7 processus d'entrepôt et comment les optimiser
Tout entrepôt, centre de distribution ou centre de distribution doit gérer un flux constant d'inventaire entrant et sortant de l'installation. La technologie a rendu ce processus beaucoup plus facile avec des plates-formes centralisées telles qu'un système de gestion d'entrepôt (WMS). Ces logiciels peuvent être connectés à des capteurs, des scanners et des codes-barres pour créer un environnement de travail numérique et automatisé.
Pour optimiser le flux des stocks, les responsables d'entrepôt doivent décomposer la répartition du travail en étapes spécifiques. Dans cet article, nous allons passer en revue les sept principaux processus d'un entrepôt et discuter de la manière dont chacun d'eux peut être optimisé. En examinant l'ensemble du système dans son ensemble, il est possible d'identifier les étapes importantes qui peuvent être rationalisées pour rendre l'entrepôt plus efficace. L'objectif ultime de tout plan d'amélioration doit être d'améliorer la précision des stocks, la précision des prévisions de la demande et d'autres mesures importantes du site.
1. Réception
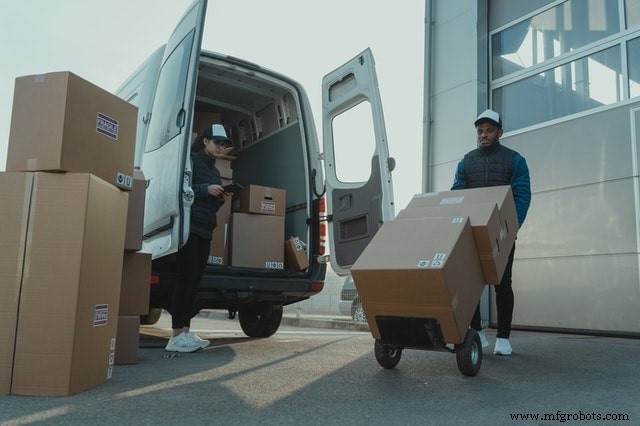
Le processus de réception est essentiel dans un environnement d'entrepôt, car il détermine le rythme de toutes les autres activités au sein de l'installation. Une opération efficace doit avoir une disposition de la zone de réception bien organisée pour éviter une accumulation inutile de livraisons. Pour optimiser les activités de réception, il peut être avantageux d'installer des convoyeurs et d'autres formes d'équipements de manutention automatisés.
L'équipement de manutention peut être particulièrement utile s'il y a une grande quantité d'espace entre la zone de réception et d'autres emplacements pour la mise en scène et le stockage des stocks. Il est également recommandé d'automatiser les procédures de réception à l'aide de codes-barres pouvant être rapidement scannés à tout moment. Une autre bonne pratique consiste à demander à vos fournisseurs des avis préalables d'expédition (ASN) qui peuvent être numérisés à la réception pour ajouter rapidement des articles à l'inventaire.
2. Rangement
Le processus suivant dans un flux de travail d'entrepôt typique est le rangement, lorsque les marchandises sont déplacées des zones de réception vers les zones de stockage. L'une des considérations les plus importantes lors de la gestion des stocks est de choisir les bons emplacements pour le stockage. Afin de rendre le processus de rangement rapide et efficace, il est important de définir à l'avance les emplacements de stockage et de créer des voies de déplacement claires pour les personnes et les chariots élévateurs dans l'entrepôt.
Ces emplacements peuvent être étiquetés avec des étiquettes de sol d'entrepôt, des panneaux et des étiquettes d'entrepôt rétroréfléchissants, des panneaux d'entrepôt suspendus et des panneaux d'allée d'entrepôt qui sont clairement visibles et/ou scannables à de plus longues distances, comme à partir d'un chariot élévateur, pour permettre aux travailleurs de localiser rapidement les bons emplacements de stockage pour les tâches de rangement. Les étiquettes et les étiquettes à code-barres des palettes et les étiquettes à code-barres pour les bacs, plateaux et conteneurs consignés peuvent également aider les employés d'entrepôt à organiser l'inventaire dans les zones de stockage appropriées. Une plate-forme WMS peut être extrêmement utile lors de l'attribution d'emplacements d'inventaire et de la numérisation d'articles entrant et sortant du stockage.
3. Stockage
Pour planifier correctement les emplacements de stockage dans une usine, la disposition doit être soigneusement étudiée afin de maximiser la quantité d'espace utilisable. Le plan d'organisation spécifique à chaque entrepôt sera unique en fonction des besoins de l'entreprise, de la structure de l'installation et des systèmes sur site utilisés.
L'un des meilleurs moyens d'optimiser le stockage consiste à définir des mesures claires permettant de suivre l'utilisation et l'efficacité de différents types de marchandises. Cela permettra d'identifier des améliorations telles que le déplacement des stocks à rotation lente vers un emplacement de stockage situé à l'écart des voies de circulation très fréquentées.
