La fabrication médicale devient plus intelligente
La fabrication numérisée et automatisée fait des progrès dans le monde de la fabrication médicale, comme en témoignent les récents systèmes mis en place dans les chaînes de production pendant la pandémie de COVID-19.
Compte tenu des normes rigoureuses régissant la fabrication des dispositifs médicaux, l'environnement de l'industrie 4.0 centré sur les données est conçu sur mesure pour les fabricants sous contrat qui tentent de respecter les spécifications tout en faisant face au manque dramatique d'opérateurs qualifiés.
Comme toujours, les matériaux deviennent de plus en plus sophistiqués et les pièces deviennent plus petites, avec des géométries plus complexes et des exigences de tolérance plus strictes.
Au sens large, les tendances en matière de soins de santé (populations vieillissantes, tendance à recourir à davantage de diagnostics et de thérapies à distance en dehors de l'environnement hospitalier coûteux, thérapies plus personnalisées) stimulent le développement des dispositifs médicaux. Et avec les incertitudes persistantes liées à la pandémie et les chaînes d'approvisionnement qui en résultent, établir une plus grande visibilité sur le fonctionnement des fournisseurs et des vendeurs est la priorité n° 1.
La numérisation des soins de santé s'accompagne de la nécessité de sécuriser toutes les données collectées. À cette fin, des initiatives telles que le nouveau Center for Medical Device Cybersecurity de l'Université du Minnesota ont été annoncées le 9 septembre. Cinq poids lourds du secteur de la santé se sont associés pour travailler ensemble dans le nouveau centre :Boston Scientific, Smiths Medical, Optum, Medtronic et Abbot Laboratoires. Leur objectif est d'éliminer les vulnérabilités logicielles des dispositifs médicaux qui pourraient potentiellement être utilisées pour nuire aux patients ou perturber les établissements de santé.
L'avenir high-tech des soins de santé signifie également plus de diagnostics et de procédures robotiques, d'où le besoin de plus d'outils médicaux et de pièces dédiées à l'utilisation avec ces systèmes. Par exemple, XACT Robotics à Hingham, Massachusetts, le développeur du système robotique XACT ACE, a annoncé le 30 août avoir terminé avec succès le recrutement des patients dans la première étude américaine évaluant XACT ACE pour une utilisation dans les procédures pulmonaires percutanées. Cela comprend des biopsies pour confirmer la présence d'un cancer. Le système robotique mains libres pourrait détecter le cancer plus tôt et de manière moins invasive.
Pendant ce temps, iData Research prévoit que 3 millions d'interventions chirurgicales robotisées seront effectuées chaque année d'ici 2025. Les bras robotiques sur des équipements tels que le système chirurgical da Vinci nécessiteront de nombreux instruments miniaturisés que les médecins contrôlent pour effectuer ces opérations peu invasives. Les chirurgies robotiques utilisent des incisions plus petites, ce qui entraîne moins de pertes de sang et de cicatrices, des séjours à l'hôpital plus courts et des récupérations plus rapides.
L'IA alimentée par les données sera également mise en avant pour améliorer les résultats des patients. Un indicateur clair de cette voie est l'acquisition par Stryker de Gauss Surgical de Menlo Park, en Californie. Gauss a développé Triton, une plateforme basée sur l'intelligence artificielle pour surveiller la perte de sang pendant la chirurgie.
La fabrication additive continuera également à étendre son rôle essentiel dans la production d'implants, d'outillages et de modèles de formation chirurgicale spécifiques aux patients. Par exemple, l'Italien Tsunami Medical impressionne l'industrie avec son utilisation des systèmes d'impression 3D laser et à faisceau d'électrons GE Additive pour produire une gamme d'implants rachidiens très complexes.
Petites pièces, défis de tri
Alors que les matériaux des dispositifs médicaux évoluent et que les pièces deviennent plus petites, les machines de style suisse de la série L de Marubeni Citizen-Cincom (MCC), Allendale, N.J., répondent à l'appel.
"Le médical a des matériaux dont vous n'avez jamais entendu parler auparavant", a plaisanté le président et directeur de l'exploitation Brian Such. Des matériaux résistants peuvent être utilisés pour des pièces simples ou des composants plus complexes nécessitant l'utilisation de nombreux outils pour créer les différentes fonctionnalités.
