Entretien d'experts :Joseph Crabtree, PDG des technologies de fabrication additive, explique pourquoi le post-traitement est essentiel pour l'impression 3D
Le post-traitement a souvent été décrit comme le "sale petit secret" de l'impression 3D. Une partie nécessaire, mais très manuelle et à forte intensité de main-d'œuvre du processus d'impression 3D, le post-traitement reste un énorme défi pour les entreprises qui cherchent à étendre leurs opérations de fabrication additive (AM). Cependant, tout cela pourrait changer, grâce aux progrès de l'automatisation du post-traitement.
Dans l'interview d'experts de cette semaine, nous sommes rejoints par Joseph Crabtree, PDG d'Additive Manufacturing Technologies (AMT), une société basée au Royaume-Uni qui développe des solutions de post-traitement automatisées. Avec Joseph, nous discutons de l'importance du post-traitement, du fonctionnement des technologies de post-traitement d'AMT et de ce que l'avenir réserve à l'industrie.
Pouvez-vous me parler d'AMT Technologies ?
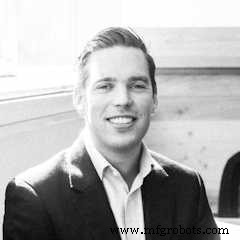
Nous avons été formés en 2017, à Sheffield au Royaume-Uni, où nos installations comprennent les opérations de R&D, le support technique, les ventes et le développement d'applications.
Nous avons une usine de fabrication en propriété exclusive en Hongrie, où nous réalisons tous nos travaux d'ingénierie, de conception et de fabrication. C'est une proposition de vente assez unique pour nous - le fait que nous réalisons toute la conception et la fabrication en interne. Nous venons d'ouvrir une installation de 20 000 pieds carrés à Austin, au Texas, qui va desservir les marchés américains, et nous venons également d'employer notre premier employé dans la région APAC. Nous nous développons à l'échelle mondiale et très rapidement.
L'objectif de l'entreprise est de véritablement permettre la FA industrielle. Ainsi, jusqu'à présent, les entreprises utilisaient régulièrement la FA pour des prototypes avec une transition vers des applications de production à faible volume, mais en réalité, ce que nous essayons de faire, c'est d'aider à faire évoluer la technologie FA des applications à faible volume à des capacités industrielles complètes. Nous voulons faire de l'impression 3D une alternative viable à la fabrication traditionnelle.
Pour être honnête, en tant qu'industrie, nous en sommes loin. Beaucoup de mots à la mode sont utilisés, mais en réalité, le plus gros problème aujourd'hui concerne les imprimantes 3D. Tout le monde s'est concentré sur le développement d'imprimantes plus grandes, plus rapides et de meilleure qualité. Ce n'est qu'une partie du puzzle. Les gens commencent à se concentrer davantage sur les documents imprimés, pour réduire les coûts et augmenter la disponibilité des matériaux.
Mais le défi reste que les pièces qui sortent des imprimantes 3D à la fin du processus ne sont souvent pas adaptées aux pièces d'utilisation finale.
Et lorsque nous parlons de pièces d'utilisation finale, nous parlons de pièces qui pourraient être utilisées dans les opérations chirurgicales dans l'industrie médicale, ou dans les chaussures, les applications intérieures aérospatiales, l'automobile sous le capot applications, ou dans les applications spatiales, par exemple. Aucun de ces exemples ne peut être utilisé directement à partir d'une imprimante 3D, sauf si vous les post-traitez ou les terminiez.
Et cette partie a été négligée jusqu'à présent parce que l'accent a été mis sur les imprimantes 3D. Ce n'était pas tellement un problème pour produire de faibles volumes de pièces. Le compromis ici était que si la finition manuelle des pièces augmentait les coûts, les marges sur ces pièces étaient plus élevées.
