Vous pouvez l'emporter avec vous :les méthodes de travail hybrides déplacent certaines tâches n'importe où
La montée en flèche de l'utilisation des outils de production et de communication numériques pendant la pandémie de COVID-19 a accéléré l'avenir du lieu de travail hybride, dans lequel certains employés et certaines tâches peuvent être redirigés en dehors de l'usine de fabrication.
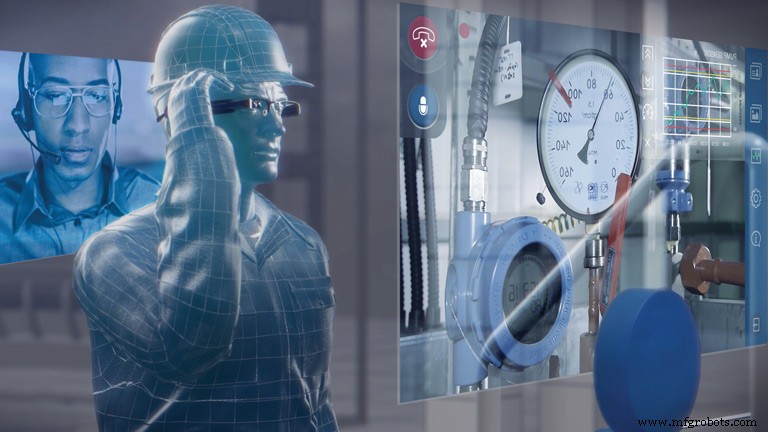
Cependant, alors que le personnel comme les concepteurs et les ingénieurs peut facilement travailler à distance - et, selon l'entreprise, le faisait avant la pandémie - les machines ont toujours besoin d'opérateurs sur place. Cela dit, des solutions telles que la réalité virtuelle ou mixte et la connectivité basée sur le cloud poussent les entreprises à repenser la façon dont elles planifient et exécutent certaines tâches de fabrication.
Les avantages de l'hybride
Confrontés non seulement à des pénuries de travailleurs qualifiés, mais également à la nécessité de réorganiser leurs lieux de travail pour s'adapter aux protocoles pandémiques, les fabricants ont intensifié leur quête pour trouver et optimiser des outils numériques pour leurs environnements uniques.
"Bien que les avantages du point de vue de la santé et de la sécurité soient clairs lors d'une pandémie mondiale, les fabricants en particulier ont vu des avantages de productivité et de rétention des employés" dans la poursuite d'arrangements de travail hybrides, a déclaré Reid Paquin, directeur de recherche pour IDC Manufacturing Insights de Needham, Mass. "Plus un tiers a également connu une expérience/satisfaction des employés plus élevée, ce qui, selon nous, jouera un rôle dans les efforts de l'industrie pour faire face aux problèmes de talent/de main-d'œuvre. »
En plus de la fabrication, "la plupart des grands équipementiers ont des éléments de service sur le terrain, et un problème qui est presque universel à l'heure actuelle est la perte d'employés et les problèmes de transfert de connaissances", a déclaré Charlie Neagoy, vice-président senior du succès client pour Librestream. "Nous avons actuellement environ trois millions de personnes en avance sur le calendrier en termes de retraite, et cela a accéléré ce déficit de connaissances. La main-d'œuvre hybride, c'est-à-dire la capacité de faire des choses à partir de différents endroits, aide à compenser la perte de connaissances qui découle de la retraite anticipée. Les effectifs hybrides peuvent offrir des emplois dans le monde entier et différents types de flexibilité à leurs employés."
