Un guide ridiculement simple pour gérer les temps d'arrêt planifiés | Temps d'arrêt planifié
La maintenance préventive est la stratégie de maintenance la plus populaire car elle apporte de nombreux avantages tout en n'étant pas incroyablement difficile ou coûteuse à mettre en œuvre.
Cela étant dit, la maintenance préventive a ses inconvénients.
L'une des objections les plus citées est que sa mise en œuvre signifie que vous effectuerez une maintenance excessive. En d'autres termes, vos techniciens perdront du temps sur des inspections inutiles et des actifs qui pourraient ne pas (encore) nécessiter ce niveau d'attention.
Si nous creusons un peu plus, nous verrons que cela conduit à un problème plus important. Lorsque vous effectuez un travail préventif sur un actif, dans de nombreux cas, cet actif doit d'abord être arrêté. En traduction, vous devez planifier des temps d'arrêt planifiés.
Comme personne ne veut arrêter un actif pendant les périodes de pointe de production ou pour des travaux de maintenance qui ne doivent pas encore être effectués, voyons comment vous pouvez développer un programme de maintenance qui prend en compte ces défis et minimise les temps d'arrêt programmés.
Qu'est-ce que le temps d'arrêt prévu | temps d'arrêt programmé ?
En termes simples, les temps d'arrêt planifiés sont une période de temps que vous réservez pour la maintenance et les mises à niveau programmées pendant laquelle vos actifs doivent être arrêtés.
Étant donné que la maintenance proactive est souvent effectuée sur des actifs critiques importants pour la production, vous n'avez pas d'autre solution que de suspendre les opérations de production normales jusqu'à ce que les réparations/inspections/mises à niveau soient effectuées.
Les organisations cherchent à éviter ces problèmes en planifiant la maintenance pendant les quarts de nuit (ou à d'autres moments où les machines ne sont pas utilisées). Cependant, si votre service de maintenance ne travaille pas de nuit ou si vous avez un cycle de production 24h/24 et 7j/7, trouver le bon moment pour planifier les temps d'arrêt planifiés peut devenir très compliqué, très rapide.
Remarque rapide :pour le reste de l'article, nous utiliserons les termes « temps d'arrêt planifié » et « temps d'arrêt planifié » de manière interchangeable car ils font référence à la même chose dans la pratique.
Temps d'arrêt planifiés et imprévus
La différence entre les temps d'arrêt planifiés et non planifiés est explicite :VOUS décidez quand vous voulez avoir des temps d'arrêt planifiés, les MACHINES décident quand elles veulent faire une pause, et elles ne prennent pas la peine de demander si cela correspond à votre emploi du temps.
Blague à part, les pannes d'équipement imprévues qui entraînent des temps d'arrêt imprévus peuvent être très coûteuses , qui est l'une des principales raisons pour lesquelles de nombreuses entreprises passent de la maintenance réactive à la maintenance préventive .
Il est essentiel de savoir combien de temps vous passez sur la maintenance planifiée par rapport à la maintenance non planifiée, c'est donc l'une des nombreuses choses que Limble garde une trace pour vous.
Voici un exemple de la façon dont vous pouvez utiliser Limble pour suivre le temps que vous passez sur les tâches de maintenance planifiées par rapport au temps que vous passez à réagir aux problèmes inattendus :
Voyons comment planifier les temps d'arrêt afin que vous puissiez effectuer une maintenance appropriée avec un impact minimum sur votre vitesse et votre volume de production.
Comment gérer les temps d'arrêt planifiés
#1) Comprendre votre production
Tout au long de l'année, vous aurez plus que probablement un flux et un reflux dans une production quotidienne. Connaissez chaque machine que vous utilisez et discernez comment les différentes saisons affectent les cycles de production et, par conséquent, l'utilisation quotidienne des machines.
Pendant le pic de production, prévoyez de trouver le meilleur moment qui affecte le moins les résultats. Trouver le temps de se préparer peut signifier après les heures. Si vous gérez une boutique 24h/24 et 7j/7, cela peut signifier l'heure la plus lente de la journée.
La clé est de savoir quand la production ralentit et quand elle accélère comme prévu.
#2) Réduisez la maintenance excessive avec une GMAO
L'un des principaux moyens d'exécuter un plan de maintenance réussi est de pouvoir organiser, gérer et suivre de grandes quantités d'informations provenant de diverses sources.
