17 Chapitre 7 :Fabrication au plus juste
OBJECTIF
Après avoir terminé cette unité, vous devriez être en mesure de :
- Appliquez 5S dans n'importe quel atelier d'usinage.
- Décrire le concept Kaizen.
- Décrire la mise en œuvre de la fabrication au plus juste.
Lean 5S :
« 5S » est une méthode d'organisation du lieu de travail qui se compose de cinq mots :trier, mettre en ordre, briller, standardiser et maintenir. Tous ces mots commencent par la lettre S. Ces cinq composants décrivent comment stocker les articles et maintenir le nouvel ordre. Lors de la prise de décisions, les employés discutent de la normalisation, ce qui rendra le processus de travail clair pour les travailleurs. Ce faisant, chaque employé se sentira propriétaire du processus.
Phase 0 : Sécurité
On suppose souvent qu'un programme 5S correctement exécuté améliorera la sécurité au travail, mais c'est faux. La sécurité n'est pas une option; c'est une priorité.
Phase 1 :Trier
Passez en revue tous les éléments du lieu de travail, en ne gardant que ce qui est nécessaire.
Phase 2 :Redresser
Tout doit avoir une place et être en place. Les articles doivent être divisés et étiquetés. Tout doit être organisé de manière réfléchie. Les employés ne devraient pas avoir à se pencher de façon répétitive. Placez l'équipement près de l'endroit où il est utilisé. Cette étape fait partie des raisons pour lesquelles lean 5s n'est pas considéré comme un "nettoyage standardisé".
Phase 3 :briller
Assurez-vous que le lieu de travail est propre et ordonné. En faisant cela, il sera plus facile de savoir où sont les choses et où elles devraient être. Après le travail, nettoyez l'espace de travail et remettez tout dans sa position initiale. Garder le lieu de travail propre doit être intégré à la routine quotidienne.
Phase 4 :Normaliser
Uniformiser les procédures de travail et les rendre cohérentes. Chaque travailleur doit être conscient de ses responsabilités lorsqu'il suit les trois premières étapes.
Phase 5 :Maintenir
Évaluer et maintenir les normes. Les étapes susmentionnées devraient devenir la nouvelle norme en vigueur. Ne revenez pas progressivement aux anciennes méthodes. Lorsque vous participez à la nouvelle procédure, pensez à des moyens de vous améliorer. Passez en revue les quatre premières étapes lorsque de nouveaux outils ou exigences de sortie sont présentés.
Kaizen
Alors que le processus Lean 5S se concentre sur l'élimination des déchets, Kaizen se concentre sur la pratique de l'amélioration continue. Comme lean 5S, Kaizen identifie trois aspects principaux du lieu de travail :M uda (déchets), M ura (incohérences) et M uri (pression sur les personnes et les machines). Cependant, le processus étape par étape Kaizen est plus étendu que le processus Lean 5S.
Présentation du processus Kaizen :
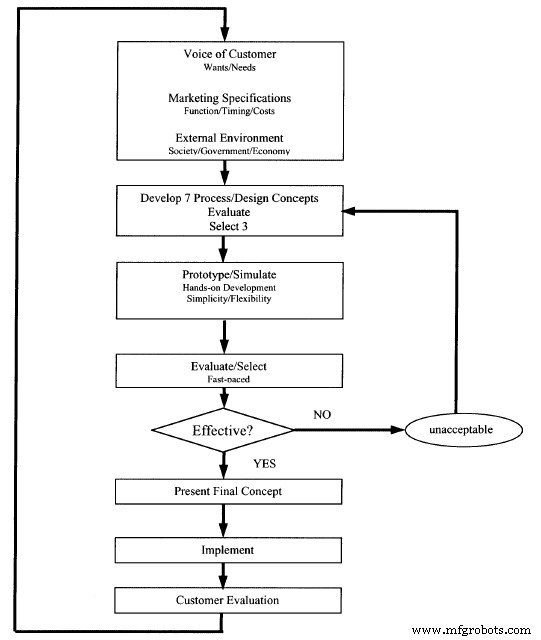
1. Identifiez un problème.
2. Formez une équipe.
3. Recueillir des informations auprès des clients internes et externes et déterminer les objectifs du projet.
4. Passez en revue la situation ou le processus actuel.
5. Faites un remue-méninges et envisagez sept alternatives possibles.
6. Choisissez les trois meilleures alternatives parmi les sept.
7. Simulez et évaluez ces alternatives avant la mise en œuvre.
8. Présentez l'idée et les suggestions aux responsables.
9. Mettre en œuvre physiquement les résultats Kaizen et tenir compte des effets.
La fabrication au plus juste s'améliore avec le temps, il est donc important de continuer à se former sur le maintien des normes. Il est crucial de changer les normes et de former les travailleurs lorsqu'ils sont confrontés à de nouveaux équipements ou règles.
