Connecter des composites à l'acier
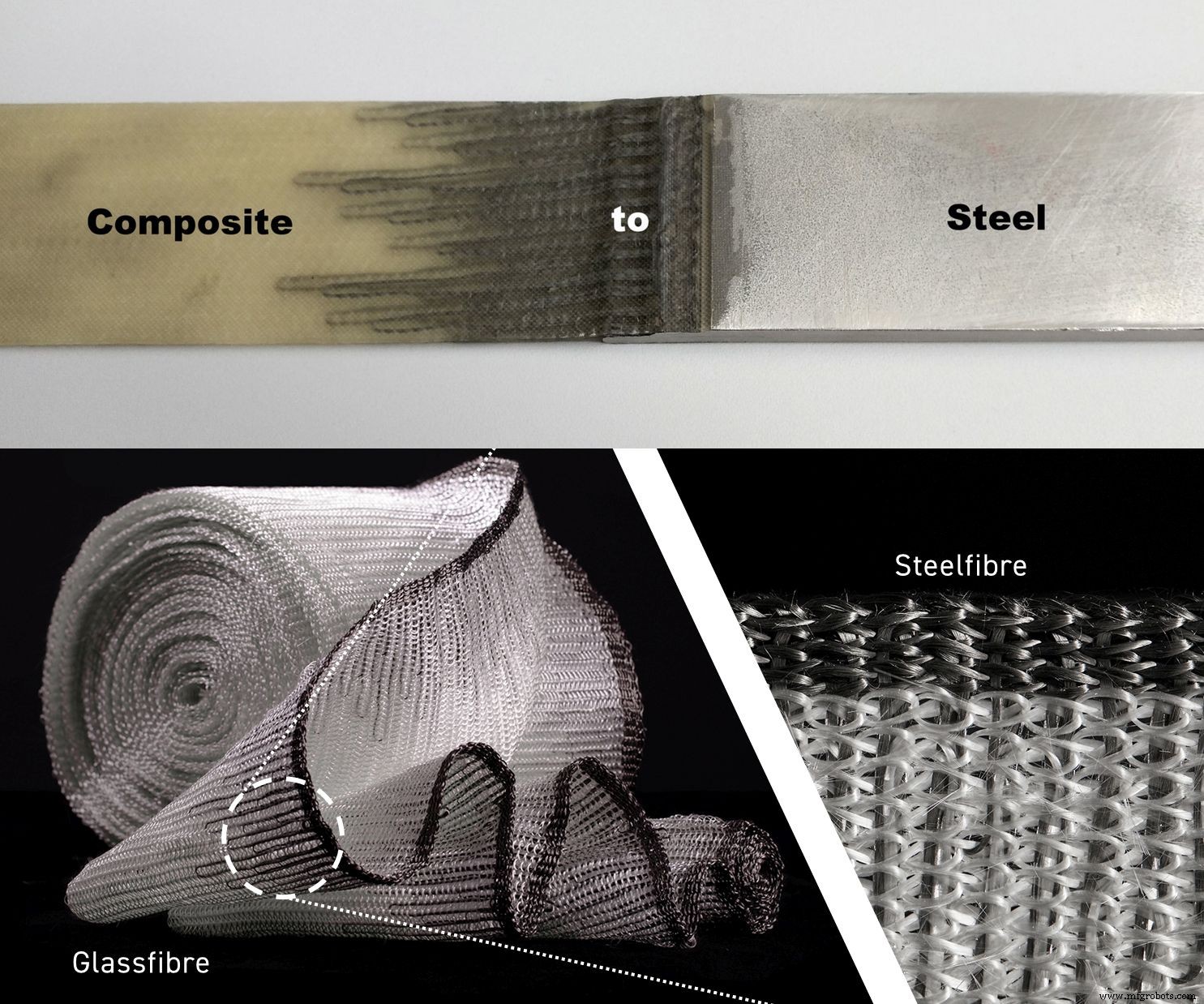
Ce blog est un complément à mon article de fond de décembre 2019, « Supprimer les obstacles à l'allègement des navires avec des composites », partageant quelques détails et visuels supplémentaires.
