L'ingénierie derrière le masque facial Fast Radius
Par Izzy de la Guardia, ingénieur d'application, Fast Radius
Si la pandémie mondiale a révélé de nombreuses vulnérabilités dans notre chaîne d'approvisionnement, elle a également favorisé l'innovation. En particulier, l'impression 3D a permis aux professionnels et aux amateurs de transformer leurs peurs en action avec une rapidité et une accessibilité sans précédent. Nous en avons fait l'expérience de première main lors de la création de notre conception de respirateur open source.
Voici un aperçu du processus et de la manière dont nous avons pu créer quatre prototypes distincts et mener trois sessions de test utilisateur en seulement deux semaines en tirant parti de l'impression 3D, d'une équipe interfonctionnelle et des réseaux personnels et professionnels de notre entreprise.
Prototypage rapide et tests utilisateurs
Alors que de nombreux Américains ont commencé à s'abriter sur place à la mi-mars, Fast Radius a reçu plusieurs demandes de respirateurs imprimés en 3D au milieu des inquiétudes croissantes concernant les pénuries d'EPI. J'ai été sollicité par notre directeur général, John Nanry, un vendredi après-midi pour diriger l'effort de conception afin de répondre à ce besoin. Quelques heures plus tard, nous avions notre premier design prêt à imprimer, inspiré des designs open source de Copper 3D et La Factoría 3D