Maintenant que les entreprises évaluent la FA pour des applications de production, à des volumes plus élevés, la marge est absolument critique. Lorsque le post-traitement peut représenter jusqu'à 60 % du coût d'une pièce, il peut devenir prohibitif et il faut faire quelque chose.
Notre entreprise se concentre sur la chaîne de post-traitement, et ce nous voulons dire par là que tout est après l'impression. Ainsi, dans le cas de la FA à base de poudre, cela inclut l'étape de dépoudrage et la modification de surface de la pièce, ce qui signifie lisser, sceller, colorer et améliorer les performances d'une pièce.
La dernière étape est l'inspection et le contrôle qualité. AMT regroupe toutes ces étapes de la chaîne de processus avec une solution automatisée de bout en bout. C'est une approche agnostique de la technologie, dans la mesure où nous travaillons avec toutes les technologies d'impression 3D.
Nous nous concentrons également sur les polymères et, en particulier, les polymères thermoplastiques, qui sont essentiellement des technologies basées sur le lit de poudre et l'extrusion. Plus de 95 polymères sont validés pour nos systèmes. Et en réalité, notre objectif est de fournir ce système d'automatisation de bout en bout à la pièce.
Maintenant, grâce à l'investissement de DSM Venturing and Foresight Group, Williams Advanced Engineering, nous pouvons réellement terminer ce que nous appeler « le polymère pour séparer l'écosystème ». Donc, essentiellement, ce que nous faisons, c'est considérer l'ensemble de l'écosystème pour la première fois. Nous examinons les matériaux, nous examinons comment concevoir les matériaux pour l'impression 3D, puis optimisons le processus d'impression en fonction de la sélection des matériaux.
Fondamentalement, ce que nous faisons est la science des matériaux, combinée à l'ingénierie mécanique et à l'automatisation. L'étape de post-traitement permet d'adapter les propriétés mécaniques de la pièce imprimée, de sorte que les propriétés mécaniques globales sont améliorées par rapport à la pièce qui sort directement de la machine.
La combinaison de tout cela est absolument essentielle pour nous, et c'est pourquoi tous nos systèmes sont industriels, destinés spécifiquement à l'utilisateur final industriel.
Quels sont les défis auxquels les entreprises sont actuellement confrontées en ce qui concerne le post-traitement en particulier ?
Le plus gros problème est le manque de sensibilisation. Ainsi, jusqu'à assez récemment, non seulement les entreprises ne comprenaient pas l'impression 3D, mais elles ne savaient pas non plus qu'une fois que vous obtenez une imprimante 3D, vous devez effectuer un post-traitement de la pièce.
C'est une situation très difficile car les fabricants d'imprimantes 3D ne vont jamais vous vendre une imprimante et vous diront que le rendu initial est de mauvaise qualité et, par conséquent, vous allez devoir acheter une pièce supplémentaire de l'équipement.
Ils n'ont jamais parlé de post-traitement, mais le temps et les coûts du post-traitement éclipsent de loin tous les avantages obtenus grâce à des vitesses d'impression accrues. Ce que nous espérons permettre aux fabricants d'imprimantes d'obtenir une pénétration plus poussée du marché, leur permettant d'offrir une solution complète à leurs clients.
C'est quelque chose dont personne ne veut jamais vraiment parler. Cela signifie que l'éducation est un défi à cet égard, en particulier pour les clients qui entrent sur le marché maintenant.
En conséquence, les entreprises qui achètent une imprimante 3D pour la première fois peuvent en savoir très peu sur l'impression 3D et sont désormais confrontées au défi du post-traitement. Par conséquent, il s'agit d'éduquer les utilisateurs finaux et de leur montrer qu'il ne s'agit pas d'une série d'articles de machines indépendants discrets que vous devez acheter pour faire de ce processus, disons, une solution à un bouton, comme peut-être certaines des vidéos promotionnelles vous le feraient. pense.
