Évolution de l'AFP pour la prochaine génération
Si le placement automatisé de fibres (AFP) et la pose automatisée de rubans (ATL) étaient les procédés de fabrication qui ont permis une application généralisée des composites dans le Boeing 787 et l'Airbus A350, ce sera également l'AFP/ATL qui ouvrira la voie à la prochaine génération d'équipements commerciaux. avion, maintenant sur des planches à dessin. La différence cette fois-ci ? Évaluez.
Boeing estime que, d'ici 2037, le monde aura besoin de plus de 31 000 nouveaux monocouloirs pour répondre à la demande des passagers. Airbus prévoit un besoin de plus de 28 000 monocouloirs d'ici 2037. Les deux sociétés envisagent de remplacer leurs piliers monocouloirs, le 737 (Boeing) et l'A320 (Airbus). On s'attend à ce que les deux sociétés emploient des composites de manière significative sur tout nouvel avion qu'elles développent. Les deux sociétés disent à leurs chaînes d'approvisionnement de s'attendre à des taux de production pour ces avions de 60 à 100 avions par mois, en mettant l'accent sur 100. La catégorie des monocouloirs, pour les deux sociétés, représente environ les deux tiers de la demande mondiale totale, ce qui signifie que le L'environnement de fabrication développé pour les avions monocouloirs deviendra l'environnement de fabrication par défaut pour les aérocomposites dans un avenir prévisible.
Tout cela signifie que la technologie d'automatisation doit être développée dès maintenant si elle veut répondre aux exigences de qualité et de taux de production des avions de nouvelle génération. Rien de tout cela n'est perdu pour l'ingénieur principal d'Electroimpact (EI, Mukilteo, Wash., États-Unis), Todd Rudberg. Rudberg et EI sont entrés dans le monde des composites en 2004 lorsque la société a développé la technologie AFP pour la fabrication de la section de fuselage avant du 787 Section 41 fabriquée par Spirit AeroSystems (Wichita, Kan., États-Unis). EI a ensuite produit des systèmes AFP et ATL pour la fabrication d'autres structures de 787, de structures A350, de structures de moteurs et, plus récemment, de longerons d'aile de Boeing 777X. Aujourd'hui, Rudberg se penche sur l'avenir de la fabrication d'avions de nouvelle génération et voit des opportunités pour l'AFP de s'améliorer. Essentiellement.
Les opportunités, dit Rudberg, sont évidentes quand on regarde les données. En fait, EI a développé plusieurs mesures pour aider l'entreprise à comprendre ce que ses machines font bien et ce qu'elles peuvent améliorer. Tout d'abord, en examinant le paysage AFP de 2019, Rudberg voit une myriade de menaces pour la technologie AFP actuelle, y compris l'ATL, le drapage à la main, les charges plates des tissus tissés et, bien sûr, l'aluminium.
Les métriques AFP développées par Rudberg proviennent d'un projet de démonstration de production complète (FPD) pour lequel EI a mené quatre versions de pré-production. Les données de l'une de ces versions, réalisées en février 2019 avec la technologie « standard » EI AFP, ont révélé un défi substantiel d'utilisation de la machine, le temps d'utilisation de la machine tombant dans l'un des sept compartiments :
- Projection laser :30 %
- Tour : 27 %
- Contrôle :22 %
- Rupture :10 %
- Arrêt provoqué par l'opérateur :6 %
- Récupération d'erreur :3 %
- Image :2 %
Vu d'une autre manière, avec la technologie actuelle, il y a une opération à valeur ajoutée dans AFP (run), avec toutes les autres opérations considérées comme sans valeur ajoutée. Ainsi, le rapport entre les opérations de valeur et les opérations sans valeur est de 1:3. "L'industrie veut vraiment 3:1, et moi aussi", dit Rudberg, "et j'aimerais que cela soit fait avant de prendre ma retraite." Le but, simplement, est de réduire le temps consommé par les opérations sans valeur ajoutée.
Il existe également une métrique AFP globale qui nécessite une explication :les bandes moyennes avant défaillance (MSBF). Il s'agit du nombre moyen de câbles de fibres placés entre les échecs de placement. Plus ce nombre est élevé, bien sûr, plus la machine et le processus sont fiables. Selon Rudberg, la version FPD de février avait un MSBF de 5 365.
Les objectifs
En regardant de plus près le fonctionnement de l'AFP, dit Rudberg, EI n'a un contrôle direct que sur trois opérations :l'exécution, la récupération d'erreur et l'inspection. Et c'est là que l'entreprise concentre ses efforts. Cela dit, Rudberg souligne que l'avionneur a également un rôle à jouer, notamment dans la réduction des inspections de qualité, des pauses et des arrêts induits par l'opérateur. « Nous devons réaliser que les temps d'exécution sont devenus très faibles car les machines sont très rapides », dit-il, « et tout ce qui n'a pas de valeur ajoutée a un impact considérable sur votre utilisation. Donc, il s'avère que c'est un sport d'équipe. Non seulement l'OEM — moi — doit faire mieux, mais l'avionneur a aussi une part de responsabilité. »
Pour la construction d'avions de nouvelle génération, Rudberg souhaite augmenter le MSBF à> 20 000, augmenter le temps d'exécution à 77 % et éliminer complètement la projection laser, l'arrêt et l'image induits par l'opérateur. Comment? Rudberg identifie trois domaines technologiques qui peuvent faciliter cette transition :les cantres servocommandés, l'inspection et la gestion des données à 100 % en cours de processus, ou EI 4.0.