L'objectif principal de notre conception était la fabricabilité de toutes nos machines additives internes (Stratasys FDM, Carbon DLS ™ et HP Multi Jet Fusion) en garantissant des angles de porte-à-faux et une ventilation sous vide appropriés. Nous avons produit notre premier prototype sur Carbon DLS cette nuit-là.
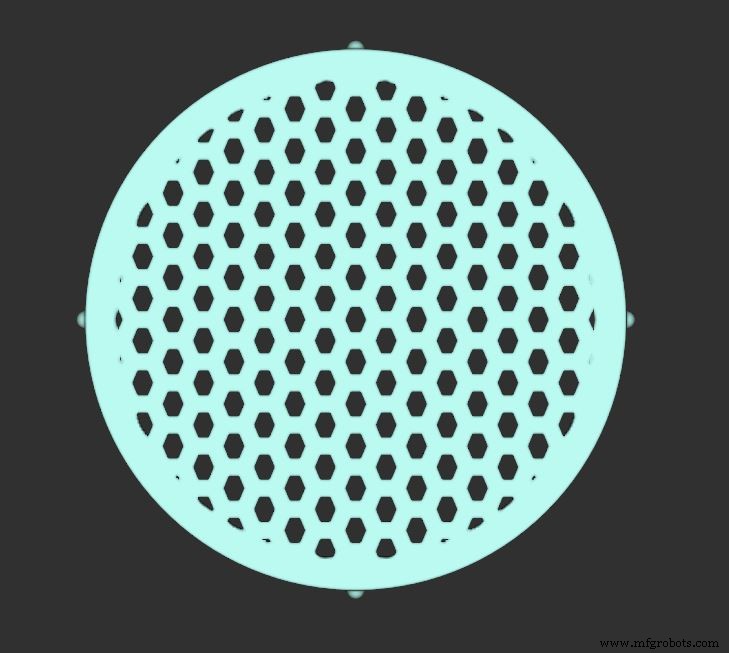
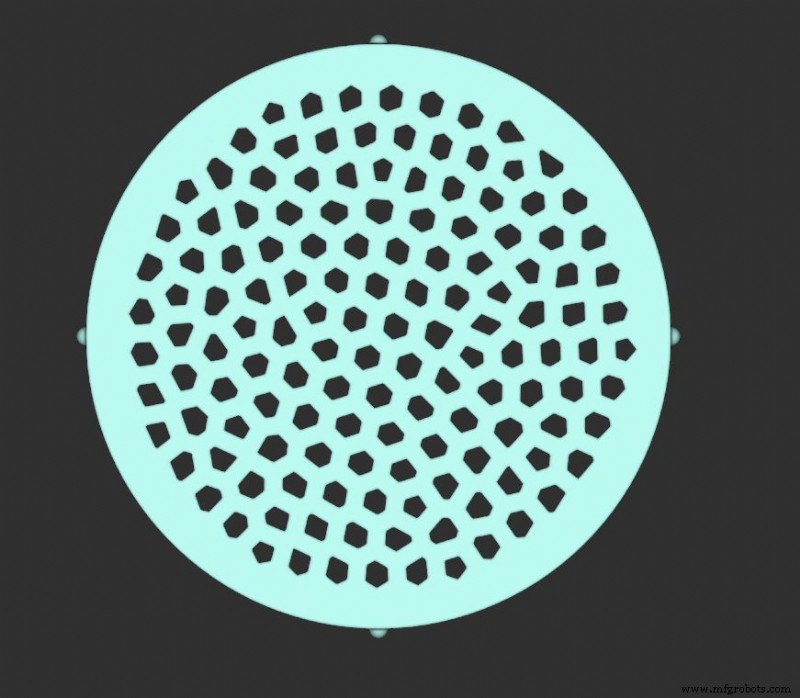
Des outils de conception avancés comme nTop Platform ont pris en charge une itération rapide, comme le passage d'un motif voronoi à un motif hexadécimal plus régulier qui était plus facile à gérer pour les imprimantes FDM amateurs
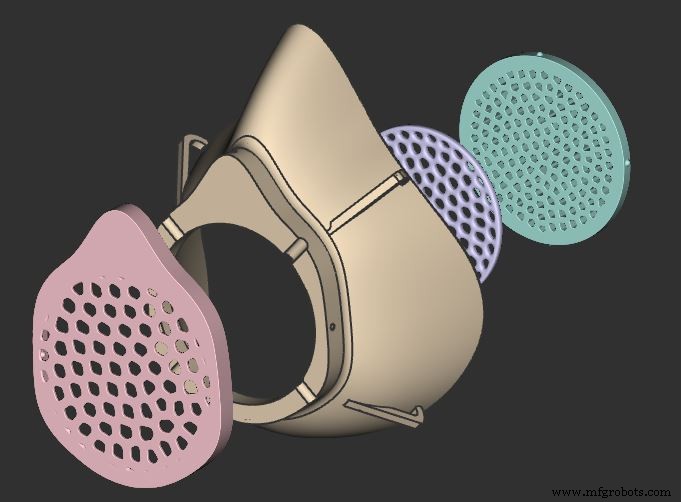
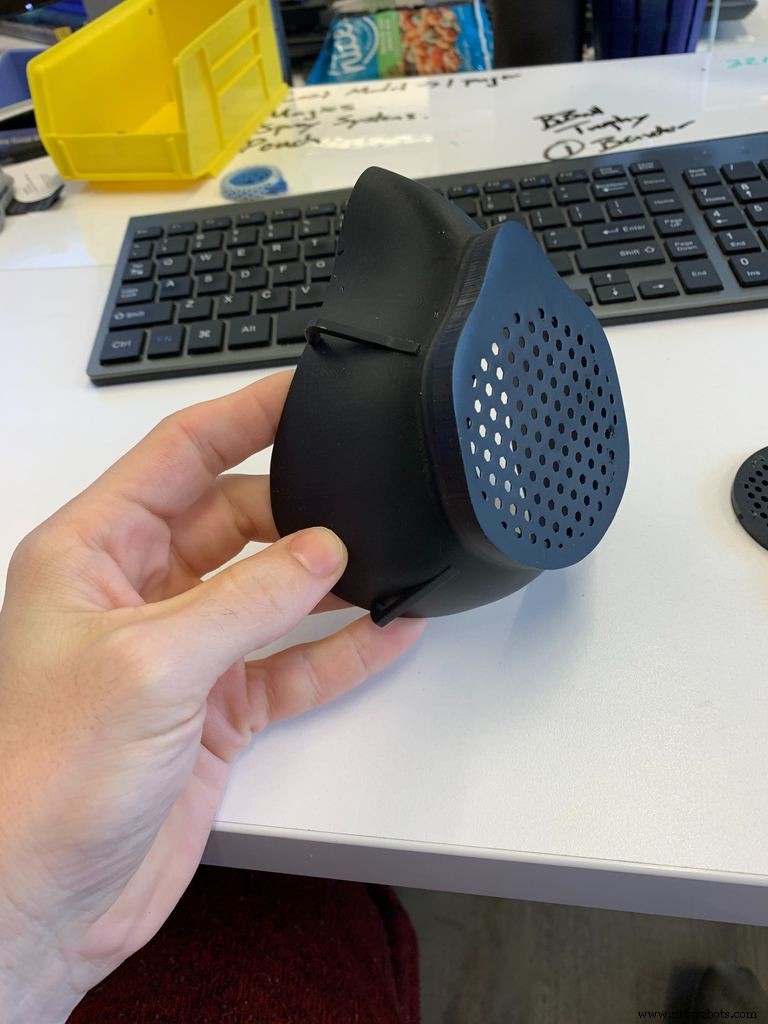
Notre premier prototype imprimé comprenait des porte-à-faux et des canaux compatibles FDM pour éviter les vides sur DLS
Ces prototypes ont apporté d'autres changements de conception :consolider la couverture avant avec le corps principal du masque pour l'imprimer en une seule pièce, épaissir les boucles de sangle pour plus de durabilité, et réduire la densité du motif de grille et le rendre circulaire pour une impression plus facile sur FDM. Nous avons pu commencer à imprimer nos deuxièmes prototypes samedi soir, seulement 24 heures après le début du projet.
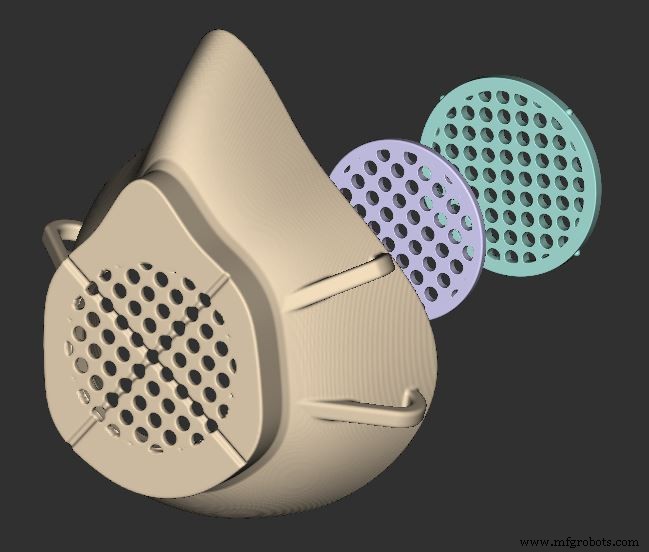
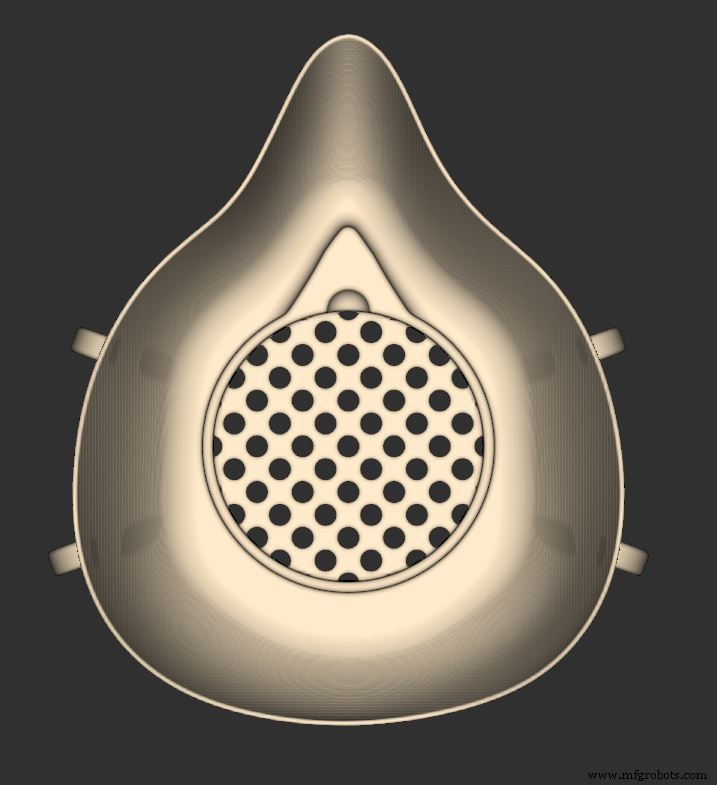
Notre deuxième prototype imprimé a consolidé les pièces (à gauche). Intérieur du masque avec évidement pour insérer le doigt et faire sortir le couvercle du filtre encliquetable (à droite).