Avoir une GMAO moderne peut grandement vous aider à suivre et à comprendre toutes ces données.
Réduire la maintenance réactive de 73,2 %
Voir les résultats que Red Hawk aime avec Limble
Lire notreÉtude de cas
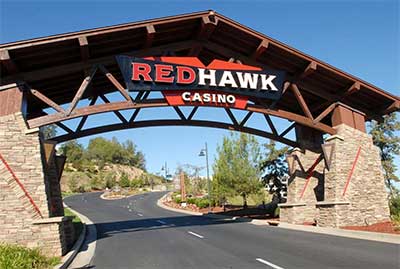
Voici quelques-unes des choses que vous faites avec une GMAO :
- enregistrer les performances de la machine et l'historique des ressources
- suivre la progression de toutes les tâches (lire les bons de travail)
- suivre l'utilisation de tous les stocks et pièces détachées
- suivre les performances du technicien
- planifier et superviser votre programme complet de maintenance préventive
En ayant toutes ces données à votre disposition, vous pouvez réduire la maintenance excessive en :
- espacer la fréquence des travaux de maintenance sur les actifs pouvant les gérer
- réduire la durée des temps d'arrêt en accélérant le diagnostic et la communication avec l'équipe
- s'assurer que toutes les pièces de rechange sont disponibles lorsque vous en avez besoin
- avoir un service de maintenance bien organisé en général
Pour un examen approfondi de la GMAO, consultez notre guide Qu'est-ce qu'un système de GMAO et comment fonctionne-t-il.
#3) Affiner le focus de votre plan de maintenance
Un excellent moyen de savoir par où commencer votre planification de maintenance consiste à répertorier tous vos actifs et à leur attribuer un rang. Cela peut sembler évident, mais savoir quelles machines sont de la plus haute priorité dans votre usine vous donnera un nord.
Une fois que vous avez répertorié vos machines importantes, répertoriez les actifs les plus mineurs qui pourraient être si secondaires qu'ils n'ont pas besoin d'être inclus dans la maintenance de routine.
Les machines individuelles, par exemple, sont moins sollicitées à l'usage. On pourrait ne pas avoir besoin d'huile ou de lubrification; un autre peut être moins impliqué que d'autres appareils, avec beaucoup moins de pièces mobiles.
Dans tous les cas, des machines spécifiques nécessitent moins de maintenance globale. Et il devrait être clair quelles machines entrent dans cette catégorie. Après tout, cela ne vaut souvent pas la peine d'avoir toutes vos machines sur un plan de maintenance préventive.
En plus de tout ce qui est mentionné, comprendre combien de temps chaque tâche de maintenance doit durer et quand la machine est le moins utilisée sera crucial pour créer un plan de maintenance préventive efficace afin que vous puissiez planifier les temps d'arrêt planifiés au moment le plus opportun.
#4) Avoir une SOP clairement définie
Avoir des procédures opérationnelles standard clairement définies car chaque opération qui doit être répétée souvent est un excellent moyen de rationaliser vos opérations de maintenance.
Comme les temps d'arrêt planifiés sont quelque chose que vous devrez planifier assez régulièrement, des directives claires aideront les techniciens à effectuer leur travail plus rapidement, ce qui signifie que vos actifs auront besoin de moins de temps pour se remettre au travail.
Gardez à l'esprit que la vitesse et la qualité des travaux de maintenance effectués sont tout aussi importants . Bien qu'il soit agréable de réduire au minimum les temps d'arrêt programmés, des travaux de maintenance mal exécutés entraîneront presque certainement une augmentation des temps d'arrêt imprévus.
Et je pense que nous pouvons tous convenir que deux heures supplémentaires de temps d'arrêt planifié sont beaucoup plus acceptables qu'une journée entière d'un arrêt ou d'une panne imprévus.
#5) Comprenez vos goulots d'étranglement
Les retards de livraison fréquents rendent difficile le maintien d'un stock de pièces de rechange nécessaires ? Certains techniciens supérieurs de maintenance ont pris leur retraite ou ont quitté l'entreprise, vous travaillez donc avec une équipe plus jeune qui manque d'expérience et de formation ? Vous travaillez avec des actifs plus anciens qui nécessitent beaucoup d'attention et aiment tomber en panne de manière inattendue ?