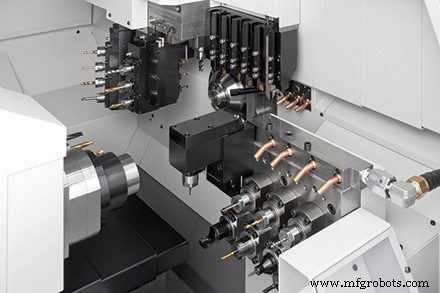
"Nos machines de la série L sont une machine à gang avec sous-broche", et leur avantage significatif pour la production médicale est qu'elles sont modulaires, a expliqué Such. "Avec un certain nombre d'outils disponibles à tout moment, nous pouvons simplement en retirer un et en mettre trois au même endroit."
Pour gérer les diamètres plus petits typiques des forets et fraises médicaux actuels, MCC propose des accélérateurs jusqu'à 4x l'accélération. « Nos outils motorisés atteignent des vitesses allant jusqu'à 6 000 ou 9 000 tr/min selon les modèles, mais nous pouvons glisser un porte-outil différent, et maintenant nous sommes à 36 000 tr/min. Lorsque cela ne suffit pas, nous pouvons moderniser nos électrobroches, qui peuvent atteindre 80 000 tr/min. »
À titre d'exemple, Tel a noté qu'un client pourrait percer un trou de huit millièmes, "vous avez donc besoin d'une certaine vitesse pour cela - ou utilisez une fraise en bout de 16 millièmes ou peut-être même une fraise en bout de huit millièmes pour incliner un coin quelque part . Avec nos électrobroches 80 000 tr/min, on peut se glisser dans ces poches. Et ce même outil peut être utilisé comme outil facial, outil croisé ou outil orienté vers l'arrière, il est donc très modulaire. MCC s'est associé au vendeur de broches à grande vitesse NSK pour créer ces broches exclusives.
Il y a environ deux ans, MCC a élargi la fonctionnalité de l'axe B de ses machines en introduisant la version ATC (changeur d'outils automatique) de sa machine L20. "Maintenant, nous avons la capacité de 13 outils sur l'axe B", a déclaré Such, alors qu'en général, un axe B n'a que quatre outils - et c'est "un truc assez chaud pour le marché médical" étant donné les angles serrés des pièces d'aujourd'hui.
Une autre innovation du MCC, introduite vers 2016, est la découpe par vibration à basse fréquence (LFV). Dans ce processus, la machine-outil « fait osciller la trajectoire de coupe de l'axe Z ou X, se déplaçant à une vitesse très élevée pour effectuer de petites coupes d'air et casser les copeaux pendant l'usinage », a déclaré Such. "Le domaine médical adore la technologie LFV, et la plupart des clients qui l'utilisent pour la première fois disent :"Je n'achèterai plus jamais une machine sans elle". il n'y a pas d'entre-deux. Une fois que vous avez lancé le processus, il est garanti. Vous devez toujours connaître vos outils de coupe, et les outils de coupe peuvent toujours tomber en panne, mais le problème de l'enveloppement des copeaux disparaît. »
Les clients de MCC vont des OEM avec 300 ou 400 machines aux plus petits fabricants avec 10 machines. Et ces clients « fabriquent toutes sortes de pièces », des vis à os courantes et des cages de chirurgie de la colonne vertébrale à divers outils chirurgicaux comme les alésoirs osseux nécessaires aux chirurgies de la hanche et du genou. Il existe de minuscules vis à os d'environ 4 mm de diamètre avec des trous pour les sutures. "Neuf outils différents entrent en jeu pour couper les différentes formes", a déclaré Such. "Il y a beaucoup de fonctionnalités dans cette petite vis à os - ce n'est pas seulement une vis avec une tête."
Une fois ces minuscules pièces fabriquées, le tri devient le principal problème, a poursuivi Such. MCC fabrique des équipements d'automatisation adaptés à la tâche.
"Ces pièces sont si petites que lorsqu'elles tombent dans le seau, il pourrait y en avoir 300. Si vous allez essayer de choisir le dernier pour essayer de le mesurer, lequel était-ce ? Nous pouvons avoir un appareil qui a différents plateaux pour compter », a déclaré Such.
Le client peut mettre 100 pièces dans un plateau, puis lorsque le plateau bouge, en mettre une dans le plateau suivant, 100 dans le plateau suivant, une dans le plateau suivant, et ainsi de suite. S'il y a 10 plateaux, il peut fonctionner pendant huit heures ou toute la nuit sans surveillance. En mesurant les pièces à intervalles réguliers, les clients peuvent déterminer si les pièces précédentes sont bonnes ou mauvaises grâce aux plateaux de collecte.