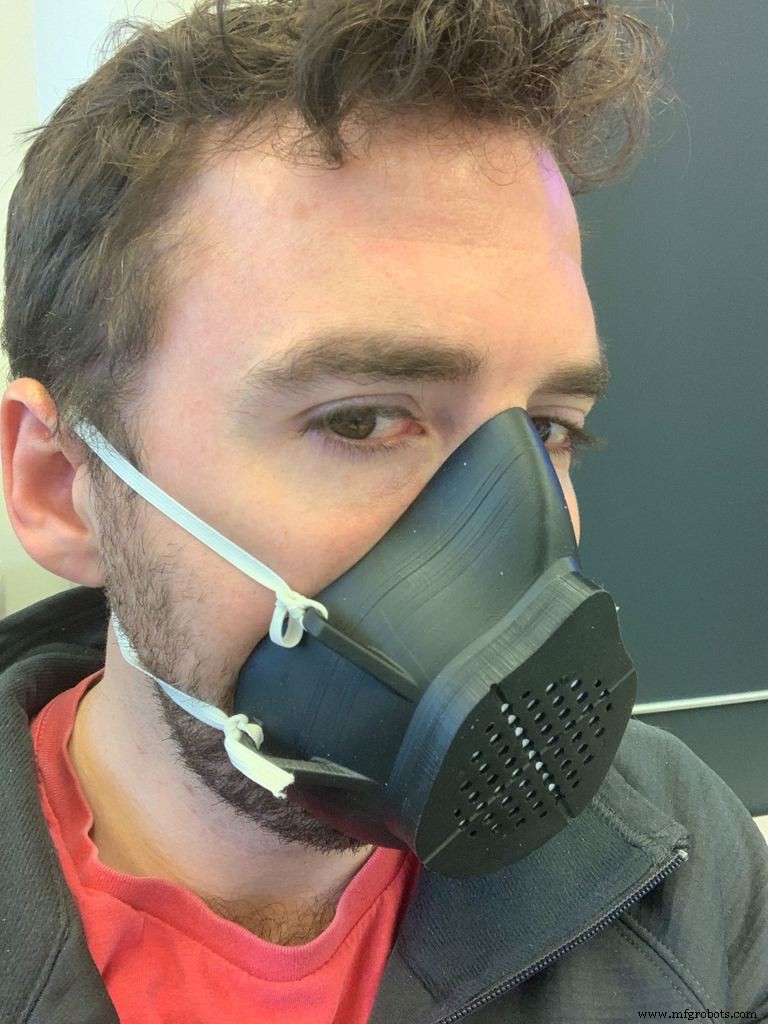
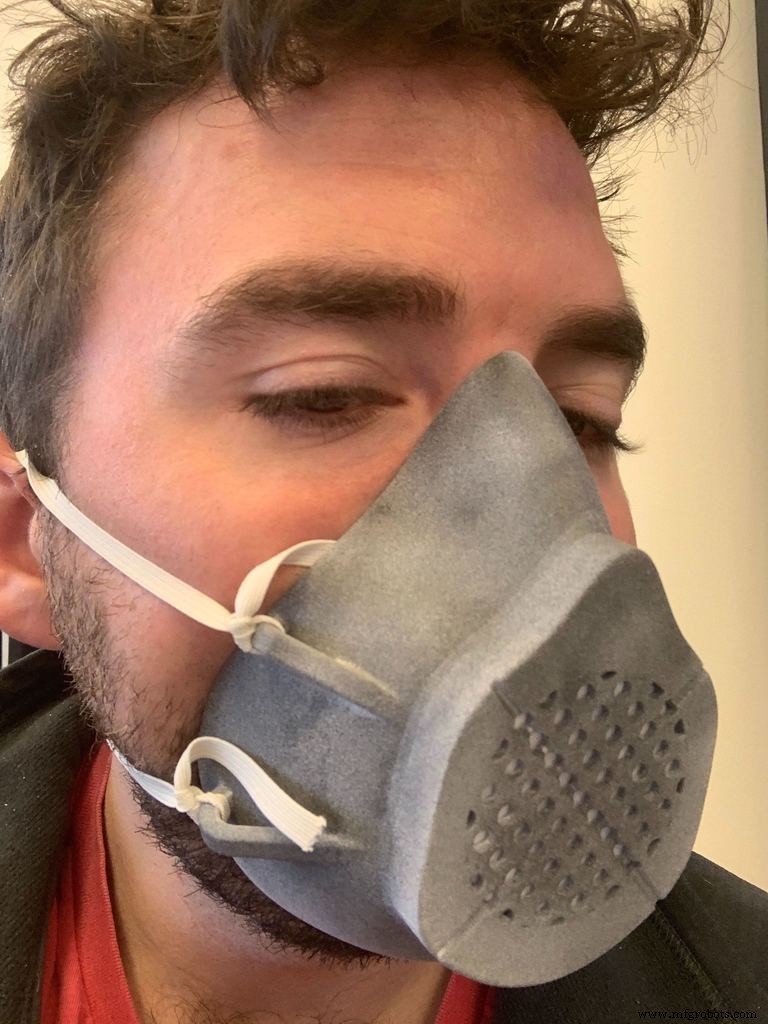
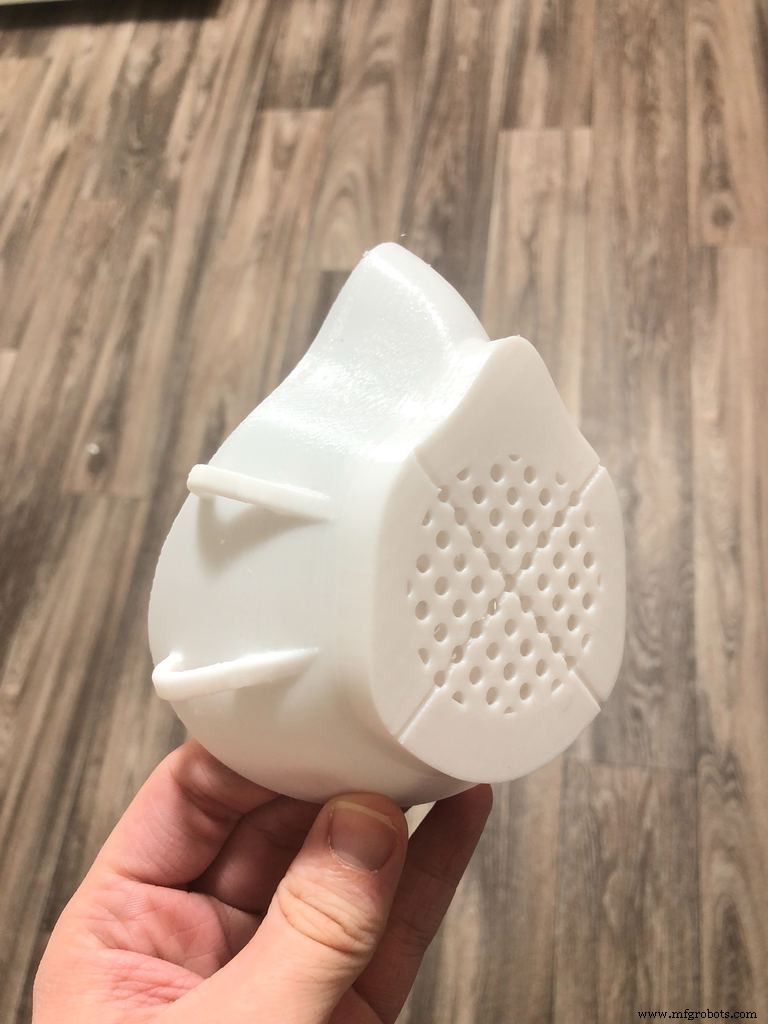
Deuxième prototype imprimé en Carbone RPU70 (gauche), HP PA12 (milieu) et PLA imprimé FDM (droite)
Parallèlement au processus de conception, nous avons puisé dans notre réseau pour mieux comprendre le besoin et identifier les personnes à tester par les utilisateurs. En moins de 24 heures, nos amis de P33 nous ont mis en contact avec une douzaine de médecins et d'employés d'une fondation de recherche médicale pour mieux comprendre les masques N95. Nos employés ont également contacté les professionnels de la santé qu'ils connaissaient. Dimanche, deux jours seulement après le lancement du projet, nous avons effectué des tests d'ajustement avec notre deuxième prototype sur 10 personnes dans quatre endroits.
