Entretien avec un expert :Spencer Wright de pencerw.com et nTopology
Presque toutes les personnes impliquées dans le monde de la fabrication auront parcouru le blog ou le bulletin de fabrication de Spencer Wright à un moment donné. Spencer est un expert de longue date des workflows pour la fabrication additive métallique et responsable de la recherche et des partenariats chez nTopology. Spencer a eu la gentillesse de s'asseoir avec RP Platform pour discuter de son expérience dans la fabrication additive et conventionnelle, son travail actuel de conception de flux de travail optimisés et la façon dont il envisage l'évolution du domaine dans un avenir proche.
Comment vous êtes-vous intéressé à l'impression 3D ?
Je me suis intéressé à l'impression sur métal juste parce que ça sonnait bien !
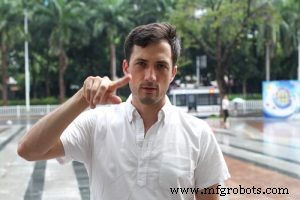
Mon expérience est dans la fabrication traditionnelle. Je suis chef de projet, chef de produit, un concepteur mécanique assez décent… J'ai construit des cadres de vélo sur mesure pendant plusieurs années. Après cela, j'ai travaillé dans un atelier de prototypage où nous développions des ensembles électromécaniques, j'ai donc acquis une certaine expérience dans la conception de systèmes embarqués.
J'ai déménagé à New York en 2012 et je prenais du recul et je réfléchissais à ce sur quoi je voulais me concentrer, tout en continuant à travailler sur des produits fabriqués de manière conventionnelle. Mais je cherchais quelque chose d'un peu différent. À l'époque, Makerbot et Shapeways étaient très importants sur la scène hardware de New York. Ce sont deux entreprises vraiment intéressantes, mais ayant une formation en mécanique – des choses structurelles et fonctionnelles – je suis devenue curieuse et j'ai entendu parler de différentes technologies d'impression sur métal. C'était à peu près au même moment où GE a acquis Morris, qui a fait sensation ici aux États-Unis. Je me suis lié d'amitié avec un groupe de personnes qui travaillaient dans une entreprise de stratégie appelée Undercurrent, qui travaillait beaucoup avec GE à l'époque, et j'ai fini par les rejoindre à temps plein.
C'est grâce à ce travail que j'ai pris conscience de la fusion sur lit de poudre métallique. Il y avait beaucoup de marketing sur la façon dont l'impression 3D allait changer X, Y et Z, mais j'ai pensé « Mettons un peu de contexte ici ». Nous avons des processus de fabrication extrêmement stables. Nous avons l'extrusion, nous avons le moulage, nous avons le forgeage, nous avons l'usinage… Ce sont des industries de plusieurs milliards de dollars. Comment l'impression sur métal se compare-t-elle à eux ?
J'ai donc commencé à y réfléchir et j'ai découvert que ces imprimantes coûtaient environ 1 million de dollars, ce qui semblait être beaucoup d'argent par rapport à une usine CNC. La question était donc :« Que peuvent-ils imprimer ? » Les plates-formes de construction avaient à peu près la taille d'une boîte à pain, alors qu'est-ce qu'une pièce de grande valeur qui tient dans une boîte à pain et qui pourrait bénéficier d'être légère ou d'avoir des éléments de conception intéressants ?
Aujourd'hui, la majeure partie de l'industrie de l'impression sur métal concerne les pièces pour l'aérospatiale, les implants médicaux ou le pétrole et le gaz, mais la réponse que j'ai trouvée était les pièces de vélo. C'est en fait une excellente industrie, car les gens paieront beaucoup d'argent pour quelque chose qui est juste un peu plus léger ou qui s'adapte un peu mieux. Si vous pouvez imprimer une pièce qui a l'air vraiment unique, qui est clairement futuriste, les gens aiment ça.
Je ne connaissais rien à la technologie, mais je savais comment concevoir des pièces, je savais comment trouver des pièces et je savais comment poser des questions. J'ai donc utilisé ces trois compétences (et le fait que j'avais un blog et une newsletter, ce qui était un gros trou sur le marché) et j'ai continué à y travailler. Je concevais et imprimais des pièces, puis j'écrivais à ce sujet, et c'est devenu une chose. Alors que je travaillais sur des trucs, j'ai commencé à recevoir de plus en plus d'appels à l'improviste de la part de gens d'entreprises comme Siemens et Philips, qui sont bien meilleurs que moi dans ce domaine. Cela m'a permis de faire entendre ma voix et d'avoir accès aux personnes de ces entreprises, afin que je puisse poser des questions et découvrir ce qu'elles traversaient.
