Les stratégies de meulage passent de bonnes à excellentes
Comment les logiciels, l'automatisation et les avancées en matière d'abrasif font passer la rectification des pièces et des outils en surmultipliée.
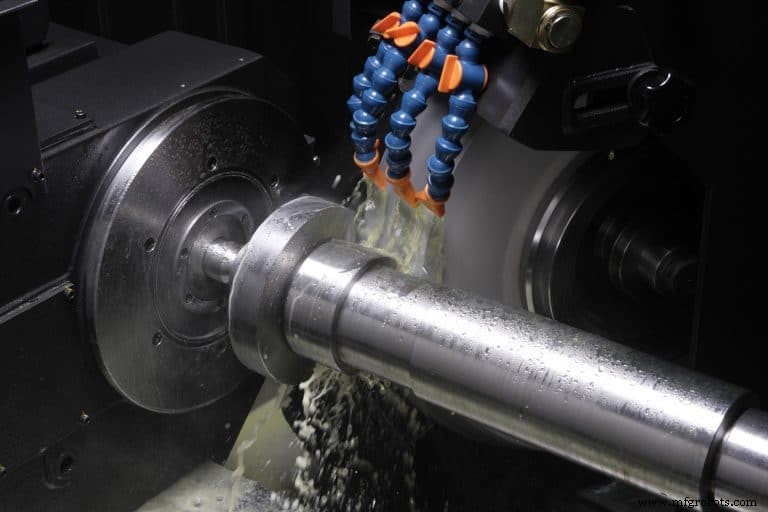
Peut-être que votre entreprise est spécialisée dans les composants aérospatiaux ou médicaux et que vous devez produire des géométries complexes dans des métaux trop difficiles à couper via des méthodes d'usinage conventionnelles. Ou peut-être travaillez-vous ou possédez-vous un atelier d'outillage et de fraisage et recherchez des moyens plus rapides et plus rentables de produire des forets, des fraises en bout et des outils de forme. Quelle que soit la raison et quelle que soit l'exigence, vous avez de la chance. Comme pour la plupart des technologies de travail des métaux, le meulage, plus précisément appelé usinage abrasif, s'est considérablement amélioré ces dernières années.
Comment? Pour commencer, les fabricants de meules ont développé de nouveaux liants et superabrasifs
qui méritent clairement le titre de "super", capables d'enlever plus de matière en moins de temps que jamais auparavant. Et les fabricants de rectifieuses proposent des équipements toujours plus performants, suffisamment rigides et puissants pour tirer pleinement parti de ces abrasifs avancés, tout en ajoutant des fonctionnalités intelligentes telles que l'automatisation, la surveillance à distance et des systèmes logiciels intelligents à leurs machines-outils.
En termes simples, le meulage est entré dans une nouvelle ère de productivité et de précision des pièces; si vous n'en profitez pas, vous risquez de passer à côté d'importantes opportunités d'amélioration des processus, d'amélioration de la qualité des produits et d'augmentation des résultats.
Un meilleur contrôle est essentiel
L'un des principaux moteurs de cette situation est la pénurie de machinistes qualifiés. C'est selon Shane Farrant, chef de produit national pour les meuleuses chez JTEKT Toyoda Americas Corp., Arlington Heights, Illinois, qui a ajouté que rendre l'interface homme-machine (IHM) plus facile à comprendre est une première étape nécessaire pour minimiser les effets d'un main-d'œuvre moins qualifiée.
"Une IHM plus simple et plus intuitive est l'une des nombreuses améliorations que nous avons développées pour notre gamme de rectifieuses universelles, cylindriques, d'arbres à cames et de vilebrequins", a-t-il déclaré. "Cela signifie un format convivial, avec une plus grande dépendance aux images et autres graphiques pour faciliter les procédures de configuration et de programmation."
Il y a également eu une grande poussée vers un environnement de travail basé sur l'Internet des objets (IoT). Par exemple, la page de diagnostic de la commande tactile TOYOPUC de Toyoda affiche les niveaux de liquide de refroidissement, les vibrations de la machine, la température de l'huile. Tout ce qui pourrait se traduire par une mauvaise qualité des pièces ou créer un problème de production enverra une alerte immédiate à la personne responsable de la résolution. De plus, il est possible de collecter ces informations à partir du contrôle de la machine et de les transmettre à une base de données en réseau pour une analyse historique.