Les deux semaines suivantes se sont poursuivies dans ce schéma - conception, impression, test, répétition. Notre troisième prototype imprimé comportait une refonte du mécanisme de rétention du filtre. La géométrie du périmètre en demi-cercle décalé fonctionne comme une came qui verrouille la pièce en place lorsqu'elle est tordue par friction (voir ci-dessous.) Il y a deux languettes qui forcent le couvercle vers le bas dans la position tournée ou verrouillée pour assurer une bonne étanchéité autour du filtre. Nous avons créé une version avec une zone perforée en forme de cœur pour rendre le masque moins intimidant. À partir de cette série de prototypes, nous avons conçu et testé des masques de deux tailles différentes.
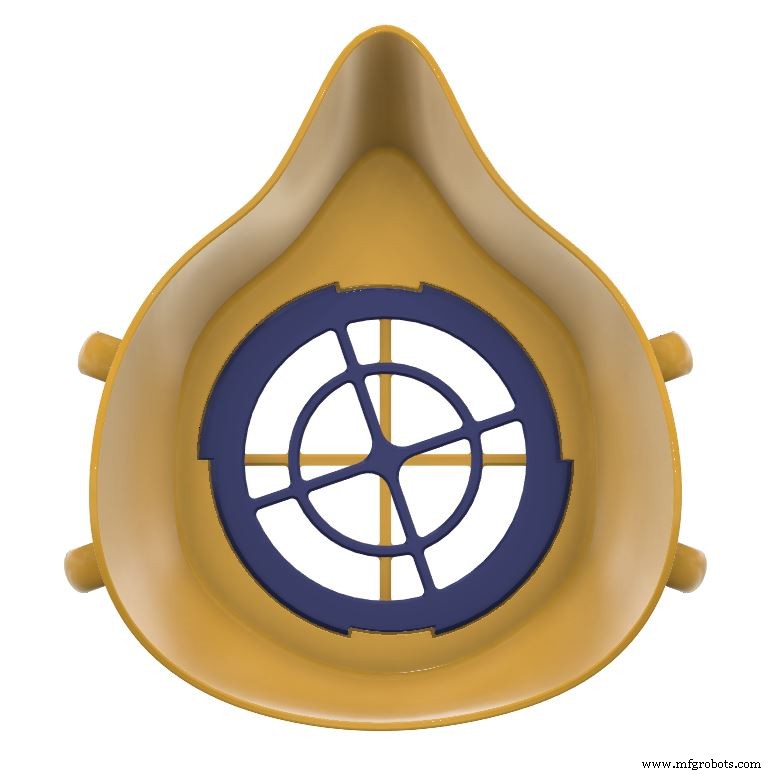
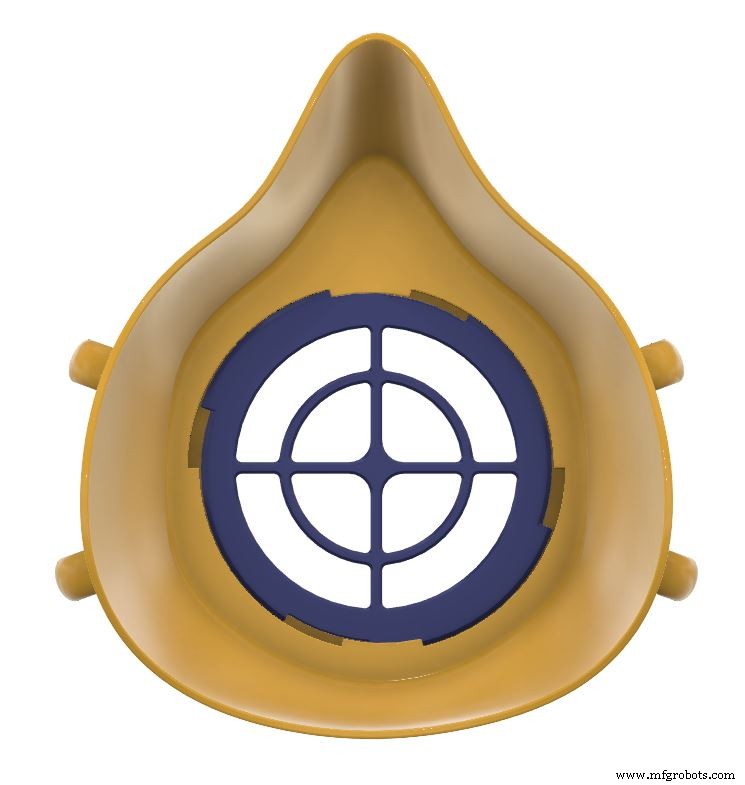
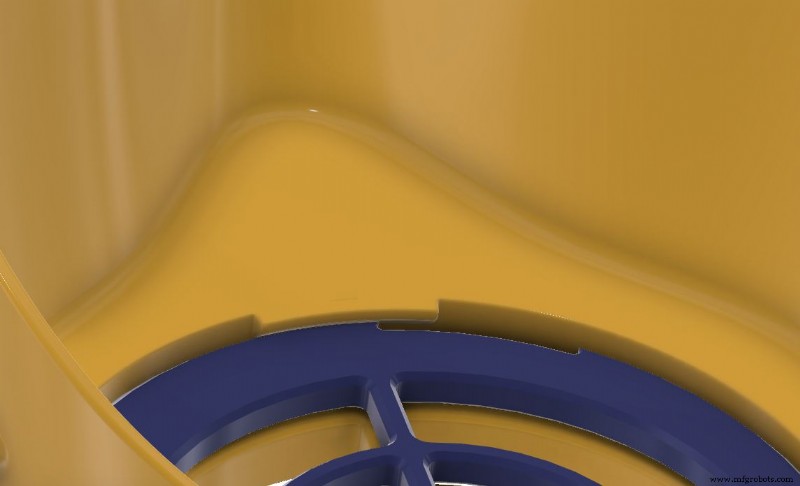
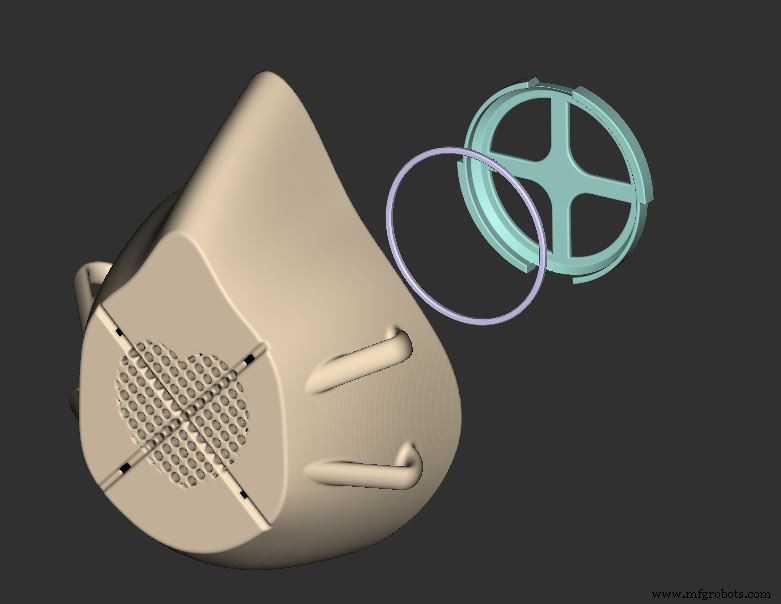
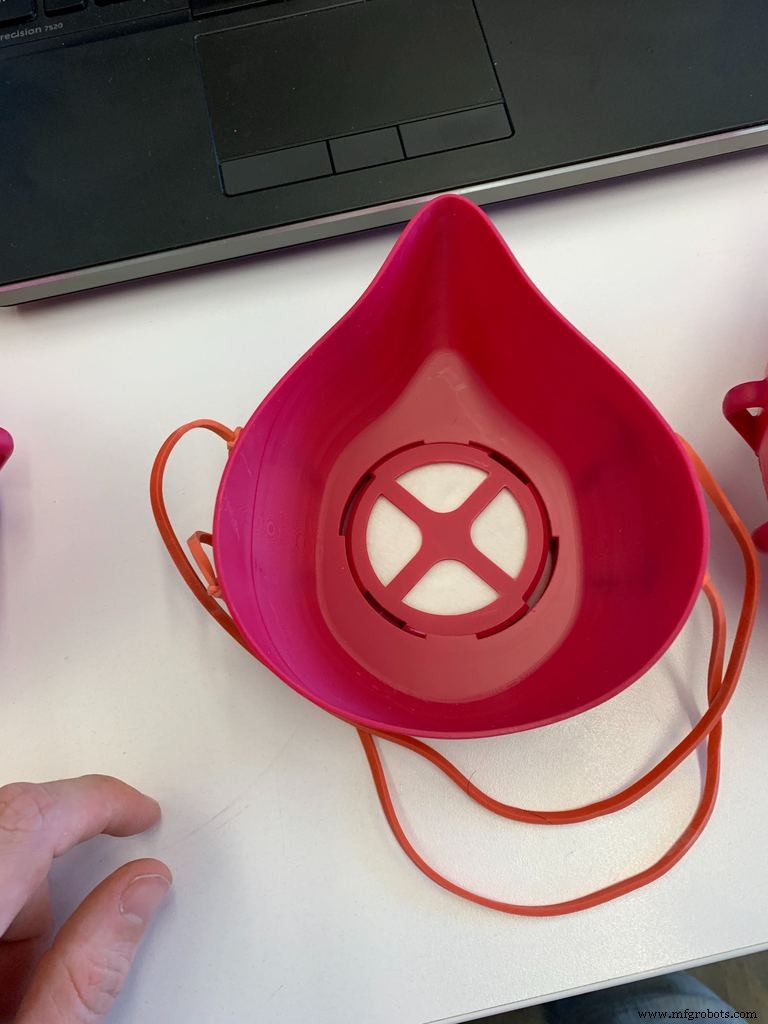
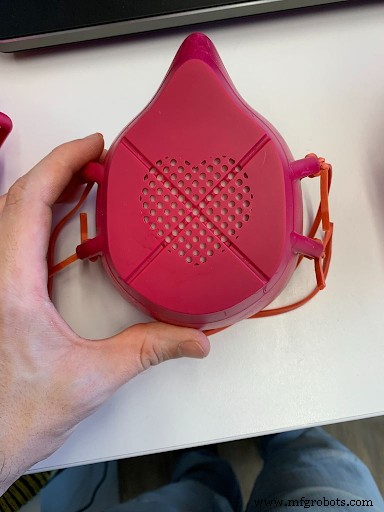
Troisième prototype imprimé avec capuchon torsadé.
Par le quatrième prototype, nous étions principalement préoccupés par la facilité de respiration et le bon ajustement. Pour résoudre ce problème, nous avons essayé de maximiser la région perforée et de minimiser sa densité (en perdant malheureusement le cœur) pour