Entretien d'experts :Doug Hedges, président de Sintavia, sur la réalisation de la production en série avec l'impression 3D en métal
Sintavia est un fabricant indépendant qui fournit des services de fabrication additive métallique pour les industries critiques telles que l'aérospatiale et la défense et le pétrole et le gaz .
En se concentrant sur la production en série de pièces métalliques à l'aide de la fabrication additive, la société fournit un service unique de bout en bout qui comprend non seulement la production et le post-traitement, mais également les tests , métallurgie et caractérisation des poudres dans son laboratoire interne.
Récemment, Sintavia a annoncé ses plans d'expansion, en emménageant dans une toute nouvelle installation de 55 000 pieds carrés qui met l'accent sur la production.
Cette semaine, nous sommes ravis d'avoir une conversation avec le président de Sintavia, Doug Hedges, pour discuter de la façon dont l'entreprise produit des pièces métalliques de haute qualité et certifiées, pourquoi la FA est parfaite pour l'industrie aérospatiale et quoi l'industrie de la FA peut faire pour accélérer l'adoption de la technologie.
Pouvez-vous nous parler un peu de Sintavia ?
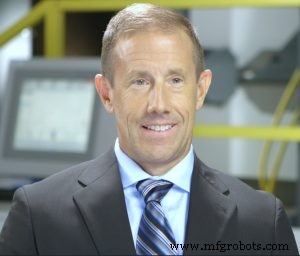
Sintavia a été fondée en 2012 par Brian Neff, PDG et président de la société. La société a été fondée en tant qu'effort interne de fabrication additive avec une société appelée CTS Engines, qui est un MRO indépendant de moteurs à réaction basé à Fort Lauderdale, en Floride.
Sintavia est devenue une société distincte en 2015 et nous avons déménagé à Davie, en Floride, où nous sommes toujours aujourd'hui.
En tant qu'entreprise, nous avons une vaste expérience dans le domaine de l'aviation. Nous avons vu qu'il y avait une opportunité d'utiliser ce contexte pour créer une entreprise verticalement intégrée avec de nombreuses offres différentes. Pour être bon en additif, vous devez également être bon en métrologie, métallurgie, usinage, traitements thermiques, essais, etc.
Ainsi, bien que notre compétence principale soit la fabrication additive, nous utilisons notre expérience dans les domaines de fabrication MRO et OEM pour créer une nouvelle entreprise autonome qui se concentre sur l'aérospatiale et la défense, ainsi que sur le pétrole et le gaz.
Ce qui est unique à propos de Sintavia, c'est que l'intégration verticale sous-tend tout ce que nous faisons :du post-traitement, de la qualité, de la métallurgie, de la numérisation, etc. Tous ces éléments sont situés sous un même toit dans notre usine de production ici à Davie, en Floride.
L'aérospatiale est au cœur des préoccupations de Sintavia. Pouvez-vous nous présenter quelques avantages de la fabrication additive pour l'industrie aérospatiale ?
La fabrication additive fonctionne bien pour l'aérospatiale pour diverses raisons.
Tout d'abord, il est important de noter que la technologie a commencé comme un outil de développement de prototypes pour les équipementiers de l'industrie aérospatiale et de la défense afin d'itérer rapidement les conceptions et les tests les moteurs. Il a maintenant évolué à un point où les entreprises construisent des moteurs avec des pièces additives.
C'est donc toujours un gros moteur. Mais ensuite, il y a tous les autres avantages typiques qui font de la FA une excellente technologie. Ici, je fais référence à la consolidation des constructions soudées, des moulages complexes, de l'allègement, de la conception sans outil. Bien sûr, la complexité n'est pas gratuite, mais elle est considérablement élargie lors de l'utilisation d'additifs.
Par exemple, un objectif principal pour nous en termes de sélection de pièces est les corps de soupape externes à l'extérieur des moteurs à réaction et des conduits. Nous voyons également un marché émergent pour les châssis et les échangeurs de chaleur au sein de l'industrie aérospatiale.
L'une des technologies d'impression 3D métalliques que vous utilisez est Powder Bed Fusion. Quels sont les avantages de cette technologie pour les applications aérospatiales ?
Eh bien, l'impression 3D métal en général se prête vraiment à des conceptions uniques.
La première étape de ce que nous faisons consiste à utiliser la fusion sur lit de poudre avec des lasers et des faisceaux d'électrons pour construire des conduits et des composants à haute pression couche par couche. Il y a évidemment l'avantage d'utiliser la technologie comme outil de remplacement pour les pièces soudées et les pièces moulées déjà utilisées dans l'industrie.
