Les 6 erreurs d'entreposage les plus coûteuses (et comment les éviter)
Les entrepôts restent un élément crucial des réseaux mondiaux de la chaîne d'approvisionnement, car les consommateurs s'attendent à des livraisons plus rapides. La mise en place d'un entrepôt nécessite une planification minutieuse et plusieurs systèmes uniques doivent être intégrés à l'équipement et aux logiciels. En outre, la haute priorité accordée à une rotation rapide et à une exécution précise et rapide des commandes nécessite que la direction supprime tout goulot d'étranglement susceptible d'entraîner des retards.
Dans cet article, nous allons explorer six erreurs d'entrepôt coûteuses et comment vous pouvez les éviter. Ces erreurs courantes peuvent être facilement ignorées lors des étapes de planification d'un projet d'entrepôt. Mais, comme nous le verrons, bon nombre de ces problèmes peuvent entraîner des perturbations dans l'entrepôt et nécessiter des solutions coûteuses pour les corriger. Comprendre ces erreurs peut vous aider à éviter des difficultés similaires lors de vos projets d'aménagement et d'amélioration d'entrepôt.
1. Un mauvais agencement d'entrepôt

La disposition d'un entrepôt définit le cadre complet de la façon dont le travail sera effectué dans l'ensemble de l'installation. Il est essentiel de créer une conception optimisée dès le départ, car il peut être difficile d'apporter des modifications après l'installation des racks, des étagères et des équipements. En plus de choisir une mise en page efficace, il est également important d'éviter les erreurs courantes qui peuvent causer des problèmes plus tard. Voici quelques-unes des erreurs d'aménagement d'entrepôt les plus courantes :
- Avoir des zones d'expédition et de réception qui se chevauchent
- Ne pas créer d'espaces pour les retours de produits et les surstocks
- Concevoir des allées et des zones de travail trop petites
- Ne pas maintenir les espaces de travail de l'entrepôt propres et rangés
Un entrepôt organisé doit avoir des zones clairement délimitées et dédiées aux différents types de travail et des voies de circulation identifiées pour les personnes, les chariots élévateurs et autres équipements mobiles. Les panneaux d'entrepôt personnalisés tels que les panneaux d'allée d'entrepôt, les panneaux de porte et de quai intérieurs, les panneaux de porte et de quai extérieurs et les panneaux de sécurité d'entrepôt fournissent des repères directionnels et aident les travailleurs à identifier les différentes zones de l'entrepôt pour une navigation facile. Les solutions de signalisation d'entrepôt transmettent des informations cruciales pour assurer la fluidité du trafic. Non seulement un flux de trafic optimal améliore la productivité, mais il améliore également la sécurité de l'entrepôt.
2. Prévisions inexactes
Même l'entrepôt le plus efficace ne sera pas en mesure de gérer les stocks sans prévisions précises. Cela comprend la planification de l'inventaire local, des fournitures et de l'exécution des commandes. Avoir des prévisions précises donne à la direction la possibilité de définir des niveaux de stockage optimaux et de diriger les ressources de l'entrepôt pour coordonner les ordres de travail. Ces informations sont également utiles lors de l'inventaire et peuvent aider à rationaliser l'exécution et d'autres fonctions essentielles de l'entrepôt.
3. Suivi manuel
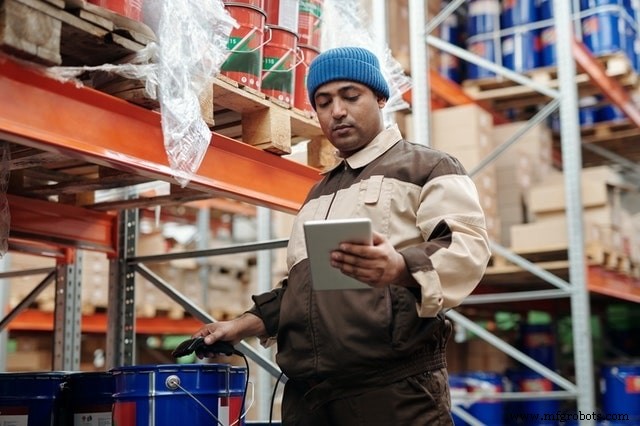
La technologie d'automatisation des entrepôts est véritablement devenue courante et constitue une excellente ressource pour améliorer les flux de travail du site. L'utilisation de procédures qui nécessitent un excès de paperasse et de saisie manuelle des données peut prendre beaucoup de temps et nécessiter plus d'efforts. L'une des étapes les plus critiques pour éliminer le travail manuel consiste à investir dans un logiciel de gestion d'entrepôt (WMS) qui peut être utilisé pour centraliser tous les flux de travail critiques de l'entrepôt.