À cette époque, j'ai fini par chercher quelque chose d'un peu différent dans ma carrière. J'ai décidé de me concentrer à temps plein sur les workflows de fabrication et de conception, alors maintenant je travaille chez nTopology, qui fabrique des logiciels de conception pour l'impression 3D industrielle. La plupart de ce que je fais est de déterminer comment notre logiciel s'intègre dans le reste de la chaîne d'outils. Comment suivre les flux de travail de nos clients tout au long de ce cycle et améliorer cette expérience ?
Il semble que votre expérience dans la fabrication traditionnelle signifie que vous abordez l'impression 3D d'une manière beaucoup plus organique que la plupart des gens :en commençant par un problème et en identifiant l'impression 3D comme le bon outil pour le résoudre. Êtes-vous d'accord avec cela ?
Ouais absolument. Je noterai qu'en même temps, mon intérêt est d'utiliser la bonne technologie pour le travail. Je suis constamment en train de bricoler des projets de design. J'en imprime certains, mais j'en CNC aussi certains. Je reçois des e-mails chaque semaine pour me dire qu'ils ont une idée d'entreprise et qu'ils veulent l'imprimer en 3D. Ma question est toujours « Pourquoi voulez-vous l'imprimer ? »
C'est vraiment une chose unique à propos de l'impression aujourd'hui, et je pense que la presse technique n'a peut-être pas fait un excellent travail pour établir pourquoi quelqu'un voudrait un jour une pièce imprimée. Il y a beaucoup d'histoires qui disent "Nous allons imprimer X et ce sera génial", mais je pense que la presse n'a pas été douée pour se demander en quoi cela serait bénéfique pour qui que ce soit. Quand je cherche quelque chose, je me fiche de savoir s'il a été imprimé. Les consommateurs ne se soucient pas de savoir si les choses sont imprimées et les entreprises s'en fichent certainement. Ce qui les intéresse, c'est de savoir si ce produit est plus performant, coûte moins cher ou est plus facilement disponible.
L'essentiel est que pour la grande majorité des pièces, l'impression n'est pas une bonne solution. Pour quelque chose qui doit être plus léger, c'est le cas, car vous pouvez intégrer des passages internes et simplifier l'assemblage. Ce sont des avantages réels. Pour moi, il s'agit de déterminer ces applications et les heuristiques que nous pouvons utiliser pour examiner une industrie et déterminer si ce sera un bon pari pour l'impression.
Mon conseil aux gens est de ne pas essayer de transformer votre application en impression. Il y a vraiment de bonnes choses pour l'impression et nous devrions nous concentrer sur celles-ci.
Quels seraient de bons exemples de ceux récemment ?
Nous travaillons dans quelques industries primaires. Dans toutes ces différentes industries, nous concevons des structures en treillis [légères] qui ont les propriétés mécaniques exactes que nos clients souhaitent.
Le plus important est l'aérospatiale — fusées et vaisseaux spatiaux — où l'environnement réglementaire est très compliqué. Il y a des questions importantes sur la façon dont vous inspectez les pièces et assurez-vous qu'elles sont toujours en bon état après X heures de vol, par exemple. L'aérospatiale a les exigences les plus strictes, donc si vous pouvez y répondre, vous pouvez généralement répondre aux besoins d'autres industries !
Nous sommes également très présents dans le domaine des implants médicaux, où les besoins de conception sont très différents, mais restent très réglementés. Nous travaillons également avec de nombreuses entreprises de technologie grand public, qui fabriquent des pièces qui absorbent l'énergie d'une manière particulière. Les entreprises de chaussures en parlent très publiquement, mais il existe d'autres entreprises de vêtements de sport qui envisagent d'imprimer des choses comme le rembourrage. Lorsque le corps d'une personne entre en collision avec quelque chose, vous voulez absorber cette énergie afin qu'elle ne soit pas transférée à ses os. La mousse convient à cela, mais vous pouvez utiliser différentes structures pour dissiper l'énergie vers l'extérieur, plutôt qu'à travers le coussin.
