Entretien d'experts :Jan Tremel sur la façon dont Bosch utilise l'impression 3D dans son centre de compétence
La multinationale allemande d'ingénierie et de technologie, Bosch, est peut-être le plus grand fournisseur mondial de composants automobiles et un important fournisseur de technologies industrielles, de biens de consommation, ainsi que de technologies énergétiques et du bâtiment.
Il n'est donc pas surprenant que l'entreprise soit également fortement impliquée dans la fabrication additive (FA). La technologie accélère la mise sur le marché des nouveaux produits lorsqu'elle est utilisée pour le prototypage et, lorsqu'elle est utilisée pour la production, elle peut introduire plus de flexibilité et d'agilité dans une chaîne d'approvisionnement en imprimant certains composants plus rapidement et à la demande.
Bosch utilise la FA dans toutes ses divisions et dispose également d'un centre de compétence dédié à l'impression 3D.
Pour en savoir plus sur la façon dont Bosch applique l'impression 3D dans son activité, nous sommes rejoints aujourd'hui par Jan Tremel, responsable du centre de compétence pour l'impression 3D (CoC), qui appartient à l'unité Powertrain Solutions .
Avec Jan, nous découvrons les avantages que la FA apporte à Bosch, les défis liés à l'adoption de l'impression 3D en interne, ainsi que l'état actuel et l'avenir de l'impression 3D dans l'industrie automobile.
Pouvez-vous me parler un peu de votre parcours et de la manière dont vous vous êtes impliqué dans la FA ?
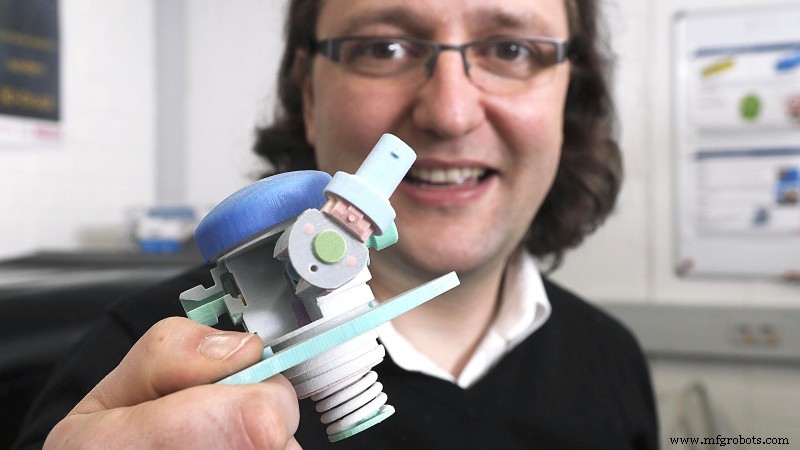
Je me suis impliqué pour la première fois entre 2006 et 2007, pendant la période où le mouvement RepRap a commencé à gagner du terrain.
J'étais fasciné par la technologie et j'ai construit moi-même ma première imprimante 3D à l'université.
Chez Bosch, j'ai pensé à quel point ce serait plus simple si nous avions accès à une petite imprimante 3D. Cette idée m'a inspiré plusieurs propositions, qui ont finalement abouti à la création d'un pôle de compétence.
À ce stade, Bosch a reconnu qu'ils devraient intégrer cette technologie, à la fois pour les plastiques et les métaux, pour pouvoir l'utiliser dans leurs développements en cours pour les pièces de moteur à combustion que nous fournissons sur le marché .
Je travaille actuellement dans l'unité commerciale Powertrain Solutions. Il génère près d'un quart du chiffre d'affaires total de Bosch par an et intègre environ un quart de tous les associés de Bosch. Ici, nous essayons de mettre en œuvre l'impression 3D dans des projets sérieux, comme des pompes à haute pression pour l'essence et le diesel, des injecteurs et d'autres systèmes hydrauliques.
Vous dirigez actuellement le Centre de compétence pour l'impression 3D. Pouvez-vous me parler du travail que vous faites là-bas et de la manière dont vous appliquez la technologie ?
Chez Bosch, nous avons plusieurs centres de compétence.
Pour vous donner un aperçu, chez Bosch, nous sommes divisés en 4 branches principales. Cela signifie que nous avons une branche pour les technologies du bâtiment, par exemple, les caméras de sécurité, les microphones pour les grandes arènes, etc.
Une autre unité est responsable des biens de consommation, des fours aux machines à laver.
Ensuite, nous avons l'unité Technologie Industrielle, spécialisée dans les machines spéciales pour les industries lourdes.
Enfin, mon unité est Powertrain Solutions, qui est le domaine automobile. Toutes les unités que j'ai décrites ont leurs propres équipes qui sont responsables de la mise en œuvre de la FA dans leurs gammes de produits.
Dans mon unité, 50 % de mon travail est consacré à l'ingénierie de nouveaux produits. Cela signifie que je soutiens mes collègues du département de développement de produits, en utilisant des composants imprimés en 3D dans les nouveaux produits.