Librestream, basé à Winnipeg, Manitoba, Canada, fournit une plate-forme de solution à distance de réalité augmentée (RA). "Un avantage connexe des lieux de travail hybrides est qu'ils permettent des plates-formes de collaboration partagées entre plusieurs parties", a ajouté Neagoy. « La sécurité est également une raison majeure d'utiliser une main-d'œuvre hybride. De nombreux sites et équipements de fabrication sont dangereux, c'est pourquoi l'accès à distance à un site diminue le risque d'accident. »
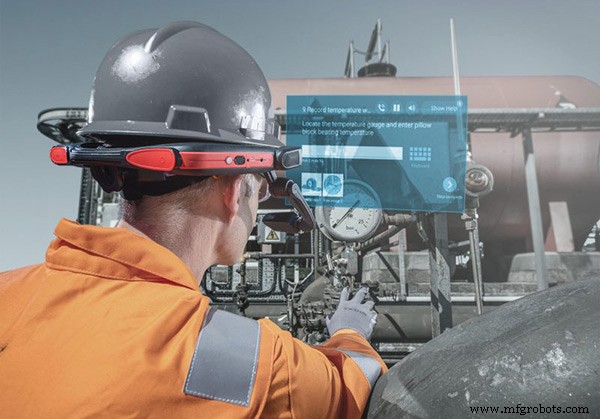
De plus, les inspections et les certifications requises peuvent être effectuées à distance, a poursuivi Neagoy. « Notre plateforme Onsight nous permet de suivre le nombre d'inspections que nos clients effectuent chaque semaine. Nos clients effectuent entre 7 000 et 8 000 inspections à distance chaque semaine. Avant le COVID, nous enregistrions environ 2 000 inspections par semaine."
La pandémie a démontré qu'une main-d'œuvre hybride apporte une résilience organisationnelle et une efficacité des travailleurs accrues, selon Federico Sciammarella, président et directeur technique de MxD, Chicago, qui se concentre sur la fabrication numérique et fait partie de Manufacturing USA, un réseau de 14 instituts de fabrication de pointe.
"Si une organisation dispose de la bonne infrastructure réseau et qu'elle est sécurisée, il est possible d'exécuter des opérations à distance", a déclaré Sciammarella. "Une infrastructure réseau appropriée rend une entreprise plus résiliente, car les individus peuvent toujours accéder aux données nécessaires pour maintenir les opérations en cours, même lorsqu'ils travaillent à distance."
Comment et par où commencer
Comme pour toute transformation organisationnelle ou industrielle, la technologie ne résoudra pas à elle seule les problèmes émergents. Les outils de surveillance et de collaboration à distance sont devenus monnaie courante, mais comme toujours, une bonne planification est essentielle pour adopter un modèle hybride.
« La collaboration, la visioconférence et les plates-formes/applications de partage de contenu sont quelques-uns des domaines dans lesquels les fabricants ont investi ou cherchent à investir pour mieux activer les modèles de travail hybrides », a noté Paquin d'IDC Manufacturing Insights. « La plupart des fabricants auront presque toujours besoin d'avoir des employés sur place. La maintenance/la gestion des actifs est l'un de ces domaines où ce sera le cas ; il doit y avoir quelqu'un qui tourne une clé. À l'avenir, les fabricants pourront peut-être en transférer davantage vers les robots, mais pour le moment, la maturité de la technologie et les coûts d'investissement n'en font pas une réalité pour la plupart des fabricants. »
Les fabricants qui avaient déjà fait d'importants investissements dans l'automatisation, la collecte de données et la connectivité à distance avaient l'infrastructure en place pour soutenir ce changement avant la pandémie, a reconnu Paquin. « Nous avons constaté que les fabricants qui avaient mis en place des systèmes cloud, comme les ERP, étaient les mieux adaptés au travail hybride. La meilleure approche consiste à élaborer une stratégie/feuille de route à l'échelle de l'organisation, mais à la déployer par étapes plus petites. Commencez par des fonctions de type back-office, car moins d'investissements seraient nécessaires pour permettre le travail à distance pour ces groupes. Faites attention aux politiques de travail à distance en place et à la façon de gérer les employés à distance, et intégrez les meilleures pratiques et les leçons apprises au fur et à mesure que vous continuez à vous étendre à d'autres fonctions."
