Entretien d'experts :PDG de PostProcess Technologies sur la résolution du goulot d'étranglement du post-traitement pour la fabrication additive
Avant et après : pièces imprimées en 3D après post-traitement à l'aide des solutions d'automatisation de PostProcess Technologies. Crédit image :PostProcess Technologies
Le post-traitement est une étape vitale du processus de fabrication additive – et pourtant peut-être la plus longue. Selon une statistique, les méthodes de post-traitement actuelles représentent entre 30 et 60 % du processus de fabrication additive.
L'une des principales raisons de ce goulot d'étranglement est que le post-traitement est encore principalement un processus manuel. Une entreprise qui vise à transformer cela est PostProcess Technologies. Avec son siège principal à Buffalo, New York, PostProcess Technologies propose des solutions automatisées pour le post-traitement, y compris l'enlèvement des supports et la finition de surface.
Dans l'interview d'experts de cette semaine, AMFG s'entretient avec le PDG de PostProcess Technologies, Jeff Mize, pour en savoir plus sur la façon dont l'entreprise ouvre la voie au post-traitement automatisé pour la fabrication additive et pourquoi le post-traitement automatisé est nécessaire pour que la technologie évolue.
Pourriez-vous me parler un peu de PostProcess Technologies et des problèmes que vous essayez de résoudre ?
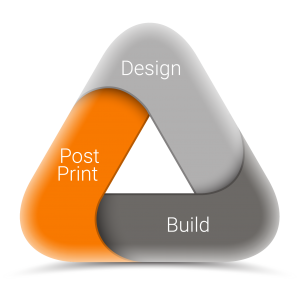
Nous résolvons deux défis majeurs, le premier étant l'automatisation de la suppression du support. Aujourd'hui, il y a encore une part importante de travail manuel lorsqu'il s'agit de retirer les supports des pièces additives. La fabrication additive ressemble beaucoup à la nature :comme vous construisez une pièce dans l'axe Z, couche par couche, la force de gravité signifie que vous aurez besoin de supports. Étant donné que la grande majorité des pièces produites de manière additive ont un certain type de supports, le premier domaine sur lequel nous nous concentrons est l'automatisation du processus de retrait des supports.
Une meilleure finition de surface pour les pièces imprimées en 3D est notre deuxième objectif. Il y a dix ou même cinq ans, la majeure partie de l'activité au sein de la FA concernait une fonction d'ajustement dans l'ingénierie - bien sûr, il y avait quelques exceptions, mais de manière générale, ces parties n'ont vraiment pas vu le jour. Mais au cours des deux dernières années, l'industrie a vu de plus en plus de pièces additives utilisées pour la fonction forme/ajustement, ce qui a conduit à une augmentation spectaculaire du besoin d'une meilleure finition de surface. Nous nous assurons que la pièce peut être « prête pour le client » — ce client peut être un client interne ou un client de nos clients.
Nous abordons ces deux fonctions à travers l'intégration du logiciel, du matériel et de la chimie. Tous nos investissements, notre expertise et nos innovations sont concentrés sur le segment industriel du marché de la FA — et le logiciel est à la sauce secrète. Cela contrôle la quantité d'énergie que nos solutions utilisent pour finir ces pièces additives délicates, nous sommes donc en mesure de retirer automatiquement les supports et d'offrir aux clients une finition de surface considérablement améliorée.
Quels avantages vos solutions offrent-elles ?
Nous offrons trois avantages clés à nos clients. L'un est la cohérence - il y a souvent plus d'art que de science lorsqu'il s'agit de post-impression pour additif aujourd'hui. Nos machines fonctionnent 24 heures sur 24 et offrent une cohérence que vous n'obtenez pas avec des méthodes manuelles.
Le deuxième avantage est le débit . À mesure que chacun de nos clients fait évoluer ses opérations de FA, il constate de plus en plus un goulot d'étranglement dans ce que nous appelons la troisième étape du processus additif :la post-impression. Avec nos solutions, ils sont capables d'automatiser ce processus et de supprimer ce goulot d'étranglement.
Le troisième est le retour sur investissement . Nous sommes en mesure de réduire considérablement le temps passé par les techniciens à assister – dans de nombreux cas, nous sommes en mesure de le réduire d'au moins 90 %. En conséquence, nos clients obtiennent un retour sur investissement très rapide, généralement dans un délai de 10 à 30 semaines.