L'avantage des six axes
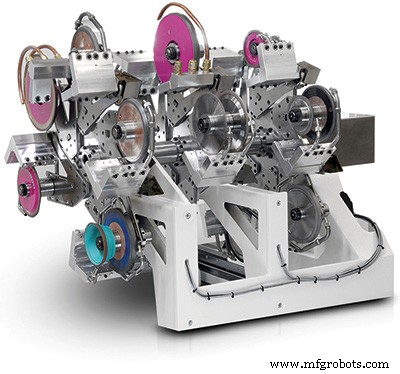
La demande constante pour les rectifieuses d'outils de coupe de Rollomatic USA Inc., Mundelein, Illinois, est un indicateur clair de la résilience de la fabrication de dispositifs médicaux, a affirmé le président Eric Schwarzenbach.
Parmi les nombreux instruments que les équipementiers et les sous-traitants font appel aux machines Rollomatic pour fabriquer, il y a divers outils de coupe orthopédiques comme les râpes, les forets à os, les perforateurs crâniens et les fraises arthroscopiques. Tout au long de la pandémie, « nos clients ont investi comme avant, ni plus, ni moins », malgré le report des chirurgies orthopédiques ou électives. "Il y avait suffisamment d'affaires pour que ces entreprises continuent de fonctionner et pour maintenir leur besoin de réinvestissement."
Au cours des deux dernières années, a-t-il noté, divers instruments pour les chirurgies robotiques sont de plus en plus demandés. Mais ces appareils posent un défi particulier.
"Une perceuse qu'un chirurgien utilise avec une pièce à main pour percer un os est différente de ce qu'un robot produit", a-t-il expliqué. « Les robots utilisent des forets plus longs que les chirurgiens. La nature de la fabrication d'un foret long est plus difficile qu'un foret plus court. Tout d'abord, des ébauches d'outils chirurgicaux sont usinées à l'état tendre sur un tour de type suisse et ensuite durcies. Ces processus provoquent intrinsèquement un gauchissement de ces flans, et plus ils sont longs, plus ils sont pliés. Et lorsqu'ils sont pliés, nous avons du mal à charger, rectifier et décharger de manière fiable. Lorsque nous enseignons aux clients notre machine et sa configuration, nous devons être très attentifs à leur enseigner en profondeur et nous assurer qu'ils comprennent les fonctionnalités permettant de contourner une ébauche pliée. Les ébauches pliées sont souvent redressées par le fabricant, mais même dans ce cas, elles ne sont jamais parfaites, même si elles ne doivent pas nécessairement être parfaites. La machine est capable de gérer une petite distorsion.”
Plus l'industrie devient robotique, « plus il faut se concentrer sur la pointe de forage. Alors qu'un chirurgien peut toujours forer dans l'os parce qu'il peut regarder, voir, ajuster sa main et sa pression pour que la pointe ne s'éloigne pas, le robot ne le fait pas. Donc, ces points doivent être conçus pour être plus centrés sur eux-mêmes. Nous aidons les fabricants de dispositifs médicaux à leur apprendre à quoi ressemble un point d'auto-centrage."
Schwarzenbach a également noté plus de variantes en acier inoxydable 17-4 pour les fraises orthopédiques. « Le matériau est devenu plus doux et moins durci, ce qui est un défi pour nous en termes de trouver les bonnes meules pour les rectifier. Comme vous le savez, plus le matériau est tendre, plus il est difficile à broyer. Pour répondre à ce besoin, Rollomatic s'est associé à des fabricants de roues en Suisse et aux États-Unis pour se procurer des roues adaptées aux matériaux plus tendres.
"Plus le matériau est mou, plus il émet de bavures", a expliqué Schwarzenbach, "l'élimination des bavures est donc un problème. Nos clients utilisent généralement des brosses en nylon pour éliminer les bavures après le meulage, en particulier avec des matériaux plus tendres. Mais aucune roue ou processus n'est jamais parfait; il y aura toujours une petite bavure lâche qui doit être éliminée par une méthode quelconque. Nous utilisons des brosses en nylon ou parfois imprégnées de céramique ou d'abrasifs pour éliminer ces bavures."