Le deuxième grand aspect est qu'il n'y a aucune autre technologie sur le marché, à part la nôtre, qui soit vraiment automatisée. Oui, il existe des technologies de post-traitement mais, en général, ce sont des remaniements de technologies très connues. Aucun d'entre eux n'est numérique.
Actuellement, vous devez être compétent dans toutes ces opérations nuancées qui nécessitent cet « art noir » pour fonctionner. C'est donc vraiment un défi de taille. Et, pour le moment, il n'y a pas d'options de post-traitement vraiment innovantes, ainsi qu'une incitation numérique.
Le plus gros défi, en termes de technologie, que nous ayons vu, est dépoussiérant. Personne n'a mis au point une solution de déballage et de dépoussiérage véritablement automatisée qui ne nécessite aucune intervention humaine. C'est un vrai défi. Ce n'est pas seulement un défi de dépoudrage et d'automatisation, c'est un défi d'apprentissage automatique, de tri automatique, et ce sont les défis communs que nous relevons.
Pensez-vous que nous arriverons au point où nous aurons une solution de dépoudrage entièrement automatisée ?
Nous avons des partenaires avec lesquels nous travaillons pour développer de vraies solutions pour cela. C'est un gros déblocage pour eux, car encore une fois, si vous avez votre lit de poudre et que vous devez retirer vos pièces, il n'y a actuellement pas d'autre moyen de le faire que manuellement. Même les solutions traditionnelles de culbutage nécessitent encore beaucoup d'interventions manuelles, car une chose que les humains sont très bons, ce sont les opérations délicates et difficiles :l'identification des choses (comme la poudre sur la pièce), l'élimination de ladite poudre sans détruire la pièce et le tri des pièces etc. Nous nous travaillons à l'automatisation de ces étapes afin d'améliorer les délais et les coûts.
Comment fonctionne votre technologie PostPro3D ?
PostPro3D est notre technologie de base. Il était basé sur la propriété intellectuelle sous licence de l'Université de Sheffield, puis développé avec une subvention Innovate UK. Il est en développement depuis environ 8 ans en termes de recherche fondamentale, puis de recherche industrielle.
Il s'agit d'un processus de lissage chimique à la vapeur qui utilise des produits chimiques exclusifs pour lisser la surface d'une pièce en polymère imprimée en 3D.
En lissant la surface, nous ne voulons pas seulement la rendre esthétique, nous concevons en fait la surface de la pièce. La solution chimique scelle la surface et élimine la porosité de la pièce. Il empêche également la pénétration d'eau ou de gaz et améliore réellement les propriétés mécaniques. Le résultat est une pièce qui présente un allongement à la rupture élevé et de meilleures propriétés de fatigue.
En plus de cela, il y a tous les matériaux élastomères que nous pouvons traiter, qui ne pourraient pas être traités même avec des méthodes mécaniques, par exemple. Le PostPro3D peut post-traiter des pièces imprimées à l'aide de polymères de haute technologie tels que l'ULTEM, les nylons, le TPU et le TPE, etc.
Le PostPro3D est la première machine dotée d'une technologie de modification de surface que nous avons mise sur le marché. Il s'agit d'un équipement industriel conçu pour les utilisateurs finaux industriels, avec une taille de chambre de traitement proche de 100 litres pour traiter des volumes de pièces plus importants.
Nous avons également sorti le PostPro3D Mini. C'est physiquement un tiers de la taille du PostPro3D, nettement moins cher mais utilisant la même technologie phare pour étendre l'utilisation aux instituts de recherche, aux petits bureaux de service et aux personnes qui peuvent n'avoir qu'une seule imprimante. Et c'est un prix approprié pour être accessible à ces personnes, afin qu'elles puissent ensuite essayer la technologie avant de s'engager dans quelque chose de plus important ou d'étendre les opérations.
L'avantage de notre processus est que toutes nos pièces et notre traitement ont a subi des tests de toxicité de cycle et est actuellement en cours d'approbation médicale par la FDA, etc. C'est donc vraiment important lorsque nous parlons d'applications d'utilisation finale industrielles réglementées.