Mais le pouvoir des additifs va bien au-delà de cela :vous êtes en mesure de fabriquer des pièces meilleures, plus légères et plus solides, ce qui facilite essentiellement l'amélioration des performances. En fin de compte, pour vraiment utiliser la puissance de la FA, les composants doivent être conçus pour la fabrication additive.
Vous pouvez utiliser la fabrication additive — je parle principalement des lasers ici — pour des composants tels que des échangeurs de chaleur et des châssis afin de créer des géométries qui étaient auparavant impossibles à fabriquer.
Vous disposez également, par exemple, de corps d'écoulement ou d'ensembles de vannes que vous pouvez accélérer et consolider à l'aide de la FA. Cela permet à nos clients non seulement d'optimiser leurs chaînes d'approvisionnement existantes, mais également de fabriquer de meilleurs produits et de tirer parti des atouts du marché OEM de l'aérospatiale et de la défense.
Prenons l'exemple des échangeurs de chaleur :la fabrication additive vous permet pour créer des parois très fines et de petites géométries complexes à l'intérieur du composant. Vous pouvez donc avoir un mur de 200 microns ou moins. De plus, avec la fabrication additive, vous disposez désormais d'un meilleur moyen d'évacuer la chaleur du composant. C'est génial parce que l'objectif final des échangeurs de chaleur est d'évacuer la chaleur du composant afin que vous puissiez y insérer plus d'électronique.
Nous utilisons la fabrication additive métallique pour améliorer leurs produits. Tout, depuis les corps de soupape, les composants externes des moteurs à réaction, les conduits et les échangeurs de chaleur jusqu'au châssis et aux différents types de structures de tubes qui ont été fabriqués par des soudures avec de nombreux gabarits et accessoires complexes pour les souder ensemble.
Cela dit , nous faisons beaucoup plus que cela aussi. Par exemple, nous travaillons sur ce qu'il y a à l'intérieur des équipements de turbomachines, qu'il s'agisse d'une plus petite turbine qui pourrait être à l'intérieur d'un compresseur, à une plus grande turbine qui pourrait être à l'intérieur d'une fusée.
Nous nous concentrons sur l'aérospatiale commerciale — les moteurs à réaction essentiellement — et une autre concentration sur la propulsion, qui serait des pièces de fusée.
Nous avons alors « l'entre-deux » au sein de l'industrie aérospatiale et de la défense, par lequel je fais référence aux composants obscurs qui étaient autrefois fabriqués de 10 à 100 pièces, mais que nous pouvons maintenant fabriquer en une pièce singulière utilisant la fabrication additive.
Pourriez-vous développer certains des défis de conception associés à ces applications ?
La FA est un processus relativement nouveau dans la fabrication. Nous utilisons des lasers ou des faisceaux d'électrons pour faire fondre la poudre en couches. Essentiellement, ce que nous faisons vraiment, c'est faire des soudures de petite à moyenne taille, ou « micro-soudage ».
Dans ce processus de micro-soudage, il y a un refroidissement rapide où le laser expose la poudre métallique. Vous avez un cas de deux extrêmes :un processus d'impression très chaud, avec un refroidissement rapide en parallèle.
En raison de ces écarts extrêmes de température, votre pièce est sujette à des déformations. Ces pièces ne sont donc pas comme des assemblages soudés traditionnels réalisés avec des pièces moulées ; ce sont des pièces uniques en elles-mêmes.
L'un des principaux défis est de pouvoir prédire comment ces pièces se déplaceront dans le processus de fabrication additive. Un élément clé de ce défi consiste à utiliser cette technologie très moderne et des outils de haute technologie pour faire la prédiction au début, afin d'aider à la coordination complète du processus.