Cela nécessite de créer de nouvelles applications innovantes qui bénéficieront de la complexité de la conception rendue possible par l'impression 3D.
D'un autre côté, je collabore également avec toutes nos usines de fabrication . Cela signifie que je permets ou que j'éduque les personnes travaillant directement sur les chaînes de montage et dans les ateliers de fabrication, afin qu'elles puissent utiliser la FA dans leur travail quotidien.
Permettez-moi de vous donner un exemple :une équipe de maintenance a pour tâche de maintenir une ligne de production en marche toute la journée. Et ils ont besoin, par exemple, de remplacer des pinces qu'ils peuvent attacher à un robot pour remplacer les pièces cassées et éviter les temps d'arrêt.
J'organise donc des ateliers avec eux, pour leur montrer ce qu'il est possible de faire avec des matériaux standards et une simple imprimante 3D, afin qu'ils puissent créer cette pièce de remplacement pour leur équipement.
De plus, nous ciblons activement des scénarios de réduction des coûts, par exemple, où nous pouvons remplacer les conceptions existantes par des pièces imprimées en 3D pour économiser de l'argent en interne. Par exemple, nous avons beaucoup d'appareils de test qui peuvent être améliorés. Avec l'impression 3D, vous pouvez améliorer le temps de cycle de la station elle-même et, par conséquent, améliorer les performances de toute la ligne. Cela nous aide à réduire les coûts et les déchets.
Quelle valeur l'impression 3D apporte-t-elle à l'industrie automobile ?
AM ajoute un autre processus utile à un portefeuille de processus déjà bien établi. Dans l'automobile, nous utilisons des procédés comme le fraisage et le tournage, nous pouvons revêtir des pièces et faire du moulage par injection plastique. Ces processus sont tous bien compris.
Mais tous ces processus ont certaines limites en termes de flexibilité de conception et de capacité d'itération.
Dans l'industrie automobile, les cycles de production sont de plus en plus courts. Cela signifie que vous souhaitez tester des pièces et des conceptions très rapidement. À cet égard, les processus standard peuvent être très coûteux et prendre beaucoup de temps.
Laissez-moi vous donner un exemple. Si vous avez besoin de l'outil de moulage pour une pièce en plastique compliquée, la production peut prendre jusqu'à 12 à 14 semaines, voire plus. Et avec AM, vous êtes en mesure de générer le même résultat dans un délai beaucoup plus rapide, peut-être en 2 à 4 semaines.
Cela signifie que vous pouvez avoir au moins 3 itérations d'une pièce avec l'impression 3D, alors qu'avec le moulage par injection, vous n'en auriez qu'une que vous pouvez utiliser pour améliorer votre composant. De cette façon, AM permet un cycle d'itération beaucoup plus court qui vous permet d'améliorer votre composant.
C'est juste un domaine où l'impression 3D peut aider.
En termes de production en série, je m'attends à ce que AM soit utilisé pour personnaliser les voitures dans une bien plus grande mesure qu'aujourd'hui. Cela n'a pas beaucoup de sens d'imprimer en 3D des composants produits en série comme des sièges ou des volants.
Mais si vous avez de petits volumes de production, comme c'est le cas pour les voitures de luxe ou les voitures de sport aujourd'hui, AM peut permettre de produire des pièces spéciales pour ces voitures de manière plus économique que si vous les produisiez en utilisant une technologie traditionnelle .
Nous verrons cela, d'abord, dans une gamme de voitures très exclusive et avec un ensemble très limité de pièces produites.
Au fur et à mesure que les processus de FA s'accélèrent et s'améliorent, nous finirons par voir les volumes de production de FA passer de quelques centaines de pièces à plusieurs milliers de pièces.
La FA a-t-elle encore des défis à relever pour accélérer sa transition vers la production en série ?
Il y a beaucoup d'obstacles.
L'un est les limitations matérielles. L'industrie a encore un long chemin à parcourir avant d'avoir les bons matériaux, à la fois des métaux et des plastiques, pour les applications automobiles. Par exemple, certains de nos composants nécessiteront un acier de haute qualité pouvant résister à des pressions très élevées.
De plus, si vous regardez une voiture moderne, il existe de nombreux composants en fibre de verre chargée matières plastiques, qui ne sont pas disponibles sur le marché actuellement, ou bien plus chères que les matériaux que nous utilisons avec les procédés traditionnels.
Par exemple, vous avez un composant en plastique à proximité d'un moteur à combustion. Cette pièce a des exigences de température très élevées et est généralement fabriquée à partir d'un polyamide chargé de fibre de verre. Les matériaux AM ne peuvent pas fabriquer cette pièce de la même manière et avec les mêmes caractéristiques que nous voyons aujourd'hui avec les plastiques traditionnels.
Un matériau usiné et un matériau fabriqué de manière additive auraient des caractéristiques totalement différentes, car la fusion du matériau couche par couche, crée une microstructure interne différente de celle à laquelle nous sommes habitués avec les matériaux standards.