Pensez-vous qu'il y a beaucoup de courbe d'apprentissage en termes de flux de travail des entreprises, en particulier lorsque plusieurs plates-formes logicielles sont impliquées ?
Ceux-ci sont assez compliqués. Il y a des moments où je me retrouve à exécuter pour 50 000 $ de logiciels d'ingénierie sur mon ordinateur en même temps ! La bonne nouvelle est que peu importe ce sur quoi vous travaillez, qu'il s'agisse de pièces de fusée ou de chaussures, le calibre des logiciels que nous voyons est généralement assez similaire. Il existe une demi-douzaine de programmes de CAO que nos clients utilisent généralement, puis il existe une poignée de packages d'analyse et de plates-formes logicielles de fabrication différents.
Bien qu'il existe des différences, les exigences globales sont très similaires. Ce sont des sociétés d'ingénierie sérieuses avec des besoins sérieux, vous devez donc maintenir la traçabilité, vous devez respecter l'environnement réglementaire, vous devez avoir de la documentation et vous devez pouvoir retracer les résultats d'analyse, ce qui peut être délicat.
La réalité est que si le monde des logiciels d'ingénierie est relativement mature, ce n'est pas le cas des logiciels de fabrication. Les packages utilisés par les entreprises (principalement Autodesk Netfabb et Materialise Magics) n'existent pas depuis si longtemps, dans le grand schéma des choses. Chaque année, ils se mettent à jour avec des différences assez importantes. De plus, vous avez des formats de fichiers qui changent constamment, donc ça peut devenir compliqué.
Que voyez-vous comme réponse en termes de rationalisation de tout cela ?
À l'heure actuelle, notre objectif est de rendre ce processus aussi fluide que possible. En fin de compte, le domaine dans lequel nous pouvons le plus affecter cela se trouve dans notre logiciel, Element. Nous pouvons rendre cette expérience formidable. Dans cette industrie, c'est difficile. Quels sont les formats de fichiers que vous allez utiliser pour passer de la CAO à Element, à votre processeur de construction ? À l'heure actuelle, c'est STL, qui est un gâchis de format de fichier.
Les structures en treillis peuvent avoir des millions de poutres. Lorsque vous utilisez STL, vous décrivez la surface de cette structure avec des triangles. Pour chaque faisceau, vous allez avoir un minimum de peut-être dix triangles, bien que dans la plupart des cas, nous trouvons qu'il est préférable d'utiliser au moins 50 triangles. Avec un million de faisceaux, cela signifie des tailles de fichiers tout simplement insensées.
Il n'est tout simplement pas pratique de décrire la géométrie de cette manière, et donc à l'intérieur d'Element, nous n'utilisons pas du tout de géométrie tesselée. Nous utilisons une structure de graphe, de sorte que chaque faisceau passe d'un nœud à un autre nœud. Chaque nœud a un emplacement X, Y et Z, et un rayon lui est assigné. Les poutres relient ensuite ces nœuds. Avec une quantité d'informations relativement faible, nous pouvons montrer des conceptions qui ont beaucoup, beaucoup de faisceaux. Nous créons des conceptions dans notre logiciel de cette façon, puis nous utilisons une spécification de fichier open source qui vous permet de les exporter et d'utiliser vos propres trancheurs et outils d'orientation.
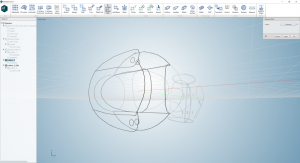
Nous travaillons à l'intégration dans la norme de fichier 3MF. Le but est d'avoir une présentation de fichier beaucoup plus simple pour communiquer des treillis. À tout le moins, cela signifie que si vous devez envoyer un fichier par courrier électronique, vous n'attendez pas 20 minutes pour qu'il soit téléchargé. Le transfert de fichiers est plus facile et le rendu est beaucoup plus facile, car la géométrie simplifiée signifie que votre processeur ne fonctionne pas aussi dur. Nous pouvons également découper cette représentation très bien. Nous sommes également en mesure d'importer cela directement dans votre logiciel FEA, afin que nous puissions exécuter une analyse de faisceau - ce qui est beaucoup plus facile que d'utiliser des éléments solides.
Comment voyez-vous l'adoption de ce nouveau format de fichier ?