HYCONNECT GmbH (Hambourg, Allemagne) est une startup fondée par le Dr Lars Molter, architecte naval et vétéran de 10 ans du Center of Maritime Technologies (CMT, Hambourg, Allemagne), un centre de R&D pour l'industrie maritime allemande. « Les entreprises allemandes qui construisent des mégayachts et des navires de croisière ont toutes le même problème », explique Molter. « Leurs clients souhaitent ajouter plus d'équipements, une autre terrasse, plus d'isolation contre le bruit et la température ou de nouvelles fonctionnalités de conception, telles que des formes courbes et un éclairage intégré. Même s'ils peuvent faire ces conceptions avec de l'aluminium ou de l'acier, cela prend beaucoup de temps et d'argent. »
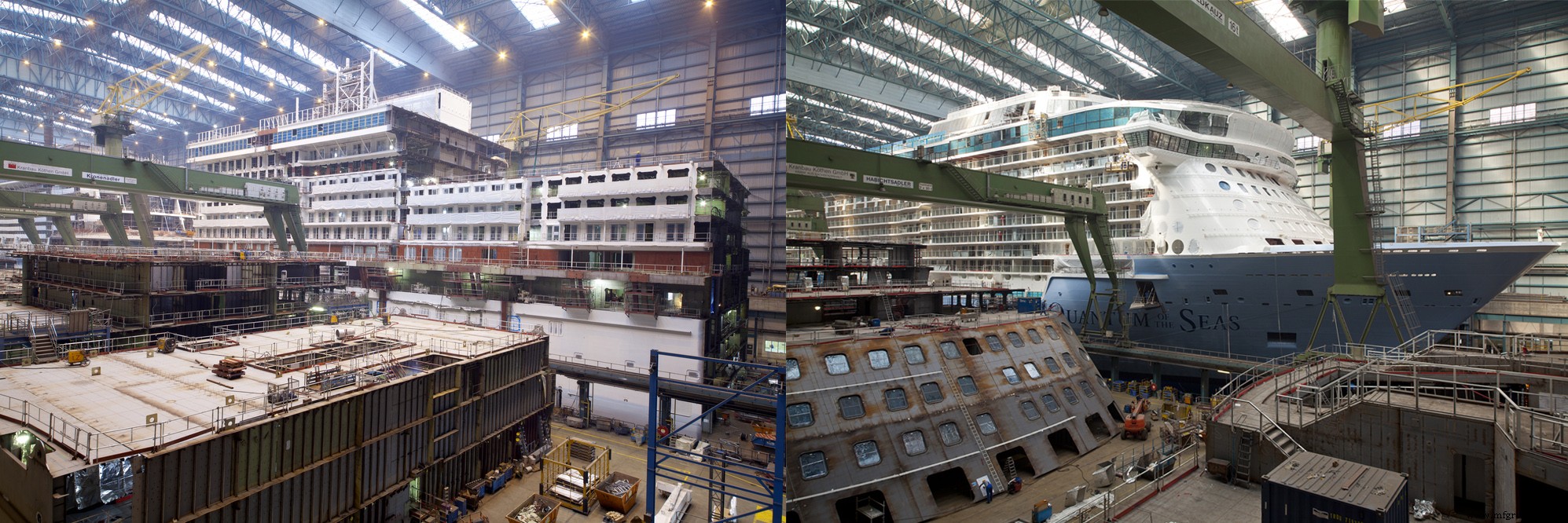
Les navires sont généralement construits dans des blocs de composants en acier soudés pour un assemblage plus rapide, comme indiqué ici. Le système de joint FAUSST permet de souder de grands panneaux muraux composites ou d'autres structures dans ces cadres en acier, offrant une construction légère utilisant les méthodes actuelles de production de navires. SOURCE | Meyer Werft
Problèmes de collage dans les structures hybrides
Molter et bien d'autres peuvent voir les avantages que les composites peuvent apporter aux navires, mais actuellement, les navires sont construits en acier. De nombreux travaux visent à développer des navires entièrement composites, mais en attendant, il existe une opportunité significative de réduire le poids et les émissions des navires avec une variété de composants composites. Un problème, cependant, est de savoir comment les joindre à la charpente en acier du navire. « Nous avons examiné le collage", explique-t-il, "mais il n'y a pas de conception de joint standardisée que vous pouvez utiliser dans tous les navires et il n'y a pas de règles générales sur la façon d'appliquer le collage dans SOLAS."