Allégé
Considérez un service de maintenance comme étant au service de clients internes :les différents services et employés de l'entreprise.
Lean est différent du modèle occidental traditionnel de production de masse qui s'appuie sur les économies d'échelle pour créer des profits. Plus vous gagnez, moins cher sera le produit, plus grande sera la marge bénéficiaire potentielle. Il est basé sur les prévisions des besoins des clients ou sur la création des besoins des clients. Il a du mal à faire face aux changements inhabituels de la demande.
La production au plus juste répond à une demande éprouvée des clients. Traitement tiré - le client tire la production. Dans un système de masse, le producteur pousse le produit sur le marché, pousse la transformation.
Construire une culture à long terme axée sur l'amélioration.
Respect des travailleurs mieux formés et éduqués, plus flexibles
Lean est une philosophie qui se concentre sur les éléments suivants :
- Répondre aux besoins des clients
- Amélioration continue et progressive
- Créer des produits toujours meilleurs
- Valoriser la contribution des travailleurs
- Une vision à long terme
- Éliminer les erreurs
- Éliminer les déchets
Gaspillage :utilisation de trop de ressources (matériel, temps, énergie, espace, argent, ressources humaines, mauvaises instructions)
Déchets :
- Surproduction
- Défauts
- Traitement inutile
- Attente (perte de temps)
- Perdre du temps et du talent humain
- Trop d'étapes ou de déplacements Transport excessif
- Inventaire excessif
La production allégée implique de travailler avec des fournisseurs, des sous-traitants et des vendeurs pour rationaliser l'ensemble du processus.
L'objectif est que la production se déroule sans heurts en évitant les démarrages et les arrêts coûteux.
L'idée s'appelle juste à temps "ne produire que ce qui est nécessaire, quand il le faut et uniquement dans la quantité nécessaire". Le processus de production doit être flexible et rapide.
Inventaire =exactement ce dont vous avez besoin
En production de masse =juste au cas où. Les fournitures et produits supplémentaires sont stockés au cas où ils seraient nécessaires.
Terminologie :
Simplification des processus – un processus en dehors du flux de production
Défauts - le système de production de masse effectue une inspection à la fin de la production pour détecter les défauts avant qu'ils ne soient expédiés. Le problème est que les ressources ont déjà été « dépensées » pour fabriquer le déchet. » Essayez de prévenir les problèmes immédiatement, au fur et à mesure qu'ils surviennent, puis prévenez-les. Inspection pendant la production, à chaque étape de la production.
Sécurité - le temps blessé est du temps perdu
Information - besoin de la bonne information au bon moment (trop, trop peu, trop tard)
Principes :
Poka-yoke - preuve d'erreur déterminant la cause des problèmes, puis supprimant la cause pour éviter d'autres erreurs
Erreurs de jugement - trouver des problèmes après le processus
Inspections informatives - analyser les données des inspections au cours du processus
Inspections à la source - inspection avant le début du processus pour éviter les erreurs.
MOYENNE MAIGRE
L'un des termes appliqués à une simple interprétation de la réduction des coûts et de la réduction des emplois du Lean est Mean Lean. Souvent, les managers modernes pensent qu'ils font du lean sans comprendre l'importance des travailleurs et des relations à long terme.
Maintenance centrée sur la fiabilité
La maintenance centrée sur la fiabilité est un système permettant de concevoir un programme de maintenance rentable. Il peut s'agir d'un ordinateur complexe et détaillé, piloté par des statistiques, mais à la base, il est assez simple. Ses idées peuvent être appliquées à la conception et à l'exploitation d'un système PM, et peuvent également guider votre apprentissage lorsque vous effectuez des travaux de maintenance, de dépannage, de réparation et d'énergie.
Ce sont les principes fondamentaux de la RCM. Ces neuf concepts fondamentaux sont :
- Des échecs se produisent.