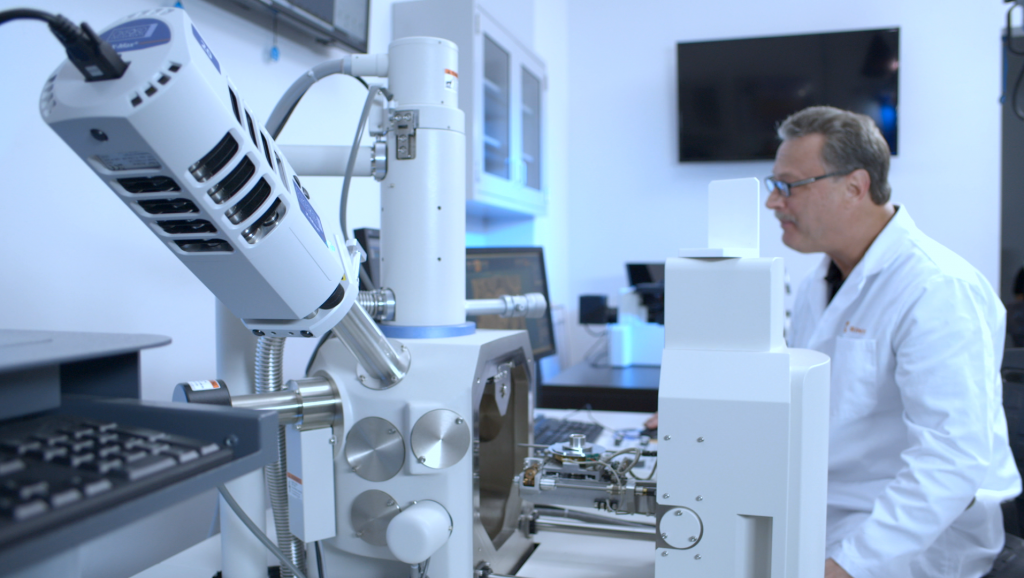
Chez Sintavia, nous utilisons l'analyse par éléments finis (FEA) au début du cycle de conception. Les ingénieurs de Sintavia obtiennent les données initiales de nos clients sous forme de modèles CAO, de dessins et de spécifications. Nos ingénieurs travaillent avec nos clients pour définir des paramètres clés tels que la manière d'orienter une pièce sur la plaque de construction, l'angle auquel une pièce sera créée et la manière dont les supports seront utilisés, soit pour maintenir la pièce vers le bas, soit pour évacuer la chaleur du part.
Nous utilisons les mathématiques pour prédire comment la pièce va se déformer et minimiser cette distorsion pour créer une pièce de très haute fidélité. Nous devons savoir comment cette pièce va se déplacer et se déplacer sur nous, afin que nous puissions ajouter du stock aux brides, aux alésages, aux trous, etc., pour nous assurer qu'il y a suffisamment de stock à nettoyer à la fin du processus. En utilisant cette approche, nous pouvons également tenir compte du post-traitement de cette partie à un moment ultérieur.
Une chose à garder à l'esprit est que la fabrication additive est un processus extrêmement puissant pour créer des pièces complexes, mais il doit être utilisé en coordination avec les processus traditionnels. La coordination du processus additif avec le processus soustractif est critique.
Nous entendons beaucoup parler des défis liés au post-traitement des pièces métalliques, et c'est l'un des services proposés par Sintavia. Pourriez-vous nous expliquer certains des plus grands défis liés au post-traitement et à votre approche ?
Le post-traitement doit être un effort coordonné entre le processus d'impression lui-même et le post-traitement qui accompagne cette partie après la production.
Un défi commun que la plupart des gens ne voient pas est l'élimination de la poudre après le processus. Après le processus d'impression, toute la poudre doit être retirée de la pièce. Étant donné que certaines de ces pièces ont des géométries très complexes, nous fabriquons des machines sur mesure - soit à ultrasons, soit à systèmes de vibration traditionnels - pour éliminer la poudre.
Il est courant d'enlever la poudre de la pièce avant l'étape suivante, qui est presque toujours un soulagement du stress. Nous soulageons le stress en interne avec un four sous vide ou un four à caisson pour éliminer le stress résiduel du processus de fabrication additive.
De là, vous passez à une électroérosion à fil ou à une scie à ruban pour retirer la pièce de la plaque. Ensuite, bien sûr, vous devez retirer les supports. Ces supports peuvent aller de simples supports en treillis à quelque chose de très solide utilisé pour maintenir la pièce et produire de très grandes pièces en superalliage de nickel. Ceux-ci sont soumis à de fortes contraintes thermiques.
Pour cette raison, vous aurez peut-être besoin d'un processus machine très robuste pour retirer les supports de ces pièces. Cela peut représenter un travail considérable. Et quand je dis « processus machine », cela peut signifier beaucoup de choses différentes. Cela pourrait signifier quelque chose d'aussi simple que de les casser avec une pince à une machine-outil à cinq axes très rigide pour retirer ces supports de la pièce.