De plus, nos technologies de coloration sont complémentaires à cette technologie. Nous possédons notre technologie unique et en instance de brevet sur la coloration, qui nous permet de colorer et de lisser une pièce en même temps, vous pouvez donc ajouter de la couleur tout en lissant. Cela ouvre donc également toute une série d'autres applications.
De l'autre côté, nous avons nos systèmes de dépoudrage que, comme je l'ai mentionné, nous testons actuellement avec certaines de nos sociétés partenaires de production. Ceux-ci nous permettent de déballer automatiquement le lit de poudre, de dépoudre et de retirer les pièces des systèmes AM à lit de poudre.
Finalement, nous devons tout lier ensemble. Nous avons des systèmes de métrologie, ou d'inspection, qui ont été développés, en collaboration avec l'Université de Nottingham, et les éléments intelligents se trouvent en fait dans les algorithmes et l'apprentissage automatique, pas dans le matériel. Ils sont donc peu coûteux, ce qui signifie que nous pouvons les utiliser conformément à nos systèmes et contrôler la qualité des pièces tout au long de nos processus.
Et puis la dernière partie est l'automatisation de bout en bout, que nous appelons notre système de fabrication numérique - ou DMS - qui nous permet d'automatiser l'ensemble du processus.
Vous avez mentionné avoir validé 95 polymères avec vos solutions. Envisagez-vous des pièces métalliques à l'avenir?
Grande question. Mon expérience est en fait dans la métallurgie. Je suis diplômé de l'Université de Sheffield dans le domaine de la fabrication additive métallique.
Mais, si le métal est ma formation, j'ai choisi les polymères, car ils sont plus faciles à manipuler. Le métal est un grand défi, en raison du type industriel des procédés requis.
Nous avons déposé des PI sur le post-traitement des métaux et nous avons développé des solutions pour les composants quasi-métalliques. Par exemple, la technologie de Desktop Metal est un processus basé sur l'extrusion dans un support en polymère, avec une pièce métallique clipsée à l'intérieur. Nous avons donc en fait une propriété intellectuelle et sommes capables, par exemple, de lisser les pièces Desktop Metal avant qu'elles ne soient frittées, et nous pouvons ensuite lisser la pièce non durcie. Au moment où il sort, vous avez une belle barre de métal lisse.
Qu'est-ce que votre récent cycle d'investissement signifie pour l'entreprise à l'avenir ?
C'est complètement transformateur. Nous sommes une entreprise génératrice de revenus depuis la première année de notre existence, ce qui est très important car cela signifie qu'il existe une excellente adéquation entre les produits et le marché. Nous ne développons donc pas des choses qui ne sont pas nécessaires.
Ce que ce financement nous permet de faire, c'est d'accélérer notre croissance mondiale. Cela nous permet de terminer notre usine à Austin et de nous développer correctement sur le marché APAC et en Europe.
Mais plus important encore, ce financement nous permet de rester agnostiques, contrairement à d'autres entreprises.
C'est parce que nous voulions rester agnostiques que nous avons choisi DSM comme entreprise de chimie des matériaux. Cela nous donne accès à toutes les expertises matériaux et chimie qui font leur renommée du côté de la fabrication traditionnelle et additive, mais, essentiellement, cela nous permet aussi de tendre vers un écosystème de FA industrielle complet qui ne peut que nous profiter.
Mais d'un autre côté, nous avons Foresight Group, Williams, qui est un VC d'un milliard de livres. Cela nous donne accès à toute leur chimie des matériaux, leur expertise en analyse, la provenance de l'ingénierie de la Formule 1 des 50 dernières années, ainsi que toutes les analyses de données, les coûts d'ingénierie, l'optimisation des produits, l'optimisation de la conception, etc. Enfin, Foresight Group nous donne accès à d'énormes VC alimente les marchés des capitaux.