Tous les trois ont été évalués par l'IE dans une série de versions récentes de projets FPD après cette version initiale de février. Les données du projet FPD lui-même prouvent que l'IE va dans la bonne direction. Rudberg dit que le système AFP utilisé - appelé MuSCLE - a atteint une puissance de crête de 1 500 chevaux, une accélération/décélération de 0,5 G, un taux de pose de 4 000 pouces/minute, un temps de rotation de la tête de 1 seconde, une vitesse de virage de 120 degrés/seconde et 6 000 MSBF (réalisé en production).
La conversion aux cantres à servomoteur, et à l'abandon des cantres servo-pneumatiques, a déclaré Rudberg, a été effectuée pour augmenter la vitesse de placement du remorquage, la précision du placement du remorquage, le contrôle de la tension du remorquage et la fiabilité globale de la construction. L'entreprise a passé les deux dernières années à travailler sur un servomoteur compact pouvant être installé sur la tête modulaire EI. Les résultats de la technologie, jusqu'à présent, sont prometteurs; les tests montrent :15 000 MSBF, une vitesse d'ajout 87 % plus rapide, une vitesse de coupe 36 % plus rapide, une meilleure précision de placement des extrémités. En outre, EI a prouvé que le système de cantre à servomoteur pouvait être utilisé pour placer des fibres de carbone sèches.
La clé de l'inspection est la partie « en cours ». EI dispose déjà d'une technologie d'inspection, développée avec Aligned Vision (Chelmsford, Mass., États-Unis) et déployée sur la ligne de fabrication d'ailes 777X qui utilise la technologie laser et de vision pour vérifier les chevauchements, les espaces, les plis, les erreurs de positionnement final et les débris d'objets étrangers ( FOD). Ce système, cependant, existe indépendamment du système AFP et nécessite un champ de vision clair pour fonctionner, ce qui signifie que la tête AFP doit être déplacée. Rudberg et EI ont développé un nouveau système d'inspection, appelé RIPIT, qui fait partie intégrante de la tête AFP et inspecte le placement des fibres dès qu'il se produit.
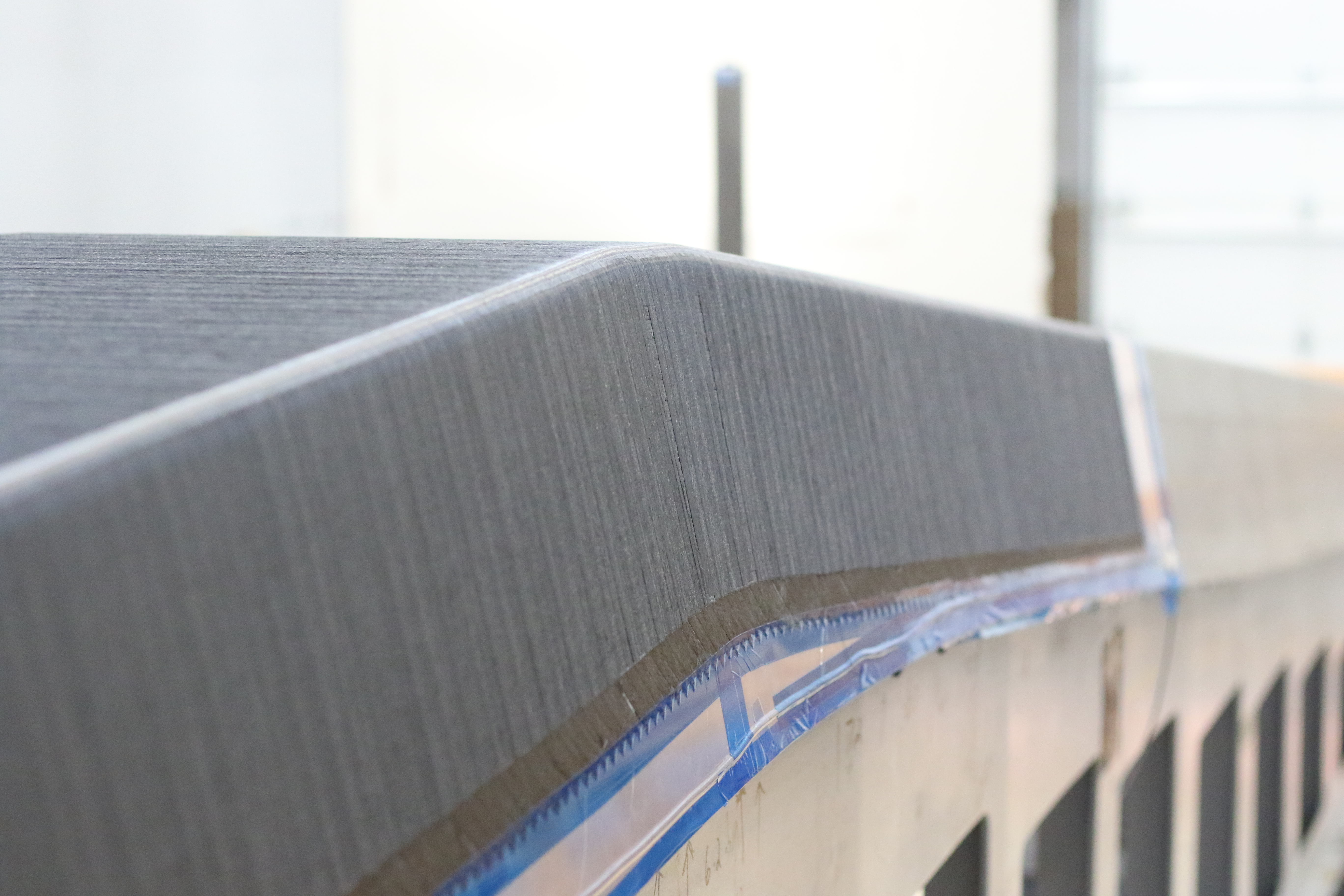
Alors que Boeing et Airbus envisagent des procédés de fabrication de composites hors autoclave, la capacité des systèmes AFP à placer efficacement des fibres de carbone sèches sera cruciale. Ce longeron de démonstration montre une fibre sèche placée par un système Electroimpact. Origine | Électrochoc
EI ne divulguera pas la nature de la technologie derrière RIPIT, sauf pour dire qu'elle n'est pas basée sur le laser ou la vision. Dans tous les cas, selon Rudberg, les tests du système révèlent qu'il est capable de détecter, en temps réel, le glissement du remorquage à ± 0,030 pouce, d'ajouter le placement à ± 0,050 pouce et de couper le placement à ± 0,050 pouce. De plus, dit Rudberg, « Nous avons effectué de nombreux essais pour corréler les données RIPIT avec le système de vision existant qualifié par Boeing [système de vision alignée utilisé sur le 777X] et nous obtenons une corrélation. »