Notant que le travailleur moyen passe 240 heures par an - 10 jours - à attendre des informations, Neagoy de Librestream a indiqué que "si vous êtes un opérateur sur le terrain, une bonne stratégie consiste à prendre les connaissances d'un expert en la matière et à les intégrer dans le numérique. instructions de travail, donc vous n'attendez plus cet expert.”
Mettre la nouvelle technologie entre les bonnes mains des travailleurs est essentiel, a poursuivi Neagoy. "Si vous allez introduire une nouvelle technologie, commencez par l'adepte de la technologie. Nos clients constatent généralement une distribution bimodale de l'utilisation :c'est radicalement différent entre les personnes à 10 ans de la retraite et les personnes à moins de 10 ans de carrière."
Soyez assuré, dit-il, que « c'est quelque chose qui peut être mis en place en trois mois. Ce ne sera pas complètement réalisé en trois mois, mais en trois mois, vous devriez être capable de déplacer l'aiguille."
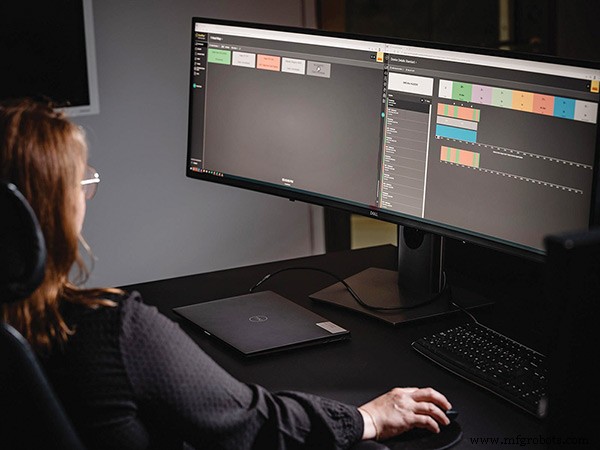
Comme lors de l'approche d'autres opérations de fabrication, a déclaré Sciammarella de MxD, "les actions doivent être planifiées avec soin et de manière holistique, en gardant à l'esprit les outils de base de l'amélioration continue. Il est important d'examiner d'abord ce que vous avez actuellement en place et pourquoi. Le « pourquoi » est essentiel et peut sembler évident, mais ce n'est pas toujours le cas, surtout si vous avez une longue histoire de flux de travail. Une entreprise voudra arriver à un point où l'équipe sait quelles données et informations peuvent être numérisées - si ce n'est pas déjà fait - et comment cela peut être utilisé pour soutenir non seulement des horaires de travail flexibles, mais aussi un processus d'amélioration continue qui peut être exploité à distance afin que la production puisse continuer à fabriquer des produits et à optimiser le travail selon les besoins."
Si une organisation a commencé à mettre en œuvre des technologies cloud pour les données d'entreprise, a-t-il ajouté, "elle pourrait tirer parti de ces technologies cloud pour la collecte de données opérationnelles et rendre les fichiers et les informations facilement disponibles pour cette main-d'œuvre".
Succès récents
Pour Fives Lund de Seattle, un producteur de machines hautement personnalisées, la flexibilité du lieu de travail et le fait de disposer des bons outils pour effectuer des tâches critiques à distance font partie de la culture depuis des années.
Saisir les opportunités pour s'assurer que leurs employés peuvent être aussi efficaces que possible où qu'ils se trouvent "est un processus continu depuis que nous avons rejoint le groupe Fives en 2015", a déclaré le PDG Casey McGarity. "Même avant la COVID, c'était un processus continu et un voyage, pas une destination."
Avant la pandémie, "notre main-d'œuvre était assez fortement concentrée dans notre usine de Seattle, mais nous avons toujours eu des ingénieurs et des techniciens qui étaient sur le terrain pour soutenir l'équipement", a ajouté Jonathan Schwedhelm, ingénieur en chef en mécanique et directeur de l'ingénierie. "Nous co-concevons également certains de nos équipements d'automatisation complexes avec nos sociétés sœurs à travers le monde."