Une autre fonction permettant de gagner du temps est la génération automatique de programmes alternatifs, qu'un opérateur peut appeler en cas de problème lié au processus. Steve Earley, responsable de l'ingénierie des propositions de JTEKT Toyoda, a déclaré que cette option de contrôle conversationnel est disponible sur la meuleuse à rouleaux GE6 de la société, une machine qui a également bénéficié de certaines modifications de la coulée, des moteurs et d'autres composants, tous conçus pour réduire les vibrations et augmenter la précision de la machine dans cette application spécialisée.
Les matériaux utilisés pour fabriquer les batteries au lithium utilisées dans les véhicules électriques sont assez fins, a-t-il expliqué, et les rouleaux produisant ce matériau doivent donc être extrêmement précis, avec des finitions de surface très fines. "Lorsqu'un opérateur configure la machine, la commande présente un programme généralisé pour commencer, ainsi que deux alternatives - une plus agressive pour des temps de cycle plus rapides et un programme plus conservateur qui produit de meilleures finitions de surface", a déclaré Earley. . "Sur la base des premiers résultats, l'opérateur peut facilement décider de passer à l'ensemble de paramètres d'usinage qui fournit la meilleure pièce dans les plus brefs délais."
Moins d'opérations requises
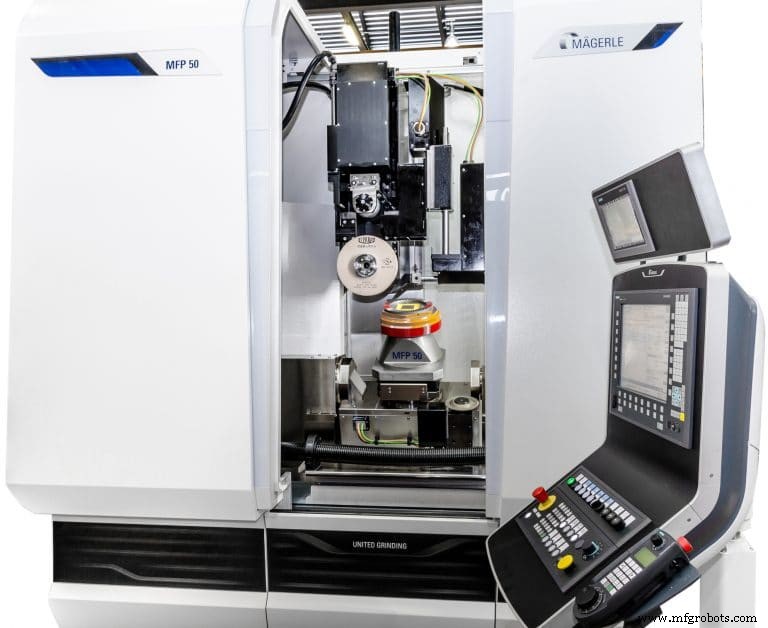
Larry Marchand, vice-président du groupe de profils chez United Grinding North America Inc., Miamisburg, Ohio, a convenu de la nécessité de commandes faciles à utiliser, d'autant plus que les rectifieuses deviennent plus performantes. Mais il a dit qu'il y avait aussi un énorme appel dans toute la communauté de fabrication pour une réduction des travaux en cours et moins d'opérations d'usinage, ce qui a conduit United Grinding et d'autres entreprises à adopter l'approche dite «faite en un» pour réduire le temps de contact de l'opérateur et augmenter la valeur par opération.
Pour soutenir cela, United Grinding a introduit des "processus, opérations et fonctionnalités supplémentaires" pour profiler les rectifieuses qui étaient autrefois à usage unique. "Les clients veulent ajouter plus de valeur dans la manutention d'une seule pièce", a déclaré Marchand. « Nous avons constaté une forte demande de machines équipées de changeurs d'outils automatiques, permettant de rectifier la pièce à usiner, puis d'apporter une perceuse ou une fraise pour terminer la pièce. Cela élimine les opérations secondaires, réduit les délais de livraison des pièces et améliore la qualité. »
Cela signifie-t-il que les ateliers d'usinage devraient échanger leurs machines-outils CNC contre une super meuleuse à tout faire ? Pas du tout. Tout comme les machines multitâches font un excellent travail de fraisage d'une fente ou de meulage d'un tourillon, une rectifieuse multitâche peut désormais effectuer des tâches autrefois réservées aux centres d'usinage et aux machines à tarauder. Cela dit, aucun type de machine-outil ne peut remplacer l'autre. Comme l'a souligné Marchand :"Si vous avez une pièce qui nécessite beaucoup de meulage, il est toujours préférable d'avoir une rectifieuse dédiée."
