipement que nous pouvions utiliser pour maintenir ces tolérances serrées était notre fil EDM. Bien sûr, le problème avec le fil EDM, c'est que tout n'est pas traversant poche. Donc, cela a limité notre flexibilité de conception parce que nous avons dû concevoir autour de cette limitation. Avec le DATRON, nous sommes en mesure de concevoir plus librement et de faire les choses comme nous le voulions."
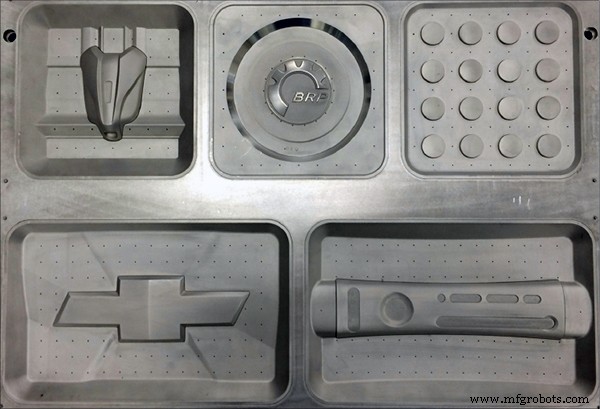
Le DATRON M10 Pro est devenu si critique pour la qualité de leur produit final et Blandino dit qu'ils se le rappellent chaque fois que le DATRON est en attente de travail et qu'ils sont obligés de déplacer le travail vers d'autres équipements CNC. "Même avec le travail manuel, vous ne pouvez pas vous approcher de la finition de surface que nous obtenons sur le DATRON. De plus, nous sommes au maximum de la vitesse de broche à 15k 12k et 10k sur les autres équipements CNC, nous devons donc réduire nos avances de 100 %. En raison de la vibration de la broche et du jeu sur le vis à billes avec nos autres centres d'usinage, la finition que nous devons faire est un ponçage lourd. C'est pourquoi je pousse vraiment pour une deuxième machine DATRON. Nous utilisons les autres centres d'usinage comme notre « machine Op One » où nous dégrossissons toute la viande à l'arrière et toutes les surfaces non critiques. Ces machines gèrent bien cette tâche."
Ouvrir les portes à une nouvelle source de revenus et à une augmentation de 25 % des revenus annuels Revenu
Le PDG, Fred Himmelein, rend hommage à DATRON pour la qualité qu'il a aidé Hytech à offrir à un large éventail d'industries, notamment l'automobile et l'aérospatiale. Himmelein est également impressionné par la flexibilité du DATRON et des autres processus auxiliaires qu'il a impactés et améliorés depuis son installation. Par exemple, ils ont un projet qu'ils font pour un client depuis une décennie où ils ont coupé de l'acrylique de 0,25" avec un laser CO2 qui fait un excellent travail en produisant un bord magnifiquement poli. Mais, après une décennie, le client a décidé de changer de matériau et d'utiliser du polycarbonate pour réduire le risque d'endommagement des pièces tout au long de leur cycle de vie. Étant donné que le polycarbonate de 0,25 pouce ne peut pas être découpé au laser sans qu'il brûle et présente un risque pour la santé, ils ont dû trouver un procédé alternatif. Ils ont donc effectué une coupe d'essai sur le DATRON M10 Pro à l'aide d'une fraise en bout DATRON spécialement conçue pour le fraisage de l'acrylique. Le résultat a été une grande victoire pour Hytech et son client. Le DATRON a en fait découpé les pièces en polycarbonate plus rapidement que le laser ne les avait découpées en acrylique, la finition de surface était comparable et le client a pu passer au matériau préféré.
Le DATRON M10 Pro est compatible avec une large gamme de progiciels de FAO et Hytech a investi dans plusieurs d'entre eux et a effectué des tests approfondis pour optimiser les performances et la finition de surface. Blandino déclare :« Nous avons probablement effectué plus de tests logiciels que la plupart des magasins. Nous utilisons le lissage de contour du logiciel DATRON, mais c'est aussi une combinaison de la dynamique et des stratégies de programmation qui contribuent toutes à un état de surface parfait. Nous avons effectué des tests avec différents logiciels de programmation, notamment SolidCam, SOLIDWORKS, FeatureCAM, Fusion 360 et PowerMill, et nous comparons des pommes avec des pommes avec différentes fraises, vitesses et avances. Ainsi, nous utilisons une combinaison de ce que le logiciel a à offrir combiné avec ce que DATRON a à offrir, et nous avons trouvé une formule pour la meilleure finition de surface que vous pouvez obtenir avec le fraisage 3 axes. Fusion a un très bon poteau pour DATRON et offre d'excellentes finitions de surface en conjonction avec la dynamique et le lissage des contours que le M10 a à offrir. Actuellement, notre CAM principal
la solution est chez Autodesk. Les tests sont effectués en continu et le DATRON complète extrêmement bien tous les post-processeurs du logiciel. »
Ils doivent être discrets à ce sujet, mais Hytech pourrait nous dire qu'ils viennent d'entrer dans une industrie existante avec une nouvelle façon de fabriquer des composants qui nécessite un usinage extrêmement précis. Les fabricants de cette industrie sont en fait venus chez Hytech parce qu'ils ont une photo de leur DATRON M10 Pro sur leur site Web. Lors de la dernière série de tests de coupe pour cette industrie, la pièce a fonctionné pendant plus de 200 heures. En effet, la pièce nécessite de très petites fraises prenant un petit pas en avant pour effectuer le contournage 3D et peut même durer des dizaines d'heures sans changement d'outil. Avec la machine fonctionnant actuellement 24 heures sur 24, 7 jours sur 7, l'ajout d'un M10 Pro supplémentaire est imminent. Cette nouvelle activité devrait entraîner une augmentation de 25 % des revenus de l'entreprise.
commande numérique par ordinateur
- De CM à EMS à MSP :l'évolution d'une industrie
- L'industrie alimentaire a besoin d'une dose de résilience cette année
- À l'ère de l'industrie 4.0, que veulent vraiment les clients ?
- Pourquoi devrions-nous être honnêtes avec les clients ?
- Usinage CNC dans l'industrie automobile
- Durabilité :le défi de l'Industrie 4.0
- Industrie 5.0 :la nouvelle révolution
- Pleins feux sur l'industrie :l'industrie minière
- Le quadrant des opportunités :quatre éléments pour réussir l'industrie 4.0