Entretien d'experts :Philip DeSimone, cofondateur de Carbon, sur la transition vers une production à haut volume avec l'impression 3D
Le carbone a connu une ascension fulgurante depuis sa création en 2013. Au cours des six dernières années, la technologie exclusive Digital Light Synthesis™ (DLS) de l'entreprise a été adoptée par des clients de divers secteurs, de l'aérospatiale à l'automobile en passant par la consommation marchandises et médical. Avance rapide jusqu'en 2019, où la société financée par le capital-risque et basée dans la Silicon Valley est désormais l'un des trois seuls fabricants d'imprimantes 3D à avoir atteint une valorisation de plus de 1,7 milliard de dollars.
Grâce à sa technologie, Carbon a de grands projets pour perturber la façon dont les pièces en polymère sont fabriquées. Et avec des clients de premier plan sur sa liste, notamment adidas, Ford Motor Company et Lamborghini, la société semble prête à poursuivre sa vision.
Nous avons pu discuter avec le cofondateur et vice-président du développement commercial de Carbon, Philip DeSimone, pour en savoir plus sur la technologie, la stratégie de croissance et la mission de l'entreprise.
Réinventer la façon dont les pièces en polymère sont fabriquées
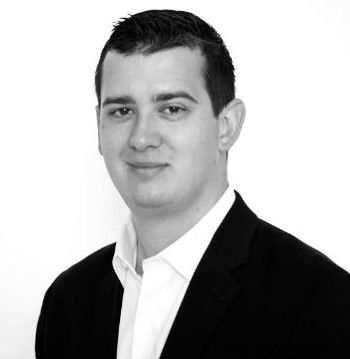
Pour DeSimone, la mission de Carbon est claire. « Notre objectif est de réinventer la façon dont les produits polymères sont conçus, fabriqués, fabriqués et livrés », dit-il. « Notre technologie propriétaire de synthèse de lumière numérique en est un élément clé. »
La synthèse de lumière numérique, ou DLS en abrégé, est un élément central de la proposition de valeur de Carbon. La technologie a été dévoilée publiquement pour la première fois en 2015, lors d'une conférence TED donnée par le cofondateur et PDG de la société, le Dr Joseph DeSimone. À l'époque, l'un des principes clés du discours était l'amélioration de la vitesse offerte par la nouvelle technologie.
Comment fonctionne exactement le processus DLS ?
En bref, DLS est une technologie d'impression 3D qui fusionne la lumière et l'oxygène pour produire des pièces à partir d'un pool de résines liquides programmables.
Le processus d'impression photochimique consiste à projeter de la lumière à travers une membrane perméable à l'oxygène dans une cuve de résine liquide durcissable aux UV. Un bain ou un four de durcissement thermique programmé est ensuite utilisé pour définir les propriétés mécaniques de la pièce afin de la renforcer.
Pour les clients, la technologie offre une gamme d'avantages, notamment la possibilité d'imprimer en 3D des pièces hautes performances et durables avec une excellente finition de surface et des propriétés mécaniques isotropes, le tout à un coût inférieur aux techniques de fabrication traditionnelles.
Bien sûr, la demande croissante d'impression 3D n'est que l'un des indicateurs clés de la numérisation croissante de la fabrication. Pour DeSimone, les avantages de cela sont indéniables.
« Une fois qu'une entreprise passe au numérique, elle ne peut plus revenir en arrière », dit-il fermement.
« L'impression 3D permet aux fabricants de débloquer de nouvelles opportunités commerciales telles que la personnalisation de masse, l'inventaire à la demande et des conceptions de produits auparavant impossibles. Cela change fondamentalement la façon dont les concepteurs et les ingénieurs pensent, comment les gens collaborent et travaillent et élimine les contraintes conventionnelles. »
Passer du prototypage à la production en grand volume
Faire passer la conversation du prototypage rapide à la production a été une prérogative clé pour l'industrie de la fabrication additive ces dernières années.
Alors que les entreprises cherchent à intégrer les technologies d'impression 3D dans leurs flux de production, les fabricants de matériel sont confrontés à la tâche de développer des machines qui offrent une vitesse améliorée et une plus grande précision des pièces.