4. Cueillette
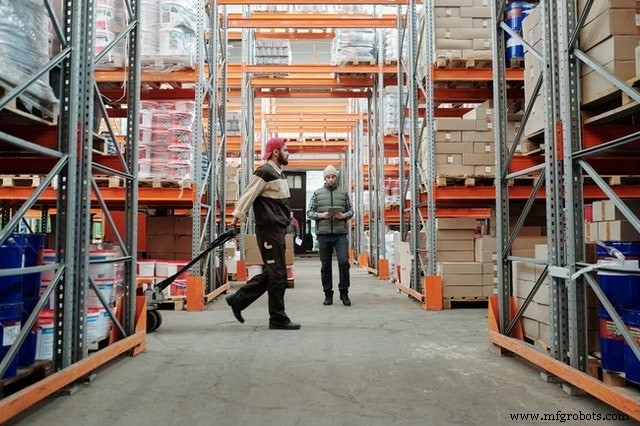
La cueillette est un processus nécessaire dans tout entrepôt pour sélectionner les marchandises qui doivent être expédiées pour exécuter les commandes. Une quantité importante de coûts et de temps est consacrée aux tâches de prélèvement, et c'est l'une des étapes les plus importantes à optimiser. Aujourd'hui, un processus de préparation de commandes efficace doit être activé par la technologie.
Bien qu'il existe de nombreuses méthodologies de prélèvement pouvant être utilisées, les étiquettes de rack d'entrepôt intégrées à un système logiciel vous permettront de suivre l'efficacité de plusieurs étapes individuelles et de trouver des moyens d'apporter d'autres améliorations. Les étiquettes pour rayonnages frigorifiques et les plaques-étiquettes pour rayonnages frigorifiques permettent d'étiqueter les rayonnages d'entrepôt même dans les zones d'entrepôt climatisées. Comprendre la précision du prélèvement dans votre entrepôt peut également vous aider à prendre des décisions concernant les ajustements à apporter à la stratégie de prélèvement et aux besoins des commandes individuelles.
5. Emballage
Lorsqu'une commande client est reçue par l'entrepôt et que les articles ont été prélevés, ils doivent ensuite être emballés et préparés pour l'expédition. L'optimisation de ce processus implique souvent la rationalisation des matériaux d'emballage et l'augmentation de la vitesse des inspections. Il est également important que chaque article dispose d'une chaîne de traçabilité complète dans l'entrepôt afin que le mouvement puisse être retracé si un problème est identifié.
6. Expédition
Le processus d'expédition, ou d'expédition, est la dernière étape avant que les articles ne quittent l'entrepôt. Afin de minimiser les retards sur les quais de chargement, les commandes doivent être soigneusement coordonnées avec la direction du centre de distribution pour s'assurer que les marchandises sont ramassées dès qu'elles sont prêtes. L'un des meilleurs moyens d'optimiser l'expédition consiste à organiser les activités de prélèvement par « vagues » afin qu'un certain nombre de colis pertinents puissent être préparés pour un seul enlèvement.
7. Retours
Une étape supplémentaire qui mérite une attention particulière est le processus de retour. Bien qu'ils ne soient pas une partie souhaitable de la gestion d'entrepôt, les retours sont une réalité commerciale. Toutes les entreprises doivent utiliser une procédure d'autorisation de gestion des retours (RMA) pour attribuer un numéro unique à chaque retour et fournir des instructions au client. Il est également important d'avoir un espace dédié dans l'entrepôt pour gérer les retours et l'inventaire pour le réapprovisionnement.
Comme vous pouvez le voir, ces sept processus majeurs sont connectés les uns aux autres au sein de l'entrepôt et ne peuvent pas être gérés dans le vide. En examinant l'ensemble du système dans son ensemble et en identifiant des mesures utiles pour chaque étape majeure, il est possible d'apporter des améliorations même à la conception d'entrepôt la plus avancée. Nous espérons que les conseils présentés dans cet article vous aideront à identifier quelques domaines d'amélioration au sein de votre propre opération d'entrepôt.
Technologie industrielle
- Sept erreurs de sélection et d'emballage courantes — et comment les corriger
- Six erreurs logistiques courantes et comment les éviter
- Sept défis de livraison du dernier kilomètre et comment les résoudre
- Comment aborder la cybersécurité par le biais de la technologie, des personnes et des processus
- Quatre types de cyberattaques et comment les prévenir
- Trois pièges de la livraison au dernier kilomètre — et comment les éviter
- Sept erreurs courantes d'expédition et comment les éviter
- 4 principales causes de défaillance d'appareillage de commutation et comment les éviter
- Principales causes de panne de machine et comment les prévenir