- Tous les échecs n'ont pas la même probabilité
- Tous les échecs n'ont pas les mêmes conséquences
- Les composants simples s'usent, les systèmes complexes tombent en panne
- Un bon entretien fournit les fonctionnalités requises au coût le plus bas possible
- La maintenance ne peut que garantir la fiabilité inhérente de la conception de l'équipement
- Une maintenance inutile détourne des ressources de la maintenance nécessaire
- Les bons programmes de maintenance font l'objet d'améliorations continues.
La maintenance comprend toutes les actions entreprises pour s'assurer que les composants, l'équipement et les systèmes remplissent les fonctions prévues lorsque cela est nécessaire.
Un système RCM est basé sur la réponse aux questions suivantes :
1. Quelles sont les fonctions et les normes de performance souhaitées de l'équipement ?
2. De quelles manières peut-il ne pas remplir ses fonctions ? (Quels sont les échecs les plus probables ? Quelle est la probabilité de chaque type d'échec ? Les échecs seront-ils évidents ? Peut-il s'agir d'un échec partiel ?)
3. Qu'est-ce qui cause chaque échec ?
4. Que se passe-t-il à chaque panne ? (Quel est le risque, le danger, etc. ?)
5. En quoi chaque échec est-il important ? Quelles sont les conséquences d'une panne totale ou partielle ?
6. Que peut-on faire pour prévoir ou prévenir chaque panne ? Combien en coûtera-t-il pour prévoir ou prévenir chaque panne ?
7. Que faire si une tâche proactive appropriée est introuvable (actions par défaut) (aucune tâche n'est peut-être disponible, ou elle peut être trop coûteuse pour le risque) ?
L'équipement est étudié dans le contexte de l'endroit, du moment et de la manière dont il est utilisé
Toutes les actions de maintenance peuvent être classées dans l'une des catégories suivantes :
- Maintenance corrective :restauration des fonctions perdues ou dégradées
- Maintenance préventive :minimise les risques d'échec de la fonction
- Maintenance alternative – Éliminer les conditions insatisfaisantes en modifiant la conception ou l'utilisation du système
Dans la catégorie de maintenance préventive, toutes les tâches accomplies peuvent être décrites comme appartenant à l'un des cinq (5) principaux types de tâches :
- Condition Directed - Renouveler la vie en fonction de l'état mesuré par rapport à une norme
- Time Directed - Renouveler la vie quelle que soit la condition
- Recherche de panne – Déterminer si une panne s'est produite
- Entretien – Ajouter/faire le plein de consommables
- Lubrification :huiler, graisser ou lubrifier d'une autre manière
Nous faisons de la maintenance parce que nous pensons que la fiabilité du matériel se dégrade avec l'âge, mais que nous pouvons faire quelque chose pour restaurer ou maintenir la fiabilité d'origine qui s'autofinance.
RCM est centré sur la fiabilité. Son objectif est de maintenir la fiabilité inhérente de la conception du système ou de l'équipement, en reconnaissant que des modifications de la fiabilité inhérente ne peuvent être obtenues que par des modifications de conception. Nous devons comprendre que l'équipement ou le système doit être étudié dans la situation dans laquelle il fonctionne.
Mise en œuvre de la fabrication au plus juste
Analysez chaque étape du processus d'origine avant d'apporter des modifications
Lean manufacturing se concentre principalement sur la réduction des coûts et l'augmentation du chiffre d'affaires et l'élimination des activités qui n'ajoutent pas de valeur au processus de fabrication. Fondamentalement, la fabrication au plus juste aide les entreprises à atteindre une production ciblée, ainsi que d'autres choses, en introduisant des outils et des techniques faciles à appliquer et à entretenir. Ce que ces outils et techniques font, c'est réduire et éliminer les déchets, des choses qui ne sont pas nécessaires dans le processus de fabrication.
Les ingénieurs de fabrication ont décidé d'utiliser la méthodologie DMAIC (conception, mesure, analyse, amélioration, contrôle) six sigma, en conjonction avec la fabrication au plus juste, pour répondre aux exigences des clients liées à la production de tubes.
Les ingénieurs de fabrication ont été chargés de concevoir une nouvelle configuration de processus de la ligne de production de tubes. Les objectifs du projet étaient notamment :
- Amélioration de la qualité
- Diminution des rebuts
- Livraison au point d'utilisation
- Tailles de lots plus petites
- Mise en place d'un système pull
- Meilleurs commentaires
- Augmentation de la production
- Responsabilité individuelle
- Diminution des travaux en cours
- Possibilité de dîner
Avant d'apporter des modifications, l'équipe analyse chaque étape de la configuration d'origine du processus de la ligne de production de tubes.