La valeur de la gestion des données, explique Rudberg, réside dans la capacité des systèmes d'EI à aider les fabricants à voir plus clairement à quel point le processus AFP fonctionne. À cette fin, EI a développé un logiciel de visualisation de données - EI 4.0 - qui offre une visibilité non seulement sur les performances d'une machine donnée (basée sur MSBF) au cours d'une construction donnée, mais également sur les performances des traits et des séquences individuels. Fondamentalement, le logiciel aide l'opérateur à voir exactement où se situe le problème dans la tête AFP. « Donc, nous utiliserons cette EI 4.0 pour indiquer où ils [les opérateurs] doivent aller chercher dans la tête de l'AFP pour apporter des modifications », explique Rudberg.
À l'aide de ce logiciel, il est possible d'afficher graphiquement le MSBF pour une variété de fonctions de la machine et d'identifier les câbles de fibres problématiques et les séquences particulièrement difficiles. Le logiciel mesure et signale également d'autres activités de la machine qui pourraient éroder l'utilisation. À l'aide de ces outils de gestion des données, EI a pu optimiser et réduire le temps de création de l'OPS de plus de 50 minutes à un peu moins de 40 minutes. D'autres outils incluent des comparaisons de performances de changement de vitesse et des comparaisons d'angles de pli.
"Je pense que l'utilisation de 75 % est un objectif ou une attente réaliste", affirme Rudberg. « Mais, il va falloir un travail d'équipe, il va falloir une initiative organisationnelle et un suivi de la part de l'avionneur, il va falloir notre technologie améliorée, il va falloir une meilleure maintenance préventive et prédictive, et de meilleurs outils pour analyser l'utilisation des cellules et performances de la machine."
Résine
- Industrie 4.0 et IoT :tendances du marché pour les prochaines années
- Réalité augmentée – La prochaine grande nouveauté pour les RH ?
- DARPA travaille sur des matériaux de nouvelle génération pour les véhicules hypersoniques
- Nouveaux cristaux pour les technologies d'affichage de nouvelle génération
- Comment se préparer à la prochaine interruption de la chaîne d'approvisionnement
- Cinq règles pour la prochaine crise de la chaîne d'approvisionnement
- Le marchandisage dans le cloud est le prochain incontournable pour la vente au détail
- Matériel pour la prochaine génération de capteurs intelligents
- COVID-19 :Demande pour la prochaine génération d'usines intelligentes