Top 5 des plastiques résistants à la chaleur
Les fabricants ont tendance à utiliser des métaux comme le nickel et l'acier inoxydable pour des applications hautes performances car ils sont très résistants à la chaleur. Les alliages à base de nickel, par exemple, conservent leur résistance dans des environnements avec des températures élevées, une exposition thermique cyclique et des niveaux élevés de carbone. Même si le métal a tendance à être plus résistant à la chaleur que le plastique, il existe de nombreux cas où les ingénieurs auraient avantage à utiliser des plastiques résistants à la chaleur pour leurs applications hautes performances.
Les plastiques résistants à la chaleur se répartissent en deux grandes catégories :les thermodurcissables et les thermoplastiques. Les thermodurcissables sont des plastiques qui durcissent lorsqu'ils sont exposés à la chaleur et ne peuvent pas être remodelés après durcissement. Les thermoplastiques haute performance sont des plastiques qui fondent lorsqu'ils sont chauffés, deviennent solides lorsqu'ils sont refroidis et peuvent être refondus après refroidissement. L'intégrité structurelle des thermoplastiques est affectée par des facteurs tels que la température de transition vitreuse (Tg) et le point de fusion inhérents à chaque matériau. Il existe des choix de thermoplastiques hautes performances qui conservent leurs capacités structurelles au-dessus de 150 °C et à court terme au-dessus de 250 °C.
En plus d'être résistants à la chaleur, ces matériaux sont résistants aux produits chimiques, à la corrosion et d'excellents isolants électriques et thermiques. Les applications hautes performances courantes incluent les composants de piston dans l'industrie automobile, les conduits de câbles dans l'industrie aérospatiale, les connecteurs sous-marins dans l'industrie des semi-conducteurs, etc. Lors de la conception de pièces qui entreront en contact avec des températures extrêmement élevées, les équipes produit doivent envisager de fabriquer avec ces cinq principaux plastiques résistants à la chaleur.
Top 5 des plastiques résistants à la chaleur
Les thermoplastiques tirent leur résistance à la chaleur de leur structure moléculaire. Lorsque des anneaux aromatiques rigides sont ajoutés à la résine au lieu de groupes aliphatiques, le squelette de la chaîne moléculaire est restreint et fortifié de telle manière que deux liens chimiques doivent être rompus pour rompre la chaîne. Grâce à cette nouvelle structure, la résistance chimique et thermique d'un thermoplastique peut être égale ou supérieure à celle d'un thermodurcissable.
Voici cinq plastiques qui peuvent supporter la chaleur.
1. Polyétherimide (PEI)
ULTEM®, le nom de marque du polyétherimide (PEI), est l'un des rares thermoplastiques amorphes disponibles dans le commerce sur le marché aujourd'hui. Il est solide, résistant aux produits chimiques et aux flammes, et est un incontournable de l'industrie manufacturière depuis plus de 35 ans. ULTEM se distingue car il possède la plus haute résistance diélectrique de tous les thermoplastiques hautes performances.
Ce matériau a un point de fusion extrêmement élevé de 219°C et une température maximale de service continu de 170°C, ce qui le rend idéal pour les circuits imprimés, les équipements de stérilisation alimentaire et, plus particulièrement, les pièces d'avion. ULTEM est l'une des rares résines à être utilisée dans l'industrie aérospatiale commerciale - elle bat les autres thermoplastiques en termes de résistance au fluage et résiste bien en présence de divers carburants et liquides de refroidissement. Cependant, il a tendance à se fissurer en présence de solvants chlorés polaires. Ce matériau peut être trouvé dans les pare-feu et les housses de siège d'avion.