1. Essayez de comprendre le processus d'état d'origine, d'identifier le problème, l'étape inutile et la non-valeur ajoutée.
2. Après avoir cartographié le processus, l'équipe Lean a collecté des données auprès du comité de révision des matériaux (MRB) pour mesurer et analyser les principaux types de défauts. Pour mieux comprendre le processus, l'équipe a également réalisé une étude de temps pour une période de production de 20 jours.
A l'origine, la ligne de tubes se composait d'un opérateur et de quatre opérations, séparées en deux stations par une grande table utilisant un système de poussée. Le tableau servait de séparateur entre la deuxième et la troisième opération.
Le premier problème découvert était le déséquilibre de la ligne. La première station a été utilisée environ 70 % du temps. Les opérateurs de la deuxième station passaient une grande partie de leur temps à attendre entre les temps de cycle. En combinant les stations un et deux, une marge d'amélioration est devenue évidente en ce qui concerne la responsabilité individuelle, le contrôle de l'inventaire par l'opérateur et la rétroaction immédiate en cas de problème. L'étude du temps et la disposition du département reflètent ces résultats.
Un deuxième problème a été identifié. En raison du déroulement du processus, la cadence de production ne permettait pas de respecter le calendrier de production avec deux stations. Parce que les opérateurs perdaient la trace des cycles de la machine, les machines attendaient l'attention de l'opérateur. Les opérateurs ont également essayé de pousser les pièces à travers la première station - l'opération de goulot d'étranglement dans le processus - puis ont continué à fabriquer les pièces lors des deux dernières opérations. En règle générale, de longues séries de travaux en cours s'accumulaient et les problèmes de qualité n'étaient pas détectés tant qu'un grand nombre de pièces défectueuses n'étaient pas produites.
Les données d'état d'origine ont été extraites des 20 derniers jours avant le changement. Les équipes analysent chaque étape de l'original et apportent des modifications. Les résultats de l'étude de temps sur le processus d'origine ont fourni la base pour réduire le temps de cycle, équilibrer la ligne, concevoir l'utilisation de kanbans et de la planification juste à temps, améliorer la qualité, réduire la taille des lots et les WIP et améliorer le flux. Les nouvelles données de processus ont été prises à partir d'un mois après la mise en œuvre. Ce retard a donné aux opérateurs de machines l'occasion de se former et de se familiariser avec le nouveau système d'agencement des processus.
Avec la conception de cellule en forme de U; Les pièces répondent à toutes les exigences du client. Le tableau du processus d'origine a été supprimé, éliminant presque le WIP. Avec la réduction des WIP et l'augmentation de la production.
Certains des concepts utilisés pour améliorer le processus comprenaient la participation totale des employés (TEI), des tailles de lots plus petites, la planification, l'inventaire des points d'utilisation et une disposition améliorée. Tous les employés et superviseurs du service ont été impliqués dans toutes les phases du projet. Leurs idées et suggestions ont été intégrées au processus de planification et de mise en œuvre afin d'obtenir une plus large acceptation des changements apportés au processus. Des tailles de lots plus petites ont été introduites pour minimiser le nombre de pièces produites avant que les défauts ne soient détectés. Des kanbans ont été introduits (sous la forme de racks de manutention) pour contrôler WIP et mettre en œuvre un système de traction. Et la disposition des cellules a réduit les déplacements entre les opérations.
Les opérateurs étaient autorisés à arrêter la ligne en cas de problème. Dans l'état d'origine, les opérateurs continuaient à exécuter des pièces lorsqu'une opération était interrompue. Avec kanban
contrôle, la disposition a éliminé la possibilité de stocker WIP, obligeant l'opérateur à arrêter toute la ligne. La disposition des cellules offre d'excellentes opportunités pour améliorer la communication entre les opérateurs sur les problèmes et les ajustements, afin d'obtenir une meilleure qualité.
Lors de l'inspection quotidienne du processus d'origine, les opérateurs ont passé beaucoup de temps soit à attendre la personne chargée de la manutention, soit à jouer le rôle de manutentionnaire. Avec la cellule en forme de U, la livraison au point d'utilisation est meilleure pour l'opérateur. L'opérateur place les boîtes de matières premières sur six chariots à rouleaux mobiles, où il est facile de les obtenir. Les six boîtes suffisent pour durer 24 heures.