Honnêtement, je ne suis pas si inquiet à ce sujet. Nous avons déjà vu des à-coups dans les formats de fichiers, mais pour nous, ce format présente un avantage si évident que je soupçonne qu'il évoluera très rapidement. La plupart des formats de fichiers d'impression utilisent encore des triangles, ce qui signifie que la représentation géométrique existe toutes dans le même paradigme. 3MF a également une géométrie triangulée (c'est un meilleur format pour un certain nombre d'autres raisons) mais nous ajoutons une représentation complètement différente en plus de cela, afin que nous puissions représenter la même pièce avec un fichier beaucoup plus petit. Je soupçonne que les avantages de cela vont l'emporter de loin sur les difficultés.
Considérez-vous la personnalisation pour les besoins spécifiques des clients comme un facteur clé du succès d'un logiciel pour la FA ?
Oui et non. Nous sommes une entreprise de produits. Nous vendons un produit que nous avons conçu pour les utilisateurs les plus exigeants et cherchons à en faire la meilleure version possible. Avoir une approche cohérente des problèmes rend l'expérience considérablement meilleure. Pour les applications de CAO plus marginales, ce qui arrive souvent, c'est qu'un client dit « Nous aimons les fonctionnalités, mais nous souhaitons vraiment qu'il y ait des menus contextuels partout ». La société de CAO veut vraiment la vente, alors elle leur donne les menus contextuels. En quelques mois, vous obtenez des menus contextuels partout, ils fonctionnent bien et ils obtiennent la grande vente.
Dans un an, quelqu'un d'autre arrive et dit « Nous aimons votre logiciel, mais nous voulons vraiment un meilleur système de dossiers de commandes, car les menus contextuels ne fonctionnent pas vraiment pour nos ingénieurs ». La société de CAO consacre six mois à cela, et vous avez ensuite deux façons de faire exactement la même chose. Vous vous retrouvez avec un logiciel schizophrène.
Nous avons tendance à préférer avoir une seule interaction. Toute nouvelle fonctionnalité que nous introduisons sera traitée de la même manière et sera cohérente dans l'ensemble du flux de travail. Nous écoutons ce dont nos clients ont vraiment besoin et proposons quelque chose qui s'intègre dans notre cadre de gestion des interactions, mais qui correspond également à ces besoins.
Mais en plus de cela, le besoin de flexibilité dans les flux de travail est définitivement un point. Avec le nouveau format de fichier, nous l'avons écrit de manière à ce qu'il soit très facile pour quiconque de le saisir, de le manipuler et de comprendre ce qui se passe.
Qu'en est-il de la rationalisation des workflows AM ? Quels moyens avez-vous trouvés pour rendre les processus globaux plus stricts et réduire les déconnexions ?
C'est dur. En fin de compte, lorsque vous regardez nos utilisateurs de l'aérospatiale, vous rebondissez constamment entre différentes choses. Même avec une pièce relativement simple, vous vous retrouvez avec un numéro de pièce, puis la version 2, la version 3 etc. et ça explose en quelque sorte. Une chose que nous avons faite est d'autoriser plusieurs versions du même design dans un seul fichier. Vous pouvez débourser dans différentes directions, mais gardez tout cela dans le même fichier réel, ce qui aide quelque peu.
En fin de compte, cependant, l'interopérabilité est plus importante que la rationalisation. Nous avons beaucoup réfléchi à la création d'une version plus simple d'Element en tant que plug-in vers d'autres logiciels de CAO, mais nous travaillons ensuite avec le noyau géométrique et l'interface utilisateur de quelqu'un d'autre. Adapter ces choses est plus difficile que de le faire dans votre propre logiciel. De plus, choisissez-vous le logiciel de CAO le plus populaire et construisez-vous pour cela ? Choisissez-vous celui que vos clients utilisent ?
Donc, pour l'instant, nous avons choisi de maintenir notre flexibilité. Vous importez dans notre logiciel, mais nous rendrons ce processus aussi simple que possible. Nous savons que si nous gardons la plupart du travail dans notre logiciel, nous pouvons garantir une bonne expérience utilisateur.
En termes plus généraux, comment voyez-vous tout cela évoluer ?