Pour certains, Carbon fait déjà partie des précurseurs en la matière. Le mois dernier, l'entreprise a dévoilé sa nouvelle imprimante L1, marquant la première machine de l'entreprise depuis son imprimante M2, lancée en 2017.
Présenté comme une « solution de fabrication de bout en bout », le L1 a été développé en pensant à la fabrication de gros volumes (notez que le « L » signifie « grand »). Il offre une surface de construction cinq fois supérieure à celle de son prédécesseur et est destiné à la production de plusieurs pièces en une seule fois.
Le fabricant d'équipement, Riddell, a été annoncé comme l'un des premiers utilisateurs de la machine. L'entreprise a déjà commencé à utiliser le L1 pour sa plate-forme de casque Diamond : des doublures de casque personnalisées et imprimées en 3D pour les joueurs de la NFL.
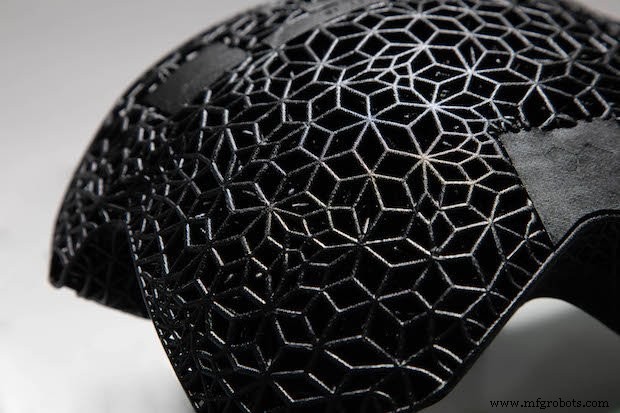
Les doublures de casque ont été imprimées à partir d'un élastomère personnalisé hautement amortissant produit par Carbon sous la forme d'une structure en treillis et ont été conçues pour absorber le plus d'impact tout en offrant un confort et un ajustement personnalisé. L'élément personnalisé signifie que les conceptions peuvent être adaptées aux dimensions d'un joueur.
Cependant, c'est peut-être le partenariat très médiatisé de Carbon avec adidas qui concrétisera véritablement les ambitions de fabrication à haut volume de l'entreprise.
Vous cherchez à développer une semelle intermédiaire qui pourrait répondre aux exigences de performance des athlètes d'élite, adidas avait besoin d'un moyen de fabriquer des semelles intermédiaires qui pourraient répondre aux besoins liés au confort, à l'amorti et au mouvement. L'impression 3D - et plus particulièrement la technologie DLS de Carbon - s'est avérée être la solution idéale.
Depuis l'annonce de leur intention d'imprimer en 3D des semelles intermédiaires pour les baskets Futurecraft 4D d'adidas, les entreprises se sont engagées à produire 100 000 paires de chaussures en 2019. Selon DeSimone, les deux ont l'intention d'étendre cela pour produire des millions de unités au cours des deux prochaines années. Se référant à la collaboration, il déclare :« Cette production de masse est rendue possible par notre imprimante L1, conçue pour produire des produits hautement spécialisés à grande échelle. »
En effet, cette montée en puissance de la production est révélatrice de l'intérêt accru de l'industrie pour l'impression 3D pour la fabrication en grand volume.
« Chez Carbon, nous avons mis à nu les imprimantes, les matériaux, les logiciels et les outils de conception nécessaires pour fournir une solution complète d'installation de fabrication. Toutes ces choses sont nécessaires pour franchir le gouffre entre le prototypage et la production. »
Stratégie de croissance de Carbon
Plongez plus loin dans la croissance de Carbon et l'importance de ses partenariats devient claire.
Au cours des dernières années, la société a annoncé un certain nombre de collaborations de haut niveau qui, notamment, ne se limitent pas à un seul secteur ou vertical.
Alors, quelle est l'approche de Carbon en matière de partenariats et quel rôle jouent-ils dans la stratégie de croissance de l'entreprise ?