Pour réduire les temps d'installation, les outils nécessaires à la réparation et aux réglages de la machine sont situés dans la cellule. Les vis ne sont pas normalisées; les outils sont mis en place par ordre croissant de taille pour identifier rapidement l'outil approprié.
Pendant trois mois, le processus a été surveillé pour vérifier qu'il était sous contrôle. La comparaison des études de temps de l'état d'origine et de l'agencement mis en œuvre a démontré une augmentation de la production de 300 à 514 produits finis par quart de travail. La nouvelle disposition a éliminé la double manipulation entre les deuxième et troisième opérations, ainsi qu'à l'étape d'emballage. Il a également été réduit au fil du temps en facilitant le cycle des quatre opérations dans un ordre de système de traction. La demande des clients a été satisfaite par deux équipes, ce qui a réduit le coût de la main-d'œuvre.
Les résultats de la refonte sont les suivants :
- WIP a diminué de 97 %
- La production a augmenté de 72 %
- Le rebut a été réduit de 43 %
- L'utilisation de la machine a augmenté de 50 %
- L'utilisation de la main-d'œuvre a augmenté de 25 %
- Les coûts de main-d'œuvre ont été réduits de 33 %
- Niveau Sigma augmenté de 2,6 à 2,8
This project yielded reduced labor and scrap costs, and allowed the organization to do a better job of making deliveries on time, while allowing a smaller finished-goods inventory. Daily production numbers and single-part cycle time served as a benchmark for monitoring progress towards the goal. Although the sigma level increase , the 43% reduction in defects, 97% reduction in WIP, and production increase of 72% contributed to the project objective.
Implementing lean is a never ending process; this is what continuous improvement is all
sur. When you get one aspect of lean implemented, it can always be improved. Don’t get hung up on it, but don’t let things slip back to the starting point. There will always be time to go back and refine some of the processes.
Before Lean Manufacturing was implemented at Nypro Oregon Inc., we would operate using traditional manufacturing. Traditional manufacturing consists of producing all of a given product for the marketplace so as to never let the equipment idle. These goods them need to be warehoused or shipped out to a customer who may not be ready for them. If more is produced than can be sold, the products will be sold at a deep discount (often a loss) or simply scrapped. This can add up to an enormous amount waste. After implementing Lean Manufacturing concepts, our company uses just in time. Just in time refers to producing and delivering good in the amount required when the customer requires it and not before. In lean Manufacturing, the manufacture only produces what the customer wants, when they want it. This often a much more cost effective way of manufacturing when compared to high priced, high volume equipment.
Unit Test:
1. What is 5S?
2. Please Explain each “S” of the 5S.
3. Please Explain Kaizen concept.
4. What is the Pull processing?
5. What is the Poka-yoke?
6. What is the six-sigma DMAIC?
7. What is the objectives for a new process layout of the tube production line?
8. Before making changes, The Manufacturing engineers team do what first?
9. Please lists the results of the redesign.
10. The key to implementing lean new idea or concept is to do what?
CHAPTER ATTRIBUTION INFORMATION
This chapter was derived from the following sources.
- Lean 5S derived from Lean Manufacturing by various authors, CC:BY-SA 3.0.
- Kaizen derived from A Kaizen Based Approach for Cellular Manufacturing System Design:A Case Study by VirginiaTech, CC:BY-SA 4.0.
- Kaizen (image) derived from A Kaizen Based Approach for Cellular Manufacturing System Design:A Case Study by VirginiaTech, CC:BY-SA 4.0.
Technologie industrielle
- Comparaison Six Sigma et production au plus juste
- Avantages de l'automatisation dans la production au plus juste
- 5 blogs sur la fabrication et la maintenance que vous devriez lire
- 6 domaines d'amélioration analysés par chaque consultant
- Qu'est-ce que le Lean Manufacturing ? Comment rationaliser avec l'automatisation flexible
- Les meilleurs outils de fabrication au plus juste dont les fabricants D2C ont besoin
- Les 8 gaspillages du Lean Manufacturing
- Réduisez les déchets en 3 étapes simples avec la fabrication au plus juste
- Comment remettre le Lean Manufacturing sur les rails