réduire la résistance au flux d'air. Nous avons également modifié les mesures pour les deux tailles en fonction des commentaires des tests des utilisateurs. À ce stade, nous étions suffisamment confiants dans la fonction et la taille du masque pour publier la première version en tant que conception open source.
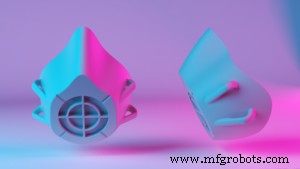
Conception pour l'accessibilité
Pour rendre le masque accessible au plus grand nombre, nous avons créé un design open source pouvant être fabriqué sur des imprimantes 3D domestiques. Cette décision a ajouté des contraintes de conception et de matériaux. Un masque rigide ne pouvait pas s'adapter à une grande variété de formes de visage, nous avons donc exploré l'ajout d'un matériau flexible au bord intérieur du masque pour améliorer son étanchéité au visage.
Nous avons prototypé un premier concept en utilisant SIL 30 sur Carbon DLS. Nous avons ensuite testé de nombreuses méthodes pour créer une étanchéité efficace au visage (décrites ci-dessous), y compris un gant découpé, du silicone imprimé et moulé, un matériau de prothèse faciale moulable, des joints en TPU et PLA imprimés en FDM et des coupe-froid. En fin de compte, nous avons opté pour un coupe-froid, qui est biocompatible, facilement nettoyable et facile à trouver.