A partir de ce point, vous avez plusieurs choix. Par exemple, vous pouvez aller chez HIP, que nous présentons sur place, ou nous utilisons l'usinage. Dans ce cas, quand je dis usinage, je veux dire usinage pour imprimer. Donc, ce n'est vraiment pas différent de ce que vous verriez dans un atelier d'usinage.
La plupart du temps, nous avons un plan 2D avec beaucoup de contrôles et nous usinons cette pièce pour la mettre en conformité avec le cahier des charges.
En passant aux poudres métalliques elles-mêmes, quel est le processus de développement des poudres métalliques chez Sintavia ?
Pour être clair, nous ne développons pas vraiment de poudres en soi. Mais nous avons aidé les entreprises à développer des alliages qui n'étaient pas disponibles dans le commerce dans le passé.
Nous avons des entreprises avec lesquelles nous travaillons qui ont, par exemple, une variante d'acier à outils ou une variante d'acier inoxydable. Ce sont généralement des alliages spéciaux qu'ils ont développés pour être utilisés pour une sorte d'avantage de performance à l'avenir.
Ce que nous avons, ce sont des solutions de poudre approuvées pour le vol pour l'industrie aérospatiale. Nous achetons la poudre, l'apportons dans notre laboratoire et la soumettons à une multitude de tests avant le début de la construction.
L'une de nos forces chez Sintavia est que nous avons une caractérisation complète sur site de notre poudre au sein de notre laboratoire. Cela nous permet d'échantillonner et de comprendre ce qui arrive à la poudre. En règle générale, d'autres entreprises sous-traitent ce processus. Ainsi, même si nous pouvons nous procurer des matériaux auprès de notre fournisseur de poudre, nous effectuons les tests de flux, la morphologie, la distribution de la taille des particules, l'analyse des gaz, l'ICP pour la chimie, etc.
Nous effectuons environ huit ou neuf tests pour nous assurer que les poudres répondent aux exigences de fabrication de nos clients. Ensuite, au fur et à mesure que la poudre est utilisée, nous prélevons et archivons ces échantillons de poudre pour comprendre ce qui arrive à la poudre au fur et à mesure que la fabrication se poursuit. Cela signifie que nous sommes en mesure de comprendre exactement ce qui arrive à la poudre au fur et à mesure qu'elle s'habitue.
Sintavia a annoncé son intention d'ouvrir une toute nouvelle usine avec une augmentation du nombre de machines ce mois-ci. Pourriez-vous partager la vision derrière cette nouvelle installation ?
Nous sommes très heureux d'ouvrir notre nouvelle installation ce mois-ci.
La nouvelle installation aura une superficie de 55 000 pieds carrés et nous allons baser cette installation sur notre succès passé.
Un point clé est qu'il sera fortement basé sur la production. Nous allons abriter pour plus de 30 millions de dollars de nouvelles machines, de plus grands équipements AM modernes, des systèmes de manipulation de poudre, des générateurs de secours, des alimentations électriques, du gaz inerte. Nous prévoyons d'ajouter jusqu'à 135 nouveaux emplois pour Sintavia et le sud de la Floride.
La nouvelle installation est vraiment la vision de prendre ce que nous avons fait à une plus petite échelle, en exécutant 12 machines ici dans notre installation actuelle, et de l'agrandir en une installation de 55 000 pieds carrés avec jusqu'à 65 Machines.
Il y aura un gros effort dans la fabrication additive, dans les traitements thermiques. post-traitement, finition, nettoyage, etc.
Essentiellement, nous cherchons à contrôler le processus additif au sein d'une seule installation. C'est vraiment le modèle commercial :nous voulons étendre ce que nous avons fait et intégrer cela dans un processus de fabrication qui garantit la qualité et la répétabilité pour nos clients OEM.
Envisageriez-vous de vous étendre à d'autres secteurs à l'avenir, comme l'automobile ou le médical, où il existe également une forte demande de pièces métalliques imprimées en 3D ?
Oui, absolument. Nous avons des choses qui se passent à la fois dans l'automobile et dans le médical. Et il y a d'autres industries pour lesquelles l'additif a également du sens.
Par exemple, nous intervenons dans les turbines à gaz industrielles. Bien que notre expérience soit celle des turbines à gaz aéronautiques, les turbines à gaz au sol pour l'énergie sont essentiellement des moteurs à turbine aéronautique à grande échelle et légèrement différents.
La technologie s'applique également très bien au secteur biomédical.