« Les partenariats sont essentiels à notre succès et importants dans tous les aspects de notre entreprise », dit DeSimone, lorsqu'on lui a demandé. « Chaque fois que nous signons un contrat d'abonnement avec un client, nous signons un partenariat avec cette entreprise pour la durée de l'accord. Le carbone permet aux clients de produire à grande échelle d'une manière qui n'a jamais été faite auparavant et la seule façon d'y parvenir avec succès est de travailler côte à côte, jour après jour, pour en faire une réalité. »
Prenez comme exemple son récent partenariat avec Ford Motor Company en janvier dernier. Lors de l'atelier de fabrication additive pour l'automobile du Salon international de l'automobile de l'Amérique du Nord 2019 à Détroit, les deux sociétés ont présenté une série de pièces automobiles, fabriquées à l'aide de l'impression 3D. Ils comprenaient des pièces de rechange de bras de levier de chauffage, de ventilation et de refroidissement (CVC) pour la Ford Focus, les prises auxiliaires Ford F-150 Raptor et les supports de frein de stationnement électrique Ford Mustang GT500.
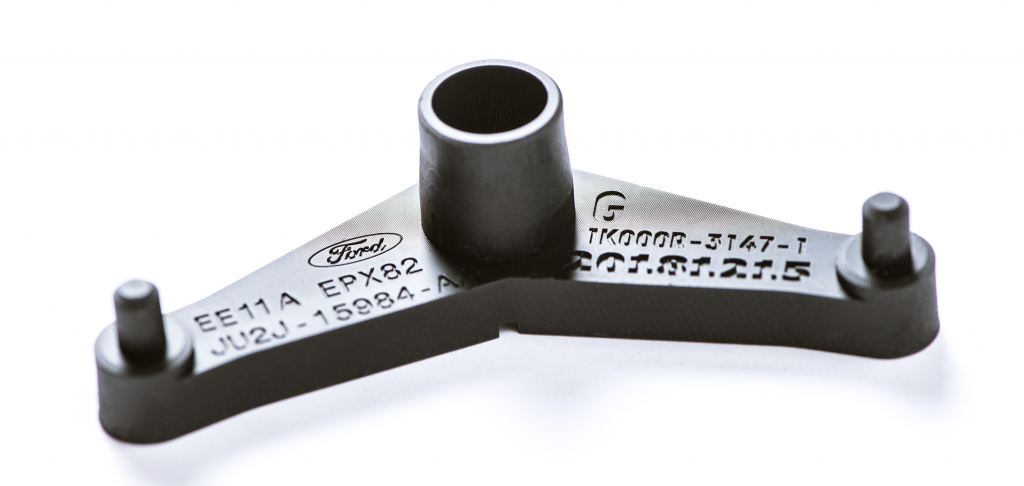
Pour Carbon, cette étape représente une autre étape dans son objectif de fournir des pièces de qualité technique pouvant être utilisées dans des applications industrielles de pièces finales. Il souligne également le potentiel durable de l'impression 3D pour le secteur automobile.
« Nous pensons qu'il existe une énorme opportunité pour Carbon de s'associer à des constructeurs automobiles pour fabriquer des voitures plus légères et des stocks à la demande », déclare DeSimone. « Avec Ford, nous avons déjà réussi à réduire de 60 % le poids des supports de frein de stationnement électrique Ford Mustang GT500, une réduction de 50 % du délai de livraison et une réduction de 90 % des coûts pour le bras de levier Ford Focus HVAC. ”
Bien entendu, les partenariats ne sont pas le seul facteur de réussite de Carbon – le positionnement du produit et la réponse à la demande du marché sont également essentiels, comme le souligne DeSimone. « Je pense que le principe sous-jacent de notre succès est que nous nous sommes positionnés et que nous nous sommes engagés avec des partenaires comme une « véritable entreprise de solutions. » »
Développement de matériaux
Outre ses développements matériels, Carbon a également les yeux rivés sur le développement de matériaux.