Il y a plusieurs raisons à cela, a-t-il dit. Le meulage nécessite beaucoup plus de liquide de coupe que les opérations de fraisage et de tournage, visant précisément l'intersection de la pièce à usiner et de la meule. Conduire une roue qui mesure quelques pieds de diamètre nécessite beaucoup de puissance, bien plus que ce qui est disponible sur une machine de fabrication de puces moyenne. Enfin, tenir des dixièmes et des finitions de surface à un chiffre toute la journée est quelque chose dans lequel la plupart des rectifieuses CNC excellent car elles sont conçues pour optimiser ces opérations. Centres d'usinage ? Pas tellement.
S'attaquer aux choses difficiles
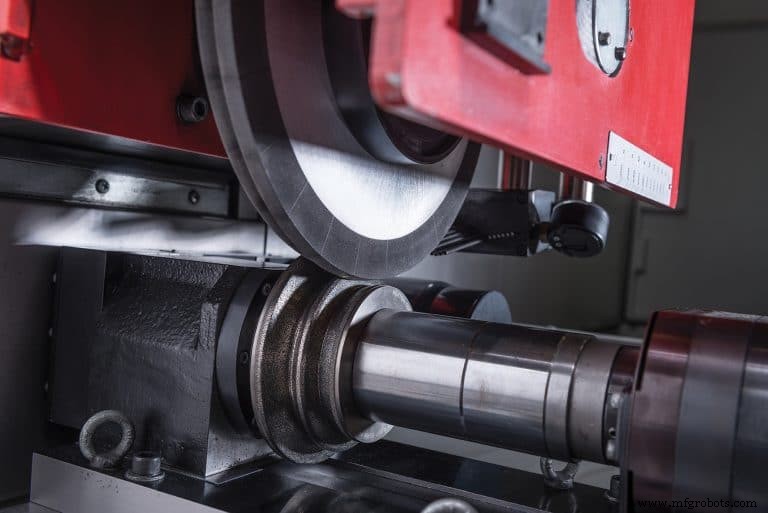
Ces capacités sont particulièrement pertinentes avec les métaux riches en nickel, chrome et cobalt, a déclaré Marchand. « Une grande partie de notre activité provient de clients produisant des pièces en Inconel et Rene, des matériaux qui, du moins dans leur état durci, sont pratiquement inusinables. Leur seule option est l'EDM ou le meulage, et grâce à la rigidité, la puissance et la précision des rectifieuses modernes, ainsi que la disponibilité de superabrasifs qui n'étaient pas disponibles jusqu'à récemment, la plupart optent pour ce dernier."
L'un des principaux fabricants de superabrasifs est Norton | Saint-Gobain Abrasives, Worcester, Mass. Alfredo Barragan, ingénieur principal d'application d'entreprise pour les super-abrasifs en Amérique du Nord, a déclaré que le meulage était autrefois considéré comme un processus de "finition uniquement", mais, avec le développement de la technologie de meulage de plus en plus performante, est devenue un processus d'usinage courant. Afin d'obtenir le plus grand succès avec ce processus, cependant, des abrasifs tout aussi modernes doivent être appliqués.
"Les meules traditionnelles à matrice diamantée à liant métallique ou en résine ont tendance à être très denses", a déclaré Barragan. "Être dense est une bonne chose car cela vous donne une structure robuste et aide à fournir une liaison solide qui maintient cette structure ensemble, mais cela soulève une considération :la roue a tendance à se charger plus rapidement, ce qui, à long terme, réduit la productivité. Les roues à liaison hybride Norton Winter Paradigm résolvent ce problème.”
On dit que les meules offrent une combinaison de rétention améliorée du grain avec des niveaux élevés de porosité, réduisant ainsi les forces de coupe. Une porosité plus élevée réduit également la charge - la meule broie plus froide, plus librement, avec moins de temps d'arrêt, produisant finalement plus de pièces par jour. En fonction de l'abrasif utilisé, les meules à liant hybride meulent efficacement le carbure, les céramiques avancées, les aciers à outils trempés et les alliages haute température que Marchand de United Grinding vient de mentionner.
Il y a cependant plus que la technologie des abrasifs. Comme les machines-outils auxquelles elles sont attachées, les roues elles-mêmes deviennent plus intelligentes, avec des étiquettes RFID intégrées pour une meilleure gestion des actifs, un approvisionnement rationalisé, un suivi des informations d'utilisation et d'habillage et une protection contre les erreurs de l'opérateur.