Sintavia est accrédité AS9100 — AS9100 est un système de gestion de la qualité pour l'industrie aérospatiale. Notre laboratoire est accrédité ISO 17025 pour les mesures mécaniques, ce qui peut aller de la caractérisation et de la chimie des poudres aux essais de traction et de fatigue.
L'industrie biomédicale a une agence d'accréditation différente ; la plupart de cela est réduit à ISO 13485. Une fois que vous avez AS9100, vous pouvez passer à ISO 13485. Il n'y a pas grand-chose à faire entre ces différentes industries. Après tout :la qualité est la qualité et les processus sont les processus. Si vous pouvez faire de l'aérospatiale, vous pouvez faire cette transition vers d'autres marchés.
Aussi, au-delà de tout ce que j'ai mentionné, le contrôle qualité est l'aspect le plus important.
Dès le premier jour, nous nous sommes concentrés sur le développement de notre système qualité avec AS9100, Certifications ISO et Nadcap. Tout cela est très bénéfique pour nos clients OEM et peut certainement être une ressource pour d'autres industries également.
À votre avis, quelles sont certaines des choses nécessaires pour accélérer l'adoption de l'impression 3D métal ?
Pour toute notre technologie et les prouesses que nous avons en matière d'analyse, nous devrions vraiment nous concentrer sur ce qui stimule les affaires. Les affaires sont motivées par l'argent et la vitesse. Cela signifie que la technologie doit devenir plus rapide, moins chère et mieux établie.
Cela dit, nous voyons comment les choses évoluent. Pendant notre séjour ici à Sintavia, nous avons vu comment la FA métal a évolué. Par exemple, à un moment donné, l'aluminium était un matériau relativement délicat à imprimer dans la fabrication additive, mais maintenant c'est presque banal. À mesure que nous voyons des lasers supplémentaires, que nous voyons l'expertise et la conception de pièces pour les additifs, cela offrira à nos clients une vitesse plus rapide et des économies de coûts.
Tout cela est historiquement issu de l'industrie du prototypage, et nous voulons déplacer cela vers la production en série. Il y a certaines choses que nous devons faire pour le rendre plus rapide et moins cher, fournir de la qualité et offrir les avantages que tout le monde sait que les additifs métalliques peuvent offrir.
Comment voyez-vous l'évolution de la fabrication additive métallique au cours des cinq prochaines années, et comment Sintavia s'intègre-t-elle dans cette vision ?
Ce que nous devons vraiment faire, c'est commencer à fabriquer des pièces en mode production. Pour les industries critiques, nous devons nous assurer que nous produisons de véritables pièces métalliques entièrement fonctionnelles.
Nous savons que ces pièces rivalisent extrêmement bien avec les pièces moulées pour les propriétés mécaniques. Avec le bon processus et les bons contrôles, ils peuvent également concurrencer les produits bruts, et même les produits contrefaits dans certains cas.
Le contrôle qualité, c'est-à-dire comprendre les exigences qualité et être capable de valider votre pièce va vraiment faire la différence pour l'avenir.
Mais nous ne pouvons pas non plus perdre de vue le fait que la technologie est encore relativement nouvelle. En tant qu'industrie, nous faisons beaucoup de choses pour la toute première fois.
Cela signifie que le début du processus doit être appris en premier lieu.
Par exemple, au début du processus, les ingénieurs devront comprendre les stratégies de support et passer du temps à apprendre comment optimiser au mieux la géométrie de la pièce et la géométrie du support, ce qui contribuera à son tour à produire de meilleures pièces et à garantir que les supports se détachent relativement facilement.
Grâce à ce travail effectué au commencer, vous aurez pris ce qui était une étape coûteuse et longue de suppression du support et l'aurez rendu beaucoup moins coûteux. L'effort d'ingénierie pour fabriquer les pièces est vraiment essentiel pour atteindre un point de maturité permettant de fabriquer des produits les uns après les autres.
À quoi ressemble l'avenir de Sintavia ?
Ça a l'air très excitant ! Bien sûr, cela semble également assez difficile alors que nous emménageons dans nos nouvelles installations. Nous mettrons en œuvre la production au plus juste. Nous possédons la première installation de fabrication additive allégée à grande échelle spécialement développée pour notre alignement pour les équipementiers et la chaîne d'approvisionnement.
En 2019, nous poursuivrons une grande partie du travail que nous avons accompli ces deux dernières années, en termes de qualification et de développement de pièces pour nos clients.