Je suis ravi que l'impression sur métal devienne plus mature. Les humains ont un siècle de coupe de métal à leur actif. Nous avons beaucoup fait cela et nous sommes bons dans ce domaine. C'est reproductible et fiable, donc je n'ai pas besoin de savoir sur quelle machine une pièce est fabriquée. Avec l'impression sur métal, c'est complètement différent. Ce n'est pas aussi reproductible, donc si je vais chez plusieurs fabricants différents avec le même fichier, ils le construiront de différentes manières et nous obtiendrons un résultat différent. J'entends des gens dire que nous avons besoin de plus de matériel ou de vitesse, et ces choses sont importantes, mais ce que je veux vraiment, c'est la maturité. C'est ce qui me passionne vraiment.
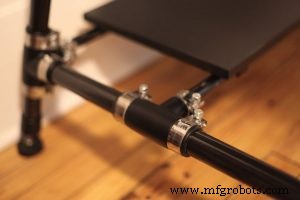
Nous avons ce gros effort pour intégrer des contraintes de conception dans notre logiciel. Si vous concevez quelque chose dans Photoshop, il a une palette de couleurs que vous appliquez à votre conception. Ils ne vous laissent pas choisir des couleurs comme l'ultraviolet, parce que vous ne pouvez pas les voir, donc ça ne sert à rien de concevoir quelque chose de cette façon ! Avec un logiciel de CAO, il est facile de concevoir des choses qui ne sont pas manufacturables. Notre objectif principal est d'aider nos utilisateurs à comprendre ce qui est manufacturable et ce qui ne l'est pas et d'intégrer cette intelligence dans le logiciel, afin qu'ils obtiennent des commentaires en temps réel sur la façon dont leur conception va s'imprimer.
C'est vraiment difficile pour nous de le faire dans un monde où non seulement les machines impriment les pièces différemment, mais les fabricants ne publient pas de spécifications sur ce qui est imprimable. Ce que je veux vraiment, c'est que les fabricants de machines publient des API qui vous donnent des commentaires sur l'imprimabilité et indiquent où se trouvent les problèmes.
En conclusion, que voyez-vous comme le « prochain grand événement » au cours des cinq prochaines années ?
Ce n'est pas une réponse sexy, mais je recherche un processus plus fiable, plus reproductible et plus stable. Ou à tout le moins, je veux un flux où les gens peuvent faire des choses folles, mais qui offre des temps de construction fiables pour fournir une base solide pour cela.
Je pense qu'il est bon de voir davantage de fabricants de machines développer davantage d'intégration avec les fabricants de pièces détachées et ouvrir leurs propres bureaux de service. Ils vont en apprendre davantage sur l'impression de pièces et, espérons-le, alimenteront leurs machines avec cette intelligence. Dans le même temps, nous constatons que les fabricants de machines sont plus étroitement associés aux logiciels.
Il y a une chose appelée la loi de Conway qui dit que les entreprises ont tendance à construire des systèmes qui sont un fac-similé de leur propre structure organisationnelle. Par exemple, si vous avez une pièce avec une carte de circuit imprimé qui est attachée au moulage par injection et que l'équipe d'ingénierie mécanique se trouve dans un bâtiment différent de l'équipe d'ingénierie des systèmes embarqués, alors le PCB va tomber de la pièce moulée par injection. .
Le corollaire raisonnable est que si vous voulez un workflow de bout en bout transparent, vous devez intégrer plus étroitement ces équipes. Faites-les travailler dans le même bâtiment et se heurter à la fontaine à eau ! J'ai hâte de voir davantage d'entreprises réunissant ces différents rôles.
www.pencerw.com
impression en 3D
- Entretien avec un expert :professeur Neil Hopkinson, directeur de l'impression 3D chez Xaar
- Entretien avec un expert :Philip Cotton, fondateur de 3Dfilemarket.com
- Entretien avec un expert :Dr Alvaro Goyanes de FabRx
- Entretien avec un expert :Dr Bastian Rapp de NeptunLab
- Entretien avec un expert :Ibraheem Khadar de Markforged
- Jigs and Fixtures :6 façons d'améliorer l'efficacité de la production avec l'impression 3D
- Entretien d'experts :Duncan McCallum, PDG de Digital Alloys, sur l'impression Joule et l'avenir de l'impression 3D sur métal
- Entretien d'experts :Guillaume de Calan, PDG de Nanoe, sur l'avenir de l'impression 3D céramique
- Entretien d'experts :John Kawola, président d'Ultimaker, sur l'avenir de l'impression 3D