Avec ce que DeSimone appelle une « approche à plusieurs volets » des matériaux, Carbon invite à la fois le développement et la validation par des tiers ainsi que le développement de matériaux en interne.
« Nous pensons que si un tiers crée un matériau différencié, c'est à nous de le valider pour la plateforme et de le proposer aux clients de notre Resin Store », explique DeSimone. « Nous avons également une équipe chez Carbon qui développe des matériaux que personne n'a vu auparavant dans l'impression 3D. Ces matériaux contribuent à créer de nouvelles opportunités pour les entreprises de fabriquer des produits auparavant impossibles à fabriquer, tels que la semelle intermédiaire Futurecraft 4D pour adidas. développer des matériaux spécialisés adaptés aux besoins de diverses industries.
Comme l'automobile. Dans sa collaboration avec Ford, le matériau Epoxy (EPX) 82 a été utilisé. La résine à haute résistance est un candidat solide pour les applications de production, avec des propriétés telles que la durabilité, la légèreté, la résistance aux températures élevées et la résistance aux pressions élevées.
L'industrie médicale est un autre domaine que Carbon a ciblé pour le développement de matériaux. En septembre 2018, Carbon a annoncé le premier matériau de qualité médicale pour sa technologie DLS :le polyuréthane médical 100 (MPU 100), conçu pour améliorer la qualité des produits médicaux et accélérer les délais de développement des produits.
La résine polymère blanche possède une gamme de propriétés mécaniques, notamment une résistance élevée, une résistance à l'abrasion, une biocompatibilité et une stérilisabilité. La combinaison de ces propriétés rend le MPU 100 idéal pour les dispositifs médicaux à usage unique, les manches d'outils chirurgicaux et les prothèses, pour ne citer que quelques applications.
Regard vers l'avenir
À quoi ressembleront les cinq, dix prochaines années pour l'industrie de la fabrication additive ? DeSimone a donné ses pensées.
L'un des principaux défis consistera à faire de l'impression 3D une industrie de prototypage et une éducation qui lui permettront d'exploiter tout son potentiel des technologies d'impression 3D », a-t-il déclaré.
Malgré cela, cependant, DeSimone défend les opportunités futures de la technologie.
« Je pense vraiment que vous verrez l'impact de la fabrication numérique comme une solution pour la fabrication à grande échelle. Il existe une énorme opportunité pour la fabrication numérique de faire une brèche sur le marché du moulage par injection de polymères de 300 milliards de dollars. Le carbone aura son rôle à jouer en démontrant ce qui est possible lorsque vous combinez des innovations dans les logiciels, le matériel et les matériaux pour rendre l'impossible. »
Quelle est la prochaine étape pour Carbon ? « Nous nous concentrons sur la croissance et la création d'une entreprise prospère », déclare DeSimone. « Nous avons enregistré une croissance à trois chiffres en 2018 et nous sommes sur la bonne voie pour une croissance à trois chiffres à nouveau en 2019. Nous avons également des partenariats et des applications plus passionnants en préparation, ce dont nous sommes très enthousiastes. »
Pour en savoir plus sur Carbon, visitez : https://www.carbon3d.com/
——————————-
Entrevues d'experts
La série d'entretiens d'experts d'AMFG présente entreprises et individus innovants qui contribuent à façonner l'avenir de la fabrication additive. Pour plus d'informations sur la participation à la série, veuillez contacter [email protected].
impression en 3D
- Entretien avec un expert :professeur Neil Hopkinson, directeur de l'impression 3D chez Xaar
- Entretien avec un expert :Philip Cotton, fondateur de 3Dfilemarket.com
- Entretien avec un expert :Spencer Wright de pencerw.com et nTopology
- Entretien avec un expert :Dr Alvaro Goyanes de FabRx
- Entretien avec un expert :Dr Bastian Rapp de NeptunLab
- Impression 3D avec du silicone — son heure arrive-t-elle ?
- Entretien avec un expert :Ibraheem Khadar de Markforged
- Sports automobiles, courses de performance et impression 3D :une interview avec Revannth Murugesan de Carbon Performance
- Impression 3D DLS carbone :Présentation de la technologie