Puis vint la pandémie. Et tandis que Fives Lund était au rythme des autres grands employeurs de sa région en ce qui concerne les personnes travaillant à domicile, "nous avons un environnement plutôt pratique", a expliqué Schwedhelm. "Nos ingénieurs et techniciens travaillent en étroite collaboration pour construire, tester et entretenir nos équipements." Cela signifiait faire preuve de créativité pour continuer à concevoir et à livrer des équipements et à soutenir les clients.
« Au début, cela signifiait que certains ingénieurs ramenaient chez eux des projets et des assemblages plus petits pour travailler. Certains de nos ingénieurs de contrôle ont installé du matériel chez eux afin de pouvoir programmer les machines, mais cela n'est vraiment pas à l'échelle."
C'est là que Run MyVirtual Machine de Siemens est entré en jeu. Le logiciel de simulation de fonctionnement de la machine "offre aux ingénieurs de contrôle la possibilité de commencer à construire les 'entrailles' de contrôle de la machine et de tester la cinématique et le fonctionnement, ainsi que de simuler les machines à l'échelle pour assurez-vous qu'ils font les choses aussi vite que vous le pensez », a déclaré Schwedhelm.
Run MyVirtual Machine a fait des merveilles sur un projet qui a commencé l'année avant la pandémie, a-t-il poursuivi.
« En 2019, nous avons commencé à travailler sur un gros équipement d'automatisation, et notre client nous a demandé d'utiliser des commandes CNC Siemens. Nous connaissons un certain nombre de systèmes de contrôle numérique différents, mais la machine que nous construisions avait une cinématique vraiment unique, et nous savions qu'elle comportait de gros obstacles techniques que nous devions éliminer avant que le matériel ne soit disponible - et assurez-vous nous pourrions le faire sans avoir à nous asseoir devant les panneaux de contrôle ici dans notre établissement."
Bien qu'expérimenté avec d'autres logiciels de modélisation, a-t-il poursuivi, "puisqu'il s'agissait d'un projet Siemens, cela nous a permis pour la première fois de tirer parti de cet outil - utilisez-le dans la planification, utilisez-le pour réduire les risques et assurez-vous que nous sommes prendre de bonnes décisions tout au long du processus de conception. Et maintenant que la chaîne d'approvisionnement devient un problème plus important et que les délais de livraison de nos composants de contrôle peuvent être difficiles, cela nous permet de continuer à avancer sans être complètement bloqués."
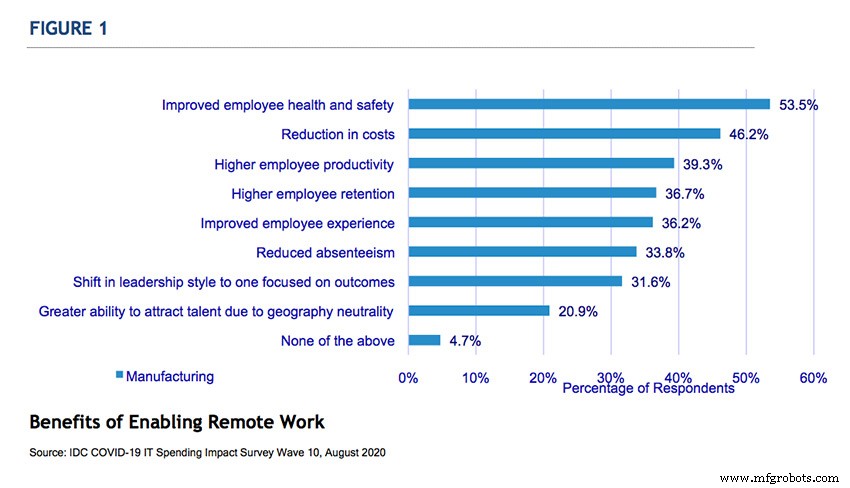
La culture de Fives Lund repose sur le fait que "nos ingénieurs (mécaniques, électriques et logiciels) travaillent souvent côte à côte sur le terrain et construisent des machines et effectuent des dépannages", a noté McGarity. « À tout le moins, les ingénieurs sont disponibles pour visiter l'atelier lorsqu'ils rencontrent des problèmes » ou pour aider à la planification, à l'assemblage ou aux tests. Dans la mesure où les ingénieurs ne "participent pas activement" aux tâches de l'atelier, "ils sont profondément impliqués dans la planification de ces choses".