La réglementation sur la sécurité de la vie en mer (SOLAS), publiée par l'Organisation maritime internationale (OMI, Londres, Royaume-Uni), exigeait que les navires commerciaux soient construits en acier jusqu'en 2002, date à laquelle MSC/Circ. 1002 a été publié, permettant des conceptions alternatives. Ces alternatives, cependant, nécessitent une analyse des risques à effectuer, montrant que la conception et la construction alternatives sont équivalentes à l'acier - un processus qui est long, coûteux et sur mesure pour chaque navire construit.
« Nous avons demandé à DNV GL ce qu'ils approuveraient pour les joints de matériaux différents », explique Molter. « Ils ont dit que la structure primaire nécessiterait généralement une fixation mécanique ; le collage pur ne serait pas certifié facilement sans attaches redondantes. Ces problèmes de certification sur mesure et d'exigences des autorités réglementaires pour les attaches redondantes par rapport aux structures primaires purement collées sont identiques dans les avions commerciaux. « De plus, avec le collage, vous devez contrôler l'environnement et le processus », dit-il, notant que cela est difficile au milieu du soudage et du découpage qui dominent généralement la construction des chantiers navals.
Joints FAUSST
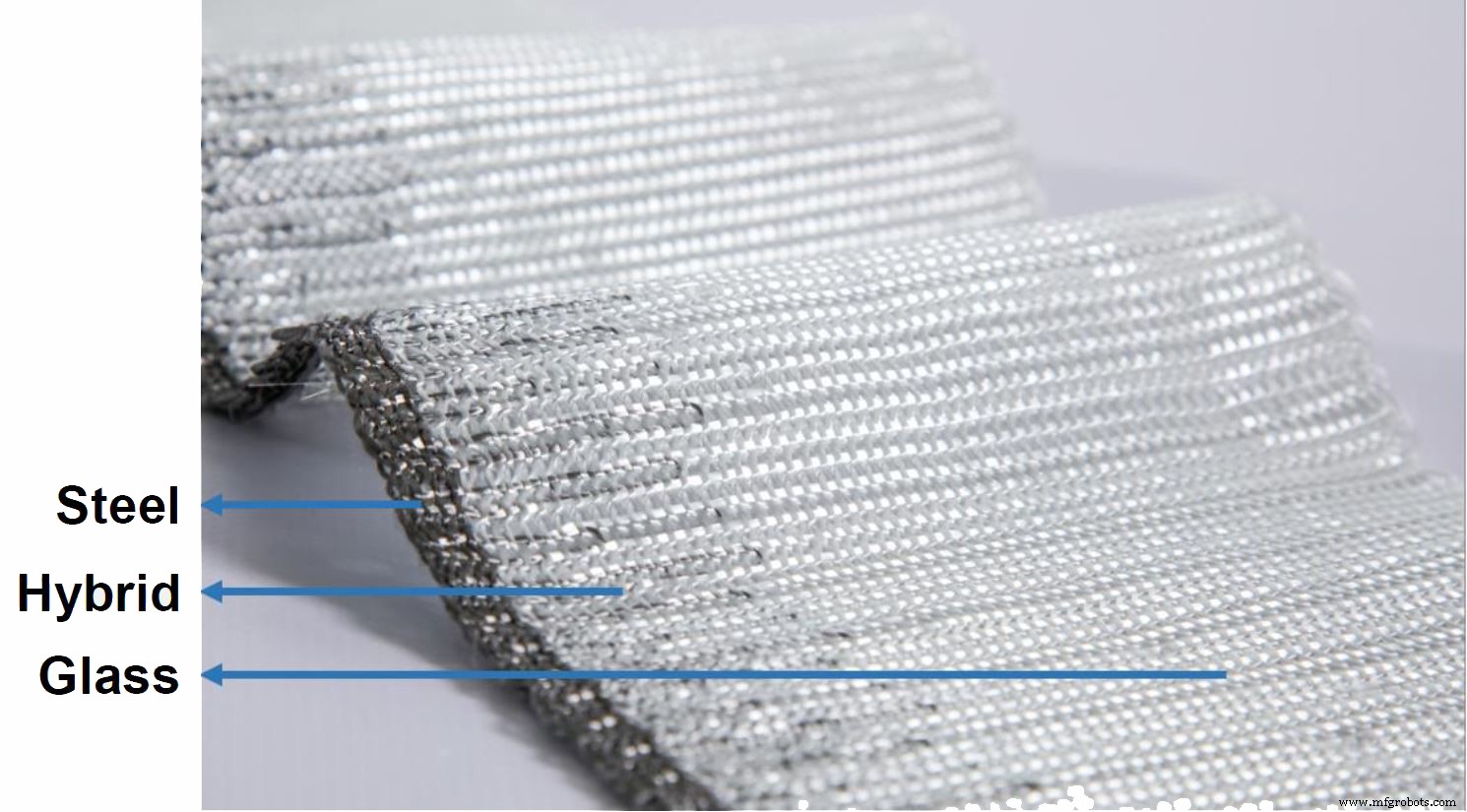
Tissu hybride FAUSST associant fibre de verre et fibre d'acier. SOURCE | Hyconnet