Nous constatons que les volumes de prototypage augmentent rapidement. Les entreprises qui produisaient un millier de prototypes dans leurs laboratoires il y a un an ou deux produisent maintenant 10 000 à 30 000 prototypes dans le même laboratoire. Même s'ils sont toujours considérés comme des prototypes, nous entendons des clients qui souhaitent trouver un moyen d'obtenir des pièces plus cohérentes. L'utilisation de méthodes manuelles prend trop de temps et il est difficile de trouver le bon technicien. Notre solution est donc absolument critique pour que ces volumes de prototypes continuent d'augmenter et c'est absolument essentiel pour entrer dans les volumes de production.
Pouvez-vous expliquer un peu plus sur la façon dont vous intégrez les logiciels, le matériel et la chimie ?
Notre concentration sur l'intégration des logiciels, du matériel et de la chimie offre vraiment une valeur unique pour l'étape de post-impression. En plus de déterminer le logiciel et de développer le matériel, nous passons également beaucoup de temps à optimiser la chimie pour les technologies les plus volumineuses comme PolyJet, FDM, SLA, puis DMLS côté métal, ainsi que MJF de HP, CLIP de Carbon – et nous avons plus de 500 000 références.
Nous avons nos codeurs assis à côté de nos chimistes et ingénieurs de développement, et les trois groupes d'ingénieurs travaillent constamment ensemble afin que nous puissions continuellement optimiser les résultats finaux pour le client. C'est une approche unique et nouvelle que personne d'autre ne fait aujourd'hui. Cela nous donne une position de leader significative sur le marché de la post-impression automatisée pour les additifs.
Donc, cette intégration à trois voies est un différenciateur clé entre vous et des solutions similaires sur le marché aujourd'hui ?
Oui. Et l'élément logiciel est essentiel. Dans cet élément logiciel, il y a un composant d'analyse de données. Nous optimisons ce logiciel pour optimiser davantage le processus. Qu'il s'agisse de l'algorithme d'agitation utilisé pour le retrait du support ou de la fréquence et de l'amplitude que nous utilisons dans nos solutions de finition de surface, le composant logiciel ou l'analyse de données est un autre domaine d'investissement important pour nous à mesure que nous progressons.
Pensez-y comme ceci :le logiciel est le cerveau de ce que nous faisons ici. Et puis, l'intégration des logiciels, du matériel et de la chimie nous permet d'offrir systématiquement les trois avantages aux clients finaux :des pièces cohérentes, un débit illimité ainsi qu'un retour sur investissement rapide.
Ciblez-vous des secteurs verticaux spécifiques ?
Les trois plus grands marchés que nous voyons émerger sont l'aérospatiale, le médical et l'automobile. Actuellement, notre clientèle couvre pratiquement tous les secteurs, mais avec le temps, nous pensons que la majorité de nos revenus proviendra des secteurs de l'aérospatiale, de la médecine, de la dentisterie et de l'automobile.
Quels sont selon vous les principaux défis auxquels la fabrication additive est encore confrontée ?
La vitesse et la réduction des coûts globaux sont des défis importants auxquels nous sommes encore confrontés aujourd'hui. La vitesse à laquelle vous pouvez imprimer des pièces est essentielle, c'est pourquoi nous voyons des entreprises comme HP et Stratasys faire beaucoup de travail dans ce domaine, afin que vous puissiez réellement imprimer plus rapidement. Le coût est un autre problème, mais je pense que nous continuerons à voir le coût des solutions baisser, non seulement du côté des polymères, mais également du côté des métaux.
Quant à savoir où PostProcess entre en jeu :nous pensons que nos solutions automatisées élimineront l'un des plus gros problèmes du moment, qui permet un débit accru avec une sortie cohérente de la fonction de post-impression.
Comment voyez-vous évoluer la fabrication additive au cours des cinq prochaines années ?
Je pense que la FA représentera 3 à 4% de la fabrication traditionnelle, soit un marché de 3 à 4 cent milliards de dollars au cours des cinq prochaines années. L'un des plus grands marchés sera le médical, où la personnalisation de masse est si importante.
Je vois donc les additifs devenir la technologie de fabrication dominante dans le domaine médical dans les années à venir. Il est prévu que ce soit le deuxième plus grand marché après l'aérospatiale.