Norton|Saint-Gobain ne limite pas non plus ses efforts aux produits abrasifs. Son système de surveillance et de diagnostic de processus 4Sight fournit une fonctionnalité IoT similaire à celle décrite précédemment, avec une surveillance en temps réel indépendante de la marque des valeurs de la rectifieuse telles que la charge de la broche et l'utilisation de la machine, et la possibilité de stocker des données pour l'analyse des tendances ou d'envoyer des alertes si nécessaire. . "C'est l'une des plus grandes initiatives de l'année pour nous et, avec nos systèmes d'étiquettes intelligentes, elle constitue la base de notre solution Industrie 4.0", a déclaré Barragan.
Venir sur votre écran :V@dison
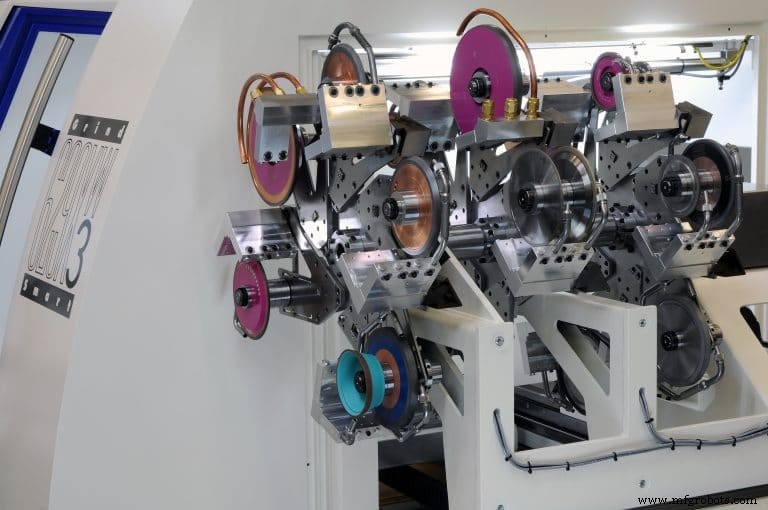
Ils ne sont pas seuls. Vollmer of America Corp., Carnegie, Pennsylvanie, en collaboration avec sa société mère, le groupe Vollmer, travaille sur un certain nombre d'outils et de services conçus pour "transformer numériquement" les opérations de meulage. Sous la marque V@dison, ceux-ci incluent l'écran V@ pour une meilleure visibilité des paramètres de la machine, V@ check pour la simulation de processus, V@ boost pour optimiser les performances de la machine en fonction de la pièce et le guide V@ pour une maintenance préventive plus cohérente.
Vollmer en est encore aux premiers stades de cette initiative, mais la directrice des ventes nord-américaine Shannon Fox a déclaré qu'il y avait encore beaucoup de fruits d'amélioration à portée de main disponibles pour la communauté de broyage. Le principal d'entre eux est l'automatisation - Fox a cité les capacités robotiques de chargement de pièces et de changement de roue de son outil VGRIND 360 et de sa rectifieuse de fraises à titre d'exemple, des options que Vollmer et en fait la plupart des fabricants de machines-outils installent régulièrement lorsque leurs clients travaillent vers des lumières- hors fabrication.