« Donc, nous avions besoin d'une solution sans liaison mais avec une fixation mécanique », déclare Molter. « Nous n'arrêtions pas de nous demander comment connecter les fibres au métal ? » CMT répondrait à cela dans le projet FAUSST (Fiber and Steel Standard conjoint) financé par l'Allemagne, qui a développé, en coopération avec Fritz Moll Textilwerke (Altshausen, Allemagne), un textile tricoté chaîne hybride qui passe de 100 % de fibres de verre à 100 % d'acier. fibres.
L'architecture du tissu est conçue pour que les fibres d'acier et de verre serpentent et se chevauchent, ce qui permet un transfert de charge dû au frottement ainsi qu'un emboîtement aux points de croisement. Cette architecture équilibre également le tissu tricoté pour un emboîtement mécanique avec des fibres unidirectionnelles pour transporter la charge à travers le joint. Le tissu est produit avec une machine à tricoter à commande électronique à des vitesses allant jusqu'à 100 mètres/heure.
L'étape suivante consiste à le fixer à un connecteur métallique, qui peut être une plaque ou un profilé creux. Les fibres d'acier sont soudées au connecteur par soudage par résistance (soudage à la presse) avec une grande roue à électrodes en cuivre. Molter explique que c'est comme le soudage par points dans l'automobile, mais adapté pour produire un long joint continu. Ce procédé permet de produire efficacement des connecteurs FAUSST à une ou plusieurs couches de tissu selon un procédé robuste et bien connu.