De plus, à travers les canaux de vente, cela nous donne un réseau de vente, de marketing et de distribution potentiel, qui est prêt à fonctionner. Donc, cela accélère vraiment notre cheminement vers la mise à l'échelle.
Nous avons beaucoup parlé des défis liés au post-traitement et de la manière dont vous les abordez. En passant pour parler un peu plus généralement de l'impression 3D, quels sont certains des défis que vous voyez toujours dans l'industrie qui pourraient encore être des barrières potentielles à l'entrée ?
Pour nous, c'est encore une fois le même défi. Les entreprises qui souhaitent adopter l'impression 3D sont confrontées à tant de choix. Et il s'agit vraiment de briser le battage médiatique qui l'entoure. Il n’y a pas autant de battage publicitaire qu’il y en avait, mais il y en a encore beaucoup.
En outre, je pense toujours que l'un des plus grands défis est que pour de nombreuses entreprises, la technologie n'est tout simplement pas prête à parier. Par exemple, si vous achetez une machine CNC aujourd'hui, vous pourrez usiner des pièces demain et usiner des pièces de très haute qualité. De même, si vous achetez une presse à injecter et disposez d'un outil, vous pouvez faire de même. Je simplifie un peu, mais d'une manière générale, c'est un défi auquel l'industrie de la fabrication additive est confrontée.
Si vous achetez une imprimante 3D, le matériel, tout cela est considéré comme de l'équipement ; vous ne pouvez toujours pas faire des pièces de bonne qualité. Et je pense que c'est là le problème :on est encore loin d'en arriver à un procédé où l'on pourrait, par exemple, fabriquer un million de pièces.
Un parfait exemple est notre stand à Formnext. Nous construisons un peu plus de six mille cinq cents pièces individuelles imprimées en 3D, reliées par des composants en aluminium. La structure mesure 4 mètres sur 6 mètres sur 14 mètres. C'est une structure énorme. Et vous vous demandez soudain pourquoi personne ne l'a fait avant, et le problème est que pour 6000 composants identiques ou adaptés d'un point de vue répétabilité et reproductibilité, c'est juste très difficile à faire. Il faudrait un mois de développement pour arriver au point où vous avez un processus stable.
Donc vraiment, quand nous sommes près du point où les processus sont stables, où nous avons la répétabilité et la reproductibilité, c'est là que nous atteignons les processus industriels.
Une autre chose est que nous devons arrêter de considérer l'impression 3D comme un processus par lots. Considérez-le plutôt comme un processus continu, avec une chaîne de processus complète et une automatisation de bout en bout.
Je pense qu'une partie du problème est que beaucoup de gens utilisent l'impression 3D depuis trop longtemps, la regardant grandir. Cependant, nous assistons maintenant à une nouvelle révolution, dans laquelle les gens la considèrent vraiment comme une technologie industrielle, mais pour que cela fonctionne réellement, un changement de mentalité est nécessaire. Et c'est pourquoi notre entreprise est si chanceuse, car tout le monde n'est pas issu de l'impression 3D. Nous apportons donc une perspective très différente au processus.
Pouvez-vous nous dire comment vous construisez votre stand chez Formnext ?
Cette année, nous avons un stand de 86 mètres carrés, qui est construit presque comme une structure en treillis. Chaque nœud est une série de pièces imprimées en 3D interconnectées, et nous construisons la structure à partir de ces composants individuels qui forment des cubes, et les cubes forment la structure, qui mesure 4 mètres de haut. Mais le fait est qu'il est très léger. L'ensemble de la structure ne pèse pas plus de 120 kilogrammes.
Nous pensons que c'est la première fois que quelqu'un essaie de le faire. Sans post-traitement, il serait extrêmement difficile à réaliser. De toute évidence, nous utilisons nos joints filetés à tolérance, nos géométries internes complexes, etc. Et ce qui est essentiel ici, c'est que sans la technologie que nous avons développée, nous n'aurions pas pu produire cela. Nous aurions pu imprimer les pièces, mais nous n'aurions pas pu les finir et les obtenir à la bonne qualité requise pour réellement construire quelque chose.