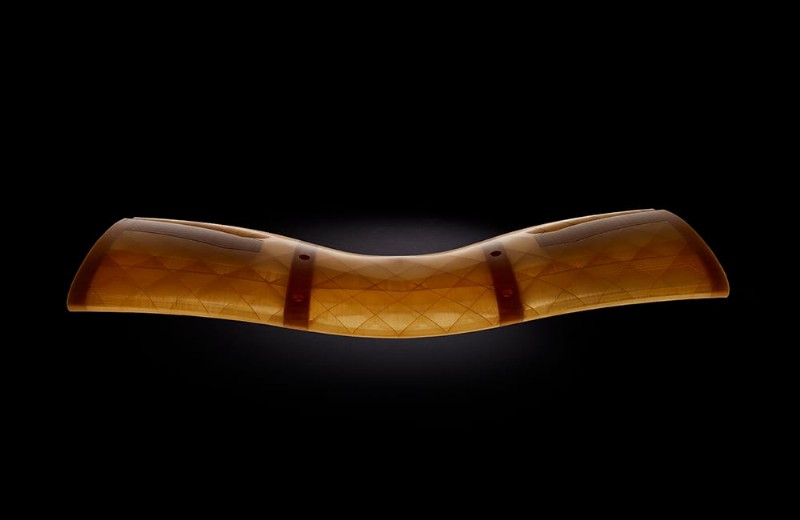
ULTEM est assez cher comme beaucoup d'autres plastiques de cette liste. En outre, il a une résistance aux chocs et une température utilisable inférieures à celles du PEEK.
Avantages d'ULTEM :
- Meilleure résistance au fluage que les thermoplastiques
- Résiste aux carburants et aux liquides de refroidissement
Inconvénients d'ULTEM :
- A tendance à se fissurer en présence de solvants chlorés polaires
- Assez cher
2. Polyéther éther cétone (PEEK)
Le PEEK, abréviation de polyéther éther cétone, est un thermoplastique semi-cristallin haute performance résistant aux produits chimiques, à l'usure, à la fatigue, au fluage et à la chaleur. Ce matériau est si résistant et adaptable aux environnements difficiles que les fabricants l'utilisent pour remplacer le métal dans de nombreuses applications, quelle que soit la température. Le PEEK peut résister à des températures aussi élevées que 310°C pendant de courtes périodes et a un point de fusion supérieur à 371°C. De plus, il possède la résistance à la traction et à la flexion la plus élevée de tous les polymères hautes performances.
En raison de sa durabilité semblable à celle du métal, le PEEK est largement utilisé pour une variété de dispositifs médicaux, de composants actifs dans les transmissions de voitures et de pièces extérieures d'avions. Il a l'avantage supplémentaire d'être facile à usiner par moulage par injection ou extrusion, et le PEEK solide est compatible avec l'usinage CNC.
Ce thermoplastique populaire présente quelques petits inconvénients, notamment sa sensibilité aux rayons UV et à certains acides. Cependant, le PEEK reste un thermoplastique très polyvalent que tous les ingénieurs devraient avoir dans leur répertoire.
Avantages du PEEK :
- Solide et adaptable aux environnements difficiles
- La plus haute résistance à la traction et à la flexion
- Capacités d'usinage de moulage par injection faciles
- Compatible avec l'usinage cnc
Inconvénients du PEEK :
- Sensibilité aux rayons UV et à certains acides
3. Polytétrafluoroéthylène (PTFE)
Le PTFE, communément appelé Téflon, est un plastique souple, résistant à la chaleur et à faible frottement avec une résistance chimique exceptionnelle. Il a une résistance élevée à la flexion, une résistance adéquate aux intempéries et un bon pouvoir isolant électrique dans les environnements chauds et humides.
Le PTFE est unique car il est presque totalement inerte chimiquement et hautement insoluble dans la plupart des solvants, ce qui le rend idéal pour les applications à haute température. Le PTFE a l'un des points de fusion les plus élevés de tous les thermoplastiques à 327 ° C et une très large plage de températures de fonctionnement. Il est suffisamment stable thermiquement pour être utilisé entre -200 °C et +260 °C.