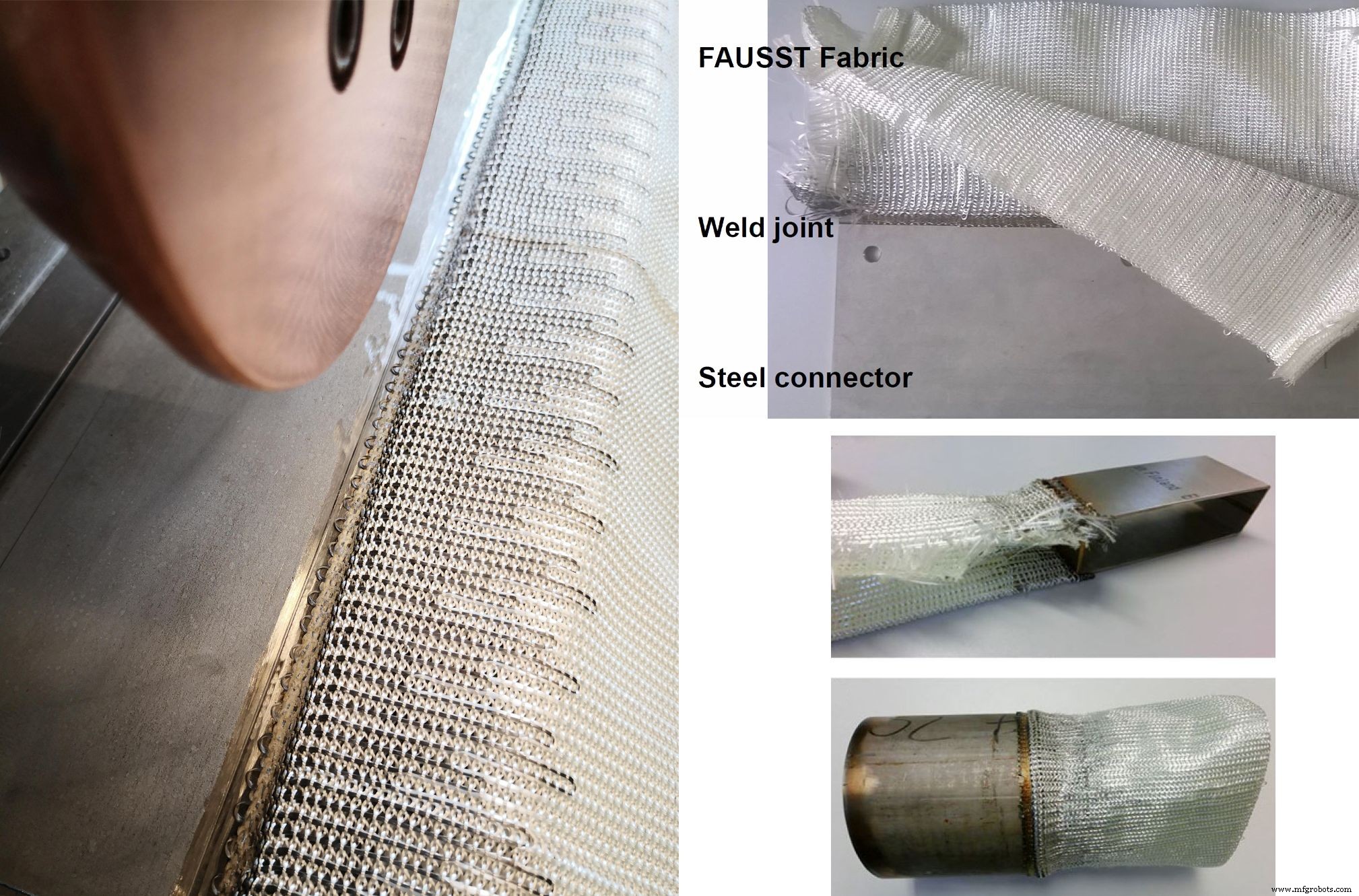
Hyconnect utilise la soudure continue pour joindre le tissu FAUSST aux connecteurs en acier. SOURCE | Hyconnect.