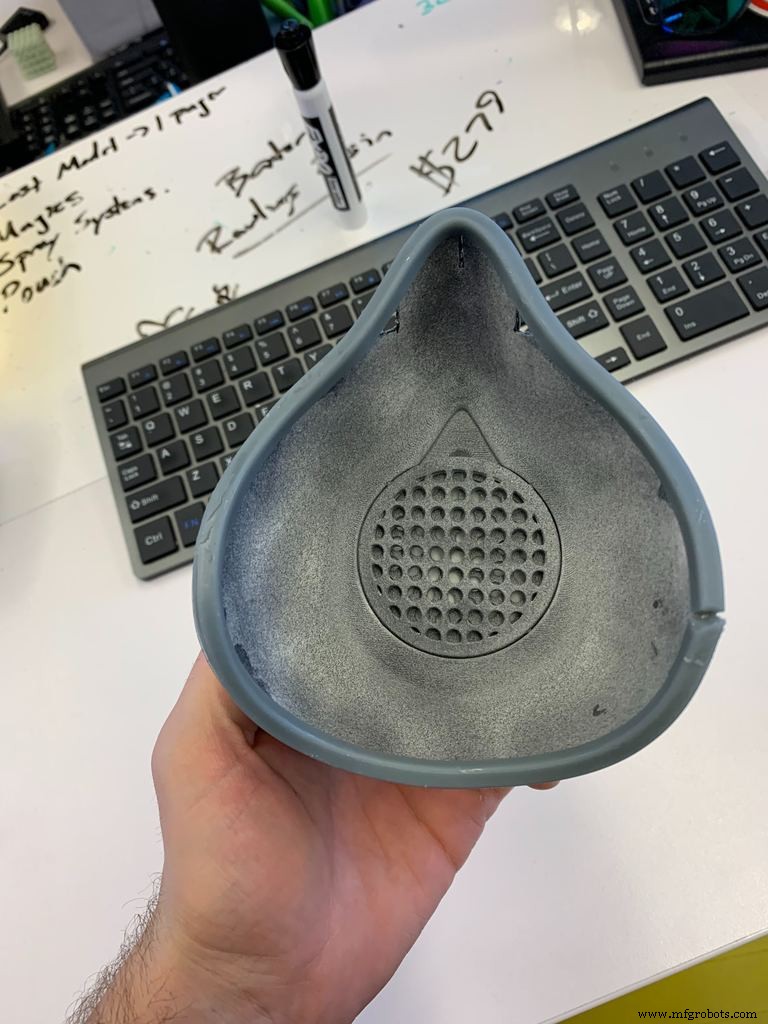
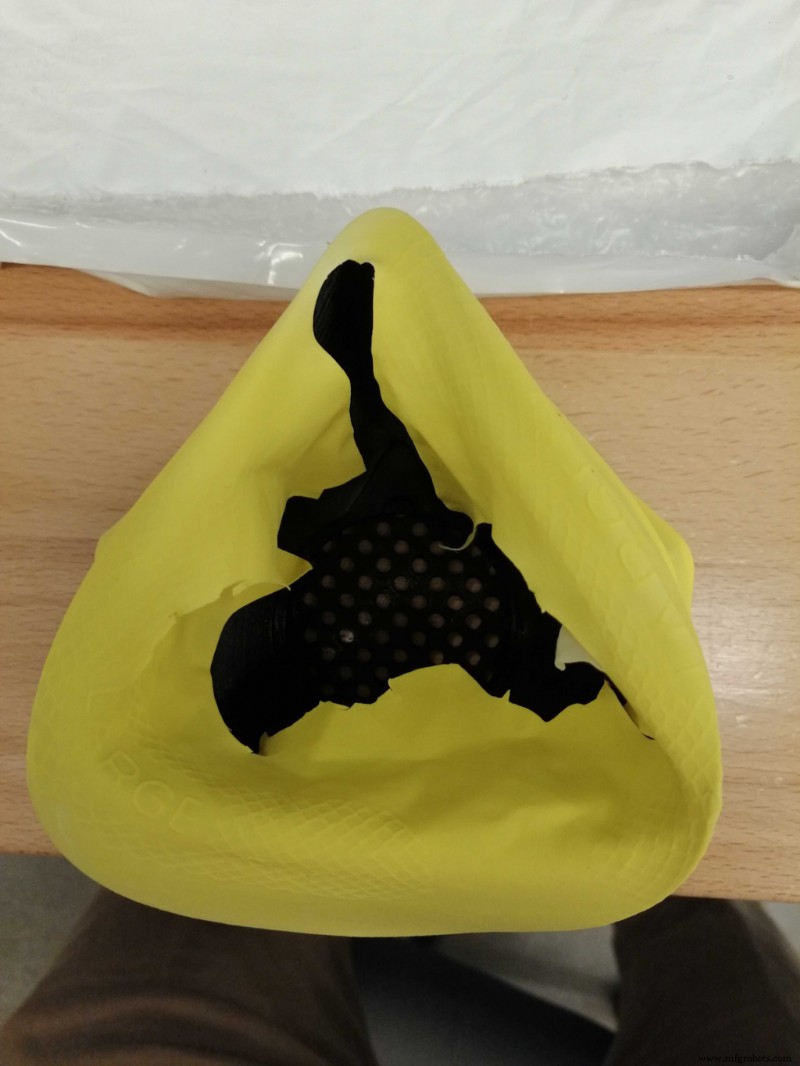
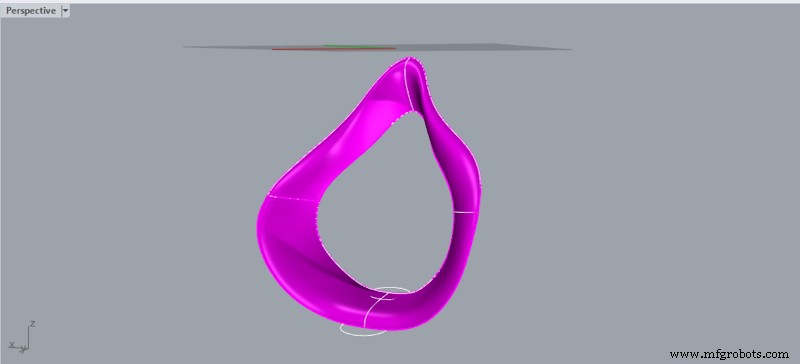
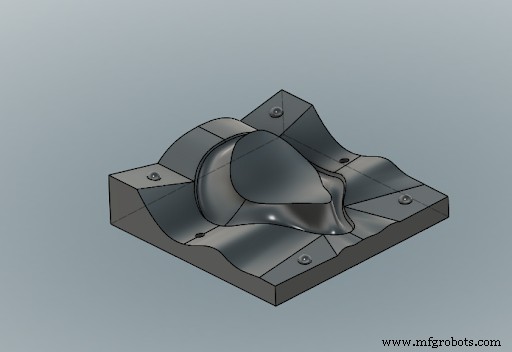
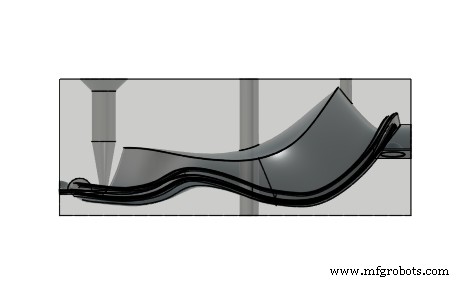
Maquette de formulaire pour silicone moulable
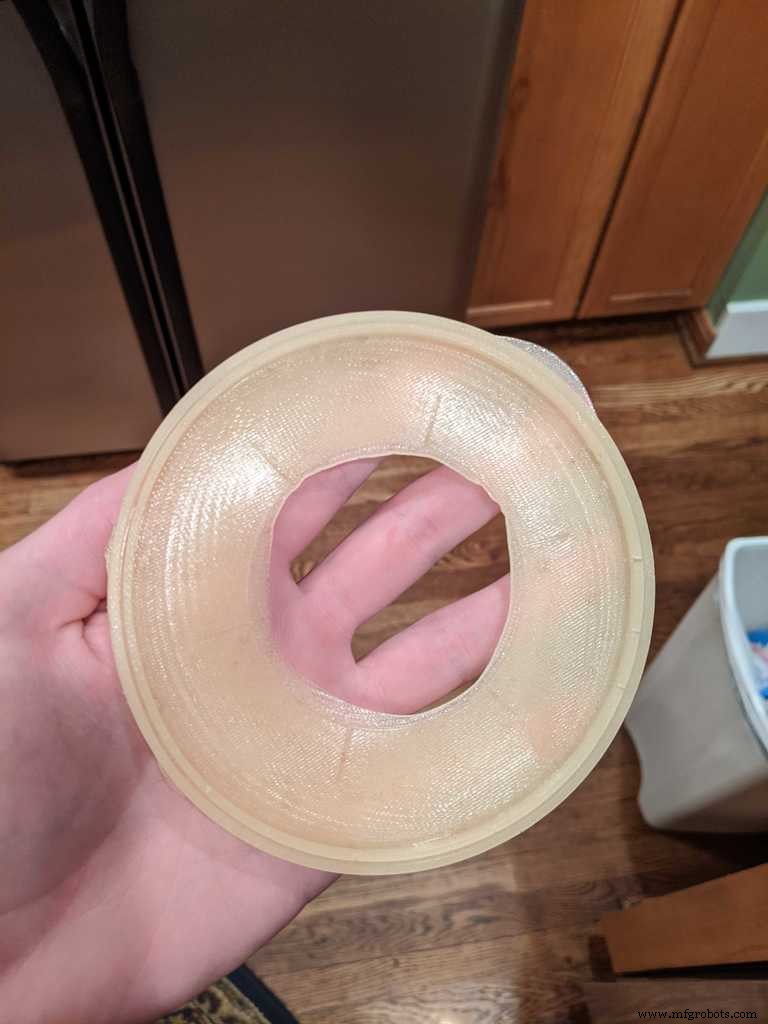
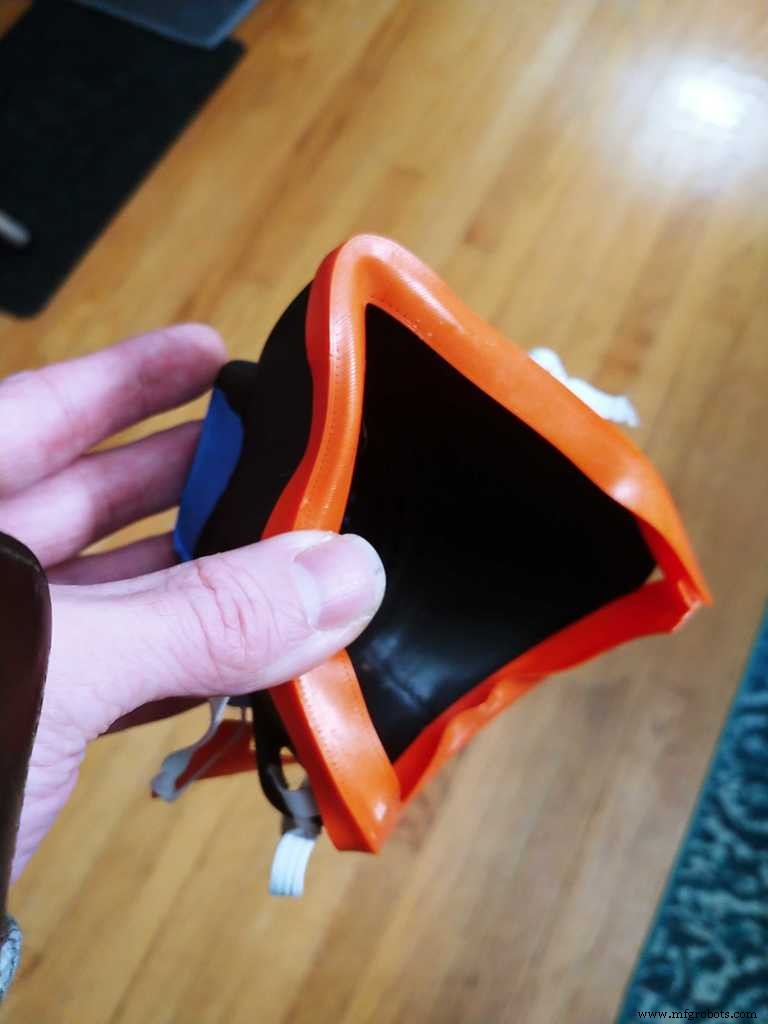
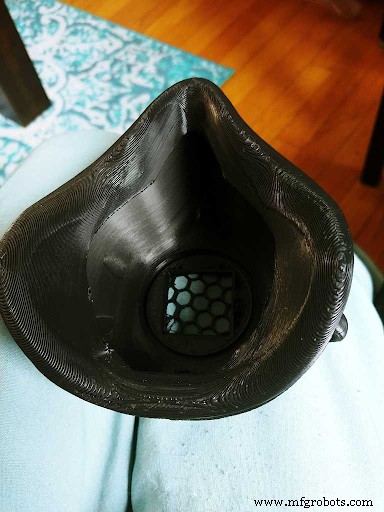
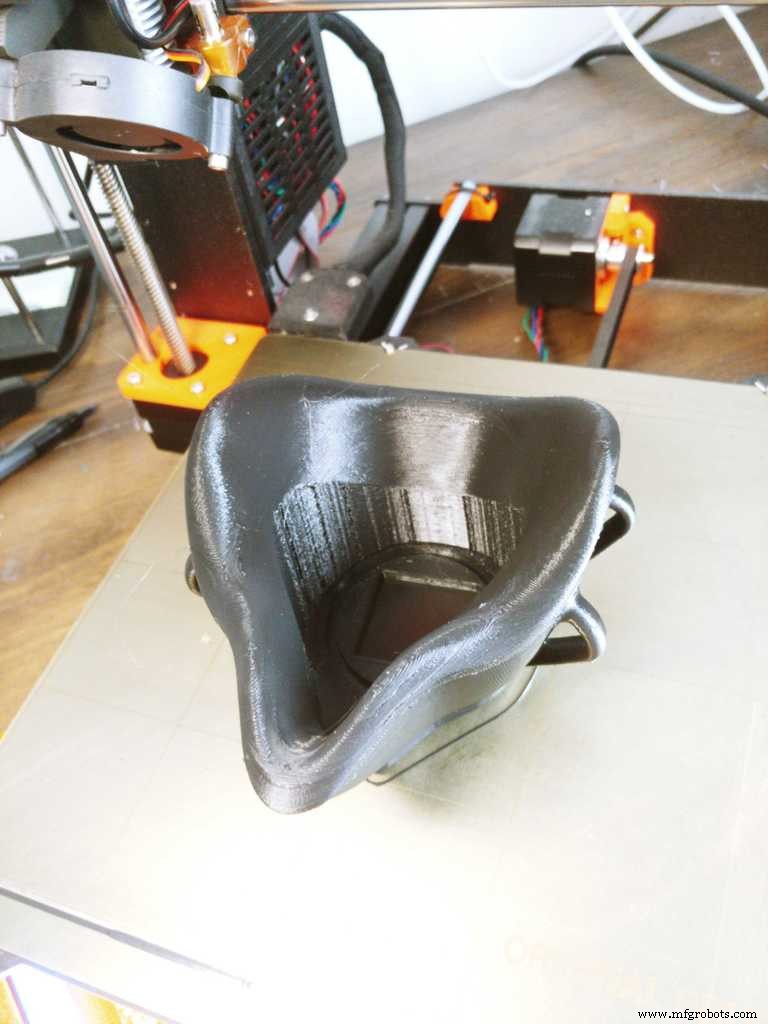
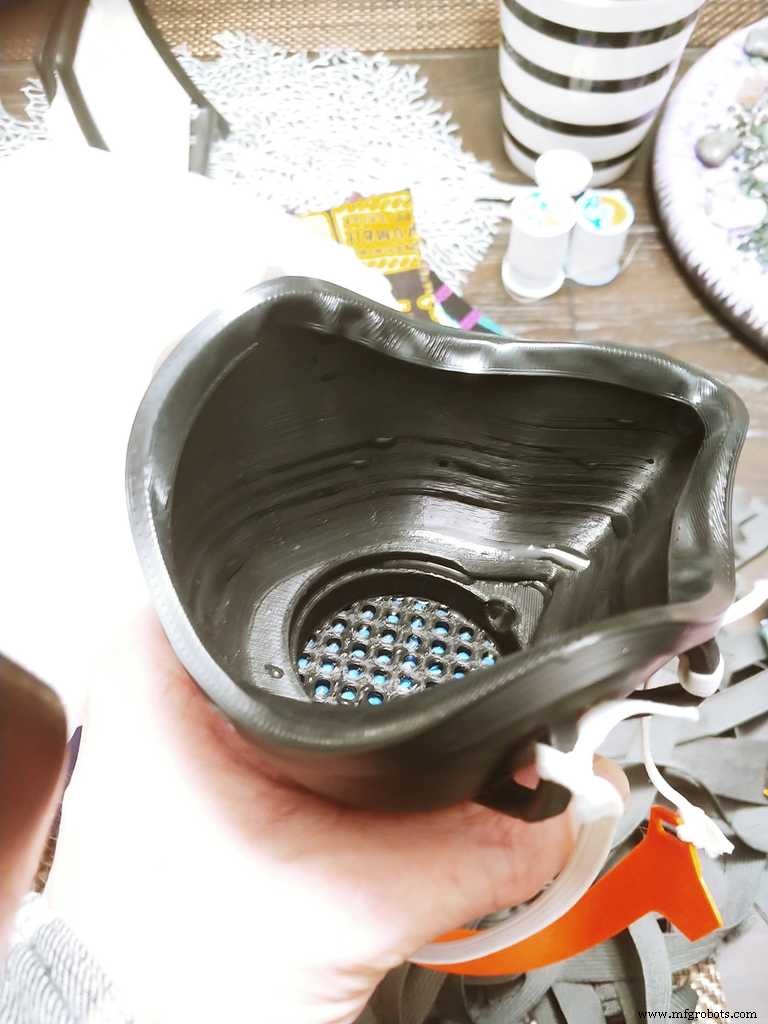
Joint fin en PLA intégré
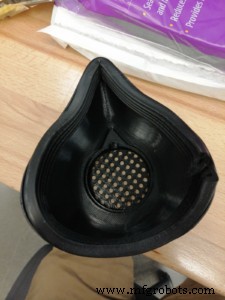
Formation rapide de l'équipe
J'attribue le succès de l'itération rapide de ce projet non seulement à la puissance des outils de conception numérique et de la technologie de fabrication additive, mais aussi au dévouement et à la diversité de l'équipe que nous avons réunie à partir de différentes parties de l'entreprise. Daniel Baker (responsable de l'ingénierie de fabrication) a fourni des commentaires à DFM et a passé des nuits blanches à imprimer et à post-traiter les prototypes. Tim Ouradnik (ingénieur d'application) s'est procuré du matériel d'étanchéité, a assemblé des prototypes et s'est rendu dans tout Chicago pour