La simulation est une autre demande de routine. Bien que le système de contrôle V@ de Vollmer soit encore en cours de développement, Fox a noté que le logiciel NUMROTOplus proposé sur Vollmer et d'autres marques d'équipements de meulage est une alternative mature et bien acceptée. "La simulation devient de plus en plus importante à mesure que les broyeurs deviennent plus capables", a-t-il déclaré. « Les quartiers sont plus serrés, les géométries d'outils sont de plus en plus complexes et de nombreuses machines, y compris la nôtre, permettent l'utilisation de plusieurs packs de roues en un seul travail, ce qui soulève des problèmes d'interférence. Sans simulation, vous courez le risque de planter une machine-outil très coûteuse. »
Voir c'est croire
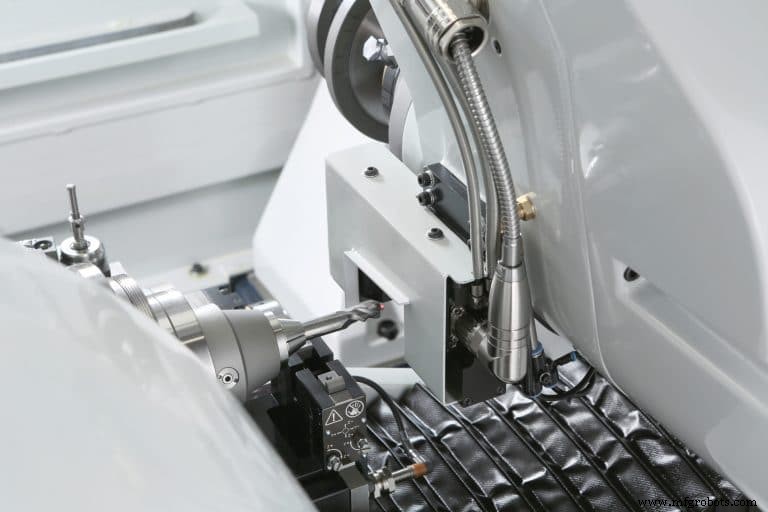
La simulation est également importante pour d'autres raisons. ANCA CNC Machines, basée à Melbourne, en Australie, par exemple, l'utilise pour prédire le déséquilibre de l'outil dans les fraises en bout à pas variable. "C'est l'un des compromis avec les fraises hautes performances - parce que l'espacement des cannelures est irrégulier, elles sont intrinsèquement déséquilibrées", a déclaré Lucas Hale, directeur du marketing mondial. « Pour lutter contre cela, nous avons développé un logiciel de simulation qui calcule le déséquilibre et ajuste le programme NC pour le compenser en supprimant des matériaux supplémentaires à des endroits stratégiques. L'outil sort de la meuleuse parfaitement équilibré, offrant une durée de vie prolongée et une meilleure finition de surface sur la pièce usinée. »
Hale a accepté l'appel à l'automatisation, y compris la manipulation robotisée des pièces et des roues, mais a proposé un certain nombre de moyens supplémentaires pour augmenter la productivité. Là où le "collage" de routine de la roue pour supprimer la charge était autrefois effectué manuellement, ANCA l'a automatisé, réduisant les coûts de main-d'œuvre et prolongeant la durée de vie de la roue. On dit que les logiciels et les machines d'ANCA offrent "une grande facilité d'utilisation", réduisant ainsi le temps de configuration. Et les systèmes de mesure au laser fournissent une vérification en cours de processus de la précision et de la géométrie des outils de coupe, suivie de décalages automatisés ou de dressage des meules pour compenser l'usure.
Et l'ANCA a poussé ce processus un peu plus loin. Grâce à une collaboration avec des sociétés telles que Zoller Inc., l'un des principaux fournisseurs d'équipements de préréglage d'outils, ANCA a développé une interface qui prend en charge l'inspection automatisée et la rétroaction vers la rectifieuse CNC :un robot place la fraise dans le prérégleur, qui la mesure et envoie les résultats. à un système logiciel qui ajuste la machine selon les besoins. Cela "boucle la boucle", a expliqué Hale, et avec les systèmes intégrés de gestion des ébauches, permet aux clients de "charger des centaines d'outils, d'appuyer sur go et de revenir le lendemain aux outils de coupe terminés", a-t-il déclaré.
"La construction de base des machines s'est également améliorée au cours des cinq dernières années environ", a poursuivi Hale. « Par exemple, les moteurs linéaires sont devenus beaucoup plus courants dans notre industrie. Ils contribuent non seulement à la qualité des outils de coupe et donc à la qualité des pièces fabriquées avec eux, mais les machines linéaires se déplacent beaucoup plus rapidement que celles à vis à billes, ce qui réduit les temps de cycle. Et parce qu'il y a moins d'usure sur les composants de la machine, la durée de vie de l'équipement est prolongée. C'est pourquoi les moteurs linéaires sont pratiquement devenus un composant standard de toute rectifieuse haute précision et haute performance. »
Première partie, bonne partie
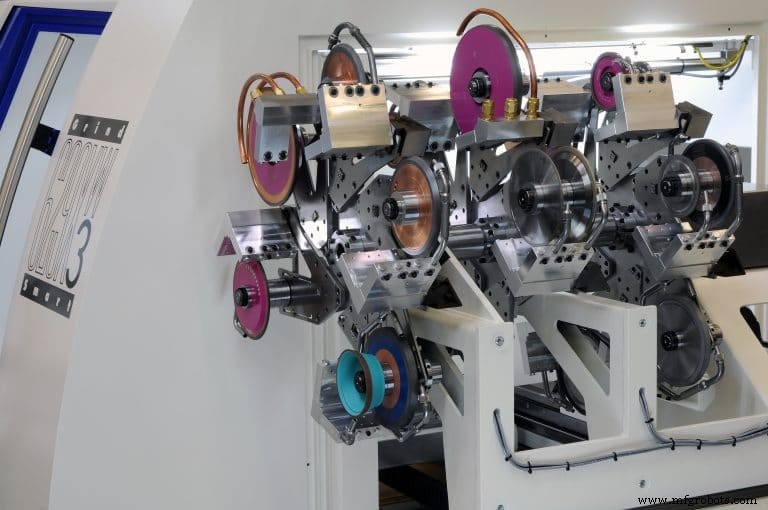
Tout comme JTEKT Toyoda s'attaque à la pénurie de machinistes qualifiés avec un logiciel de contrôle plus intuitif, Rollomatic Inc., Mundelein, Illinois, s'efforce de rendre les configurations de machines à la fois plus faciles et plus rapides. C'est parce que la plupart des fabricants d'outils et de fraises ne sont pas différents de n'importe quel atelier de coupe de métal ; ils sont confrontés à des tailles de lots plus petites et à des délais d'exécution plus courts, ce qui fait du temps de configuration un pourcentage plus important de tout cycle de production. Une partie de la solution ? Meilleur logiciel.