La capacité de créer des géométries uniques avec des matériaux qui pèsent beaucoup moins pour les applications dans l'aérospatiale et l'automobile va rapidement augmenter. Nous sommes actuellement au point d'inflexion où nous verrons des taux de croissance moyens de plus de 40 % dans certains secteurs verticaux.
Il y a aussi de plus en plus de clients qui se lancent dans la production. Récemment, nous discutions avec une entreprise de cosmétiques qui prévoit de produire 50 millions de pièces additives par an au cours des deux à trois prochaines années.
Nous voyons des entreprises automobiles planifier de produire des milliers de pièces additives pour continuer la production. Véhicules. Ainsi, à un niveau supérieur, nous verrons davantage d'entreprises poursuivre des volumes de production plus élevés. L'automatisation de la troisième étape de ce processus sera essentielle pour cette cohérence, ce débit et cette traçabilité.
PostProcess a récemment annoncé son expansion en Europe. Pourquoi avez-vous pris cette décision et avez-vous d'autres projets d'expansion à l'avenir ?
La demande d'additifs est mondiale et ne cesse de croître. Plus de 2000 entreprises dans le monde ont demandé des informations sur nos solutions. Sans surprise, une grande partie de cette demande vient d'Europe, c'est pourquoi nous avons maintenant ouvert notre siège européen à Sophia-Antipolis, juste à l'extérieur de Nice, en France.
Le marché européen est à peu près de la même taille que le marché nord-américain en termes de potentiel. J'irais même jusqu'à dire que l'Europe est en avance, notamment du côté des métaux, avec des sociétés comme EOS, SLM et Renishaw.
En dehors de la France, nous pensons que l'Allemagne sera notre plus grand marché et nous avons récemment annoncé notre partenariat avec Rösler Mass Finishing, le premier fournisseur mondial de technologies de finition de surface. Rösler sera notre bras de distribution en Europe. Avec Rösler, nous aurons une forte présence en Allemagne et pourrons couvrir très rapidement tous les pays industriels clés, de l'Allemagne à la France à l'Espagne au Royaume-Uni à la Pologne à l'Italie.
Donc, pour répondre à votre question, il s'agissait d'un alignement de plusieurs facteurs - nous avons également des plans pour un lancement en Asie, bien que ce soit très probablement fin 2019/2020.
Pourriez-vous partager ce qui se profile à l'horizon pour PostProcess Technologies ?
Nous continuons à recevoir des commentaires de notre clientèle, et la majorité de nos investissements actuels sont utilisés pour améliorer notre solutions pour pouvoir gérer un débit plus élevé avec de nouveaux matériaux. L'équipe de chimie innove constamment pour essayer de suivre la quantité de travail de science des matériaux qui se transforme en additif. Ainsi, des améliorations viennent du point de vue de la suppression du support ainsi que du point de vue de la finition de surface.
Il y a quelques autres problèmes que nous voyons devenir plus aigus dans la post-impression et que nous aborderons à l'avenir. À ce stade, nous ne divulguons pas publiquement ce que nous faisons là-bas, mais cela va certainement au-delà du retrait du support et de la finition de surface. Nous apporterons quelques solutions supplémentaires sur le marché - une en 2019 et une autre en 2020. Celles-ci offriront une suite de produits de post-finition de bout en bout qui, selon nous, répondront à la grande majorité des besoins des clients en matière d'additifs. .
En savoir plus sur les technologies de post-traitement ici .
impression en 3D
- Repenser le processus d'intégration logicielle pour les opérations de fabrication additive
- Entretien d'experts :Pat Warner, spécialiste de la fabrication additive de Renault Formula One Team
- La vérité sur les économies d'échelle pour les processus de fabrication additive
- Entretien d'experts :Felix Ewald, PDG de DyeMansion
- Technologies de fabrication additive :l'entreprise de post-traitement qui façonne l'avenir de la fabrication
- Qu'est-ce que l'« Internet des objets » et qu'est-ce que cela signifie pour la fabrication additive ?
- La prochaine frontière pour la fabrication additive évolutive ? Logiciel MES additif
- Entretien d'experts :Guillaume de Calan, PDG de Nanoe, sur l'avenir de l'impression 3D céramique
- Le cas de l'impression 3D dans le secteur manufacturier