C'est ce que vend HYCONNECT :le tissu soudé à un connecteur en acier. « Un chantier naval ou son fournisseur de structures composites décide d'utiliser notre système de joint, explique Molter. « Ils spécifient la charge de joint et le type de connecteur en acier, puis nous concevons et produisons le joint FAUSST. C'est ce que nous livrons et ils infusent ensuite cela dans leurs structures composites et le chantier naval les soude ensuite dans la charpente en acier du navire. »
Gestion de la rigidité et de l'inadéquation CTE
Il existe un décalage de rigidité entre les fibres d'acier et les fibres de verre dans le tissu hybride FAUSST. Molter explique que cela est quelque peu atténué par la façon dont le tissu est fabriqué, « en utilisant 5 à 7 plis où les fils sont imbriqués, et nous varions dans quelle mesure les fibres d'acier s'étendent dans le tissu en fibre de verre. Vous ne voulez pas de gros pics de transfert de charge. Nous pouvons modifier la rigidité en modifiant ces couches et leurs fibres constitutives, par exemple le pourcentage et la direction de la fibre de verre, etc. Des fibres supplémentaires de ± 45° peuvent être ajoutées pour gérer une contrainte de cisaillement plus élevée et aident également à gérer les différents coefficients de dilatation thermique (CTE) entre le connecteur en acier et le composite en fibre de verre. "Nous pouvons également concevoir pour des charges plus élevées ou des constructions spéciales en renforçant dans l'épaisseur à l'aide de fibres tuftées", explique Molter.