"Pendant des décennies, les ateliers ont brûlé trois, quatre, cinq ébauches de pièces par configuration, composant progressivement la machine jusqu'à ce qu'ils obtiennent une bonne pièce", a déclaré Eric Schwarzenbach, président de Rollomatic Inc. "Mais en utilisant un logiciel intelligent, il est très possible pour réduire le nombre de pièces de rebut, zéro étant l'objectif ultime. Non seulement cela réduit les coûts de matériel, mais aussi le temps d'installation."
Le logiciel assiste l'opérateur en créant une représentation 3D de la machine-outil, de la pièce à usiner et de la meule, a déclaré Schwarzenbach, éliminant ainsi le besoin d'un essai à vide. L'opérateur peut accélérer l'animation, la ralentir, reculer ou zoomer sur les zones problématiques, ce qui l'aide à éviter les collisions potentielles entre le pack de roues et la pièce à usiner. Et lorsque l'animation est terminée et que la machine est en train de fabriquer des pièces, le logiciel fonctionne pour éliminer les "mouvements vides" et réduit les distances de sécurité au minimum.
Les logiciels intelligents sont formidables, mais Schwarzenbach n'a pas tardé à souligner que la machine-outil et ses systèmes associés sont tout aussi importants. Plus la machine-outil est précise et stable, plus il est facile d'atteindre la cote cible du premier coup. En outre, une technologie de dressage de meule améliorée, des procédures d'étalonnage automatisées, des contrôles plus rapides qui traitent les calculs plus rapidement et des liaisons de meule hybrides qui résistent à l'usure, coupent librement et conservent plus longtemps les angles vifs sont essentiels. Ces facteurs jouent un grand rôle dans des configurations plus rapides et une meilleure capacité à faire de la première partie une bonne partie, avec des temps de cycle plus courts pour démarrer.
Comme d'autres l'ont mentionné, le changement de meule automatisé est un autre changeur de jeu de meulage - Schwarzenbach a déclaré que les changeurs à grande vitesse de Rollomatic peuvent échanger un pack de meules en cinq secondes, arbre à arbre, et atteindre des temps de meulage à meulage de 11 secondes. L'avantage va cependant au-delà des temps de cycle plus courts. "Si vous avez un sac à quatre roues dessus, le potentiel de collision est plus élevé qu'un avec une ou deux roues. Cela complique la configuration. Donc, si vous pouvez diviser un gros paquet de roues et vous permettre de changer les roues en 11 à 12 secondes, c'est la meilleure façon de procéder de nos jours. »
Système de contrôle d'automatisation
- Quelle est la qualité de GCP comme choix de carrière ?
- Bon à excellent :regardez dans le miroir
- Stratégies pour des composants de transmission d'énergie plus fiables
- Pourquoi les bons de travail méritent plus d'amour de nous tous
- Pourquoi et quand passer des voyants lumineux à un écran IHM
- Comment tirer le meilleur parti de votre investissement dans un tombereau articulé
- Avantages de l'utilisation d'une meule ou d'un disque à lamelles de 5 ou 6 pouces
- EU Automation :les meilleures tendances technologiques de 2020
- 7 stratégies des grands responsables de la sécurité