Je ne citerai pas de noms, mais si vous regardez les principales entreprises aérospatiales dans le monde, il est très probable que nous fassions affaire pour elles.
Dans certains cas, comme notre relation avec Honeywell, où nous sommes le premier fournisseur AM approuvé pour fabriquer des pièces prêtes au vol pour Honeywell Aerospace. Nous nous sommes associés à Honeywell pour utiliser notre usine actuelle et notre prochaine usine pour les sortir et fabriquer des pièces de production pour Honeywell.
Honeywell est un adepte relativement rapide de la technologie et ils ont beaucoup, beaucoup d'applications. Mais si vous sortez d'Honeywell, il y a de fortes chances, qu'il s'agisse d'un avionneur ou d'un groupe motopropulseur, que ce soit un fournisseur d'aérospatiale et de défense, que nous travaillions pour eux maintenant.
Nous considérons 2019 et 2020 comme des années relativement importantes pour nous, en ce qui concerne l'adoption d'additifs métalliques. C'est vraiment excitant qu'Honeywell soit là aujourd'hui, mais nous allons voir que nous aurons plus de clients faisant de la production en série dans les années à venir.
Nous alignons notre entreprise pour fournir cette ressource aux équipementiers du monde entier afin qu'ils puissent avoir un guichet unique, un partenaire verticalement intégré pour produire ces pièces avec la fabrication additive.
Une dernière réflexion ?
Je tiens à réitérer que la qualité est notre priorité.
Nos clients sont, sans aucun doute, les clients les plus averses au risque au monde. Pour qu'ils se sentent à l'aise avec ces composants critiques fabriqués par fabrication additive, la qualité est primordiale.
En fin de compte, nous voulons conformer les produits aux dessins techniques et aux spécifications, pour les utiliser dans des applications réelles. Pour ce faire, il faut se concentrer sur la conformité.
De plus, aujourd'hui, la FA est l'endroit où se concentre toute l'attention des médias et où beaucoup de temps et d'argent sont dépensés. Mais en fin de compte, il devrait s'agir de prendre la pièce que vous avez fabriquée par fabrication additive et de la conformer aux exigences d'ingénierie de vos clients.
Alors oui, nous aimons parler de fabrication additive. Mais j'aime aussi le considérer comme avancé fabrication. J'aimerais m'éloigner des mots à la mode de la fabrication additive pour dire que nous sommes un fabricant avancé de pièces aérospatiales de précision. Nous voulons fabriquer des pièces avancées pour nous assurer que nos clients peuvent améliorer considérablement leurs conceptions actuelles.
Pour en savoir plus sur Sintavia, visitez : https://sintavia.com/
À propos de Doug Hedges
Doug Hedges a plus de 20 ans d'expérience dans l'industrie aérospatiale, de la conception de composants expérimentaux OEM aux réparations, modifications et développement de composants approuvés par la FAA sur la base des spécifications et des contrôles standard de l'industrie.
Avant Sintavia, il a servi en tant qu'ingénieur principal chez CTS Engines, développant des réparations et des processus pour la révision des moteurs à réaction de General Electric, ingénieur de projet principal pour HEICO Aerospace, ingénieur principal PMA pour Kapco Global et ingénieur de conception pour Rolls-Royce. Doug est titulaire d'un diplôme BSME en génie mécanique de l'Université du Minnesota.
Entrevues d'experts
La série d'entretiens d'experts d'AMFG présente des entreprises et des individus innovants qui contribuent à façonner l'avenir de la fabrication additive. Pour plus d'informations sur la participation à la série, veuillez contacter [email protected].
impression en 3D
- Comment passer à la production additive en série avec Additive MES ?
- Entretien avec un expert :professeur Neil Hopkinson, directeur de l'impression 3D chez Xaar
- Entretien avec un expert :Philip Cotton, fondateur de 3Dfilemarket.com
- Entretien avec un expert :Dr Alvaro Goyanes de FabRx
- Entretien d'experts :John Kawola, président d'Ultimaker, sur l'avenir de l'impression 3D
- Entretien d'experts :Doug Hedges, président de Sintavia, sur la réalisation de la production en série avec l'impression 3D en métal
- Entretien d'experts :Brian Alexander de Solvay sur le développement de polymères hautes performances pour l'impression 3D
- Entretien d'experts :Philip DeSimone, cofondateur de Carbon, sur la transition vers une production à haut volume avec l'impression 3D
- 4 défis de fabrication additive pouvant être résolus avec un logiciel