Un autre obstacle est le manque de précision et de répétabilité. Il y a encore des améliorations à apporter aux systèmes AM pour leur permettre d'imprimer les mêmes pièces sur différentes imprimantes avec des dimensions exactes à chaque fois.
Si vous jetez un œil aux connecteurs et autres composants qui ont des trous très petits et des tolérances très serrées, alors c'est aussi un défi pour les imprimantes 3D à produire.
Enfin, nous voyons beaucoup de processus manuels dans la FA. Bien que, je l'admets, l'industrie essaie d'introduire davantage d'automatisation, il existe encore de nombreux processus manuels, par exemple l'élimination de la poudre dans l'impression 3D métallique, ce qui rend la technologie très coûteuse.
La productivité est un facteur crucial pour l'industrie automobile, lorsqu'il s'agit d'adopter la FA.
Comment voyez-vous la FA évoluer dans l'industrie automobile au cours des 5 prochaines années ?
L'industrie automobile a une approche différente des applications par rapport aux secteurs médical ou aérospatial, où les produits ont généralement une longue durée de vie, par ex. 20 ans ou plus pour un avion.
Le prix de la production automobile est également plus bas, et vous devez avoir des calculs de prix très serrés. Cela signifie que la FA ne sera utilisée que si elle présente un avantage financier clair.
Je suis assez prudent avant de dire que la FA sera utilisée pour des composants automobiles sérieux au cours des prochaines années. Il continuera certainement à servir d'accélérateur pour le développement de produits.
Il faudra encore longtemps avant que la fabrication additive soit utilisée pour la production de masse au sein de l'industrie automobile.
Est-il difficile de convaincre les gens de la valeur de l'impression 3D, ou trouvez-vous que les gens sont très réceptifs à l'adoption de la technologie ?
Cela dépend beaucoup. Lorsque nous avons commencé, nous avions une approche assez missionnaire pour convaincre tout le monde que l'impression 3D est l'une des meilleures choses au monde.
Aujourd'hui, nous nous concentrons davantage sur des projets qui font vraiment la différence dans la production. Tout ce qui peut être fait de manière additive ne doit pas être fait avec cette technologie. Nous étudions d'assez près les applications qui pourraient bénéficier de l'impression 3D.
Au cours des 4 années qui se sont écoulées depuis mon arrivée, nous avons constaté que de nombreuses personnes ont également déjà une imprimante à la maison. Nous leur donnons donc la possibilité d'utiliser une imprimante 3D, non seulement dans leur vie privée, mais aussi au travail pour leur permettre de faire quelque chose de nouveau.
Y a-t-il des tendances au sein de l'industrie qui vous passionnent ?
C'est une question intéressante.
Je suis très intéressé par les start-up qui peuvent vraiment tenir leurs promesses. J'ai vu beaucoup de start-up essayer de créer un business model autour d'un processus qui n'était pas clairement développé.
Mais je suis fasciné par les nouveaux processus qui fonctionnent vraiment. Dans les domaines des plastiques et des métaux, nous constatons de nombreux développements intéressants de la part des plus grands fabricants qui prennent vraiment au sérieux la FA.
Auparavant, les gens étaient contents quand ils avaient une pièce en main, et on pouvait leur dire qu'elle était imprimée en 3D. Aujourd'hui, les gens se soucient beaucoup plus de tous les détails techniques, de sorte que les caractéristiques du matériau imprimé soient respectées.
Ce que j'aime aussi, c'est que le marché se professionnalise. Cela signifie que même pour les filaments, vous pouvez obtenir des données techniques qualifiées, qui incluent non seulement les contraintes de traction mécaniques, mais également les fiches de données de sécurité. Cela rend l'impression 3D beaucoup plus simple à utiliser dans notre travail quotidien.
Qu'est-ce que 2020 réserve à l'unité commerciale Powertrain Solutions de Bosch, en ce qui concerne la FA ?
Les 12 prochains mois seront clairement axés sur la réduction des coûts et l'amélioration de nos processus de fabrication en interne.
Nous ferons pression pour une plus grande disponibilité de l'impression 3D dans Powertrain Solutions. Cela signifie qu'il y aura plus de possibilités pour nos gens d'utiliser la FA pour la production de petites et moyennes séries.
impression en 3D
- Entretien avec un expert :professeur Neil Hopkinson, directeur de l'impression 3D chez Xaar
- Entretien avec un expert :Philip Cotton, fondateur de 3Dfilemarket.com
- Entretien avec un expert :Spencer Wright de pencerw.com et nTopology
- Entretien avec un expert :Dr Alvaro Goyanes de FabRx
- Comment l'impression 3D fait sa marque dans le monde de la médecine
- Entretien d'experts :Guillaume de Calan, PDG de Nanoe, sur l'avenir de l'impression 3D céramique
- Entretien d'experts :John Kawola, président d'Ultimaker, sur l'avenir de l'impression 3D
- Comment Ford Motor Company innove l'impression 3D pour l'industrie automobile :entretien d'expert avec Harold Sears
- Entretien d'experts :Philip DeSimone, cofondateur de Carbon, sur la transition vers une production à haut volume avec l'impression 3D