Dans le cadre de la minimisation des temps d'arrêt planifiés pour la maintenance préventive, pièces de rechange , techniciens inexpérimentés/non qualifiés , et actifs vieillissants sont les 3 goulots d'étranglement les plus courants que vous devez contourner.
La bonne nouvelle est que ces goulots d'étranglement sont évitables avec un peu de contournement et de prévoyance.
Si vos pièces de rechange ne vous parviennent pas rapidement, envisagez de les commander plus tôt ou de changer de fournisseur si possible.
Lorsque vous savez que vous avez des techniciens inexpérimentés, vous pouvez :
- associez-les à des collègues plus expérimentés
- avoir une SOP clairement définie dont nous venons de parler
- leur fournir la formation nécessaire
- avoir un processus de recrutement plus rigoureux
Et enfin, vous devez trouver un moyen de comptabiliser les actifs vieillissants. Dans la plupart des cas, cela signifie que vous devrez porter une attention particulière à ces actifs car ils peuvent être très gênants et être la cause de nombreux temps d'arrêt imprévus. Voici quelques façons de le faire :
- suivre attentivement l'historique des actifs pour extrapoler les schémas de panne courants afin que vous puissiez chercher à les résoudre pendant les temps d'arrêt planifiés
- planifier des inspections supplémentaires qui peuvent être effectuées pendant que l'actif est en fonction
- installer des capteurs pour effectuer une surveillance basée sur l'état
#6) Réduisez la durée des temps d'arrêt programmés grâce à une collaboration efficace
Les services qui interagissent avec le personnel de maintenance doivent être sur la même longueur d'onde et coordonner les mises au point et les réparations de routine. Tant que tout le monde comprend où se trouvera l'équipe de maintenance pour chaque arrêt planifié, les opérateurs de machines, le personnel de nettoyage et les autres travailleurs peuvent commencer à préparer l'environnement pour se concentrer uniquement sur ce qu'ils doivent faire et assurer un temps d'arrêt minimal.
Lorsque le contraire se produit et qu'il y a une mauvaise communication entre les départements, il n'est pas difficile d'imaginer différentes erreurs et accidents qui peuvent se produire et prolonger le temps que vos actifs passent en veille.
Ne laissez pas une mauvaise organisation et une mauvaise communication être la raison pour laquelle vos arrêts planifiés ont causé des retards de production.
Quand planifier les temps d'arrêt ?
En tant que responsable de la maintenance des installations, il est clair que vous seul pouvez trouver le bon moment pour planifier les temps d'arrêt planifiés dans votre installation.
Cela étant dit, nous avons quelques conseils qui pourraient vous aider :
- Planifier les travaux de maintenance planifiés après les heures d'ouverture
- Immédiatement avant les grandes vacances
- Avant des phénomènes météorologiques violents très attendus
- Un tous les deux ans simule une panne et teste tous les équipements critiques en même temps
Pour des explications plus détaillées, vous pouvez consulter mon article d'invité qui explique quand planifier la maintenance planifiée .
Il s'agit de planifier à l'avance
Comme vous pouvez le voir, avec suffisamment de planification et d'organisation, vous pouvez réduire considérablement le temps d'arrêt pendant la maintenance planifiée.
Que ce soit pendant une saison de production de pointe ou la saison la plus lente de l'année, être organisé et avoir un calendrier de maintenance précis garantira que votre production fonctionne au plus haut niveau et que vos machines sont en parfait état de fonctionnement.
Si vous souhaitez explorer pleinement comment Limble peut vous aider à réduire au minimum le temps consacré aux temps d'arrêt planifiés, laissez un commentaire ci-dessous ou envoyez-nous un message .
Entretien et réparation d'équipement
- Vs programmés. Maintenance imprévue dans les installations de fabrication
- Guide de mise en œuvre de la maintenance productive totale
- Guide des KPI de fabrication
- L'avenir de la maintenance :Guide pratique de l'Industrie 4.0
- Un guide simple pour créer un programme de maintenance prédictive
- La planification de la maintenance nécessite un backlog planifié
- Un guide simple pour l'analyse comparative de la maintenance
- Qu'est-ce que la maintenance planifiée ?
- Guide de base de l'entretien des chargeuses compactes