Abordant le problème central de la mise en œuvre de flux de travail hybrides dans la fabrication, McGarity a noté que même si le personnel de l'atelier devait rester sur place, « il était très difficile et très différent pour Fives Lund de ne pas avoir les ingénieurs sur place pour aider à ce processus. Comme beaucoup d'entreprises, nous pesions les risques de COVID par rapport au risque de la culture et de l'efficacité qui découlent d'une équipe solide et cohésive. Les outils dont nous disposons aident à maintenir cette culture. Nous avons commencé avec un groupe particulièrement sain et fort, mais ces muscles collectifs s'atrophient un peu, même avec de bons outils. Plus les outils sont efficaces, plus nous sommes capables de conserver nos forces plus longtemps. Mais nous devons aussi revenir en arrière et nous rappeler :"Nous sommes plus forts lorsque nous sommes physiquement proches".
Adaptation avec des workflows ajustés
Les solutions hybrides viennent également naturellement chez Sandvik Coromant, qui fournit non seulement des outils qui favorisent les possibilités de travail à distance pour ses clients, mais a également ajusté les flux de travail dans ses propres usines d'outils de coupe.
« Le fait d'avoir la technologie en place, en ce qui concerne la CAO/FAO, nous a aidés, mais nous avons évidemment encore besoin de personnes ici pour faire fonctionner l'équipement », a déclaré le directeur de l'unité de production, Richard Boyle. « Nous n'en sommes pas au point où nos équipements s'éteignent - nous avons toujours besoin de nos opérateurs ici - mais cela nous a donné une bonne occasion d'aller de l'avant avec les aspects techniques de notre atelier de fabrication, avec des ingénieurs de fabrication au bureau, sur l'atelier de production et pouvoir travailler à domicile un pourcentage du temps. »
Lorsque la pandémie a frappé, les concepteurs de Sandvik ont également travaillé à distance la plupart du temps, a déclaré Boyle, se rendant à l'atelier à vélo chaque semaine selon un horaire rotatif pour fournir un soutien à la production tout en limitant l'exposition d'une personne. En attendant, l'entreprise emploie ce qu'elle appelle une production sans personnel, en alternant les opérateurs de machine "lorsque nous avons un équipement qui est automatisé et fonctionne sans la présence d'un opérateur".
Boyle a expliqué qu'entre deux postes d'opérateur de machine de huit heures, un intervalle de quatre heures est prévu. Avec deux cellules en face l'une de l'autre, ces horaires peuvent être échelonnés de sorte qu'un seul opérateur doit être sur place pour assister à une interruption dans l'une ou l'autre des cellules. "Nous avons des gens qui commencent à travailler presque 24 heures sur 24 pour s'assurer que nous avons une couverture complète."
Il attribue également au partenariat de Sandvik avec Microsoft et à sa technologie de réalité mixte HoloLens la facilitation du travail hybride. « La plupart des technologies que nous utilisons en production à partir de notre MES et de nos tableaux de bord (toutes les données disponibles) proviennent de leurs solutions. Nous avons eu des pannes ici et là, peut-être pendant quelques heures où nous ne pouvons pas nous connecter à un service, mais elles sont rares."