La différence d'épaisseur entre le connecteur en acier et le plastique renforcé de fibres (PRF) doit également être corrigée. « L'axe neutre des deux matériaux doit être aligné », explique Molter. "Ceci est généralement réalisé en usinant le bord du connecteur en acier à un cône de 30°, créant, en effet, un joint conique pour un transfert de charge efficace vers le FRP."
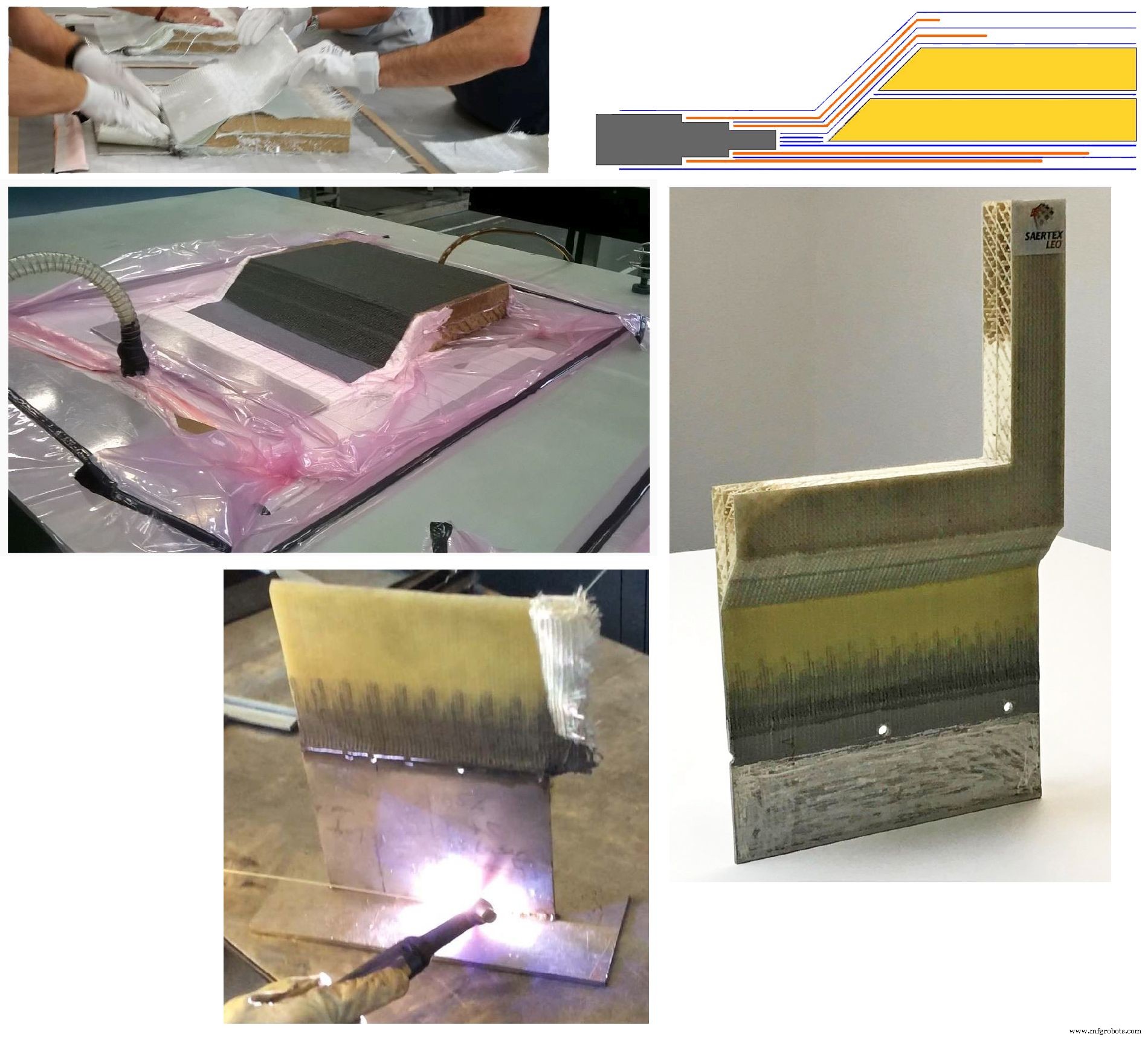
Hyconnect conçoit et produit des joints FAUSST, qui sont ensuite infusés dans des structures composites et, enfin, soudés dans la charpente en acier d'un navire. SOURCE | Hyconnect.
Développer un système commun standardisé
Molter a quitté CMT et a fondé HYCONNECT en 2018 pour commercialiser la technologie commune FAUSST. La société a travaillé avec une variété de partenaires industriels et d'autorités de réglementation pour effectuer des tests et itérer des conceptions communes. L'objectif est de développer une « famille » de produits communs FAUSST. « Il y a une augmentation linéaire de la capacité de charge en appliquant plus de couches de tissu FAUSST », explique Molter. « Donc, un produit de base pourrait être constitué de quatre couches de FAUSST avec une barre plate de 1 mètre soudée dessus, évaluée pour une certaine charge de traction et de flexion. Ensuite, il