Entretien d'experts :Pat Warner, spécialiste de la fabrication additive de Renault Formula One Team
Pat Warner est ADM Manager chez Renault Sport Formula One Team - un spécialiste interne de la fabrication additive, travaillant à fournir des composants imprimés de première classe à des fins de prototypage et de production. Ayant été profondément impliqué dans la fabrication additive au sein de la F1 depuis plus de 19 ans, Pat a été témoin d'un certain nombre de développements clés dans la technologie et ses applications, dont il a eu la gentillesse de discuter avec AMFG dans l'interview ci-dessous :
AMFG :Comment avez-vous commencé à vous impliquer dans la fabrication additive ?
Pat :J'étais à l'origine un machiniste CNC dans l'équipe de Formule Benetton de l'époque et j'ai rejoint le département FAO en 1997. Nous avons acheté notre première machine SLA en 98, mais nous ne savions pas vraiment quoi en faire. La machine a été placée dans une pièce adjacente à l'atelier d'usinage et la tâche de programmation a été confiée au groupe CAM. En 2000, nous avions trouvé suffisamment d'applications pour PX la machine SLA pour deux modèles plus récents et plus rapides. En 2002, nous en avons acheté deux autres. En 2003, nous avons ajouté le frittage laser au département et nous nous sommes progressivement étendus depuis au département existant de neuf machines.
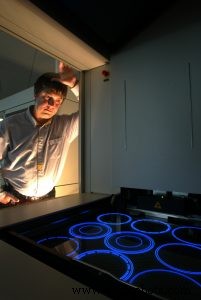
AMFG :Quelles ont été les plus belles réussites de la FA dont vous avez été témoin pendant votre séjour chez Renault ?
Pat :Il y en a eu tellement au fil des ans.
Nous prototypons chaque nouveau composant de la voiture et l'assemblons pour la fonction/l'ajustement. Ce n'est pas nouveau dans le monde de l'additif, mais cela signifie que nous pouvons trouver nos erreurs très rapidement. L'emballage d'une voiture de F1 moderne est un défi pour l'équipe de conception, car laisser de l'espace aux mécaniciens pour accéder aux pièces de la voiture est une chose difficile à réaliser en regardant un écran.
Nous fabriquons nos propres modèles de moulage de précision pour nos composants structurels en titane, tels que le boîtier de la boîte de vitesses. Nous avons consacré beaucoup de temps et d'efforts à affiner ce processus et nous nous retrouvons généralement avec la fonderie que nous utilisons nous demandant de nous acheter des modèles (à ce stade, nous ne fabriquons que des composants pour l'équipe).
La fabrication additive a sans aucun doute accéléré le rythme de développement des souffleries de F1. Lorsque nous exploitions des heures de soufflerie illimitées, nous produisions plus de 600 pièces par semaine, juste pour alimenter le tunnel. La quantité de ressources de fabrication conventionnelles nécessaires pour atteindre le même objectif serait immense.
Des gabarits et des montages rapides ont aidé à la production de la voiture et aux modifications de dernière minute sur le circuit. Trouver un problème le vendredi, fabriquer des articles de remplacement et les livrer à la piste à temps pour être montés pour les qualifications s'est produit à plusieurs reprises.
Bien sûr, nous avons aussi eu nos petits désastres, mais ils aident tous au processus d'apprentissage.
AMFG :Quels sont les principaux défis que vous avez rencontrés en ce qui concerne la FA en tant qu'outil à la fois pour le prototypage et la production ?
Pat :Encore une fois, il y en a eu tellement.
Lorsque nous avons commencé avec cela, la longévité de la pièce était un énorme problème, les matériaux SLA étaient très fragiles et ne supportaient pas bien l'humidité. Si vous pouviez garder une pièce sur votre bureau pendant une semaine sans que personne ne la casse, elle se déformerait en absorbant l'humidité de l'air. Le développement de matériaux a résolu ces problèmes et a apporté de grandes améliorations en cours de route.