Pendant la pandémie, Sandvik a commandé un nouvel équipement qui a été acheminé par avion depuis la Suède lorsque tous les voyages de passagers ont été annulés, a rappelé Boyle. "Au lieu d'attendre que le voyage soit à nouveau autorisé et que le technicien suédois puisse venir et terminer l'installation, grâce à l'utilisation d'une technologie comme HoloLens, nous avons pu faire travailler notre personnel de maintenance local directement avec cette personne, qui pouvait voir directement à travers son regardons ce qu'ils faisaient et s'assuraient que nous nous concentrions sur les bonnes choses pour que cette machine soit mise en service et opérationnelle. »
En fin de compte, a déclaré Boyle, équilibrer les flux de travail hybrides et traditionnels est « toujours difficile ». C'est quelque chose que vous devez travailler. Avec l'hybride, nous ne disons pas que quiconque est distant à 100 %. Si vous pouvez essayer d'ouvrir un processus à distance qui n'est pas tout à fait prêt pour cela, il est parfois difficile de le réintégrer. Nous avons été très lents et méticuleux pour ouvrir un processus à l'hybride, en nous assurant que nous sommes capable de le maintenir et de le modifier rapidement pour qu'il n'échoue pas.”
Pour les clients, Sandvik fournit des produits prêts à l'emploi à distance, notamment CoroPlus Machining Insights et CoroPlus Process Control, a déclaré Jeff Rizzie, directeur des ventes d'usinage numérique pour les Amériques.
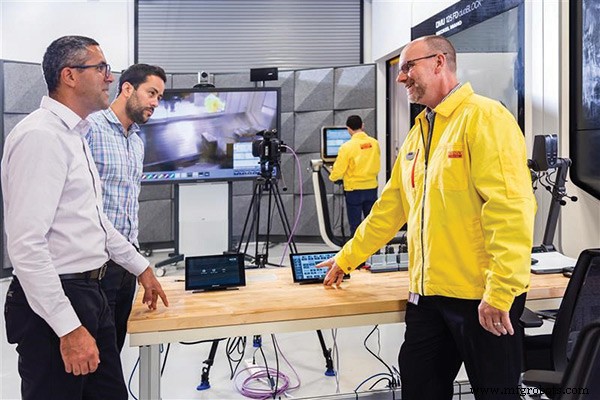
Machining Insights est une plate-forme logicielle en tant que service qui surveille les conditions de la machine, a expliqué Rizzie. « Nous pouvons dire ce qui se passe avec une machine-outil particulière simplement en nous connectant à un site. Je peux comprendre les données d'utilisation, le nombre de pièces que je fabrique et examiner la planification et les multiples points de données provenant directement de la machine. Ces types de solutions sont d'une valeur inestimable, même du point de vue des opérations. Désormais, je n'ai plus besoin d'être dans l'atelier pour comprendre ce qui se passe dans ma boutique en utilisant les données de la bonne manière."
CoroPlus Process Control va encore plus loin dans la mesure de la santé de l'ensemble d'un processus de fabrication, a poursuivi Rizzie. « Il peut effectuer un contrôle adaptatif et remplacer la machine. S'il détecte une collision ou un outil cassé, il peut arrêter automatiquement la machine. Il peut émettre une commande pour acquérir un outil frère ou un outil redondant et redémarrer la fabrication. De plus, il peut faciliter l'usinage sans personnel, ce qui ajoute une mesure de sécurité supplémentaire au processus. »
De plus, Sandvik s'efforce de « perfectionner » ses employés afin de mieux les équiper pour assister les clients à distance, a noté Annika Langeen, vice-présidente du marketing pour les Amériques. « Nous avons équipé nos centres Sandvik Coromant des dernières technologies pour permettre une assistance à distance dans les projets clients et des cours de formation virtuels en direct », a-t-elle déclaré. « Grâce aux dernières technologies audio et vidéo, les clients peuvent voir ce qui se passe à l'intérieur et à l'extérieur des machines dans nos centres Sandvik Coromant et interagir avec nos experts en blouse jaune en temps réel, où qu'ils se trouvent. Depuis de nombreuses années, nous proposons également un vaste programme d'apprentissage en ligne pour fournir aux clients, aux étudiants et aux employés des connaissances en matière d'usinage des métaux. Les participants peuvent suivre le programme de formation et obtenir une certification où ils veulent, à tout moment. »
Le travail hybride dans le futur
La fabrication numérique est souvent présentée comme un outil de recrutement et de rétention des travailleurs. Paquin d'IDC est d'accord.