Les poignées à déconnexion rapide pour les outils médicaux sont un autre domaine de croissance, a-t-il poursuivi. Ces outils peuvent être encliquetés dans une pièce à main par un chirurgien ou fixés à un bras robotique. De telles poignées "sont devenues beaucoup plus complexes que nous ne l'avons jamais vu. Nous utilisons un broyeur de peau pour la plupart d'entre eux.”
La capacité à six axes de Rollomatic change la donne pour les fabricants médicaux qui ont besoin de plus de flexibilité pour la programmation et d'une configuration plus facile des roues, a déclaré Schwarzenbach.
« Vous n'avez pas besoin d'utiliser des roues complexes; vous pouvez utiliser des roues de forme plus simple, en particulier sur les points de forage », a-t-il déclaré. « Vous pouvez produire une pointe de perçage plus facilement que sur une machine à cinq axes. Et n'oubliez pas :les points de forage deviennent maintenant aussi bas que 50 à 60 degrés inclus. Ils sont très raides, contrairement à un foret au carbure dans le métal à 120 ou 130 degrés. Nos machines à six axes aident vraiment à rectifier ces points de forage beaucoup plus facilement que de se débattre avec la configuration d'une machine à cinq axes. »
Et, le changeur de roue rapide de Rollomatic offre encore plus d'avantages, a-t-il ajouté. « Nous vendons beaucoup plus de machines de changement de roues. Le changeur de roues de base a six stations, vous pouvez donc mettre six packs de roues pour augmenter la flexibilité, ce qui sert pour des lots plus courts. Les lots plus courts nécessitent plus de flexibilité avec les changements fréquents. Les changeurs de roues sont très bons pour cela. Alors qu'environ 80 % des machines que Rollomatic vend à l'industrie médicale conservent les broches standard qui abritent une paire de roues avant et arrière, certains fabricants "commencent à adopter notre nouvelle technologie".
Le rôle des tests de force
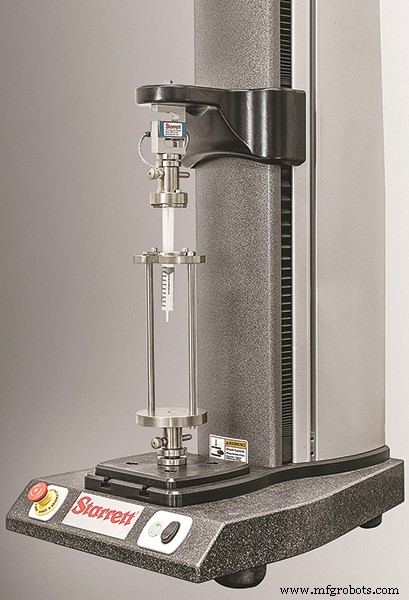
From the preparation for manufacturing to after the part is made, force testing equipment and its integrated software performs important functions for medical products–often with the goal of patient comfort.
For instance, the contours and coating of a needle can be tested for how easily they enter the skin, while adhesives can be evaluated for how well they adhere to skin, or how easily they are removed.
Prior to manufacturing, “you can build tests to make sure your equipment functions the way it should before you use it in manufacturing,” explained Jacob Morales, technical support engineer for The L.S. Starrett Co., Athol, Mass. And for bandages, “you can test the adhesive before you use it in your manufacturing line,” in batches ranging, for example, from one in 100 to one in 10,000 samples. “Post-process, you can run those tests again to ensure consistency.”
Such tests are particularly important when manufacturing in line with ASTM and ISO standards as well as for producing documentation critical for traceability, added Eric Perkins, Starrett technology manager for force and material testing. Starrett software enables both force and material properties tests, and simply by clicking the right icon, the software can engage the appropriate test. Force measurement covers go/no-go scenarios include testing for peak load, average load, compression testing and more. Syringes, a prime example requiring uniaxial force application, can be tested with sample substances to determine injection force for controlled injection rates.
While these tests provide sample information, they don’t always return data specific to the material composing the sample. Material testing goes further, using material properties to test for elongation and stress-strain, for example.
Starrett software can be integrated into the manufacturing process, Morales explained.
“If you have a force system testing a sample, you can have it programmed with an input-output system so the test is running constantly. The manufacturing equipment moves a sample to the machine and sends a signal; the machine responds by running the test and provides a signal output based on the test results. The rest of your manufacturing equipment can respond appropriately. If you get a result that falls out of tolerance, the signal can alert an operator.”
That flexibility means “you can hook the force system up to a PLC and put it in-line with the production environment, so you’ve taken potential human data entry error out of the picture,” Perkins said. “Users can automatically have a product tested every time it’s queued.”