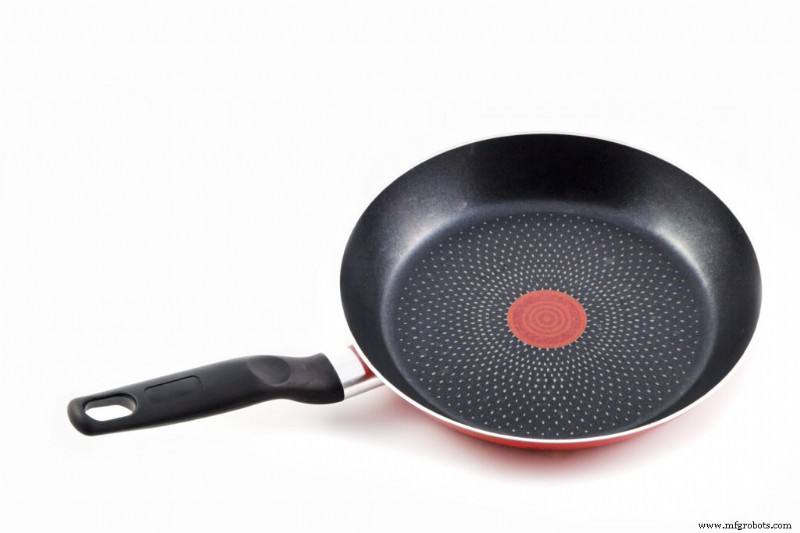
Le PTFE est surtout connu pour ses applications commerciales. Il est également utilisé pour protéger les tuyaux des matériaux corrosifs, recouvrir les échangeurs de chaleur et fournir une isolation pour les composants électriques.
Le PTFE excelle à des températures extrêmement élevées et basses, mais ses propriétés mécaniques sont généralement inférieures à celles des plastiques comparables à température ambiante. Il est sensible au fluage, à l'abrasion et aux radiations, et ses fumées peuvent être toxiques. En outre, il convient de noter que le PTFE est assez coûteux à traiter.
Avantages du PTFE :
- Haute résistance à la flexion
- Résistance adéquate aux intempéries
- Bon pouvoir isolant électrique dans les environnements chauds et humides
Inconvénients du PTFE :
- Inférieur aux plastiques comparables à température ambiante
- Sensible au fluage, à l'abrasion et aux radiations
- Fès peut être toxique
- Traitement assez coûteux
4. Polybenzimidazole (PBI)
Le polybenzimidazole (PBI) a la plus haute résistance à la chaleur et à l'usure, la résistance et la stabilité des propriétés mécaniques de tous les thermoplastiques techniques sur le marché aujourd'hui. Les fibres PBI n'ont pas de point de fusion connu, ne brûlent pas et ne collent pas aux autres plastiques. Ce matériau a une température maximale de service continu de 398 °C dans des environnements inertes, de 343 °C dans l'air et un potentiel d'exposition à court terme pouvant atteindre 537 °C.
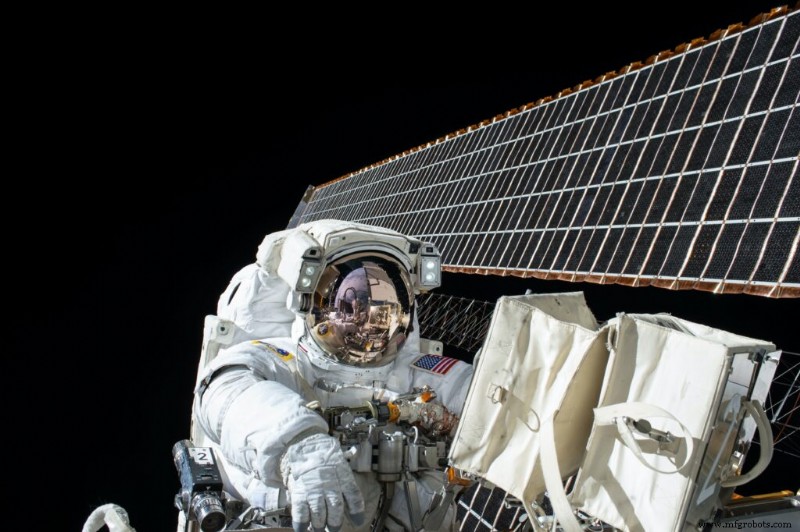
Malgré tous ses atouts, le PBI est incroyablement coûteux et difficile à fabriquer. Les ingénieurs doivent souvent utiliser des outils diamantés pour usiner ce matériau, ce qui augmente encore les coûts. Du point de vue de la conception, l'un des principaux inconvénients du PBI est sa sensibilité à l'encoche. Les concepteurs de produits doivent veiller à éviter tous les bords ou coins tranchants et à lisser toutes les finitions de surface.