Lorsque nous avons commencé à acheter des composants auprès de fournisseurs externes, nous avons découvert que vous obteniez rarement la même pièce deux fois, même si elle provenait de la même construction, dans certains cas. Cela nous a encouragés à apporter plus en interne, à passer plus de temps à comprendre l'équipement et les matériaux et à affiner nos processus. En 2004, nous nous sommes associés à Boeing. Ce partenariat nous a aidés dans cette voie et nous a permis de mettre plus de composants sur nos véhicules. Nous avons développé des matériaux spécifiquement pour nos besoins, qui sont disponibles dans le commerce (les règlements de la FIA imposent qu'ils doivent l'être) et sont utilisés ailleurs.
L'éducation a également été un défi, bien que la technologie existe depuis un certain temps maintenant, son adoption dans la fabrication traditionnelle a été progressive, tout comme l'éducation. En conséquence, nous obtenons toujours de nouveaux concepteurs qui n'ont jamais été exposés à la fabrication additive.
AMFG :Quelles nouvelles innovations aimeriez-vous le plus voir en termes de plates-formes et de matériaux d'impression ?
Pat :Les deux domaines ont parcouru un long chemin au cours des 19 années où j'ai été impliqué, mais il y a encore de la marge pour que la technologie mûrisse. Nous devons encore prêter beaucoup d'attention à nos processus pour obtenir les résultats dont nous avons besoin et nous constatons toujours des incohérences dans certains des composants que nous achetons. Certaines de ces incohérences pourraient concerner l'équipement que nous utilisons, mais de bonnes mesures ont été prises récemment. dans ce domaine, certaines sont dans la manière dont les fournisseurs utilisent lesdits équipements et recyclent les matériaux. Cependant, tout ne concerne pas les plates-formes et les matériaux ; nous avons également besoin de meilleurs outils de conception pour la FA.
Nous avons tous vu les structures creuses légères avec un treillis à l'intérieur. Cela devrait être parfait pour le sport automobile et l'aérospatiale, mais en réalité, nous ne sommes pas en mesure de prédire suffisamment bien les mécanismes de résistance, de rigidité et de défaillance de ces composants pour pouvoir les utiliser à leur plein potentiel.
AMFG :Comment voyez-vous l'utilisation de la FA évoluer au sein de la F1 dans les prochaines années ?
Pat :Nous trouvons de nouvelles applications tout le temps. Au fur et à mesure que la taille de la boîte à outils augmente, le nombre d'applications augmentera également.
Les métaux font d'énormes progrès chaque année, tout comme les polymères à haute température. Au fur et à mesure qu'ils progresseront et que nous comprendrons mieux comment les utiliser, nous pourrons obtenir beaucoup plus des pièces AM.
C'est une période assez excitante pour AM, elle gagne beaucoup d'attention et de financement. Cela ne peut être que bénéfique pour l'ensemble de l'industrie, car il reste encore du chemin à parcourir avant de pouvoir remettre complètement en question la fabrication conventionnelle.
www.renaultsport.com
impression en 3D
- Repenser le processus d'intégration logicielle pour les opérations de fabrication additive
- Entretien d'experts :Felix Ewald, PDG de DyeMansion
- Entretien avec un expert :Ibraheem Khadar de Markforged
- Entretien :Dominic Parsonson de Fuji Xerox Australie
- Entretien d'experts :James Hinebaugh d'Expanse Microtechnologies
- Entretien d'experts :PDG de PostProcess Technologies sur la résolution du goulot d'étranglement du post-traitement pour la fabrication additive
- Entretien d'experts :Doug Hedges, président de Sintavia, sur la réalisation de la production en série avec l'impression 3D en métal
- Entretien d'experts :Brian Alexander de Solvay sur le développement de polymères hautes performances pour l'impression 3D
- Fabrication additive dans l'aérospatiale