effectuer des tests d'utilisateurs à distance sociale. Uriah Foley et Eldon Whitis (techniciens de laboratoire) ont testé des prototypes et exploré des joints intégrés sur leurs imprimantes 3D personnelles à la maison après les heures.
Nick Tonini (gestionnaire de programme) a fourni des solutions inventives sans fin et des commentaires sur la conception. Jerry O'Leary (concepteur en chef) a amélioré nos conceptions et créé des rendus conceptuels. Charlie Wood (directeur de l'ingénierie informatique) a assuré la direction de la conception des joints. Hallee Deutchman (directrice des matériaux et de la technologie de fabrication) a assuré la liaison avec nos partenaires et notre équipe juridique avant de publier la conception. Sheila Seles (Senior Content Manager) et Austin Belisle (Content Specialist) ont conçu, publié et promu notre design.
La liste de remerciements ci-dessus vise non seulement à rendre hommage aux personnes qui ont contribué à ce processus, mais également à démontrer le pouvoir de la culture d'entreprise pour rendre de nouvelles choses possibles. Nous avons travaillé sur ce projet en dehors de nos responsabilités et structures d'équipe normales parce que nous voulions créer un produit qui pourrait avoir un impact sur le monde au-delà de Fast Radius. Cet esprit a aussi traversé les frontières de l'entreprise; nous sommes reconnaissants à P33 et à tous les médecins qui ont donné de leur temps et de leur expertise. Si nous n'apprenons rien d'autre de cette pandémie, j'espère que nous continuerons d'avoir l'intention de créer une culture de diversité, d'humilité et de collaboration alors que nous nous efforçons de répondre aux défis mondiaux urgents.
Notre design est disponible et prêt à être imprimé. Vous pouvez trouver des fichiers CAO et des instructions sur notre site Web.
Prêt à fabriquer vos pièces avec Fast Radius ?
Commencez votre devisTechnologie industrielle
- L'avenir, c'est… la collaboration
- Fonctionnalité dans le magazine MRO
- Le Mark Two
- Dans les coulisses de notre blog
- Les effets du COVID-19 sur la fabrication
- Les avantages tangibles de la réalité virtuelle dans le domaine de l'ingénierie
- Tableau, les données derrière les informations
- L'importance de la détection des décharges partielles
- L'ingénierie de maintenance du futur