From Starrett’s basic L1 force software to its more advanced L2, L2Plus and L3 options, “we give customers the ability to test exactly as any manufacturing standard states,” Perkins said. And since Starrett software is compatible across platforms, adding optical and vision systems creates an extremely broad metrology solution.
That level of customization doesn’t stop at software, however. Starrett has been working with manufacturers to create completely automated systems.
“We’re using robots to insert parts into our force test system,” Perkins said. “We’re using pneumatic grippers to grab the parts.” With a constantly running test platform married to this level of automation, “our system will tell if you have a good or bad part, then the robot executes whatever program is required and puts those parts in the designated bin.”
GE’s Big-Picture View
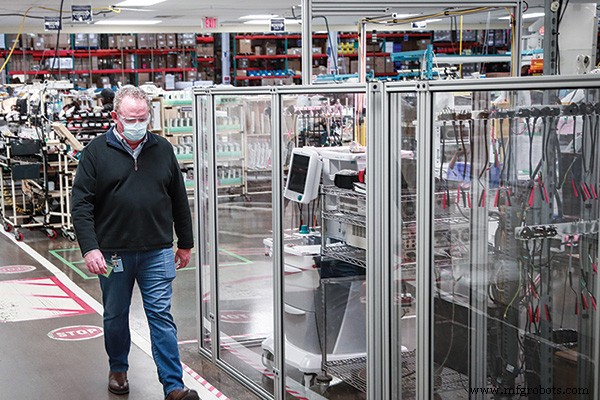
Improving hospital workflows and maintaining supply-chain resiliency have been top of mind for GE Healthcare during the pandemic.
“We’re seeing increased requests for more automation–not just from a typical productivity standpoint but in terms of leveraging automation so we can maintain production at different locations,” said Jimmie Beacham, executive chief engineer for advanced manufacturing at GE Healthcare in Milwaukee. “That’s easier than having to train a new or revolving workforce. It’s not necessarily about the labor but the supply chain security of it where automation makes sense. If I have to switch production from one region to another, it’s a lot easier if the process is automated already.”
A major part of that philosophy is mistake-proofing, he added. “We would train operators and have written procedures,” Beacham explained. “Now we’re looking at employing other technologies that digitize what the operators need to do and that interacts with them. Say you have torque station, where you’re torqueing bolts, followed by a complex assembly and then a cobot. We’re looking at technologies that digitally connect all that–that work in lockstep with the operator so it interacts with that person and doesn’t require the operator to remember it all. That gives us a lot of flexibility when we’re making the same product in three regions around the world. We now have one control process. We’re not relying on operators memorizing paper procedures when they have to cycle through several complex parts of the operation.”
That’s vital for GE Healthcare, which produces an array of smart diagnostic equipment. Additive manufacturing is a big part of the equation, and GE Healthcare has refined its processes in that regard, as well.
“When we first started, probably 80 percent to 90 percent of our time was invested in R&D, trying to figure out how additive works, how you develop materials and parameters to meet our engineering requirements,” he said. “Now we’re at about 80 percent execution, where we’re moving things in to production, and the other 20 percent of our time is devoted to developing new materials for the new funnels coming in. We have a production facility in Monterrey, Mexico, and we have a pretty active funnel of things going there. Then we have some other additive applications we run at the point of use.”
Ultimately, while the pandemic has proved challenging, GE Healthcare has weathered the storm.
“Our big challenge was supply, getting people safely in the plant,” Beacham said. “In some cases, like with ventilators, we relied a lot on automation to enable us to meet unprecedented demand. We brought a lot of people in to do the work, but we still had to find creative ways to manufacture the volume of products our customers desperately needed. And we learned we can manufacture things differently; that has inspired even more ideas.”
Système de contrôle d'automatisation
- Évaluer l'impact de l'industrie 4.0 sur la fabrication
- 8 mythes importants sur la fabrication de métaux démystifiés
- Des technologies pour une fabrication plus efficace de composants médicaux présentées à MD&M West 2018
- 6 façons dont l'IIoT rend la fabrication plus efficace
- Stratasys :être plus durable avec l'impression 3D
- RAPPORT :2016 sera un « point de basculement » pour la technologie de fabrication
- Rendre la fabrication britannique plus intelligente :attentes pour 2018
- Combler le déficit de compétences dans la fabrication automobile
- Stora Enso :l'avenir de la fabrication devient plus intelligent