Ces plates-formes peuvent également être intégrées avec des codes-barres et des scanners pour automatiser plusieurs fonctions d'entrepôt telles que le prélèvement, l'emballage et l'expédition. Un WMS entièrement intégré est l'épine dorsale d'un entrepôt qui fonctionne bien et peut être continuellement amélioré avec de futures intégrations et modules complémentaires.
4. Choisir les inefficacités
Le processus de préparation des commandes est un domaine critique pour la direction et le personnel chargé de l'exécution des commandes dans un entrepôt. De nombreux entrepôts modernes comprennent des tapis roulants, des emballeurs et d'autres équipements pour faciliter le déplacement des stocks, ce qui peut rendre la préparation des commandes plus efficace, mais peut également créer des goulots d'étranglement si ces outils ne sont pas soigneusement intégrés aux flux de travail de l'entrepôt. Un picking optimisé nécessite des trajets soigneusement aménagés et une disposition qui priorise le flux des stocks. Il est également recommandé d'avoir une signalisation claire et des étiquettes de rack dans tout l'entrepôt pour une identification facile de l'inventaire.
Avec une variété d'étiquettes et de panneaux de code-barres d'entrepôt disponibles, tels que des étiquettes de rack d'entrepôt, des étiquettes de sol d'entrepôt, des panneaux d'entrepôt suspendus, des étiquettes de rack d'entrepôt frigorifique et des pancartes de rack d'entrepôt frigorifique, des étiquettes et des étiquettes de code-barres pour palettes et des étiquettes de code-barres pour les conteneurs consignés, plateaux et bacs, vous pouvez facilement étiqueter chaque zone de l'entrepôt pour assurer une numérisation et un suivi transparents et éliminer la saisie manuelle des données pour une précision améliorée.
5. Gérer tous les stocks de manière égale
Une autre erreur courante dans les entrepôts consiste à traiter tous les stocks sur un pied d'égalité. Chaque élément de stock peut avoir des exigences de stockage, de demande et de manutention différentes. Les stocks à rotation élevée doivent être placés dans des emplacements de stockage et de préparation de commandes au sein de l'entrepôt, ce qui facilite leur accès pour les préparateurs de commandes et les chariots élévateurs.
Il est également recommandé de stocker les stocks avec une demande plus faible loin des zones à fort trafic pour maximiser l'efficacité. Les stocks saisonniers et périssables doivent être soigneusement pris en compte, et il peut être avantageux d'avoir un plan de placement des stocks rotatif qui tire parti des tendances saisonnières tout au long de l'année. Il est également important de ne pas surcharger les stocks au point de nuire à l'efficacité. Non seulement un stock trop important peut rendre l'utilisation de l'espace un défi important, mais il augmente également vos frais généraux, surtout si vous finissez par conserver un stock excédentaire pendant une longue période.
6. Planification à court terme
Ne pas préparer l'avenir est un risque majeur pour toute entreprise. Il est impossible de tenir compte de chaque tendance de l'industrie ou de la clientèle, mais l'adoption d'une planification à long terme peut être très utile. La croissance future peut nécessiter un investissement important dans de nouveaux équipements, systèmes et technologies d'automatisation. La création d'un plan formel vous donne un point focal et une base de référence qui peuvent être révisés périodiquement et mis à jour pour refléter les dernières informations disponibles. Ces périodes d'examen constituent également un excellent moment pour recueillir les commentaires des employés sur ce qui fonctionne bien et sur les points à améliorer.
Les entrepôts modernes ont prouvé qu'un agencement efficace, une planification appropriée et le respect des meilleures pratiques de l'industrie peuvent être combinés pour créer un centre de distribution de haute qualité. La direction de l'entrepôt et les autres membres du personnel doivent être conscients des erreurs courantes qui peuvent souvent être surmontées grâce à une planification minutieuse au cours des premières étapes de la configuration ou de la rénovation d'un entrepôt. Éviter ces erreurs donne à toute votre équipe plus d'énergie à consacrer au travail à valeur ajoutée et à la création d'une opération efficace.
Technologie industrielle
- 6 risques liés à l'exportation de produits manufacturés — et comment les éviter
- Six erreurs logistiques courantes et comment les éviter
- Trois pièges de la livraison au dernier kilomètre — et comment les éviter
- Sept erreurs courantes d'expédition et comment les éviter
- Comment tirer le meilleur parti de votre système de numérisation d'entrepôt
- 4 principales causes de défaillance d'appareillage de commutation et comment les éviter
- Qu'est-ce que la cavitation de la pompe et comment l'éviter ?
- 3 principaux processus d'entrepôt (et comment les améliorer)
- 5 dangers courants liés aux grues et comment les éviter