y aurait des produits disponibles à gauche, en utilisant deux ou trois couches pour une charge nominale inférieure, et d'autres à droite, tels que cinq ou six couches pour une charge nominale plus élevée. Nous sommes encore en train de finaliser ces détails, mais l'objectif est un système standardisé et facile à utiliser. »
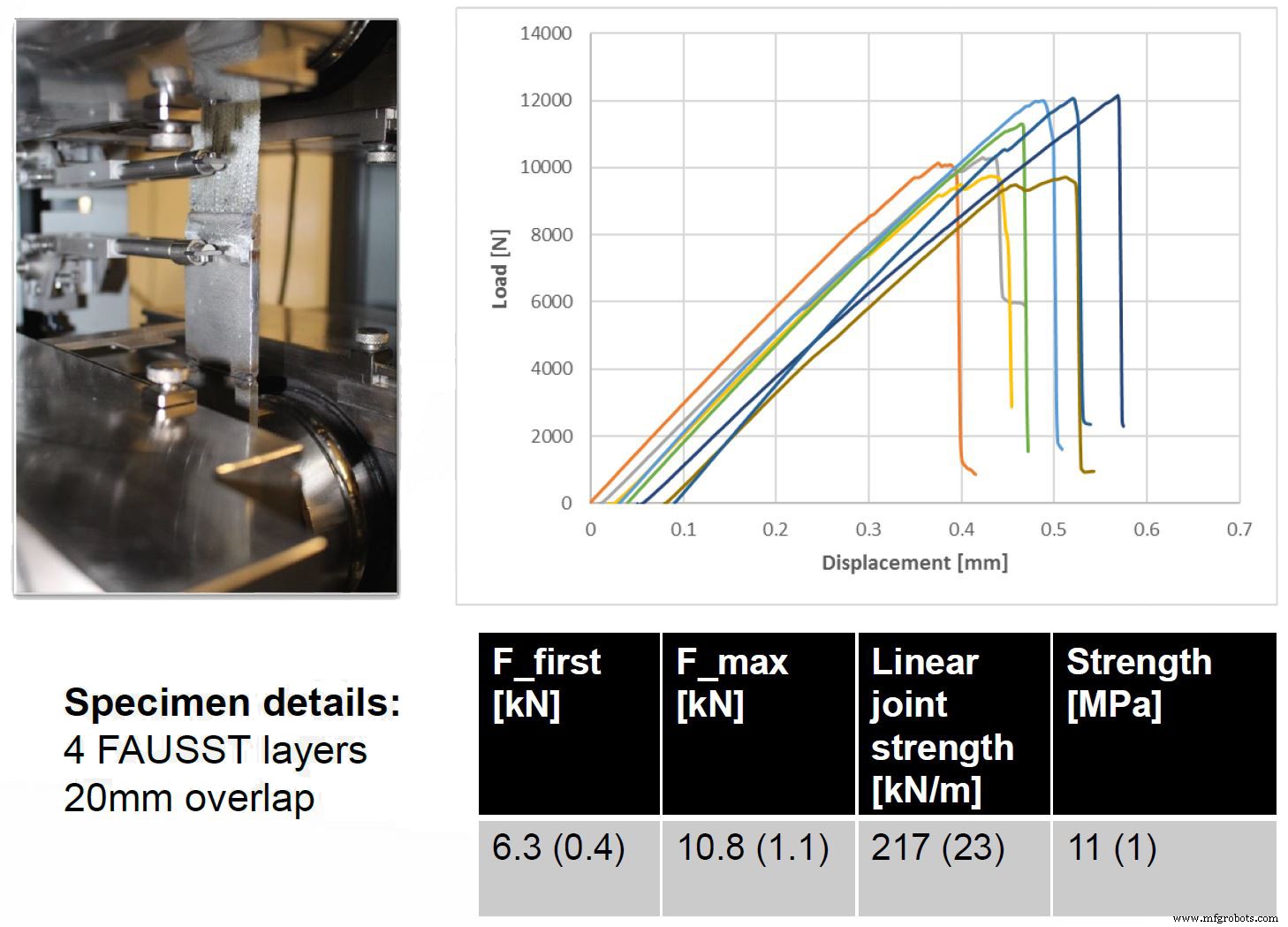
Les tests Hyconnect de joints comprenant quatre couches de tissu FAUSST fournissent une résistance de joint de revêtement de 217 kN/M. SOURCE | Hyconnect.
La caractérisation mécanique des produits de joint FAUSST est toujours en cours, mais Molter souligne qu'ils sont compétitifs avec les joints adhésifs. « Ils permettent également une inspection à 100 % à l'aide d'ultrasons ou de tests aux rayons X de la soudure », ajoute-t-il. Des prototypes sont actuellement produits pour des clients sélectionnés et seront mis à l'échelle en 2020.
Parallèlement, HYCONNECT a également suscité l'intérêt des constructeurs et constructeurs automobiles intéressés par les applications ferroviaires. « Il est possible d'utiliser cette technologie pour les inserts métalliques et nous voyons également des applications possibles dans la construction de bâtiments », déclare Molter. "De plus en plus d'industries voient l'intérêt des structures hybrides et la possibilité de temps d'assemblage courts en utilisant des produits semi-finis pré-équipés."
fibre