Y a-t-il des tendances ou des développements passionnants qui vous passionnent personnellement ?
Je suis ravi que les gens reconnaissent le post-traitement comme un problème et souhaitent faire quelque chose à ce sujet. C'est formidable de voir enfin le post-traitement pris au sérieux.
Dans le paysage industriel AMFG, il était intéressant de voir qu'il y avait 2 ou 3 sociétés de post-traitement. Pour moi, c'était une excellente représentation visuelle du fait que, de toutes les sociétés d'impression 3D, il n'y en a que quelques-unes en post-traitement.
Mais les gens en parlent certainement plus, et l'éducation est vraiment impérative ici. Parce que si vous ne le savez pas, vous ne savez pas que c'est un problème. Nous devons donc éduquer avant de pouvoir vendre, et également nous éduquer en termes de ce dont nos utilisateurs ont besoin.
L'autre tendance passionnante est que nous voyons maintenant des acteurs industriels arriver sur le marché, et je ne parle pas des fabricants d'imprimantes, je veux dire des utilisateurs de la technologie. Les entreprises recherchent donc vraiment des applications d'impression 3D et envisagent désormais sérieusement l'impression 3D, et c'est une grande tendance.
En fin de compte, nous devons nous concentrer sur les applications réelles.
Je vais vous donner une analogie :à quand remonte la dernière fois que quelqu'un est venu vous voir et vous a dit : « Regardez cette pièce moulée par injection, regardez comme elle est géniale ». Tu t'en fiches, personne ne s'en soucie, ça n'a pas d'importance. C'est ce dont nous avons besoin pour sortir de nos têtes et simplement passer à la nouvelle technologie. Et le temps viendra où personne ne saura faire la différence.
Nous avons déjà commencé, et nous montrons aux gens en disant :« Regardez, c'est une pièce moulée par injection », et ils ne clignent même pas des yeux. Ensuite, nous leur montrons une pièce imprimée en 3D que nous avons post-traitée et ils disent :« Oh mon Dieu, c'est incroyable ». Nous devons surmonter cela et pouvoir simplement l'accepter comme une autre technologie de fabrication.
À quoi ressembleront les 12 prochains mois pour AMT ?
Les 12 prochains mois verront une croissance très rapide, à la fois en termes d'expansion et de chiffre d'affaires.
Nous lancerons également notre système DMS de bout en bout à la fin de l'année prochaine, qui comprennent le dépoudrage, le lissage, la coloration et l'inspection — entièrement automatisés. Et c'est vraiment notre objectif à l'aube de 2020 - lier ces éléments entre eux, afin que nous puissions vraiment offrir un système de post-traitement de bout en bout dans le vrai sens du terme.
Pour en savoir plus sur AMT, visitez :https://amtechnologies.co.uk/
impression en 3D
- Keyvan Karimi d'AMFG :« Pourquoi il est temps que les logiciels de fabrication additive évoluent »
- Technologies de fabrication additive :l'entreprise de post-traitement qui façonne l'avenir de la fabrication
- 6 raisons pour lesquelles vous devez envisager la conception pour la fabrication additive
- Entretien d'experts :Guillaume de Calan, PDG de Nanoe, sur l'avenir de l'impression 3D céramique
- Comment Ford Motor Company innove l'impression 3D pour l'industrie automobile :entretien d'expert avec Harold Sears
- Entretien d'experts :PDG de PostProcess Technologies sur la résolution du goulot d'étranglement du post-traitement pour la fabrication additive
- Entretien d'experts :Doug Hedges, président de Sintavia, sur la réalisation de la production en série avec l'impression 3D en métal
- Entretien d'experts :Brian Alexander de Solvay sur le développement de polymères hautes performances pour l'impression 3D
- Le cas de l'impression 3D dans le secteur manufacturier