Avantages du PBI :
- Haute stabilité
- Résistance à la chaleur extrême :la plus élevée de tous les thermoplastiques actuellement sur le marché
- Les fibres n'ont pas de point de fusion :elles ne brûlent pas et ne collent pas aux autres plastiques
Inconvénients du PBI :
- Coûteux et difficile à fabriquer
- Sensibilité élevée à l'encoche
5. Polydicyclopentadiène (pDCPD)
Le polydicyclopentadiène (pDCPD) est un polymère thermodurcissable conçu sur mesure pour offrir une excellente combinaison de résistance chimique, à la corrosion et à la chaleur, ainsi que de rigidité et de résistance aux chocs. Ce matériau allie la flexibilité de moulage d'un thermodurcissable aux caractéristiques de haute performance des meilleurs thermoplastiques techniques. Il a une température de déflexion thermique allant jusqu'à 120 °C.
Le pDCPD est unique car il n'a pratiquement aucune limitation de taille ou de poids des pièces - les pièces avec des épaisseurs de paroi variables, des nervures de renforcement moulées, etc. ne ralentiront pas la production. Le pDCPD est un matériau relativement nouveau et ses applications sont encore limitées, mais il s'avère prometteur dans les équipements de traitement chimique résistant à la corrosion, les fosses septiques et les équipements de traitement de l'eau.
Avantages du pDCPD :
- Combine résistance aux produits chimiques, à la corrosion et à la chaleur
- Aucune limitation de taille ou de poids des pièces :ne ralentit pas la production
- Allie flexibilité de moulage et hautes performances
Inconvénients du pDCPD :
- Nouveau matériel :les applications sont limitées
Les fabricants peuvent-ils améliorer la résistance à la chaleur ?
Les ingénieurs et les fabricants peuvent augmenter la chaleur et améliorer les performances de la plupart des types de plastiques en utilisant des additifs et/ou des stabilisants thermiques. Les trois types d'additifs les plus courants sont les antioxydants, les retardateurs de flamme et les auxiliaires technologiques. Chaque additif offre une caractéristique différente et contribue à la durabilité d'un polymère.
Les stabilisants thermiques protègent un polymère des dommages causés par la chaleur pendant la fabrication ou pendant l'utilisation normale de la pièce finale, et ils sont ajoutés à la majorité des polymères aujourd'hui. Les stabilisants thermiques peuvent également préserver l'apparence, la résistance et l'élasticité du polymère.
Choisissez un fabricant expert pour vous aider dans la sélection des matériaux
Pour les applications à haute température, n'importe lequel de ces plastiques haute performance peut vraiment supporter la chaleur. Cependant, pas n'importe quel matériau fera l'affaire. Les ingénieurs doivent faire leurs recherches pour s'assurer qu'ils choisissent le plastique résistant à la chaleur qui convient le mieux à leur application particulière. Si les ingénieurs choisissent le mauvais matériau, ils risquent de compromettre la fonctionnalité de leur pièce et de devoir recommencer à zéro.
Un partenaire de fabrication expérimenté comme Fast Radius peut simplifier le processus de sélection des matériaux grâce à nos services de conseil en ingénierie d'experts. Nous pouvons aider n'importe quelle équipe produit à choisir le bon matériau pour sa pièce et ses exigences uniques.
Au-delà de la sélection des matériaux, notre équipe d'ingénieurs et de concepteurs chevronnés est prête à rationaliser le processus de développement de produits et à fournir des pièces de qualité supérieure à des tarifs abordables et dans des délais ultra-rapides. Ainsi, chaque client peut être assuré qu'il obtient le meilleur produit pour la meilleure offre. . Contactez-nous aujourd'hui pour un devis.
Pour plus de guides de matériaux et d'informations sur la fabrication avec des plastiques, consultez le centre de ressources Fast Radius.
Prêt à fabriquer vos pièces avec Fast Radius ?
Commencez votre devisTechnologie industrielle
- Les 5 meilleurs matériaux pour les roulements en plastique utilisés sur les surfaces métalliques
- Les 10 principales tendances modernes des plastiques de performance
- Recrutement des meilleurs talents
- Composites hautes performances en Israël
- Top 50 des blogs sur la fiabilité des sites
- Meilleures résolutions de logiciels GMAO
- Top 8 des blogs de fabrication industrielle
- Principales applications pour les machines de plasturgie
- Qu'est-ce qu'une plaque supérieure ?