"Le travail hybride/à distance peut élargir le bassin de candidats pour certains rôles, et les fabricants nous disent régulièrement que c'est la partie la plus jeune de leur main-d'œuvre qui souhaite plus de flexibilité et d'options autour des modèles de travail", a-t-il noté. "Pour une industrie qui a du mal à attirer de nouveaux talents, ne pas adopter de modèles de travail hybrides pourrait rendre cela encore plus difficile."
Le grand défi, a noté Neagoy de Librestream, "est simplement de comprendre où un lieu de travail hybride peut être appliqué. Quatre-vingt pour cent de la main-d'œuvre est sur le terrain, donc la création de main-d'œuvre hybride peut être une perspective écrasante. La recette du succès dans la mise en œuvre d'une main-d'œuvre hybride consiste à identifier des objectifs commerciaux très clairs. Ayez quelque chose de quantifiable et mesurable, et commencez petit. Si vous avez différents domaines fonctionnels qui sont essentiellement des doublons les uns des autres, choisissez-en un et réussissez avec celui-ci, puis appliquez ce que vous avez appris à l'ensemble de l'organisation."
Notez également qu '«il existe une dualité étrange dans la façon dont les gens s'adaptent à la main-d'œuvre hybride», a conseillé Neagoy. « Les personnes qui connaissent le mieux l'entreprise peuvent être celles qui sont les moins douées sur le plan technologique. Faites savoir aux employés expérimentés que les nouvelles technologies hybrides ne sont pas là pour les aider, elles sont là pour aider les autres."
Alors que les plates-formes et les technologies qui existent pour faire de l'hybride une réalité ont évolué pendant la COVID, le problème est maintenant de "comment les intégrer d'une manière qui sera efficace pour les besoins de chaque entreprise", a observé Sciammarella. « Les bons réseaux et la bonne connectivité, c'est-à-dire la 5G, sont-ils présents et comment leur sécurité peut-elle être assurée ? Cela peut être coûteux et nécessitera une réflexion approfondie sur la manière d'intégrer ces outils et plates-formes de la manière la plus économique possible.
« MxD a toujours vu les entreprises qui utilisent le numérique mieux s'en sortir en cas de crise. La pandémie n'était pas différente », a-t-il poursuivi. "Les organisations empruntent des voies différentes pour accomplir la transformation numérique, et celles qui étaient plus avancées pouvaient naturellement passer facilement aux pratiques hybrides en général."
En fin de compte, juste parce que les outils sont disponibles pour créer une main-d'œuvre hybride, cela dépend vraiment de la culture d'une entreprise donnée et de sa volonté "d'investir dans un changement significatif pour que son entreprise non seulement survive, mais prospère". Honnêtement, le plus grand défi est le changement de culture. Dans le secteur manufacturier, les gens sont des créatures d'habitudes et il est difficile d'en sortir. L'autre grand défi est le coût financier du passage au numérique pour autonomiser une main-d'œuvre hybride », a noté Sciammarella. "Il est extrêmement difficile pour les petites entreprises d'évaluer ce qui pourrait apporter le meilleur retour sur investissement alors qu'il y en a tellement."
Système de contrôle d'automatisation
- Comment les entreprises aérospatiales peuvent-elles faire passer la fabrication additive au niveau supérieur avec le MES ?
- Avec l'IA, les magasins à grande surface peuvent rivaliser avec les e-Tail
- Routeur CNC à vendre :que pouvez-vous en faire ?
- Cinq façons d'automatiser le processus de fabrication peuvent vous faire économiser de l'argent
- Comment les robots logiciels peuvent vous aider à prendre le contrôle de la « nouvelle normalité »
- Que pouvez-vous faire avec une machine CNC ?
- Connectivité dans l'industrie :comment l'améliorer ?
- L'IA peut-elle créer des emplois dans le secteur manufacturier ?
- ABB déclare que la flexibilité est nécessaire avec le passage à l'électrification des véhicules